Principle of Cold Isostatic Pressing (CIP)
Table of Contents
Understanding the principle of CIP based on Blaise Pascal's concept of pressure
Cold isostatic pressing (CIP) is a method of processing materials that is based on the principle proposed by Blaise Pascal, known as Pascal's law. According to this principle, pressure applied in an enclosed fluid is transmitted in all directions throughout the fluid without any change in magnitude.
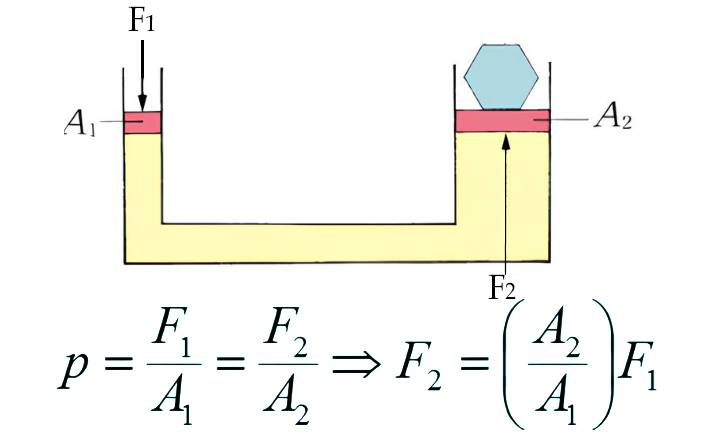
In CIP, powders are compacted by enclosing them in an elastomer mold, which has low resistance to deformation. The mold is then subjected to uniform liquid pressure, which compresses the powders. This results in the formation of a highly compact solid.
CIP can be used for processing a variety of materials, including plastics, graphite, powdered metallurgy, ceramics, and sputtering targets. It is a versatile method for shaping and compacting powders into components of varying sizes and shapes.
Process of powder materials being sealed in a forming mold and application of liquid pressure
In the CIP process, powder materials are sealed in a forming mold with low deformation resistance, such as a rubber bag. Liquid pressure is then applied to the mold uniformly, compressing the powders. This liquid pressure is transmitted throughout the mold, resulting in the uniform compression of the molded body over its entire surface.
CIP is performed at room temperature and uses a mold made from an elastomer material, such as urethane, rubber, or polyvinyl chloride. The fluid used in CIP is usually oil or water, and the pressure applied during the operation typically ranges from 60,000 lbs/in2 (400 MPa) to 150,000 lbs/in2 (1000 MPa).
The advantage of CIP is that it helps reduce distortion, improve accuracy, and minimize the risk of air entrapment and voids. It is widely used in various industries, including medical, aerospace, and automotive, for the production of components.
Metal mold pressing is a similar method to CIP. In this process, powder materials are filled into a space confined by the metal mold and the lower punch. They are then compressed by narrowing the distance between the upper and lower punches.
Overall, CIP is an effective method for shaping and compacting powdered materials into solid components, providing a high level of accuracy and reducing the risk of defects.
Comparison between CIP and Metal Mold Pressing
Introduction to Metal Mold Pressing
Metal mold pressing is a material processing method that is similar to Cold Isostatic Pressing (CIP). In this pressing method, powder materials are filled into a space enclosed by the metal mold and the lower punch. They are then compressed by narrowing the distance between the upper and lower punches.
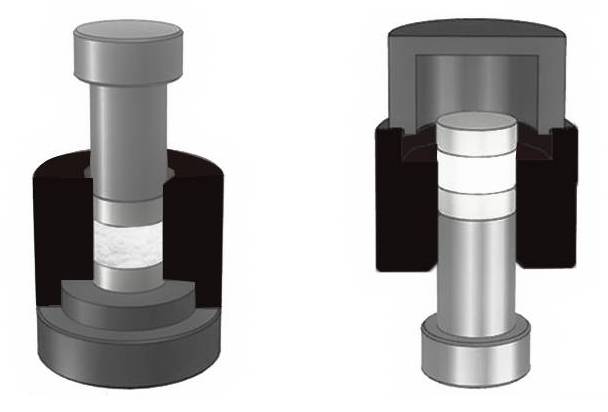
Automated processes in industrial metal mold pressing equipment
Metal mold pressing equipment used in industrial settings consists of a series of automated processes. These processes include powder filling, compression, and the removal of the molded body. Single-acting pressing, a common method used, compresses the powder into shape with the lower punch fixed.
Differences in pressurization processes of CIP and Metal Mold Pressing
The main difference between CIP and metal mold pressing lies in the pressurization processes they utilize. CIP applies isostatic pressure to materials using liquid pressure, while metal mold pressing applies only uniaxial pressure. This difference results in the production of products with different density distributions.
Comparison of density distribution in products molded by CIP and Metal Mold Pressing
CIP produces products with a uniform density and homogeneity due to the absence of frictions with a metal mold. On the other hand, metal mold pressing can result in variations in density distribution. The lower part of a molded body produced by metal mold pressing tends to have a lower density compared to its upper part. This is due to the frictions between the powder and the metal mold or the punch, as well as between powder particles.
In summary, both CIP and metal mold pressing are material processing methods used in various industries. While they share similarities, such as the use of powder materials and compression, they differ in their pressurization processes and the resulting density distribution in the molded products. CIP offers a uniform density and homogeneity, while metal mold pressing may result in variations in density.
Types of CIP Processing
The CIP molding methods are classified into two types; the wet bag process and the dry bag process, according to the relationship between a forming mold for filling powder and a pressure medium for transmitting pressure.
Wet Bag Process
In the wet bag process, as shown in the figure below, powder is filled in a forming mold and sealed airtight outside the high-pressure vessel before direct immersion into a pressure medium. Then, isostatic pressure is applied to the outer surfaces of the mold to compress the powder into a shape. This method is suitable for various kinds of small-quality production for complicated-shape or large-scale products and trial production research.
Limitations:
- Cycle Time: 5-30 min for wet bag
- Cold (room temperature)
- Uniform green density
- Slower than uniaxial pressing
- Waxless, complex shapes
- Parts may require post-machining
Dry Bag Process
In the dry bag process, automated, one part at a time, the powder is filled in a forming mold and sealed airtight inside the high-pressure vessel. Then, the pressure medium is introduced into the pressure vessel and isostatic pressure is applied to the outer surfaces of the mold to compress the powder into a shape. This method is suitable for producing different-shaped parts in a cost-effective manner.
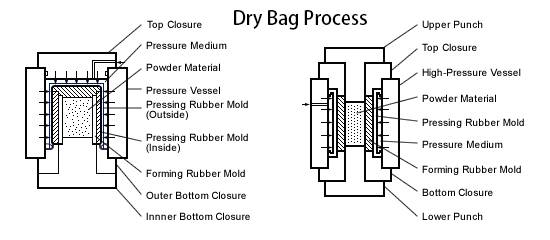
Limitations:
- Cycle Time: 3-5 min
- Warm (100°C)
- Eliminates post-sintering
- Hot (2200°C)
- Improves mechanical and physical properties
- Cycle times can be slow: 10-15 h
- Near net shape
- Full density
Wet-Bag CIP
Two types of CIP methods have evolved over the years: wet-bag and dry-bag. The so-called wet-bag method is used for producing mixed shapes. It is estimated that there are more than 3000 wet-bag presses in use worldwide today, ranging in size from 50 to 2000 mm in diameter.
Applications of the CIP Process
As a near-net-shape processing technology, CIP is typically used in the following applications:
- Applications where the material is relatively expensive and therefore minimizing waste (e.g. in the form of machining swarf) by using a near-net-shape process would offer a significant economic and environmental advantage.
- Applications where materials are difficult to machine, and it is more viable to shape the part through powder-processing.
- Applications where the geometrical complexity of the part requires expensive tooling (e.g. sacrificial canisters in HIP). CIP utilizes relatively inexpensive reusable (or potentially disposable) flexible tools that allow for complex shapes to be produced.
- Applications where uniformity and homogeneity of microstructure is required to achieve specific mechanical performance. Processing powders isostatically offers a relative advantage over other processes, such as uniaxial pressing or casting.
- Applications where multi-materials or graded structures are required. In some applications traditional joining techniques are not suitable, so CIP offers a solid-state joining process.
Although the CIP process was developed many years ago, commercial applications for metals have been relatively limited. Traditional applications focused on preforms and relatively simple shapes, such as tubular or solid parts with high aspect ratios, such as pipes, hydraulic pressure fittings, and vessel liners with thin walls. Recently, CIP has been considered for relatively advanced applications across high-value sectors. For example, automotive applications include forging preforms for connecting rods and aluminum components of the vehicle cam phaser system. Aerospace applications include regeneratively cooled thrust chambers. Power generation applications include fission reactor parts, structural components of nuclear reactors, and oxide dispersion strengthened ferritic alloys used for fuel cladding or structural materials in future nuclear systems. Defense applications include missile warhead casings. CIP+HIP was implemented to make Stinger missile warhead casings (with production volumes up to).
Segmentation of the Market
Based on product type, the cold isostatic pressing (CIP) equipment market is bifurcated into:
- Wet Bag Pressing
In the wet bag process, the powder material is enclosed in a flex mold bag, which is submerged into a high-pressure liquid in a pressure vessel. Then, isostatic pressure is applied to the outer surfaces of the mold to compress the powder into a shape. This process is ideal for multi-shape and small to large quantity production, and the pressing of large products.
Both the CIP and HIP process use multi-material constructs: polymer shells with ceramic powders in CIP, and welded mild steel sheet material casing with high-end powder metallurgy alloys in HIP. Both methods thus present an opportunity for single step pre-processing of constructs via multi-material additive manufacturing. This approach could be particularly beneficial for producing small series or prototypes, and might even decrease manufacturing costs by allowing for increased part complexity with fewer processing steps and time.
Details of Wet Bag Process
Explanation of the Wet Bag Process
Wet bag technology is a method used to mold powder by filling it in a mold and sealing it tightly. The mold is then submerged in a pressure fluid within a pressure vessel. Isostatic pressure is applied to the external surface of the mold, compressing the powder into a solid mass. This process is suitable for multi-shape and small to large quantity production.
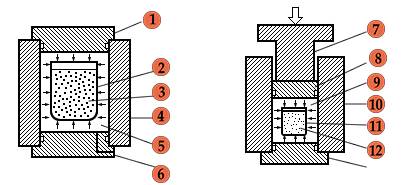
The wet bag process is not as common as the dry bag process, but it is still widely used. There are over 3000 wet bag presses in use worldwide today, ranging in size from 50mm to 2000mm in diameter. High-volume pumps and improved loading mechanisms can help to speed up the process, which typically takes from 5 to 30 minutes to complete.
Suitability of Wet Bag Process for various types of production
The wet bag process is suitable for various types of production, especially for complicated-shaped or large-scale products and trial production research. It allows for the production of products with complex shapes that may be difficult to achieve using other methods. This process is also suitable for small-quantity production and can be used for mass production as well.
Structural types of Wet Bag Process: external pressurization type and piston direct pressurization type
There are two structural types of the wet bag process: the external pressurization type and the piston direct pressurization type.
The external pressurization type involves pressurizing the pressure medium into the pressure vessel from outside. The pressure medium is applied externally to the mold, compressing the powder inside.
The piston direct pressurization type, on the other hand, directly pressurizes the pressure medium sealed inside the high-pressure vessel with a piston installed instead of the top closure. This type of wet bag process eliminates the need for external pressurization, making it more efficient.
Overall, the wet bag process offers a unique method for molding powder and is suitable for various types of production. It allows for the production of complex-shaped products and can be used for both small-quantity and mass production. The two structural types of the wet bag process provide flexibility and efficiency in the molding process.
Details of Dry Bag Process
Explanation of Dry Bag Process
Dry Bag process is a method to mold powder filled in a forming rubber mold by transmitting pressure through a pressing rubber mold in the high-pressure vessel. This method is suitable for mass production of simple and limited variety of products with its labor-saving automatic operation.
Suitability of Dry Bag Process for mass production
Dry Bag pressing is different from wet bag in a way that a flexible membrane is made into the pressure vessel and is utilized during all pressing cycles. This membrane secludes the pressure fluid from the mold, which becomes a "dry bag." This process is a lot cleaner due to the flex mold does not become contaminated with wet powder. Moreover, less cleaning of the vessel is needed. This method has rapid cycles and is very ideal for automated mass production of powder products.
Classification of Dry Bag Process systems: circumferential + axial pressurization system and circumferential pressurization system
The Dry Bag process is classified into two systems: the circumferential + axial pressurization system and the circumferential pressurization system. The circumferential + axial pressurization system involves pressurizing the pressure medium into the pressure vessel from outside, while the circumferential pressurization system directly pressurizes the pressure medium sealed inside the high-pressure vessel with a piston installed instead of the top closure.
Dry Bag technology is ideal for the mass production of materials. This process usually takes as little as 1 minute, making it much faster than wet bag technology.
If you are interested in our products, please visit our company website:https://kindle-tech.com/product-categories/isostatic-press, where innovation has always been a priority. Our R&D team consists of experienced engineers and scientists who closely follow industry trends and are constantly pushing the boundaries of what is possible. Our laboratory equipment incorporates the latest technology to ensure that you can obtain accurate and repeatable results during your experiments. From high-precision instruments to intelligent control systems, our products will provide you with unlimited possibilities for your experimental work.
CONTACT US FOR A FREE CONSULTATION
KINTEK LAB SOLUTION's products and services have been recognized by customers around the world. Our staff will be happy to assist with any inquiry you might have. Contact us for a free consultation and talk to a product specialist to find the most suitable solution for your application needs!