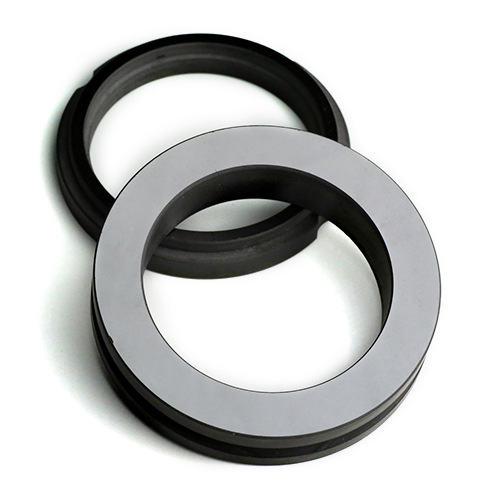
CVD materials
Custom CVD Diamond Coating for Lab Applications
Item Number : cvdm-05
Price varies based on specs and customizations
- Thickness:
- <50μm
- Thickness after polishing:
- <30μm
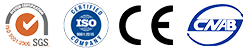
Shipping:
Contact us to get shipping details Enjoy On-time Dispatch Guarantee.
Why Choose Us
Reliable PartnerEasy ordering process, quality products, and dedicated support for your business success.
Introduction
Chemical vapor deposition (CVD) diamond coating is a process for depositing a thin film of diamond onto a substrate. The process involves the deposition of a carbon-containing gas onto a heated substrate in the presence of a hydrogen-containing gas. The carbon atoms in the gas are ionized and accelerated towards the substrate, where they react with the hydrogen atoms to form diamond.
CVD diamond coatings have a number of advantages over natural diamond, including their low friction coefficient, excellent wear resistance, thermal stability, good uniformity, and good adhesion. These properties make CVD diamond coatings ideal for a wide range of applications, including cutting tools, wire drawing dies, acoustic devices, and friction and wear applications.
CVD diamond coatings are typically deposited on a variety of substrates, including silicon, carbide, and metal. The thickness of the coating can be controlled by varying the deposition time and temperature. CVD diamond coatings can be grown with a variety of surface structures, including smooth, faceted, and textured. The surface structure of the coating can be tailored to optimize the film for a given application.
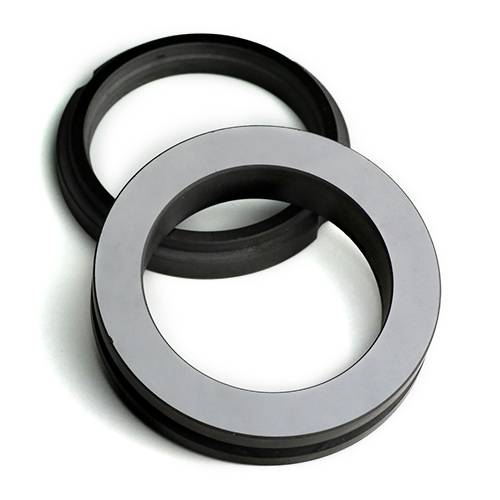
Applications
CVD diamond coating application has a wide range of applications due to its exceptional properties such as low friction coefficient, excellent wear resistance, good thermal stability, uniformity, and adhesion. Some of the main application areas include:
- Diamond thin film coated SiC for sealing applications in harsh environments.
- Diamond thin film coated deep-cavity cemented carbide wire drawing dies with circular cross-section cavities.
- Diamond thin film coated deep-cavity cemented carbide wire drawing dies with irregular-shaped cavities.
- Diamond thin film coated silicon wafer for acoustic applications (high-frequency (GHz) surface acoustic wave (SAW) devices).
- Diamond thin film coatings for friction and wear applications.
Features
The CVD Diamond coating feature offers a range of benefits and features that make it a valuable choice for various applications:
-
Low friction coefficient: This feature reduces friction and wear, leading to improved performance and longer lifespan of tools and components.
-
Excellent wear resistance: The diamond coating provides exceptional resistance to wear and abrasion, making it suitable for applications where durability is critical.
-
Excellent thermal stability: The coating exhibits high thermal stability, enabling it to withstand extreme temperatures without compromising its properties.
-
Good uniformity: The CVD process ensures uniform coating thickness and consistency, resulting in reliable and predictable performance.
-
Good adhesion: The diamond coating adheres strongly to the substrate, ensuring a durable and long-lasting bond.
-
Wide range of surface structures: The CVD process allows for the growth of various surface structures, such as thin and smooth surfaces, thicker films, and faceted surfaces, enabling optimization for specific applications.
Principle
Chemical vapor deposition (CVD) diamond coating is a process in which a diamond film is deposited on a substrate by the chemical reaction of a hydrocarbon gas with atomic hydrogen. The atomic hydrogen is generated by a plasma, which is created by an electric arc or a microwave discharge. The diamond film grows on the substrate by the deposition of carbon atoms from the hydrocarbon gas onto the substrate surface. The properties of the diamond film, such as its thickness, grain size, and surface morphology, can be controlled by varying the process parameters, such as the gas composition, pressure, temperature, and substrate bias.
Advantages
-
Low friction coefficient, significantly reducing friction and wear during use.
-
Excellent wear resistance, extending the service life of tools and components.
-
Excellent thermal stability, maintaining performance even in high-temperature environments.
-
Good uniformity, ensuring consistent coating thickness and properties across the surface.
-
Good adhesion, providing a strong bond between the coating and the substrate.
-
Ability to grow a wide range of surface structures, optimizing the film for specific applications.
-
Can be used on various substrates, including metals, ceramics, and polymers.
-
Chemically inert, making it resistant to corrosion and chemical attack.
-
Biocompatible, making it suitable for medical and biological applications.
Specifications
Vickers hardness: | 8000-10000mm2 |
Young's Modulus: | 1000-1100GPa |
Friction Coefficient: | 0.05-0.1 |
Thickness: | <50μm |
Thickness after polishing: | <30μm |
FAQ
What Are The Main Applications Of Diamond Materials?
What Is CVD (Chemical Vapor Deposition) And What Are Its Key Advantages?
What Is The Unique Advantage Of The CVD Diamond-coating Process?
What Are The Advantages Of Using Diamond Materials In Industrial Applications?
What Are Some Common Applications Of CVD Materials?
What Are The Applications Of CVD Diamond Coating?
What Types Of Diamond Materials Are Available?
What Types Of CVD Materials Are Available?
What Are The Advantages Of CVD Diamond Coating?
What Is The Principle Behind The Use Of Diamond Materials In Cutting Tools?
How Does CVD Diamond Enhance The Performance Of Cutting Tools?
Why Is Synthetic Diamond Preferred Over Natural Diamond In Industrial Applications?
What Makes CVD Diamond Domes Suitable For High-performance Loudspeakers?
How Does CVD Diamond Improve Thermal Management In Electronic Devices?
4.9
out of
5
The CVD Diamond coating has been a game-changer for our laboratory. Its durability and precision have significantly improved our research outcomes.
4.8
out of
5
We were skeptical at first, but the CVD Diamond coating has exceeded our expectations. Its versatility and cost-effectiveness make it an excellent investment.
4.7
out of
5
The CVD Diamond coating has revolutionized our micro-grinding applications. Its fine-grained structure and sharp edges ensure exceptional precision and surface finish.
4.9
out of
5
The CVD Diamond coating's low friction coefficient and wear resistance have drastically reduced maintenance costs and downtime in our laboratory.
4.8
out of
5
The CVD Diamond coating's thermal stability has been a lifesaver in our high-temperature applications. It has significantly reduced tool wear and improved our productivity.
4.7
out of
5
The CVD Diamond coating has opened up new possibilities for our research. Its ability to coat complex geometries has enabled us to create tools with unparalleled precision.
4.9
out of
5
The CVD Diamond coating's uniform thickness and consistency ensure reliable performance and predictable results in our laboratory.
4.8
out of
5
The CVD Diamond coating's strong adhesion to the substrate has eliminated delamination issues and extended the lifespan of our tools.
4.7
out of
5
The CVD Diamond coating's biocompatibility has made it an indispensable tool in our biomedical research.
4.9
out of
5
The CVD Diamond coating's ability to withstand extreme conditions has made it a valuable asset in our harsh environment applications.
4.8
out of
5
The CVD Diamond coating's low friction coefficient has significantly improved the efficiency and accuracy of our cutting operations.
4.7
out of
5
The CVD Diamond coating's excellent wear resistance has reduced tool wear and maintenance costs, saving us time and money.
4.9
out of
5
The CVD Diamond coating's versatility has enabled us to use it in a wide range of applications, from micro-machining to medical devices.
4.8
out of
5
The CVD Diamond coating's high thermal stability has improved the performance and longevity of our tools in high-temperature environments.
4.7
out of
5
The CVD Diamond coating's good adhesion has ensured a strong and durable bond between the coating and the substrate.
4.9
out of
5
The CVD Diamond coating's ability to grow a wide range of surface structures has allowed us to tailor the coating to our specific application needs.
4.8
out of
5
The CVD Diamond coating's chemically inert nature has made it resistant to corrosion and chemical attack, extending its lifespan.
4.7
out of
5
The CVD Diamond coating's biocompatibility has opened up new possibilities for our biomedical research.
4.9
out of
5
The CVD Diamond coating's excellent wear resistance has reduced maintenance costs and downtime, improving our productivity.
Products
Custom CVD Diamond Coating for Lab Applications
REQUEST A QUOTE
Our professional team will reply to you within one business day. Please feel free to contact us!
Related Products
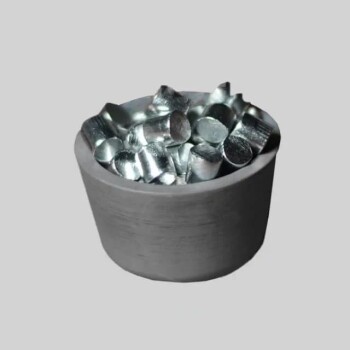
Electron Beam Evaporation Coating Conductive Boron Nitride Crucible BN Crucible
High-purity and smooth conductive boron nitride crucible for electron beam evaporation coating, with high temperature and thermal cycling performance.
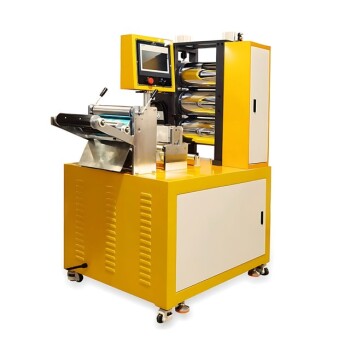
Small Lab Rubber Calendering Machine
Small lab rubber calendering machine is used for producing thin, continuous sheets of plastic or rubber materials. It is commonly employed in laboratories, small-scale production facilities, and prototyping environments to create films, coatings, and laminates with precise thickness and surface finish.
Related Articles
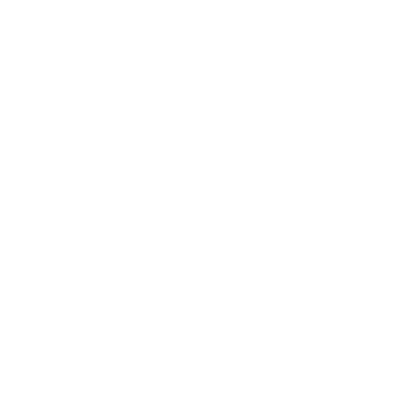
An Introduction to Chemical Vapor Deposition (CVD)
Chemical vapor deposition, or CVD, is a coating process that involves the use of gaseous reactants to produce thin films and coatings of high quality.
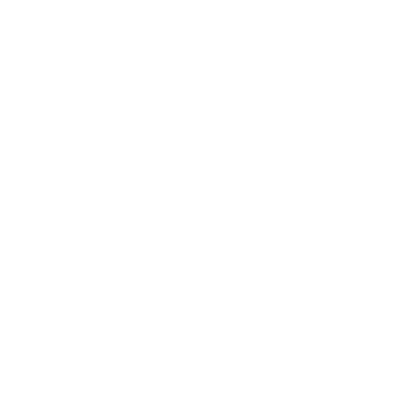
Advantages and Disadvantages of Chemical Vapor Deposition (CVD)
Chemical vapor deposition (CVD) is a versatile thin-film deposition technique widely used in various industries. Explore its advantages, disadvantages, and potential new applications.
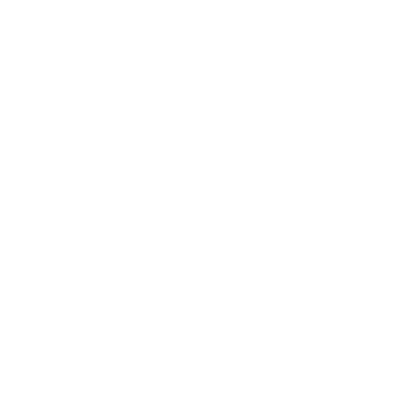
CVD Systems Common Problems and How to Solve Them
Understanding the basics of CVD systems and their importance is crucial for optimizing the process and solving common problems encountered during operation.
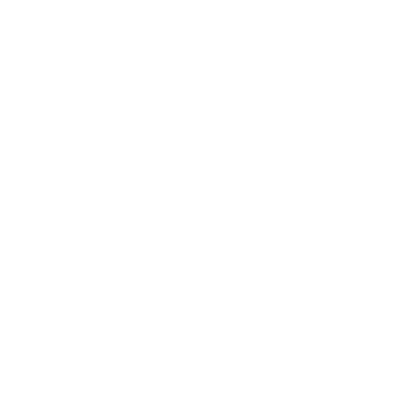
Mastering Handheld Coating Thickness Gauges: A Comprehensive Guide for Industrial and Automotive Applications
Explore the intricacies of handheld coating thickness gauges, their applications in electroplating, automotive paint, and powder coatings. Learn how to choose and use these instruments effectively for quality control and cost efficiency.
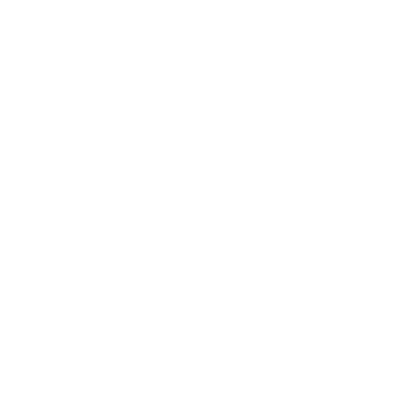
How CVD Coating Can Help You Achieve High Purity and Density
The CVD process offers several advantages over other coating techniques, such as high purity, uniformity, and the ability to deposit coatings with high-density.
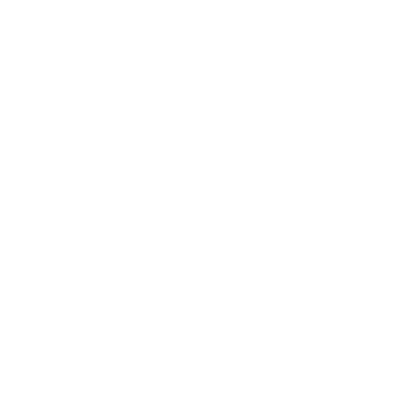
Chemical Vapor Deposition (CVD) of Graphene Challenges and Solutions
Chemical Vapor Deposition (CVD) is a widely adopted method for the production of high-quality graphene.
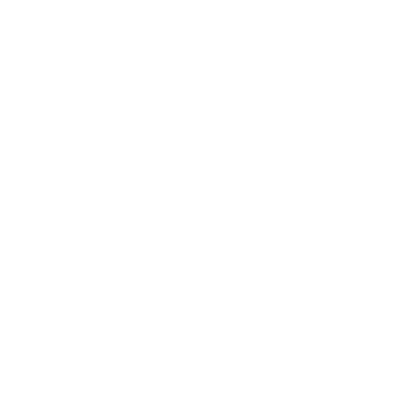
Plasma Enhanced Chemical Vapor Deposition (PECVD): A Comprehensive Guide
Learn everything you need to know about Plasma Enhanced Chemical Vapor Deposition (PECVD), a thin film deposition technique used in the semiconductor industry. Explore its principles, applications, and benefits.
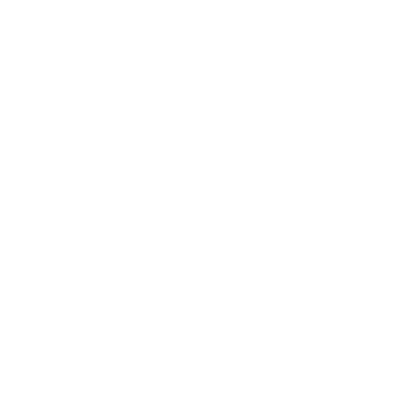
Advantages of Using CVD Tube Furnace for Coating
CVD coatings have several advantages over other coating methods, such as high purity, density, and uniformity, making them ideal for many applications in various industries.
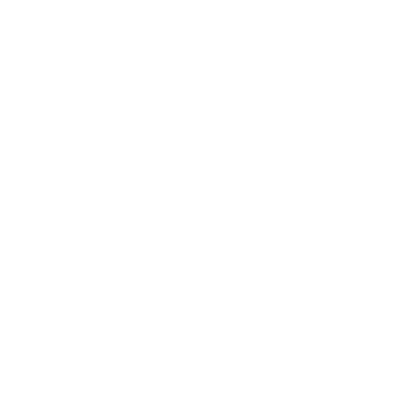
The Process of Fabricating a CVD Diamond By MPCVD Machine
CVD diamond machines have gained significant importance in various industries and scientific research.
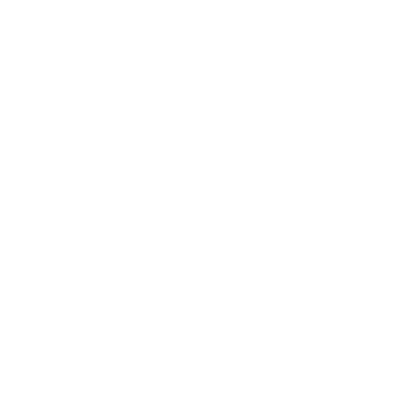
How CVD is Used in the Semiconductor Industry
CVD has revolutionized the semiconductor industry, enabling the production of high-performance electronic devices with enhanced functionality and reliability.
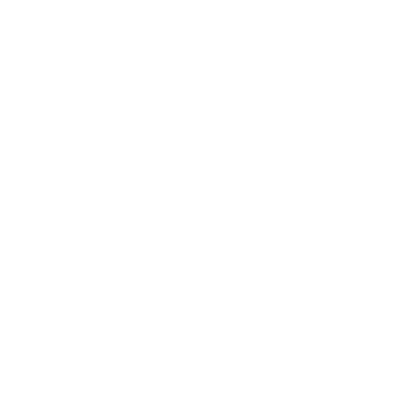
CVD furnace for the growth of carbon nanotubes
Chemical vapor deposition (CVD) furnace technology is a widely used method for growing carbon nanotubes.
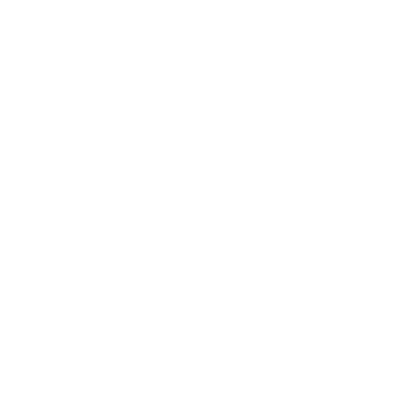
CVD Machines for Thin Film Deposition
Chemical Vapor Deposition (CVD) is a widely used technique for deposition of thin films on various substrates.