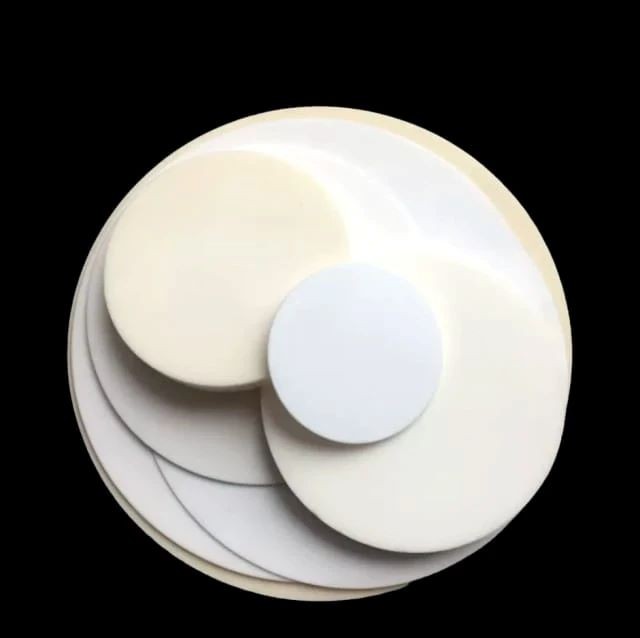
fine ceramics
Engineering Advanced Fine Ceramics Aluminum Oxide Al2O3 Heat Sink for Insulation
Item Number : KM-C013
Price varies based on specs and customizations
- Material
- Aluminum oxide
- Specification
- See the form
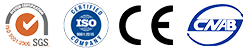
Shipping:
Contact us to get shipping details Enjoy On-time Dispatch Guarantee.
Why Choose Us
Reliable PartnerEasy ordering process, quality products, and dedicated support for your business success.
Application
A ceramic heat sink is a device for dissipating heat from electronic components in electrical appliances. The hole structure of the ceramic heat sink increases the heat dissipation area in contact with the air, which greatly enhances the heat dissipation effect, and the heat dissipation effect is better than that of super copper and aluminum. Ceramic insulation, high temperature resistance, oxidation resistance, acid and alkali resistance, thermal shock, low thermal expansion coefficient, ensuring stability in high and low temperature or other harsh environments. Ceramics can withstand large currents, withstand high voltages, prevent leakage breakdown, have no noise, and will not generate coupling parasitic capacitance with MOS and other power tubes, thus simplifying the filtering process.
- It maintains hardness at high temperatures, so it can be used as a material for industrial furnaces.
- Used in the manufacture of CVD, ion implantation, lithography and semiconductor parts.
- In traditional industries, alumina ceramics are used in products such as injection pipes, gas nozzles and insulators
- LED lighting, loudspeaker/audio, power transistor, power module, etc. and some high-power equipment.
- IC, MOS, triode, Schottky, IGBT and other surface heat sources that need heat dissipation!
- Especially suitable for high-power equipment, the design space is especially suitable for light, thin, short and small.
Detail & Parts
Technical specifications
1.7*3mm | 10*4mm | 16*1mm | 20*20mm | 29.5*1mm | 60*1mm | 100*8mm |
3*3mm | 10*5mm | 16*4mm | 20.5*1mm | 30.5*1mm | 57.8*6mm | 107*3mm |
4*2.3mm | 10.5*2mm | 16*5mm | 22*1mm | 32*5mm | 70*1mm | 150*5mm |
6*6mm | 10.5*10.5mm | 17*1mm | 23.5*2.5mm | 35*1mm | 74*1mm | 200*5mm |
7*3.3mm | 12*1mm | 18*0.63mm | 25*0.5mm | 40*1mm | 80*1mm | |
8*5mm | 12*5mm | 19*0.8mm | 26*4mm | 45*0.5mm | 90*1mm | |
9.5*1.3mm | 14*1mm | 20*1mm | 26*5mm | 51*1mm | 100*1mm | |
10*1mm | 16*0.5mm | 20*10mm | 28*6.5mm | 50*5mm | 100*2mm |
The produce we show are available in different sizes and custom sizes are available on request.
Advantages
- Compared to aluminum radiators of the same volume, ceramic models have porosity that increases the surface area for heat dissipation.
- No heat storage, direct heat dissipation, multi-directional heat dissipation, further speeding up heat dissipation.
- Polycrystalline in nature, enhancing the rate of heat dissipation.
- Ceramic insulation, high temperature resistance, oxidation resistance, acid and alkali resistance, long service life.
- Effective anti-interference (EMI) and anti-static.
- Natural inorganic materials meet environmental protection requirements.
- Its insulating properties give it high electrical resistance, and its texture makes it stable, resistant to high temperatures and light in weight.
FAQ
What Are The Main Applications Of Fine Ceramics?
Comparison Of Radiator Choices.
What Are The Main Types Of Fine Ceramics?
What Is The Principle Behind Fine Ceramics?
What Are The Advantages Of Using Fine Ceramics?
4.8
out of
5
I am amazed by its high temperature stability and thermal conductivity.
4.9
out of
5
The ceramic heat sink is fantastic, it dissipates heat efficiently and ensures stability in various environments.
4.7
out of
5
The alumina ceramic crucible's insulation properties and mechanical strength are exceptional, making it perfect for high-temperature applications.
4.9
out of
5
The tungsten boats with alumina barrier offer excellent heat concentration, preventing sample creeping and wetting.
4.6
out of
5
The ceramic heat sink's porosity increases the surface area for heat dissipation, resulting in faster cooling.
4.7
out of
5
The alumina ceramic's hardness and wear-resistance make it ideal for wear-resistant inserts and products.
4.8
out of
5
The alumina's resistance to strong acids and alkalis at elevated temperatures makes it suitable for corrosive environments.
4.9
out of
5
The ceramic heat sink's ability to withstand large currents and high voltages prevents leakage breakdown and simplifies filtering.
4.7
out of
5
The alumina's high hardness at high temperatures makes it a suitable material for industrial furnaces.
4.8
out of
5
The alumina's applications in CVD, ion implantation, lithography, and semiconductor parts are highly valuable.
4.9
out of
5
The alumina ceramics' use in injection pipes, gas nozzles, and insulators in traditional industries is commendable.
4.6
out of
5
The ceramic heat sink's compact design is perfect for light, thin, short, and small spaces, especially in high-power equipment.
4.7
out of
5
The alumina's insulating properties provide high electrical resistance and stability under extreme conditions.
4.8
out of
5
The ceramic heat sink's multi-directional heat dissipation speeds up the cooling process significantly.
4.9
out of
5
The alumina's polycrystalline nature enhances the rate of heat dissipation, making it highly efficient.
4.7
out of
5
The ceramic heat sink's effective anti-interference and anti-static properties ensure reliable performance.
Products
Engineering Advanced Fine Ceramics Aluminum Oxide Al2O3 Heat Sink for Insulation
REQUEST A QUOTE
Our professional team will reply to you within one business day. Please feel free to contact us!
Related Products
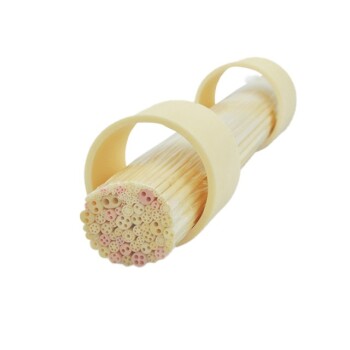
High Temperature Aluminum Oxide (Al2O3) Protective Tube for Engineering Advanced Fine Ceramics
Alumina oxide protective tube, also known as high temperature resistant corundum tube or thermocouple protection tube, is a ceramic tube mainly made of alumina (aluminum oxide).
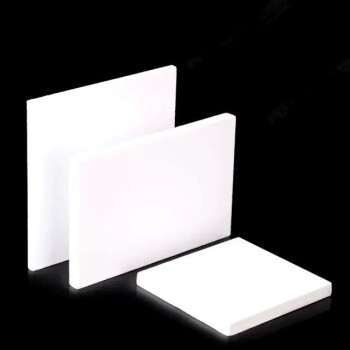
High Temperature Wear-Resistant Alumina Al2O3 Plate for Engineering Advanced Fine Ceramics
High temperature wear-resistant insulating alumina plate has excellent insulation performance and high temperature resistance.
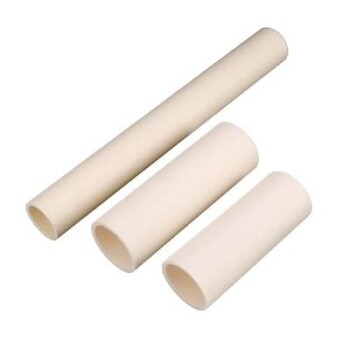
High Temperature Alumina (Al2O3) Furnace Tube for Engineering Advanced Fine Ceramics
High temperature alumina furnace tube combines the advantages of high hardness of alumina, good chemical inertness and steel, and has excellent wear resistance, thermal shock resistance and mechanical shock resistance.
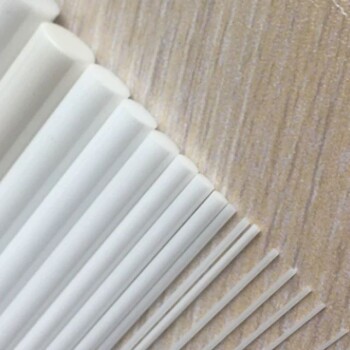
Engineering Advanced Fine Alumina Al2O3 Ceramic Rod Insulated for Industrial Applications
Insulated alumina rod is a fine ceramic material. Alumina rods have excellent electrical insulating properties, high chemical resistance and low thermal expansion.
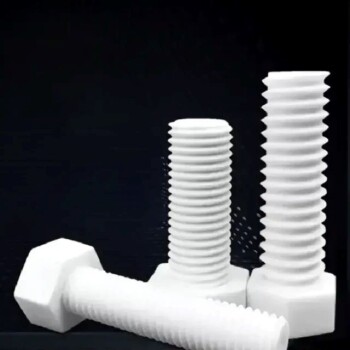
Alumina ceramic screws are fastening components made of 99.5% alumina, ideal for extreme applications requiring excellent thermal resistance, electrical insulation and chemical resistance.
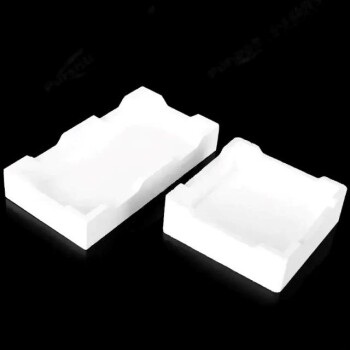
Advanced Engineering Fine Ceramics Alumina Ceramic Saggar for Fine Corundum
Alumina sagger products have the characteristics of high temperature resistance, good thermal shock stability, small expansion coefficient, anti-stripping, and good anti-powdering performance.
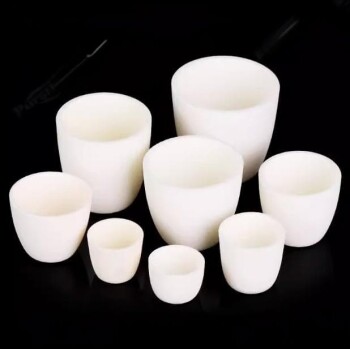
In the journey of scientific exploration and industrial production, every detail is crucial. Our arc-shaped alumina ceramic crucibles, with their excellent high temperature resistance and stable chemical properties, have become a powerful assistant in laboratories and industrial fields. They are made of high-purity alumina materials and manufactured through precision processes to ensure excellent performance in extreme environments.
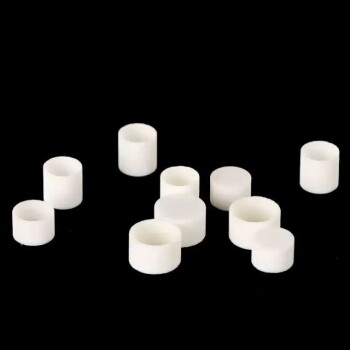
Engineering Advanced Fine Ceramics Alumina Crucibles (Al2O3) for Thermal Analysis TGA DTA
TGA/DTA thermal analysis vessels are made of aluminum oxide (corundum or aluminum oxide). It can withstand high temperature and is suitable for analyzing materials that require high temperature testing.
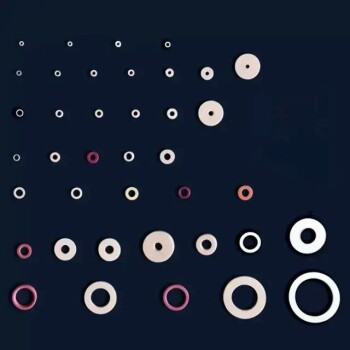
Alumina wear-resistant ceramic washer are used for heat dissipation, which can replace aluminum heat sinks, with high temperature resistance and high thermal conductivity.
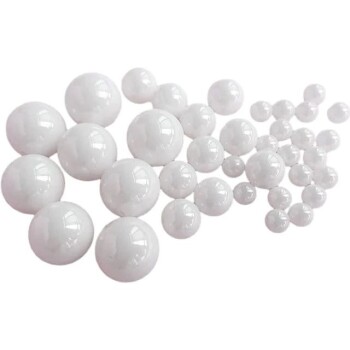
Precision Machined Zirconia Ceramic Ball for Engineering Advanced Fine Ceramics
zirconia ceramic ball have the characteristics of high strength, high hardness, PPM wear level, high fracture toughness, good wear resistance, and high specific gravity.
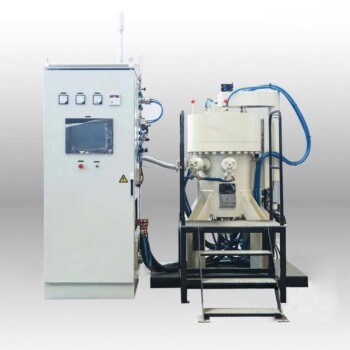
Vacuum Heat Treat and Sintering Furnace with 9MPa Air Pressure
The air pressure sintering furnace is a high-tech equipment commonly used for the sintering of advanced ceramic materials. It combines vacuum sintering and pressure sintering techniques to achieve high-density and high-strength ceramics.
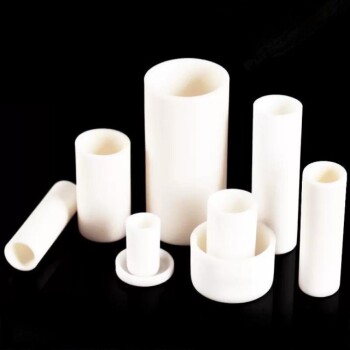
Engineering Advanced Fine Ceramics Alumina Al2O3 Crucible With Lid Cylindrical Laboratory Crucible
Cylindrical Crucibles Cylindrical crucibles are one of the most common crucible shapes, suitable for melting and processing a wide variety of materials, and are easy to handle and clean.
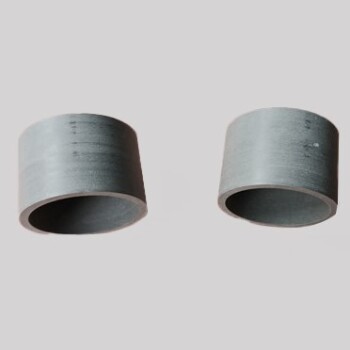
Conductive Boron Nitride BN Ceramics Composite for Advanced Applications
Due to the characteristics of boron nitride itself, the dielectric constant and dielectric loss are very small, so it is an ideal electrical insulating material.
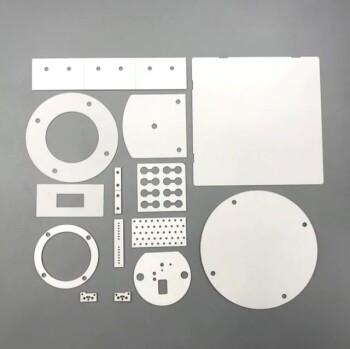
Alumina ceramics have good electrical conductivity, mechanical strength and high temperature resistance, while zirconia ceramics are known for their high strength and high toughness and are widely used.

Silicon Carbide (SIC) Ceramic Sheet Wear-Resistant Engineering Advanced Fine Ceramics
Silicon carbide (sic) ceramic sheet is composed of high-purity silicon carbide and ultra-fine powder, which is formed by vibration molding and high-temperature sintering.
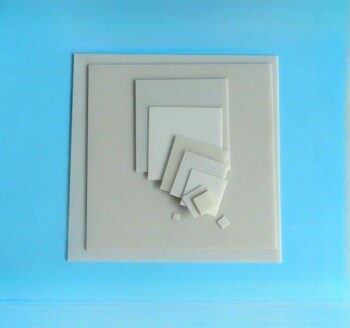
Advanced Engineering Fine Ceramics Aluminum Nitride (AlN) Ceramic Sheet
Aluminum nitride (AlN) has the characteristics of good compatibility with silicon. It is not only used as a sintering aid or reinforcing phase for structural ceramics, but its performance far exceeds that of alumina.
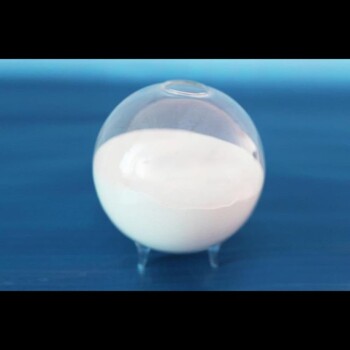
High Purity Alumina Granulated Powder for Engineering Advanced Fine Ceramics
Ordinary alumina granulated powder is alumina particles prepared by traditional processes, with a wide range of applications and good market adaptability. This material is known for its high purity, excellent thermal stability and chemical stability, and is suitable for a variety of high-temperature and conventional applications.
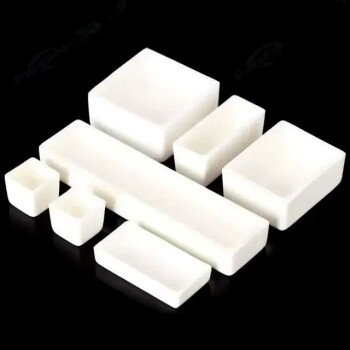
Engineering Advanced Fine Alumina Al2O3 Ceramic Crucible for Laboratory Muffle Furnace
Alumina ceramic crucibles are used in some materials and metal melting tools, and flat-bottomed crucibles are suitable for melting and processing larger batches of materials with better stability and uniformity.
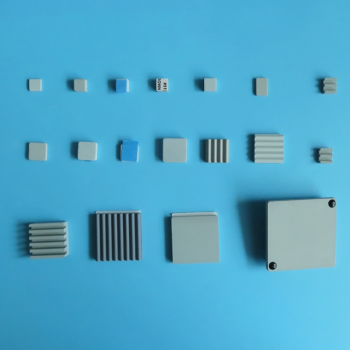
Silicon Carbide (SIC) Ceramic Sheet Flat Corrugated Heat Sink for Engineering Advanced Fine Ceramics
Silicon carbide (sic) ceramic heat sink not only does not generate electromagnetic waves, but also can isolate electromagnetic waves and absorb part of electromagnetic waves.
Related Articles
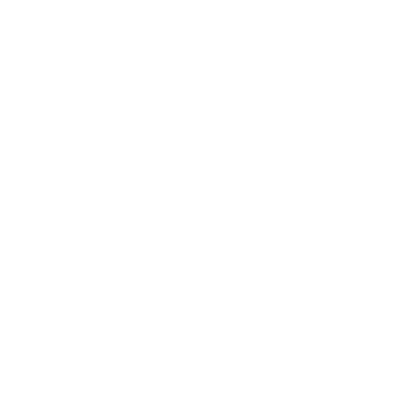
Electrode Fixture Guide: Types, Design, and Applications
Discover the comprehensive guide to electrode fixtures, covering various types, design considerations, and their indispensable role in industries like electroplating, welding, and electrochemical cells.
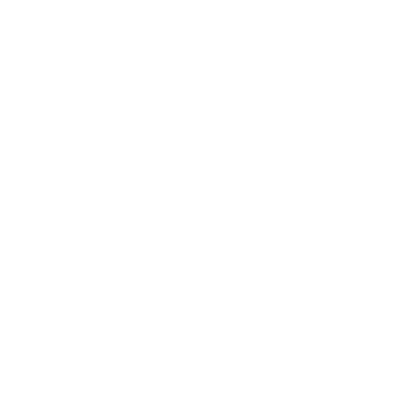
Dos and don'ts during the installation of molybdenum disilicide (MoSi2) heating element
Precautions when installing MoSi2 heating elements
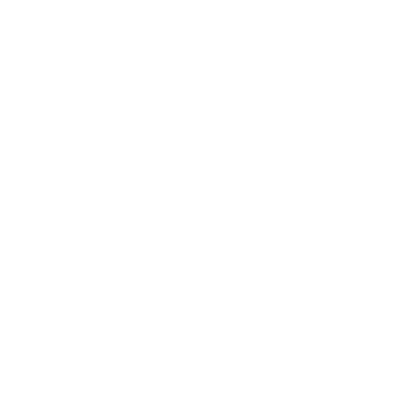
Investigating the Factors Affecting the Slow Temperature Rise in Box Furnaces
Sometimes, the temperature of the furnace may not rise as quickly as expected, or may not be able to reach the desired temperature at all.
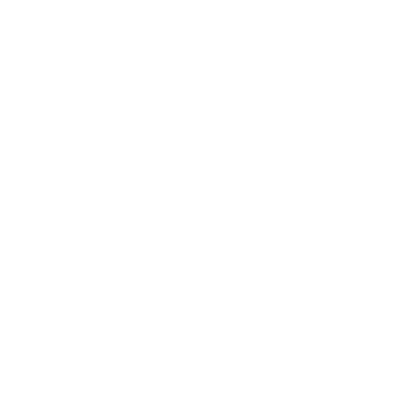
Advanced Alumina Ceramics: Applications and Manufacturing Techniques
This article discusses the applications and manufacturing techniques of advanced alumina ceramics, including molds, isostatic pressing, and green bodies.
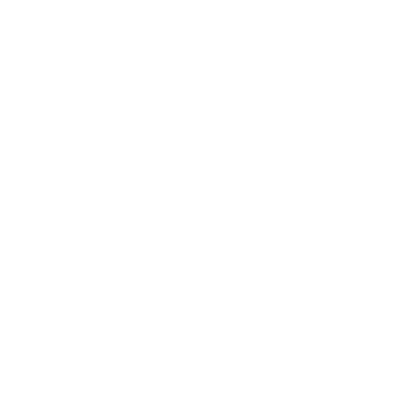
Advanced Alumina Ceramics: Applications and Manufacturing Techniques
Overview of alumina ceramics' applications and manufacturing methods, including molds, isostatic pressing, and green body formation.
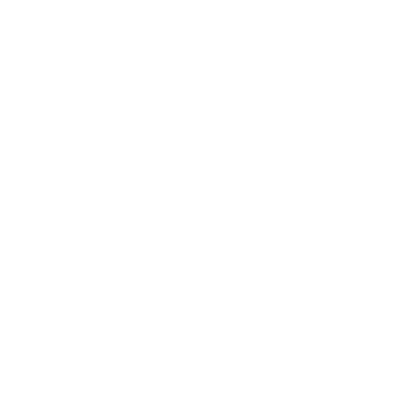
Understanding Oxide Ceramics: Concepts, Classification, and Applications
This article delves into the concept, classification, and diverse applications of oxide ceramics, highlighting their significance in various high-tech fields.
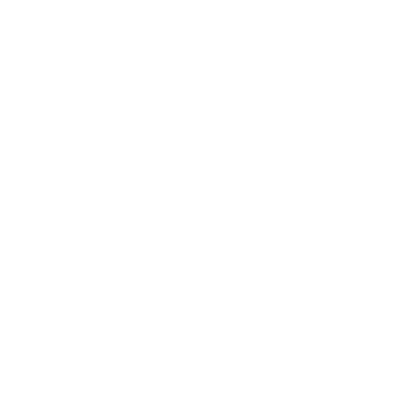
Precision Ceramics in Semiconductor Applications
Exploring the use of precision ceramics in semiconductor equipment, their properties, and manufacturing processes.
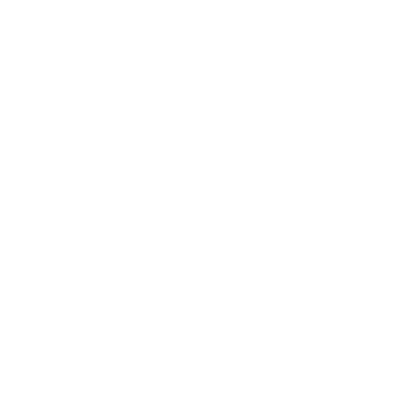
The 5 Hottest Advanced Ceramic Powders Currently Available!
An overview of the top 5 advanced ceramic powders: High Purity Aluminum Oxide, Boehmite, Aluminum Nitride, Silicon Nitride, and Spherical Alumina, highlighting their applications and market trends.
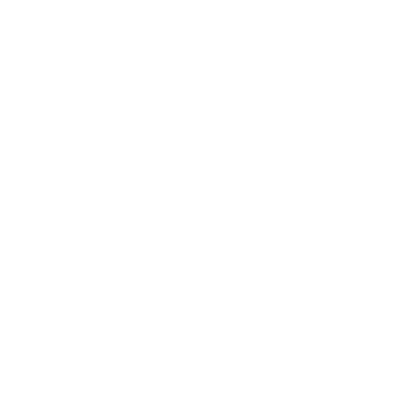
AI Chip Advancement Driven by Metallic New Materials
Explores how AI chip upgrades are fueled by new metal materials, impacting computing power and semiconductor manufacturing.
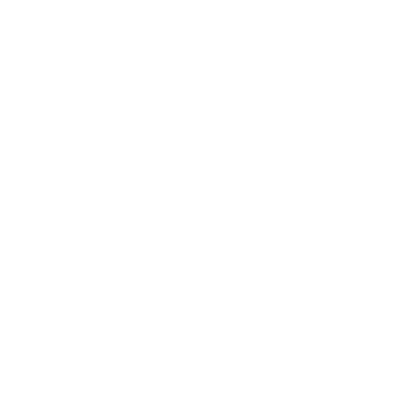
Structure and Properties of High-Temperature Engineering Ceramics
Explore the applications, structural features, and performance advantages of high-temperature engineering ceramics across various industries.
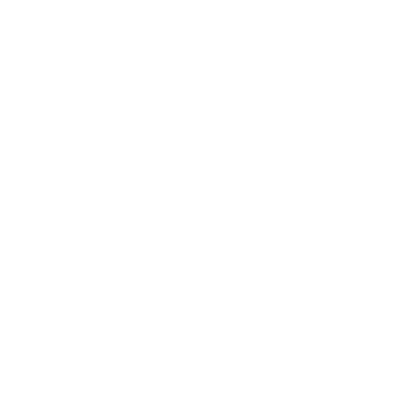
Engineering Ceramic Materials: Applications in Aerospace, Electronic Information, New Energy, and Environmental Protection
This article explores the diverse applications of engineering ceramic materials across aerospace, electronic information, new energy, and environmental protection sectors.
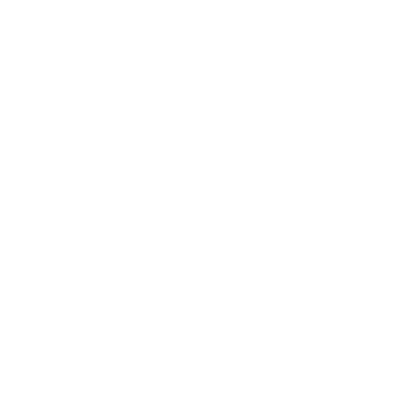
Precision Ceramic Materials for Energy Conversion Applications
Overview of various ceramic materials used in energy conversion technologies, including heaters, piezoelectric ceramics, and solid oxide fuel cells.