Introduction to Dental Porcelain Furnaces
Dental porcelain furnaces are essential equipment used in the dental industry for porcelain processing. These furnaces are designed explicitly for the firing process of dental porcelain, which is a crucial step in the dental restoration process. The porcelain firing process is essential for achieving the desired color, translucency, and strength of the dental restorations. These furnaces are available in different types and models, each with its unique features. Dental professionals must consider several factors when selecting dental porcelain furnaces, such as the type of porcelain and the required firing temperature. The right furnace can significantly impact the quality and success of dental restorations.
Table of Contents
Advantages of Using Burners over Traditional Systems
Dental furnaces have become an essential tool in modern dental laboratories. They offer a range of advantages over traditional systems. One of the main benefits of dental furnaces is that they use burners, which allow for precise temperature control and faster heating and cooling times. This results in more consistent and accurate results, as well as shorter processing times.
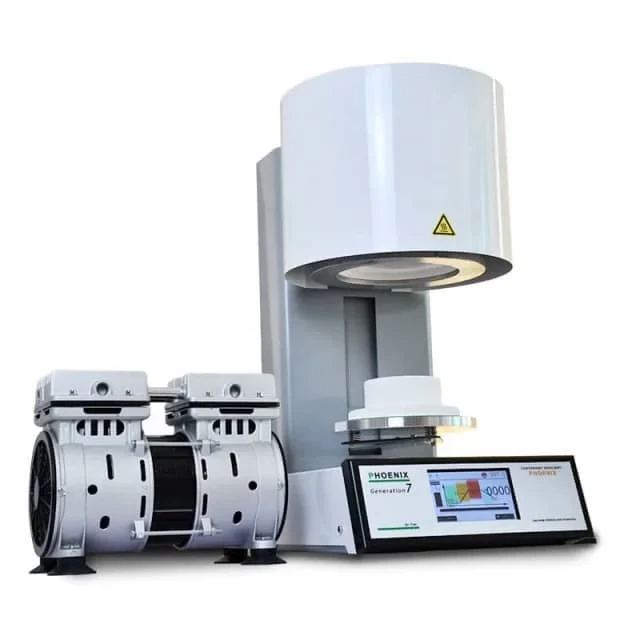
Precise Temperature Control
Burners in dental furnaces allow for precise temperature control, which is essential for producing porcelain restorations. Unlike traditional indirect heat systems, dental furnaces are heated on all sides, which results in a more uniform temperature distribution. This means that the dental crown of the fired crown has better consistency. The heating element in dental furnaces adopts imported alloy resistance wire, making it more durable and efficient.
Faster Heating and Cooling Times
Dental furnaces' burners also allow for faster heating and cooling times. This results in shorter processing times, which is essential for dental laboratories looking to improve their productivity. Dental porcelain furnace offers high temperature accuracy for outstanding firing results. The furnace's touch screen and self-explanatory menu design make it easy to operate, and the durable quartz firing crucible and integrated storage trays make it resistant and rugged.
Safety Features
Dental furnaces are designed with safety features to prevent overheating and ensure that the porcelain is not damaged during the firing process. This makes it a safer and more reliable option for producing dental restorations.
Flexibility in Material Use
Dental furnaces offer flexibility in terms of the types of materials that can be used. This allows for a wider range of products to be produced, including various types of ceramics. Dental furnaces are designed to work with a range of ceramic materials, and some furnaces are designed to also produce the pressure needed to press glass ceramics, and other pressable materials.
In conclusion, dental furnaces are an excellent investment for any dental laboratory looking to improve their porcelain processing capabilities and achieve better, more consistent results. The use of burners in dental furnaces offers precise temperature control, faster heating and cooling times, safety features, and flexibility in material use.
Process of Making Dental Porcelains
The process of making dental porcelains involves the use of a special type of furnace that can heat the porcelain to incredibly high temperatures. This process is essential for creating strong and durable dental restorations that can withstand the constant wear and tear of daily use.
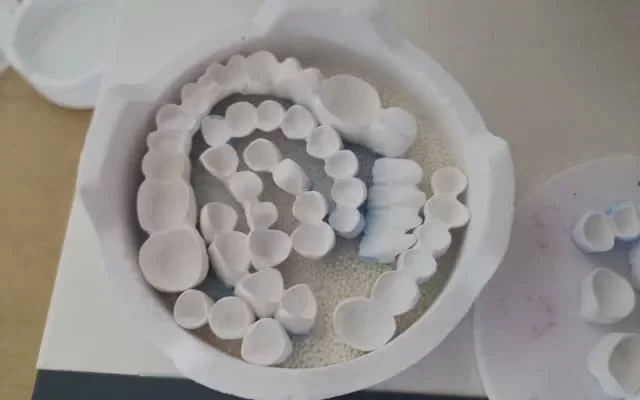
Step 1 - Mixing and Shaping
The first step in making dental porcelains is to mix the porcelain powder with a special liquid to create a paste. The paste is then shaped into the desired form of the restoration, such as a crown or bridge. The restoration is then left to dry before moving on to the firing process.
Step 2 - Firing
The next step in the process is firing the porcelain in a dental furnace. The porcelain is placed inside the furnace, and the temperature is slowly raised to a specific temperature for a set amount of time. This process is essential for hardening the porcelain and making it durable enough to withstand daily use.
Step 3 - Glazing
After firing, the porcelain is left to cool before moving on to the glazing process. Glaze is applied to the surface of the porcelain restoration and then fired again in the dental furnace at a lower temperature. This process gives the porcelain a smooth and shiny surface that mimics the natural appearance of teeth.
Step 4 - Finishing
The final step in making dental porcelains is finishing the restoration. The restoration is polished and buffed to give it a natural appearance that matches the surrounding teeth. The restoration is then ready to be cemented in place by a dentist.
In conclusion, the process of making dental porcelains involves mixing and shaping the porcelain, firing it in a dental furnace, glazing it, and finishing it. This process is essential for creating strong and durable dental restorations that can withstand the rigors of daily use. With the help of dental furnaces, dental technicians can create restorations that are not only functional but also aesthetically pleasing.
Components of Dental Ceramic Furnaces
Dental ceramic furnaces are essential tools for porcelain processing in the dental industry. They are designed with specific components that ensure accurate temperature control, consistent heating, and cooling down processes.
Heating Chamber
The heating chamber is the heart of the dental furnace. It is where the porcelain is placed for firing and glazing. It is usually made of high-quality ceramic material that can withstand high temperatures and thermal shocks. The chamber is designed to be spacious enough to accommodate different sizes and shapes of dental restorations.
Heating Elements
The heating elements are responsible for generating heat within the chamber. They are usually made of high-resistance wires that can withstand high temperatures. The number and size of the heating elements depend on the size and capacity of the furnace. They are strategically placed around the chamber to ensure uniform heating and prevent hotspots.
Control Unit
The control unit is the brain of the dental furnace. It regulates the temperature within the chamber and ensures that it remains within the desired range. The control unit is usually equipped with a microprocessor that monitors the temperature and adjusts it accordingly. It also has a display screen that shows the current temperature, set temperature, and other important information.
Thermocouple
The thermocouple is a temperature sensor that measures the temperature inside the chamber. It is usually made of two different metals that produce a voltage when they are heated. The voltage produced is proportional to the temperature, and it is sent to the control unit for processing. The thermocouple is vital for accurate temperature control and prevents overheating or underheating of the porcelain.
Cooling Fan
The cooling fan ensures that the porcelain cools down at a controlled rate, which is essential for preventing cracks and other defects. It is usually located at the back of the furnace and is activated automatically when the firing process is complete. The fan blows cool air into the chamber, reducing the temperature gradually until it reaches room temperature.
In conclusion, dental ceramic furnaces are critical to the dental industry. They provide a controlled environment for firing and glazing dental ceramics, ensuring that dental professionals can produce high-quality prosthetics, crowns, and other dental ceramics. With the right dental furnace, dental technicians can achieve the perfect combination of strength, durability, and aesthetics in their porcelain work, making dental furnaces an essential tool in any dental laboratory.
Criteria to Consider When Selecting Dental Furnaces
The selection of a dental furnace is an important part of any dental laboratory's operations. Here are some criteria to consider when selecting dental furnaces:
Size of the Furnace
The size of the furnace is an important factor to consider when selecting a dental furnace. The size of the furnace should be appropriate for the size of the laboratory. If the laboratory is small, then a small furnace is required. Conversely, if the laboratory is large, then a large furnace is needed.
Temperature Range
The temperature range of the furnace is another important factor to consider. The temperature range of the furnace should be suitable for the types of materials being processed. Different materials have different temperature requirements. It is important to choose a furnace that can handle the highest temperature required by the materials used in the laboratory.
Easy to Operate and Maintain
The furnace should be easy to operate and maintain. A furnace that is easy to operate and maintain will save time and money in the long run. The furnace should have a large, movable color touchscreen that allows the technician to operate the unit without any complications using the same type of icon controls which are known from mobile phones.
Reliable and Accurate Temperature Control System
It is essential to choose a furnace that has a reliable and accurate temperature control system. The temperature control system should be able to maintain the desired temperature throughout the firing process. A reliable and accurate temperature control system will ensure that the materials being processed are of good quality.
Safety Features
The furnace should have safety features such as over-temperature protection and automatic shut-off. Over-temperature protection is important because it prevents the furnace from overheating and damaging the materials being processed. Automatic shut-off is important because it prevents the furnace from continuing to operate when it is not in use.
High-Quality Materials
The furnace should be made of high-quality materials that are durable and long-lasting. A furnace made of high-quality materials will last longer and require less maintenance.
In conclusion, when selecting a dental furnace, it is essential to consider the size, temperature range, ease of operation and maintenance, reliable and accurate temperature control system, safety features, and the quality of the materials used to build the furnace. By considering these criteria, dental laboratories can ensure that they choose the best furnace for their needs, which will ultimately result in the production of high-quality dental prosthetics.
CONTACT US FOR A FREE CONSULTATION
KINTEK LAB SOLUTION's products and services have been recognized by customers around the world. Our staff will be happy to assist with any inquiry you might have. Contact us for a free consultation and talk to a product specialist to find the most suitable solution for your application needs!