Introduction to Vapor Deposition Silicon-Carbon (VPD-SiC)
Advantages of VPD-SiC
VPD-SiC demonstrates substantial enhancements over conventional materials in several critical areas, making it a superior choice for advanced battery applications. Firstly, the first turn efficiency of VPD-SiC is notably higher, which translates to more effective initial charge-discharge cycles and reduced energy loss. This improvement is pivotal for the rapid deployment of high-performance batteries in various industries.
Additionally, VPD-SiC significantly boosts energy density. By integrating silicon particles within a porous carbon matrix, the material can store more energy per unit volume or mass, offering longer operational times and reduced charging frequencies. This is particularly advantageous for portable electronics, electric vehicles, and renewable energy storage systems.
The cycling performance of VPD-SiC is also superior, with enhanced stability over repeated charge-discharge cycles. This durability is crucial for the longevity and reliability of battery systems, ensuring consistent performance over extended periods without degradation.
Furthermore, VPD-SiC effectively mitigates cell expansion issues common with traditional silicon-based anodes. This reduction in volume expansion during charging and discharging processes helps maintain the structural integrity of the battery, thereby enhancing its lifespan and safety.
In terms of cost reduction, VPD-SiC offers promising industrialization potential. The streamlined synthesis process, combined with the efficient use of raw materials, can lead to more cost-effective production methods. This economic benefit is essential for scaling up production and making high-performance batteries more accessible.
Overall, VPD-SiC's comprehensive advantages in first turn efficiency, energy density, cycling performance, cell expansion, and cost reduction make it a transformative material for the next generation of battery technologies.
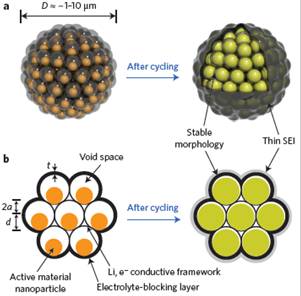
Main Steps in VPD-SiC Technology
The Vapor Phase Deposition (VPD) process for creating silicon-carbon (SiC) anode materials is a multi-stage procedure that integrates several critical steps to achieve high-performance energy storage solutions. The technology can be broken down into three primary phases: the preparation of a porous carbon skeleton, the deposition of silicon particles, and the application of a carbon layer coating.
-
Preparation of Porous Carbon Skeleton:
- The foundation of the VPD-SiC process, the porous carbon skeleton, is meticulously crafted to provide a robust framework that enhances the material's overall performance. This step is essential for creating a structure with high specific surface area and excellent electrical conductivity, which are vital for improving the anode's capacity and cycling stability.
-
Deposition of Silicon Particles:
- Once the porous carbon skeleton is established, the next step involves the deposition of silicon particles within the pores. This is typically achieved through the use of silane gas, which plays a pivotal role in the formation of silicon within the carbon matrix. The deposition process is highly sensitive to parameters such as temperature and gas flow rates, which must be precisely controlled to ensure uniform particle distribution and optimal material properties.
-
Carbon Layer Coating:
- The final step in the VPD-SiC technology is the coating of the silicon-carbon composite with a carbon layer. This layer serves multiple purposes: it protects the silicon particles from degradation, enhances the material's electrical conductivity, and provides additional mechanical stability. The carbon coating is usually applied through chemical vapor deposition (CVD) or other similar techniques, ensuring a uniform and continuous layer that encapsulates the silicon particles effectively.
Each of these steps is interdependent, and their successful integration is crucial for the production of high-quality silicon-carbon anode materials that meet the stringent demands of modern energy storage applications.
Synthesis of Porous Carbon Materials
Importance of Porous Carbon
Porous carbon materials play a pivotal role in the optimization of silicon-carbon anodes, significantly enhancing their overall performance. This enhancement is primarily attributed to several key properties inherent in porous carbon.
Firstly, the high specific surface area of porous carbon provides an extensive platform for the deposition of silicon particles. This large surface area ensures that the silicon particles are evenly distributed, which is crucial for maintaining the structural integrity and performance of the anode.
Secondly, the excellent electrical conductivity of porous carbon facilitates efficient electron transfer within the anode material. This property is vital for maintaining high energy efficiency and reducing internal resistance, which are essential for the long-term performance and durability of the anode.
Lastly, the good mechanical stability of porous carbon contributes to the structural resilience of the anode. This stability is particularly important during the repeated charging and discharging cycles, as it helps to mitigate the volume changes that silicon particles undergo, thereby preventing degradation and prolonging the anode's lifespan.
In summary, the combination of high specific surface area, excellent electrical conductivity, and good mechanical stability makes porous carbon materials indispensable for the advancement of silicon-carbon anodes in battery technology.
Synthesis Considerations
When synthesizing porous carbon materials for silicon-carbon anodes, several critical factors must be meticulously considered to ensure optimal performance and scalability. The design of the pore structure is paramount, as it directly influences the material's ability to accommodate volume changes during lithiation and delithiation cycles. A well-designed pore structure can significantly enhance the anode's cycling stability and capacity retention.
Precursor selection is another pivotal aspect. The choice of precursor material affects not only the final properties of the porous carbon but also the ease of synthesis and the material's cost. Precursors with high carbon yield and low ash content are typically preferred, as they facilitate the formation of a uniform and conductive carbon matrix. Additionally, the precursor should be compatible with scalable production techniques to ensure large-scale manufacturing feasibility.
Scalability for large-scale production is a non-negotiable consideration. The synthesis process must be adaptable to industrial-scale reactors, ensuring consistent quality and yield. This involves optimizing reaction conditions, such as temperature, pressure, and reactant concentrations, to achieve uniform deposition of silicon particles within the porous carbon. Furthermore, the process should minimize energy consumption and waste generation, aligning with sustainable manufacturing practices.
In summary, the synthesis of porous carbon materials for silicon-carbon anodes requires a holistic approach, balancing pore structure design, precursor selection, and scalability to meet the demands of both performance and industrial application.
Silane and Deposition Process
Role of Silane Gas
Silane gas (SiH₄) plays a pivotal role in the deposition of silicon particles within the porous carbon structure, a critical step in the fabrication of silicon-carbon anode materials. The effectiveness of this process hinges on the careful management of silane's properties and the intricate balance of deposition parameters.
One of the primary challenges in using silane is its sensitivity to environmental conditions. For instance, the introduction of oxygen into the deposition chamber can lead to the formation of SiOH, which impairs the quality of the silicon film. Conversely, in the absence of oxygen, amorphous silicon films can be achieved, which are both pure and suitable for deposition. This highlights the necessity of precise control over the deposition environment to prevent unwanted chemical reactions.
Moreover, the cost and availability of silane are significant factors that influence the feasibility of large-scale production. The material must be handled with care due to its reactive nature, which necessitates specialized equipment and safety protocols to mitigate risks. Additionally, the deposition process requires a delicate balance of silane and other gases, such as oxygen and xenon, to achieve the desired silicon-carbon composite.
To optimize the deposition process, it is essential to maintain medium rates of silane introduction. Excess silane can result in the formation of SIH, while an excess of oxygen can lead to SiOH, both of which degrade the quality of the final product. Achieving the right balance is crucial for obtaining silicon films that are both amorphous and hard, which enhances the anode's performance characteristics.
In summary, the role of silane gas in the deposition process is multifaceted, requiring a deep understanding of its chemical properties and careful management of deposition parameters to ensure the production of high-quality silicon-carbon anode materials.
Deposition Process Parameters
The deposition process parameters play a pivotal role in determining the quality and performance of silicon-carbon (Si-C) anode materials. Key parameters include deposition temperature, reaction conditions, and stringent safety measures, each of which significantly influences the final product's characteristics.
Temperature Influence
Deposition temperature is a critical factor that directly affects the uniformity and density of silicon particles within the porous carbon matrix. Higher temperatures can enhance the diffusion of silane gas into the carbon pores, leading to more uniform deposition. However, excessively high temperatures can also cause thermal degradation of the carbon structure, reducing its mechanical stability and specific surface area. Therefore, optimizing the deposition temperature is essential to balance these competing effects.
Reaction Conditions
The reaction conditions, such as gas flow rates and pressure, are equally important. These conditions determine the residence time of the reactants within the deposition chamber and the rate of silicon particle formation. For instance, a higher gas flow rate can lead to shorter residence times, potentially reducing the uniformity of silicon deposition. Conversely, lower flow rates can enhance the deposition process but may also increase the risk of clogging or other operational issues. Thus, precise control of these conditions is necessary to achieve optimal silicon-carbon material properties.
Safety Measures
Given the hazardous nature of silane gas, stringent safety measures are indispensable during the deposition process. These measures include the use of advanced gas detection systems, emergency shutdown protocols, and robust ventilation systems to mitigate the risk of leaks or explosions. Ensuring a safe working environment not only protects personnel but also ensures the reliability and consistency of the deposition process, which is crucial for industrial-scale production.
In summary, the deposition process parameters—temperature, reaction conditions, and safety measures—are intricately linked to the performance and quality of silicon-carbon anode materials. Optimizing these parameters is essential for enhancing the material's electrochemical properties and ensuring its viability for large-scale applications.
Deposition Equipment
Types of Deposition Equipment
Rotary kilns and fluidized beds are the primary types of equipment utilized in the deposition process for silicon-carbon anode materials. Each type of equipment offers distinct advantages and challenges, which are crucial considerations for achieving optimal material properties and scalability.
Rotary Kilns
- Operational Simplicity: Rotary kilns are relatively straightforward in operation, making them a preferred choice for initial experiments and small-scale production.
- Cost-Effective: They are generally more cost-effective in terms of both capital investment and operational costs, which can be beneficial for pilot-scale projects.
- Flexibility: Rotary kilns offer flexibility in handling various precursor materials and can be adapted for different deposition conditions.
Fluidized Beds
- Uniformity and Efficiency: Fluidized beds are renowned for their superior uniformity in particle distribution and higher silane gas utilization rates. This results in more consistent material properties and improved overall performance.
- Enhanced Safety Measures: The use of fluidized beds necessitates stringent safety protocols due to the high reactivity of silane gas. Advanced safety systems and continuous monitoring are essential to mitigate risks associated with gas leaks and other hazards.
- Complexity and Reliability: Despite their advantages, fluidized beds are more complex and require high reliability to ensure continuous and stable operation. This complexity can pose challenges in scaling up for industrial-scale production.
In summary, while rotary kilns provide a simpler and more cost-effective solution, fluidized beds offer enhanced uniformity and efficiency, albeit with increased complexity and safety requirements. The choice of equipment depends on the specific needs and scale of the production process.
Challenges in Industrialization
Large-scale production of silicon-carbon anode materials using fluidized beds presents several significant challenges. These challenges primarily revolve around ensuring continuous operation, maintaining uniformity in the deposition process, and achieving high silane gas utilization.
One of the primary hurdles is the need for equipment and process optimization. Fluidized beds, while offering superior uniformity and silane utilization, require meticulous control over various parameters such as temperature, gas flow rates, and particle size distribution. Any deviation from these optimal conditions can lead to inconsistent material properties, which are detrimental to the overall performance of the anode.
Moreover, the reliability and safety of the fluidized bed system are critical. The use of silane gas, which is highly reactive and potentially explosive, necessitates robust safety measures and continuous monitoring. This adds a layer of complexity to the industrialization process, demanding advanced automation and control systems to ensure safe and efficient operation.
Additionally, the scalability of the fluidized bed process is a significant concern. Transitioning from laboratory-scale experiments to full-scale industrial production requires careful consideration of how to maintain the same level of control and uniformity over larger volumes. This often involves significant capital investment in equipment upgrades and process enhancements.
In summary, while fluidized beds offer promising advantages for the production of silicon-carbon anodes, their industrialization requires overcoming substantial technical and operational challenges. These include equipment and process optimization, ensuring reliability and safety, and addressing scalability issues to achieve large-scale, continuous production.
CONTACT US FOR A FREE CONSULTATION
KINTEK LAB SOLUTION's products and services have been recognized by customers around the world. Our staff will be happy to assist with any inquiry you might have. Contact us for a free consultation and talk to a product specialist to find the most suitable solution for your application needs!