Introduction to CVD systems and their importance
Chemical Vapor Deposition (CVD) is a widely used process in the semiconductor and microelectronics industry to deposit thin films of materials on a substrate. CVD systems are essential for the production of advanced electronic devices, high-performance coatings, and other industrial applications. The importance of CVD systems lies in their ability to produce high-quality and uniform films with precise control over the film thickness and composition. CVD systems offer a wide range of advantages over other deposition techniques, including the ability to deposit materials at low temperatures, high deposition rates, and the ability to produce complex material structures. Understanding the basics of CVD systems and their importance is crucial for optimizing the process and solving common problems encountered during operation.
Table of Contents
Common Problems Faced by CVD Systems
Chemical Vapor Deposition (CVD) is a widely used method to deposit thin films of material onto a substrate. However, like any other equipment, CVD systems can experience problems that hinder their efficiency and effectiveness. In this section, we will discuss the common problems faced by CVD systems and how to solve them.
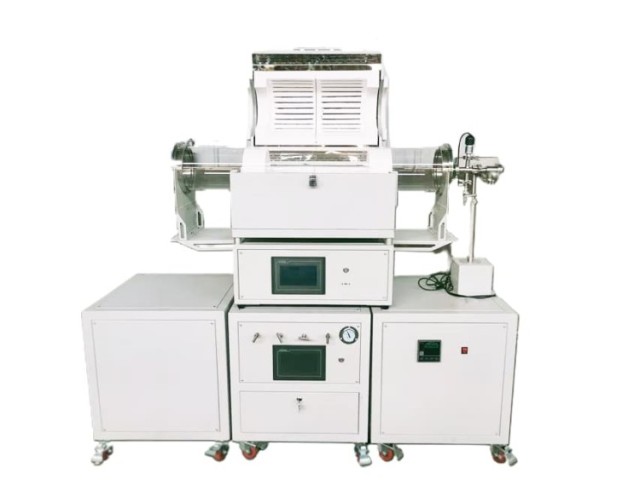
Poor Film Quality
Poor film quality is one of the most common problems faced by CVD systems. This can be due to a variety of factors such as incorrect temperature, flow rates of the reactants, and substrate preparation. To solve this problem, it is important to adjust the temperature and flow rates of the reactants to ensure that they are within the optimal range. Additionally, proper substrate preparation can also improve the film quality.
Poor Adhesion
Poor adhesion is another common problem faced by CVD systems. This can be due to surface contamination or inadequate preparation of the substrate. To solve this problem, the substrate surface should be cleaned with plasma or UV irradiation. This will ensure that the surface is free of any contaminants and is ready for deposition.
Particle Contamination
Particle contamination is a significant problem faced by CVD systems. This can be due to the use of contaminated gases or improper cleaning of the equipment. To prevent particle contamination, it is important to use clean and dry gases and to clean the equipment regularly.
Uniformity Issues
Uniformity issues are another common problem faced by CVD systems. This can be due to improper gas flow patterns or substrate rotation. To solve this problem, it is important to adjust the gas flow pattern and substrate rotation to ensure that the deposition is uniform across the entire substrate.
In addition to the above, regular maintenance and cleaning of the CVD equipment can also help to prevent common problems. It is important to note that troubleshooting CVD systems requires a thorough understanding of the process and equipment and should only be performed by trained personnel.
By addressing the common problems faced by CVD systems, it is possible to improve their efficiency and reliability, and thereby reduce the overall cost of thin film deposition in the semiconductor industry.
Vacuum pump failures and their causes
Vacuum pumps are essential components of Chemical Vapor Deposition (CVD) systems as they create and maintain the low-pressure environment required for the deposition process. However, like any other equipment, CVD systems may encounter issues that can affect their performance and efficiency. One of the most common problems in CVD systems is vacuum pump failures.
Causes of Vacuum Pump Failures
The causes of vacuum pump failures can be numerous, including insufficient maintenance, contamination, and mechanical wear and tear. Particles entering the pump can score the walls of the pump, reducing its efficiency. Additionally, the particulate inside of the pump can also cause damage, setting off a chain of events leading to seizing and failure as well as long repair times if one does not have a back-up pump or an experienced pump repair shop at close quarters.
Preventing Vacuum Pump Failures
To avoid vacuum pump failures, it is crucial to conduct routine maintenance, including regular oil changes, cleaning, and inspections. Inlet Filters with paper, poly, or activated carbon and water traps also keep vacuum oil un-contaminated for longer periods of service. Filters help to avoid particulates. It is also essential to prevent contamination by keeping the system clean and regularly replacing or cleaning filters.
Monitoring Vacuum Pump Performance
It is recommended to monitor the vacuum pump's performance regularly and to replace any worn or damaged parts promptly. For optimal performance, conduct regular inspections to ensure there are no leaks in the system, including equipment and related accessories, such as downstream and upstream piping. Effective process control requires real-time measurement with high sensitivity and repeatability.
Common Vacuum Pump Problems and Solutions
Even with frequent inspections, this type of pump has a few common problems. Non-Starting Pump - Make sure the pump is properly connected and check the set motor protection switch. If the engine is not starting because the operating voltage does not match to the motor, the motor needs replacing. In addition, look at the oil temperature. Low Speed - This is often caused by trapped dirt in the intake. However, the exhaust filter could also be clogged, the connecting lines might be too long or narrow, or the length of the spring on the anti-suck-back valve prevents it from opening. Pressure Rises Too Fast - If the pressure rises too fast when the pump is switched off under vacuum, the system may have a leak or the anti-suck-back valve has malfunctioned and needs replacing.
In conclusion, vacuum pump failures can be a significant issue for CVD systems, leading to costly downtime and damage to wafers. By conducting routine maintenance, monitoring the vacuum pump's performance, and promptly replacing any worn or damaged parts, CVD users can ensure that their vacuum pumps remain in good working condition, avoiding costly downtime and ensuring continuous and reliable operation of the CVD system.
Components of a CVD Apparatus
To understand and solve common problems associated with Chemical Vapor Deposition (CVD) systems, it is important to have a good understanding of the components that make up the apparatus. A CVD apparatus is comprised of several basic components that work together to deposit thin films of various materials for different applications.
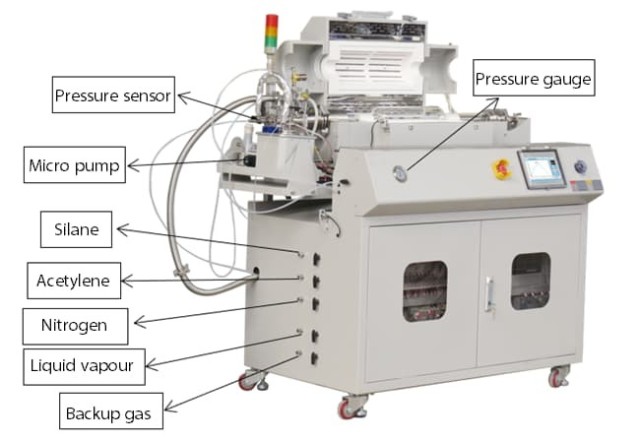
Gas Delivery System
The gas delivery system is responsible for supplying precursors to the reaction chamber. Precursors for CVD processes must be volatile and stable enough to be delivered to the reactor. Generally, precursor compounds provide a single element to the deposited material, with others being volatilized during the CVD process. However, sometimes precursors may provide more than one element.
Reaction Chamber
The reaction chamber is where the deposition takes place. It is an enclosed container designed to accommodate the substrate and the precursors for the deposition process.
Substrate Loading Mechanism
The substrate loading mechanism is responsible for introducing and removing substrates, mandrels, etc. The mechanism should be designed to ensure accurate and consistent positioning of the substrate in the reaction chamber.
Energy Source
The energy source provides the energy or heat required to get the precursors to react/decompose. The type of energy source used will depend on the specific application of the CVD process.
Vacuum System
The vacuum system is responsible for removing all other gaseous species other than those required for the reaction/deposition. Vacuum pumps are used to maintain the desired pressure inside the chamber.
Exhaust System
The exhaust system is responsible for removing volatile by-products from the reaction chamber. The chemical by-products and unreacted atoms or molecules removed from the chamber with the exhaust tend to be toxic, flammable or damaging to the pumps, and therefore need to be treated to make them harmless to people and the environment.
Exhaust Treatment Systems
In some instances, exhaust gases may not be suitable for release into the atmosphere and may require treatment or conversion to safe/harmless compounds.
Process Control Equipment
Process control equipment includes gauges, controls, etc., to monitor process parameters such as pressure, temperature, and time. Alarms and safety devices are also included in this category.
Proper maintenance and cleaning of these components can help prevent many of the common issues associated with CVD systems. For example, the gas delivery system should be checked regularly for leaks and blockages, while the heating system should be calibrated to ensure accurate and consistent temperatures. Additionally, proper handling and storage of precursor materials can help prevent contamination of the substrate. Overall, understanding the components of a CVD system and implementing proper maintenance procedures can help ensure optimal performance and minimize downtime.
Materials that can be produced by CVD processes
Chemical Vapor Deposition (CVD) is a versatile process that can produce a wide range of materials, including metals, ceramics, semiconductors, and even diamonds. The process can be used to produce coatings, powders, fibers, nanotubes, and monolithic components. The materials produced by CVD systems have a broad range of applications, from electronic components to medical implants, and are crucial in the advancement of technology and scientific research.
Metals and Metal Alloys
CVD can produce most of the metal and metal alloys and their compounds, such as carbides, nitrides, and oxides. Diverse pre-materials can be used during the process which is because of the high temperature of the reaction. One of the oldest applications of the CVD process is the manufacturing of different pigments in the industry. Usually, TiO2, SiO2, Al2O3, Si3N4, and even carbon black powders can be made in nano or micron sizes by the CVD process.
Semiconductors
CVD can be used to prepare semiconductors, including carbon and silicon, and nonmetal systems such as metal oxides. The CVD technology is extensively used to produce thin film semiconductor and nanocomposite ceramic coatings with much-improved surface properties such as abrasion protection, corrosion/oxidation resistance, chemical reactions, thermal stress, and neutron absorption.
Non-Metal Systems
CVD can produce most metals, some non-metals such as carbon and silicon, as well as many components including carbides, nitrides, oxides, and intermetallic phases, etc. Using this process, a variety of nanostructures such as quantum dots, ceramic nanostructures, carbides, carbon nano-pipes, and even diamonds are producible.
Ceramic Nanocomposite Coatings
CVD technology is often used to produce coatings, powders, fibers, and unified components. It is possible to produce ceramic nanocomposite coatings with much improved surface properties, such as wear resistance, corrosion resistance, high-temperature protection, and erosion protection, among others. By varying the parameters of the CVD process, such as substrate type, substrate temperature, the chemical composition of the mixtures of the reactant gases, and the total pressure of the gas that flows, a wide range of products, including ceramic nanocomposite coatings, dielectrics, single-crystalline silicone, polymeric materials, and metals, can be coated to the substrate by such a layering process.
Optical Fibers
CVD can be used to produce optical fibers for telecommunications, which are essential in the modern-day communication industry.
Composites
Preforms can be infiltrated using CVD techniques to produce ceramic matrix composites such as carbon-carbon, carbon-silicon carbide, and silicon carbide-silicon carbide composites. This process is sometimes called chemical vapor infiltration or CVI.
Powder Production
CVD is used in the production of novel powders and fibers, which can be used in various applications.
Catalysts and Nanomachines
CVD technology has found many applications in materials science and engineering, including the production of catalysts and nanomachines.
In conclusion, CVD is a powerful technology capable of producing a wide range of materials with unique properties. The materials produced using this technology find applications in various fields, including aerospace, military, aviation, nuclear, and general materials engineering. With proper maintenance and troubleshooting, CVD systems can produce materials with excellent quality and consistency.
Conclusion: Importance of addressing CVD system problems
In conclusion, addressing CVD system problems is crucial for maintaining the quality of the materials produced. Common problems like vacuum pump failures and in-situ measurement challenges can be mitigated by using real-time monitoring and suitable sources of heat for CVD processes. Legacy metrology solutions should be updated to overcome their limitations. By understanding the types of CVD systems and their advantages, it is possible to select the appropriate system for the desired material. Overall, addressing CVD system problems can improve the efficiency and reliability of the system, leading to high-quality materials and increased productivity.
CONTACT US FOR A FREE CONSULTATION
KINTEK LAB SOLUTION's products and services have been recognized by customers around the world. Our staff will be happy to assist with any inquiry you might have. Contact us for a free consultation and talk to a product specialist to find the most suitable solution for your application needs!