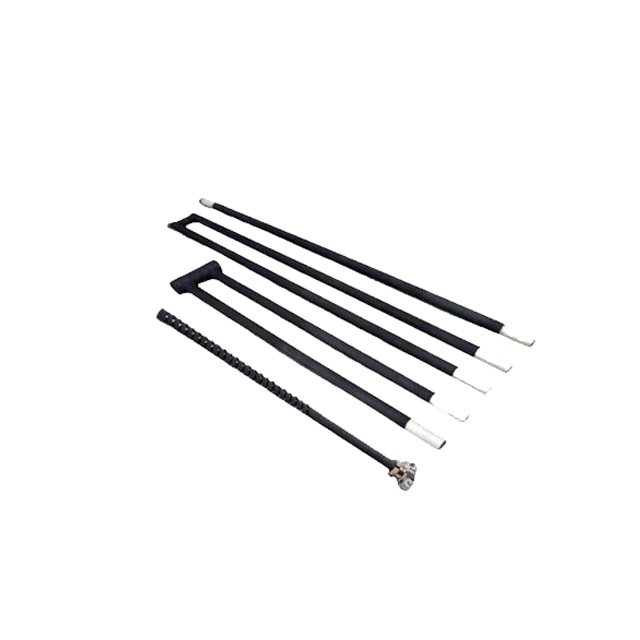
Thermal Elements
Silicon Carbide SiC Thermal Heating Elements for Electric Furnace
Item Number : KT-SH
Price varies based on specs and customizations
- Bulk Density
- 2.5 g/cm3
- Porosity
- 23%
- Thermal Conductivity
- 14-19 W/m·℃ (1000℃)
- Rupture Strength
- 50Mpa(25℃)
- Specific Heat
- 1.0 kj/kg·℃(25~1300℃)
- Coefficient Of Thermal Expansion
- 4.5×10-⁶
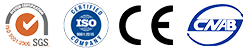
Shipping:
Contact us to get shipping details Enjoy On-time Dispatch Guarantee.
Why Choose Us
Reliable PartnerEasy ordering process, quality products, and dedicated support for your business success.
Introduction
Silicon carbide (SiC) heating elements are high-temperature ceramic components used in electric furnaces, renowned for their high electrical conductivity and resistance to extreme temperatures. Made of silicon and carbon, these elements are formed through a recrystallization process at temperatures exceeding 2150°C, resulting in a long service life and high energy efficiency. SiC heaters are versatile and available in various configurations for applications ranging from 600°C to 1600°C, making them an ideal choice for industries such as metallurgy, ceramics, and semiconductor manufacturing.
Applications
Silicon carbide heating elements are widely used in machinery, metallurgy, light chemical industry, ceramics, semiconductors, analytical testing, and scientific research. They serve as electric heating elements for various electric furnaces, such as tunnel kilns, roller hearth kilns, glass kilns, vacuum furnaces, muffle furnaces, smelting furnaces, and various other heating equipment. Key applications for silicon carbide heating elements are as follows:
- Metallurgy: Silicon carbide heating elements are crucial in the production and processing of metals due to the high temperatures required for smelting and refining.
- Ceramics: In the ceramics industry, these elements are used in the firing and sintering processes, ensuring uniform heating and a high-quality end product.
- Glassmaking: Silicon carbide heating elements play a vital role in the melting and forming of glass, which requires sustained high temperatures.
- Chemical Processing: They are used in chemical reactors and processing equipment that require a controlled, high-temperature environment.
- Laboratory Furnaces: In scientific research and analytical testing, SiC elements are integral to laboratory furnaces used for a variety of high-temperature experiments and tests.
- Semiconductor Manufacturing: The precise temperature control provided by SiC heating elements is essential for the production of semiconductors and other electronic components.
- Environmental Testing: These elements are used in environmental test chambers to simulate extreme temperature conditions for product durability testing.
- Food Processing: In the food industry, silicon carbide heating elements are used in ovens and other equipment that requires high-temperature processing.
Details and Parts
Different Types of Silicon Carbide (SiC) Heating Elements
Advantages
Silicon carbide (SiC) heating elements offer numerous advantages, making them ideal for a variety of heating applications. These elements are made of a hard ceramic compound called silicon carbide, which offers high conductivity and exceptional durability. Here are some of the key advantages of using SiC heating elements:
- High-Temperature Performance: Silicon carbide heating elements operate efficiently in a temperature range of 600°C to 1600°C, making them ideal for high-temperature furnaces and processes.
- Energy Efficiency: These elements have low resistance at the hot end, which reduces wasted heat and improves the overall efficiency of the heating system, saving energy.
- Long Service Life: Due to their robust ceramic construction, silicon carbide heating elements offer a longer service life than other types of heating elements, especially in corrosive environments.
- Precise Temperature Control: The ability to precisely control and maintain temperature is crucial in many industrial processes. Silicon carbide elements provide more precise, controlled heat, improving product quality and consistency.
- Safety and Environmental Benefits: Using silicon carbide heating elements eliminates the need for fume exhaust, improving the safety and environmental impact of heating processes. This also contributes to a more comfortable working environment.
- Design Versatility: SiC heating elements are available in eight different basic configurations, allowing them to be customized for specific applications, extending their service life and effectiveness, especially in challenging environments.
- Cost-Effectiveness: Although initially more expensive than other heating elements, such as MoSi2, SiC elements offer long-term savings due to their energy efficiency and extended service life, thereby reducing overall operating costs.
- Enhanced Power Radiance: Silicon carbide heating elements can radiate higher power, which is beneficial for processes requiring rapid heating or high-temperature stability.
Features
The continuous-duty electrically heated pyrolysis furnace is a precision device designed specifically for continuous pyrolysis processes. It incorporates a range of features that enhance its functionality while ensuring operational safety, efficiency, and longevity. Key features include an extended service life, an internal rotation mechanism for continuous operation, and an advanced control system for safe and efficient management of the pyrolysis process.
- Extended Operating Life: The furnace utilizes indirect hot air to heat the reactor, significantly reducing damage and extending the equipment's service life.
- Internal Rotation for Optimal, Constant Operation: Unlike external rotating systems that require frequent seal material replacement, this furnace utilizes internal rotation technology.
- Advanced Control and Monitoring System: The furnace is equipped with an integrated control loop for real-time monitoring of key parameters. Additionally, improved burner management and automatic decoking further enhance furnace reliability and safety.
Characteristics
Physical Properties
Property | Value |
---|---|
Bulk Density | 2.5 g/cm³ |
Porosity | 23% |
Thermal Conductivity | 14-19 W/m·°C (1000°C) |
Fracture Strength | 50 MPa (25°C) |
Specific Heat | 1.0 kJ/kg·°C (25-1300°C) |
Thermal Expansion Coefficient | $4.5 \times 10^{-6}$ |
Chemical Properties
Silicon carbide heating elements are chemically stable and resistant to acids. However, alkaline substances can attack them at high temperatures.
Long-term use of silicon carbide components above 1000°C will cause the following effects when exposed to oxygen and water vapor:
① $SiC + 2O_2 \rightarrow SiO_2 + CO_2$ ② $SiC + 4H_2O = SiO_2 + 4H_2 + CO_2$
This gradually increases the $SiO_2$ content in the component, slowly increasing its resistance and leading to aging. Excessive water vapor accelerates SiC oxidation. The $H_2$ generated in reaction ② combines with $O_2$ in the air to form $H_2O$, creating a vicious cycle that shortens component life. Hydrogen ($H_2$) can reduce the mechanical strength of the component. Nitrogen ($N_2$) prevents SiC oxidation below 1200°C. However, above 1350°C, it reacts with SiC, decomposing it to produce chlorine ($Cl_2$), which completely decomposes it.
How to specify the model number of a silicon carbide (SiC) heating element?
The model number for a silicon carbide (SiC) heating element is specified based on its dimensions and resistance.
- OD: Outer Diameter
- HZ: Hot Zone Length
- CZ: Cold Zone Length
- OL: Total Length
For example: An SCR type with OD = 8mm, HZ = 100mm, CZ = 130mm, OL = 230mm, and a resistance of 4.46 ohms would be specified as: 8*100*230/4.46 ohms.
Available Ranges of SiC Heating Elements
OD (mm) | HZ (mm) | CZ (mm) | OL (mm) | Resistance (ohms) |
---|---|---|---|---|
8 | 100-300 | 60-200 | 240-700 | 2.1-8.6 |
12 | 100-400 | 100-350 | 300-1100 | 0.8-5.8 |
14 | 100-500 | 150-350 | 400-1200 | 0.7-5.6 |
16 | 200-600 | 200-350 | 600-1300 | 0.7-4.4 |
18 | 200-800 | 200-400 | 600-1600 | 0.7-5.8 |
20 | 200-800 | 250-600 | 700-2000 | 0.6-6.0 |
25 | 200-1200 | 250-700 | 700-2600 | 0.4-5.0 |
30 | 300-2000 | 250-800 | 800-3600 | 0.4-4.0 |
35 | 400-2000 | 250-800 | 900-3600 | 0.5-3.6 |
40 | 500-2700 | 250-800 | 1000-4300 | 0.5-3.4 |
45 | 500-3000 | 250-750 | 1000-4500 | 0.3-3.0 |
50 | 600-2500 | 300-750 | 1200-4000 | 0.3-2.5 |
54 | 600-2500 | 300-750 | 1200-4000 | 0.3-3.0 |
Installation Precautions
Click here to view precautions for installing silicon carbide rods.
Warnings
Operator safety is the top important issue! Please operate the equipment with cautions. Working with inflammable& explosive or toxic gases is very dangerous, operators must take all necessary precautions before starting the equipment. Working with positive pressure inside the reactors or chambers is dangerous, operator must fellow the safety procedures strictly. Extra caution must also be taken when operating with air-reactive materials, especially under vacuum. A leak can draw air into the apparatus and cause a violent reaction to occur.
Designed for You
KinTek provide deep custom made service and equipment to worldwide customers, our specialized teamwork and rich experienced engineers are capable to undertake the custom tailoring hardware and software equipment requirements, and help our customer to build up the exclusive and personalized equipment and solution!
Would you please drop your ideas to us, our engineers are ready for you now!
FAQ
What Is A Thermal Element?
How Does A Thermal Element Work?
What Are The Advantages Of Using Thermal Elements?
What Are The Different Types Of Thermal Elements?
How Should Thermal Elements Be Calibrated And Maintained?
4.9
out of
5
Speedy delivery, excellent quality, and top-notch customer service. Thank you!
4.8
out of
5
The SiC heating element is a game-changer for our lab. It's efficient, durable, and has significantly improved our productivity.
4.7
out of
5
I'm impressed with the performance and longevity of this heating element. It's a reliable workhorse in our lab.
5.0
out of
5
Exceptional product! The SiC heating element delivers consistent results and has exceeded our expectations.
4.9
out of
5
Great value for money. The heating element is well-made and has held up well in our demanding lab environment.
4.8
out of
5
The SiC heating element is a reliable and efficient addition to our lab equipment. Highly recommended!
5.0
out of
5
Outstanding product! The heating element's durability and performance are unmatched. We're very satisfied with our purchase.
4.9
out of
5
The SiC heating element has proven to be an excellent investment. It's a high-quality product that delivers exceptional results.
4.7
out of
5
This heating element is a solid performer. It's easy to install and maintain, and it has met all our requirements.
5.0
out of
5
We're thrilled with the SiC heating element. It has significantly improved the efficiency of our lab processes.
4.8
out of
5
The heating element arrived promptly and was exactly as described. It's a great addition to our lab setup.
4.9
out of
5
The SiC heating element is a reliable workhorse. It's been operating flawlessly since we installed it.
4.7
out of
5
We're very satisfied with the performance of the heating element. It's a durable and efficient piece of equipment.
5.0
out of
5
The SiC heating element has exceeded our expectations. It's a top-quality product that has enhanced our lab's capabilities.
4.9
out of
5
We highly recommend the SiC heating element. It's a valuable addition to any lab.
Products
Silicon Carbide SiC Thermal Heating Elements for Electric Furnace
REQUEST A QUOTE
Our professional team will reply to you within one business day. Please feel free to contact us!
Related Products
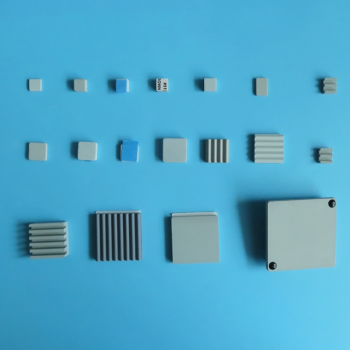
Silicon Carbide (SIC) Ceramic Sheet Flat Corrugated Heat Sink for Engineering Advanced Fine Ceramics
Silicon carbide (sic) ceramic heat sink not only does not generate electromagnetic waves, but also can isolate electromagnetic waves and absorb part of electromagnetic waves.

Silicon Carbide (SIC) Ceramic Sheet Wear-Resistant Engineering Advanced Fine Ceramics
Silicon carbide (sic) ceramic sheet is composed of high-purity silicon carbide and ultra-fine powder, which is formed by vibration molding and high-temperature sintering.
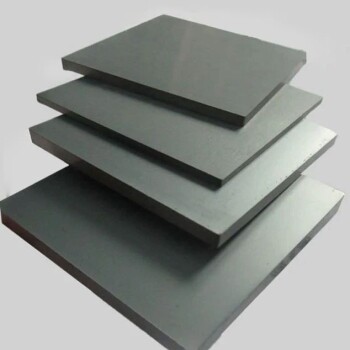
Silicon Carbide (SIC) Ceramic Plate for Engineering Advanced Fine Ceramics
Silicon nitride (sic) ceramic is an inorganic material ceramic that does not shrink during sintering. It is a high-strength, low-density, high-temperature-resistant covalent bond compound.
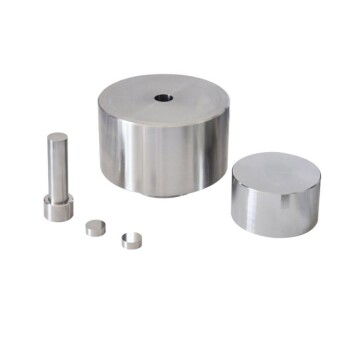
Anti-Cracking Press Mold for Lab Use
The anti-cracking press mold is a specialized equipment designed for molding various shapes and sizes of film using high pressure and electric heating.
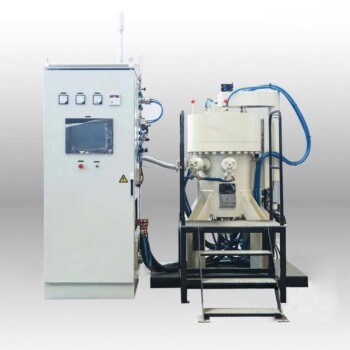
Vacuum Heat Treat and Sintering Furnace with 9MPa Air Pressure
The air pressure sintering furnace is a high-tech equipment commonly used for the sintering of advanced ceramic materials. It combines vacuum sintering and pressure sintering techniques to achieve high-density and high-strength ceramics.
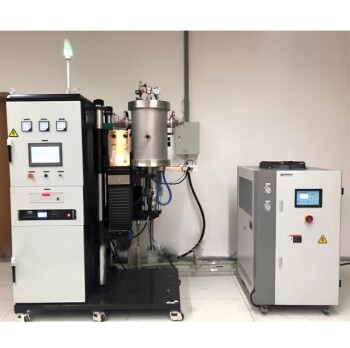
Vacuum Heat Treat and Molybdenum Wire Sintering Furnace for Vacuum Sintering
A vacuum molybdenum wire sintering furnace is a vertical or bedroom structure, which is suitable for withdrawal, brazing, sintering and degassing of metal materials under high vacuum and high temperature conditions. It is also suitable for dehydroxylation treatment of quartz materials.
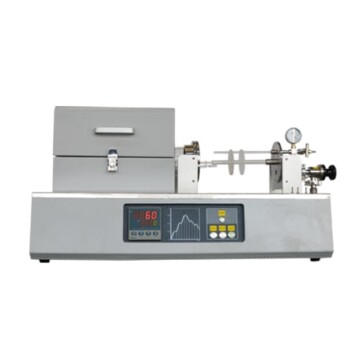
Laboratory Quartz Tube Furnace Tubular RTP Heating Furnace
Get lightning-fast heating with our RTP Rapid Heating Tube Furnace. Designed for precise, high-speed heating and cooling with convenient sliding rail and TFT touch screen controller. Order now for ideal thermal processing!
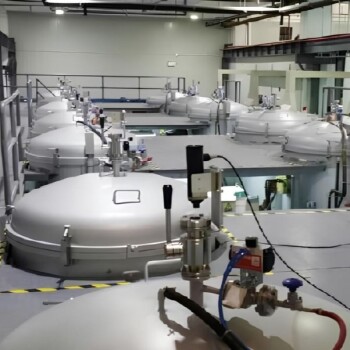
Graphite Vacuum Furnace High Thermal Conductivity Film Graphitization Furnace
The high thermal conductivity film graphitization furnace has uniform temperature, low energy consumption and can operate continuously.
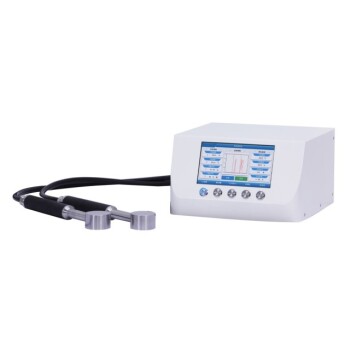
Infrared Heating Quantitative Flat Plate Press Mold
Discover advanced infrared heating solutions with high-density insulation and precise PID control for uniform thermal performance in various applications.
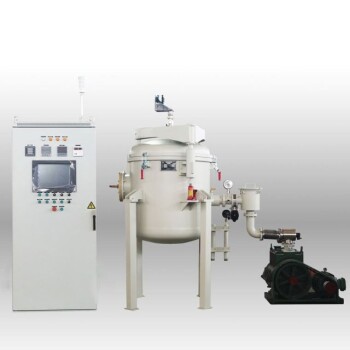
Ultra-High Temperature Graphite Vacuum Graphitization Furnace
The ultra-high temperature graphitization furnace utilizes medium frequency induction heating in a vacuum or inert gas environment. The induction coil generates an alternating magnetic field, inducing eddy currents in the graphite crucible, which heats up and radiates heat to the workpiece, bringing it to the desired temperature. This furnace is primarily used for graphitization and sintering of carbon materials, carbon fiber materials, and other composite materials.
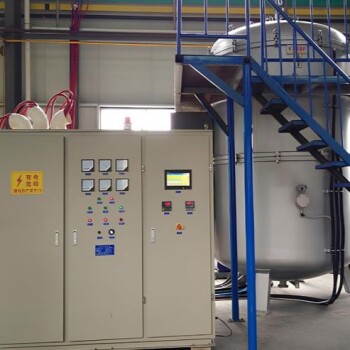
Large Vertical Graphite Vacuum Graphitization Furnace
A large vertical high-temperature graphitization furnace is a type of industrial furnace used for the graphitization of carbon materials, such as carbon fiber and carbon black. It is a high-temperature furnace that can reach temperatures of up to 3100°C.

Graphite Vacuum Furnace Bottom Discharge Graphitization Furnace for Carbon Materials
Bottom-out graphitization furnace for carbon materials, ultra-high temperature furnace up to 3100°C, suitable for graphitization and sintering of carbon rods and carbon blocks. Vertical design, bottom discharging, convenient feeding and discharging, high temperature uniformity, low energy consumption, good stability, hydraulic lifting system, convenient loading and unloading.
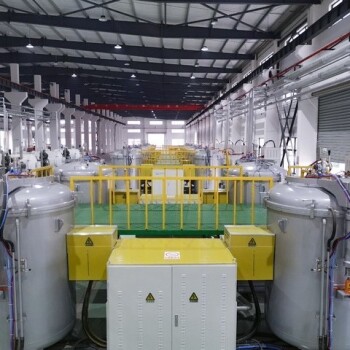
Vertical High Temperature Graphite Vacuum Graphitization Furnace
Vertical high temperature graphitization furnace for carbonization and graphitization of carbon materials up to 3100℃.Suitable for shaped graphitization of carbon fiber filaments and other materials sintered in a carbon environment.Applications in metallurgy, electronics, and aerospace for producing high-quality graphite products like electrodes and crucibles.
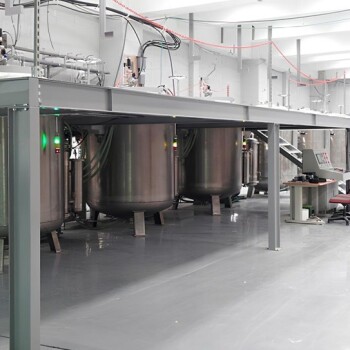
Graphite Vacuum Furnace Negative Material Graphitization Furnace
Graphitization furnace for battery production has uniform temperature and low energy consumption. Graphitization furnace for negative electrode materials: an efficient graphitization solution for battery production and advanced functions to enhance battery performance.
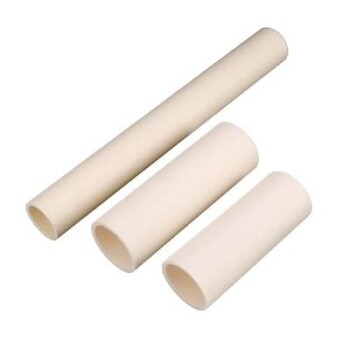
High Temperature Alumina (Al2O3) Furnace Tube for Engineering Advanced Fine Ceramics
High temperature alumina furnace tube combines the advantages of high hardness of alumina, good chemical inertness and steel, and has excellent wear resistance, thermal shock resistance and mechanical shock resistance.
Electric Rotary Kiln Continuous Working Small Rotary Furnace Heating Pyrolysis Plant
Efficiently calcine and dry bulk powder and lump fluid materials with an electric heating rotary furnace. Ideal for processing lithium ion battery materials and more.
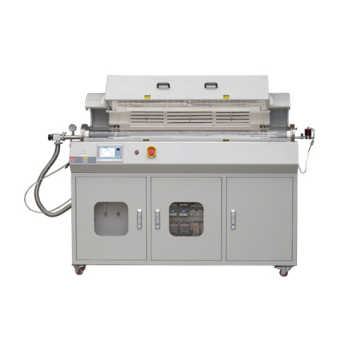
Rotary Tube Furnace Split Multi Heating Zone Rotating Tube Furnace
Multi zone rotary furnace for high-precision temperature control with 2-8 independent heating zones. Ideal for lithium ion battery electrode materials and high-temperature reactions. Can work under vacuum and controlled atmosphere.
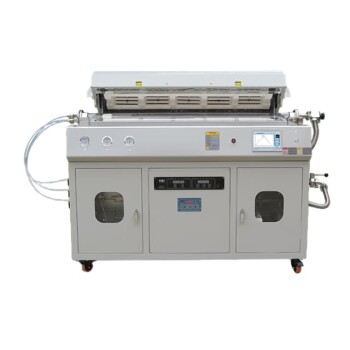
Multi Heating Zones CVD Tube Furnace Machine Chemical Vapor Deposition Chamber System Equipment
KT-CTF14 Multi Heating Zones CVD Furnace - Precise Temperature Control and Gas Flow for Advanced Applications. Max temp up to 1200℃, 4 channels MFC mass flow meter, and 7" TFT touch screen controller.
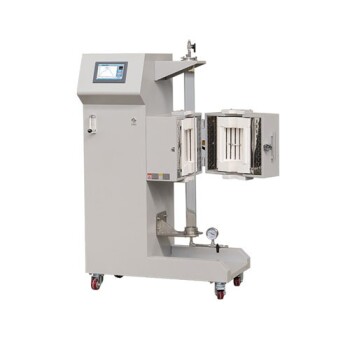
Vertical Laboratory Quartz Tube Furnace Tubular Furnace
Elevate your experiments with our Vertical Tube Furnace. Versatile design allows for operation under various environments and heat treatment applications. Order now for precise results!
Related Articles
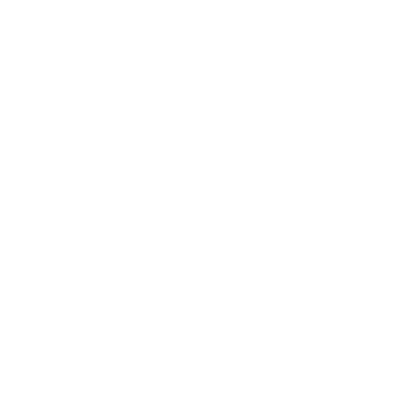
Precautions for installing silicon carbide stick
Precautions for installing silicon carbide stic.
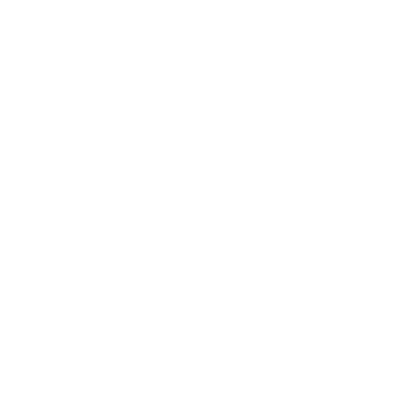
Dos and don'ts during the installation of molybdenum disilicide (MoSi2) heating element
Precautions when installing MoSi2 heating elements
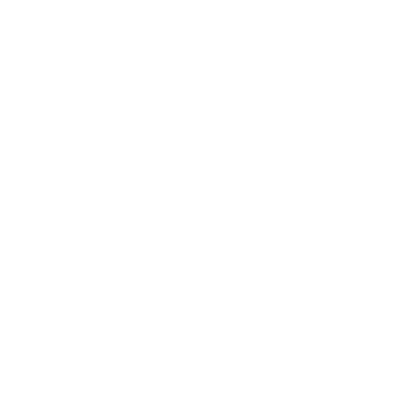
How to Maintain Your Dental Ceramic Furnace
The dental furnaces are expensive and require regular maintenance to ensure they function properly and produce accurate results.
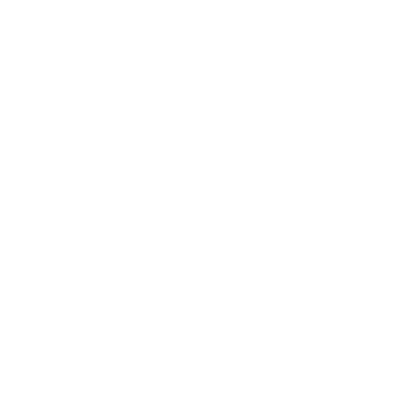
Understanding Electric Heating Systems(2): From Furnaces to Heating Elements
Discover how electric heating systems work, from electric furnaces to heating element basics. Learn about the benefits of electric heating and why it's a viable option for various applications. Find insights on heat treating furnaces and their subassemblies.
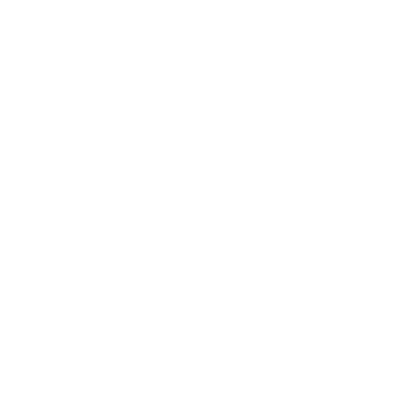
Optimizing Performance with Graphite Vacuum Furnaces: A Comprehensive Guide
Unlock the potential of graphite vacuum furnaces for high-temperature material treatment. Learn about their efficiency, customization options, automation, and key considerations for graphite rod usage.
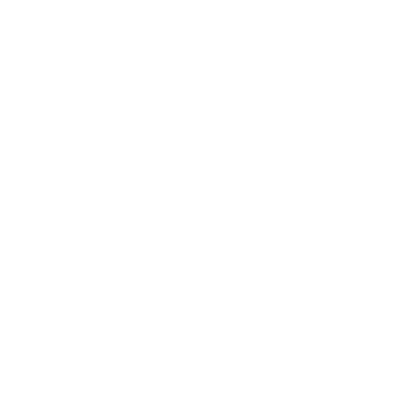
Electric Heating Systems(3): Understanding, Benefits, and Applications
Explore the world of electric heating systems, including electric furnaces, heating elements, and their benefits. Learn about the advantages, disadvantages, and applications of electric heating technology. Discover how electric heating systems work and their role in modern heating solutions.
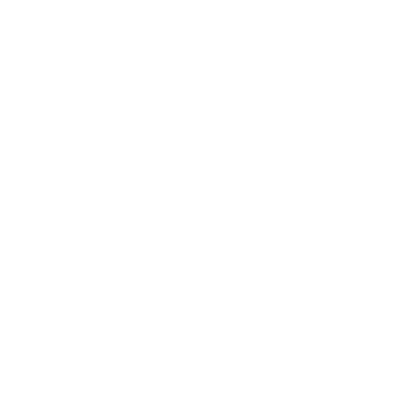
Effective Maintenance Strategies for Vertical Tubular Electric Furnaces
There are several key areas to focus on when it comes to maintaining a multi temperature zone vertical tubular electric furnace.
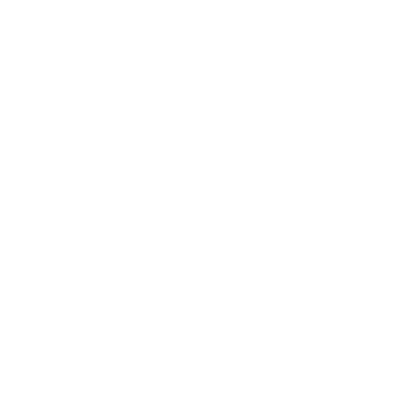
Investigating the Factors Affecting the Slow Temperature Rise in Box Furnaces
Sometimes, the temperature of the furnace may not rise as quickly as expected, or may not be able to reach the desired temperature at all.
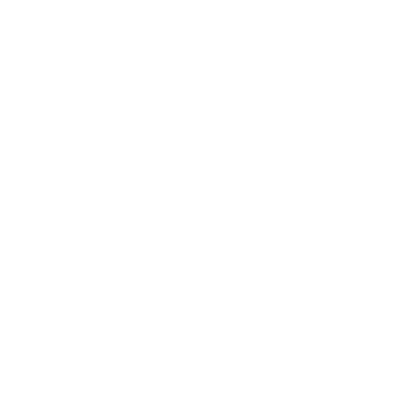
Precision Ceramic Materials for Energy Conversion Applications
Overview of various ceramic materials used in energy conversion technologies, including heaters, piezoelectric ceramics, and solid oxide fuel cells.
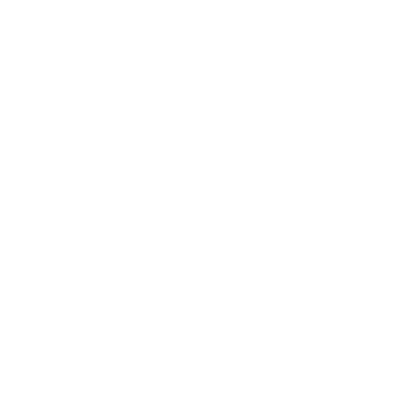
Precision Ceramics in Semiconductor Applications
Exploring the use of precision ceramics in semiconductor equipment, their properties, and manufacturing processes.
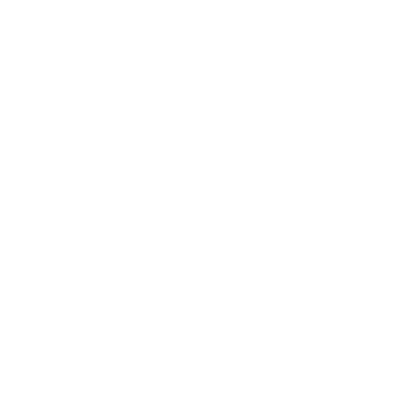
Technical Overview of Silicon-Carbon Anode Materials Prepared by CVD Method
This article discusses the key technical aspects of silicon-carbon anode materials prepared via CVD, focusing on their synthesis, performance improvements, and industrial application potential.
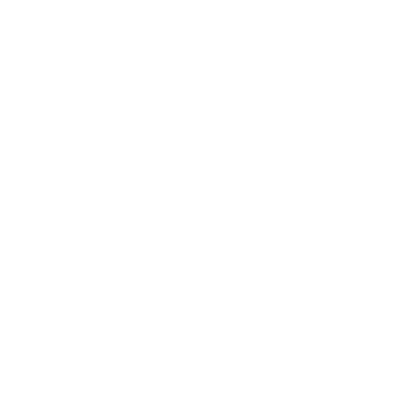
Comprehensive Guide to Muffle Furnace Resistance Wire Design
Detailed analysis of resistance wire design principles, parameters, and calculation techniques for muffle furnace applications.