Introduction to Spark Plasma Sintering Furnaces (SPS)
Spark Plasma Sintering Furnaces (SPS) represent a cutting-edge technology in the field of material science, offering a unique approach to sintering through the use of on-off DC pulse current for plasma generation. This comprehensive guide delves into the intricacies of SPS technology, exploring its components such as the axial pressure device, water-cooled punch electrode, and vacuum chamber. By understanding the key features and versatile applications of SPS, we can appreciate how this technology revolutionizes the rapid, efficient, and high-quality sintering of various materials, from metals and ceramics to nanomaterials and composites.
Key Features of Spark Plasma Sintering Furnaces
Spark Plasma Sintering (SPS) furnaces have revolutionized the field of material science with their unique capabilities and rapid processing times. These furnaces utilize a high pulsed DC current to heat and sinter powder compacts, offering several distinct advantages over traditional sintering methods. Here, we delve into the key features of SPS furnaces, including rapid sintering, purification and activation sintering, fine-grain sintering, wide-range temperature sintering, density control sintering, and temperature gradient sintering.
Rapid Sintering
One of the most significant advantages of SPS furnaces is their ability to achieve rapid sintering. The heating rate can exceed 500°C/min, which is significantly faster than traditional methods such as hot pressing, hot isostatic pressing (HIP), and pressureless sintering. This rapid heating rate allows for much shorter sintering times, often reducing the process from hours to mere minutes. The fast heating and cooling rates also minimize coarsening processes and help maintain the intrinsic nanostructures of the material after full densification.
Purification & Activation Sintering
SPS furnaces offer a unique purification and activation sintering process. The high pulsed DC current induces a particle surface purification effect, which removes adsorbed gases and oxide films. This purification process, combined with the particle surface activation effect, enables the sintering of materials that are traditionally difficult to sinter. This feature is particularly beneficial for materials with high purity requirements or those that are sensitive to surface contaminants.
Fine-Grain Sintering
The rapid temperature rise in SPS furnaces inhibits grain growth, allowing for the regulation of the microstructure and the preparation of fine-grain sintered bodies. This feature makes SPS an excellent method for preparing nanocrystalline materials. By controlling the sintering parameters, researchers can achieve the desired grain size and microstructure, which is crucial for optimizing the material's mechanical, electrical, and thermal properties.
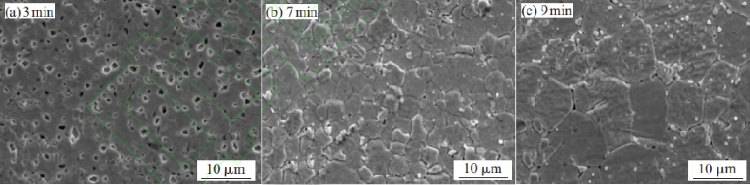
Wide-Range Temperature Sintering
SPS furnaces can operate over a wide range of temperatures, from low temperatures to as high as 2300°C. This wide temperature range makes SPS furnaces versatile for sintering a variety of materials, including ceramics, metals, and composites. The ability to reach high temperatures quickly and efficiently is particularly useful for materials that require high-temperature processing to achieve full densification and optimal properties.
Density Control Sintering
Another notable feature of SPS furnaces is their ability to control the density of the sintered body. From porous bodies to fully dense sintered bodies, SPS furnaces offer flexible density control. This is achieved by adjusting the sintering parameters, such as the applied force, piston travel, and current. The precise control over density is essential for tailoring the material's properties to specific applications, such as in aerospace, automotive, and medical industries.
Temperature Gradient Sintering
SPS furnaces can create a temperature gradient within the mold, allowing for the simultaneous sintering of materials with different melting points. This feature is particularly useful for preparing functionally graded materials (FGMs), where different layers or regions of the material require different processing conditions. The ability to create a temperature gradient (hundreds of °C/mm) within the mold enables the production of complex, multi-layered materials with tailored properties and functionalities.
In conclusion, SPS furnaces offer a range of advanced features that make them a powerful tool in the field of material science. Their ability to achieve rapid sintering, purification and activation sintering, fine-grain sintering, wide-range temperature sintering, density control sintering, and temperature gradient sintering makes them versatile and efficient for a wide range of applications. As research and development in this field continue to advance, SPS furnaces are poised to play an increasingly important role in the production of high-performance materials.
Versatility in Material Processing with SPS
Spark Plasma Sintering (SPS) is a highly efficient and versatile technique used in the sintering of a wide range of materials, including metals, ceramics, nanomaterials, and composite materials. This method leverages direct current pulses to generate spark plasma between particles, facilitating rapid heating and densification processes. SPS is renowned for its ability to achieve high-quality material preparation with significant advantages over traditional sintering methods.
Wide Applicability of SPS
Nanomaterials
SPS technology is particularly effective in the preparation of nanomaterials. Traditional sintering methods often struggle to maintain the nanometer-scale grain size and achieve complete density. SPS, with its rapid heating and short synthesis times, effectively suppresses grain coarsening. This rapid process also allows for the retention of defects and substructures in the powder, which can be beneficial for the synthesis of metastable materials and nanomaterials.
Gradient Functional Materials
Functional Gradient Materials (FGMs) are composites with a gradient distribution in a certain direction, often requiring different sintering temperatures for each layer. Traditional methods like Chemical Vapor Deposition (CVD) and Physical Vapor Deposition (PVD) are costly and challenging for industrial production. SPS overcomes these challenges by enabling the sintering of materials with gradients in heat resistance, wear resistance, hardness, conductivity, and porosity, with the ability to handle multiple layers.
Electromagnetic Materials
SPS is also utilized in producing various electromagnetic materials, including thermoelectric conversion elements and materials used in the electronics field such as superconducting materials, magnetic materials, dielectric materials, and more. These materials are crucial for applications ranging from energy storage to biomedical engineering.
Intermetallic Compounds
Intermetallic compounds, known for their brittleness and high melting points, require specialized processes for preparation. SPS offers an efficient method for preparing these compounds by utilizing self-heating and surface activation between particles, enabling low-temperature and rapid sintering.
High-Density, Fine-Grained Ceramics and Cermets
The SPS process significantly shortens sintering times and reduces temperatures by leveraging the heat generated within each powder particle and the gaps between them. This makes SPS an excellent method for preparing high-density, fine-grained ceramics and cermets, which are essential for various industrial applications.
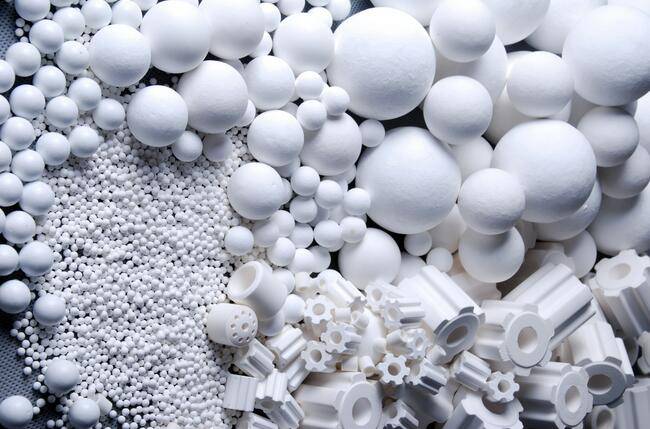
Advantages of SPS
- Shorter Cycle Times: SPS significantly reduces sintering cycles from hours or days to just minutes, enhancing productivity and rapid material development capabilities.
- Lower Sintering Temperatures: It allows for sintering at lower temperatures compared to conventional processes, which is particularly beneficial for heat-sensitive materials.
- High Precision Process Control: SPS provides fine control over sintering parameters such as temperature and pressure, ensuring optimal outcomes and enabling the creation of unique chemistries not feasible with conventional methods.
- Versatility: It can densify a wide range of materials, from low melting point metals to ultra-high temperature ceramics, and even bond dissimilar materials requiring non-uniform temperature distributions.
Applications of SPS
SPS technology finds applications in various fields, including:
- Energy Storage: High-capacity lithium-ion batteries and other advanced energy storage materials.
- Biomedical Engineering: Porous ceramics for drug delivery and scaffolds for tissue engineering.
- Advanced Ceramics: High-temperature superconductors and high-performance piezoelectric ceramics.
- Intermetallics: Advanced alloys with improved mechanical, thermal, and electrical properties.
- Composites: Reinforced ceramics and metals with enhanced mechanical properties.
In conclusion, Spark Plasma Sintering stands out as a highly versatile and efficient method for the sintering of diverse materials, offering significant advantages in terms of process control, energy efficiency, and the ability to produce high-quality materials for a wide array of applications.
Operational Ease and Safety Features of SPS Furnaces
Spark Plasma Sintering (SPS) furnaces are renowned for their advanced operational ease and robust safety features, making them a preferred choice in various industrial applications. These furnaces are designed with a focus on user-friendly interfaces and comprehensive safety mechanisms to ensure efficient and secure operations.
User-Friendly Design and Control Systems
The SPS furnaces are equipped with state-of-the-art control systems that enhance operational ease. A notable feature is the integration of touch screen interfaces and Programmable Logic Controllers (PLCs) for central control. This setup allows operators to easily monitor and adjust furnace parameters, reducing the complexity of operation and minimizing the potential for human error. The Allen-Bradley PLC system, for instance, is known for its ease of programming and modification, which further simplifies the management of furnace operations.
The control cabinet of these furnaces is designed to house all electrical controls in a standard NEMA 12 cabinet, ensuring compliance with safety standards such as NFPA 70. This centralized control not only enhances safety but also makes maintenance and troubleshooting more straightforward. The inclusion of an integrated main electrical switch interlock adds an extra layer of safety by preventing unauthorized or accidental operations.
Advanced Safety Mechanisms
Safety is a paramount concern in the operation of SPS furnaces, and these systems are equipped with multiple layers of protection. Key safety features include over-temperature and over-pressure malfunction alarms, which alert operators to potential hazards in real-time. Additionally, mechanical automatic pressure protection systems are in place to safeguard against pressure-related issues, ensuring the integrity of the furnace and the materials being processed.
The furnaces also feature interlocking functions that prevent operations under unsafe conditions. For example, interlocks are used to disable the furnace in cases of electricity or water shortages, insufficient pressure, or over-temperature conditions. These interlocks are crucial for preventing accidents and protecting both the equipment and the operators.
Remote control capabilities are another significant safety feature, allowing for remote malfunction diagnosis and program updates. This not only enhances the efficiency of maintenance but also reduces the risk of exposure to hazardous conditions for technicians.
Thermocouple Integration
Accurate temperature control is essential in sintering processes, and SPS furnaces utilize high-quality thermocouples, such as Type "S" and Type "K," for precise temperature monitoring and control. These thermocouples are integrated with appropriate jack panels for work monitoring and survey, ensuring that the sintering process remains within safe and optimal temperature ranges.
Conclusion
In summary, the operational ease and safety features of SPS furnaces are designed to provide a seamless and secure sintering experience. With user-friendly control systems, advanced safety mechanisms, and precise temperature control, these furnaces are ideal for a wide range of applications in the processing of metals, ceramics, nanomaterials, and more. The integration of modern technology and robust safety protocols ensures that operators can work efficiently while minimizing risks.
Advanced Control and Monitoring Systems in SPS
Advanced control and monitoring systems are integral to the Spark Plasma Sintering (SPS) process, enabling precise regulation of temperature, pressure, and current, along with comprehensive data acquisition to track and analyze sintering parameters. These systems are crucial for ensuring the quality and reproducibility of the sintered materials.
Automated Program Control
The SPS process begins with loading a known quantity of dried and milled powder sample into a cylindrical die lined with a graphite sheet, which facilitates easy removal of the sintered compact. The die is then placed inside the SPS chamber, and the specific time-temperature profile required for the experiment is set. The atmosphere inside the chamber is maintained as needed, whether vacuum, argon, or other controlled environments. The power is set to maximum in Auto mode, and the required load is applied to the die. The z-axis position is set to zero, and the timer is activated before pressing SINTER to commence the sintering process.
For temperature measurement, SPS utilizes two types of instruments: thermocouples for sintering temperatures below 1000°C and pyrometers for temperatures exceeding 1000°C. A high DC pulse is passed between graphite electrodes, and axial pressure is simultaneously applied from the beginning of the sintering cycle. The sample is heated by Joule heating and sparking among the particles, leading to faster heat and mass transfer instantaneously. After sintering, the power is turned off, and the sample is allowed to cool.
Computerized Control Systems
The control system in SPS is typically computerized, featuring an automatic PLC flat panel touch computer control system that allows manual switching to automatic modes. The control system software is developed in-house, offering a user-friendly interface with real-time monitoring of furnace conditions. The system is stable and reliable, with a fast response and strong anti-interference capabilities. The software displays a color simulation screen, integrating temperature display and vacuum valve control for intuitive operation.
The device can adopt various curves for analysis, such as temperature, power, vacuum, water temperature, air pressure, and sintering time curves. These curves provide a user-friendly way to analyze the sintering process based on historical data. The system can automatically generate Excel files through the USB interface for further analysis.
The temperature control method utilizes a thermocouple for temperatures up to 1700°C, with infrared instruments taking over for temperatures above 1700°C. The system supports various communication interfaces like RS232, RS422, CAN, LAN, and USB, facilitating easy networking with other equipment. The software control interface is visualized, dynamically displaying the workflow for convenience and intuitiveness. The software is also free to upgrade for life.
Controllers and Data Acquisition
Much like other testing chambers, SPS offers various choices for controllers, ranging from completely manual to fully automated systems. Automated controllers allow users to set the parameters of the process, and as the procedure unfolds, the system makes adjustments in pressure, temperature, and other programmed factors. These control systems are configurable with customizable software and a variety of data collection methods. The choice of controller is determined by the criticality of the application and the size of the vacuum chamber. Smaller chambers may only need a simple gauge for monitoring pumping and pressure, while larger chambers may demand a more aggressive and sophisticated system.
Sintering Machine Components
The SPS machine is assisted by several components, including a uniaxial press, punch electrodes, vacuum chamber, controlled atmosphere, DC pulse generator, and position, temperature, and pressure measuring units. The control of sintering temperature is achieved by setting parameters such as holding time, ramp rate, pulse duration, and pulse current and voltage. The DC pulse discharge generates spark plasma, spark impact pressure, Joule heating, and an electrical field diffusion effect. In SPS, sintering is assisted by the on-off DC pulse voltage, which is different from conventional hot pressing. The application of pressure helps the plastic flow of the material, and the flow of DC pulse current through the particles is illustrated in detailed diagrams.
In conclusion, advanced control and monitoring systems in SPS are essential for achieving precise and reproducible sintering outcomes. These systems enable real-time adjustments and comprehensive data acquisition, ensuring the quality and consistency of the sintered materials. With the integration of computerized control, customizable software, and advanced data collection methods, SPS technology continues to push the boundaries of material science and engineering.
Applications of Spark Plasma Sintering in Material Science
Spark Plasma Sintering (SPS) is a versatile and advanced sintering technique that has revolutionized the field of material science. By combining uniaxial pressure, pulsed direct current, and rapid heating, SPS enables the synthesis of a wide array of materials with unique properties and structures. This section delves into the multifaceted applications of SPS, including sintering, joining, forming, surface modification, and the synthesis of materials such as solid electrolytes and electric thermal materials.
Sintering of Advanced Materials
SPS is particularly renowned for its ability to sinter high-melting-point materials and nanomaterials efficiently. The rapid heating rates (up to 1000°C/min) and short processing times inherent to SPS help maintain the nanostructure of powders, preventing grain growth and preserving the inherent properties of nano-sized particles. This makes SPS an ideal method for producing high-density, fine-grained ceramics and cermets. For instance, titanium nitride, a material known for its poor sintering properties and brittleness, can be densified to high levels using SPS, achieving densities close to theoretical values under pressures of 1-5 GPa.
Joining and Forming
Beyond sintering, SPS is also employed for joining dissimilar materials and forming complex shapes. The direct current applied during the process not only heats the material but also enhances the diffusion bonding between particles, facilitating the joining of materials that are traditionally difficult to bond, such as ceramics to metals. This capability is particularly useful in the aerospace and automotive industries, where the demand for lightweight, high-strength composites is high.
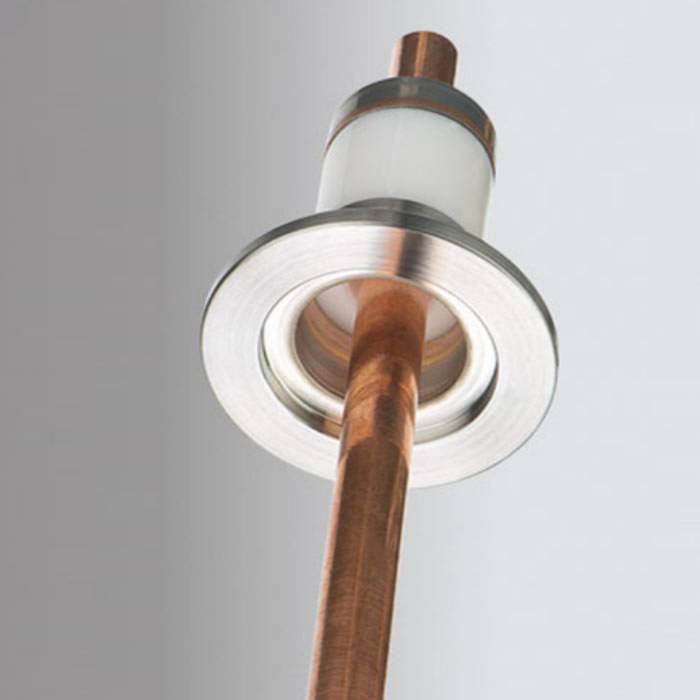
Surface Modification
SPS can also be utilized for surface modification, enhancing the surface properties of materials without affecting their bulk characteristics. By controlling the current density and pressure, specific surface layers can be tailored to achieve desired properties such as increased hardness, wear resistance, or corrosion resistance. This application is particularly beneficial for tooling materials and components exposed to harsh environments.
Synthesis of Functional Materials
One of the most significant applications of SPS is in the synthesis of functional materials, including solid electrolytes and electric thermal materials. Solid electrolytes, crucial for applications in solid-state batteries and fuel cells, require a high degree of densification and purity. SPS facilitates the synthesis of these materials with minimal grain boundary segregation and excellent ionic conductivity. Similarly, electric thermal materials, used in various heating applications, can be synthesized with controlled thermal conductivity and electrical resistivity through precise SPS processing parameters.
Industrial Significance and Future Prospects
The industrial significance of SPS lies in its ability to produce high-performance materials with reduced energy consumption and shorter processing times. The technology is particularly suited for the production of nanomaterials, bulk amorphous alloys, and gradient functional materials, which are challenging to synthesize using traditional methods. As research continues to uncover new applications and optimize processing parameters, SPS is poised to play a crucial role in the future of material science, driving advancements in various high-tech industries.
In conclusion, Spark Plasma Sintering stands out as a transformative technology in material science, offering a broad spectrum of applications from sintering and joining to surface modification and the synthesis of advanced functional materials. Its ability to process materials with high efficiency and precision makes it an indispensable tool for researchers and industrial practitioners alike.
Challenges and Considerations in Using SPS Technology
Spark Plasma Sintering (SPS) technology has revolutionized the field of material science by enabling the synthesis of advanced materials with unique properties. However, the implementation of SPS comes with its own set of challenges and considerations that must be addressed to achieve optimal sintering results. This section delves into the critical aspects of mold selection and maintenance, as well as the broader considerations for effective SPS operations.
Mold Selection and Maintenance
The choice of mold material is a pivotal factor in SPS technology. Traditionally, graphite has been the preferred material due to its high temperature resistance, excellent electrical and thermal conductivity, and chemical stability. However, graphite molds have limitations such as low mechanical strength, short lifespan, and potential contamination of the sintered materials. These issues necessitate the exploration of alternative mold materials.
Recent advancements have led to the development of alternative mold materials such as cemented carbide, conductive ceramics, and carbon fiber graphite. Each of these materials offers unique advantages but also presents challenges. For instance, cemented carbide molds provide higher strength but can be prone to deformation at high temperatures. Conductive ceramics offer a balance of properties but are often expensive. Carbon fiber graphite molds combine the benefits of graphite with enhanced mechanical properties but require careful handling to prevent damage.
Maintaining the integrity of the mold is crucial for consistent sintering outcomes. Regular inspection and replacement of worn-out molds are essential to prevent inconsistencies in the sintering process. Additionally, proper cleaning and conditioning of the molds between uses can extend their lifespan and maintain the quality of the sintered materials.
Achieving Optimal Sintering Results
To achieve optimal sintering results, several considerations must be taken into account. These include the selection of appropriate sintering parameters, the control of the sintering environment, and the understanding of the sintering mechanism.
Sintering Parameters
The sintering parameters, such as temperature, pressure, and dwell time, play a critical role in determining the final properties of the sintered material. The rapid heating and cooling rates achievable with SPS can lead to non-equilibrium microstructures, which can be advantageous for obtaining unique material properties. However, these rates must be carefully controlled to prevent excessive grain growth or other defects.
Sintering Environment
The sintering environment, including the atmosphere and temperature gradients, can significantly influence the sintering process. Controlling the atmosphere can prevent oxidation and other chemical reactions that may degrade the material. Temperature gradients within the mold can lead to non-uniform densification, which necessitates careful design and optimization of the sintering setup.
Understanding the Sintering Mechanism
The sintering mechanism in SPS involves the generation of a spark plasma between the particles, which facilitates rapid heating and densification. However, the exact mechanisms governing this process are still not fully understood and are the subject of ongoing research. Finite element simulations have emerged as a valuable tool for studying the sintering process, providing insights into the temperature and electric field distributions within the material.
Future Directions
The continuous improvement of SPS technology requires ongoing research and development. Key areas for future exploration include the development of new mold materials with enhanced properties, the optimization of sintering parameters through advanced simulation techniques, and a deeper understanding of the sintering mechanism.
In conclusion, while SPS technology offers significant advantages for the synthesis of advanced materials, it also presents several challenges and considerations that must be addressed to achieve optimal results. By carefully selecting and maintaining molds, controlling sintering parameters, and advancing our understanding of the sintering mechanism, we can continue to push the boundaries of what is possible with SPS technology.
Future Trends and Innovations in SPS Technology
Spark Plasma Sintering (SPS) technology, known for its rapid sintering capabilities, has been a focal point in the field of material science due to its ability to produce high-quality materials with unique properties. As research continues to evolve, several trends and innovations are emerging, promising to enhance the efficiency, broaden the applications, and improve the safety of SPS technology.
Industrialization and Mass Production
One of the most significant trends in SPS technology is its transition towards industrialization. Compared to traditional sintering methods, SPS offers substantial advantages in terms of energy and time savings, increased production efficiency, and superior control over product performance. Countries like Japan have already achieved industrial applications of SPS, primarily in the production of magnetic materials, hard alloys, and gradient functional materials. For instance, Ohta Seiki in Japan has successfully implemented mass production of 100% WC superhard materials using SPS, supplying to over 40 manufacturers globally. In contrast, SPS technology in other regions, such as China, remains largely in the laboratory research phase, focusing on the preparation and process research of new materials.
Diversification of Sintered Shapes
Currently, SPS is limited to producing simple cylindrical samples due to the constraints of the sintering mechanism and graphite molds. However, there is a growing trend towards developing SPS technology to create more complex shapes and structures. This advancement would significantly expand the applicability of SPS in various engineering sectors, allowing for the production of intricate components that are currently unattainable.
Material Synthesis and Connection
SPS technology is not only used for sintering bulk materials but also for the synthesis of powders, particularly those that are challenging to obtain through conventional methods. For example, SPS has been utilized to synthesize ultra-high temperature ZrC material powder, achieving high purity and a fine grain size of approximately 100 nm. Additionally, SPS is being explored for material connection (welding), including ceramic-ceramic and ceramic-metal joints. The ability to connect materials without an intermediate layer, through self-diffusion enhanced by the SPS electric field, opens new possibilities for creating robust and durable composite structures.
Performance Optimization of Sintering Molds
Graphite, while commonly used in SPS due to its high-temperature resistance and excellent electrical and thermal conductivity, has limitations such as low strength and potential contamination of sintered materials. There is a trend towards developing new mold materials that offer higher strength, reusability, and reduced contamination. Materials like cemented carbide molds, conductive ceramic molds, and carbon fiber graphite molds are being researched, although challenges such as deformation at high temperatures and high costs persist.
Advancements in Simulation and Modeling
Understanding the complex sintering process in SPS is crucial for optimizing its parameters and predicting outcomes. Finite element simulation has emerged as a valuable tool in this regard, allowing researchers to analyze the temperature and electric field distributions during sintering. Software like ABAQUS, MATLAB, and MSC.MARC are being used to simulate the sintering process, providing insights into the impact of various parameters and aiding in the theoretical guidance of production.
Enhanced Safety Features
As SPS technology continues to evolve, there is an increasing focus on enhancing its safety features. This includes developing safer operating protocols, improving the reliability of SPS equipment, and ensuring that the technology can be used in a wider range of environments without compromising safety.
In conclusion, the future of SPS technology looks promising with ongoing research and development aimed at improving efficiency, broadening material applications, and enhancing safety features. These advancements are set to revolutionize the field of material science, enabling the production of high-performance materials and components that were previously unattainable. As SPS technology continues to mature, it will undoubtedly play a pivotal role in shaping the future of manufacturing and material innovation.
CONTACT US FOR A FREE CONSULTATION
KINTEK LAB SOLUTION's products and services have been recognized by customers around the world. Our staff will be happy to assist with any inquiry you might have. Contact us for a free consultation and talk to a product specialist to find the most suitable solution for your application needs!