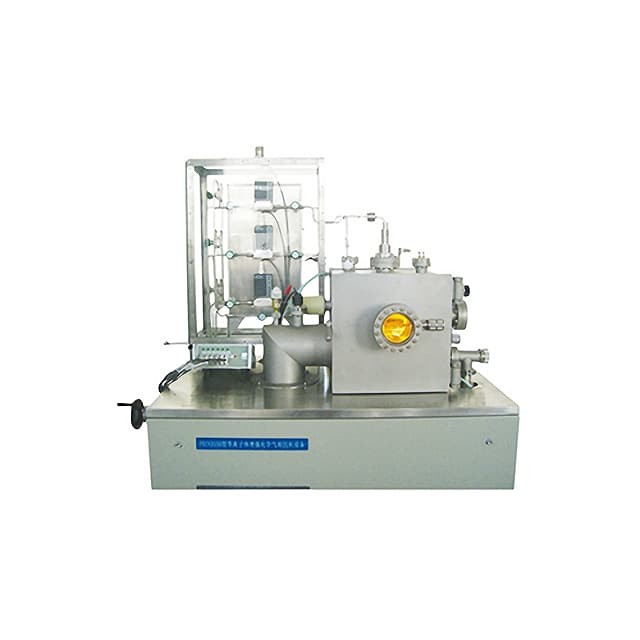
CVD & PECVD Furnace
Inclined Rotary Plasma Enhanced Chemical Vapor Deposition PECVD Equipment Tube Furnace Machine
Item Number : KT-PED
Price varies based on specs and customizations
- Sample holder heating temperature
- ≤800℃
- Gas purge channels
- 4 channels
- Vacuum chamber chamber size
- Φ500mm × 550 mm
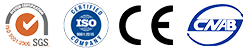
Shipping:
Contact us to get shipping details Enjoy On-time Dispatch Guarantee.
Why Choose Us
Reliable PartnerEasy ordering process, quality products, and dedicated support for your business success.
Introduction
Plasma Enhanced Chemical Vapor Deposition (PECVD) is a vacuum thin film deposition process that uses vapors or gases as precursors to create a coating. PECVD is a variation of chemical vapor deposition (CVD) that uses plasma instead of heat to activate the source gas or vapor. Since high temperatures can be avoided, the range of possible substrates expands to low melting point materials – even plastics in some cases. Moreover, the range of coating materials that can be deposited also grows. PECVD is used to deposit a wide variety of materials, including dielectrics, semiconductors, metals, and insulators. PECVD coatings are used in a wide variety of applications, including solar cells, flat panel displays, and microelectronics.
Applications
Plasma Enhanced Chemical Vapor Deposition (PECVD) coating machines offer a versatile solution for various industries and applications:
- LED Lighting:** Deposition of high-quality dielectric and semiconductor films for light-emitting diodes (LEDs).
- Power Semiconductors:** Formation of insulating layers, gate oxides, and other critical components in power semiconductor devices.
- MEMS:** Fabrication of thin films for microelectromechanical systems (MEMS), such as sensors and actuators.
- Optical Coatings:** Deposition of anti-reflection coatings, optical filters, and other optical components.
- Thin Film Solar Cells:** Production of amorphous and microcrystalline silicon thin films for solar cell devices.
- Surface Modification:** Enhancement of surface properties, such as corrosion resistance, wear resistance, and biocompatibility.
- Nanotechnology:** Synthesis of nanomaterials, including nanoparticles, nanowires, and thin films.
Features
The Plasma Enhanced Chemical Vapor Deposition (PECVD) Coating Machine offers numerous advantages that enhance productivity and deliver exceptional results:
- Low-temperature deposition: Enables the formation of high-quality films at temperatures significantly lower than traditional CVD methods, making it suitable for delicate substrates.
- High deposition rates: Maximizes efficiency by depositing films rapidly, reducing production time and increasing output.
- Uniform and crack-resistant films: Ensures consistent film properties and minimizes the risk of cracking, leading to reliable and durable coatings.
- Excellent adhesion to substrates: Provides strong bonding between the film and the substrate, ensuring long-lasting performance and preventing delamination.
- Versatile coating capabilities: Allows for the deposition of a wide range of materials, including SiO2, SiNx, and SiOxNy, to meet diverse application requirements.
- Customization for complex geometries: Accommodates substrates with intricate shapes, ensuring uniform coating and optimal performance.
- Low maintenance and easy installation: Minimizes downtime and simplifies setup, enhancing productivity and cost-effectiveness.
Technical specifications
Sample holder | Size | 1-6 inches |
Rotate speed | 0-20rpm adjustable | |
Heating temperature | ≤800℃ | |
Control accuracy | ±0.5℃ SHIMADEN PID Controller | |
Gas purge | Flow meter | MASS FLOWMETER CONTROLLER (MFC) |
Channels | 4 channels | |
Cooling method | Circulating water cooling | |
Vacuum chamber | Chamber size | Φ500mm X 550mm |
Observation port | Full view port with baffle | |
Chamber material | 316 Stainless steel | |
Door type | Front open type door | |
Cap material | 304 Stainless steel | |
Vacuum pump port | CF200 flange | |
Gas inlet port | φ6 VCR connector | |
Plasma power | Source power | DC power or RF power |
Coupling mode | Inductively coupled or plate capacitive | |
Output power | 500W—1000W | |
Bias power | 500v | |
Vacuum pump | Pre- pump | 15L/S Vane vacuum pump |
Turbo pump port | CF150/CF200 620L/S-1600L/S | |
Relief port | KF25 | |
Pump speed | Vane pump:15L/s,Turbo pump:1200l/s或1600l/s | |
Vacuum degree | ≤5×10-5Pa | |
Vacuum sensor | Ionization/resistance vacuum gauge/film gauge | |
System | Electric power supply | AC 220V /380 50Hz |
Rated power | 5kW | |
Dimensions | 900mm X 820mm X870mm | |
Weight | 200kg |
Principle
Plasma Enhanced Chemical Vapor Deposition (PECVD) utilizes plasma to stimulate chemical reactions during deposition, enabling high-quality solid films to be formed at low temperatures. By employing high-energy plasma, PECVD machines enhance reaction rates and lower reaction temperatures. This technique is widely used in LED lighting, power semiconductors, and MEMS. It allows for the deposition of SiO2, SiNx, SiOxNy, and other media films, as well as high-speed deposition of SiO thick films on composite substrates. PECVD offers excellent film-forming quality, minimizes pinholes, and reduces cracking, making it suitable for producing amorphous and microcrystalline silicon thin film solar cell devices.
Advantage
- Ability to deposit various materials: PECVD can deposit a wide range of materials, including diamond-like carbon, silicon compounds, and metal oxides, allowing for the creation of films with tailored properties.
- Low-temperature operation: PECVD operates at low temperatures (typically 300-450°C), making it suitable for heat-sensitive substrates.
- High-quality thin films: PECVD produces thin films with exceptional uniformity, thickness control, and resistance to cracking.
- Excellent adhesion: The films deposited by PECVD exhibit strong adhesion to the substrate, ensuring durability and reliability.
- Conformal coating: PECVD enables the coating of complex geometries, providing uniform coverage and protection.
- High deposition rates: PECVD offers fast deposition rates, increasing productivity and reducing production time.
- Low maintenance: PECVD systems are designed for low maintenance, minimizing downtime and maximizing uptime.
- Easy installation: PECVD equipment is relatively easy to install and integrate into existing production lines.
- Rigid design: PECVD systems are built with robust designs, ensuring stability and long-lasting performance.
- Extended working life: PECVD systems are designed for longevity, providing a cost-effective solution for long-term thin film deposition needs.
Warnings
Operator safety is the top important issue! Please operate the equipment with cautions. Working with inflammable& explosive or toxic gases is very dangerous, operators must take all necessary precautions before starting the equipment. Working with positive pressure inside the reactors or chambers is dangerous, operator must fellow the safety procedures strictly. Extra caution must also be taken when operating with air-reactive materials, especially under vacuum. A leak can draw air into the apparatus and cause a violent reaction to occur.
Designed for You
KinTek provide deep custom made service and equipment to worldwide customers, our specialized teamwork and rich experienced engineers are capable to undertake the custom tailoring hardware and software equipment requirements, and help our customer to build up the exclusive and personalized equipment and solution!
Would you please drop your ideas to us, our engineers are ready for you now!
FAQ
What Is PECVD Method?
What Is Mpcvd?
What Is PECVD Used For?
What Is Mpcvd Machine?
What Are The Advantages Of PECVD?
What Are The Advantages Of Mpcvd?
What Is The Difference Between ALD And PECVD?
Are CVD Diamonds Real Or Fake?
What Is The Difference Between PECVD And Sputtering?
4.9
out of
5
I'm impressed by how quickly my PECVD coating machine arrived. It was delivered within a week of ordering, which was much faster than I expected.
4.7
out of
5
The PECVD coating machine is an excellent value for the price. It's well-made and produces high-quality coatings.
4.8
out of
5
I've been using the PECVD coating machine for a few months now, and I'm very happy with its performance. The coatings are durable and have improved the performance of my products.
4.9
out of
5
The PECVD coating machine is a game-changer for my business. It's helped me to increase my production capacity and improve the quality of my products.
4.7
out of
5
I'm very impressed with the technological advancements of the PECVD coating machine. It's a cutting-edge piece of equipment that has helped me to stay ahead of the competition.
4.8
out of
5
The PECVD coating machine is easy to use and maintain. I've had no problems with it since I purchased it.
4.9
out of
5
I highly recommend the PECVD coating machine to anyone who needs a high-quality, durable coating for their products.
4.7
out of
5
The PECVD coating machine is a great investment for any business. It's helped me to save money and improve the quality of my products.
4.8
out of
5
I'm very satisfied with the PECVD coating machine. It's a reliable and efficient piece of equipment that has helped me to improve my production process.
4.9
out of
5
The PECVD coating machine is a must-have for any business that wants to improve the quality of its products. It's a versatile and easy-to-use machine that can be used for a variety of applications.
4.7
out of
5
I'm very happy with the PECVD coating machine. It's a well-made and durable machine that has helped me to improve the performance of my products.
4.8
out of
5
The PECVD coating machine is a great value for the price. It's a high-quality machine that has helped me to improve the efficiency of my production process.
4.9
out of
5
I'm very impressed with the PECVD coating machine. It's a versatile and easy-to-use machine that has helped me to improve the quality of my products.
4.7
out of
5
The PECVD coating machine is a great investment for any business. It's a reliable and efficient machine that has helped me to save money and improve the quality of my products.
4.8
out of
5
I'm very happy with the PECVD coating machine. It's a well-made and durable machine that has helped me to improve the performance of my products.
4.9
out of
5
The PECVD coating machine is a must-have for any business that wants to improve the quality of its products. It's a versatile and easy-to-use machine that can be used for a variety of applications.
4.7
out of
5
I'm very happy with the PECVD coating machine. It's a well-made and durable machine that has helped me to improve the performance of my products.
4.8
out of
5
The PECVD coating machine is a great investment for any business. It's a reliable and efficient machine that has helped me to save money and improve the quality of my products.
4.9
out of
5
I'm very impressed with the PECVD coating machine. It's a versatile and easy-to-use machine that has helped me to improve the quality of my products.
Products
Inclined Rotary Plasma Enhanced Chemical Vapor Deposition PECVD Equipment Tube Furnace Machine
REQUEST A QUOTE
Our professional team will reply to you within one business day. Please feel free to contact us!
Related Products
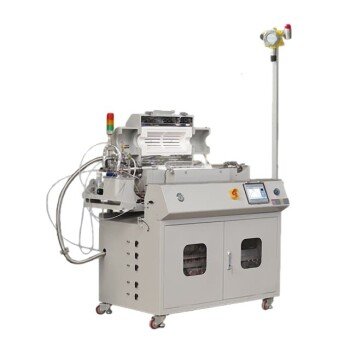
Customer Made Versatile CVD Tube Furnace Chemical Vapor Deposition Chamber System Equipment
Get your exclusive CVD furnace with KT-CTF16 Customer Made Versatile Furnace. Customizable sliding, rotating, and tilting functions for precise reactions. Order now!
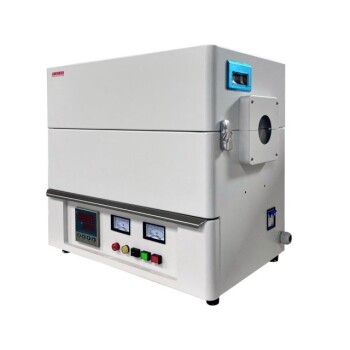
1200℃ Split Tube Furnace with Quartz Tube Laboratory Tubular Furnace
KT-TF12 split tube furnace: high-purity insulation, embedded heating wire coils, and max. 1200C. Widely used for new materials and chemical vapour deposition.
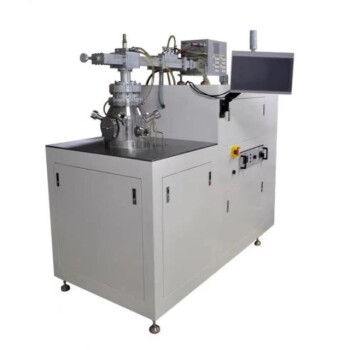
Learn about Cylindrical Resonator MPCVD Machine, the microwave plasma chemical vapor deposition method used for growing diamond gemstones and films in the jewelry and semi-conductor industries. Discover its cost-effective advantages over traditional HPHT methods.
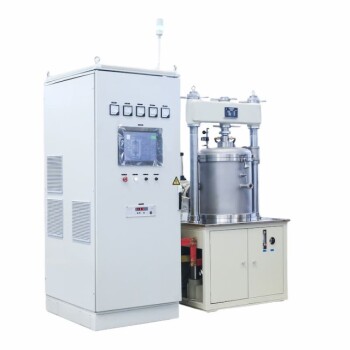
Vacuum Hot Press Furnace Machine Heated Vacuum Press
Discover the advantages of Vacuum Hot Press Furnace! Manufacture dense refractory metals & compounds, ceramics, and composites under high temp and pressure.
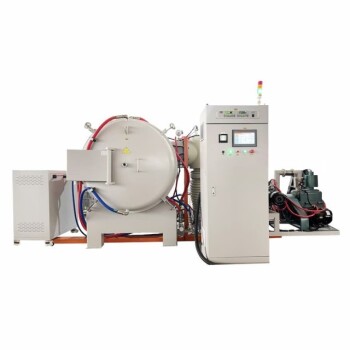
Molybdenum Vacuum Heat Treat Furnace
Discover the benefits of a high-configuration molybdenum vacuum furnace with heat shield insulation. Ideal for high-purity, vacuum environments like sapphire crystal growth and heat treatment.
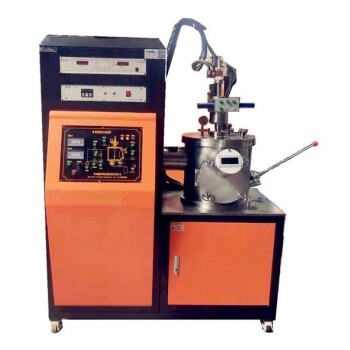
Non Consumable Vacuum Arc Induction Melting Furnace
Explore the benefits of Non-Consumable Vacuum Arc Furnace with high melting point electrodes. Small, easy to operate & eco-friendly. Ideal for laboratory research on refractory metals & carbides.
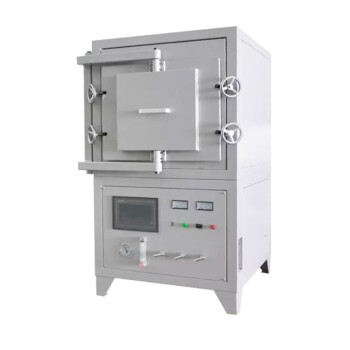
1200℃ Controlled Atmosphere Furnace Nitrogen Inert Atmosphere Furnace
Discover our KT-12A Pro Controlled atmosphere furnace - high precision, heavy duty vacuum chamber, versatile smart touch screen controller, and excellent temperature uniformity up to 1200C. Ideal for both laboratory and industrial application.
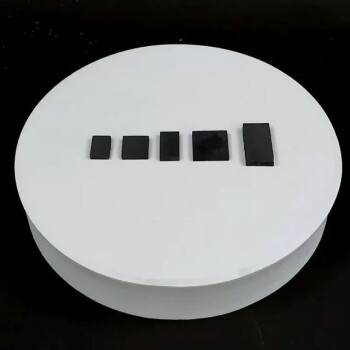
Glassy Carbon Sheet RVC for Electrochemical Experiments
Discover our Glassy Carbon Sheet - RVC. Perfect for your experiments, this high-quality material will elevate your research to the next level.
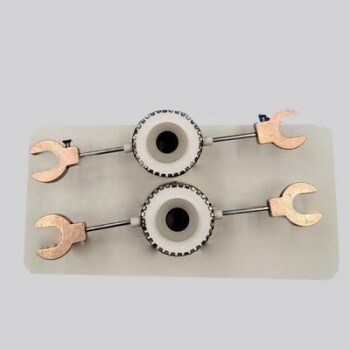
Aluminized Ceramic Evaporation Boat for Thin Film Deposition
Vessel for depositing thin films; has an aluminum-coated ceramic body for improved thermal efficiency and chemical resistance. making it suitable for various applications.
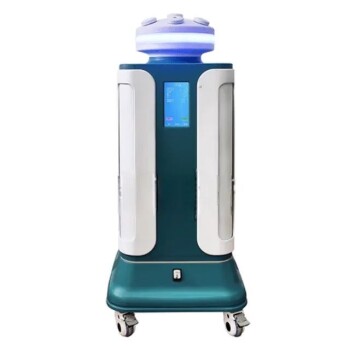
VHP Sterilization Equipment Hydrogen Peroxide H2O2 Space Sterilizer
A hydrogen peroxide space sterilizer is a device that uses vaporized hydrogen peroxide to decontaminate enclosed spaces. It kills microorganisms by damaging their cellular components and genetic material.
Related Articles
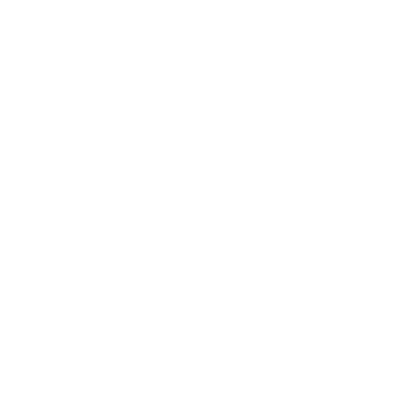
Plasma Enhanced Chemical Vapor Deposition (PECVD): A Comprehensive Guide
Learn everything you need to know about Plasma Enhanced Chemical Vapor Deposition (PECVD), a thin film deposition technique used in the semiconductor industry. Explore its principles, applications, and benefits.
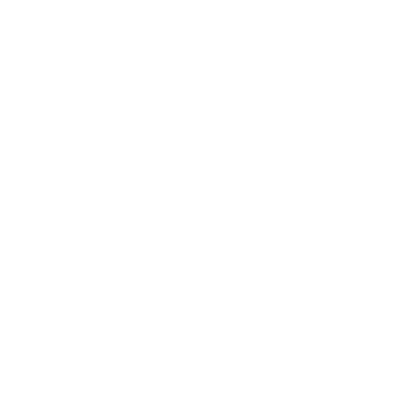
Understanding PECVD: A Guide to Plasma-Enhanced Chemical Vapor Deposition
PECVD is a useful technique for creating thin film coatings because it allows for the deposition of a wide variety of materials, including oxides, nitrides, and carbides.
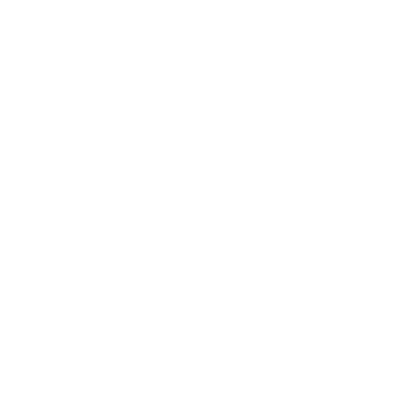
The Role of Plasma in PECVD Coatings
PECVD (Plasma Enhanced Chemical Vapor Deposition) is a type of thin film deposition process that is widely used for creating coatings on various substrates. In this process, a plasma is used to deposit thin films of various materials onto a substrate.
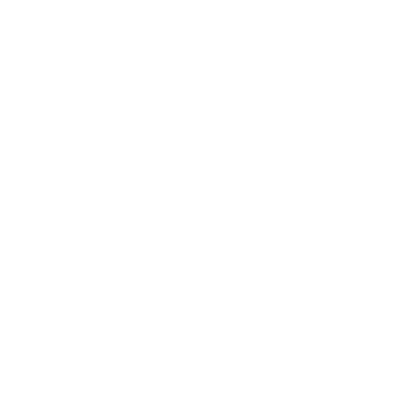
An Introduction to Chemical Vapor Deposition (CVD)
Chemical vapor deposition, or CVD, is a coating process that involves the use of gaseous reactants to produce thin films and coatings of high quality.
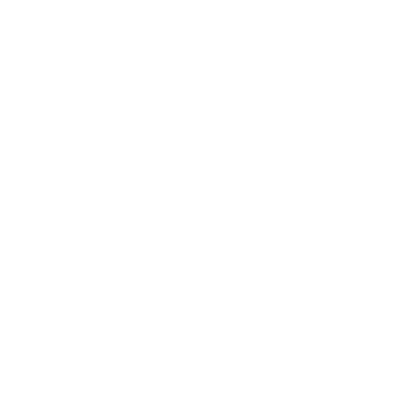
Advantages and Disadvantages of Chemical Vapor Deposition (CVD)
Chemical vapor deposition (CVD) is a versatile thin-film deposition technique widely used in various industries. Explore its advantages, disadvantages, and potential new applications.
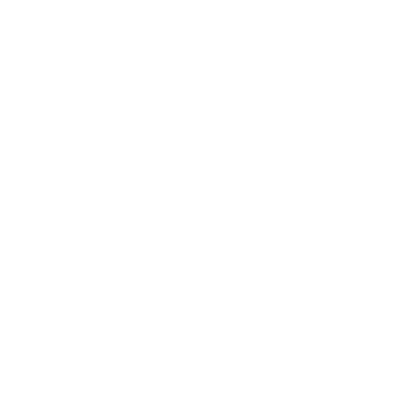
Comparing the Performance of PECVD and HPCVD in Coating Applications
Although both PECVD & HFCVD are used for coating applications, they differ in terms of deposition methods, performance, and suitability for specific applications.
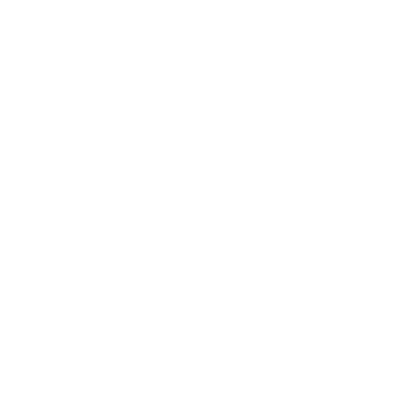
CVD Machines for Thin Film Deposition
Chemical Vapor Deposition (CVD) is a widely used technique for deposition of thin films on various substrates.
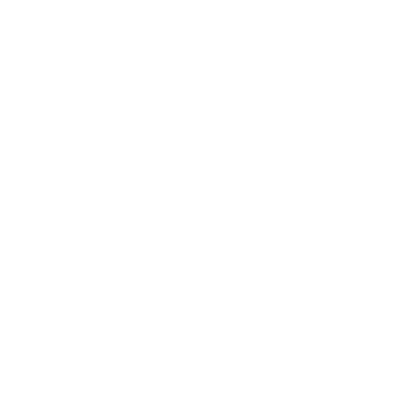
Why PECVD is Essential for Microelectronic Device Fabrication
PECVD (Plasma-Enhanced Chemical Vapor Deposition) is a popular thin film deposition technique used in microelectronics device fabrication.
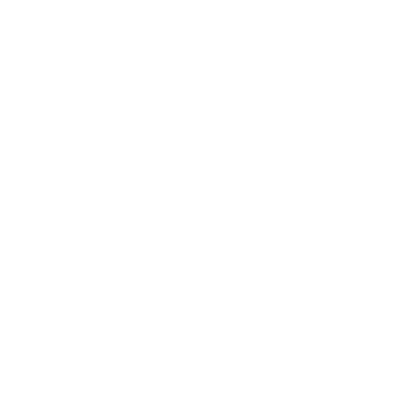
A Step-by-Step Guide to the PECVD Process
PECVD is a type of chemical vapor deposition process that uses plasma to enhance the chemical reactions between the gas-phase precursors and the substrate.
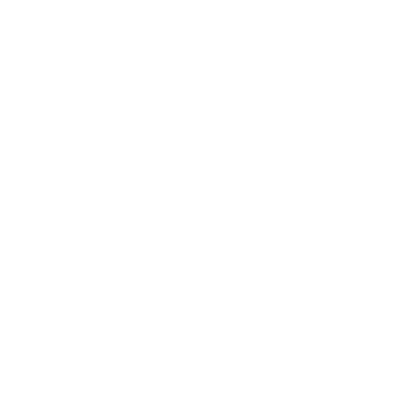
A Comprehensive Guide to PECVD Equipment Maintenance
Proper maintenance of PECVD equipment is crucial to ensure its optimal performance, longevity, and safety.
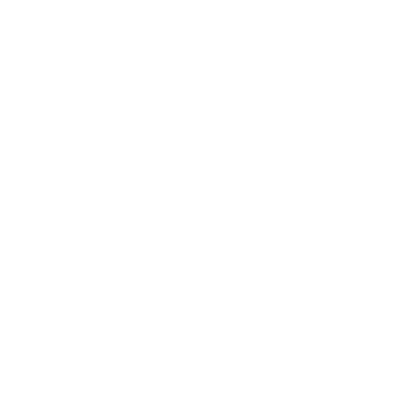
Comparing Chemical Vapor Deposition and Physical Vapor Deposition
Chemical Vapor Deposition (CVD) VS Physical Vapor Deposition (PVD)
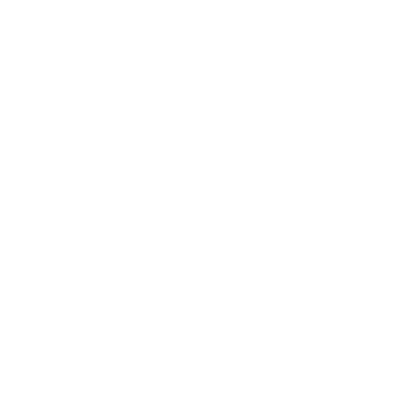
The Process of Fabricating a CVD Diamond By MPCVD Machine
CVD diamond machines have gained significant importance in various industries and scientific research.