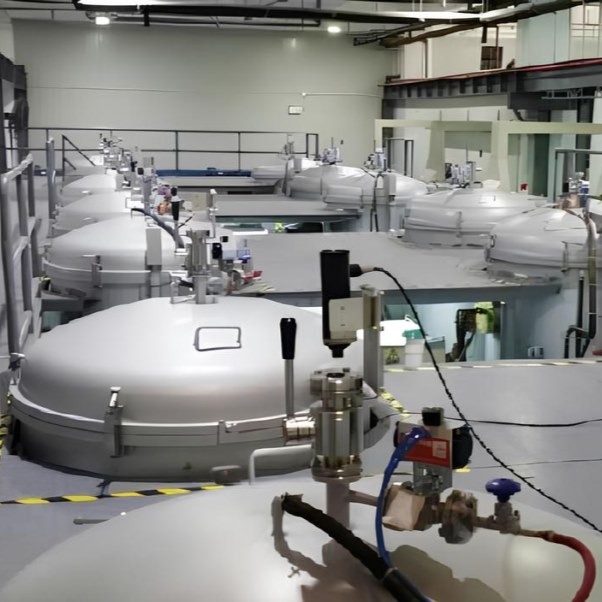
Graphitization furnace
Graphite Vacuum Furnace High Thermal Conductivity Film Graphitization Furnace
Item Number : GF-03
Price varies based on specs and customizations
- Maximum operating temperature
- 3100℃
- Commonly used temperature
- 2800℃
- Temperature uniformity
- ≤±25℃
- Temperature measurement
- far-infrared optical temperature measurement (1000-3200℃)
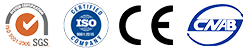
Shipping:
Contact us to get shipping details Enjoy On-time Dispatch Guarantee.
Why Choose Us
Reliable PartnerEasy ordering process, quality products, and dedicated support for your business success.
Introduction
A high thermal conductivity film graphitization furnace is a specialized equipment designed for the graphitization process of high thermal conductivity films, particularly polyimide (PI) films. This furnace utilizes medium frequency induction heating to achieve rapid temperature rise and high efficiency. Its unique design ensures exceptional temperature uniformity throughout the furnace chamber. The furnace is constructed with double-layer alumina brick insulation to prevent short circuits, providing excellent heat insulation and fire resistance, resulting in minimal heat loss and enhanced equipment stability. It offers the flexibility of configuring multiple electric furnaces with a single power supply, allowing continuous operation by powering on furnaces for heating and powering off for cooling. The furnace is equipped with a digital flow monitoring system for each water channel, ensuring comprehensive protection in the power cabinet. It employs high-performance medium frequency contactors and a PLC-based automatic control and protection system for water, electricity, and gas.
Applications
The high thermal conductivity film graphitization furnace is widely used in various industries, including:
- Ceramic firing
- Carbide growth
- Carbonization
- Graphitization
- Sintering
- Annealing
- Brazing
- Degassing
Features
The High thermal conductivity film graphitization furnace feature:
- Temperature uniformity: The unique furnace design ensures excellent temperature uniformity throughout the furnace chamber, resulting in consistent and high-quality graphitization.
- Energy efficiency: Double-layer alumina brick insulation minimizes heat loss, reducing energy consumption and operating costs.
- Stability: The high-performance medium frequency contactor and comprehensive PLC control system ensure stable and reliable operation.
- Multiple furnace operation: A single power supply can be configured with multiple furnaces, allowing for continuous operation and increased productivity.
- Digital flow monitoring: Each channel of water flow is monitored and protected in the power cabinet, ensuring safe and efficient operation.
Principle
The high thermal conductivity film graphitization furnace uses medium frequency induction heating to rapidly increase the temperature of the furnace body, greatly improving temperature uniformity. The double-layer alumina brick insulation material prevents short circuits between carbon felt and the coil, providing good heat insulation and fire resistance, reducing heat loss, and ensuring equipment stability. The furnace can be configured with multiple power supplies to meet the sintering process time requirements, enabling continuous operation with multiple furnaces heating up and cooling down separately. A digital flow monitoring system monitors and protects each water channel in the power cabinet, while the furnace conversion uses a high-performance medium frequency contactor. The PLC water, electricity, gas automatic control and protection system provides comprehensive monitoring and protection.
Advantages
- High temperature uniformity: The furnace's unique design ensures excellent temperature uniformity throughout the furnace chamber, resulting in consistent and reliable results.
- Low energy consumption: The double-layer alumina brick insulation material provides excellent heat insulation and fire resistance, minimizing heat loss and reducing energy consumption.
- Good stability: The furnace's robust construction and high-performance components ensure stable and reliable operation, even under demanding conditions.
- Continuous operation: Multiple furnaces can be powered on and off independently, allowing for continuous operation and maximizing productivity.
- Comprehensive control system: The PLC-based water, electricity, and gas control system provides comprehensive monitoring and protection, ensuring safe and efficient operation.
- Digital flow monitoring system: Each channel of water flow is monitored and protected in the power cabinet, providing real-time feedback and preventing potential issues.
- High-performance medium frequency contactor: The use of high-performance medium frequency contactors ensures reliable and efficient power conversion.
Technical parameters
Maximum operating temperature: 3100℃
Commonly used temperature: 2800℃
Working atmosphere in the furnace: vacuum, hydrogen, nitrogen, inert gas, etc.
Temperature uniformity: ≤±25℃
Temperature measurement: far-infrared optical temperature measurement (1000-3200℃);
Temperature measurement accuracy: 0.2~0.75%
Temperature control: program control and manual control; temperature control accuracy: ±1℃
Product model specifications | GF-03-Ф40×100 | GF-03-Ф50×100 | GF-03-Ф60×100 | GF-03-Ф90×160 |
---|---|---|---|---|
Volume(L) | 125 | 196 | 282 | 1000 |
Rated temperature(C) | 2800 | 2800 | 2800 | 2800 |
Limit temperature(C) | 3100 | 3100 | 3100 | 3100 |
Effective heating area (mm) | Ф400×1000 | Ф500×1000 | Ф600×1000 | Ф900×1000 |
Power(KW) | 150 | 200 | 30 | 600 |
Frequency(HZ) | 1500 | 1000 | 1000 | 1000 |
Temperature control method | Japan Shima Electric Thermostat | |||
Heating method | Induction heating | |||
Vacuum system | Rotary vane vacuum pump (for high vacuum requirements, Roots vacuum pump and oil diffusion pump are required) | |||
Sintering atmosphere | N² Ar and other gases | |||
Rated power supply voltage (V) | 380 | |||
Rated heating voltage (V) | 750 | |||
Vacuum limit (Pa) | 100 (vacuum cold state) |
FAQ
What Is A Graphitization Furnace?
What Is A Graphite Vacuum Furnace Used For?
What Is Polytetrafluoroethylene (PTFE)?
What Are The Advantages Of Using A High Thermal Conductivity Film Graphitization Furnace?
What Is The Difference Between A High Thermal Conductivity Film Graphitization Furnace And A Graphite Tube Furnace?
What Are The Applications Of High Thermal Conductivity Film Graphitization Furnaces?
What Are The Main Applications Of Graphitization Furnaces?
What Are The Main Types Of Graphite Vacuum Furnaces?
What Are The Key Properties And Characteristics Of PTFE?
What Are The Different Types Of Graphitization Furnaces?
How Does A Graphite Vacuum Furnace Work?
What Are The Applications Of PTFE?
How Does A Graphitization Furnace Work?
What Are The Advantages Of Using A Graphite Vacuum Furnace?
What Are The Advantages Of Using PTFE?
What Are The Advantages Of Using A Graphitization Furnace?
What Temperature Range Can A Graphite Vacuum Furnace Achieve?
Are There Any Limitations Or Considerations When Using PTFE?
What Industries Benefit From Graphite Vacuum Furnaces?
4.8
out of
5
The furnace is well-designed and stable, allowing for continuous operation with multiple furnaces heating up and cooling down separately.
4.9
out of
5
I am impressed with the excellent temperature uniformity throughout the furnace chamber, resulting in consistent and high-quality graphitization.
4.6
out of
5
The digital flow monitoring system monitors and protects each water channel in the power cabinet, ensuring safe and efficient operation.
4.7
out of
5
The high-performance medium frequency contactor ensures reliable and efficient power conversion.
4.8
out of
5
The double-layer alumina brick insulation provides excellent heat insulation and fire resistance, minimizing heat loss and reducing energy consumption.
4.9
out of
5
The PLC-based water, electricity, and gas control system provides comprehensive monitoring and protection, ensuring safe and efficient operation.
4.7
out of
5
The furnace's robust construction and high-performance components ensure stable and reliable operation, even under demanding conditions.
4.6
out of
5
The furnace is easy to operate and maintain, which saves us time and resources.
4.8
out of
5
The furnace's unique design ensures excellent temperature uniformity throughout the furnace chamber, resulting in consistent and reliable results.
Products
Graphite Vacuum Furnace High Thermal Conductivity Film Graphitization Furnace
REQUEST A QUOTE
Our professional team will reply to you within one business day. Please feel free to contact us!
Related Products
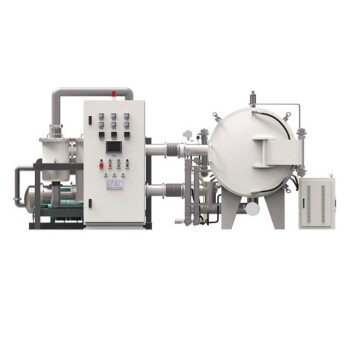
Horizontal High Temperature Graphite Vacuum Graphitization Furnace
Horizontal Graphitization Furnace: This type of furnace is designed with the heating elements placed horizontally, allowing for uniform heating of the sample. It's well-suited for graphitizing large or bulky samples that require precise temperature control and uniformity.
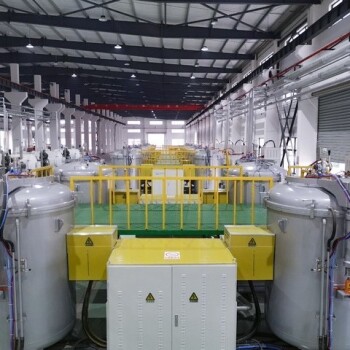
Vertical High Temperature Graphite Vacuum Graphitization Furnace
Vertical high temperature graphitization furnace for carbonization and graphitization of carbon materials up to 3100℃.Suitable for shaped graphitization of carbon fiber filaments and other materials sintered in a carbon environment.Applications in metallurgy, electronics, and aerospace for producing high-quality graphite products like electrodes and crucibles.
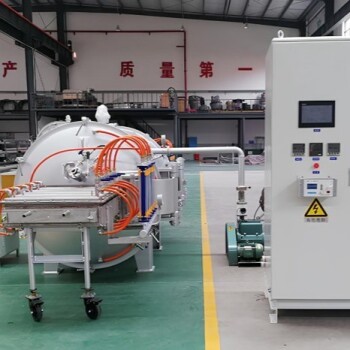
Graphite Vacuum Continuous Graphitization Furnace
High-temperature graphitization furnace is a professional equipment for graphitization treatment of carbon materials. It is a key equipment for the production of high-quality graphite products. It has high temperature, high efficiency and uniform heating. It is suitable for various high-temperature treatments and graphitization treatments. It is widely used in metallurgy, electronics, aerospace, etc. industry.
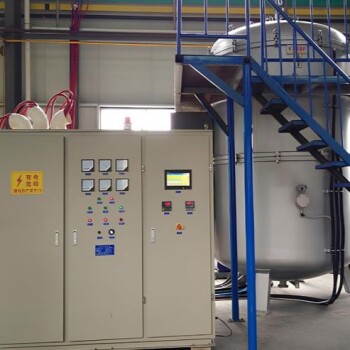
Large Vertical Graphite Vacuum Graphitization Furnace
A large vertical high-temperature graphitization furnace is a type of industrial furnace used for the graphitization of carbon materials, such as carbon fiber and carbon black. It is a high-temperature furnace that can reach temperatures of up to 3100°C.
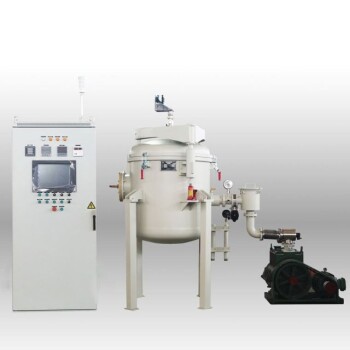
Ultra-High Temperature Graphite Vacuum Graphitization Furnace
The ultra-high temperature graphitization furnace utilizes medium frequency induction heating in a vacuum or inert gas environment. The induction coil generates an alternating magnetic field, inducing eddy currents in the graphite crucible, which heats up and radiates heat to the workpiece, bringing it to the desired temperature. This furnace is primarily used for graphitization and sintering of carbon materials, carbon fiber materials, and other composite materials.

Graphite Vacuum Furnace Bottom Discharge Graphitization Furnace for Carbon Materials
Bottom-out graphitization furnace for carbon materials, ultra-high temperature furnace up to 3100°C, suitable for graphitization and sintering of carbon rods and carbon blocks. Vertical design, bottom discharging, convenient feeding and discharging, high temperature uniformity, low energy consumption, good stability, hydraulic lifting system, convenient loading and unloading.
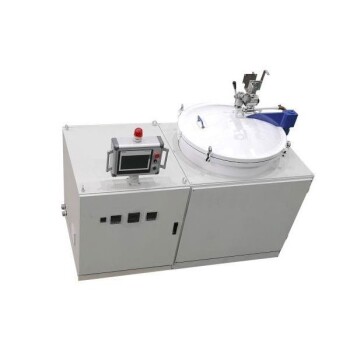
Graphite Vacuum Furnace IGBT Experimental Graphitization Furnace
IGBT experimental graphitization furnace, a tailored solution for universities and research institutions, with high heating efficiency, user-friendliness, and precise temperature control.
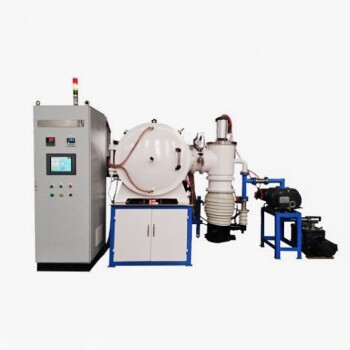
2200 ℃ Graphite Vacuum Heat Treat Furnace
Discover the power of the KT-VG Graphite Vacuum Furnace - with a maximum working temperature of 2200℃, it's perfect for vacuum sintering of various materials. Learn more now.
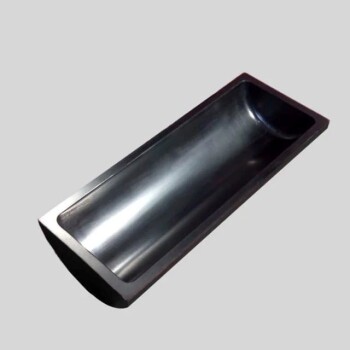
Carbon Graphite Boat -Laboratory Tube Furnace with Cover
Covered Carbon Graphite Boat Laboratory Tube Furnaces are specialized vessels or vessels made of graphite material designed to withstand extreme high temperatures and chemically aggressive environments.
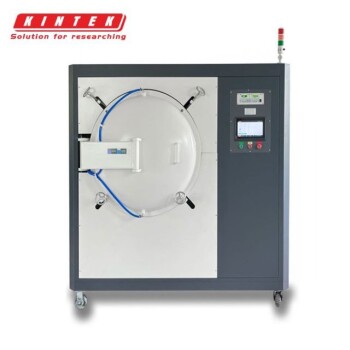
Vacuum Heat Treat Furnace with Ceramic Fiber Liner
Vacuum furnace with polycrystalline ceramic fiber insulation liner for excellent heat insulation and uniform temperature field. Choose from 1200℃ or 1700℃ max. working temperature with high vacuum performance and precise temperature control.
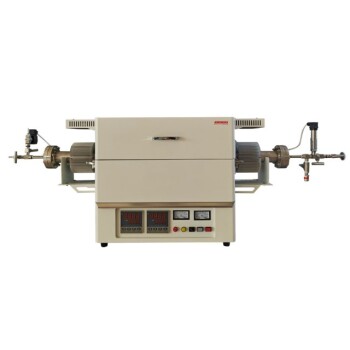
High Pressure Laboratory Vacuum Tube Furnace Quartz Tubular Furnace
KT-PTF High Pressure Tube Furnace: Compact split tube furnace with strong positive pressure resistance. Working temp up to 1100°C and pressure up to 15Mpa. Also works under controller atmosphere or high vacuum.
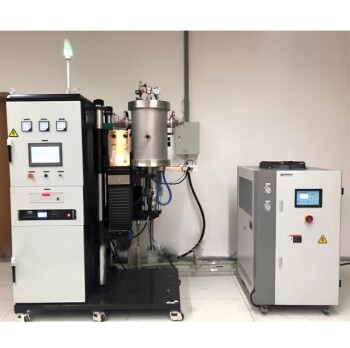
Vacuum Heat Treat and Molybdenum Wire Sintering Furnace for Vacuum Sintering
A vacuum molybdenum wire sintering furnace is a vertical or bedroom structure, which is suitable for withdrawal, brazing, sintering and degassing of metal materials under high vacuum and high temperature conditions. It is also suitable for dehydroxylation treatment of quartz materials.
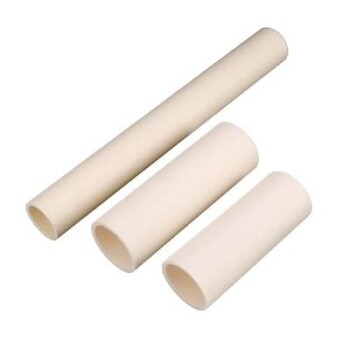
High Temperature Alumina (Al2O3) Furnace Tube for Engineering Advanced Fine Ceramics
High temperature alumina furnace tube combines the advantages of high hardness of alumina, good chemical inertness and steel, and has excellent wear resistance, thermal shock resistance and mechanical shock resistance.
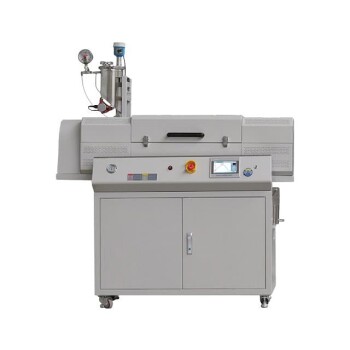
Laboratory Vacuum Tilt Rotary Tube Furnace Rotating Tube Furnace
Discover the versatility of Laboratory Rotary Furnace: Ideal for calcination, drying, sintering, and high-temperature reactions. Adjustable rotating and tilting functions for optimal heating. Suitable for vacuum and controlled atmosphere environments. Learn more now!
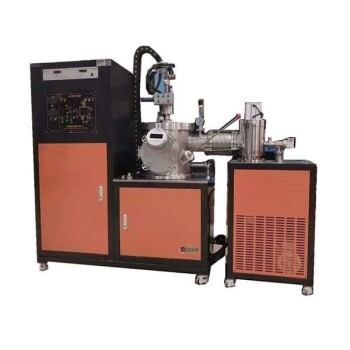
Vacuum Arc Induction Melting Furnace
Discover the power of Vacuum Arc Furnace for melting active & refractory metals. High-speed, remarkable degassing effect, and free of contamination. Learn more now!
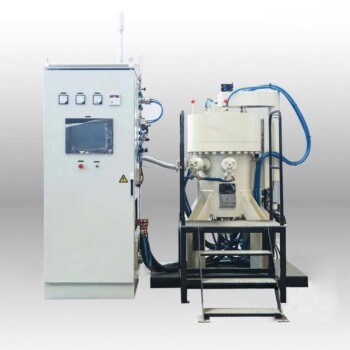
Vacuum Heat Treat and Sintering Furnace with 9MPa Air Pressure
The air pressure sintering furnace is a high-tech equipment commonly used for the sintering of advanced ceramic materials. It combines vacuum sintering and pressure sintering techniques to achieve high-density and high-strength ceramics.
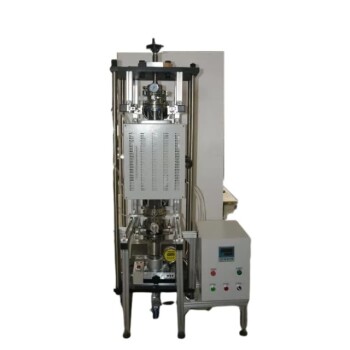
Vacuum Hot Press Furnace Heated Vacuum Press Machine Tube Furnace
Reduce forming pressure & shorten sintering time with Vacuum Tube Hot Press Furnace for high-density, fine-grain materials. Ideal for refractory metals.
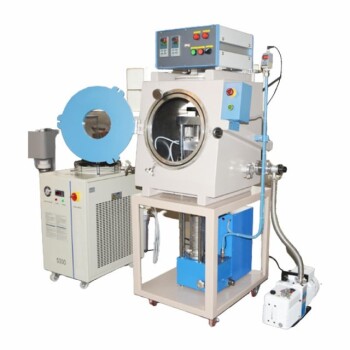
Vacuum Hot Press Furnace Machine for Lamination and Heating
Experience clean and precise lamination with Vacuum Lamination Press. Perfect for wafer bonding, thin-film transformations, and LCP lamination. Order now!
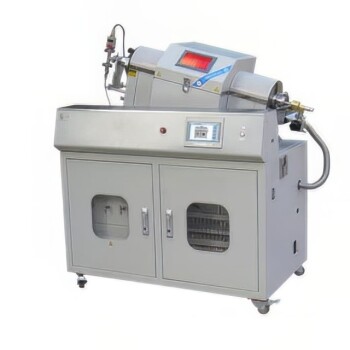
Inclined Rotary Plasma Enhanced Chemical Vapor Deposition PECVD Equipment Tube Furnace Machine
Introducing our inclined rotary PECVD furnace for precise thin film deposition. Enjoy automatic matching source, PID programmable temperature control, and high accuracy MFC mass flowmeter control. Built-in safety features for peace of mind.
Related Articles
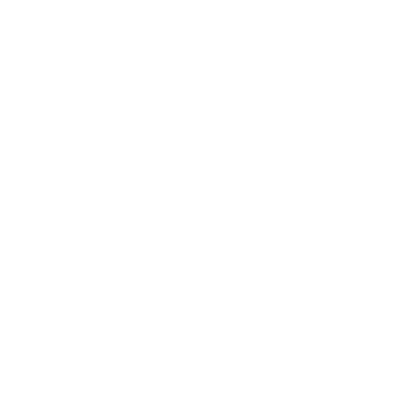
Maximizing Efficiency and Precision with Vacuum Graphite Furnaces
Discover how vacuum graphite furnaces revolutionize high-temperature material treatments with unmatched precision and efficiency. Explore customized solutions for various industries, advanced automation, and sustainable energy practices.
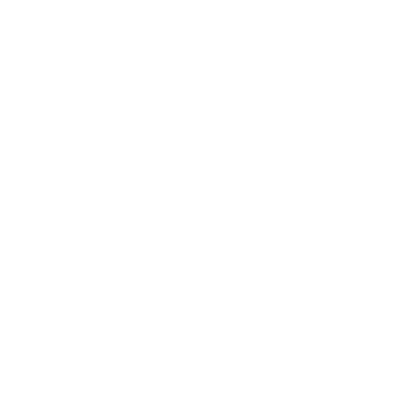
Unveiling Vacuum Graphite Furnaces: Performance, Applications, and Expert Insights
Delve into the world of vacuum graphite furnaces, exploring their exceptional performance, diverse applications, and crucial considerations. Our expert insights empower you to make informed decisions for your laboratory's high-temperature material treatment needs.
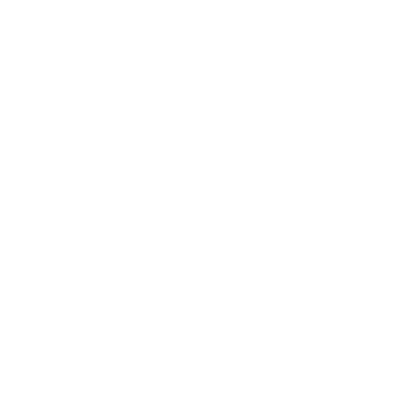
Enhancing Dental Work with a High-Quality Dental Furnace
A dental furnace is a specialized piece of equipment used in dentistry to heat materials to high temperatures. It is typically used to manipulate metal alloys or ceramics, such as those used in crowns, bridges, and other restorative treatments.
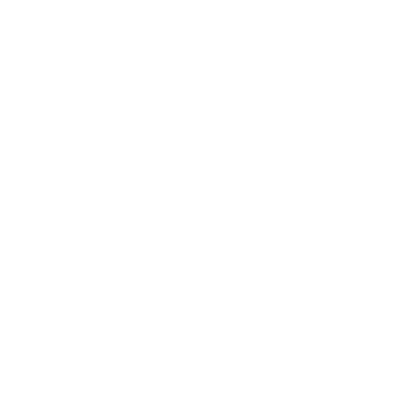
Optimizing Performance with Graphite Vacuum Furnaces: A Comprehensive Guide
Unlock the potential of graphite vacuum furnaces for high-temperature material treatment. Learn about their efficiency, customization options, automation, and key considerations for graphite rod usage.
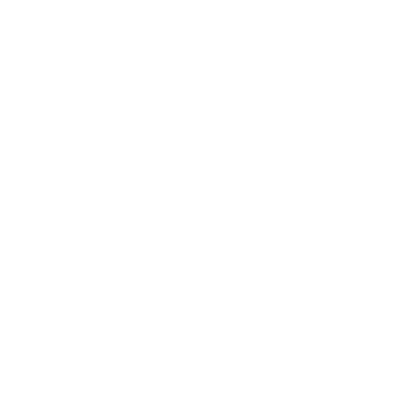
The Role of a Porcelain Furnace in Dental Restorations
Porcelain furnaces play a crucial role in the creation of dental restorations, as they are used to fire ceramic materials, such as porcelain, to create durable and natural-looking dental prosthetics.
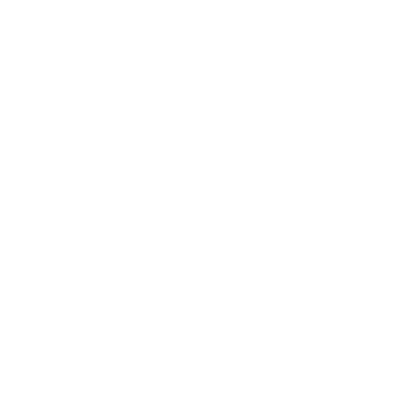
How to Maintain Your Dental Ceramic Furnace
The dental furnaces are expensive and require regular maintenance to ensure they function properly and produce accurate results.
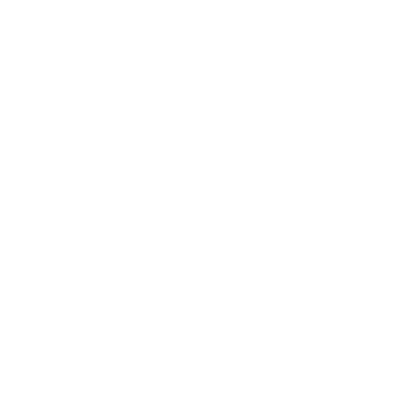
The Importance of Inert Atmosphere Gases in Furnace Atmospheres
Furnace atmospheres play an essential role in the heat treatment process of materials.
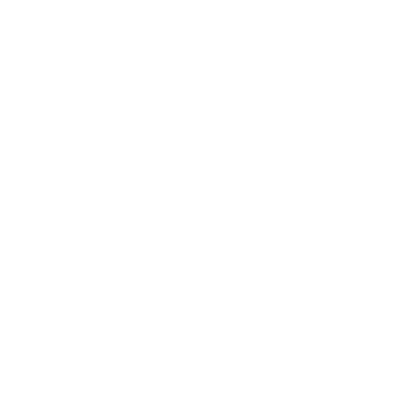
Understanding Electric Heating Systems(1): How Electric Furnaces Work and Their Advantages
Discover how electric heating systems, particularly electric furnaces, work efficiently without the need for flues or chimneys. Explore the benefits and components of electric furnaces, including heating elements, contactors, sequencers, and transformers.
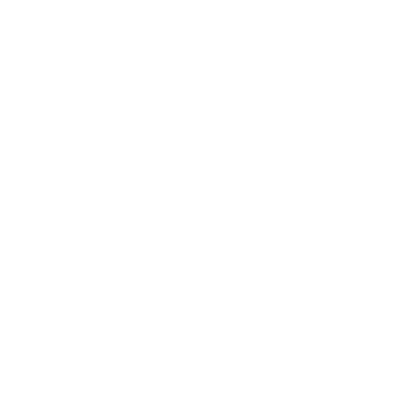
Melting process and maintenance of vacuum induction melting furnace
Melting process and maintenance of vacuum induction melting furnace
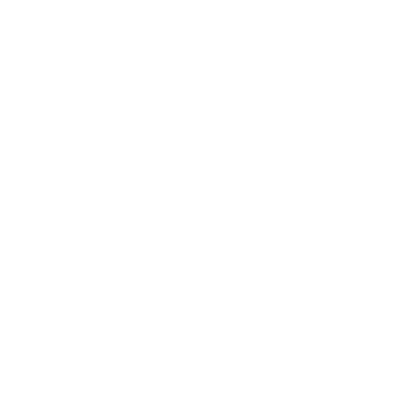
Electric Rotary Kiln Pyrolysis Furnace: A Comprehensive Guide to Pyrolysis Technology
Discover the principles, applications, and advantages of electric rotary kiln pyrolysis furnaces. Explore various heating methods, factors affecting efficiency, and the environmental benefits of this technology.
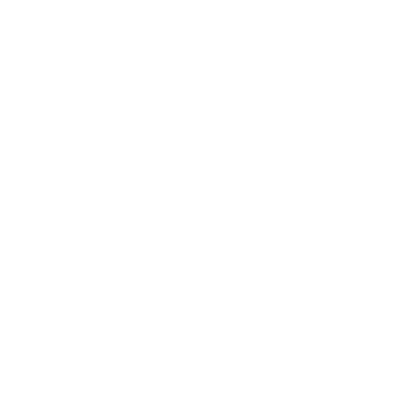
The Advantages and Disadvantages of Different Biomass Feedstocks for Pyrolysis
Different feedstocks have their own unique advantages and disadvantages for pyrolysis, which must be carefully considered when selecting the most suitable feedstock for a particular application.
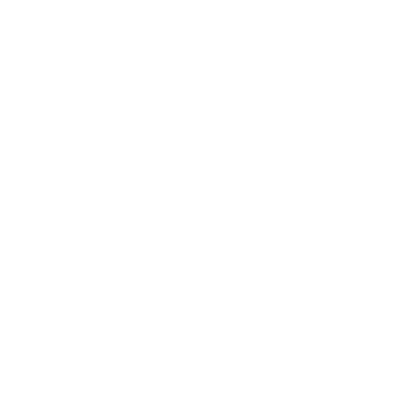
Investigating the Factors Affecting the Slow Temperature Rise in Box Furnaces
Sometimes, the temperature of the furnace may not rise as quickly as expected, or may not be able to reach the desired temperature at all.