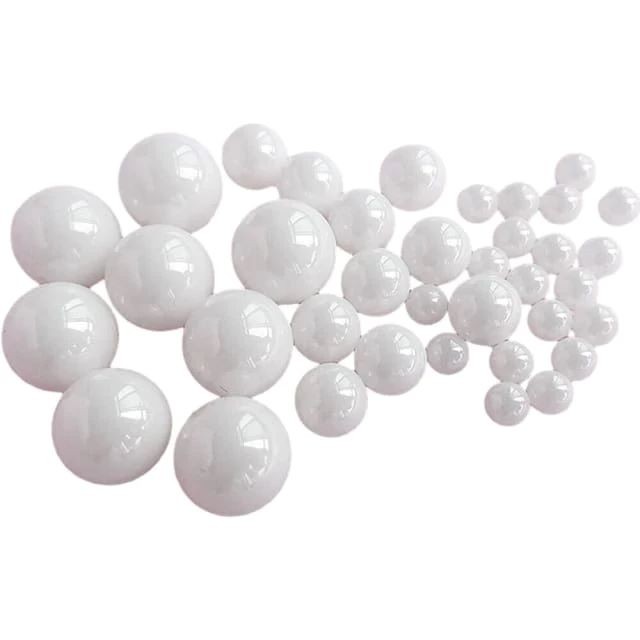
fine ceramics
Precision Machined Zirconia Ceramic Ball for Engineering Advanced Fine Ceramics
Item Number : KM-G03
Price varies based on specs and customizations
- Material
- Zirconia
- Specification
- See the form
- Size
- Customizable
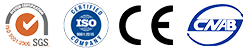
Shipping:
Contact us to get shipping details Enjoy On-time Dispatch Guarantee.
Why Choose Us
Reliable PartnerEasy ordering process, quality products, and dedicated support for your business success.
Application
Zirconia is a strong and tough ceramic material. zirconia ceramic ball made from it are durable, have a high load-carrying capacity and are easy to polish. They have properties such as hardness, wear resistance, heat resistance and corrosion resistance. Ceramic ball bearings use these zirconia balls instead of steel balls, which have the advantages of preventing arcing, reducing wear and temperature, and extending service life. They are lighter, stiffer and more durable than steel bearings, making them ideal for high speeds and harsh environments such as aerospace and medical applications. Ceramic ball bearings outperform steel bearings, spin faster, do not generate excessive heat, and provide superior performance in a variety of applications.
- Various high-speed and high-precision machine tools, motors, engines, and industrial machinery.
- Grinding of ceramic materials, magnetic materials, paints, dyes, inks.
- Food, pharmaceutical, specialty chemical industries.
- Valves, pumps, bearings and other mechanical parts.
- Medical and cosmetic applications, including dental implants, prosthetics and cosmetics.
- Manufacture of grinding and polishing media, etc.
Detail & Parts
Technical specifications
1mm | 2.778mm | 4.763mm | 6.747mm | 9.0mm | 12.7mm | 16.668mm | 25.0mm | 40mm |
1.2mm | 3.0mm | 5.0mm | 7.0mm | 9.525mm | 13.494mm | 17.4625mm | 25.4mm | 50mm |
1.5mm | 3.175mm | 5.556mm | 7.144mm | 10.0mm | 14mm | 18.256mm | 28mm | |
1.588mm | 3.5mm | 5.953mm | 7.938mm | 10.318mm | 14.288mm | 19.05mm | 28.575mm | |
2.0mm | 3.969mm | 6.0mm | 8.0mm | 11.1125mm | 15.0mm | 20.0mm | 30.0mm | |
2.381mm | 4.0mm | 6.35mm | 8.5mm | 11.509mm | 15.875mm | 20.638mm | 35mm | |
2.5mm | 4.5mm | 6.5mm | 8.731mm | 12.0mm | 16.0mm | 22.225mm | 38.1mm |
The produce we show are available in different sizes and custom sizes are available on request.
Advantages
- Low wear and contamination.
- High grinding efficiency, improve production efficiency.
- Long service life results in low overall cost.
- For high viscosity, wet grinding and dispersing applications.
- More durable and corrosion resistant compared to other materials.
- stability and physical strength.
- Low friction uncertainty.
- Excellent electrical insulation.
- Non-magnetic and non-conductive.
- Zirconia balls are lightweight and ideal for weight sensitive applications.
FAQ
What Are Advanced Ceramics?
What Are Engineering Ceramics?
What Are The Main Applications Of Fine Ceramics?
The Difference Between Different Materials Of Ceramic Ball Bearings.
What Are The Main Types Of Advanced Ceramics?
What Are The Main Types Of Engineering Ceramics?
What Are The Main Types Of Fine Ceramics?
The Difference Between Ceramic Hybrid And Full Ceramic.
What Are The Applications Of Advanced Ceramics?
What Are The Applications Of Engineering Ceramics?
What Is The Principle Behind Fine Ceramics?
How Are Advanced Ceramics Manufactured?
How Do Engineering Ceramics Differ From Traditional Ceramics?
What Are The Advantages Of Using Fine Ceramics?
What Are The Advantages Of Using Advanced Ceramics?
What Are The Advantages Of Using Alumina Ceramics?
What Is The Difference Between Alumina And Zirconia Ceramics?
Why Are Zirconia Ceramics Preferred In Certain Applications?
Why Are Silicon Carbide Ceramics Used In High-temperature Applications?
What Makes Silicon Carbide Ceramics Suitable For High-temperature Applications?
What Makes Boron Nitride Ceramics Unique?
How Are Boron Nitride Ceramics Used In Electronics?
How Do Advanced Ceramics Contribute To Energy Efficiency?
What Is The Manufacturing Process Of Engineering Ceramics?
Can Engineering Ceramics Be Customized For Specific Applications?
4.8
out of
5
Fast delivery and excellent customer service. The zirconia ceramic balls are of exceptional quality.
4.7
out of
5
I am very happy with the zirconia ceramic balls. They are durable and have a long service life.
4.9
out of
5
The zirconia ceramic balls are of excellent quality and the price is reasonable. I will definitely buy from KINTEK SOLUTION again.
4.6
out of
5
I am very satisfied with the zirconia ceramic balls. They are very durable and have a long service life.
5.0
out of
5
The zirconia ceramic balls are of the highest quality and meet all my expectations. I highly recommend them.
4.8
out of
5
The zirconia ceramic balls are very durable and have a long service life. I am very happy with them.
4.9
out of
5
I am very impressed with the zirconia ceramic balls. They are very efficient and have improved my production efficiency.
4.7
out of
5
The zirconia ceramic balls are very durable and have a long service life. I am very happy with them.
5.0
out of
5
The zirconia ceramic balls are of the highest quality and meet all my expectations. I highly recommend them.
Products
Precision Machined Zirconia Ceramic Ball for Engineering Advanced Fine Ceramics
REQUEST A QUOTE
Our professional team will reply to you within one business day. Please feel free to contact us!
Related Products
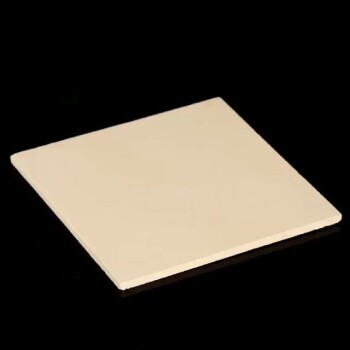
Precision Machined Yttria Stabilized Zirconia Ceramic Plate for Engineering Advanced Fine Ceramics
Yttrium-stabilized zirconia has the characteristics of high hardness and high temperature resistance, and has become an important material in the field of refractories and special ceramics.
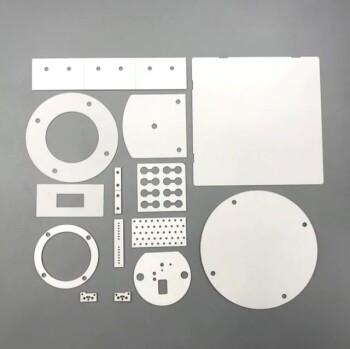
Alumina ceramics have good electrical conductivity, mechanical strength and high temperature resistance, while zirconia ceramics are known for their high strength and high toughness and are widely used.
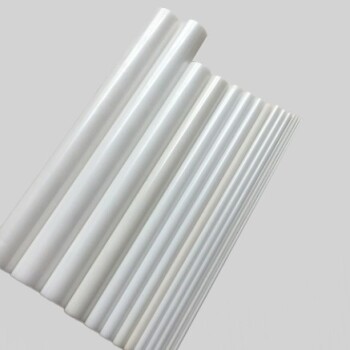
Precision Machined Yttrium Stabilized Zirconia Ceramic Rod for Engineering Advanced Fine Ceramics
Zirconia ceramic rods are prepared by isostatic pressing, and a uniform, dense and smooth ceramic layer and transition layer are formed at high temperature and high speed.
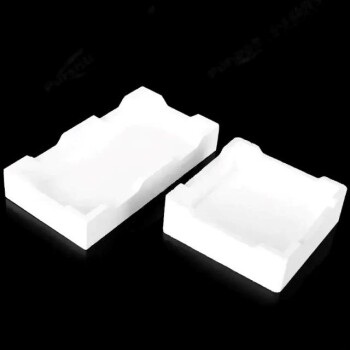
Advanced Engineering Fine Ceramics Alumina Ceramic Saggar for Fine Corundum
Alumina sagger products have the characteristics of high temperature resistance, good thermal shock stability, small expansion coefficient, anti-stripping, and good anti-powdering performance.
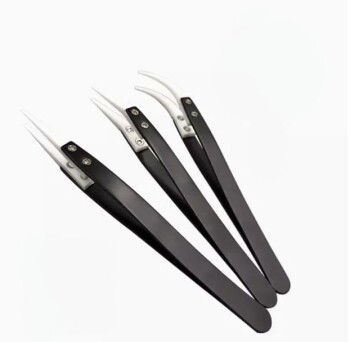
Engineering Advanced Fine Ceramics Head Tweezers with Pointed Elbow Zirconia Ceramic Tip
Zirconia ceramic tweezers are a high-precision tool made of advanced ceramic materials, especially suitable for operating environments that require high precision and corrosion resistance. This type of tweezers not only has excellent physical properties, but is also popular in the medical and laboratory fields because of its biocompatibility.
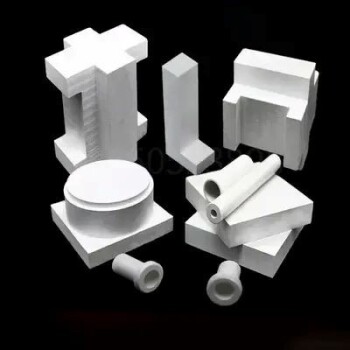
Advanced Engineering Fine Ceramics Boron Nitride (BN) Ceramic Parts
Boron nitride ((BN) is a compound with high melting point, high hardness, high thermal conductivity and high electrical resistivity. Its crystal structure is similar to graphene and harder than diamond.
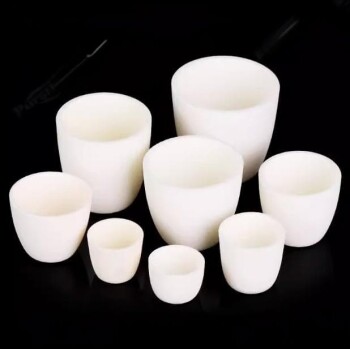
In the journey of scientific exploration and industrial production, every detail is crucial. Our arc-shaped alumina ceramic crucibles, with their excellent high temperature resistance and stable chemical properties, have become a powerful assistant in laboratories and industrial fields. They are made of high-purity alumina materials and manufactured through precision processes to ensure excellent performance in extreme environments.
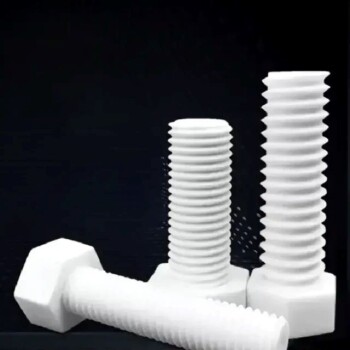
Alumina ceramic screws are fastening components made of 99.5% alumina, ideal for extreme applications requiring excellent thermal resistance, electrical insulation and chemical resistance.

Silicon Carbide (SIC) Ceramic Sheet Wear-Resistant Engineering Advanced Fine Ceramics
Silicon carbide (sic) ceramic sheet is composed of high-purity silicon carbide and ultra-fine powder, which is formed by vibration molding and high-temperature sintering.
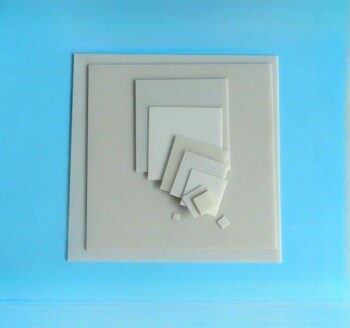
Advanced Engineering Fine Ceramics Aluminum Nitride (AlN) Ceramic Sheet
Aluminum nitride (AlN) has the characteristics of good compatibility with silicon. It is not only used as a sintering aid or reinforcing phase for structural ceramics, but its performance far exceeds that of alumina.
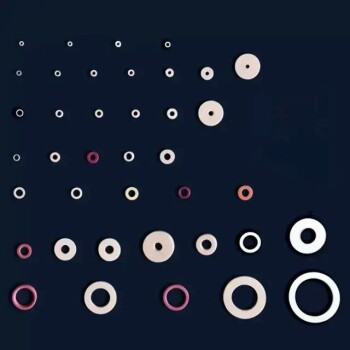
Alumina wear-resistant ceramic washer are used for heat dissipation, which can replace aluminum heat sinks, with high temperature resistance and high thermal conductivity.
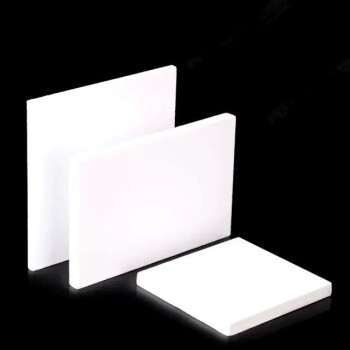
High Temperature Wear-Resistant Alumina Al2O3 Plate for Engineering Advanced Fine Ceramics
High temperature wear-resistant insulating alumina plate has excellent insulation performance and high temperature resistance.
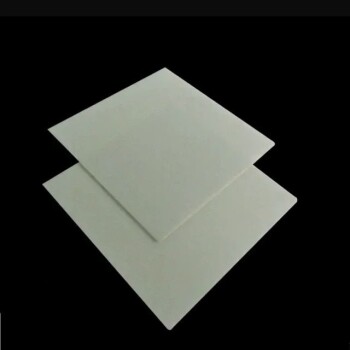
Precision Machined Silicon Nitride (SiN) Ceramic Sheet for Engineering Advanced Fine Ceramics
Silicon nitride plate is a commonly used ceramic material in the metallurgical industry due to its uniform performance at high temperatures.
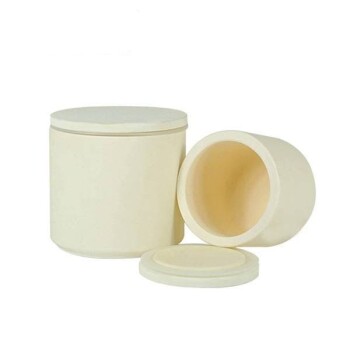
Laboratory Jar Ball Mill with Alumina Zirconia Grinding Jar and Balls
Grind to perfection with alumina/zirconia grinding jars and balls. Available in volume sizes from 50ml to 2500ml, compatible with various mills.
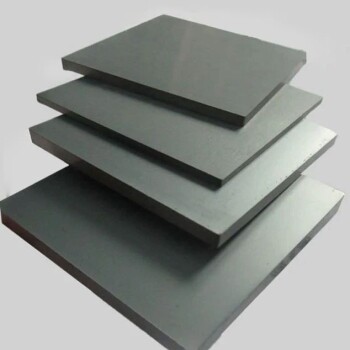
Silicon Carbide (SIC) Ceramic Plate for Engineering Advanced Fine Ceramics
Silicon nitride (sic) ceramic is an inorganic material ceramic that does not shrink during sintering. It is a high-strength, low-density, high-temperature-resistant covalent bond compound.
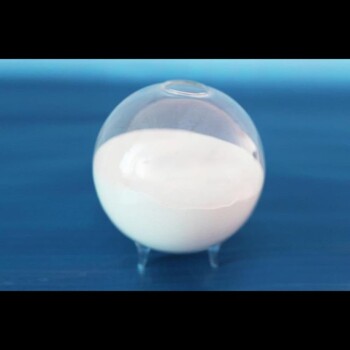
High Purity Alumina Granulated Powder for Engineering Advanced Fine Ceramics
Ordinary alumina granulated powder is alumina particles prepared by traditional processes, with a wide range of applications and good market adaptability. This material is known for its high purity, excellent thermal stability and chemical stability, and is suitable for a variety of high-temperature and conventional applications.
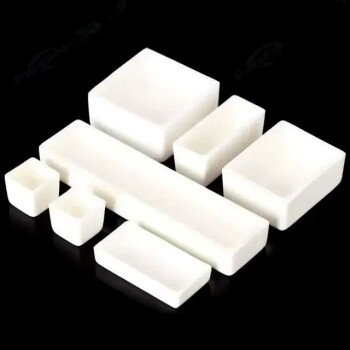
Engineering Advanced Fine Alumina Al2O3 Ceramic Crucible for Laboratory Muffle Furnace
Alumina ceramic crucibles are used in some materials and metal melting tools, and flat-bottomed crucibles are suitable for melting and processing larger batches of materials with better stability and uniformity.
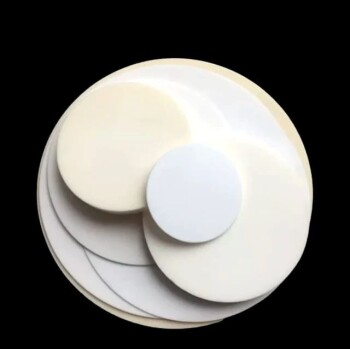
Engineering Advanced Fine Ceramics Aluminum Oxide Al2O3 Heat Sink for Insulation
The hole structure of the ceramic heat sink increases the heat dissipation area in contact with the air, which greatly enhances the heat dissipation effect, and the heat dissipation effect is better than that of super copper and aluminum.
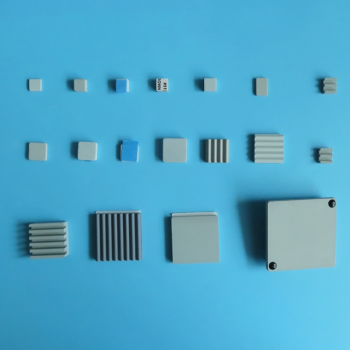
Silicon Carbide (SIC) Ceramic Sheet Flat Corrugated Heat Sink for Engineering Advanced Fine Ceramics
Silicon carbide (sic) ceramic heat sink not only does not generate electromagnetic waves, but also can isolate electromagnetic waves and absorb part of electromagnetic waves.
Related Articles
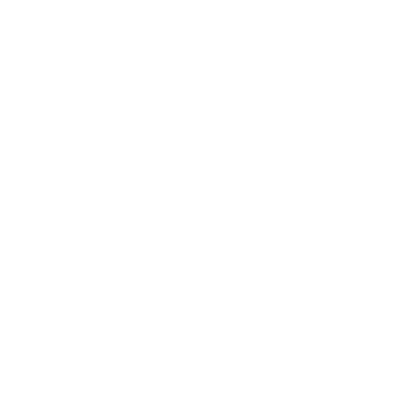
Choosing the Best Material for Ball Mill: Essential Factors and Recommendations
Discover the best material for ball mill applications and grinding success. Learn about the features and benefits of stainless steel, ceramic, agate, and tungsten carbide media. Find out how to ensure grinding success and the ideal grinding jars and media for planetary ball milling. Explore the applications of ball mills and the advantages of high-energy ball mills for ultra-fine particles.
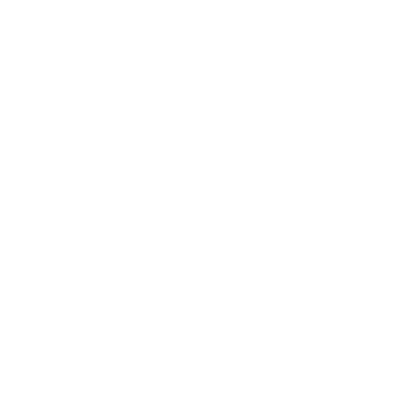
An In-depth Study of Isostatic Presses: Types, Applications, and Advantages
Isostatic presses play a crucial role in various industries, offering unique capabilities for material consolidation and product creation. These powerful machines apply equal pressure from all directions, resulting in products with uniform density and reduced defects. Isostatic presses are divided into two main types: Cold Isostatic Presses (CIP) and Hot Isostatic Presses (HIP). Each type functions under different conditions, allowing for a wide range of applications.
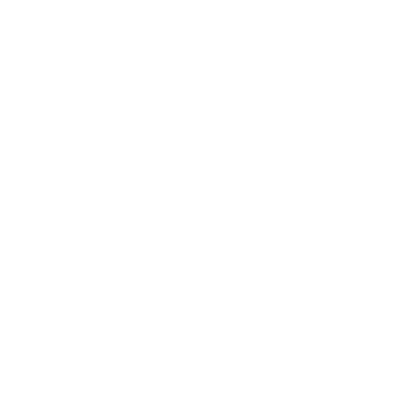
Isostatic Pressing of Ceramics: Process and Precision
When it comes to producing high-quality ceramic components, one of the most crucial processes is isostatic pressing. This technique ensures the uniformity and precision required for manufacturing ceramics used in various industries. Isostatic pressing involves carefully selecting the pressing powders and controlling the tools to achieve the desired uniformity. By understanding the process of isostatic pressing, manufacturers can ensure the production of ceramics that meet the strict standards of dimensional accuracy and performance.
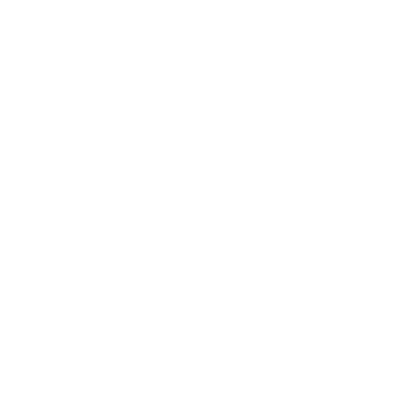
The Benefits of Cold Isostatic Pressing
Cold Isostatic Pressing (CIP) is a process used to compact powders into a specific shape or size. This method involves subjecting the powders to high pressure, typically between 100 and 200 MPa, in a liquid medium.
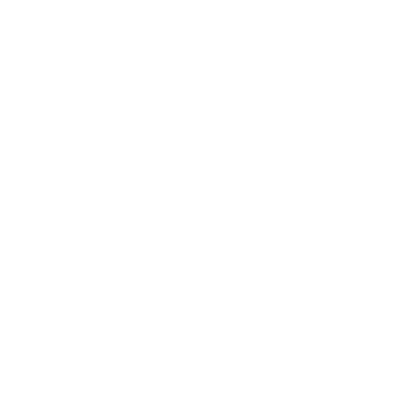
Understanding Cold Isostatic Pressing: Process, Advantages and Types
Cold Isostatic Pressing (CIP), also known as cold isostatic compaction, is a materials processing technique that involves subjecting a material to uniform pressure from all sides. This is achieved by immersing the material in a high-pressure fluid medium and applying hydraulic pressure. CIP is particularly effective for shaping and consolidating powdered materials, allowing for the creation of intricate shapes and achieving high green density.
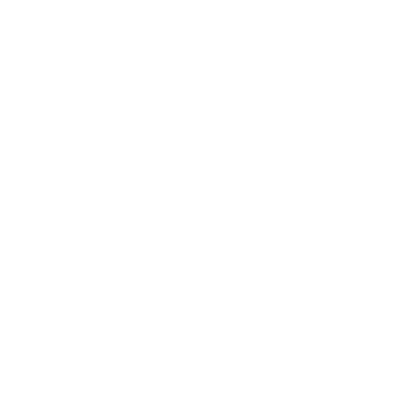
A Guide to Choosing the Right Temperature for Warm Isostatic Press
Warm Isostatic Pressing (WIP) is a process used to eliminate porosity and improve the mechanical properties of materials. In this process, the material is subjected to high pressure and temperature in an inert gas environment.
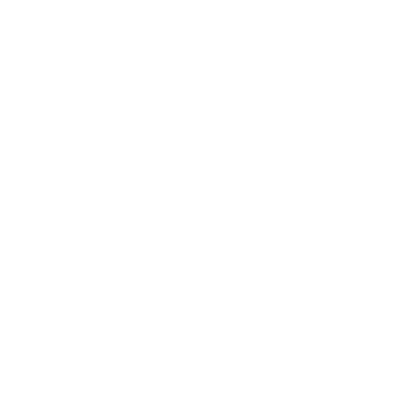
How to Achieve Uniform Pressure with Warm Isostatic Press
Warm Isostatic Pressing (WIP) is a manufacturing process that subjects materials to high pressure and high temperature simultaneously. The process involves using an isostatic press to apply uniform pressure to the material from all directions while it is heated to a specific temperature.
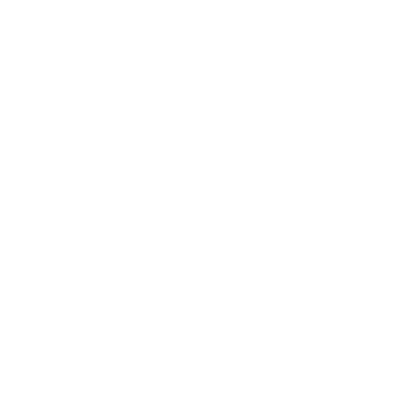
Cold Isostatic Pressing for Medical Applications Challenges and Solutions
Cold Isostatic Pressing (CIP) is a process used to compact and densify powders, ceramics, and metals. This process uses high-pressure fluids, usually water or oil, to apply uniform pressure to the material from all directions.
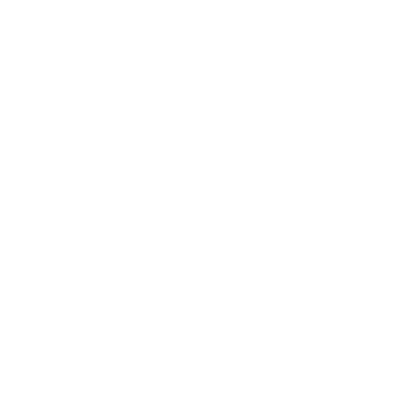
Understanding Cold Isostatic Pressing and its Types
Cold isostatic pressing (CIP) is a method of processing materials that is based on the principle proposed by Blaise Pascal, known as Pascal's law. According to this principle, pressure applied in an enclosed fluid is transmitted in all directions throughout the fluid without any change in magnitude.
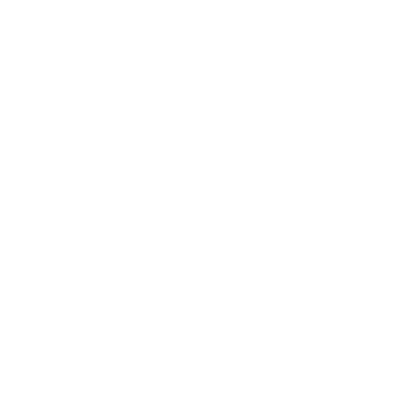
Dental Furnaces The Perfect Solution for Porcelain Processing
The dental furnaces are designed explicitly for the firing process of dental porcelain, which is a crucial step in the dental restoration process.
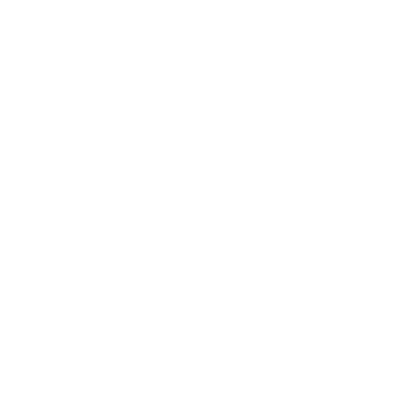
Understanding Quartz Electrolytic Cells: Applications, Mechanisms, and Advantages
Explore the detailed workings, applications, and benefits of quartz electrolytic cells in various industries. Learn how these cells facilitate precise chemical reactions and their role in high-purity metal production.
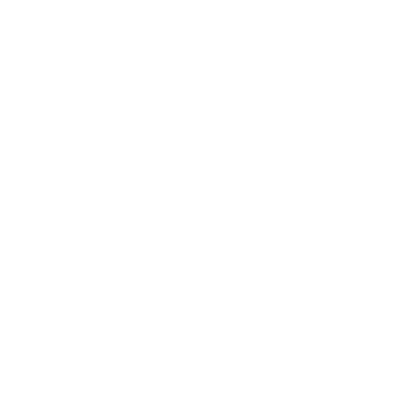
Comprehensive Overview of Zirconia Ceramic Materials
A detailed exploration of zirconia ceramics, including properties, history, preparation, molding, sintering, and applications.