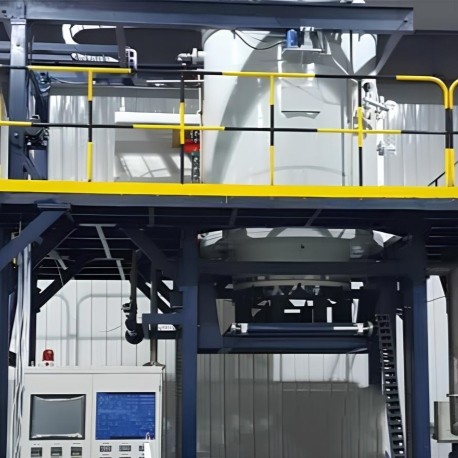
Graphitization furnace
Graphite Vacuum Furnace Bottom Discharge Graphitization Furnace for Carbon Materials
Item Number : GF-06
Price varies based on specs and customizations
- Volume(L)
- 1250 / 196 / 282 / 550 / 1000 / 1500
- Power(KW)
- 150-800
- Frequency(HZ)
- 1000 / 1500
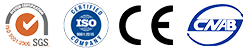
Shipping:
Contact us to get shipping details Enjoy On-time Dispatch Guarantee.
Why Choose Us
Reliable PartnerEasy ordering process, quality products, and dedicated support for your business success.
Introduction
The Bottom Discharge Graphitization Furnace is a type of high-temperature furnace, typically used for graphitization and sintering of carbon materials. It can reach temperatures up to 3100°C, making it suitable for processing large bars and high-density blocks. The bottom-discharging design facilitates feeding and discharging materials, simplifying the process and improving efficiency.
The furnace employs medium frequency induction heating for rapid temperature rise and high efficiency. It features double-layer alumina brick insulation for optimal heat retention and fire resistance, minimizing heat loss and enhancing stability. The hydraulic lifting system allows for convenient loading and unloading at ground level, while the digital flow monitoring system ensures water flow monitoring and protection. Additionally, the furnace is equipped with a PLC water, electricity, gas automatic control and protection system for comprehensive monitoring and safety.
Applications
Bottom discharge graphitization furnaces are widely used in various industries, including:
- Carbonization and graphitization of carbon materials
- Shaped graphitization of carbon fiber filaments
- Sintering of materials in a carbon environment
Features
- Improved temperature uniformity: The unique furnace design ensures consistent temperatures throughout the furnace chamber, leading to more precise and reliable results.
- Reduced energy consumption: The double-layer alumina brick insulation material minimizes heat loss, resulting in lower operating costs and increased energy efficiency.
- Enhanced stability: The stable hydraulic lifting system and comprehensive PLC water, electricity, and gas automatic control and protection system ensure smooth and reliable operation, minimizing downtime and maintenance costs.
- Convenient loading and unloading: The user-friendly design, with ground guide rails and material trucks, simplifies the loading and unloading process, providing increased efficiency and safety.
- Advanced monitoring system: The digital flow monitoring system ensures precise control over the water flow and provides comprehensive protection, preventing equipment damage and ensuring safe operation.
Principle
The bottom discharge graphitization furnace uses medium frequency induction heating to quickly raise the temperature. The furnace design improves temperature uniformity. Double-layer alumina brick insulation material prevents short circuits and provides heat insulation, reducing heat loss. The hydraulic lifting system allows for convenient loading and unloading on the ground. The digital flow monitoring system and PLC control system ensure water, electricity, and gas monitoring and protection.
Advantages
- High temperature resistance: The furnace can withstand ultra-high temperatures of up to 3100°C, making it suitable for graphitization and sintering of carbon materials such as large bars and high-density blocks.
- Convenient feeding and discharging: The bottom-discharging design allows for easy loading and unloading of materials, facilitating efficient processing.
- Improved temperature uniformity: The medium frequency induction heating technology ensures rapid temperature rise and enhanced temperature uniformity throughout the furnace chamber.
- Energy efficiency and stability: Double-layer alumina brick insulation effectively reduces heat loss and improves equipment stability, resulting in lower energy consumption.
- Enhanced safety: The digital flow monitoring system and comprehensive PLC control system provide real-time monitoring and protection against potential hazards, ensuring safe operation.
- Versatile applications: The bottom-discharging vertical graphitization furnace is suitable for carbonization, graphitization, and sintering of various carbon materials, including carbon fiber filaments.
Technical parameters and specifications
Furnace body temperature uniformity: Using medium frequency induction heating, the temperature rises quickly and the efficiency is high. The unique furnace design greatly improves the furnace body temperature uniformity;
Low energy consumption and good stability: Double-layer alumina brick insulation material is used to prevent short circuit between carbon felt and coil, good heat insulation and fire resistance, small heat loss, and good equipment stability;
According to the needs of the sintering process time, a single power supply can be configured with multiple electric furnaces, and the multiple furnaces can be powered on to heat up and power off to cool down respectively to achieve continuous operation;
Digital flow monitoring system, each channel of water flow monitoring and protection in the power cabinet, furnace conversion using high-performance medium frequency contactor; comprehensive PLC water, electricity, gas automatic control and protection system.
Product model specifications | GF-06-Ф40X100 | GF-06-Ф50X100 | GF-06-Ф60X100 | GF-06-Ф70X140 | GF-06-Ф90X160 | GF-06-100X200 |
---|---|---|---|---|---|---|
Volume(L) | 125 | 196 | 282 | 550 | 1000 | 1500 |
Rated temperature(C) | 2800 | 2800 | 2800 | 2800 | 2800 | 2600 |
Limit temperature(C) | 3100 | 3100 | 3100 | 3100 | 300 | 2800 |
Effective heating area (mm) | Ф400×1000 | Ф500×1000 | Ф600×1000 | Ф700×1400 | Ф900×1600 | Ф1000×2000 |
Power(KW) | 150 | 200 | 300 | 500 | 600 | 800 |
Frequency(HZ) | 1500 | 1000 | 1000 | 1000 | 1000 | 1000 |
Temperature control method | Japan Shima Electric Thermostat | |||||
heating method | Induction heating | |||||
Vacuum system | Rotary vane vacuum pump (for high vacuum requirements, Roots vacuum pump and oil diffusion pump are required) | |||||
sintering atmosphere | N² Ar and other gases | |||||
Rated power supply voltage (V) | 380 | |||||
Rated heating voltage (V) | 750 | |||||
Vacuum limit (Pa) | 100 (vacuum cold state) |
FAQ
What Is A Graphitization Furnace?
What Is A Graphite Vacuum Furnace Used For?
What Is A Vacuum Furnace Used For?
What Is The Purpose Of A Bottom Discharge Graphitization Furnace?
What Are The Key Features Of A Bottom Discharge Graphitization Furnace?
What Are The Advantages Of Using A Bottom Discharge Graphitization Furnace?
What Are The Main Applications Of Graphitization Furnaces?
What Are The Main Types Of Graphite Vacuum Furnaces?
What Is The Process Of A Vacuum Furnace?
What Are The Different Types Of Graphitization Furnaces?
How Does A Graphite Vacuum Furnace Work?
What Gas Is Used In A Vacuum Furnace?
How Does A Graphitization Furnace Work?
What Are The Advantages Of Using A Graphite Vacuum Furnace?
What Is The Heating Element Used In A Vacuum Furnace?
What Are The Advantages Of Using A Graphitization Furnace?
What Temperature Range Can A Graphite Vacuum Furnace Achieve?
What Industries Benefit From Graphite Vacuum Furnaces?
4.9
out of
5
The furnace delivered within the promised time frame, which was a lifesaver for our project. I highly recommend this product.
4.8
out of
5
The furnace is a great value for the money. It's well-made and performs as advertised. I'm very satisfied with my purchase.
4.9
out of
5
The furnace is of exceptional quality. It's built to last and has exceeded my expectations. I'm confident it will serve us well for many years to come.
4.7
out of
5
The furnace is very durable and has withstood the rigors of our demanding production environment. I'm impressed with its resilience.
4.8
out of
5
The furnace incorporates cutting-edge technology that gives us a competitive edge. It's a game-changer for our research and development.
4.9
out of
5
The furnace is easy to use and maintain. The user-friendly design makes it a pleasure to operate.
4.7
out of
5
The furnace is highly efficient and has significantly reduced our energy consumption. I'm pleased with its cost-saving benefits.
4.8
out of
5
The furnace is environmentally friendly and meets all regulatory requirements. I'm happy to contribute to a more sustainable future with this purchase.
4.9
out of
5
The furnace is backed by excellent customer service. The team is responsive and knowledgeable, providing prompt support whenever needed.
4.7
out of
5
The furnace has transformed our production process, leading to increased efficiency and productivity. I highly recommend it to any company looking to upgrade their equipment.
4.9
out of
5
The furnace is an indispensable tool in our research. Its precision and reliability have enabled us to achieve groundbreaking results.
Products
Graphite Vacuum Furnace Bottom Discharge Graphitization Furnace for Carbon Materials
REQUEST A QUOTE
Our professional team will reply to you within one business day. Please feel free to contact us!
Related Products
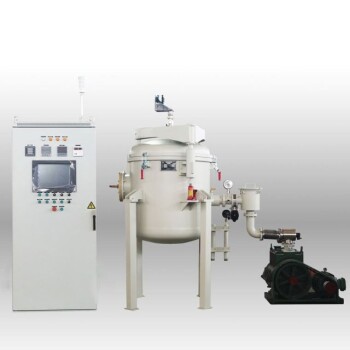
Ultra-High Temperature Graphite Vacuum Graphitization Furnace
The ultra-high temperature graphitization furnace utilizes medium frequency induction heating in a vacuum or inert gas environment. The induction coil generates an alternating magnetic field, inducing eddy currents in the graphite crucible, which heats up and radiates heat to the workpiece, bringing it to the desired temperature. This furnace is primarily used for graphitization and sintering of carbon materials, carbon fiber materials, and other composite materials.
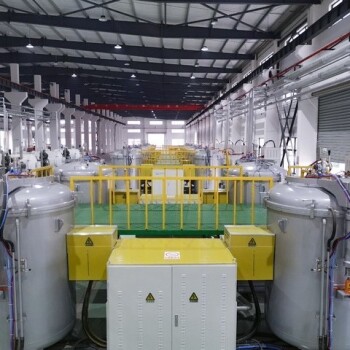
Vertical High Temperature Graphite Vacuum Graphitization Furnace
Vertical high temperature graphitization furnace for carbonization and graphitization of carbon materials up to 3100℃.Suitable for shaped graphitization of carbon fiber filaments and other materials sintered in a carbon environment.Applications in metallurgy, electronics, and aerospace for producing high-quality graphite products like electrodes and crucibles.
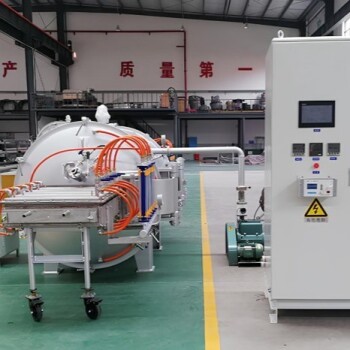
Graphite Vacuum Continuous Graphitization Furnace
High-temperature graphitization furnace is a professional equipment for graphitization treatment of carbon materials. It is a key equipment for the production of high-quality graphite products. It has high temperature, high efficiency and uniform heating. It is suitable for various high-temperature treatments and graphitization treatments. It is widely used in metallurgy, electronics, aerospace, etc. industry.
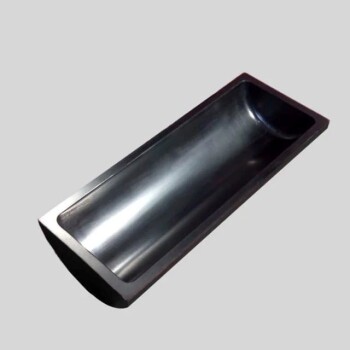
Carbon Graphite Boat -Laboratory Tube Furnace with Cover
Covered Carbon Graphite Boat Laboratory Tube Furnaces are specialized vessels or vessels made of graphite material designed to withstand extreme high temperatures and chemically aggressive environments.
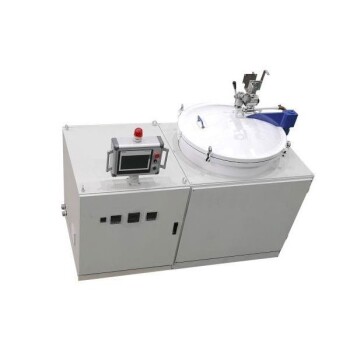
Graphite Vacuum Furnace IGBT Experimental Graphitization Furnace
IGBT experimental graphitization furnace, a tailored solution for universities and research institutions, with high heating efficiency, user-friendliness, and precise temperature control.
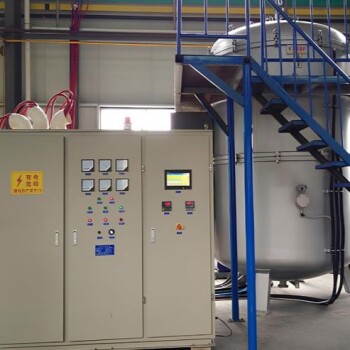
Large Vertical Graphite Vacuum Graphitization Furnace
A large vertical high-temperature graphitization furnace is a type of industrial furnace used for the graphitization of carbon materials, such as carbon fiber and carbon black. It is a high-temperature furnace that can reach temperatures of up to 3100°C.
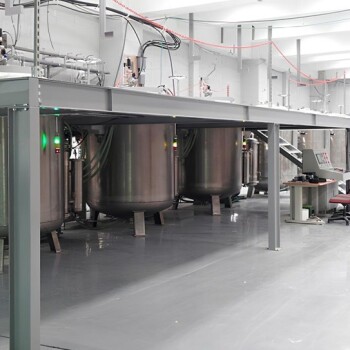
Graphite Vacuum Furnace Negative Material Graphitization Furnace
Graphitization furnace for battery production has uniform temperature and low energy consumption. Graphitization furnace for negative electrode materials: an efficient graphitization solution for battery production and advanced functions to enhance battery performance.
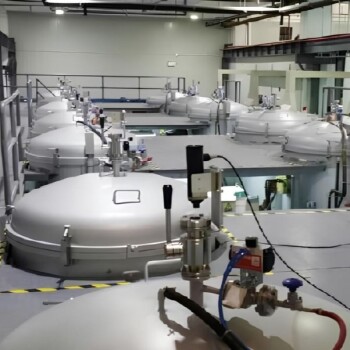
Graphite Vacuum Furnace High Thermal Conductivity Film Graphitization Furnace
The high thermal conductivity film graphitization furnace has uniform temperature, low energy consumption and can operate continuously.
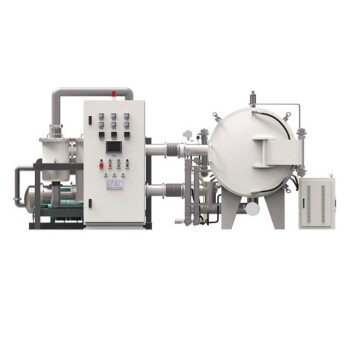
Horizontal High Temperature Graphite Vacuum Graphitization Furnace
Horizontal Graphitization Furnace: This type of furnace is designed with the heating elements placed horizontally, allowing for uniform heating of the sample. It's well-suited for graphitizing large or bulky samples that require precise temperature control and uniformity.
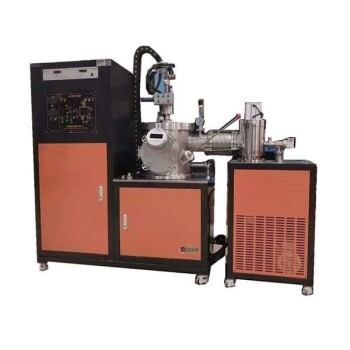
Vacuum Arc Induction Melting Furnace
Discover the power of Vacuum Arc Furnace for melting active & refractory metals. High-speed, remarkable degassing effect, and free of contamination. Learn more now!
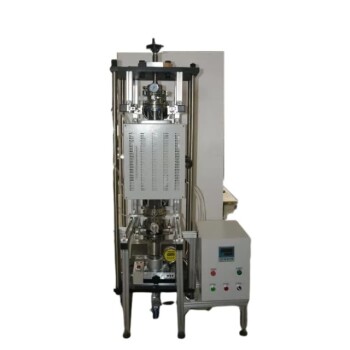
Vacuum Hot Press Furnace Heated Vacuum Press Machine Tube Furnace
Reduce forming pressure & shorten sintering time with Vacuum Tube Hot Press Furnace for high-density, fine-grain materials. Ideal for refractory metals.
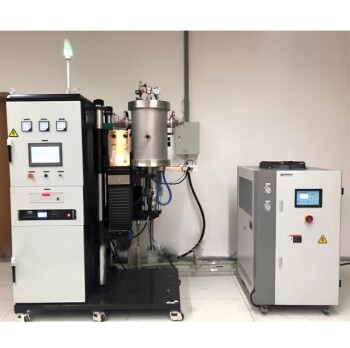
Vacuum Heat Treat and Molybdenum Wire Sintering Furnace for Vacuum Sintering
A vacuum molybdenum wire sintering furnace is a vertical or bedroom structure, which is suitable for withdrawal, brazing, sintering and degassing of metal materials under high vacuum and high temperature conditions. It is also suitable for dehydroxylation treatment of quartz materials.
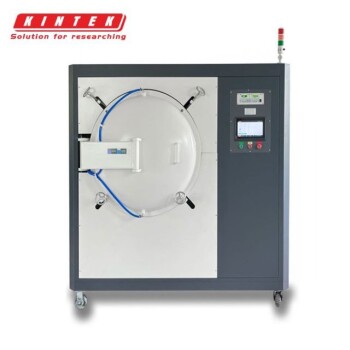
Vacuum Heat Treat Furnace with Ceramic Fiber Liner
Vacuum furnace with polycrystalline ceramic fiber insulation liner for excellent heat insulation and uniform temperature field. Choose from 1200℃ or 1700℃ max. working temperature with high vacuum performance and precise temperature control.
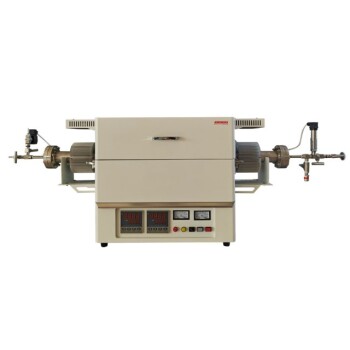
High Pressure Laboratory Vacuum Tube Furnace Quartz Tubular Furnace
KT-PTF High Pressure Tube Furnace: Compact split tube furnace with strong positive pressure resistance. Working temp up to 1100°C and pressure up to 15Mpa. Also works under controller atmosphere or high vacuum.
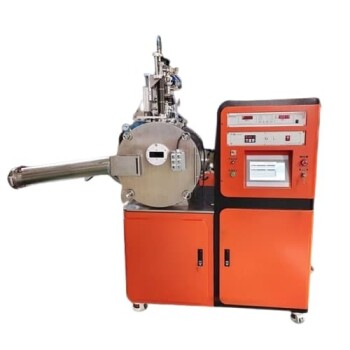
Vacuum Induction Melting Spinning System Arc Melting Furnace
Develop metastable materials with ease using our Vacuum Melt Spinning System. Ideal for research and experimental work with amorphous and microcrystalline materials. Order now for effective results.
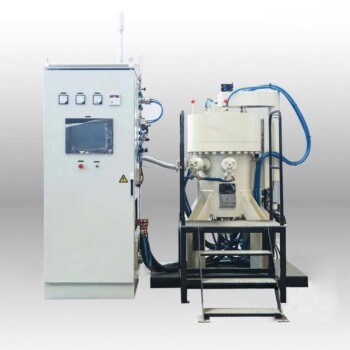
Vacuum Heat Treat and Sintering Furnace with 9MPa Air Pressure
The air pressure sintering furnace is a high-tech equipment commonly used for the sintering of advanced ceramic materials. It combines vacuum sintering and pressure sintering techniques to achieve high-density and high-strength ceramics.
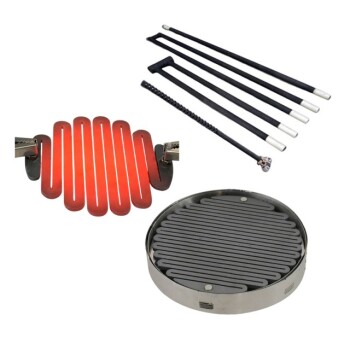
Silicon Carbide SiC Thermal Heating Elements for Electric Furnace
Experience the advantages of Silicon Carbide (SiC) Heating Element: Long service life, high corrosion and oxidation resistance, fast heating speed, and easy maintenance. Learn more now!
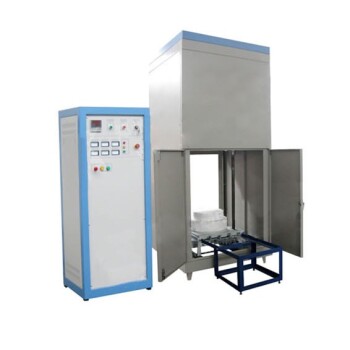
Laboratory Muffle Oven Furnace Bottom Lifting Muffle Furnace
Efficiently produce batches with excellent temperature uniformity using our Bottom Lifting Furnace. Features two electric lifting stages and advanced temperature control up to 1600℃.
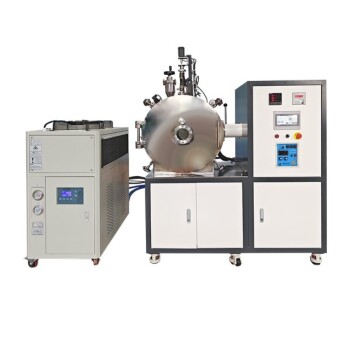
Lab-Scale Vacuum Induction Melting Furnace
Get precise alloy composition with our Vacuum Induction Melting Furnace. Ideal for aerospace, nuclear energy, and electronic industries. Order now for effective smelting and casting of metals and alloys.
Related Articles
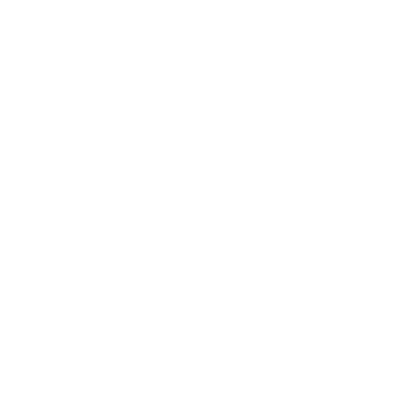
Guide to Bottom Loading Furnace
A bottom loading furnace is a type of industrial furnace that is designed for the efficient processing of materials by heating them to high temperatures.
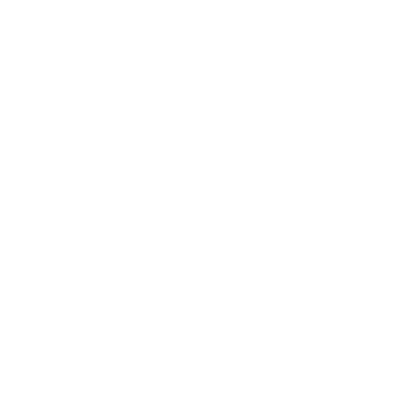
What is activated carbon regeneration Rotary Furnace
Electric activated carbon regeneration furnace is one typical electric external heating rotary furnace
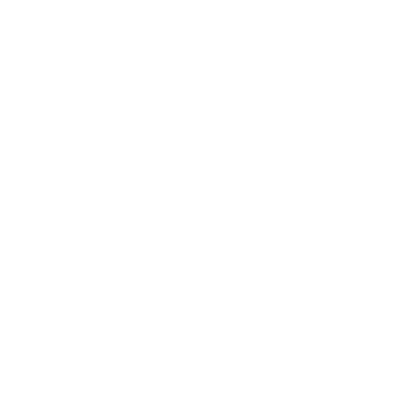
Guide To QUENCHING FURNACE
A quenching furnace is a type of heat treatment furnace that is commonly used in industrial production. It is used to harden or temper materials, and plays an important role in the production process. Quenching furnaces are available in a variety of sizes and configurations, and can be custom-designed to meet the specific needs of the application.
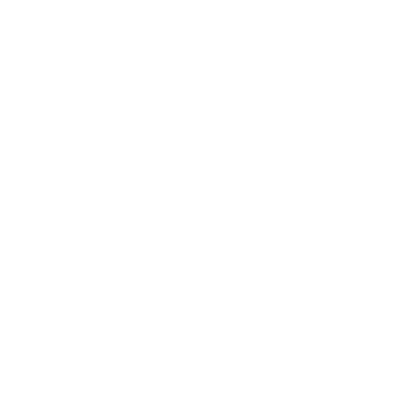
Optimizing Performance with Graphite Vacuum Furnaces: A Comprehensive Guide
Unlock the potential of graphite vacuum furnaces for high-temperature material treatment. Learn about their efficiency, customization options, automation, and key considerations for graphite rod usage.
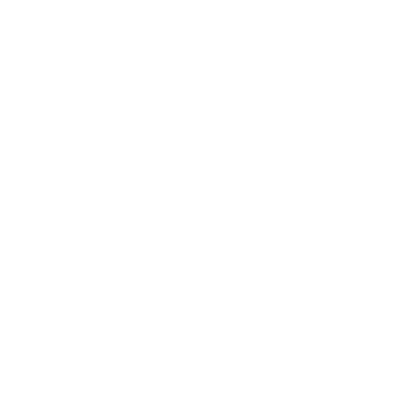
The Advantages and Disadvantages of Different Biomass Feedstocks for Pyrolysis
Different feedstocks have their own unique advantages and disadvantages for pyrolysis, which must be carefully considered when selecting the most suitable feedstock for a particular application.
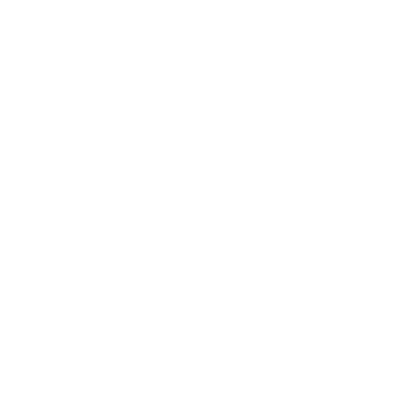
Common Problems and Considerations in Graphite Rods for Vacuum Sintering Furnaces
Discusses the selection, performance, installation, and maintenance of graphite rods in vacuum sintering furnaces.
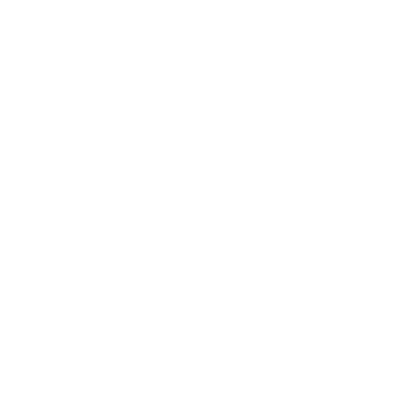
Advances in Carburizing Technology: Conventional vs. Low Pressure Vacuum Carburizing
This article compares conventional carburizing with low-pressure vacuum carburizing, highlighting their differences and advantages.