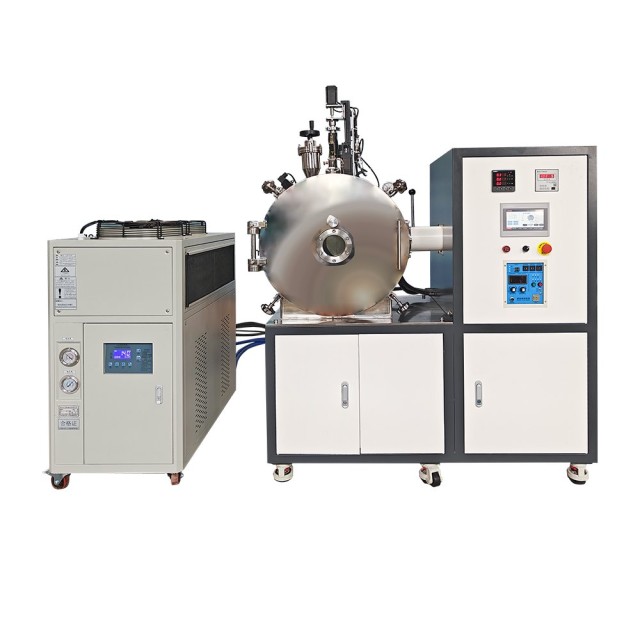
Vacuum Furnace
Lab-Scale Vacuum Induction Melting Furnace
Item Number : KT-VI
Price varies based on specs and customizations
- Temperature
- 1700 ℃
- Vacuum
- 6x10-3 Pa
- Capacity
- 5-20 kg
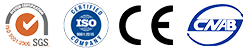
Shipping:
Contact us to get shipping details Enjoy On-time Dispatch Guarantee.
Why Choose Us
Reliable PartnerEasy ordering process, quality products, and dedicated support for your business success.
Engineered for Precision, Designed for the Modern Laboratory. At KINTEK, we understand the unique demands of the research environment. Our Vacuum Induction Melting (VIM) Furnace is specifically designed for R&D, materials science, and small-scale production where purity, precision, and repeatability are paramount. It is the ideal solution for universities, research institutions, and corporate R&D labs looking to develop next-generation alloys and high-purity metals.
Why Choose the KINTEK VIM Furnace for Your Laboratory?
Leveraging KINTEK's expertise in specialized lab equipment, this furnace offers distinct advantages for the research-focused user:
- Unmatched Purity for Reliable Data: By melting materials in a high-vacuum or controlled inert gas environment, our furnace minimizes contamination from atmospheric gases like oxygen and nitrogen. This ensures the intrinsic properties of your alloys are preserved, leading to accurate and repeatable experimental results.
- Compact Design, Powerful Performance: We know lab space is valuable. Our VIM furnace series offers a compact footprint without compromising on power, reaching temperatures up to 2000°C (model dependent) to handle a wide range of metals, including high-temperature alloys, active metals, and special steels.
- Precision Control for Repeatable Processes: Equipped with an intuitive PLC and touch-screen controller, the furnace allows for precise programming and monitoring of the entire melting cycle. This guarantees process consistency, which is critical for comparative studies and quality control.
- Versatile for Diverse Research Needs: Whether you are developing novel superalloys, refining precious metals, creating magnetic materials, or preparing samples for further analysis, the KINTEK VIM furnace provides the flexibility to meet a broad spectrum of research applications.
- Designed for Safety and Ease of Use: With features like a water-cooled furnace body, comprehensive monitoring, and a user-friendly tilting mechanism, our furnace is built to ensure safe and straightforward operation within a laboratory setting.
Applications in Research & Development
The KINTEK VIM Furnace is an indispensable tool for cutting-edge materials research. Key laboratory applications include:
- Materials Science & New Alloy Development
- High-Purity Metal Sample Preparation
- Academic Research and Metallurgical Studies
- Prototyping of Small, High-Performance Components
- Processing of Active and Reactive Metals (e.g., Titanium alloys)
- Development of High-Temperature Superalloys
- Creation of a High-Purity Magnetic Materials
- Smelting of Precious Metals (e.g., Gold, Platinum)
A Closer Look: Key Features & Components
Every component of the KINTEK VIM Furnace is engineered for performance and reliability.
- High-Integrity Vacuum Chamber: The water-cooled, stainless steel furnace body and cover ensure an air-tight seal, achieving high vacuum levels (up to 6x10⁻³ Pa) to prevent oxidation and remove dissolved gas impurities.
- Advanced Induction Heating: A powerful medium-frequency power supply and a custom-wound induction coil provide rapid, efficient, and uniform heating. The electromagnetic stirring effect naturally homogenizes the melt for superior alloy consistency.
- Intuitive Control System: The PLC system with a color touch-screen interface provides full control over the vacuum system, heating power, temperature, and pouring. It features data logging and recipe storage for process repeatability.
- Robust Vacuum System: A multi-stage vacuum system, typically consisting of a rotary vane pump, a roots pump, and a diffusion pump, allows for fast pump-down times and maintains the deep vacuum required for high-purity melts.
- User-Centric Design: Features like an observation window, an alloy feeder for making additions during the melt, and a smooth, controllable tilting mechanism (manual, electric, or hydraulic options) make the furnace easy and safe to operate.
Available Models & Technical Specifications
KINTEK offers a range of models to perfectly match your lab's capacity and research requirements. Our most popular lab-scale models are listed below. Larger production models are also available upon request.
Model | Capacity (Steel) | Max. Temperature | Ultimate Vacuum | Rated Power |
---|---|---|---|---|
KT-VI5 | 5 kg | 1700 ℃ (2000 ℃ optional) | 6 x 10⁻³ Pa | 40 Kw |
KT-VI10 | 10 kg | 40 Kw | ||
KT-VI25 | 25 kg | 75 Kw | ||
KT-VI50 | 50 kg | 100 Kw | ||
KT-VI100 | 100 kg | 160 Kw | ||
KT-VI200 | 200 kg | 200 Kw | ||
KT-VI500 | 500 kg | 500 Kw | ||
Note: Custom configurations and semi-continuous melting systems are available. Contact us to discuss your specific needs. |
Partner with KINTEK for Your Lab's Success
As a specialist in laboratory equipment and consumables, KINTEK is committed to empowering researchers with tools that deliver exceptional performance and value. Our team is ready to help you select the perfect VIM furnace configuration for your application and provide ongoing support to ensure you get the most out of your investment. Contact us today to request a quote or discuss your project with a technical expert.
Further Reading
Learn More: Melting Process and Maintenance of a Vacuum Induction Melting Furnace
Warnings
Operator safety is the top important issue! Please operate the equipment with cautions. Working with inflammable& explosive or toxic gases is very dangerous, operators must take all necessary precautions before starting the equipment. Working with positive pressure inside the reactors or chambers is dangerous, operator must fellow the safety procedures strictly. Extra caution must also be taken when operating with air-reactive materials, especially under vacuum. A leak can draw air into the apparatus and cause a violent reaction to occur.
Designed for You
KinTek provide deep custom made service and equipment to worldwide customers, our specialized teamwork and rich experienced engineers are capable to undertake the custom tailoring hardware and software equipment requirements, and help our customer to build up the exclusive and personalized equipment and solution!
Would you please drop your ideas to us, our engineers are ready for you now!
FAQ
What Is A Vacuum Induction Furnace And How Does It Work?
What Is A Vacuum Furnace Used For?
How Does A Vacuum Induction Melting Furnace Work?
What Is Vacuum Arc Melting Process?
What Are The Main Applications Of Vacuum Induction Furnaces?
What Is The Process Of A Vacuum Furnace?
What Is A Atmospheric Furnace?
What Are The Advantages Of Vacuum Induction Melting?
What Is VAR Vacuum Arc Remelting (VAR)Furnace?
What Are The Advantages Of Using A Vacuum Induction Furnace?
What Gas Is Used In A Vacuum Furnace?
What Is The Use Of Atmosphere Furnace?
How Does Vacuum Help In Induction Melting Furnace?
How Does Vacuum Arc Melting Furnace Work?
What Types Of Materials Can Be Processed In A Vacuum Induction Furnace?
What Is The Heating Element Used In A Vacuum Furnace?
How Does An Atmosphere Furnace Work?
What Is Vacuum Induction Melting Furnace?
What Are The Applications Of Vacuum Arc Melting Furnaces?
How Does The Vacuum Environment In A Vacuum Induction Furnace Improve Material Properties?
What Are The Advantages Of Using Atmosphere Furnaces?
What Are The Advantages Of Using Vacuum Arc Melting Furnaces?
What Factors Should Be Considered When Selecting An Atmosphere Furnace?
What Safety Precautions Should Be Followed When Using A Vacuum Arc Melting Furnace?
4.9
out of
5
I was very impressed with the speed of delivery. The product arrived much sooner than I expected.
4.7
out of
5
The product was exactly as described, and the quality is excellent. It is definitely worth the money.
4.8
out of
5
I have been using this product for a few months now, and I am very happy with it. It is durable and has held up well to heavy use.
4.9
out of
5
The product is very technologically advanced and has helped me to improve my productivity.
4.7
out of
5
I would highly recommend this product to anyone who is looking for a high-quality, durable, and technologically advanced product.
4.8
out of
5
The product is very easy to use and has a user-friendly interface.
4.9
out of
5
I am very satisfied with the product and would definitely recommend it to others.
4.7
out of
5
The product is very well-made and has exceeded my expectations.
4.8
out of
5
I am very impressed with the product and would definitely recommend it to others.
4.9
out of
5
The product is very easy to use and has a user-friendly interface.
4.7
out of
5
The product is very well-made and has exceeded my expectations.
4.8
out of
5
I am very impressed with the product and would definitely recommend it to others.
4.9
out of
5
The product is very easy to use and has a user-friendly interface.
4.7
out of
5
The product is very well-made and has exceeded my expectations.
4.8
out of
5
I am very impressed with the product and would definitely recommend it to others.
Products
Lab-Scale Vacuum Induction Melting Furnace
REQUEST A QUOTE
Our professional team will reply to you within one business day. Please feel free to contact us!
Related Products
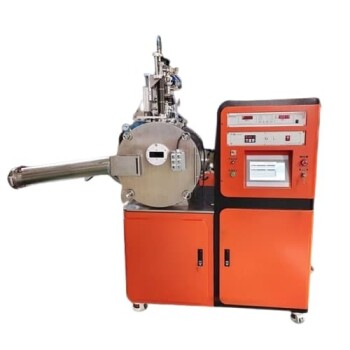
Vacuum Induction Melting Spinning System Arc Melting Furnace
Develop metastable materials with ease using our Vacuum Melt Spinning System. Ideal for research and experimental work with amorphous and microcrystalline materials. Order now for effective results.
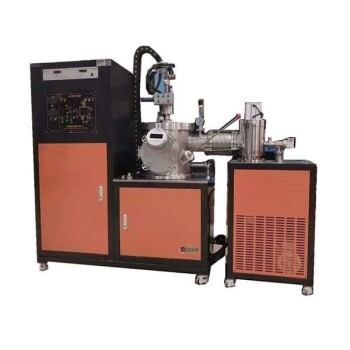
Vacuum Arc Induction Melting Furnace
Discover the power of Vacuum Arc Furnace for melting active & refractory metals. High-speed, remarkable degassing effect, and free of contamination. Learn more now!
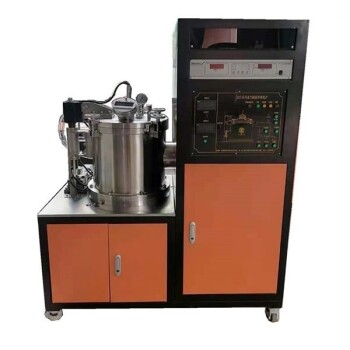
Vacuum Heat Treat Furnace and Levitation Induction Melting Furnace
Experience precise melting with our Vacuum Levitation Melting Furnace. Ideal for high melting point metals or alloys, with advanced technology for effective smelting. Order now for high-quality results.
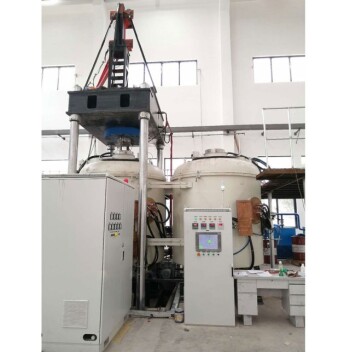
600T Vacuum Induction Hot Press Furnace for Heat Treat and Sintering
Discover the 600T Vacuum Induction Hot Press Furnace, designed for high-temperature sintering experiments in vacuum or protected atmospheres. Its precise temperature and pressure control, adjustable working pressure, and advanced safety features make it ideal for nonmetal materials, carbon composites, ceramics, and metal powders.
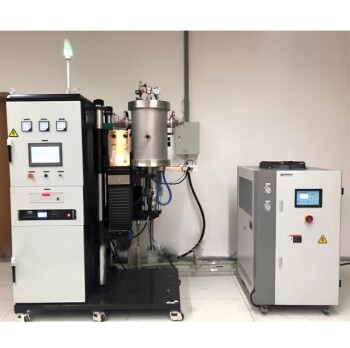
Vacuum Heat Treat and Molybdenum Wire Sintering Furnace for Vacuum Sintering
A vacuum molybdenum wire sintering furnace is a vertical or bedroom structure, which is suitable for withdrawal, brazing, sintering and degassing of metal materials under high vacuum and high temperature conditions. It is also suitable for dehydroxylation treatment of quartz materials.
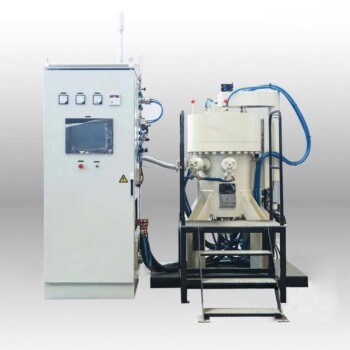
Vacuum Heat Treat and Sintering Furnace with 9MPa Air Pressure
The air pressure sintering furnace is a high-tech equipment commonly used for the sintering of advanced ceramic materials. It combines vacuum sintering and pressure sintering techniques to achieve high-density and high-strength ceramics.
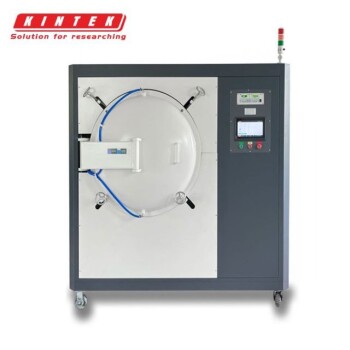
Vacuum Heat Treat Furnace with Ceramic Fiber Liner
Vacuum furnace with polycrystalline ceramic fiber insulation liner for excellent heat insulation and uniform temperature field. Choose from 1200℃ or 1700℃ max. working temperature with high vacuum performance and precise temperature control.
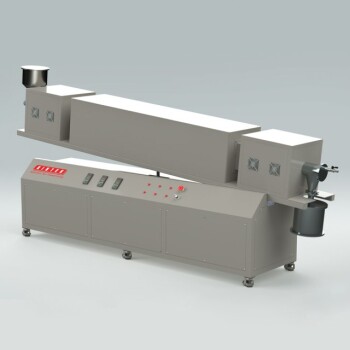
Vacuum Sealed Continuous Working Rotary Tube Furnace Rotating Tube Furnace
Experience efficient material processing with our vacuum-sealed rotary tube furnace. Perfect for experiments or industrial production, equipped with optional features for controlled feeding and optimized results. Order now.
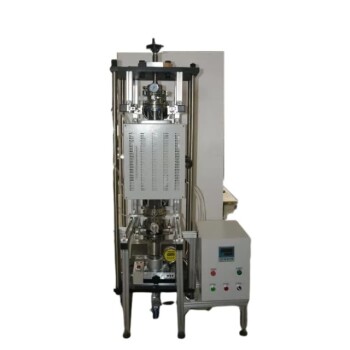
Vacuum Hot Press Furnace Heated Vacuum Press Machine Tube Furnace
Reduce forming pressure & shorten sintering time with Vacuum Tube Hot Press Furnace for high-density, fine-grain materials. Ideal for refractory metals.
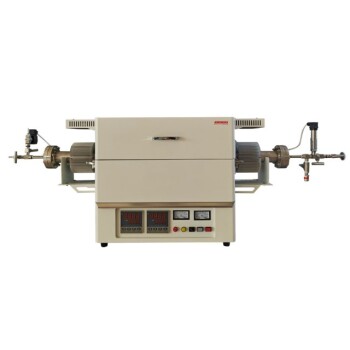
High Pressure Laboratory Vacuum Tube Furnace Quartz Tubular Furnace
KT-PTF High Pressure Tube Furnace: Compact split tube furnace with strong positive pressure resistance. Working temp up to 1100°C and pressure up to 15Mpa. Also works under controller atmosphere or high vacuum.
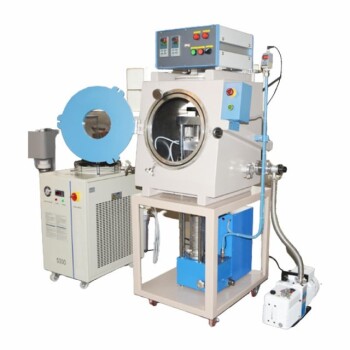
Vacuum Hot Press Furnace Machine for Lamination and Heating
Experience clean and precise lamination with Vacuum Lamination Press. Perfect for wafer bonding, thin-film transformations, and LCP lamination. Order now!
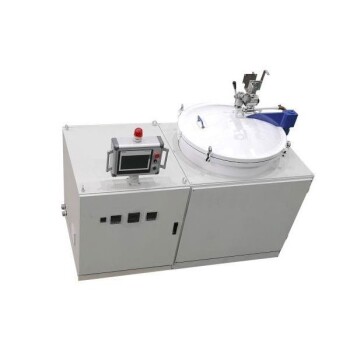
Graphite Vacuum Furnace IGBT Experimental Graphitization Furnace
IGBT experimental graphitization furnace, a tailored solution for universities and research institutions, with high heating efficiency, user-friendliness, and precise temperature control.
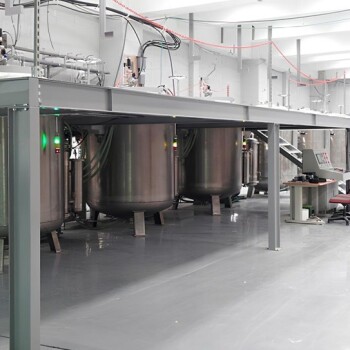
Graphite Vacuum Furnace Negative Material Graphitization Furnace
Graphitization furnace for battery production has uniform temperature and low energy consumption. Graphitization furnace for negative electrode materials: an efficient graphitization solution for battery production and advanced functions to enhance battery performance.
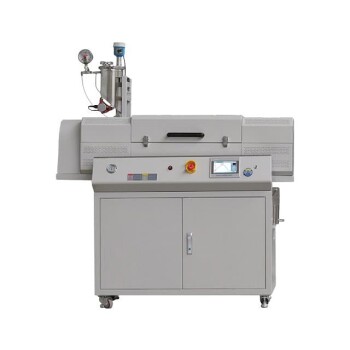
Laboratory Vacuum Tilt Rotary Tube Furnace Rotating Tube Furnace
Discover the versatility of Laboratory Rotary Furnace: Ideal for calcination, drying, sintering, and high-temperature reactions. Adjustable rotating and tilting functions for optimal heating. Suitable for vacuum and controlled atmosphere environments. Learn more now!
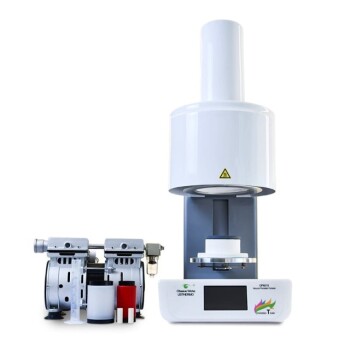
Dental Porcelain Zirconia Sintering Ceramic Vacuum Press Furnace
Get precise dental results with Dental Vacuum Press Furnace. Automatic temperature calibration, low noise tray, and touch screen operation. Order now!
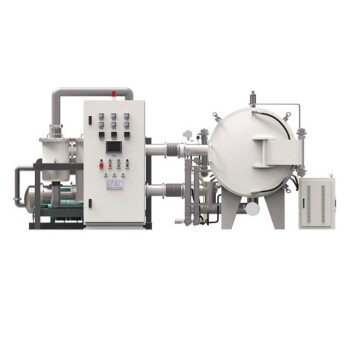
Horizontal High Temperature Graphite Vacuum Graphitization Furnace
Horizontal Graphitization Furnace: This type of furnace is designed with the heating elements placed horizontally, allowing for uniform heating of the sample. It's well-suited for graphitizing large or bulky samples that require precise temperature control and uniformity.
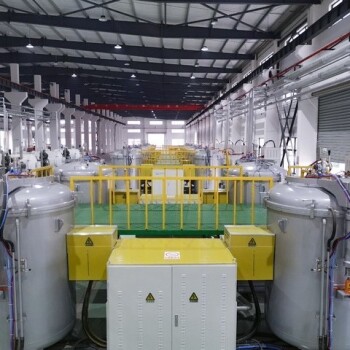
Vertical High Temperature Graphite Vacuum Graphitization Furnace
Vertical high temperature graphitization furnace for carbonization and graphitization of carbon materials up to 3100℃.Suitable for shaped graphitization of carbon fiber filaments and other materials sintered in a carbon environment.Applications in metallurgy, electronics, and aerospace for producing high-quality graphite products like electrodes and crucibles.

Graphite Vacuum Furnace Bottom Discharge Graphitization Furnace for Carbon Materials
Bottom-out graphitization furnace for carbon materials, ultra-high temperature furnace up to 3100°C, suitable for graphitization and sintering of carbon rods and carbon blocks. Vertical design, bottom discharging, convenient feeding and discharging, high temperature uniformity, low energy consumption, good stability, hydraulic lifting system, convenient loading and unloading.
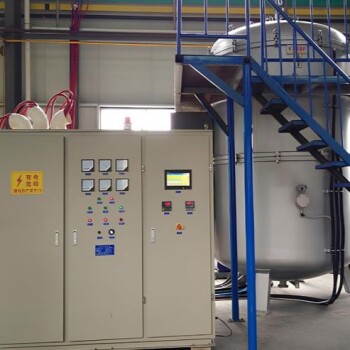
Large Vertical Graphite Vacuum Graphitization Furnace
A large vertical high-temperature graphitization furnace is a type of industrial furnace used for the graphitization of carbon materials, such as carbon fiber and carbon black. It is a high-temperature furnace that can reach temperatures of up to 3100°C.
Related Articles
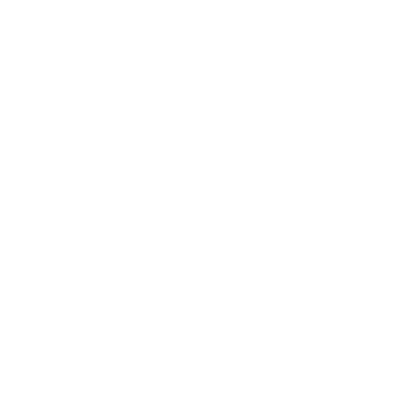
How Vacuum Induction Melting Powers Superior Material Performance in Critical Industries
Discover how Vacuum Induction Melting (VIM) ensures 99.99% pure alloys for aerospace and medical industries, boosting performance and compliance.
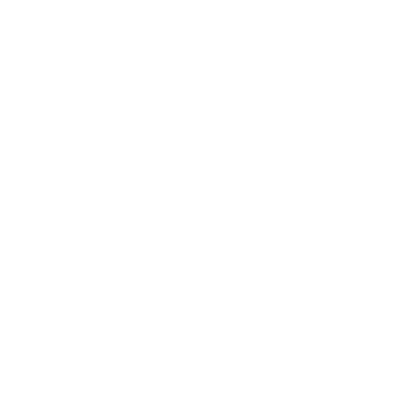
How Vacuum Induction Melting Ensures Unmatched Reliability in Critical Industries
Vacuum induction melting (VIM) ensures metallurgical purity, durability, and efficiency in aerospace, nuclear, and critical industries. Learn why VIM outperforms traditional methods.
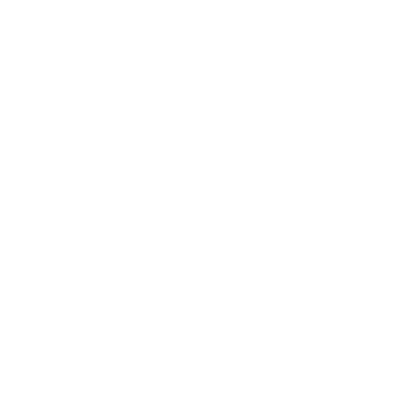
How Vacuum Induction Melting (VIM) Transforms High-Performance Alloy Production
Discover how Vacuum Induction Melting (VIM) enhances alloy purity for aerospace, medical, and nuclear industries, reducing defects and costs.
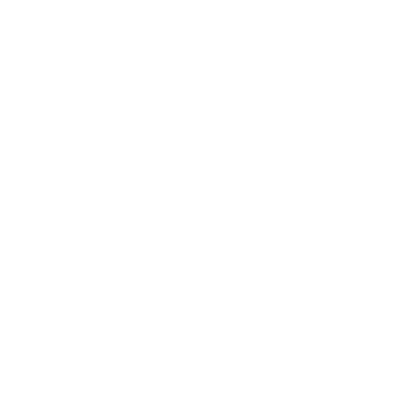
How Vacuum Induction Melting Outperforms Traditional Methods in Advanced Alloy Production
Discover how vacuum induction melting (VIM) outperforms traditional methods in advanced alloy production, offering precision, purity, and cost savings.
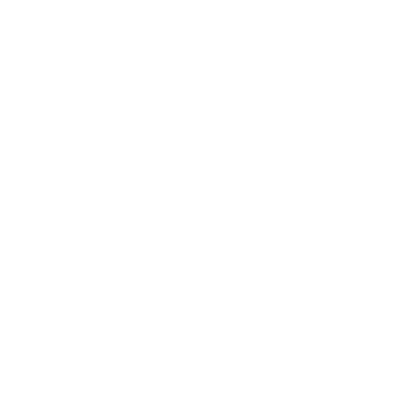
How Vacuum Induction Melting Elevates High-Performance Alloy Production
Discover how Vacuum Induction Melting (VIM) enhances alloy purity, reduces defects, and optimizes costs for aerospace and energy sectors.
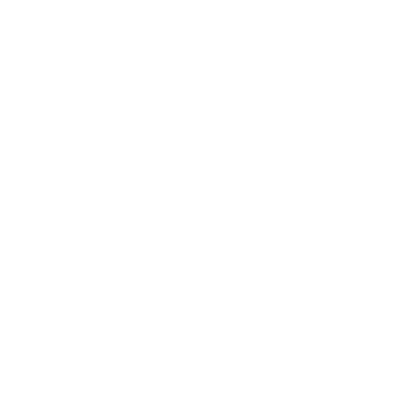
How Vacuum Induction Melting Prevents Catastrophic Material Failures in Critical Components
Discover how Vacuum Induction Melting (VIM) prevents material failures in aerospace, nuclear, and EV components by eliminating atomic-level contamination.
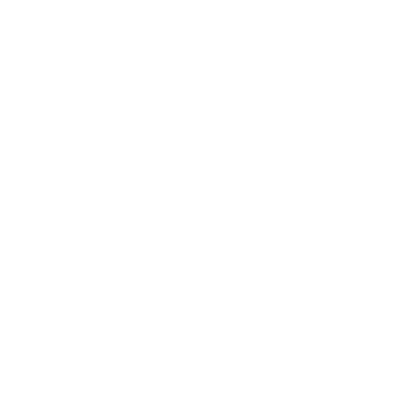
How to Choose Crucible Materials That Prevent Chemical Degradation in Vacuum Induction Melting
Learn how to choose crucible materials for vacuum induction melting to prevent chemical degradation and optimize alloy purity. Essential guide for industrial applications.
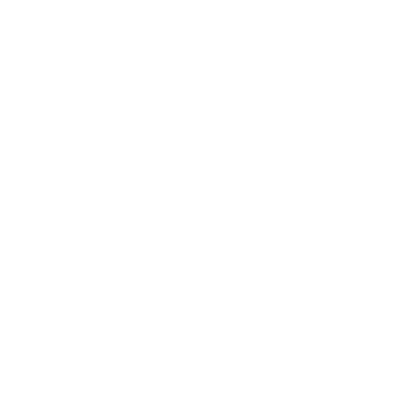
Melting process and maintenance of vacuum induction melting furnace
Melting process and maintenance of vacuum induction melting furnace
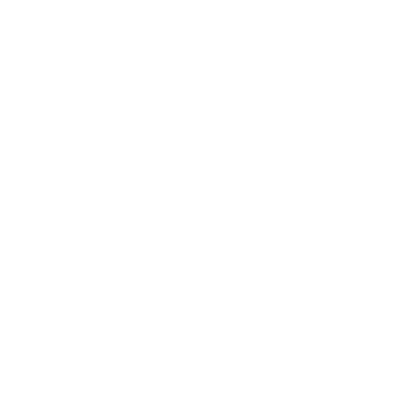
Application of Hot Isostatic Pressing Technology in Nickel-Based Casting High-Temperature Alloys
Explores the use of hot isostatic pressing to enhance the properties of nickel-based casting high-temperature alloys in aerospace applications.
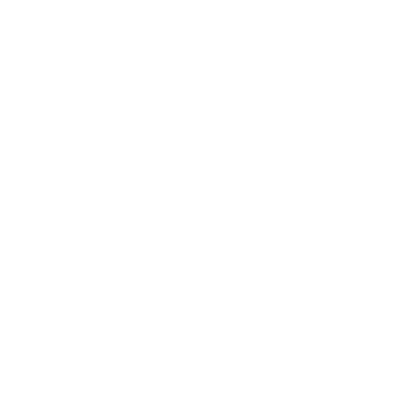
Vacuum Induction Melting Furnace: Principle, Advantages, and Applications
Discover the Vacuum Induction Melting Furnace, a specialized equipment that employs vacuum and induction heating to refine metals and alloys, ensuring high purity and precise composition control. Explore its principle, advantages, applications, and components in this comprehensive guide.
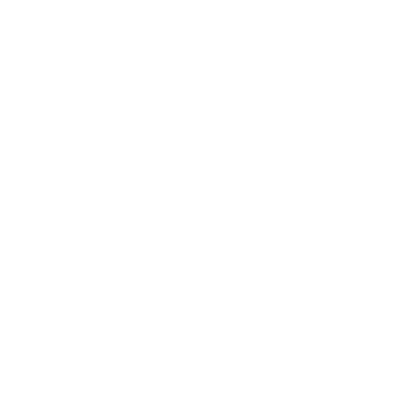
Vacuum Melting Furnace: A Comprehensive Guide to Vacuum Induction Melting
Discover the intricacies of vacuum induction melting furnaces, their components, operation, advantages, and applications. Explore how these furnaces revolutionize metal processing and achieve exceptional material properties.
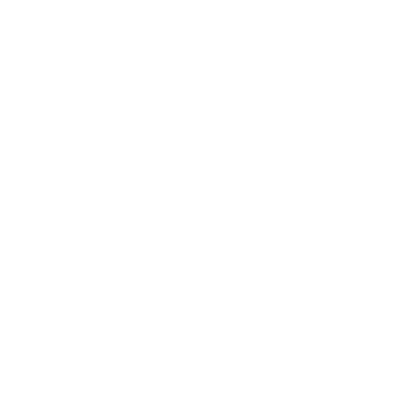
Vacuum Induction Furnace Fault Inspection: Essential Procedures and Solutions
Discover the essential procedures for inspecting and troubleshooting common faults in vacuum induction furnace. Learn how to troubleshoot electrical failures, conduct post-operation inspections, maintain records, and monitor the furnace's operation. Take corrective actions to ensure the furnace's optimal performance. Find expert solutions for temperature abnormalities, vacuum level deviations, and furnace chamber inspections.