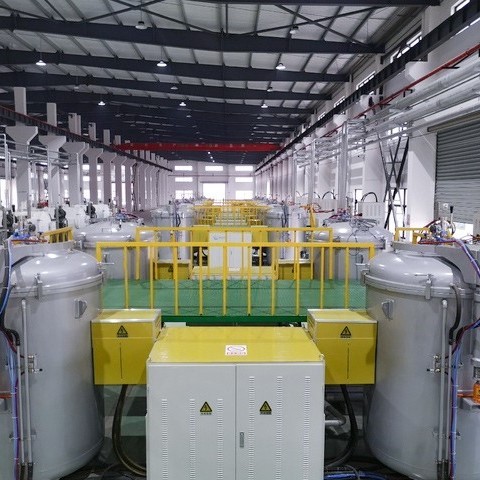
Graphitization furnace
Vertical High Temperature Graphite Vacuum Graphitization Furnace
Item Number : GF-05
Price varies based on specs and customizations
- Volume (L)
- 125 / 196 / 282 / 550 / 1000 / 1500
- Effective heating area (mm)
- Φ400×1000 / Φ500×1000 / Φ600×1000 / Φ700×1400 / Φ900×1600 / Φ1000×2000
- Power (KW)
- 150 / 200 / 300 / 500 / 600 / 800
- Frequency (HZ)
- 1500 / 1000
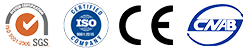
Shipping:
Contact us to get shipping details Enjoy On-time Dispatch Guarantee.
Why Choose Us
Reliable PartnerEasy ordering process, quality products, and dedicated support for your business success.
Introduction
The vertical high temperature graphitization furnace is a high-temperature furnace used for graphitization experiments and the production of various carbon materials. It is characterized by its rapid temperature rise, high efficiency, and uniform temperature distribution. The furnace uses double-layer alumina brick insulation to prevent short circuits and ensure heat insulation, fire resistance, and stability. It features a digital flow monitoring system and a comprehensive PLC water, electricity, and gas automatic control and protection system.
Applications
Vertical high temperature graphitization furnaces are widely used in various industries, including:
- Ceramic firing
- Carbide growth
- Carbonization
- Graphitization
- Sintering
- Annealing
- Brazing
- Degassing
Features
The Vertical High Temperature Graphitization Furnace is a top-of-the-line piece of laboratory equipment that offers a number of benefits to users. These benefits include:
- High temperature uniformity: The furnace's unique design ensures that the temperature is evenly distributed throughout the furnace chamber, which is essential for achieving consistent results.
- Low energy consumption: The furnace's double-layer alumina brick insulation material helps to minimize heat loss, which reduces energy consumption and operating costs.
- Good stability: The furnace's high-performance medium frequency contactor and comprehensive PLC water, electricity, gas automatic control and protection system ensure that the furnace operates stably and reliably.
- Digital flow monitoring system: The furnace's digital flow monitoring system provides real-time monitoring of the water flow in the power cabinet, which helps to prevent overheating and damage to the furnace.
- Multiple furnaces can be powered on to heat up and power off to cool down respectively to achieve continuous operation: This feature allows users to run multiple furnaces simultaneously, which can increase productivity and throughput.
Principle
The vertical high temperature graphitization furnace is a high-temperature vacuum furnace that uses graphite as the heating element. The furnace consists of a cylindrical graphite chamber with a water-cooled jacket. The chamber is heated by passing an electric current through the graphite walls. The temperature of the furnace is controlled by adjusting the current flow.
The vertical high temperature graphitization furnace is used for a variety of applications, including:
- Graphitization of carbon materials
- Sintering of metal powders
- Heat treatment of metals and ceramics
- Annealing of metals
- Crystal growth
Advantages
- Rapid heating and cooling: Graphite's excellent thermo-mechanical properties allow for quick temperature changes, reducing process cycles.
- High-temperature uniformity: Unique furnace design ensures consistent temperature distribution throughout the furnace chamber.
- Low energy consumption: Double-layer alumina brick insulation minimizes heat loss and enhances energy efficiency.
- Multiple furnace operation: Single power supply can accommodate multiple furnaces, enabling continuous operation.
- Comprehensive monitoring and control: PLC-based system provides real-time monitoring and automatic control of water, electricity, and gas.
- Economical: High-temperature graphite furnaces offer a cost-effective solution for high-temperature applications.
- Easy maintenance: Field replacement of the graphite hot zone is simple and quick, minimizing downtime.
Technical parameters and specifications
Furnace body temperature uniformity: Using medium frequency induction heating, the temperature rises quickly and the efficiency is high. The unique furnace design greatly improves the furnace body temperature uniformity;
Low energy consumption and good stability: Double-layer alumina brick insulation material is used to prevent short circuit between carbon felt and coil, good heat insulation and fire resistance, small heat loss, and good equipment stability;
According to the needs of the sintering process time, a single power supply can be configured with multiple electric furnaces, and the multiple furnaces can be powered on to heat up and power off to cool down respectively to achieve continuous operation;
Digital flow monitoring system, each channel of water flow monitoring and protection in the power cabinet, furnace conversion using high-performance medium frequency contactor; comprehensive PLC water, electricity, gas automatic control and protection system.
Product model specifications | GF-05-Ф40×100 | GF-05-Ф50×100 | GF-05-Ф60×100 | GF-05-Ф70×140 | GF-05-Ф90×160 | GF-05-Ф100×200 |
---|---|---|---|---|---|---|
Volume(L) | 125 | 196 | 282 | 550 | 1000 | 1500 |
Rated temperature(C) | 2800 | 2800 | 2800 | 2800 | 2800 | 2600 |
Limit temperature(C) | 3100 | 3100 | 3100 | 3100 | 300 | 2800 |
Effective heating area (mm) | Ф400×1000 | Ф500×1000 | Ф600×1000 | Ф700×1400 | Ф900×1600 | Ф1000×2000 |
Power(KW) | 150 | 200 | 300 | 500 | 600 | 800 |
Frequency(HZ) | 1500 | 1000 | 1000 | 1000 | 1000 | 1000 |
Temperature control method | Japan Shima Electric Thermostat | |||||
heating method | Induction heating | |||||
Vacuum system | Rotary vane vacuum pump (for high vacuum requirements, Roots vacuum pump and oil diffusion pump are required) | |||||
sintering atmosphere | N² Ar and other gases | |||||
Rated power supply voltage (V) | 380 | |||||
Rated heating voltage (V) | 750 | |||||
Vacuum limit (Pa) | 100 (vacuum cold state) |
FAQ
What Is A Graphitization Furnace?
What Is A Graphite Vacuum Furnace Used For?
What Is A Vacuum Furnace Used For?
What Are The Differences Between The Vertical High Temperature Graphitization Furnace And The High-temperature Graphite (HTG) Furnace?
What Is The Purpose Of The Vertical High Temperature Graphitization Furnace?
What Are The Main Applications Of Graphitization Furnaces?
What Are The Main Types Of Graphite Vacuum Furnaces?
What Is The Process Of A Vacuum Furnace?
What Are The Different Types Of Graphitization Furnaces?
How Does A Graphite Vacuum Furnace Work?
What Gas Is Used In A Vacuum Furnace?
How Does A Graphitization Furnace Work?
What Are The Advantages Of Using A Graphite Vacuum Furnace?
What Is The Heating Element Used In A Vacuum Furnace?
What Are The Advantages Of Using A Graphitization Furnace?
What Temperature Range Can A Graphite Vacuum Furnace Achieve?
What Industries Benefit From Graphite Vacuum Furnaces?
4.8
out of
5
This furnace has been a great addition to our lab. It's easy to use and maintain, and the temperature uniformity is excellent.
4.9
out of
5
We've been using this furnace for several months now and have been very impressed with its performance. It's very efficient and has helped us to reduce our energy consumption.
4.7
out of
5
The technical support from KINTEK SOLUTION has been outstanding. They've been very responsive to our questions and have helped us to get the most out of this furnace.
4.8
out of
5
This furnace is a great value for the price. It's well-made and has a lot of features that are typically found on more expensive models.
4.9
out of
5
We've used other furnaces in the past, but this one is by far the best. It's very durable and has held up well to heavy use.
4.7
out of
5
This furnace is very easy to use. The controls are intuitive and the display is clear and easy to read.
4.8
out of
5
The temperature uniformity of this furnace is excellent. We've been able to achieve very consistent results with it.
4.9
out of
5
This furnace is very efficient. We've been able to reduce our energy consumption by over 20% since we started using it.
4.7
out of
5
The technical support from KINTEK SOLUTION has been excellent. They've been very responsive to our questions and have helped us to get the most out of this furnace.
4.8
out of
5
This furnace is a great value for the price. It's well-made and has a lot of features that are typically found on more expensive models.
4.9
out of
5
We've used other furnaces in the past, but this one is by far the best. It's very durable and has held up well to heavy use.
4.7
out of
5
This furnace is very easy to use. The controls are intuitive and the display is clear and easy to read.
4.8
out of
5
The temperature uniformity of this furnace is excellent. We've been able to achieve very consistent results with it.
4.9
out of
5
This furnace is very efficient. We've been able to reduce our energy consumption by over 20% since we started using it.
4.7
out of
5
The technical support from KINTEK SOLUTION has been excellent. They've been very responsive to our questions and have helped us to get the most out of this furnace.
4.8
out of
5
This furnace is a great value for the price. It's well-made and has a lot of features that are typically found on more expensive models.
4.9
out of
5
We've used other furnaces in the past, but this one is by far the best. It's very durable and has held up well to heavy use.
Products
Vertical High Temperature Graphite Vacuum Graphitization Furnace
REQUEST A QUOTE
Our professional team will reply to you within one business day. Please feel free to contact us!
Related Products
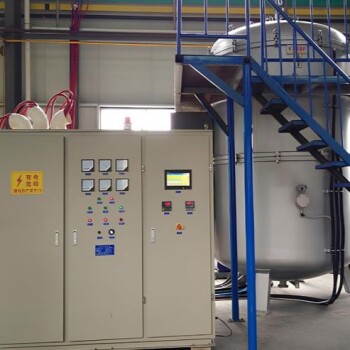
Large Vertical Graphite Vacuum Graphitization Furnace
A large vertical high-temperature graphitization furnace is a type of industrial furnace used for the graphitization of carbon materials, such as carbon fiber and carbon black. It is a high-temperature furnace that can reach temperatures of up to 3100°C.
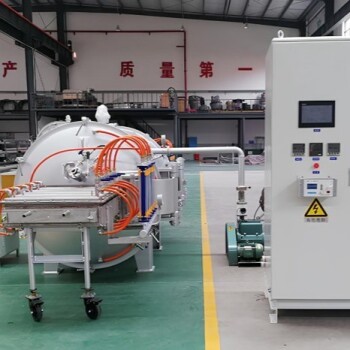
Graphite Vacuum Continuous Graphitization Furnace
High-temperature graphitization furnace is a professional equipment for graphitization treatment of carbon materials. It is a key equipment for the production of high-quality graphite products. It has high temperature, high efficiency and uniform heating. It is suitable for various high-temperature treatments and graphitization treatments. It is widely used in metallurgy, electronics, aerospace, etc. industry.
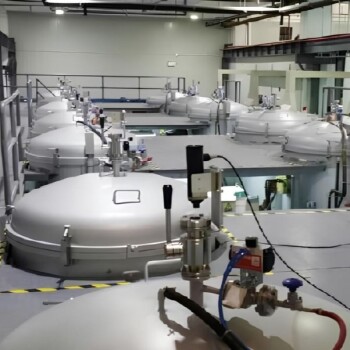
Graphite Vacuum Furnace High Thermal Conductivity Film Graphitization Furnace
The high thermal conductivity film graphitization furnace has uniform temperature, low energy consumption and can operate continuously.
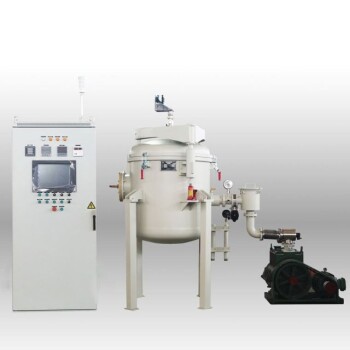
Ultra-High Temperature Graphite Vacuum Graphitization Furnace
The ultra-high temperature graphitization furnace utilizes medium frequency induction heating in a vacuum or inert gas environment. The induction coil generates an alternating magnetic field, inducing eddy currents in the graphite crucible, which heats up and radiates heat to the workpiece, bringing it to the desired temperature. This furnace is primarily used for graphitization and sintering of carbon materials, carbon fiber materials, and other composite materials.

Graphite Vacuum Furnace Bottom Discharge Graphitization Furnace for Carbon Materials
Bottom-out graphitization furnace for carbon materials, ultra-high temperature furnace up to 3100°C, suitable for graphitization and sintering of carbon rods and carbon blocks. Vertical design, bottom discharging, convenient feeding and discharging, high temperature uniformity, low energy consumption, good stability, hydraulic lifting system, convenient loading and unloading.
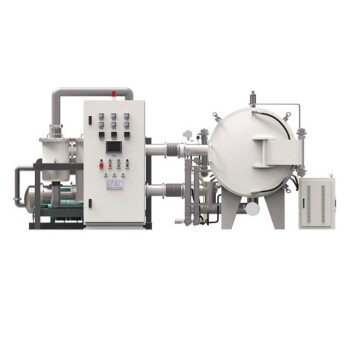
Horizontal High Temperature Graphite Vacuum Graphitization Furnace
Horizontal Graphitization Furnace: This type of furnace is designed with the heating elements placed horizontally, allowing for uniform heating of the sample. It's well-suited for graphitizing large or bulky samples that require precise temperature control and uniformity.
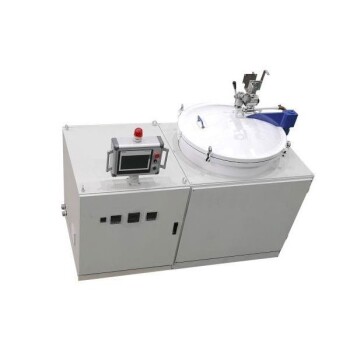
Graphite Vacuum Furnace IGBT Experimental Graphitization Furnace
IGBT experimental graphitization furnace, a tailored solution for universities and research institutions, with high heating efficiency, user-friendliness, and precise temperature control.
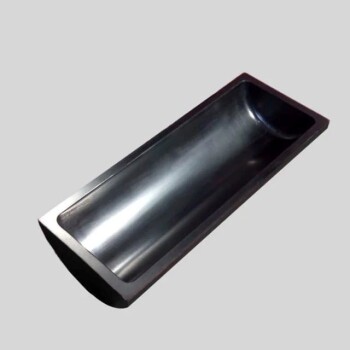
Carbon Graphite Boat -Laboratory Tube Furnace with Cover
Covered Carbon Graphite Boat Laboratory Tube Furnaces are specialized vessels or vessels made of graphite material designed to withstand extreme high temperatures and chemically aggressive environments.
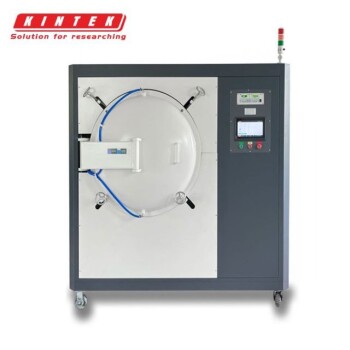
Vacuum Heat Treat Furnace with Ceramic Fiber Liner
Vacuum furnace with polycrystalline ceramic fiber insulation liner for excellent heat insulation and uniform temperature field. Choose from 1200℃ or 1700℃ max. working temperature with high vacuum performance and precise temperature control.
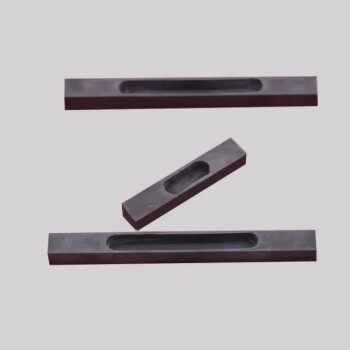
High Purity Pure Graphite Crucible for Evaporation
Vessels for high temperature applications, where materials are kept at extremely high temperatures to evaporate, allowing thin films to be deposited on substrates.
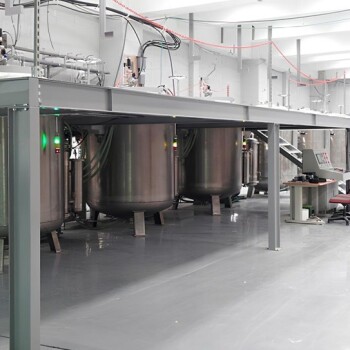
Graphite Vacuum Furnace Negative Material Graphitization Furnace
Graphitization furnace for battery production has uniform temperature and low energy consumption. Graphitization furnace for negative electrode materials: an efficient graphitization solution for battery production and advanced functions to enhance battery performance.
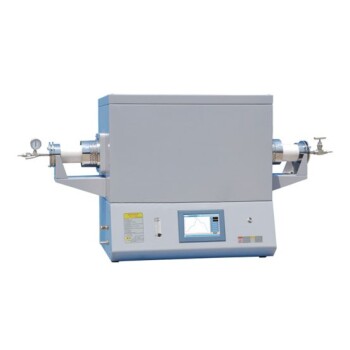
1700℃ Laboratory Quartz Tube Furnace with Alumina Tube Tubular Furnace
Looking for a high-temperature tube furnace? Check out our 1700℃ Tube Furnace with Alumina Tube. Perfect for research and industrial applications up to 1700C.
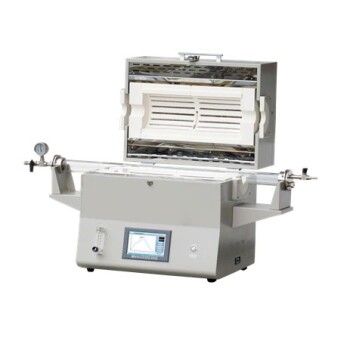
1400℃ Laboratory Quartz Tube Furnace with Alumina Tube Tubular Furnace
Looking for a tube furnace for high-temperature applications? Our 1400℃ Tube Furnace with Alumina Tube is perfect for research and industrial use.
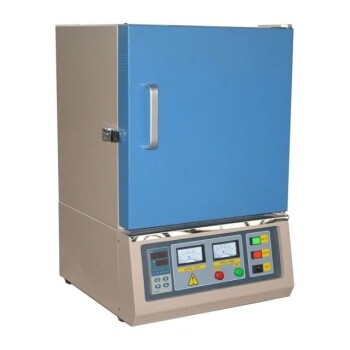
1400℃ Muffle Oven Furnace for Laboratory
Get precise high-temperature control up to 1500℃ with KT-14M Muffle furnace. Equipped with a smart touch screen controller and advanced insulation materials.
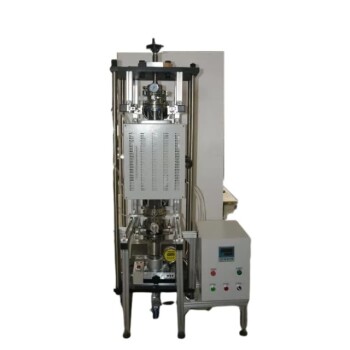
Vacuum Hot Press Furnace Heated Vacuum Press Machine Tube Furnace
Reduce forming pressure & shorten sintering time with Vacuum Tube Hot Press Furnace for high-density, fine-grain materials. Ideal for refractory metals.
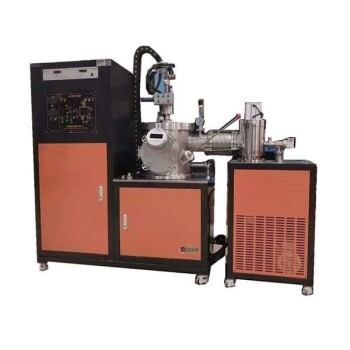
Vacuum Arc Induction Melting Furnace
Discover the power of Vacuum Arc Furnace for melting active & refractory metals. High-speed, remarkable degassing effect, and free of contamination. Learn more now!
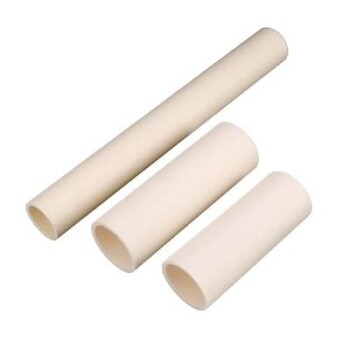
High Temperature Alumina (Al2O3) Furnace Tube for Engineering Advanced Fine Ceramics
High temperature alumina furnace tube combines the advantages of high hardness of alumina, good chemical inertness and steel, and has excellent wear resistance, thermal shock resistance and mechanical shock resistance.
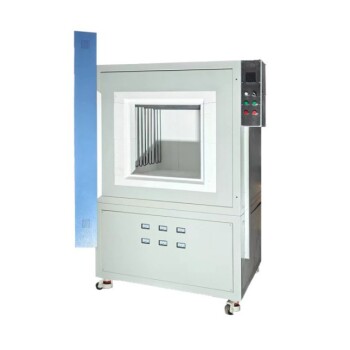
High Temperature Muffle Oven Furnace for Laboratory Debinding and Pre Sintering
KT-MD High temperature debinding and pre-sintering furnace for ceramic materials with various molding processes. Ideal for electronic components such as MLCC and NFC.
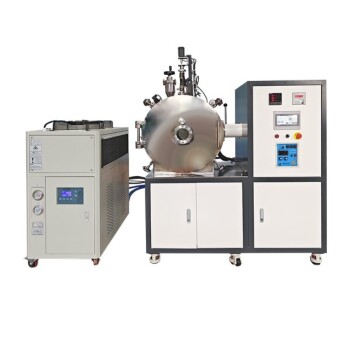
Lab-Scale Vacuum Induction Melting Furnace
Get precise alloy composition with our Vacuum Induction Melting Furnace. Ideal for aerospace, nuclear energy, and electronic industries. Order now for effective smelting and casting of metals and alloys.
Related Articles
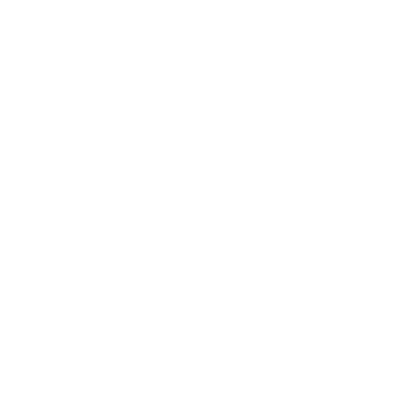
Optimizing Performance with Graphite Vacuum Furnaces: A Comprehensive Guide
Unlock the potential of graphite vacuum furnaces for high-temperature material treatment. Learn about their efficiency, customization options, automation, and key considerations for graphite rod usage.
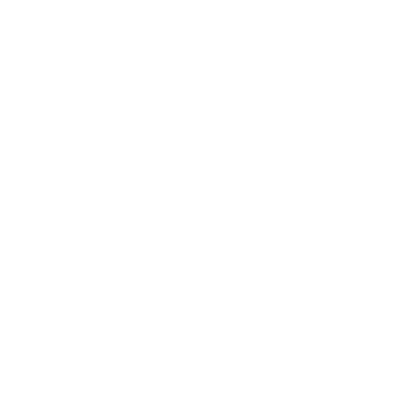
Maximizing Efficiency and Precision with Vacuum Graphite Furnaces
Discover how vacuum graphite furnaces revolutionize high-temperature material treatments with unmatched precision and efficiency. Explore customized solutions for various industries, advanced automation, and sustainable energy practices.
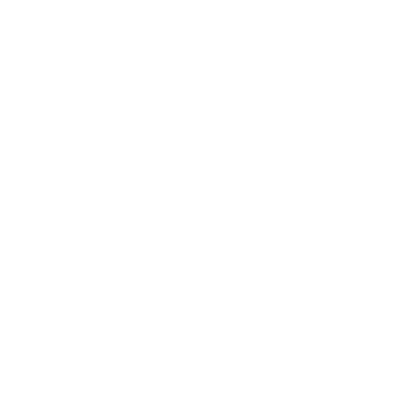
Unveiling Vacuum Graphite Furnaces: Performance, Applications, and Expert Insights
Delve into the world of vacuum graphite furnaces, exploring their exceptional performance, diverse applications, and crucial considerations. Our expert insights empower you to make informed decisions for your laboratory's high-temperature material treatment needs.
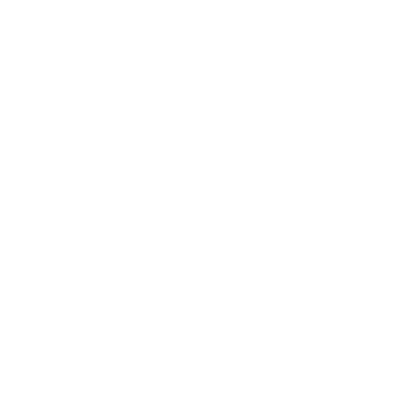
Comprehensive Guide to Muffle Furnaces: Applications, Types, and Maintenance
Explore the world of muffle furnaces with our detailed guide. Learn about their applications in various industries, types available, and essential maintenance tips to ensure optimal performance.
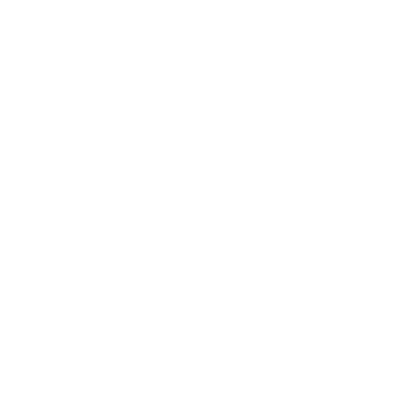
Hydrogen Atmosphere Furnaces: Applications, Safety, and Maintenance
Explore the comprehensive guide on hydrogen atmosphere furnaces, including their applications in high-end alloy sintering, safety measures, and maintenance tips. Learn about the types, components, and operational considerations for optimal performance.
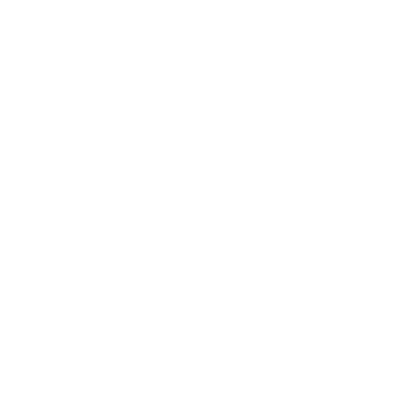
Comprehensive Guide to Spark Plasma Sintering Furnaces: Applications, Features, and Benefits
Explore the advanced features and applications of Spark Plasma Sintering Furnaces (SPS) in material science. Learn how SPS technology offers rapid, efficient, and versatile sintering for various materials.
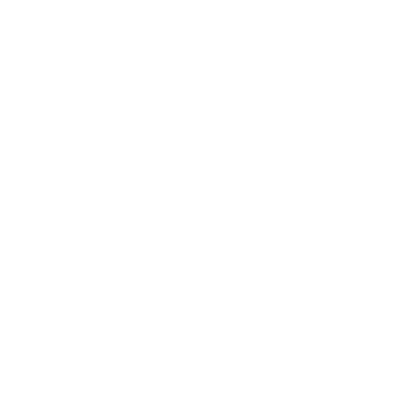
Exploring Spark Plasma Sintering Furnace (SPS): Technology, Applications, and Advantages
Dive into the comprehensive guide on Spark Plasma Sintering Furnace (SPS), covering its technology, applications in materials science, and significant advantages over traditional sintering methods.
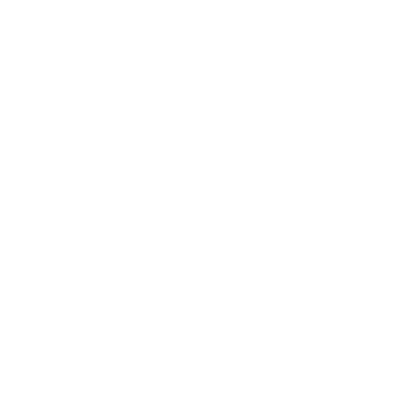
Comprehensive Guide to Atmosphere Furnaces: Types, Applications, and Benefits
Explore the world of atmosphere furnaces with our detailed guide. Learn about their types, applications in metallurgy and beyond, and the benefits they offer for precise material heat treatment.
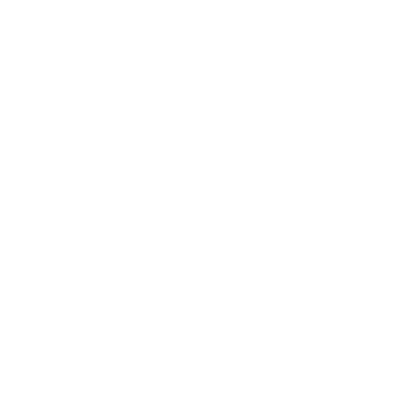
Molybdenum Vacuum Furnace: High-Temperature Sintering and Advanced Applications
Explore the advanced features and applications of molybdenum vacuum furnaces in high-temperature sintering and material treatment. Learn about their construction, control systems, and maintenance tips.
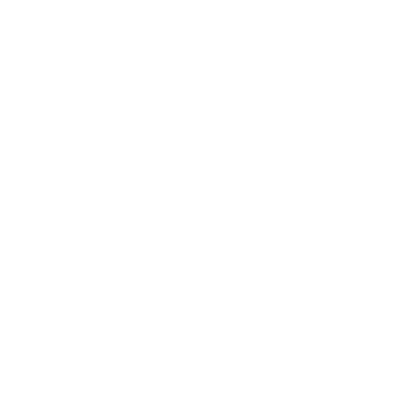
Exploring the Advanced Capabilities of Spark Plasma Sintering (SPS) Furnaces
Dive into the world of Spark Plasma Sintering (SPS) furnaces, their innovative technology, and applications in material science. Learn how SPS furnaces revolutionize the sintering process with high-speed, efficiency, and precision.
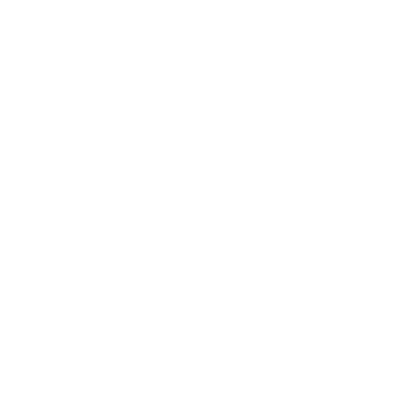
Ultimate Guide to High Pressure Tube Furnaces: Applications, Types, and Benefits
Explore the comprehensive guide to high pressure tube furnaces, including their applications in materials science, types such as horizontal and vertical, and key benefits for precise high-temperature processes.
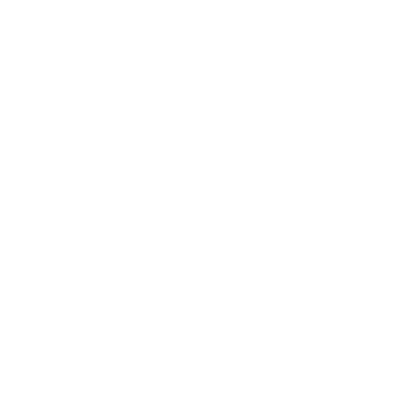
Atmosphere Furnaces: Comprehensive Guide to Controlled Heat Treatment
Explore the advanced world of atmosphere furnaces with our detailed guide. Learn about their operation, applications, and benefits in various industries. Perfect for those seeking in-depth knowledge on controlled heat treatment.