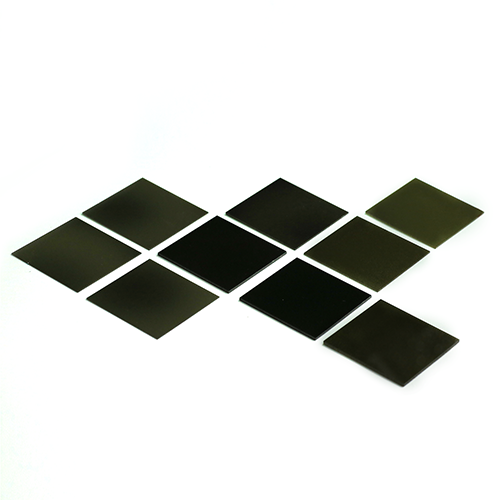
CVD materials
CVD Diamond Cutting Tool Blanks for Precision Machining
Item Number : cvdm-04
Price varies based on specs and customizations
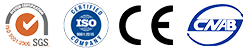
Shipping:
Contact us to get shipping details Enjoy On-time Dispatch Guarantee.
Why Choose Us
Reliable PartnerEasy ordering process, quality products, and dedicated support for your business success.
Introduction
Diamond tools are metal cutting tools with diamond grains fixed on the functional parts of the tool via a bonding material. Diamond tools have many advantages, including high working efficiency, low grinding force, high wear resistance, and high grinding quality and precision.
CVD diamond cutting tools are widely used for cutting non-ferrous materials, ceramics, abrasive composites, high silicon-content aluminum alloy, graphite, and other difficult machining materials. They offer excellent wear resistance, low friction coefficient, perfect thermal conductivity, high fracture strength and toughness, and better dimensional and thermal stability.
Applications
CVD diamond cutting tools are widely used in various industrial sectors due to their exceptional properties. These tools have proven their effectiveness in cutting and machining a wide range of materials, including:
-
Non-ferrous materials: CVD diamond tools excel in cutting non-ferrous metals such as aluminum, copper, and their alloys. Their high thermal conductivity and low friction coefficient ensure clean and precise cutting operations.
-
Ceramics: The extreme hardness and wear resistance of CVD diamond make it an ideal choice for cutting ceramic materials. It can effectively machine ceramics with high precision and minimal chipping or breakage.
-
Abrasive composites: CVD diamond tools are highly effective in cutting abrasive composites, which are often encountered in industries such as aerospace and automotive. These tools can withstand the abrasive nature of the material, resulting in longer tool life and improved cutting performance.
-
High silicon-content aluminum alloy: CVD diamond tools are well-suited for cutting high silicon-content aluminum alloys, which are known for their hardness and abrasiveness. The diamond's exceptional wear resistance enables it to maintain its sharpness and deliver consistent cutting results.
-
Graphite: CVD diamond tools are commonly used for cutting graphite, a soft and brittle material that requires careful handling. The diamond's high thermal conductivity prevents the buildup of heat at the cutting edge, ensuring clean and precise cuts.
-
Other difficult-to-machine materials: CVD diamond tools have demonstrated their capabilities in cutting a variety of other challenging materials, including glass, carbon fiber, and certain types of plastics. Their versatility makes them a valuable asset in various industrial applications.
Features
CVD diamond cutting tools offer a range of benefits for users, including:
-
Excellent wear resistance: This means that CVD diamond tools can be used for longer periods of time before they need to be replaced, resulting in reduced downtime and increased productivity.
-
Low friction coefficient: This helps to reduce the amount of heat generated during machining, which can lead to improved surface finishes and longer tool life.
-
Perfect thermal conductivity: This allows CVD diamond tools to operate at lower temperatures, which can help to prevent damage to the workpiece and the tool itself.
-
High fracture strength and toughness: This makes CVD diamond tools more resistant to chipping and breakage, even under heavy cutting loads.
-
Better dimensional and thermal stability: This helps to ensure that CVD diamond tools maintain their shape and cutting performance over time, resulting in more consistent results.
-
Wide range of applications: CVD diamond tools can be used to cut a wide variety of materials, including non-ferrous metals, ceramics, abrasive composites, high silicon-content aluminum alloys, graphite, and other difficult-to-machine materials.
Principle
Cutting tool blanks fabricated by DC arc Plasma Jet usually have a substantially higher thermal conductivity than those by other techniques even at a relatively high growth rate. This is apparently favorable for heavy load high-speed cutting operations. Very low friction coefficient, higher fracture strength and fracture toughness, very high thermal oxidation resistance, in combination with the higher thermal conductivity, should make it to be an ideal material for high-performance cutting.
Advantages
-
Excellent wear resistance: CVD diamond cutting tools can last up to 100 times longer than traditional carbide tools, resulting in less downtime for tool changes and increased productivity.
-
Low friction coefficient: This reduces the amount of heat generated during cutting, which can help to prevent workpiece damage and improve surface finish.
-
Perfect thermalconductivity: CVD diamond has a very high thermalconductivity, which helps to dissipate heat away from the cutting edge and prevent tool wear.
-
High fracture strength and toughness: CVD diamond is a very tough material, which can resist chipping and breakage even under heavy cutting loads.
-
Betterdimensional and thermal stability: CVD diamond is very stable at high temperatures, which helps to maintain its cutting performance even in harsh conditions.
-
Orientation independent: CVD diamond is a polycrystalline material, which means that it does not have a preferred orientation. This makes it ideal for use in applications where the cutting tool is subjected to multiple orientations.
FAQ
What Is The Difference Between Cutting Tool Blanks Fabricated By DC Are Plamsa Jet And Those By Other Techniques?
What Is CVD Diamond Machine?
What Are The Applications Of CVD Dimand Cutting Tools?
How Does A CVD Diamond Machine Work?
How To Solve The Problem Of Tight Tolerances Of Forging Blanks?
What Are The Advantages Of Using CVD Diamond Machines?
What Considerations Should Be Made When Selecting A CVD Diamond Machine?
What Are The Common Applications Of Diamonds Produced By CVD Diamond Machines?
4.9
out of
5
KINTEK SOLUTION's Cutting Tool Blanks are a game-changer! They are incredibly durable and have significantly improved our productivity.
4.8
out of
5
I highly recommend these Cutting Tool Blanks. They offer an exceptional balance of quality and value. The fast delivery is a bonus!
4.7
out of
5
KINTEK SOLUTION's Cutting Tool Blanks have exceeded my expectations. The quality is top-notch, and they have significantly reduced our production costs.
4.6
out of
5
These Cutting Tool Blanks are a must-have for any laboratory. They are reliable, efficient, and built to last.
4.9
out of
5
I was impressed by the cutting-edge technology used in these Cutting Tool Blanks. They have revolutionized our laboratory operations.
4.8
out of
5
KINTEK SOLUTION's Cutting Tool Blanks are worth every penny. They have significantly improved the accuracy and precision of our cutting processes.
4.7
out of
5
These Cutting Tool Blanks are incredibly user-friendly and have made our laboratory work much easier. I highly recommend them.
4.6
out of
5
KINTEK SOLUTION's Cutting Tool Blanks are a valuable addition to our laboratory. They have increased our productivity and efficiency.
4.9
out of
5
I am highly satisfied with the durability and performance of these Cutting Tool Blanks. They are an excellent investment.
4.8
out of
5
These Cutting Tool Blanks are a testament to KINTEK SOLUTION's commitment to innovation. They have transformed our cutting operations.
4.7
out of
5
I highly recommend these Cutting Tool Blanks for their exceptional quality and reliability. They have exceeded our expectations.
4.6
out of
5
KINTEK SOLUTION's Cutting Tool Blanks are a great value for the price. They have significantly reduced our downtime and increased our productivity.
4.9
out of
5
I am extremely impressed with the speed of delivery and the exceptional customer service I received from KINTEK SOLUTION.
4.8
out of
5
These Cutting Tool Blanks are a fantastic investment. They have significantly improved the quality of our cutting operations.
4.7
out of
5
KINTEK SOLUTION's Cutting Tool Blanks are a perfect fit for our laboratory. They are precise, efficient, and built to last.
4.6
out of
5
I am very satisfied with the performance and durability of these Cutting Tool Blanks. They have made a noticeable difference in our operations.
4.9
out of
5
KINTEK SOLUTION's Cutting Tool Blanks are a game-changer for our laboratory. They have increased our efficiency and improved the accuracy of our cutting processes.
4.8
out of
5
These Cutting Tool Blanks are a testament to the quality and innovation of KINTEK SOLUTION. They have exceeded our expectations.
4.7
out of
5
I highly recommend KINTEK SOLUTION's Cutting Tool Blanks. They are a valuable addition to any laboratory and have significantly improved our operations.
4.6
out of
5
These Cutting Tool Blanks are an excellent investment. They have significantly reduced our production costs and improved the quality of our products.
Products
CVD Diamond Cutting Tool Blanks for Precision Machining
REQUEST A QUOTE
Our professional team will reply to you within one business day. Please feel free to contact us!
Related Products
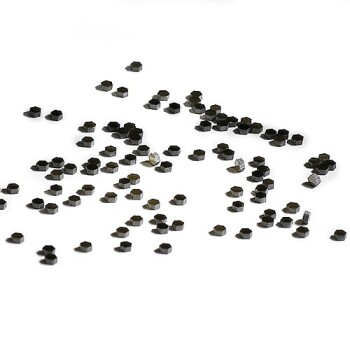
CVD Diamond Wire Drawing Die Blanks for Precision Applications
CVD diamond wire drawing die blanks: superior hardness, abrasion resistance, and applicability in wire drawing various materials. Ideal for abrasive wear machining applications like graphite processing.
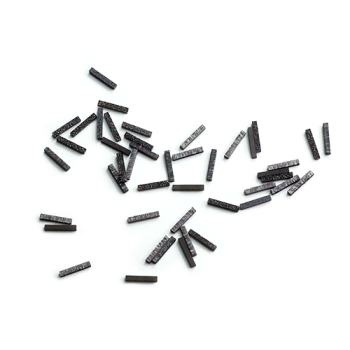
CVD Diamond Dressing Tools for Precision Applications
Experience the Unbeatable Performance of CVD Diamond Dresser Blanks: High Thermal Conductivity, Exceptional Wear Resistance, and Orientation Independence.
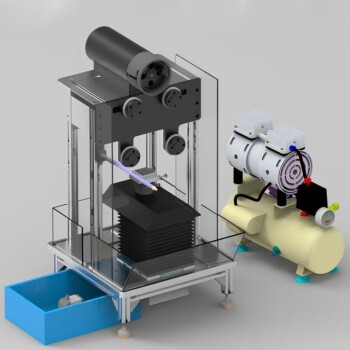
High Precision Diamond Wire Cutting Machine Laboratory Saw Precision Wire EDM Cutting Machine
The high precision diamond wire cutting machine is a versatile and precise cutting tool designed specifically for material researchers. It utilizes a continuous diamond wire cutting mechanism, enabling precise cutting of brittle materials such as ceramics, crystals, glass, metals, rocks, and various other materials.

CVD Diamond for Thermal Management Applications
CVD diamond for thermal management: High-quality diamond with thermal conductivity up to 2000 W/mK, ideal for heat spreaders, laser diodes, and GaN on Diamond (GOD) applications.
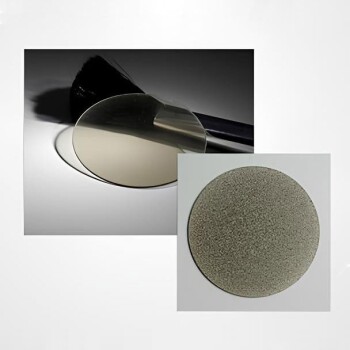
CVD Diamond Optical Windows for Lab Applications
Diamond optical windows: exceptional broad band infrared transparency, excellent thermal conductivity & low scattering in infrared, for high-power IR laser & microwave windows applications.
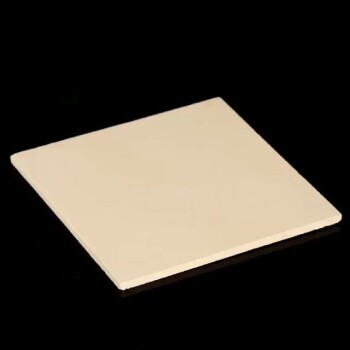
Precision Machined Yttria Stabilized Zirconia Ceramic Plate for Engineering Advanced Fine Ceramics
Yttrium-stabilized zirconia has the characteristics of high hardness and high temperature resistance, and has become an important material in the field of refractories and special ceramics.
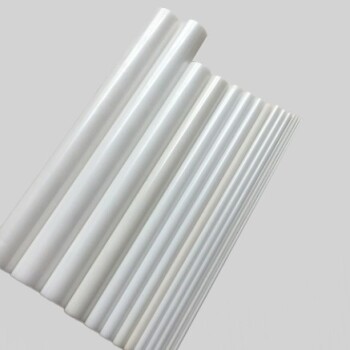
Precision Machined Yttrium Stabilized Zirconia Ceramic Rod for Engineering Advanced Fine Ceramics
Zirconia ceramic rods are prepared by isostatic pressing, and a uniform, dense and smooth ceramic layer and transition layer are formed at high temperature and high speed.
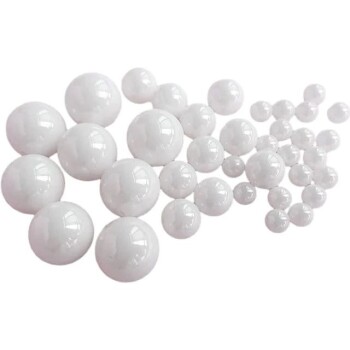
Precision Machined Zirconia Ceramic Ball for Engineering Advanced Fine Ceramics
zirconia ceramic ball have the characteristics of high strength, high hardness, PPM wear level, high fracture toughness, good wear resistance, and high specific gravity.
Related Articles
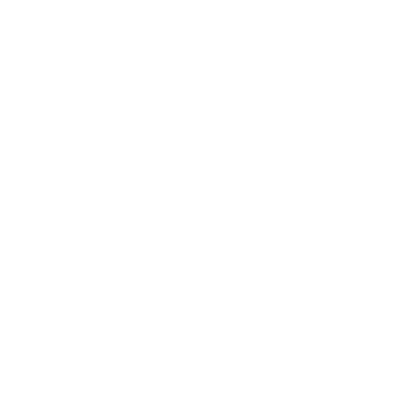
The Process of Fabricating a CVD Diamond By MPCVD Machine
CVD diamond machines have gained significant importance in various industries and scientific research.
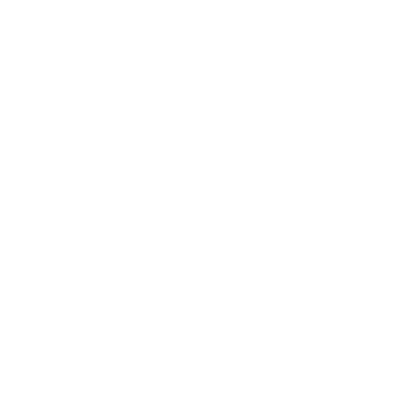
Diamond Growing Machines For Modern Machining and Need for New Cutting Tools
Diamonds have become popular due to their exceptional hardness, superior thermal conductivity, and chemical stability.
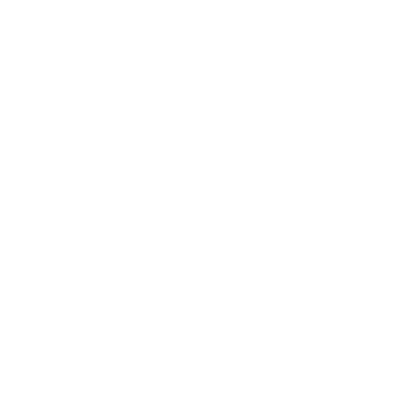
Understanding the CVD Diamond Machine and How It Works
CVD (Chemical Vapor Deposition) diamond creation process involves the deposition of carbon atoms onto a substrate using a gas phase chemical reaction. The process starts with the selection of a high-quality diamond seed, which is then placed in a growth chamber along with a carbon-rich gas mixture.
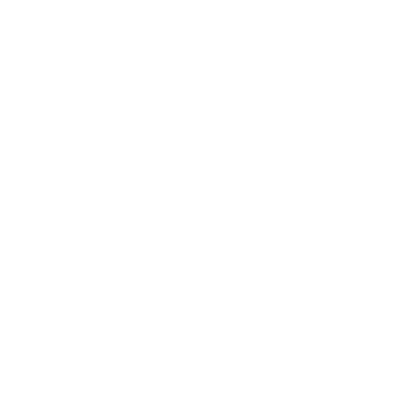
How CVD is Used in the Semiconductor Industry
CVD has revolutionized the semiconductor industry, enabling the production of high-performance electronic devices with enhanced functionality and reliability.
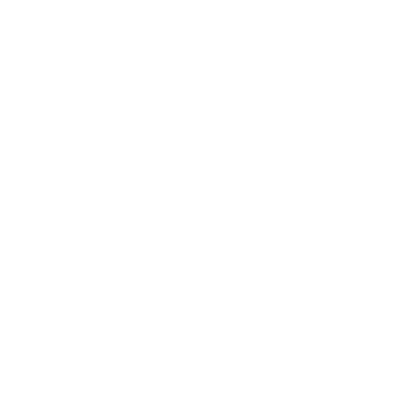
Key Materials for Successful CVD Processes
The success of CVD processes is dependent on the availability and quality of precursors used during the process.
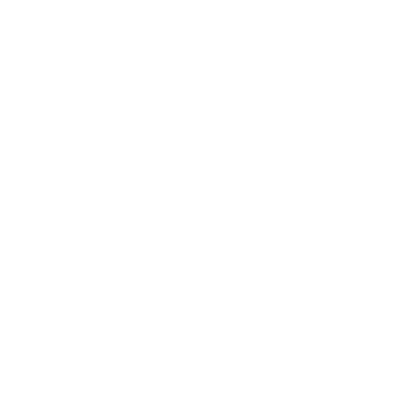
The Advancements in MPCVD Systems for Large Size Single Crystal Diamonds
Advancements in MPCVD systems have enabled the production of larger and higher quality single-crystal diamonds, offering promising potential for future applications.
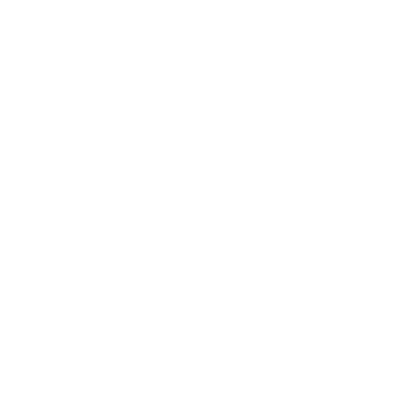
A Comprehensive Guide to MPCVD: Diamond Synthesis and Applications
Explore the fundamentals, advantages, and applications of Microwave Plasma Chemical Vapor Deposition (MPCVD) in diamond synthesis. Learn about its unique capabilities and how it compares to other diamond growth methods.
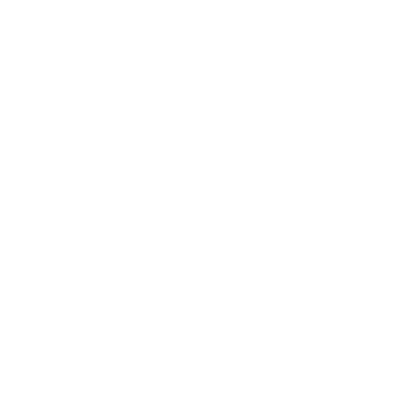
Advantages of Using CVD Tube Furnace for Coating
CVD coatings have several advantages over other coating methods, such as high purity, density, and uniformity, making them ideal for many applications in various industries.
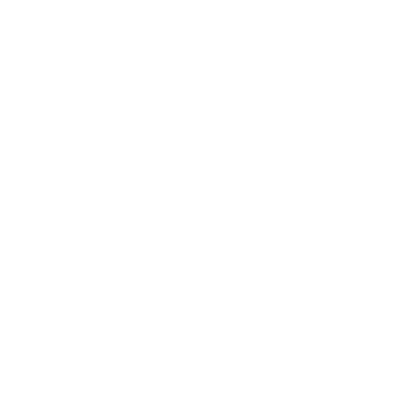
How CVD Coating Can Help You Achieve High Purity and Density
The CVD process offers several advantages over other coating techniques, such as high purity, uniformity, and the ability to deposit coatings with high-density.
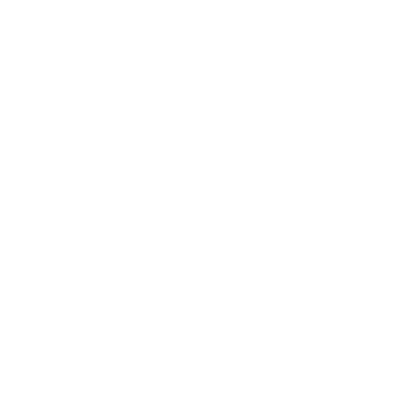
Comparing CVD Synthetic Diamonds and HPHT Cultivated Diamonds: What are the Differences?
Both CVD and HPHT diamonds are considered to be real diamonds, as they are made up of pure carbon and have the same physical and chemical properties as natural diamonds.
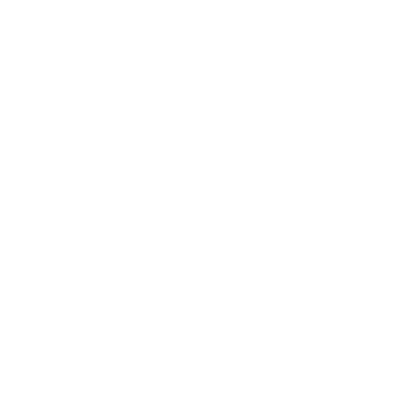
How to Check if Your Diamond is CVD-Produced
When it comes to buying a diamond, it's important to understand the difference between a naturally occurring diamond and one produced using CVD technology.
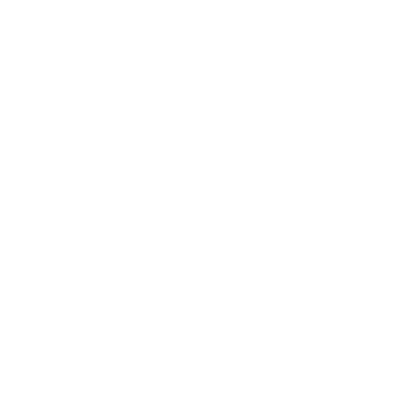
A Beginner's Guide to CVD Thin Film Technology
CVD is used in various industries, including the semiconductor industry, where it is used to produce thin films for electronic devices.