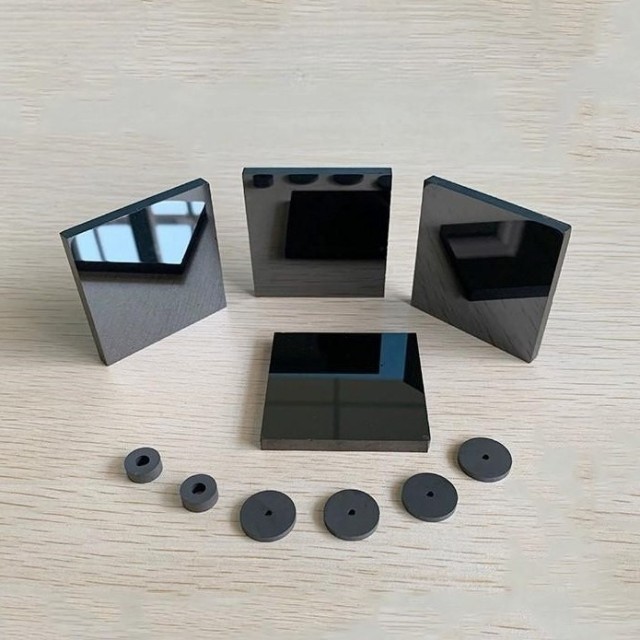
fine ceramics
Silicon Carbide (SIC) Ceramic Sheet Wear-Resistant Engineering Advanced Fine Ceramics
Item Number : KM-DG02
Price varies based on specs and customizations
- Material
- Silicon carbide
- Specification
- See the form
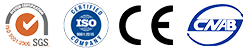
Shipping:
Contact us to get shipping details Enjoy On-time Dispatch Guarantee.
Why Choose Us
Reliable PartnerEasy ordering process, quality products, and dedicated support for your business success.
Application
Wear-resistant silicon carbide plate/RBSiC/SiSiC silicon carbide plate is composed of high-purity silicon carbide and ultrafine powder, which is formed by vibration molding and high-temperature sintering, and has good high-temperature thermal conductivity and load-bearing capacity. The manufacturing process is cost-effective and simple, and it is easy to use. They are easy to install and integrate seamlessly into various systems. Reaction Bonded Silicon Carbide (RBSiC) plates feature thinner walls and a space-saving design for efficient use of furnace or application space. The plates last longer compared to alumina ceramic and polyurethane, ensuring durability. They can be customized in porous, edged or multi-edged shapes to meet specific requirements.
- Daily-use ceramics: Silicon nitride plates are used to produce sanitary ware, electric porcelain and other daily-use ceramics.
- Industrial Furnace: It is used in industrial furnace because of its high temperature resistance and thermal shock resistance.
- Flue gas desulfurization: Silicon nitride plates are used in the flue gas desulfurization process, which can withstand high temperature and corrosive environments.
- Automotive and Machinery: Due to their wear resistance and durability, these sheets are used in the automotive industry, water pumps, boilers and machinery.
- Metallurgy and chemical industry: It is used in metallurgical process and chemical industry because of its corrosion resistance and high temperature resistance.
- Aerospace and Military: Silicon nitride sheets are used in aerospace and military applications due to their high strength and thermal properties.
Detail & Parts
Technical specifications
Round 15*3mm | 40*40*1mm | 50*50*4/5/6mm | 100*100*5mm | 150*150*5mm |
5*5*1mm | 40*40*2mm | 50*50*8/10mm | 100*100*7mm | 15*15*1mm (one side polished) |
10*10*4mm | 50*50*1mm | 50*50*14mm | 100*100*10mm | 50*50*1mm (one side polished) |
20*20*3mm | 50*50*2mm | 100*100*3mm | 100*100*15mm | |
20*20*5mm | 50*50*3mm | 100*100*4mm | 100*100*20mm |
The produce we show are available in different sizes and custom sizes are available on request.
Project | Unit | Vacuum Sintering SiC | Reaction Bonded SiC |
---|---|---|---|
Density | g/cc | >3.12 | 3.05-3.08 |
Surface roughness | um | 0.6 | 0.6-0.8 |
Hardness | Hs | >115 | >110 |
Apparent porosity | % | <0.2 | <0.3 |
Compressive strength | MPa | >2500 | >2500 |
Flexural strength | MPa | >380 | >350 |
Free silicon content | % | <1 | <10 |
Purity (Silicon Carbide Content) | % | ≥99 | ≥90 |
Elastic modulus | GPa | 410 | 400 |
Thermal conductivity | Cal/cm.s.℃ | 0.3 | 0.32 |
Coefficient of thermal expansion | i/℃ | 4.2×10^6 | 4×10^6 |
Operating temperature | ℃ | 1400 | 1300 |
Advantages
- Good temperature resistance: the silicon nitride plate can withstand a wide temperature range, from -50°C to 1350°C.
- Smooth Surface: The ceramic surface is smooth, dirt-resistant and dust-proof.
- High strength, high hardness: Silicon nitride plate has excellent mechanical properties, including high strength, high hardness and high wear resistance.
- Thermal shock resistance: It has good thermal shock resistance and can be heated and cooled rapidly in high temperature environment.
- Corrosion resistance and oxidation resistance: Silicon nitride plate has the characteristics of corrosion resistance and oxidation resistance, and is suitable for various harsh environments.
- Good thermal conductivity: It has high thermal conductivity, which is conducive to efficient heat transfer.
- Energy saving: The silicon nitride board is ultra-thin and has a high packing density, which can save energy.
FAQ
What Are Advanced Ceramics?
What Are The Main Applications Of Fine Ceramics?
What Are Engineering Ceramics?
What Are The Main Types Of Advanced Ceramics?
What Are The Main Types Of Fine Ceramics?
What Are The Main Types Of Engineering Ceramics?
What Are The Applications Of Advanced Ceramics?
What Is The Principle Behind Fine Ceramics?
What Are The Applications Of Engineering Ceramics?
How Are Advanced Ceramics Manufactured?
What Are The Advantages Of Using Fine Ceramics?
How Do Engineering Ceramics Differ From Traditional Ceramics?
What Are The Advantages Of Using Advanced Ceramics?
What Are The Advantages Of Using Alumina Ceramics?
What Is The Difference Between Alumina And Zirconia Ceramics?
Why Are Zirconia Ceramics Preferred In Certain Applications?
Why Are Silicon Carbide Ceramics Used In High-temperature Applications?
What Makes Silicon Carbide Ceramics Suitable For High-temperature Applications?
What Makes Boron Nitride Ceramics Unique?
How Are Boron Nitride Ceramics Used In Electronics?
How Do Advanced Ceramics Contribute To Energy Efficiency?
What Is The Manufacturing Process Of Engineering Ceramics?
Can Engineering Ceramics Be Customized For Specific Applications?
4.9
out of
5
The silicon carbide ceramic sheet from KINTEK SOLUTION is a game-changer. Its durability and resistance to wear and tear are remarkable.
4.8
out of
5
KINTEK SOLUTION's silicon carbide ceramic sheet is an excellent choice for applications requiring high-temperature resistance and thermal shock resistance.
4.7
out of
5
The delivery of the silicon carbide ceramic sheet was lightning fast. I was impressed with the promptness and efficiency of KINTEK SOLUTION.
5.0
out of
5
The value for money offered by KINTEK SOLUTION's silicon carbide ceramic sheet is unbeatable. It's an investment that pays for itself in the long run.
4.9
out of
5
The quality of the silicon carbide ceramic sheet from KINTEK SOLUTION is exceptional. It's evident that they prioritize quality over quantity.
4.8
out of
5
I've used silicon carbide ceramic sheets from various suppliers, but KINTEK SOLUTION's product stands out with its superior durability.
4.7
out of
5
The technological advancement of KINTEK SOLUTION's silicon carbide ceramic sheet is impressive. It's a testament to their commitment to innovation.
5.0
out of
5
I highly recommend KINTEK SOLUTION's silicon carbide ceramic sheet to anyone looking for a reliable and high-performance solution.
4.9
out of
5
The silicon carbide ceramic sheet from KINTEK SOLUTION has exceeded my expectations. It's a valuable addition to our laboratory equipment.
4.8
out of
5
The speed of delivery for the silicon carbide ceramic sheet was remarkable. KINTEK SOLUTION understands the importance of timely delivery.
4.7
out of
5
The silicon carbide ceramic sheet from KINTEK SOLUTION has proven to be a cost-effective solution for our laboratory needs.
5.0
out of
5
KINTEK SOLUTION's silicon carbide ceramic sheet is a testament to their commitment to quality and customer satisfaction.
4.9
out of
5
The durability of KINTEK SOLUTION's silicon carbide ceramic sheet is remarkable. It's a long-lasting investment for our laboratory.
4.8
out of
5
I'm thoroughly impressed with the technological advancements incorporated into KINTEK SOLUTION's silicon carbide ceramic sheet.
4.7
out of
5
The silicon carbide ceramic sheet from KINTEK SOLUTION is a game-changer in our laboratory. It has improved our efficiency and productivity.
5.0
out of
5
I highly recommend KINTEK SOLUTION's silicon carbide ceramic sheet to anyone seeking a reliable and high-performance solution.
4.9
out of
5
The value for money offered by KINTEK SOLUTION's silicon carbide ceramic sheet is exceptional. It's a wise investment for any laboratory.
Products
Silicon Carbide (SIC) Ceramic Sheet Wear-Resistant Engineering Advanced Fine Ceramics
REQUEST A QUOTE
Our professional team will reply to you within one business day. Please feel free to contact us!
Related Products
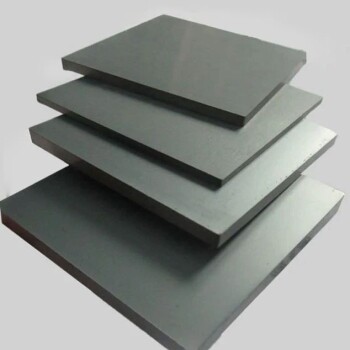
Silicon Carbide (SIC) Ceramic Plate for Engineering Advanced Fine Ceramics
Silicon nitride (sic) ceramic is an inorganic material ceramic that does not shrink during sintering. It is a high-strength, low-density, high-temperature-resistant covalent bond compound.

Zirconia Ceramic Gasket Insulating Engineering Advanced Fine Ceramics
Zirconia insulating ceramic gasket has high melting point, high resistivity, low thermal expansion coefficient and other properties, making it an important high temperature resistant material, ceramic insulating material and ceramic sunscreen material.
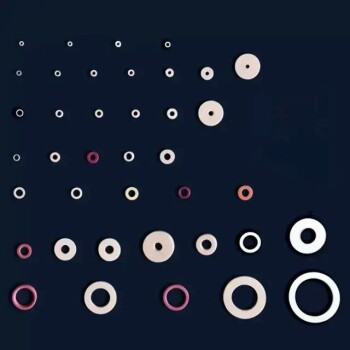
Alumina wear-resistant ceramic washer are used for heat dissipation, which can replace aluminum heat sinks, with high temperature resistance and high thermal conductivity.
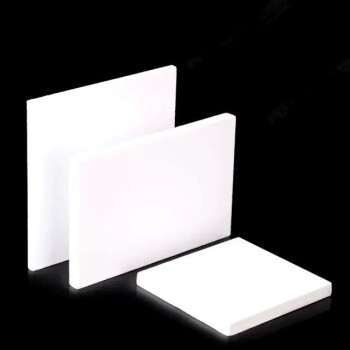
High Temperature Wear-Resistant Alumina Al2O3 Plate for Engineering Advanced Fine Ceramics
High temperature wear-resistant insulating alumina plate has excellent insulation performance and high temperature resistance.
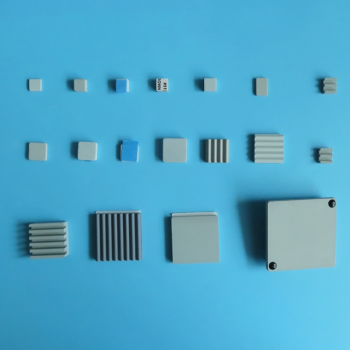
Silicon Carbide (SIC) Ceramic Sheet Flat Corrugated Heat Sink for Engineering Advanced Fine Ceramics
Silicon carbide (sic) ceramic heat sink not only does not generate electromagnetic waves, but also can isolate electromagnetic waves and absorb part of electromagnetic waves.
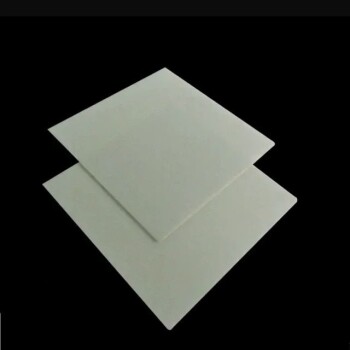
Precision Machined Silicon Nitride (SiN) Ceramic Sheet for Engineering Advanced Fine Ceramics
Silicon nitride plate is a commonly used ceramic material in the metallurgical industry due to its uniform performance at high temperatures.
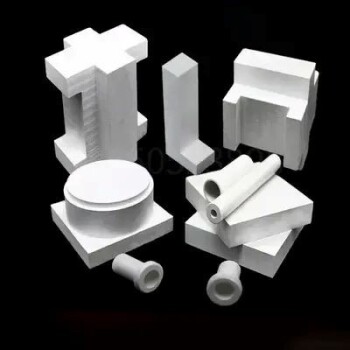
Advanced Engineering Fine Ceramics Boron Nitride (BN) Ceramic Parts
Boron nitride ((BN) is a compound with high melting point, high hardness, high thermal conductivity and high electrical resistivity. Its crystal structure is similar to graphene and harder than diamond.
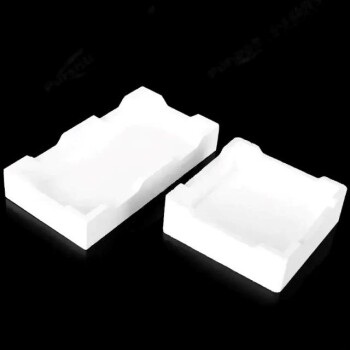
Advanced Engineering Fine Ceramics Alumina Ceramic Saggar for Fine Corundum
Alumina sagger products have the characteristics of high temperature resistance, good thermal shock stability, small expansion coefficient, anti-stripping, and good anti-powdering performance.
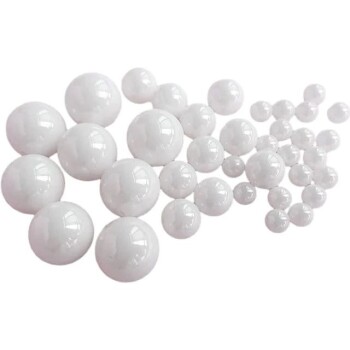
Precision Machined Zirconia Ceramic Ball for Engineering Advanced Fine Ceramics
zirconia ceramic ball have the characteristics of high strength, high hardness, PPM wear level, high fracture toughness, good wear resistance, and high specific gravity.
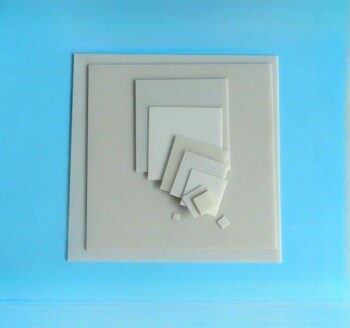
Advanced Engineering Fine Ceramics Aluminum Nitride (AlN) Ceramic Sheet
Aluminum nitride (AlN) has the characteristics of good compatibility with silicon. It is not only used as a sintering aid or reinforcing phase for structural ceramics, but its performance far exceeds that of alumina.
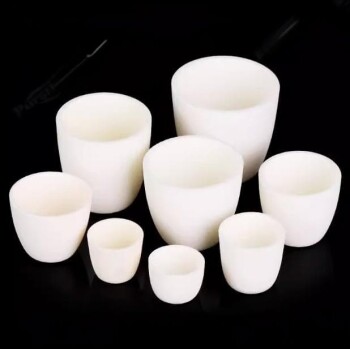
In the journey of scientific exploration and industrial production, every detail is crucial. Our arc-shaped alumina ceramic crucibles, with their excellent high temperature resistance and stable chemical properties, have become a powerful assistant in laboratories and industrial fields. They are made of high-purity alumina materials and manufactured through precision processes to ensure excellent performance in extreme environments.
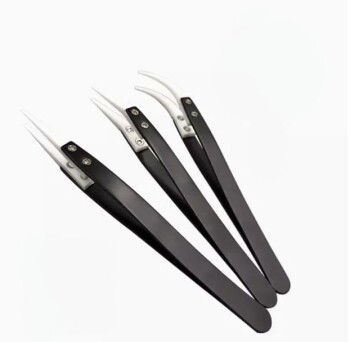
Engineering Advanced Fine Ceramics Head Tweezers with Pointed Elbow Zirconia Ceramic Tip
Zirconia ceramic tweezers are a high-precision tool made of advanced ceramic materials, especially suitable for operating environments that require high precision and corrosion resistance. This type of tweezers not only has excellent physical properties, but is also popular in the medical and laboratory fields because of its biocompatibility.
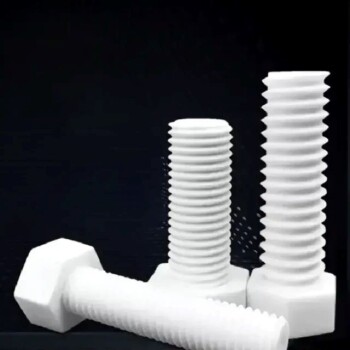
Alumina ceramic screws are fastening components made of 99.5% alumina, ideal for extreme applications requiring excellent thermal resistance, electrical insulation and chemical resistance.
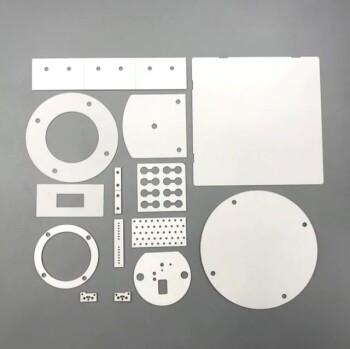
Alumina ceramics have good electrical conductivity, mechanical strength and high temperature resistance, while zirconia ceramics are known for their high strength and high toughness and are widely used.
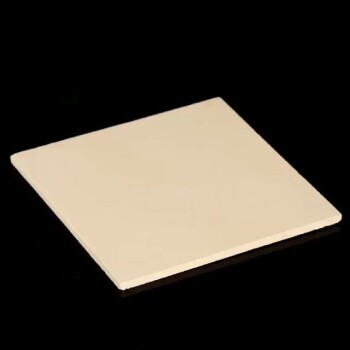
Precision Machined Yttria Stabilized Zirconia Ceramic Plate for Engineering Advanced Fine Ceramics
Yttrium-stabilized zirconia has the characteristics of high hardness and high temperature resistance, and has become an important material in the field of refractories and special ceramics.
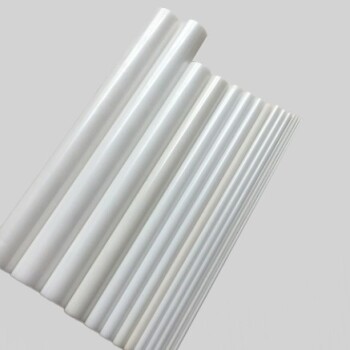
Precision Machined Yttrium Stabilized Zirconia Ceramic Rod for Engineering Advanced Fine Ceramics
Zirconia ceramic rods are prepared by isostatic pressing, and a uniform, dense and smooth ceramic layer and transition layer are formed at high temperature and high speed.
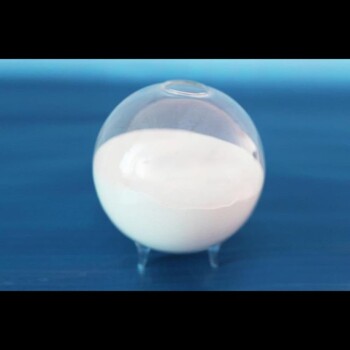
High Purity Alumina Granulated Powder for Engineering Advanced Fine Ceramics
Ordinary alumina granulated powder is alumina particles prepared by traditional processes, with a wide range of applications and good market adaptability. This material is known for its high purity, excellent thermal stability and chemical stability, and is suitable for a variety of high-temperature and conventional applications.
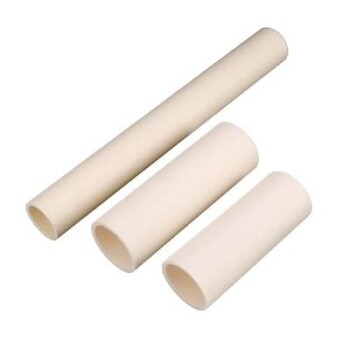
High Temperature Alumina (Al2O3) Furnace Tube for Engineering Advanced Fine Ceramics
High temperature alumina furnace tube combines the advantages of high hardness of alumina, good chemical inertness and steel, and has excellent wear resistance, thermal shock resistance and mechanical shock resistance.
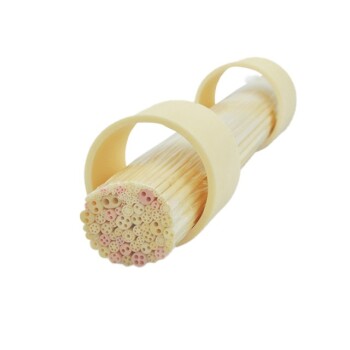
High Temperature Aluminum Oxide (Al2O3) Protective Tube for Engineering Advanced Fine Ceramics
Alumina oxide protective tube, also known as high temperature resistant corundum tube or thermocouple protection tube, is a ceramic tube mainly made of alumina (aluminum oxide).
Related Articles
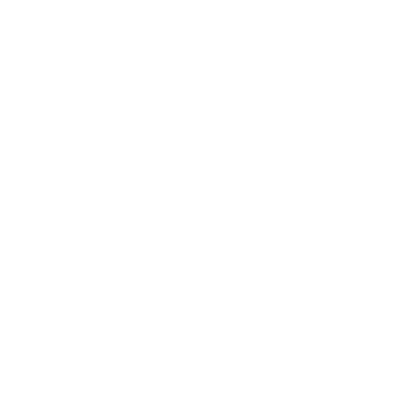
Precautions for installing silicon carbide stick
Precautions for installing silicon carbide stic.
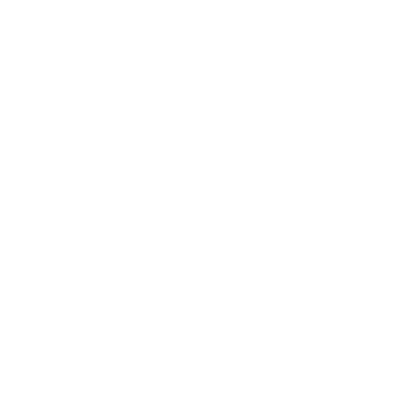
The Benefits of Cold Isostatic Pressing
Cold Isostatic Pressing (CIP) is a process used to compact powders into a specific shape or size. This method involves subjecting the powders to high pressure, typically between 100 and 200 MPa, in a liquid medium.
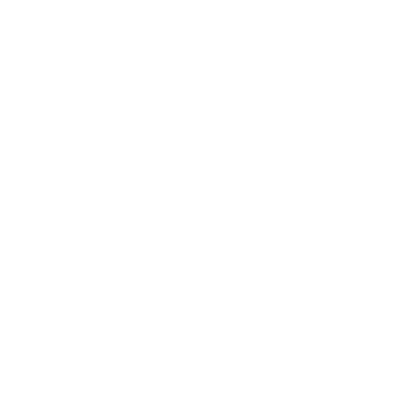
A Guide to Choosing the Right Temperature for Warm Isostatic Press
Warm Isostatic Pressing (WIP) is a process used to eliminate porosity and improve the mechanical properties of materials. In this process, the material is subjected to high pressure and temperature in an inert gas environment.
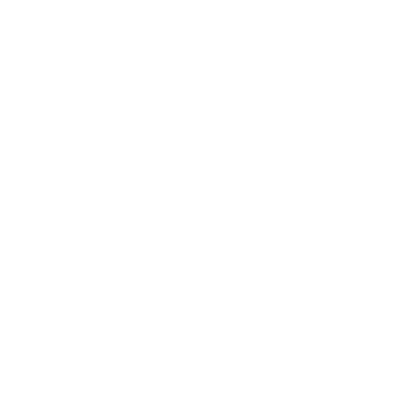
Dos and don'ts during the installation of molybdenum disilicide (MoSi2) heating element
Precautions when installing MoSi2 heating elements
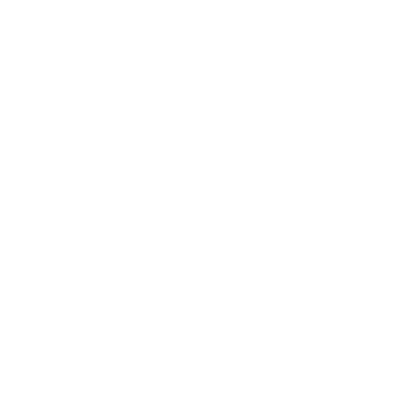
What Makes Hot Isostatic Pressing So Effective
Hot Isostatic Pressing (HIP) is a manufacturing process that uses high temperature and pressure to improve the mechanical properties of materials. The process involves placing a part in a sealed chamber and subjecting it to high temperatures and pressures.
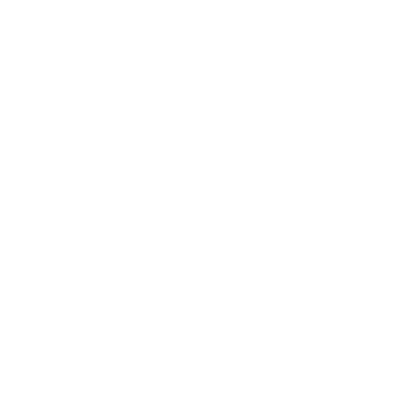
Technical Overview of Silicon-Carbon Anode Materials Prepared by CVD Method
This article discusses the key technical aspects of silicon-carbon anode materials prepared via CVD, focusing on their synthesis, performance improvements, and industrial application potential.
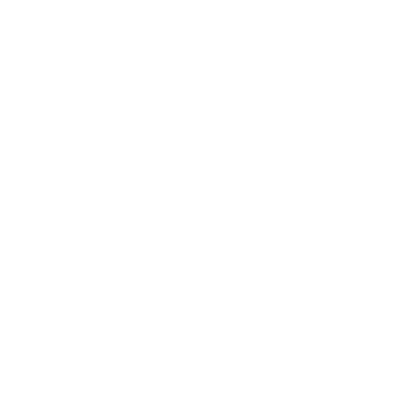
Carbon Coating for Surface Modification of Silicon-Based Materials in Lithium-Ion Batteries
This article discusses the application of carbon coatings to improve the performance of silicon-based anode materials in lithium-ion batteries.
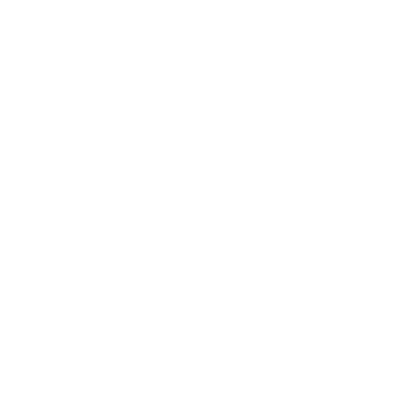
Advanced Technologies for Precision Ceramics
Explores key technologies and preparation methods for precision ceramic components, highlighting their applications and challenges.
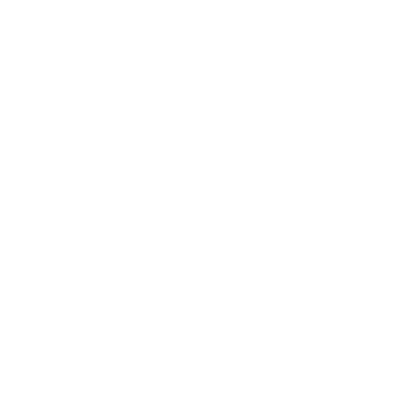
Precision Ceramic Materials for Energy Conversion Applications
Overview of various ceramic materials used in energy conversion technologies, including heaters, piezoelectric ceramics, and solid oxide fuel cells.
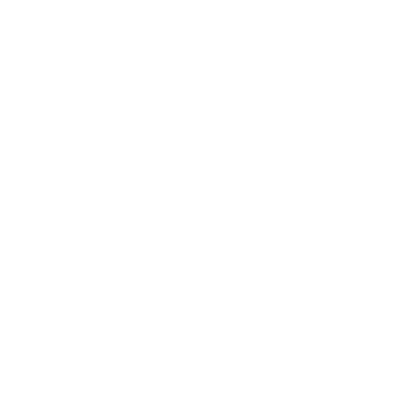
Precision Ceramics in Semiconductor Applications
Exploring the use of precision ceramics in semiconductor equipment, their properties, and manufacturing processes.
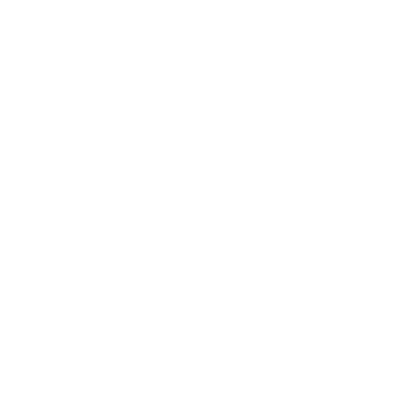
Advancements in Engineering Ceramic Materials
Explores new engineering ceramics with exceptional properties and applications in harsh environments, comparing them to traditional materials.
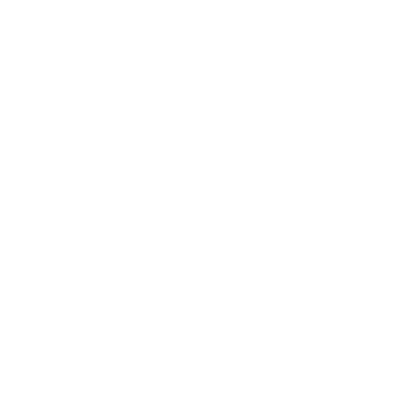
Engineering Ceramic Materials: Applications in Aerospace, Electronic Information, New Energy, and Environmental Protection
This article explores the diverse applications of engineering ceramic materials across aerospace, electronic information, new energy, and environmental protection sectors.