Introduction to Warm Isostatic Pressing
Warm Isostatic Pressing (WIP) is a process used to eliminate porosity and improve the mechanical properties of materials. In this process, the material is subjected to high pressure and temperature in an inert gas environment. The pressure is applied uniformly on all sides of the material, which ensures that there are no voids or pores in the final product. WIP is commonly used in the production of aerospace components, medical implants, and other high-performance materials. The benefits of WIP include improved strength, increased ductility, and enhanced fatigue life. Understanding the temperature requirements for WIP is crucial to achieving optimal results.
Table of Contents
Benefits of Warm Isostatic Pressing
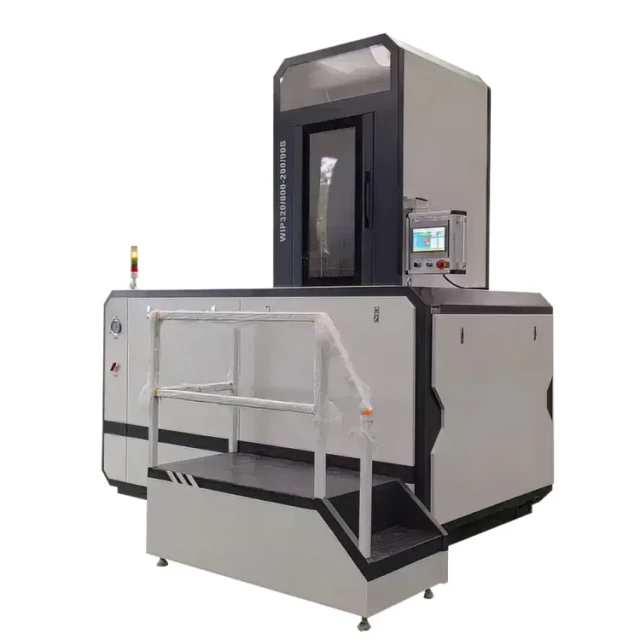
Warm isostatic pressing (WIP) is a highly beneficial technique for consolidating and shaping materials. Here are some of the advantages of using WIP:
Increased Material Density
WIP can significantly increase the density of materials, resulting in a more robust and durable final product. By applying high-pressure compression uniformly from all sides, WIP eliminates any voids or porosity in the material, resulting in a denser structure.
Improved Strength
WIP enhances the strength properties of the final product, making it more resistant to wear and tear. The high-pressure compression applied by WIP results in a more compact and uniform structure, which increases the material's strength, toughness, and ductility.
Better Corrosion and Wear Resistance
WIP can improve the material's resistance to corrosion and wear. By compressing the material uniformly, WIP eliminates any weak spots or defects, making the material more resistant to damage caused by corrosion or wear and tear.
Improved Surface Finish
WIP can also improve the surface finish of parts, resulting in a smoother and more uniform appearance. By eliminating any voids or porosity in the material, WIP results in a more uniform surface texture, reducing the need for secondary finishing processes.
Reduced Residual Stresses
WIP can reduce the residual stresses in the final product, resulting in a more stable and reliable structure. By applying high-pressure compression uniformly from all sides, WIP eliminates any internal stresses in the material, reducing the risk of cracking or deformation.
Overall, using WIP can result in a more robust, durable, and high-quality final product, making it an excellent choice for a wide range of applications.
Understanding Temperature in Warm Isostatic Pressing
Warm isostatic pressing is a technique used to eliminate voids or defects in materials by applying high pressure and high temperature. When it comes to warm isostatic pressing, temperature plays a crucial role in determining the success of the process. Choosing the appropriate temperature for the material being processed is essential to achieve a successful outcome.
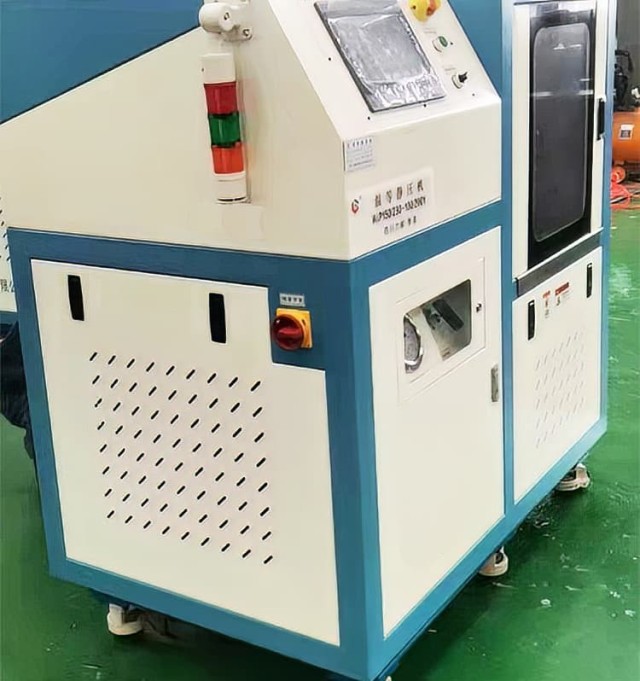
Importance of Temperature in Warm Isostatic Pressing
To choose the right temperature for warm isostatic pressing, it is important to consider the material being processed and its specific properties. Different materials require different temperatures, and choosing the wrong temperature can lead to poor results. Generally, the temperature range for warm isostatic pressing is between 50°C to 200°C, depending on the material and the desired outcome.
Constant Temperature Throughout the Process
The temperature should be constant throughout the process to ensure uniformity in the end product. Additionally, the temperature should be monitored and controlled carefully to prevent overheating or underheating, which can result in damage to the material or equipment.
Heating Medium
Warm isostatic pressing uses a special liquid or gas as the pressure transfer medium (generally at temperatures between 80 and 120°C). The medium can be heated outside the high-pressure cylinder (i.e. in the supply tank), or inside the high-pressure cylinder when precise temperature control is required. The medium can also be heated inside the high-pressure cylinder with a heat generator. Usually, the oil heated in the supply tank is used to maintain the oil temperature at a stable level, or the oil is heated and cooled according to the process requirements.
Conclusion
In conclusion, understanding the importance of temperature in warm isostatic pressing and choosing the appropriate temperature for the material being processed are essential steps to achieving a successful outcome. The temperature should be constant throughout the process and monitored and controlled carefully to prevent overheating or underheating. The heating medium is also an important consideration in warm isostatic pressing. By following these guidelines, the warm isostatic pressing process can provide isotropic, ultra-high molding pressure for products and deliver compressed bodies of higher quality than those manufactured by the conventional uniaxial press method.
Factors to Consider When Choosing the Right Temperature
When it comes to using a warm isostatic press, choosing the right temperature is crucial for achieving successful results. Here are some factors to consider when selecting the appropriate temperature for your particular application:
Material being used
Different materials will have different optimal temperatures at which they can be effectively processed using a warm isostatic press. It is important to take into account the material being used when selecting the appropriate temperature.
Desired outcome of the process
The desired outcome of the process should be taken into account. If the goal is to achieve maximum density, a higher temperature may be necessary. On the other hand, if preserving the integrity of the material is of utmost importance, a lower temperature may be more appropriate.
Equipment being used
Not all warm isostatic presses are created equal, and some may have limitations on the range of temperatures that can be achieved. It is important to ensure that the chosen temperature falls within the capabilities of the equipment being used.
Environment
The environment in which the process will take place should be considered. Factors such as ambient temperature and humidity can affect the performance of the warm isostatic press and should be taken into account when selecting the temperature.
In conclusion, by carefully considering these factors and selecting the appropriate temperature, users can optimize the performance of their warm isostatic press and achieve the desired results.
Applications of Warm Isostatic Pressing
Warm isostatic pressing (WIP) is a process that has found various applications in different industries due to its ability to improve the mechanical properties of materials. In this section, we will discuss some of the most common applications of WIP.
Aerospace Engineering
One of the primary applications of WIP is in aerospace engineering, where it is used to enhance the mechanical properties of components such as turbine blades, engine parts, and structural components. WIP can improve the strength, ductility, and reliability of these components, making them more durable and efficient.
Medical Implants
WIP is also used in the production of medical implants such as dental implants, hip replacements, and spinal implants. The process is carefully controlled to achieve the desired microstructure and properties, which are crucial for the success of the implant. WIP can enhance the biocompatibility, strength, and corrosion resistance of the implant, making it more suitable for the intended application.
Advanced Ceramics and Composites
WIP is also used in the production of advanced ceramics and composites, where it can enhance the strength, toughness, and reliability of the material. The process is particularly useful for materials that are difficult to shape using conventional methods, such as powder metallurgy. WIP can also improve the uniformity of the microstructure and eliminate defects such as porosity.
Tooling and Cutting
WIP is also used in the production of tooling and cutting components such as dies, molds, and cutting inserts. The process can improve the wear resistance, toughness, and dimensional stability of these components, making them more reliable and efficient.
Powder Metallurgy
WIP is widely used in powder metallurgy, where it is used to enhance the mechanical properties of various metal and ceramic parts. The process can improve the density, toughness, and fatigue resistance of the parts, making them more suitable for the intended application.
In conclusion, warm isostatic pressing (WIP) has various applications in different industries, including aerospace engineering, medical implants, advanced ceramics and composites, tooling and cutting, and powder metallurgy. The process can improve the mechanical properties of materials, making them more reliable, efficient, and suitable for the intended application.
Conclusion
In conclusion, warm isostatic pressing (WIP) provides numerous benefits for a wide range of applications. The right temperature is crucial in achieving the desired properties of the material being processed. Factors such as material type, geometry, and desired properties should be considered when selecting the appropriate temperature for your application. It is important to consult with experienced professionals to ensure that the desired outcome is achieved. With proper temperature selection and processing techniques, WIP can produce high-quality components with excellent properties that meet the requirements of various industries.
CONTACT US FOR A FREE CONSULTATION
KINTEK LAB SOLUTION's products and services have been recognized by customers around the world. Our staff will be happy to assist with any inquiry you might have. Contact us for a free consultation and talk to a product specialist to find the most suitable solution for your application needs!