Introduction: Embracing Vacuum Graphite Furnaces for High-Temperature Material Treatment
Vacuum graphite furnaces are revolutionizing high-temperature material treatment with their unparalleled performance and versatility. These advanced furnaces utilize graphite wafers as heating elements, providing exceptional thermal efficiency and uniform heating. Their vacuum environment enables precise control of reactive or inert gases, making them ideal for various applications in aerospace, automotive, and medical industries. By embracing vacuum graphite furnaces, researchers and engineers can unlock new possibilities in material processing, ensuring optimal results and advancing scientific discoveries.
Graphite-Based Furnaces: Unlocking Thermal Efficiency and Performance
Graphite wafers, renowned for their exceptional properties, serve as ideal materials for furnace construction. Their inherent low density and reduced weight contribute to the overall efficiency of the furnace. However, it is their high emissivity that sets graphite apart, enabling it to approach ideal black body conditions. This characteristic ensures uniform heating, minimizing temperature gradients within the furnace chamber.
The thermal conductivity of graphite is another crucial factor contributing to its suitability for furnace applications. Graphite exhibits high thermal conductivity, allowing for efficient heat transfer from the heating elements to the furnace chamber. This efficient heat transfer ensures uniform temperature distribution, reducing the risk of thermal gradients and hotspots within the furnace.
Graphite's high temperature resistance is yet another advantage that makes it a preferred choice for furnace materials. Graphite can withstand extreme temperatures, up to 3000°C in inert gas and 2200°C in a vacuum, without melting or losing its structural integrity. This exceptional temperature resistance enables graphite furnaces to operate at higher temperatures, expanding their applicability in demanding thermal processes.
The chemical inertness of graphite is another significant advantage. Graphite exhibits resistance to oxidation, corrosion, and chemical reactions with most gases and liquids. This inertness allows graphite furnaces to be used in various chemical processes without the risk of contamination or degradation of the furnace materials.
In addition to its thermal and chemical properties, graphite also offers benefits in terms of maintenance and repair. Graphite furnace chambers are relatively easy to repair, allowing for quick and cost-effective maintenance. Furthermore, the use of sacrificial layers made of CFC or graphite laminate provides additional protection against high temperatures and gas erosion, extending the lifespan of the furnace chamber.
In summary, the exceptional properties of graphite wafers, including their low density, high emissivity, thermal conductivity, temperature resistance, and chemical inertness, make them ideal materials for furnace construction. Graphite furnaces offer superior thermal efficiency, uniform heating, high temperature capabilities, and ease of maintenance, making them a valuable asset in various thermal applications.
Exploring Vacuum Furnace Options and Applications
Vacuum furnaces offer exceptional versatility in handling both reactive and inert gases, enabling precise control over the furnace atmosphere during heat treatment processes. This versatility makes them suitable for a wide range of applications across various industries, including:
Aerospace
Vacuum furnaces play a crucial role in the aerospace industry, where they are utilized for:
- Brazing high-temperature alloys for aircraft engines and components
- Heat treating titanium and superalloys used in aircraft structures
- Annealing and stress relieving critical parts for satellites and spacecraft
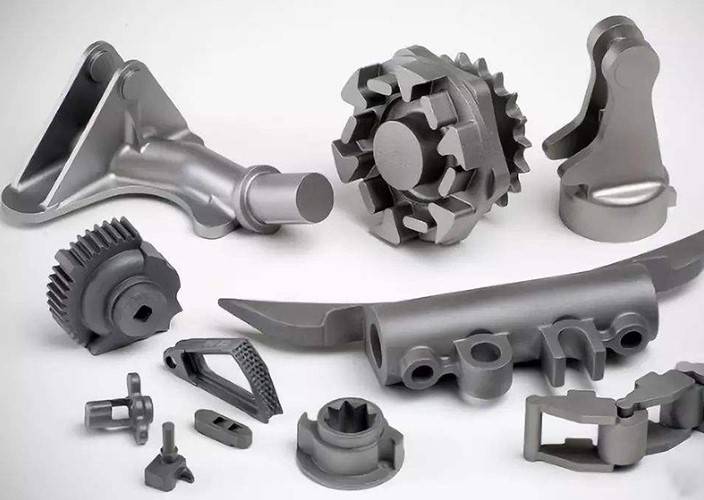
Automotive
In the automotive industry, vacuum furnaces are employed for:
- Carburizing and nitriding gears and other transmission components
- Sintering and heat treating powder metallurgy parts
- Annealing and aging high-strength steels used in vehicle frames and safety systems
Medical
Vacuum furnaces are essential in the medical device industry for:
- Brazing implants and surgical instruments
- Sterilizing and annealing medical tools
- Heat treating biocompatible materials used in prosthetics and implants
The versatility of vacuum furnaces extends beyond these core industries. They are also used in the following applications:
- Vacuum degassing and purification of metals and alloys
- Heat treating cutting tools and molds
- Sintering and brazing electronic components
Vacuum furnaces provide several advantages over conventional heat treatment methods:
- Controlled Atmosphere: By creating a vacuum environment, oxidation, decarburization, and contamination are minimized, ensuring the production of high-quality components with consistent properties.
- Precise Temperature Control: Vacuum furnaces offer precise temperature control, allowing for tailored heat treatment cycles that optimize the material's mechanical properties.
- Enhanced Efficiency: The vacuum environment reduces heat loss, leading to improved energy efficiency and faster processing times.
- Wide Temperature Range: Vacuum furnaces can operate over a wide temperature range, from low-temperature annealing to high-temperature sintering.
The choice of vacuum furnace type (hot wall or cold wall) and gas atmosphere (inert or reactive) depends on the specific application requirements. Inert gases, such as argon or nitrogen, are typically used to maintain a non-oxidizing environment, while reactive gases, such as hydrogen or methane, can be used for carburizing or nitriding processes.
Overall, vacuum furnaces offer a versatile and precise solution for heat treating a wide range of materials and components across numerous industries. Their ability to control the atmosphere, temperature, and processing parameters makes them an indispensable tool for manufacturers and researchers seeking to produce high-quality and reliable products.
Customized Solutions: Tailoring Furnaces to Specific Requirements
In today's demanding industrial landscape, standard laboratory equipment and consumables often fall short of meeting the unique and evolving needs of research and development teams. Customized vacuum furnace solutions have emerged as a powerful tool for addressing these challenges, empowering engineers and scientists to push the boundaries of innovation.
Vacuum furnaces offer a controlled environment for heat treatment processes, allowing for precise temperature and atmosphere control. However, off-the-shelf furnaces may not always align with the specific requirements of a particular application. This is where customized vacuum furnace engineering comes into play.
By collaborating closely with clients, engineers can design furnaces that are tailored to meet their unique objectives and processes. This collaborative approach ensures that the furnace's design, configuration, and performance characteristics are optimized for the intended application.
Custom vacuum furnaces offer a wide range of benefits, including:
- Tailored performance: Furnaces can be engineered to achieve specific temperature profiles, heating rates, and cooling rates, ensuring optimal process conditions for the materials being treated.
- Increased efficiency: Furnaces can be designed to minimize heat loss and optimize energy consumption, resulting in reduced operating costs and improved productivity.
- Enhanced safety: Custom furnaces can incorporate safety features that meet specific industry standards and regulations, minimizing risks and ensuring operator safety.
- Integration with existing systems: Furnaces can be designed to seamlessly integrate with existing laboratory equipment and automation systems, streamlining workflows and improving overall efficiency.
The customization process typically involves the following steps:
- Consultation: Engineers discuss the client's requirements, including process parameters, material properties, and desired outcomes.
- Design: Based on the consultation, engineers develop a detailed design for the furnace, including its dimensions, heating elements, temperature control systems, and safety features.
- Fabrication: The furnace is fabricated using high-quality materials and components, ensuring durability and reliability.
- Testing and validation: The finished furnace undergoes rigorous testing to ensure that it meets the client's specifications and performs as intended.
By leveraging customized vacuum furnace solutions, engineers and scientists can unlock new possibilities in materials research and development. These furnaces enable the precise control of heat treatment processes, leading to the creation of innovative materials with enhanced properties and performance.
Advanced Automation and Control: Enhancing Precision and Efficiency
Vacuum graphite furnaces incorporate advanced automation and control systems to ensure precise temperature regulation and process optimization. Programmable logic controllers (PLCs) and data acquisition systems monitor and control process parameters, adjusting temperature, atmosphere, and other variables to achieve desired outcomes.
These systems provide real-time monitoring and data logging, allowing operators to track process progress and make informed decisions. They automatically adjust settings based on predefined parameters, optimizing conditions for different materials and applications. This automation reduces the risk of human error and ensures consistent product quality.
Advanced control systems also enable remote monitoring and control, allowing operators to access and manage furnaces from any location with an internet connection. This capability facilitates remote troubleshooting, reduces downtime, and improves overall process efficiency.
By integrating advanced automation and control systems, vacuum graphite furnaces provide precise temperature regulation, optimized process parameters, and enhanced efficiency, leading to consistent, high-quality results and reduced operating costs.
Energy Efficiency and Sustainability: Embracing Green Practices
The vacuum furnace industry is actively committed to environmental sustainability, recognizing the importance of minimizing energy consumption and reducing carbon emissions. Vacuum furnaces are inherently energy-efficient devices, but manufacturers are continuously innovating to further enhance their sustainability credentials.
One key aspect of energy efficiency in vacuum furnaces is the precise control of heating and cooling cycles. By using advanced automation and control systems, vacuum furnaces can be programmed to deliver the exact amount of energy required to heat the workload to the desired temperature. This eliminates unnecessary energy consumption during non-heating phases, such as pumping down, loading, unloading, and cooling.
Furthermore, vacuum furnaces are designed with efficient heating elements and thermal insulation to minimize heat loss. This ensures that the majority of the energy used is directed towards heating the workload rather than escaping into the surrounding environment.
In addition to optimizing the heating process, manufacturers are also focusing on reducing the energy consumption of auxiliary systems. Water-cooling systems, gas cooling systems, and vacuum pumps can all contribute to the overall energy footprint of a vacuum furnace. By using energy-efficient components and optimizing the operation of these systems, manufacturers can significantly reduce energy consumption.
By embracing energy-efficient practices, vacuum furnace manufacturers are not only contributing to a greener future but also helping their customers save money on energy costs. By reducing energy consumption, businesses can lower their operating expenses and improve their profitability.
As the demand for sustainable solutions continues to grow, vacuum furnace manufacturers are well-positioned to meet the needs of their customers. By investing in energy efficiency and sustainability, they are demonstrating their commitment to environmental stewardship and providing their customers with the tools they need to reduce their carbon footprint and achieve their sustainability goals.
Unrivaled Technical Support and Service: Ensuring Optimal Performance
Reliable technical support and service are essential for ensuring optimal performance of vacuum graphite furnaces. Expert assistance can help you troubleshoot issues quickly, minimize downtime, and maximize the efficiency of your furnace.
Our team of experienced technicians is available 24/7 to provide support via phone, email, or live chat. We also offer on-site service and training to ensure that your furnace is operating at peak performance.
Benefits of Unrivaled Technical Support and Service:
- Reduced Downtime: Expert assistance can help you quickly identify and resolve issues, minimizing downtime and keeping your furnace running smoothly.
- Improved Performance: Regular maintenance and calibration ensure that your furnace is operating at optimal efficiency, producing high-quality results.
- Extended Lifespan: Proper maintenance and support can extend the lifespan of your furnace, saving you money in the long run.
- Peace of Mind: Knowing that you have access to expert support provides peace of mind and allows you to focus on your research or production.
Our Commitment to Customer Satisfaction:
We believe that customer satisfaction extends beyond the initial purchase. Our comprehensive technical support and service is designed to ensure that your vacuum graphite furnace performs optimally throughout its lifespan. We are committed to providing you with the highest level of support and service to help you achieve your research or production goals.
Experience the Graphite Furnace Systems Difference:
When you choose Graphite Furnace Systems, you not only get a high-quality vacuum graphite furnace, but also access to our unparalleled technical support and service. Our team of experts is dedicated to helping you get the most out of your furnace and achieve optimal performance.
Contact us today to learn more about our technical support and service offerings, and experience the Graphite Furnace Systems difference!
CONTACT US FOR A FREE CONSULTATION
KINTEK LAB SOLUTION's products and services have been recognized by customers around the world. Our staff will be happy to assist with any inquiry you might have. Contact us for a free consultation and talk to a product specialist to find the most suitable solution for your application needs!