Introduction to CVD Process
Chemical Vapor Deposition (CVD) is a widely used process in which a thin film of material is deposited onto a substrate by introducing reactive gases into a chamber. The gases react to form a solid material that adheres to the substrate surface. CVD is commonly used to deposit metals, ceramics, and semiconductors for use in a wide range of applications, including microelectronics, optics, and coatings. The process is highly controllable, allowing for precise deposition of materials with controlled thickness, composition, and properties. However, the process requires specialized equipment and can be costly, making it suitable only for high-precision applications.
Table of Contents
Precursors for CVD Processes
Chemical Vapor Deposition (CVD) is a highly utilized technique in the production of various materials including ceramics, metals, and semiconductors. The success of CVD processes is dependent on the availability and quality of precursors used during the process. Precursors are chemicals that are used to deposit thin films on a substrate, and their properties determine the quality of the final product. The key materials used in CVD processes include metalorganic precursors, inorganic precursors, and halogenated precursors.
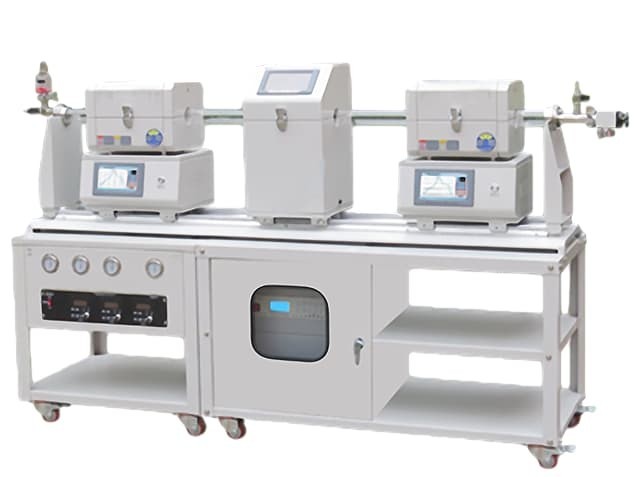
Metalorganic Precursors
Metalorganic precursors are commonly used in the production of semiconductors, and they consist of metal atoms bonded to organic molecules. These precursors are often volatile and can be transported easily to the reaction chamber. The use of metalorganic precursors ensures that the deposited film has the desired composition, and the properties of the precursor molecules determine the quality of the final product.
Inorganic Precursors
Inorganic precursors contain only inorganic molecules and are used in the production of materials like ceramics. These precursors are often more stable than metalorganic precursors and are used mainly in high-temperature CVD processes. Inorganic precursors are usually transported to the reaction chamber using carrier gases such as hydrogen, nitrogen, or argon, and their properties determine the quality of the final product.
Halogenated Precursors
Halogenated precursors are used in the production of metals and semiconductors, and they contain halogen atoms that help in the deposition process. The halogen atoms in these precursors act as ligands, and they form strong bonds with the metal atoms, which helps in the deposition process. The use of halogenated precursors ensures that the deposited film has the desired composition, and the properties of the precursor molecules determine the quality of the final product.
Choosing the Right Precursor
The properties of the precursors, such as their volatility, thermal stability, and reactivity, determine their suitability for use in CVD processes. It is essential to identify the right precursor for a specific CVD process to achieve the desired quality and efficiency. Precursors are expensive, and their availability can be limited, making it imperative to optimize their use in CVD processes.
Conclusion
Overall, the use of appropriate precursors is vital for the successful application of CVD in various industries, and research in this area continues to uncover new and better precursors for use in the process. The availability of different types of precursors allows for a wide range of materials to be deposited using the CVD technique, offering significant advantages in various applications.
Materials that can be produced by CVD processes
Chemical vapor deposition (CVD) is a process that is widely used in materials science to deposit a thin film of material onto a substrate. This process can produce a variety of materials, including metals, ceramics, and semiconductors. These materials are chosen for their unique properties such as high strength, thermal stability, and electrical conductivity.
Metals
Metals such as tungsten, copper, and aluminum can be produced by CVD processes. Tungsten is used in the production of microelectronic devices due to its high melting point and thermal stability. Copper can be used in the production of interconnects and electrodes. Aluminum is used in the aerospace and automotive industries due to its lightweight and high strength.
Ceramics
Ceramics such as silicon carbide, aluminum oxide, and boron nitride can be produced by CVD processes. Silicon carbide is used in the production of cutting tools and electronic devices due to its high hardness and thermal conductivity. Aluminum oxide is used in the production of wear-resistant coatings due to its high hardness and chemical stability. Boron nitride is used in the production of high-temperature materials due to its high thermal conductivity and electrical insulation properties.
Semiconductors
Semiconductors such as silicon, germanium, and gallium arsenide can be produced by CVD processes. Silicon is used in the production of microelectronic devices due to its electrical properties. Germanium is used in the production of infrared optics and solar cells. Gallium arsenide is used in the production of high-frequency electronic devices due to its high electron mobility.
Diamond
Diamond can be produced by CVD processes and is used in the production of cutting tools and electronic devices due to its high hardness and thermal conductivity.
The production of materials by CVD requires the use of specialized equipment and techniques, including the use of specific precursor chemicals, controlled temperatures, and precise gas flow rates. In addition to producing materials with unique properties, CVD also allows for the production of materials with precise dimensions and shapes, making it a valuable tool in the field of microfabrication.
Overall, the selection of appropriate materials is essential for the success of CVD processes, and the ability to produce a wide range of materials with diverse applications has revolutionized the field of materials science.
CVD Gas Products
Chemical Vapor Deposition (CVD) is a widely-used process for depositing thin films of various materials onto different substrates. The success of the CVD process largely depends on the quality of the key materials used, including the CVD gas products.
Types of CVD Gas Products
CVD gas products are essential for the deposition of high-quality films with specific properties, such as thickness, uniformity, and purity. The gas products used in CVD processes are usually inorganic or organometallic compounds that are vaporized to form a gas phase. The most commonly used CVD gas products include:
1. Metal-Organic Compounds (MOCVD)
Metal-organic compounds (MOCVD) are often used to deposit metal oxides and nitrides. MOCVD is a CVD technique that uses metal-organic precursors to deposit thin films. The metal-organic precursors are usually liquid at room temperature and vaporize when heated.
2. Halides
Halides are used to deposit metals and metal nitrides. Halides are a group of compounds that contain a halogen atom, such as chlorine, fluorine, or bromine. The most common halides used in CVD are metal halides, such as tungsten hexafluoride.
3. Carbonyls
Carbonyls are used to deposit metal carbides. Carbonyls are a group of compounds that contain a carbon monoxide molecule. The most common carbonyls used in CVD are metal carbonyls, such as iron pentacarbonyl.
4. Hydrides
Hydrides are used to deposit semiconductor materials. Hydrides are a group of compounds that contain a hydrogen atom. The most common hydrides used in CVD are metal hydrides, such as silane.
Importance of Quality CVD Gas Products
The quality of the CVD gas products used is crucial to the success of the process, as even minor impurities in the gas can result in poor-quality films with defects or inconsistent properties. Therefore, it is essential to choose high-quality CVD gas products from reputable suppliers and ensure proper storage and handling to maintain their purity.
In summary, the success of CVD processes depends on the quality of the CVD gas products used. Four commonly used CVD gas products include metal-organic compounds (MOCVD), halides, carbonyls, and hydrides. Each gas product has unique properties that make it suitable for depositing specific materials. It is important to choose high-quality CVD gas products from reputable suppliers and ensure proper storage and handling to maintain their purity.
Closed and Open Reactor CVD Process
Chemical vapor deposition or CVD is a widely used technique in the semiconductor and materials industry to deposit thin films of materials on a substrate. The success of a CVD process depends on several factors, including the choice of materials used in the process. One of the factors that affect the outcome of the process is whether it is a closed or open reactor CVD process.
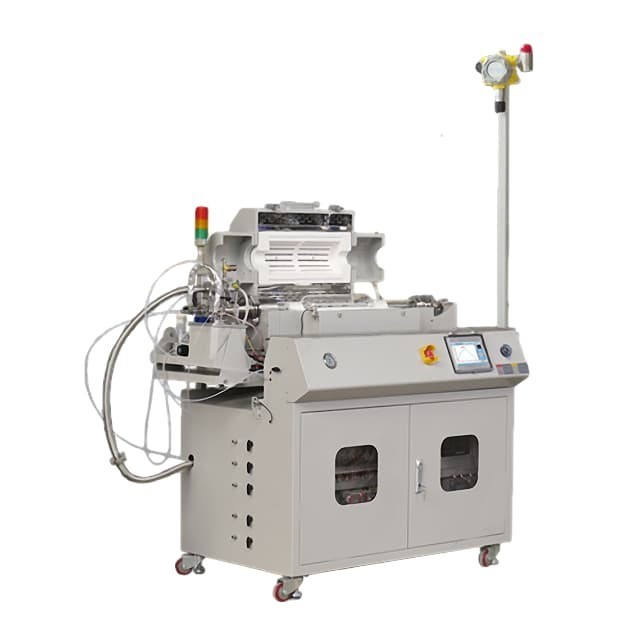
Closed Reactor CVD Process
In a closed reactor CVD process, the reactants are confined within a sealed chamber. A closed reactor CVD process is typically used for the deposition of films that require high purity or to prevent contamination from the atmosphere. The closed reactor CVD process is achieved by sealing the reaction chamber and pumping out the air to create a vacuum condition. The vacuum condition reduces the number of gas molecules, which reduces the likelihood of unwanted reactions occurring. Closed reactor CVD is ideal for depositing films that require a high degree of purity, such as those used in the semiconductor industry.
Open Reactor CVD Process
In an open reactor CVD process, the reactants are exposed to the atmosphere. Open reactor CVD is used when the deposition of the film is not dependent on a high degree of purity. Open reactor CVD is simpler and less expensive than closed reactor CVD because it doesn't require a vacuum chamber. The open reactor CVD process is achieved by introducing the reactants into the reactor and allowing the reaction to occur in the presence of air. Open reactor CVD is commonly used for depositing films that do not require a high degree of purity or when the cost of pumping down the chamber to achieve a vacuum condition is not practical.
In conclusion, the choice of closed or open reactor CVD process depends on the specific requirements of the deposition process. Closed reactor CVD is used for the deposition of films that require a high degree of purity or to prevent contamination from the atmosphere. Open reactor CVD is used when the deposition of the film is not dependent on a high degree of purity or when the cost of pumping down the chamber to achieve a vacuum condition is not practical. The choice of the reactor type is an important factor for a successful CVD process and should be carefully considered during the process design.
CONTACT US FOR A FREE CONSULTATION
KINTEK LAB SOLUTION's products and services have been recognized by customers around the world. Our staff will be happy to assist with any inquiry you might have. Contact us for a free consultation and talk to a product specialist to find the most suitable solution for your application needs!