Introduction: Importance of Dental Restorations
Dental restorations are vital for maintaining the functionality and aesthetics of teeth. They are used to repair damaged, decayed, or missing teeth, and can improve a patient's quality of life by restoring their ability to chew and speak properly. Without dental restorations, patients may experience pain, discomfort, and difficulty performing daily tasks. Porcelain furnaces play a crucial role in the creation of dental restorations, as they are used to fire ceramic materials, such as porcelain, to create durable and natural-looking dental prosthetics. In this blog post, we will explore the importance of porcelain furnaces in dental restorations and how they are used to create high-quality dental prosthetics.
Table of Contents
- Introduction: Importance of Dental Restorations
- What is a Porcelain Furnace?
- Components of a Porcelain Furnace
- Types of Porcelain Furnaces
- How a Porcelain Furnace Works
- Importance of Porcelain Furnaces
- Components of a Porcelain Furnace
- Types of Dental Furnaces
- How to Choose a Dental Furnace
- Working of Dental Furnace
- Benefits of Using Porcelain Furnaces
- Importance of Ceramic Materials
- Process of Making Porcelain
- Conclusion: Advantages of using porcelain furnaces
What is a Porcelain Furnace?
A porcelain furnace is a vital piece of laboratory equipment used in the production of dental restorations. It is utilized to fire dental crowns, veneers, and bridges made of porcelain or ceramic material. The furnace is designed to heat the material to a high temperature, causing it to fuse together and form a solid, durable piece. This process is known as sintering.
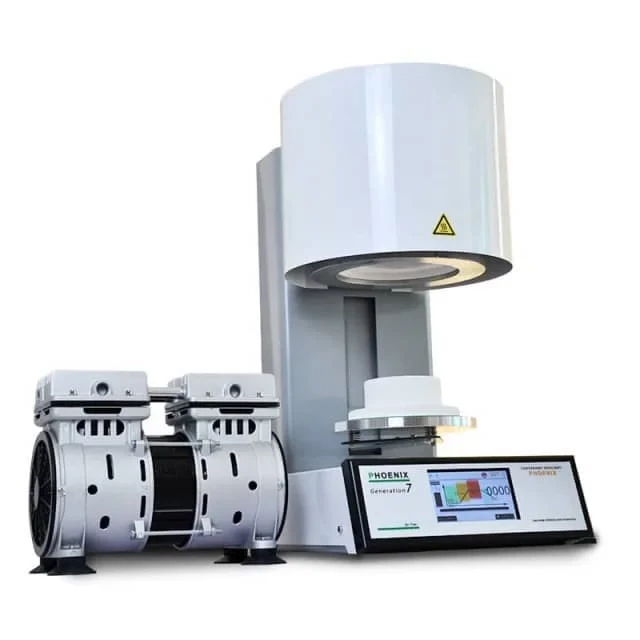
Components of a Porcelain Furnace
Porcelain furnaces come in different sizes and configurations, but they all have some basic components. These include a heating element, a temperature controller, and a chamber for holding the restoration during firing. Some porcelain furnaces may also have additional features, such as vacuum or pressure capabilities, which can improve the quality and consistency of the restoration.
Types of Porcelain Furnaces
There are two main types of dental porcelain furnace systems: direct-fired or cold-press fired, and hot-pressed or heat-fused fired. Direct-fired technology uses an external source to directly fire the ceramic material. This means that there are no internal components needed to preheat the device. Therefore, these devices are considered more cost-effective than indirect-fired technologies due to their lower production costs.
How a Porcelain Furnace Works
A porcelain furnace works by taking an un-glazed ceramic plate and heating it up until it’s soft enough to shape. Then you can use a third-party manufacturer’s pre-made dies to cut and shape the piece into your desired tooth pattern. Once it’s cooled down, you can luster and polish the item to give it its final shine! There are some great benefits of using burners over traditional indirect heat systems.
Importance of Porcelain Furnaces
Porcelain furnaces play a critical role in the production of high-quality dental restorations that are strong, long-lasting, and aesthetically pleasing. Recent developments in dental porcelains have allowed for new ways to create beautiful smiles. A new technology that has surged in popularity is called a dental porcelain furnace, more commonly known as a burner. These furnaces have made it possible to create restorations that are more durable, natural-looking, and lifelike than ever before.
In conclusion, a porcelain furnace is a crucial piece of laboratory equipment that is used to produce high-quality dental restorations. It works by heating the material to a high temperature to fuse it together, resulting in a strong and durable piece. Porcelain furnaces come in different types and configurations, and they are essential in creating beautiful and long-lasting dental restorations.
Components of a Porcelain Furnace
A porcelain furnace is a crucial piece of equipment used in the field of dental restorations. It is used to fire porcelain materials that are used to create dental restorations such as crowns, bridges, and veneers. The furnace is designed to heat the porcelain material to a very high temperature, which causes it to fuse and become hardened. This process, known as sintering, ensures that the porcelain restoration is strong and durable.
Heating Chamber
The heating chamber is the main component of the porcelain furnace. It is where the porcelain material is placed and heated. The size and shape of the heating chamber can vary based on the type of porcelain furnace.
Heating Element
The heating element is responsible for providing the heat necessary to sinter the porcelain material. Typically, the heating element is made of molybdenum disilicide. The heating element is usually located in the upper housing of the furnace and arranged concentrically around the restoration.
Temperature Controller
The temperature controller is used to regulate the temperature inside the furnace, ensuring that it stays within the desired range. Many modern porcelain furnaces have a digital display that allows the operator to easily monitor and adjust the temperature.
Cooling System
The cooling system is used to cool down the furnace after the firing process is complete. This is an essential component of the porcelain furnace as cooling the porcelain too quickly can cause it to crack or break. The cooling system is usually built into the furnace design and can be programmed to cool down at a specific rate.
Additional Features
Some porcelain furnaces may include additional features to improve the accuracy and consistency of the firing process. These features may include programmable firing cycles, multiple heating elements for even heat distribution, and a vacuum pump for removing air from the heating chamber.
In conclusion, a porcelain furnace consists of several components that work together to achieve the desired results. The heating chamber, heating element, temperature controller, and cooling system are the core components of the porcelain furnace. Additional features such as programmable firing cycles, multiple heating elements, and a vacuum pump can help to improve the accuracy and consistency of the firing process, resulting in higher quality dental restorations.
Types of Dental Furnaces
Dental furnaces are an essential piece of equipment used in the production of ceramic dental restorations, such as crowns, bridges, and inlays. There are different types of dental furnaces available in the market that are used for specific purposes. Below are the three main types of dental furnaces that are commonly used:
1. Ceramic Furnaces
Ceramic furnaces are used to process conventional ceramics, which are suitable for all metal-free and porcelain-fused-to-metal crowns. These furnaces are fully automated and allow for exceptional productivity. The firing time in a ceramic furnace is typically longer than other types of furnaces, but it is more cost-effective and can handle a variety of different materials.
2. Combination Furnaces
A combination dental furnace is designed to handle both pressing ceramics and firing ceramic restorations. These furnaces can work with various dental materials and are suitable for different laboratory workflows. Combination furnaces are more versatile than ceramic furnaces, but they are also more expensive.
3. Sintering Furnaces
Sintering furnaces are used primarily to process dental zirconia material and mill it into a bridge, crown, framework, or other forms of restoration. These furnaces can reach high temperatures, which is necessary for zirconia to achieve hardness. During the sintering process, zirconia undergoes a significant amount of shrinkage, which must be taken into account during the design and production of dental restorations.
In addition to these three types of dental furnaces, there are also glazing furnaces that are used for setting certain stains and glazes that add the final shade details to a restoration. When choosing a dental furnace, it is important to consider the specific needs of your dental practice and the materials you will be working with.
Investing in a high-quality dental furnace from a reputable manufacturer is essential to ensure accurate and consistent results in dental restorations. Proper maintenance and calibration of the furnace are also important to ensure its longevity and effectiveness.
How to Choose a Dental Furnace
Choosing the right dental furnace is an important decision for any dental practice. There are several factors to consider when selecting a furnace that will best meet your needs. Here are some of the key factors to consider when choosing a dental furnace:
1. Firing Behavior and Firing Quality
The firing behavior and quality of ceramics are essential factors to consider when selecting a dental furnace. The furnace's temperature should be evenly distributed to ensure consistent firing results. Look for a furnace that is designed to maintain a consistent temperature throughout the firing process.
2. Infrared - A Sensor for Successful Results
Consider a dental furnace with built-in infrared technology to achieve more reliable and faster firing results. This type of technology will provide peace of mind, especially for those who are concerned about the lack of process reliability in firing procedures.
3. Handling - As Easy As Possible
Choose a furnace that is easy to operate and handle. Look for a model that has a large, movable color touchscreen that allows you to operate the unit without any fuss using the same type of icon controls which you know from your mobile phone.
4. Energy-saving Function: For the Benefit of the Environment and Your Wallet
Consider a dental furnace with an energy-saving function that automatically switches over to a stand-by mode to save up to 40% energy. This feature will help you save electricity and use other valuable resources efficiently and responsibly. In the process, you will protect the environment and reduce your electricity bill at the same time.
5. Shade Determination - Leave Nothing to Chance
Consider a dental furnace model that can help you with shade selection. The dentist takes a picture of the selected shades and the natural teeth with a smartphone and sends it to the laboratory. This feature is particularly useful when the dental practice and the laboratory are quite far apart, and the patient may not be able to go to the laboratory to have the tooth shade determined.
In conclusion, when selecting a dental furnace, consider the features that are indispensable to you, the price you can afford and are willing to pay. Good firing behavior and easy handling are the paramount features. Other than that, good judgment will guide you in selecting the perfect furnace that fulfills your needs.
Working of Dental Furnace
A porcelain furnace is an essential tool used in the dental restorations process. The furnace is specifically designed to heat porcelain to high temperatures, allowing it to fuse with metal or ceramic substrates. The working of a dental furnace begins with the preparation of the porcelain mixture, which is then applied to a metal or ceramic substrate.
Substrate Placement
The substrate is then placed inside the furnace, and the temperature is increased gradually to around 900-1000 degrees Celsius. The furnace's chamber is designed to manage the temperature and atmosphere inside, ensuring that the firing process occurs in a controlled environment.
Heating and Fusing
At this temperature, the porcelain begins to melt, and the substrate and porcelain fuse together, creating a strong bond. The firing process is critical to the quality of the final dental restoration, and the furnace's accuracy plays a crucial role in achieving the desired outcome.
Cooling Down
Once the firing process is complete, the furnace is then allowed to cool down slowly, ensuring that the restoration remains intact and does not crack or break. The process of cooling down can take several hours, depending on the type of porcelain and the complexity of the restoration.
Quality Assurance
The use of a porcelain furnace ensures that dental restorations are of high quality, durable, and able to withstand the wear and tear of everyday use. The furnace's accuracy and precision play a crucial role in achieving the desired outcome, and it is crucial to ensure that the furnace is properly calibrated and maintained to ensure consistent results.
In conclusion, the working of a dental furnace is a critical part of the dental restorations process. The furnace's accuracy and precision play a crucial role in achieving the desired outcome, and it is essential to ensure that the furnace is properly calibrated and maintained to ensure consistent results.
Benefits of Using Porcelain Furnaces
Porcelain furnaces are essential tools in modern dentistry, and their use offers numerous benefits for creating high-quality and durable dental restorations. Here are some of the key benefits:
Accurate and Consistent Firing
Porcelain furnaces are designed to provide accurate and consistent firing of porcelain materials, ensuring that the final product meets the required standards. The furnace works by controlling the temperature and timing of the firing process, which ensures the accuracy of the restoration.
Uniform Heating Process
Porcelain furnaces provide a consistent and uniform heating process, which is essential for achieving a precise and accurate fit of the restoration. The porcelain material is heated to high temperatures, allowing it to fuse with metal or ceramic substrates, creating a strong and durable restoration.
Versatile Applications
Porcelain furnaces can handle different types of porcelain materials, including high translucency, high-strength, and low fusing ceramics, making them versatile for different dental applications. The use of porcelain furnaces ensures that the final product is free from defects such as cracks, porosities, and bubbles, which can compromise the quality and longevity of the restoration.
Cost-Effective
While porcelain furnaces are a significant investment for dental laboratories, they can be cost-effective in the long run. The use of porcelain furnaces ensures that the final product is of high quality and durability, reducing the need for costly repairs or replacements.
Time-Efficient
Porcelain furnaces are designed to provide efficient firing times, allowing for faster turnaround times for dental restorations. This can be especially beneficial for dental practices that need to provide quick and efficient services to their patients.
In conclusion, the use of porcelain furnaces in dental restorations offers numerous benefits, including accurate and consistent firing, uniform heating process, versatile applications, cost-effectiveness, and time-efficiency. By investing in a high-quality porcelain furnace, dental laboratories and practices can provide their patients with high-quality and durable restorations that meet the required standards.
Importance of Ceramic Materials
Ceramic materials are highly valued in dental restorations because of their strength, durability, and aesthetic appeal. They can be used to create a wide range of dental restorations, including crowns, bridges, and veneers. The use of ceramic materials has become increasingly popular in recent years due to their biocompatibility and natural appearance.
Strength and Durability
Ceramic materials are known for their strength and durability, making them an ideal choice for dental restorations. They can withstand the forces of biting and chewing, and are resistant to wear and tear. With proper care, ceramic restorations can last for many years, providing patients with a long-lasting and reliable solution for their dental needs.
Aesthetic Appeal
Ceramic materials are also highly valued for their aesthetic appeal. They can be matched to the natural color of the patient's teeth, providing a seamless and natural-looking restoration. This is particularly important for restorations that are visible when the patient smiles or speaks.
Precision Firing with Porcelain Furnace
To achieve the best results with ceramic materials, it is important to use a high-quality porcelain furnace that is capable of delivering consistent, precise heat. This ensures that the ceramic materials are fired at the correct temperature and for the correct amount of time, resulting in restorations that are strong, durable, and aesthetically pleasing. Without a reliable porcelain furnace, dental professionals would not be able to produce the high-quality restorations that patients demand.
Types of Ceramic Materials
There are several types of ceramic materials used in dental restorations, including leucite-based and lithium disilicate-based ceramics. Each type has its own unique properties and benefits, and the choice of material will depend on the specific needs of the patient.
Conclusion
In conclusion, the importance of ceramic materials in dental restorations cannot be overstated. They provide a strong, durable, and aesthetically pleasing solution for patients with a wide range of dental needs. To achieve the best results with ceramic materials, it is important to use a high-quality porcelain furnace that is capable of delivering consistent, precise heat. Dental professionals must invest in high-quality porcelain furnaces to ensure that they are able to produce restorations that meet the needs and expectations of their patients.
Process of Making Porcelain
The process of making porcelain restorations is an intricate and precise one that involves several steps. Here is a step-by-step breakdown of the process:
Step 1: Taking Impressions of the Patient's Teeth
The process of making porcelain restorations begins with the dentist taking impressions of the patient's teeth. These impressions are sent to the dental laboratory where technicians will use them to create a model of the patient's mouth.
Step 2: Creating a Wax Replica
The model of the patient's mouth is then used to create a wax replica of the patient's teeth. This wax replica is used to create a mold.
Step 3: Filling the Mold with Porcelain Powder
The mold is then filled with porcelain powder. The porcelain powder is heated in a porcelain furnace, which heats the porcelain to a high temperature, causing it to fuse together and become a solid, durable material.
Step 4: Polishing and Shaping the Restoration
Once the porcelain has cooled, it is polished and shaped to fit the patient's mouth. The finished restoration is then sent back to the dentist, who cements it in place in the patient's mouth.
The use of a porcelain furnace ensures that the porcelain is heated to the correct temperature and that it is fused together properly, resulting in a high-quality restoration that is both functional and aesthetically pleasing.
It is important to note that the process of creating porcelain restorations is a delicate one that requires precision and attention to detail. Any mistakes made during the process can result in a restoration that is not properly fitted or aesthetically pleasing. This is why it is important for dental laboratories to have access to the latest porcelain furnace technology and skilled technicians who are trained in its use.
Conclusion: Advantages of using porcelain furnaces
In conclusion, porcelain furnaces play an essential role in dental restorations. They help with the creation of high-quality ceramic materials that can withstand the harsh conditions of the human mouth. Porcelain furnaces come in different types, and it's crucial to choose the right one for your needs. By using porcelain furnaces, dental practitioners can create customized restorations that match the patient's natural teeth. The benefits of using porcelain furnaces include the ability to produce durable and long-lasting restorations, improved aesthetics, and increased patient satisfaction. Overall, the use of porcelain furnaces in dental restorations is a reliable and cost-effective solution for creating high-quality dental restorations.
CONTACT US FOR A FREE CONSULTATION
KINTEK LAB SOLUTION's products and services have been recognized by customers around the world. Our staff will be happy to assist with any inquiry you might have. Contact us for a free consultation and talk to a product specialist to find the most suitable solution for your application needs!