Introduction to CVD Technology
Chemical Vapor Deposition (CVD) is a process used to deposit thin films of materials onto a substrate. It involves the reaction of vapor-phase chemicals to produce a solid material on a heated surface. CVD is commonly used to deposit coatings on a variety of materials, including metals, ceramics, and polymers, to improve their properties. The process offers several advantages over other coating techniques, such as high purity, uniformity, and the ability to deposit coatings with high-density. However, CVD also has some disadvantages, such as the high cost of equipment and the need for high-temperature processing.
Table of Contents
Advantages of CVD Coating
Chemical vapor deposition (CVD) coating is a versatile process that can produce high purity and density films with controllable properties suitable for various applications. The following are some of the advantages of CVD coating:
1. High Purity
CVD coating can produce films with very high purity levels of over 99.995%. This high level of purity is due to the process's ability to control the chemical reaction and minimize impurities. CVD processes use distillation techniques to evacuate impurities from gaseous precursors, resulting in high-purity films.
2. High-Density Films
CVD coating can produce high-density films that are beneficial in applications where mechanical, thermal, or electrical properties are critical. The high-density films are achieved because the process can deposit uniform films with thicknesses ranging from a few nanometers to several microns.
3. Controllable Properties
CVD coating can produce films with controllable properties by adjusting the deposition parameters such as temperature, pressure, and reactant flow rate. The films' properties can be tailored to specific applications, making CVD coating a versatile process suitable for various industries.
4. Scalability
CVD coating is suitable for depositing films on a small laboratory scale to large industrial-scale production. The process is easily scalable, making it suitable for batch production runs that provide major cost savings with economies of scale.
5. Wide Range of Materials
CVD coating can deposit a range of materials, including metals, ceramics, and semiconductors. This versatility allows for the production of a wide range of coated manufacturing materials.
6. Uniform Coating
CVD is a conformal deposition process, which means it uniformly coats a substrate regardless of the shape to produce an even coating. This method builds the desired layer from the substrate up, a significant advantage in creating conductive films.
7. Application Variety
CVD can create thin layers on many materials regardless of rigidity, flexibility, or density. CVD systems can be found across industries, from electronics manufacturing to producing crisp bags.
In summary, CVD coating is a versatile process that can produce high purity and density films with controllable properties suitable for various applications. The process's scalability, wide range of materials, and ability to produce uniform coatings make it a popular method used in various industries.
Disadvantages of CVD Coating
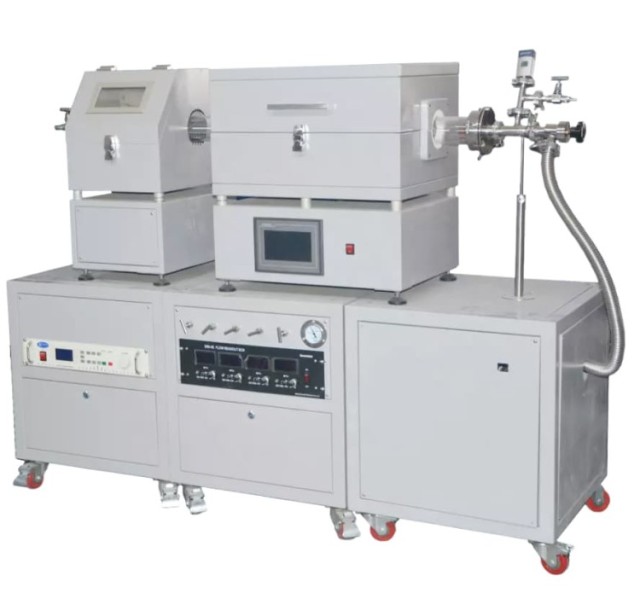
CVD coating, being a popular method for coating materials with high-purity, high-density material, has its fair share of disadvantages. Some of the major drawbacks of CVD coating are as follows:
High cost of equipment and materials
One of the main disadvantages of CVD coating is the high cost of equipment and materials required for the process. CVD requires expensive equipment and specialized gases, making it impractical for small-scale applications or laboratories with limited budgets.
Time-consuming process
Additionally, the process can be time-consuming, requiring several hours or even days to complete a single coating. This can be a major drawback for industries that require a quick turnaround time for their products.
Difficulty in controlling thickness and uniformity of coating
Another disadvantage of CVD coating is that it can be difficult to control the thickness and uniformity of the coating. Variations in temperature, pressure, and gas flow can all affect the quality of the coating, leading to inconsistencies or defects.
Limitations in coating certain materials
Additionally, some materials may not be suitable for CVD coating due to their chemical properties or reactivity with the coating gases. This can limit the range of substrates that can be coated using this method.
Specialized training and expertise required
CVD coating also requires specialized training and expertise to operate the equipment and ensure consistent and high-quality coatings. This can be a major drawback for small laboratories or industries that do not have access to trained personnel.
Overall, while CVD coating can be an effective method for achieving high-purity, high-density coatings on substrates, it is important to consider the cost, complexity, and limitations of the process before deciding if it is the right choice for a given application.
CVD Coating Equipment and Process
CVD coating is a complex process that requires specialized equipment to achieve high-purity, high-performance thin solid films. Here's a step-by-step breakdown of the CVD coating process and the equipment required:
The CVD Coating Process
-
Material Preparation: The source material is first prepared for the coating process. This involves mixing source materials with one or more volatile precursors that serve as carrier devices.
-
Transport and Deposition: Once prepared, the source material is transported into the reaction chamber, which contains a substrate, by forced convection. Through the process of diffusion, reactants are deposited onto the substrate. After the mixture adheres to the substrate, the precursor eventually breaks down, is removed by diffusion and leaves behind the desired layer of source material on the substrate. The decomposition process can be facilitated or accelerated using heat, plasma or various techniques.
-
Result: The result of the CVD coating process is a thin film with a uniform thickness and high purity, which is highly resistant to wear and corrosion, making it ideal for use in harsh environments. The coatings also have excellent adhesion properties, making them useful for bonding dissimilar materials.
CVD Coating Equipment
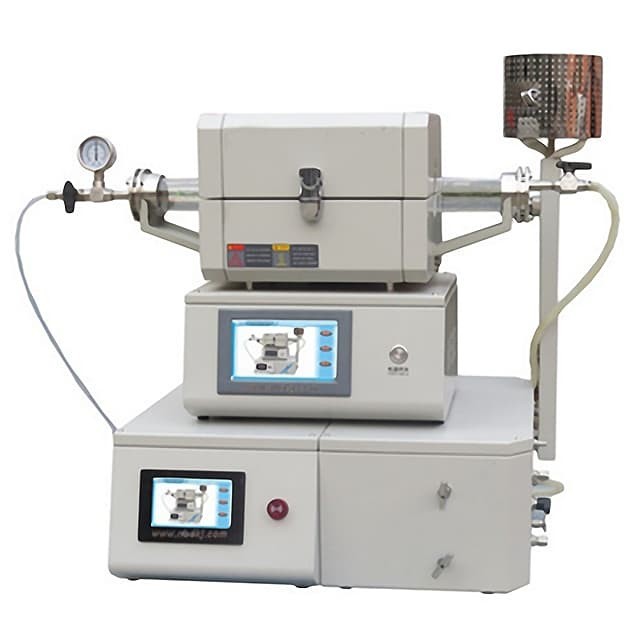
To achieve high-quality CVD coatings, specialized equipment is required. The equipment must be able to maintain a high vacuum, control temperature, and provide precise gas flows. Here are the main components of CVD coating equipment:
-
Reaction Chamber: The reaction chamber is where the CVD process takes place. It is typically made of high-quality materials such as quartz or ceramic, which can withstand high temperatures and are not reactive with the source material.
-
Vacuum System: A high vacuum system is required to create the necessary conditions for the CVD process. This system includes a vacuum pump, which is used to create a low-pressure environment inside the reaction chamber.
-
Gas Delivery System: The gas delivery system is used to deliver the source material and other gases into the reaction chamber. It includes gas flow controllers, which are used to precisely control the flow rate of each gas.
-
Heating System: The heating system is used to raise the temperature inside the reaction chamber to the required level for the CVD process. It typically uses a combination of resistance heating and radiant heating.
-
Substrate Holder: The substrate holder holds the substrate in place inside the reaction chamber during the CVD process. It is typically made of a material that can withstand high temperatures and is not reactive with the source material.
Overall, the CVD coating process is complex and requires a skilled operator to ensure consistent results. However, the benefits of CVD coating are numerous, making it an important technology for achieving high-quality, high-performance materials.
Applications of CVD Technology
CVD technology has a wide range of applications in various industries, including laboratory equipment. The process involves the deposition of a thin film of material onto a substrate using a chemical reaction. This results in high purity and density of the materials being coated. Here are some of the applications of CVD technology:
Aerospace and Defense Industry
CVD technology is extensively used in the manufacturing of components in the aerospace and defense industry. The technology is used to develop high-quality coatings for engines, turbines, and other critical components that require high wear-resistance, corrosion resistance, and thermal stability. CVD technology can also be used to produce nanocomposite ceramic coatings that offer excellent neutron absorption and thermal management properties.
Semiconductor Industry
CVD technology is highly useful in the production of high-quality thin films for electronic devices. The technology is used to deposit materials such as silicon, silicon dioxide, and silicon nitride used in the fabrication of integrated circuits, micro-electronics, and photonics. The technology offers precise control over the thickness and quality of the thin films produced.
Medical Industry
CVD technology is used to develop new materials for medical implants. The technology is used to produce coatings that offer excellent biocompatibility, corrosion resistance, and wear-resistance. CVD-coated materials can also have improved thermal conductivity, making them ideal for use in high-temperature applications.
Chemical Industry
CVD technology is used to enhance the corrosion resistance of materials used in chemical processing. The technology is used to produce coatings that offer excellent resistance to acids, alkalis, and other corrosive substances. CVD technology can also be used to produce coatings that offer excellent adhesion to various substrates, making them ideal for use in chemical processing.
Automotive Industry
CVD technology is used to produce coatings for automotive components. The technology is used to produce coatings that offer excellent wear-resistance, corrosion resistance, and thermal management properties. CVD-coated components can also have improved mechanical properties, making them ideal for use in high-performance engines and transmissions.
In conclusion, CVD technology has a wide range of applications in various industries, including aerospace, semiconductor, medical, chemical, and automotive industries. The technology offers high purity and density of the materials being coated, making it ideal for producing coatings with excellent wear-resistance, corrosion resistance, and thermal management properties. CVD technology is expected to continue to play a crucial role in the advancement of laboratory equipment and materials science.
CONTACT US FOR A FREE CONSULTATION
KINTEK LAB SOLUTION's products and services have been recognized by customers around the world. Our staff will be happy to assist with any inquiry you might have. Contact us for a free consultation and talk to a product specialist to find the most suitable solution for your application needs!