Introduction
Table of Contents
- Introduction
- Understanding Isostatic Presses and their Types
- Applications of Isostatic Presses
- Operational Details of Cold Isostatic Presses
- Advantages of Cold Isostatic Presses
- Varieties of Cold Isostatic Presses
- Operation and Uses of Hot Isostatic Presses
- Additional Applications of Hot Isostatic Presses
- Types of Hot Isostatic Presses
- Conclusion
Isostatic presses play a crucial role in various industries, offering unique capabilities for material consolidation and product creation. These powerful machines apply equal pressure from all directions, resulting in products with uniform density and reduced defects. Isostatic presses are divided into two main types: Cold Isostatic Presses (CIP) and Hot Isostatic Presses (HIP). Each type functions under different conditions, allowing for a wide range of applications. In this article, we will delve into the types, applications, and advantages of isostatic presses, providing an in-depth understanding of their operational details and uses in different industries. So, let's explore the world of isostatic presses!
Understanding Isostatic Presses and their Types
The two main types: Cold Isostatic Presses (CIP) and Hot Isostatic Presses (HIP)
Isostatic pressing is a process involving the application of equal pressure to a compacted powder to achieve optimal density and microstructure uniformity. There are two main types of isostatic presses: Cold Isostatic Presses (CIP) and Hot Isostatic Presses (HIP).
Cold Isostatic Pressing (CIP)
Cold Isostatic Pressing involves subjecting a material to uniform pressure from all sides by immersing it in a high-pressure fluid medium and applying hydraulic pressure. This method is particularly effective for shaping and consolidating powdered materials, creating intricate shapes, and achieving high green density. CIP is often used for shaping and initial consolidation of powdered materials.
Hot Isostatic Pressing (HIP)
Hot Isostatic Pressing takes the process a step further by combining high pressure with elevated temperatures. This method subjects a material to simultaneous high pressure and high temperature within a high-pressure chamber. HIP is used to densify materials, eliminate defects, and enhance properties through diffusion and consolidation. It is especially valuable for materials requiring improved structural integrity, reduced porosity, and higher mechanical properties.
Different conditions in which CIP and HIP function
The key differences between Cold Isostatic Pressing (CIP) and Hot Isostatic Pressing (HIP) lie in the pressure and temperature conditions under which they operate, as well as their applications.
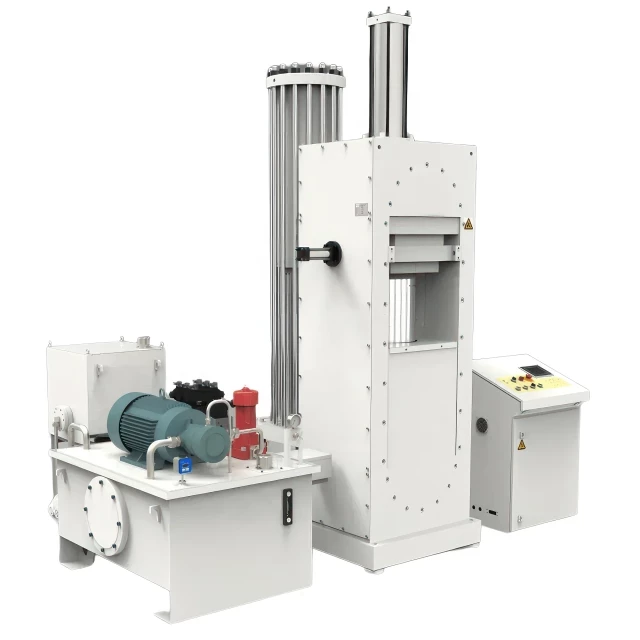
Pressure and Temperature
CIP involves cold compaction using isostatic pressure, while HIP employs both high pressure and high temperature to achieve densification and enhanced properties.
Applications
CIP is often used for shaping and initial consolidation of powdered materials. It is suitable for creating intricate shapes and achieving high green density.
HIP, on the other hand, is favored for creating high-performance materials with superior mechanical properties and structural integrity. It is used to densify materials, eliminate defects, and enhance properties through diffusion and consolidation. HIP is particularly valuable for materials that require improved structural integrity, reduced porosity, and higher mechanical properties.
In summary, Cold Isostatic Pressing and Hot Isostatic Pressing represent distinct approaches to materials processing, each with its own advantages. The decision between the two depends on the specific goals of your project and the characteristics of the materials involved.
Other industries that apply isostatic press include pharmaceuticals, explosives, chemicals, nuclear fuel, and ferrites.
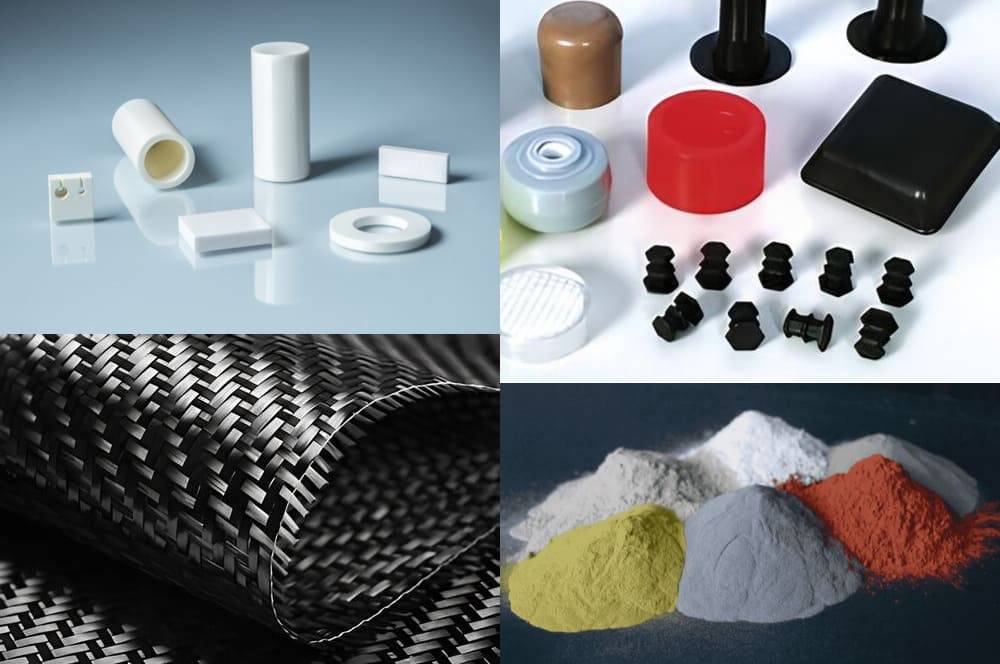
Applications of Isostatic Presses
Use in consolidation of various materials
Isostatic pressing is a technique used to consolidate powders or defect healing of castings in various industries. It can be applied to a range of materials such as ceramics, metals, composites, plastics, and carbon. The process applies a uniform, equal force over the entire product, regardless of its shape or size. This makes it particularly advantageous for ceramic and refractory applications. Isostatic pressing allows for the formation of product shapes with precise tolerances, reducing the need for costly machining.
Additional processing required for cold pressed metals and ceramic powder compacts
Cold isostatic pressing is a specific method within isostatic pressing that involves compacting a powder in an elastomeric container submerged in a fluid at high pressure. This technique is used for powders that are difficult to press, such as hard metals. Cold isostatic pressing allows for the production of simple-shaped small or large powder compacts with a uniform green density. However, it may require subsequent machining in the green compact due to slower pressing speeds and less dimensional control compared to other pressing methods.
The variety of products created via cold isostatic pressing
Cold isostatic pressing is particularly advantageous for producing parts where the high initial cost of pressing dies cannot be justified or when very large or complex compacts are needed. It can be used for a variety of powders, including metals, ceramics, plastics, and composites. The pressures required for compacting range from less than 5,000 psi to more than 100,000 psi. Cold isostatic pressing allows for the production of a wide range of ceramic products, such as balls, tubes, rods, nozzles, fuse tubes, teeming tubes, lighting tubes, grinding wheels, and more.
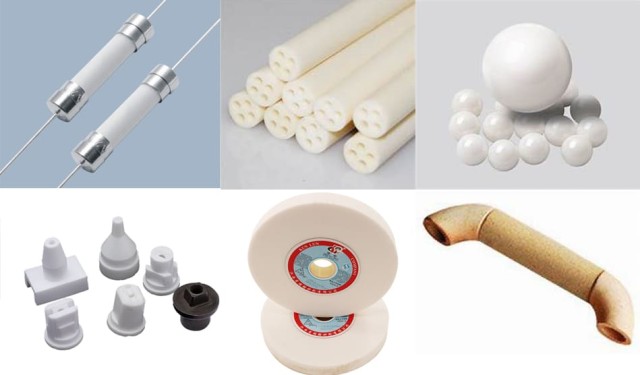
Isostatic pressing offers several advantages, including the ability to achieve high and uniform density, the removal of constraints on part geometry, and efficient material utilization. Some common applications of isostatic presses include pharmaceuticals, explosives, chemicals, food, and nuclear fuel ferrites.
Operational Details of Cold Isostatic Presses
The role of molds and processing chambers in CIP
Cold isostatic pressing (CIP) services utilize molds and processing chambers to achieve the desired density and shape of the final product. These molds, made of rubber or elastomer, encase the powder materials and provide low deformation resistance. The liquid pressure medium, such as water or oil, evenly distributes pressure throughout the mold, resulting in uniform compression of the molded body. This process allows for the creation of net or near-net shape parts, reducing the need for excessive material removal through machining.
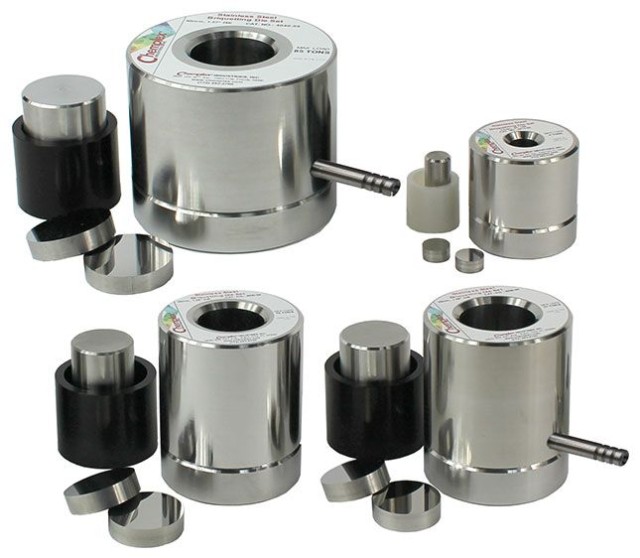
The pressurization process and the role of the liquid medium
During cold isostatic pressing, the powder materials enclosed in the mold are subjected to high pressure at room temperature or slightly higher. Pressures ranging from 100-600 MPa are applied using a liquid medium. The liquid medium, acting as an incompressible fluid, transmits the pressure undiminished to every part of the mold and the surface of its container. This uniform compression ensures the formation of a "raw" part with sufficient strength for handling and further processing.
The choice of liquid medium, whether water, oil, or a glycol mixture, depends on the specific requirements of the materials being processed. Cold isostatic pressing achieves a theoretical density of about 100% for metals and approximately 95% for ceramic powders. By utilizing the liquid medium and the encasing mold, CIP provides a method for forming powdered materials at room temperature, serving as a precursor to sintering or hot isostatic pressing processes.
Maximum pressure achievable with CIP
The maximum pressure achievable with cold isostatic pressing depends on the design and capabilities of the equipment used. Cold isostatic pressing equipment is available in various sizes, ranging from laboratory units with an inner diameter as small as 77 mm (3") to larger units exceeding 2m (6 ft) in width. Operational pressure levels of up to 900 MPa (130,000 psi) can be achieved.
Custom-designed CIP systems offer highly specialized solutions for specific applications. These systems can feature automated loading and unloading systems, high pressurization rates, and customized depressurization profiles. However, standard off-the-shelf solutions are also available for more general requirements.
In conclusion, cold isostatic pressing services utilize molds, processing chambers, and a liquid medium to achieve uniform compression and desired densities of powdered materials. The pressurization process and the choice of liquid medium play crucial roles in ensuring the strength and quality of the formed parts. With a wide range of equipment options and customizable systems, cold isostatic pressing offers a versatile method for shaping and densifying materials.
Advantages of Cold Isostatic Presses
Creation of products with uniform density
Cold isostatic pressing (CIP) offers the advantage of producing products with uniform density distribution. This ensures that the resulting compacted piece will have consistent shrinkage during sintering or hot isostatic pressing, with little to no warpage. The uniform density also contributes to greater homogeneity and more precise control of the finished product dimensions.
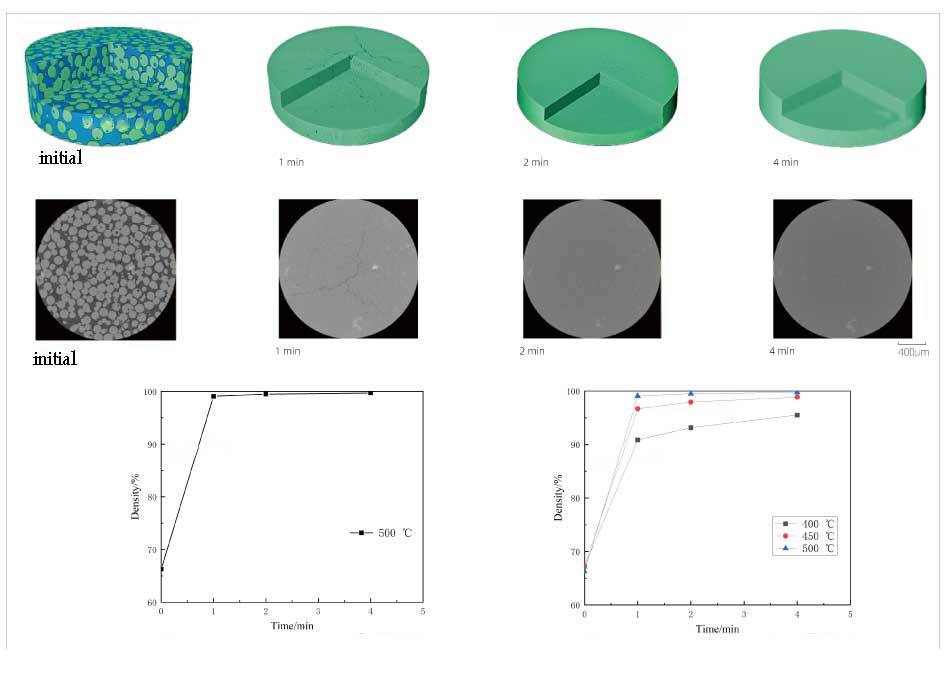
Reduction of internal stresses and elimination of defects
By using cold isostatic pressing, internal stresses and defects can be minimized or eliminated. The isostatic pressing technique allows for the removal of human error, reducing any pressing flaws. This results in products with improved compaction of the powder, leading to improved densification and enhanced mechanical properties.
Production of products with higher green strength
Cold isostatic pressing offers increased possibilities for machining the compact in its green state. The high green strength of the compact allows for in-process handling and treatment, reducing production costs. Additionally, the green strength permits the processing of difficult-to-press materials, as powders can be isostatically pressed dry without the need for water, lubricants, or binders.
Economic benefits of the CIP process
The CIP process offers several economic benefits. Firstly, it allows for the fabrication of near-net shape parts, greatly reducing material and machining costs. The low tooling cost, especially for short production runs, makes it a cost-effective manufacturing method. Moreover, the reduced lead times for complex shapes, from prototype to production quantities, further contribute to cost savings.
According to a detailed report by DataIntelo, the Global Cold Isostatic Pressing (CIP) Equipment Market is projected to grow with a substantial CAGR, during the forecast period, 2020-2026. The expected growth can be attributed to the surge in demand for CIP-processed products in several industries, consisting of precision manufacturing, aerospace & defense, and automotive.
In addition to the advantages of cold isostatic pressing, there are also merits of the CIP process itself. High compaction and uniform density offer predictable compression during the subsequent sintering process. The process has the ability to process large, complicated, and perfect shapes, saving time and cost during after-treatment. It can generate large aspect ratio parts with uniform densities, and the green strength permits in-process handling and treatment, reducing production costs.
Overall, cold isostatic presses offer numerous advantages in the manufacturing of products with uniform density, reduced internal stresses, higher green strength, and economic benefits. These advantages make cold isostatic pressing a valuable technique for various industries, leading to its growing demand in the market.
Varieties of Cold Isostatic Presses
Different styles for industrial and laboratory applications
Cold isostatic pressing (CIP) is a materials processing technique that offers distinct advantages for both industrial and laboratory applications. There are different styles of cold isostatic presses available, each with its own unique features and benefits.
One popular style of cold isostatic press is the wet bag method. In this process, the powder material is placed into a forming mold, also known as the casing, and then sealed. The mold is then submerged in a high-pressure cylinder filled with liquid, allowing for direct contact with the pressure transmission medium. Wet bag isostatic pressing is highly versatile and is particularly suitable for experimental research and small batch production. It can also accommodate multiple different shapes of parts in one high-pressure cylinder, making it ideal for producing large and complex parts. Additionally, the wet bag process is known for its shorter production time and lower cost.
Another style of cold isostatic press is the dry bag method. In this process, an elastomeric tool is attached to a pressure vessel, and the process is automated, allowing for high-volume production of relatively simple shapes. The elastomer tool is filled and sealed outside the pressure vessel, then loaded into the vessel, pressurized, unloaded, and finally extracted from the tool for further post-processing. The dry bag method is less manual compared to the wet bag method and is suitable for producing a large quantity of relatively simple shapes.
Specific CIP processes including wet bag processing, dry bag processing, and warm isostatic pressing
Cold isostatic pressing (CIP) encompasses various specific processes, including wet bag processing, dry bag processing, and warm isostatic pressing.
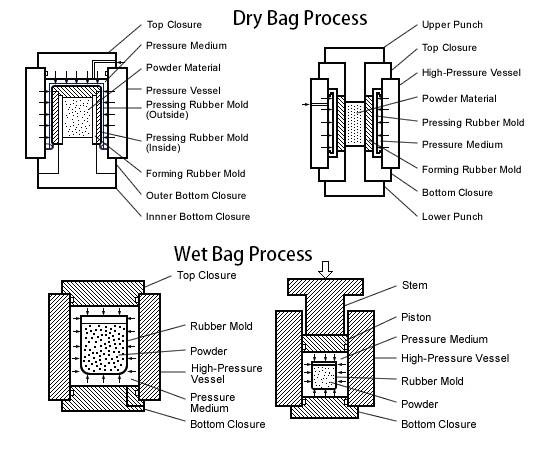
In wet bag processing, the powder material is enclosed in a flex mold bag, which is then submerged into a high-pressure liquid in a pressure vessel. Isostatic pressure is applied to the outer surfaces of the mold, compressing the powder into the desired shape. This process is particularly useful for producing parts with multiple shapes and for both small and large quantity production. Wet bag processing is also suitable for pressing large products.
Dry bag processing, on the other hand, involves attaching an elastomeric tool to a pressure vessel and automating the process. This allows for high-volume production of relatively simple shapes. The elastomer tool is filled and sealed outside the pressure vessel before being loaded into the vessel, pressurized, unloaded, and finally extracted for post-processing.
Warm isostatic pressing is another specific CIP process where the pressing is performed at elevated temperatures. This allows for the consolidation of metal and ceramic powders. Warm isostatic pressing offers the advantage of achieving denser and stronger parts compared to cold isostatic pressing.
Overall, the choice between different styles and specific CIP processes depends on the specific goals of your project and the characteristics of the materials involved. Wet bag processing is suitable for experimental research and small batch production, while dry bag processing is ideal for high-volume production of simple shapes. Warm isostatic pressing offers the advantage of achieving denser and stronger parts.
Operation and Uses of Hot Isostatic Presses
Use of gas mixtures and high temperature in HIP
Hot isostatic pressing (HIP) is a material processing method that compresses materials by applying high temperature and isostatic pressure simultaneously. It uses gas mixtures, typically argon, as the pressure medium. HIP can reach temperatures of several hundreds to 2000°C and pressures of several tens to 200MPa.
HIP equipment comes in various sizes, with compact machines used for small parts and industrial-sized equipment for large industrial parts. The components to be pressed are loaded into the machine's chamber, which can be loaded from the top or bottom depending on the machine. Computers program the equipment to produce the desired results, allowing users to control the temperature ramp-up, pressure, and duration of the process.
Functioning of HIP by increasing temperature and pressure simultaneously
Hot isostatic presses use gas mixtures, such as argon, heated up to 3000º F and pressurized up to 100,000 psi to process powders and other materials into dense preformed metals, plastics, and ceramics. The HIP process involves introducing gas into the HIP furnace and simultaneously increasing the temperature and pressure. This combination adds density to the materials being processed.
HIP functions by subjecting the materials to equal pressure in all directions, allowing voids to collapse and surfaces to diffusion bond together. This eliminates defects and achieves near theoretical density in the processed materials. HIP is particularly effective in processing high-performance ceramics, ferrites, cemented carbides, nickel-base super alloys, titanium powders, high-speed tool steel, and for diffusion bonding of similar and dissimilar materials.
Applications of HIP in processing high-performance ceramics, ferrites, and cemented carbides, among others
Hot isostatic pressing (HIP) has a wide range of applications in various industries. It is used in automotive, aerospace, military, heavy equipment, industrial machinery, marine, oil and gas, and medical sectors.
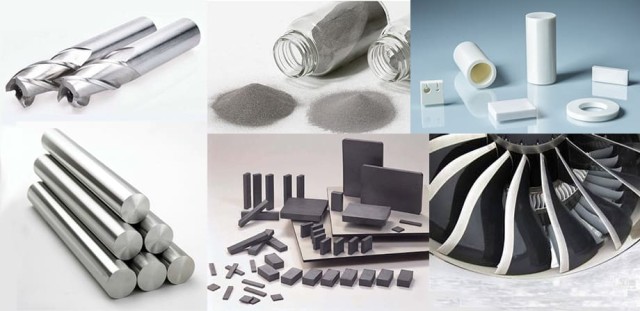
In powder metallurgy, HIP allows the compression of metal powders at high temperatures and pressures, creating a product with a homogenous annealed microstructure and minimal impurities. HIP is crucial in through-processing, from alloy design to component manufacture, and is essential for aerospace components. The HIP process can be scaled up using equipment with a 150mm diameter x 300mm long hot zone.
Hot isostatic pressing equipment consists of a high-pressure vessel, heating furnace, compressor, vacuum pump, storage tank, cooling system, and computer control system. The high-pressure vessel is the key device in the equipment.
Overall, hot isostatic pressing (HIP) is a valuable process for increasing the density of materials, eliminating defects, and improving mechanical properties in various applications and industries.
Additional Applications of Hot Isostatic Presses
Hot isostatic pressing (HIP) is a versatile manufacturing process that offers several additional applications beyond its traditional use in net-shape forming, compacting of high-speed tool steel, and bonding. This article explores some of these applications and highlights the advantages of using hot isostatic presses in various industries.
Elimination of Voids in Aerospace Castings
One of the key benefits of hot isostatic pressing is its ability to eliminate voids in castings, particularly in the aerospace industry. Voids, also known as porosities, are small holes or impurities that can negatively impact the quality and performance of metal parts. By subjecting castings to high temperature and isostatic gas pressure, hot isostatic pressing removes these voids, resulting in higher quality and more reliable aerospace castings.
Removal of Defects from Castings and Treatment of Creep Damaged Products
In addition to eliminating voids, hot isostatic pressing can also be used to remove other defects from castings and treat creep damaged products. Creep refers to the gradual deformation of materials under constant stress, which can lead to structural failures in high-temperature applications. By subjecting creep damaged products to hot isostatic pressing, the defects can be repaired and the material's performance can be restored.
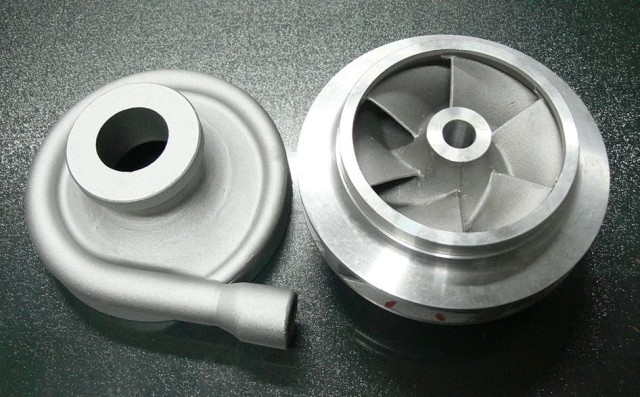
Expansion into Ceramic Additive Manufacturing
Interest in ceramic additive manufacturing has been steadily increasing in recent years, particularly in the aerospace and automotive sectors. Hot isostatic pressing is expected to play a significant role in this field as it offers a viable solution for consolidating and heat treating ceramic materials. With its ability to create fully dense materials and bond similar and dissimilar materials together, hot isostatic pressing is well-suited for the manufacturing of unique and cost-effective ceramic components.
Advantages of Hot Isostatic Pressing Tools
Hot isostatic pressing tools offer several advantages in various industries. Here are some of the key benefits:
-
High and Uniform Density: Hot isostatic pressing allows for the compaction of powder materials with high and uniform density in all directions. This results in improved material performance and stability.
-
Greater Design Flexibility: Unlike traditional forming methods, hot isostatic pressing removes the constraints on part geometry imposed by rigid dies. This opens up possibilities for creating complex shapes and intricate designs.
-
Efficient Material Utilization: Hot isostatic pressing is highly efficient in utilizing difficult-to-compact and expensive materials such as superalloys, titanium, and stainless steel. This reduces material waste and improves cost-effectiveness.
In conclusion, hot isostatic presses have additional applications beyond their traditional uses in net-shape forming, compacting of high-speed tool steel, and bonding. From eliminating voids in aerospace castings to treating creep damaged products and enabling ceramic additive manufacturing, hot isostatic pressing offers a versatile solution for improving material performance and creating high-quality components. With its numerous advantages, hot isostatic pressing tools are a valuable asset in various industries.
Types of Hot Isostatic Presses
Different styles for laboratory and industrial needs
Hot Isostatic Pressing for metal Additive Manufacturing
Cold Isostatic Pressing
The design and manufacture of these presses typically includes programmable controls, allowing users to press products more accurately, consistently and according to specific requirements. Though many lab presses are fit for the countertop, there are also many floor standing presses available. Either way, it is not uncommon to find laboratory presses designed with two-columns and four-columns and that press either manually or automatically.
With such a vast selection of laboratory presses out in the market, it could become confusing as to which one is best suited for a particular job. An important factor to remember when choosing this particular kind of hydraulic press is how much force is needed for a specific sample? It is also necessary to consider how much space is provided in the lab, how much energy and strength is required to pump the press and whether or not the press will have to move.
Cold isostatic presses, warm isostatic presses, and hot isostatic presses are a type of equipment that uses high-pressure gases to process materials. They are based on the principle of heating or cooling the gas to a certain temperature and then applying a uniform pressure to the material through a closed vessel. This method can improve the density, structure and properties of materials and is suitable for ceramics, metals, composites, etc.
The main difference between cold isostatic presses, warm isostatic presses and hot isostatic presses is their high and low temperatures during forming and consolidation. Cold isostatic presses are generally used in room temperature environments and are suitable for temperature sensitive materials such as ceramics, metal powders, etc. Warm isostatic presses work at medium temperature and are suitable for materials with certain requirements on temperature, such as plastics, rubber, etc. The working temperature of hot isostatic press is high temperature, suitable for materials with high temperature requirement, such as metals, alloys, etc.
In summary, Cold Isostatic Pressing and Hot Isostatic Pressing represent distinct approaches to materials processing, each with its own advantages. The decision between the two depends on the specific goals of your project and the characteristics of the materials involved.
Other industries that applied isostatic press include: pharmaceuticals, explosives, chemicals, nuclear fuel Ferrites. There are two main types of isostatic presses; cold isostatic presses (CIP) that function at room temperature and hot isostatic presses (HIP) that function at elevated temperatures.
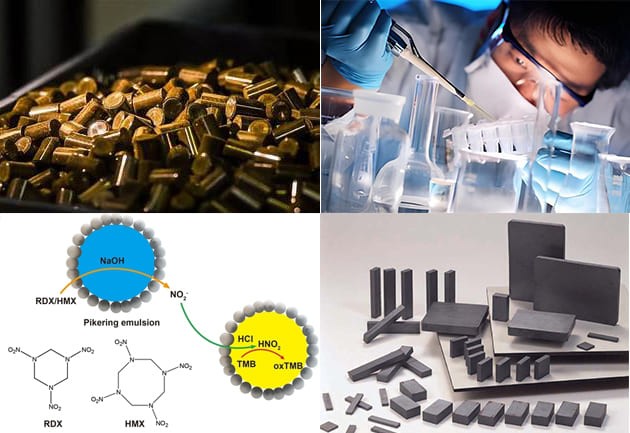
Conclusion
In conclusion, isostatic presses, both cold and hot, offer a wide range of applications and advantages in various industries. Cold isostatic presses (CIP) are known for their ability to create products with uniform density, reduced internal stresses, and higher green strength. They also provide economic benefits through their efficient manufacturing process. On the other hand, hot isostatic presses (HIP) utilize gas mixtures and high temperatures to process materials like ceramics and cemented carbides. They are highly effective in eliminating defects, bonding, and shaping high-speed tool steel. Overall, isostatic presses play a crucial role in achieving high-quality products with consistent performance.
If you are interested in this product you can browse our company website:https://kindle-tech.com/product-categories/isostatic-press, as an industry-leading laboratory equipment manufacturer, we are committed to providing the most advanced and high-quality laboratory equipment solutions. Whether you are engaged in scientific research, teaching or industrial production, our products will meet your needs for accurate and reliable laboratory equipment.
CONTACT US FOR A FREE CONSULTATION
KINTEK LAB SOLUTION's products and services have been recognized by customers around the world. Our staff will be happy to assist with any inquiry you might have. Contact us for a free consultation and talk to a product specialist to find the most suitable solution for your application needs!