Table of Contents
- Understanding MPCVD: A Superior Diamond Synthesis Technique
- Types of MPCVD and Their Applications
- Advantages of MPCVD over Other Diamond Growth Methods
- MPCVD Setup for High-Quality Diamond Film Deposition
- Challenges and Advancements in MPCVD
- Applications of MPCVD in Diamond Manufacturing
- Conclusion: The Future of MPCVD in Diamond Synthesis
Understanding MPCVD: A Superior Diamond Synthesis Technique
MPCVD (microwave plasma chemical vapor deposition) stands out as a superior diamond synthesis technique, offering advantages over conventional methods like HFCVD (hot filament chemical vapor deposition) and DC-PJ CVD (direct current plasma jet chemical vapor deposition).

Advantages of MPCVD
-
Avoids Contamination: MPCVD eliminates contamination by hot wires, commonly used in HFCVD. These wires release impurities at high temperatures, compromising diamond quality. MPCVD's non-polar discharge prevents such contamination, resulting in high-purity diamonds.
-
Stable Temperature Control: MPCVD offers precise and stable temperature control, crucial for diamond growth. Unlike DC-PJ CVD, it enables smooth and continuous adjustment of microwave power, ensuring consistent reaction temperatures. This stability prevents crystal seeds from detaching from the substrate due to arcing and flame failure.
-
Multiple Gas Compatibility: MPCVD allows the introduction of multiple gases into the reaction system. This versatility meets diverse industrial needs, enabling the synthesis of diamonds with tailored properties.
-
Large Plasma Area: MPCVD generates a stable plasma over a large area, enhancing diamond growth efficiency. The uniform discharge ensures consistent diamond deposition rates and minimizes defects.
-
High Growth Rates: MPCVD achieves exceptionally high growth rates, up to 150 μm/h. This is significantly higher than the standard processes used for polycrystalline MPCVD diamond, which typically yield rates of around 1 μm/h.
-
Reproducible Sample Quality: MPCVD's controlled environment and stable conditions guarantee reproducible sample quality. This consistency is essential for industrial applications where consistency and reliability are paramount.
-
Cost-Effectiveness: MPCVD offers a reasonable cost compared to other CVD diamond-coating techniques. The elimination of hot wires and the use of multiple gases contribute to its cost-effectiveness.
In conclusion, MPCVD's non-polar discharge, stable temperature control, multiple gas compatibility, large plasma area, high growth rates, reproducible sample quality, and cost-effectiveness make it the preferred diamond synthesis method for industrial applications. Its ability to produce high-quality, contamination-free diamonds with tailored properties has revolutionized diamond synthesis and paved the way for its widespread use in various industries.
Types of MPCVD and Their Applications
Microwave plasma chemical vapor deposition (MPCVD) is a widely used technique for the growth of diamond films. Based on the microwave power and gas pressure employed, MPCVD can be classified into two main types: low-pressure plasma MPCVD and high-pressure plasma MPCVD.
Low-Pressure Plasma MPCVD
In low-pressure plasma MPCVD, the gas pressure inside the reactor is maintained at a relatively low level, typically in the range of 10-100 Torr. This low pressure results in a longer electron mean free path, leading to a significant temperature difference between neutral gaseous species and electrons. The electron temperature can reach several thousand Kelvin, while the gas temperature remains relatively low, typically below 1000 K.
The low-pressure plasma environment promotes the generation of highly reactive species, including atomic hydrogen, atomic oxygen, and various radicals. These reactive species play a crucial role in the growth of diamond films by promoting the formation of sp3 bonds and inhibiting the formation of non-diamond phases such as graphite.
Low-pressure plasma MPCVD is particularly suitable for the growth of high-quality diamond films with low defect densities and high purity. This type of MPCVD is commonly used in the production of diamond films for various applications, including cutting tools, heat sinks, and optical windows.
High-Pressure Plasma MPCVD
In high-pressure plasma MPCVD, the gas pressure inside the reactor is maintained at a relatively high level, typically in the range of 1-10 atm. This high pressure results in a shorter electron mean free path, leading to less imbalance in the temperatures of electrons and neutral gaseous species. The electron temperature and gas temperature are typically in the range of 1000-2000 K.
The high-pressure plasma environment favors the generation of a higher concentration of atomic hydrogen and atomic & molecular radicals. These reactive species promote the growth of diamond films at a faster rate compared to low-pressure plasma MPCVD. However, the high-pressure plasma can also lead to the formation of non-diamond phases such as graphite due to the increased probability of collisions between reactive species and gas molecules.
High-pressure plasma MPCVD is particularly suitable for the growth of thick diamond films at a high deposition rate. This type of MPCVD is commonly used in the production of diamond films for applications such as wear-resistant coatings, thermal management, and electronic devices.
Classification of MPCVD Applications Based on Microwave Power and Gas Pressure
MPCVD can be further classified into different applications based on the combination of microwave power and gas pressure used:
-
Low Microwave Power, Low Pressure: This regime is typically used for the growth of high-quality diamond films with low defect densities and high purity. It is suitable for applications such as cutting tools, heat sinks, and optical windows.
-
High Microwave Power, Low Pressure: This regime is used for the growth of diamond films at a higher deposition rate while maintaining good film quality. It is suitable for applications such as wear-resistant coatings and thermal management.
-
Low Microwave Power, High Pressure: This regime is used for the growth of thick diamond films at a relatively low deposition rate. It is suitable for applications such as wear-resistant coatings and electronic devices.
-
High Microwave Power, High Pressure: This regime is used for the growth of thick diamond films at a high deposition rate. It is suitable for applications such as wear-resistant coatings and thermal management.
The choice of microwave power and gas pressure depends on the specific application and the desired properties of the diamond film. By carefully controlling these parameters, MPCVD can be used to produce diamond films with a wide range of properties and applications.
Advantages of MPCVD over Other Diamond Growth Methods
Microwave plasma chemical vapor deposition (MPCVD) is a versatile and widely used technique for diamond synthesis, offering several advantages over other methods such as hot filament chemical vapor deposition (HFCVD) and plasma torch methods.
Comparison of MPCVD with HFCVD and Plasma Torch Methods
Unlike HFCVD, MPCVD employs a non-polar discharge, eliminating the risk of diamond contamination from hot wires. This allows for the use of multiple gases in the reaction system, catering to diverse industrial applications. Additionally, MPCVD provides more stable control over the reaction temperature and microwave power, preventing crystal seed detachment from the substrate due to arcing or flame failure.
Plasma torch methods, on the other hand, often face challenges in maintaining a stable and uniform plasma, leading to variations in film quality. In contrast, MPCVD produces a large area of stable discharge plasma, ensuring consistent film properties across the growth surface.
Benefits of MPCVD in Terms of Charged Particle Density, Large Area Film Deposition, and Film Quality
MPCVD excels in generating a high density of charged particles and reactive gaseous species, which promotes efficient diamond nucleation and growth. The lower pressure growth conditions in MPCVD facilitate the deposition of large area films with improved homogeneity. This is particularly advantageous for applications requiring uniform and high-quality diamond films.
Compared to other CVD methods, MPCVD offers superior control over the film morphology, allowing for the synthesis of single crystal diamond (SCD) with exceptional electronic properties. SCD grown by MPCVD surpasses other laboratory-grown diamond forms, such as polycrystalline diamond (PCD), high-pressure high-temperature (HPHT) diamond, and natural diamond, in terms of electrical conductivity and thermal stability.
In summary, MPCVD's advantages over other diamond growth methods include:
- Elimination of diamond contamination by hot wires
- Use of multiple gases for tailored industrial applications
- Stable control of reaction temperature and microwave power
- Large area of stable discharge plasma
- High density of charged particles and reactive gaseous species
- Deposition of large area films at lower pressure growth
- Better homogeneity and film quality
- Superior electronic properties of single crystal diamond grown by MPCVD
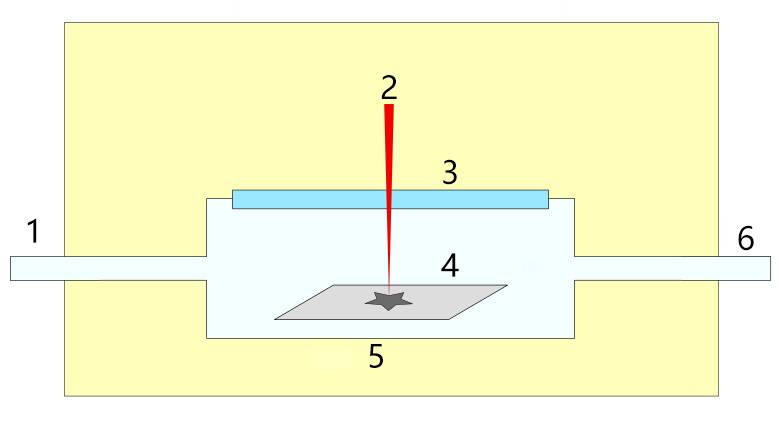
MPCVD Setup for High-Quality Diamond Film Deposition
MPCVD (microwave plasma chemical vapor deposition) is a technique for synthesizing diamond films, which involves the use of microwave radiation to generate plasma and deposit the films. An MPCVD setup consists of several essential components that influence the quality and properties of the deposited diamond films.
Essential Components of an MPCVD Reactor for Diamond Film Deposition
Microwave power generator (magnetron head): Generates microwave radiation to excite the plasma.
Wave guide: Transmits the microwave radiation to the deposition chamber.
Stub tuner: Adjusts the forward and reflected microwave power to optimize plasma generation.
Deposition chamber: Houses the substrate and provides a controlled environment for film deposition. It includes a substrate stage, view ports, and a substrate height adjuster.
Substrate temperature measurement assembly (optical pyrometer): Monitors the temperature of the substrate during deposition.
Gas flow and circulation system: Controls the flow of gases (e.g., methane, hydrogen) into and out of the deposition chamber.
Controlled temperature water circulator (chiller): Regulates the temperature of the substrate stage.
Vacuum system: Maintains a low-pressure environment within the deposition chamber.
Factors Influencing the Quality and Properties of MPCVD Diamond Films
The quality and properties of MPCVD diamond films are influenced by several factors, including:
Air pressure: Higher pressure promotes diamond nucleation but can lead to film contamination.
Gas source concentration and type: The type and concentration of gases (e.g., methane, hydrogen) affect the film's crystal structure, morphology, and properties. Power stability and density: Stable and uniform power delivery ensures consistent plasma generation and film deposition.
Substrate temperature: The substrate temperature influences the nucleation, growth, and properties of the diamond film.
Substrate preparation: Proper substrate preparation (e.g., surface cleaning, nucleation layer deposition) enhances film adhesion and quality.
Deposition time: Longer deposition times typically result in thicker films with improved crystallographic properties.
Optimizing these factors is essential for producing high-quality MPCVD diamond films with desired characteristics for specific applications.
Challenges and Advancements in MPCVD
Despite its advantages, MPCVD faces challenges that hinder its widespread adoption. One significant drawback is its slow growth rate, typically around 1 µm/h, which is considerably lower than other CVD diamond-coating techniques. This slow growth rate limits the practical applications of MPCVD.
Another challenge with MPCVD is the formation of polycrystalline diamond structures. Polycrystalline diamond consists of a patchwork of tiny crystals welded together along misaligned grain boundaries. These grain boundaries can disrupt the flow of current and degrade the overall quality of the diamond film.
To overcome these challenges, ongoing research and development efforts are focused on improving the MPCVD process. Researchers are exploring various strategies to enhance growth rates and promote the formation of single-crystal diamond (SCD). These efforts include optimizing the plasma generation parameters, developing new substrate materials, and refining the deposition conditions.
Recent advancements in MPCVD technology have shown promising results. By optimizing the plasma generation parameters, researchers have achieved growth rates of up to 150 µm/h, a significant improvement over traditional MPCVD techniques. Additionally, the development of new substrate materials, such as high-purity synthetic diamond seeds, has enabled the growth of larger and higher-quality SCD films.
These advancements are paving the way for broader applications of MPCVD in various industries. With continued research and development, MPCVD holds the potential to become a cost-effective and versatile technique for producing high-quality diamond films for a wide range of applications, including electronics, optics, and biomedical devices.
Applications of MPCVD in Diamond Manufacturing
MPCVD (Microwave Plasma Chemical Vapor Deposition) is a versatile technique widely used in the production of high-quality diamonds for various applications. Its unique ability to control diamond growth parameters enables the fabrication of diamonds with tailored properties for specific industrial needs.
Use of MPCVD in the Production of Polycrystalline Diamond Optical Components
MPCVD has revolutionized the production of polycrystalline diamond (PCD) optical components. PCD exhibits exceptional optical properties, including high refractive index, low optical loss, and broad transparency range. These attributes make PCD an ideal material for fabricating optical windows, lenses, and prisms.
MPCVD enables the precise control of crystal orientation, grain size, and impurity levels, resulting in PCD components with superior optical performance. The high thermal conductivity and low thermal expansion coefficient of MPCVD-grown PCD also make it resistant to thermal shock and deformation, ensuring long-term stability in optical systems.
Applications of MPCVD Diamond in Cutting, Grinding, and Polishing Tools
The exceptional hardness and wear resistance of MPCVD diamond make it an ideal material for cutting, grinding, and polishing tools. Diamond-coated tools offer several advantages over conventional tools:
- Increased tool life: The extreme hardness of diamond significantly extends the lifespan of cutting tools, reducing downtime and replacement costs.
- Improved cutting efficiency: Diamond's sharp cutting edge allows for precise and efficient cutting operations, resulting in superior surface finishes.
- Reduced manufacturing costs: For mass production, diamond-coated tools can significantly reduce manufacturing costs by eliminating the need for frequent tool replacements and downtime.
MPCVD is the primary method for producing diamond-coated tools, offering several advantages over other coating techniques. MPCVD-grown diamond coatings exhibit excellent adhesion to the substrate, ensuring durability and longevity. The precise control of diamond growth parameters allows for tailored coatings with specific properties, such as high hardness, wear resistance, and corrosion resistance, to meet the demands of various industrial applications.
Conclusion: The Future of MPCVD in Diamond Synthesis
MPCVD has revolutionized diamond synthesis, offering unparalleled precision, versatility, and scalability. Its ability to produce high-quality diamond films with tailored properties makes it a promising solution for a wide range of industries, from optics and electronics to medical applications. As research and development continue, MPCVD technology is poised to drive further advancements in diamond synthesis, paving the way for novel applications and transformative breakthroughs.
CONTACT US FOR A FREE CONSULTATION
KINTEK LAB SOLUTION's products and services have been recognized by customers around the world. Our staff will be happy to assist with any inquiry you might have. Contact us for a free consultation and talk to a product specialist to find the most suitable solution for your application needs!