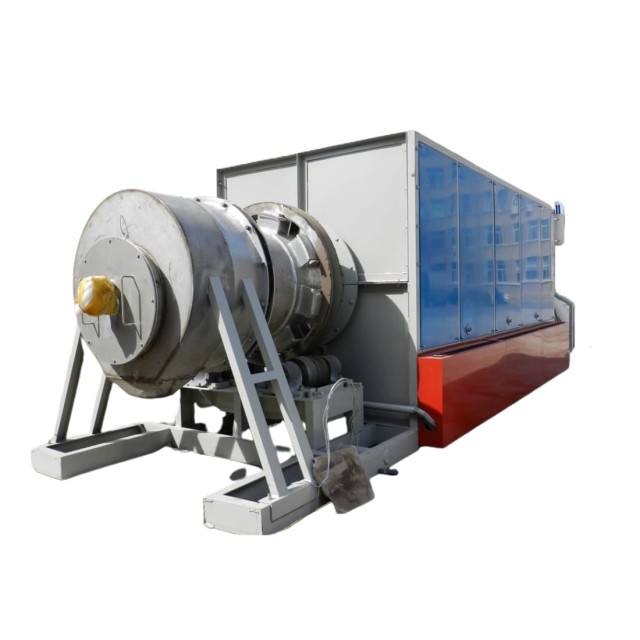
Rotary Furnace
Electric Rotary Kiln Small Rotary Furnace for Activated Carbon Regeneration
Item Number : KT-CRF
Price varies based on specs and customizations
- Constant work temperature
- < 800 ℃
- Rotary drum speed
- 0-5 rpm
- Rotary drum angle
- 0-6 degree
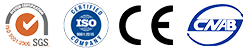
Shipping:
Contact us to get shipping details Enjoy On-time Dispatch Guarantee.
Why Choose Us
Reliable PartnerEasy ordering process, quality products, and dedicated support for your business success.
Introduction
Electric activated carbon regeneration furnace is a highly automated rotary kiln used to restore the adsorption performance of activated carbon. It consists of a feeding system, rotary kiln drum, heating and insulation body, discharging and dust collecting system, and center control cabinet. The furnace features adjustable feeding and rotary drum speeds, high-accurate PID intelligent thermal controller, touch screen controller with intelligent PID thermal control technology, high recovery rate of iodine value, low carbon loss in production, and superior quality Silicon Carbide (SiC) heating element.
Applications
Electric activated carbon regeneration furnaces are widely used in various industries, including:
- Environmental protection: Regeneration of activated carbon used in wastewater treatment, air purification, and soil remediation.
- Metallurgy: Removal of impurities from activated carbon used in metal processing and refining.
- Chemical industry: Regeneration of activated carbon used in chemical production and purification processes.
- Medicine: Regeneration of activated carbon used in pharmaceutical manufacturing and medical applications.
- Food industry: Regeneration of activated carbon used in food processing and beverage production.
Detail & Parts
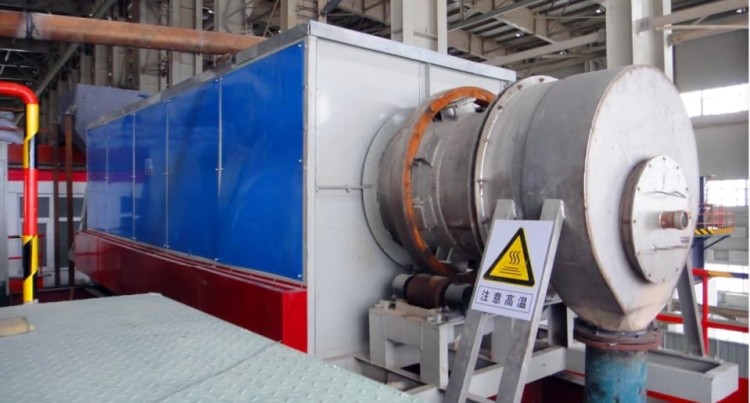
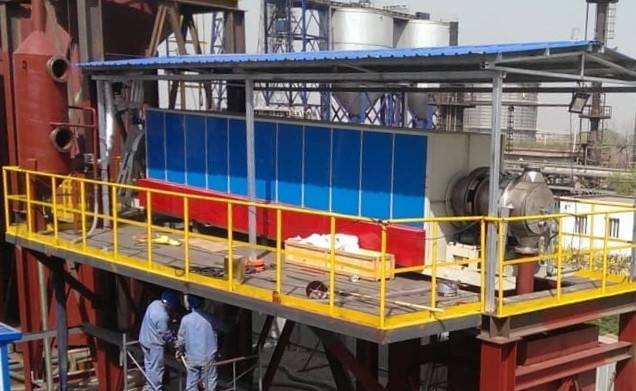
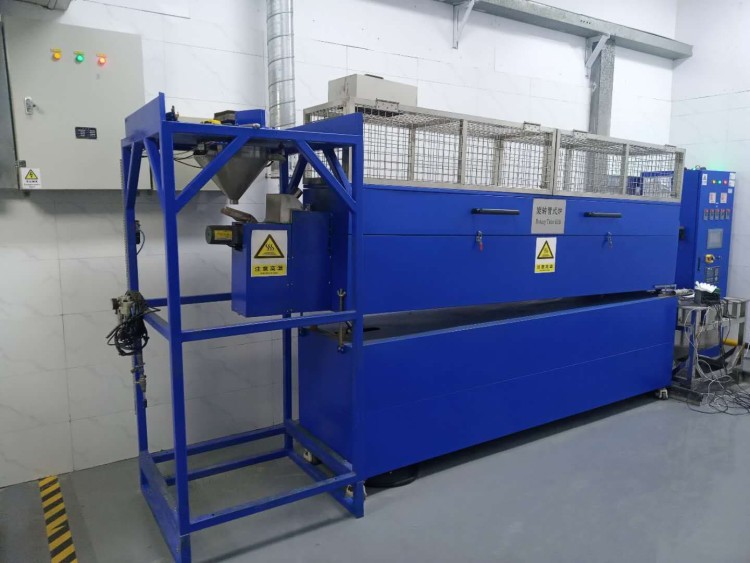
Principle
Electric activated carbon regeneration furnace is a type of electric external heating rotary furnace that utilizes a high-speed electric heating system to reduce furnace stopping and starting time. It consists of a feeding system, rotary kiln drum, drum support and drive system, furnace heating and insulation body, discharging and dust collecting system, and a center control cabinet. The furnace employs touch screen control with intelligent PID thermal control technology, allowing for precise temperature regulation and monitoring. It also features a high recovery rate of iodine value, economical steam inert atmosphere to prevent carbon oxidation, low carbon loss in production, and advanced dynamic sealing technology to prevent carbon burn loss.
Features
Electric activated carbon regeneration furnace features high automation, adjustable feeding speed and rotary drum speed, high-precision PID intelligent thermal controller, and three independently controlled heating zones to optimize the temperature gradient of the drying, calcining, and activating stages. It also boasts a high recovery rate of iodine value, economical steam inert atmosphere to prevent carbon oxidation, and advanced dynamic sealing technology capable of bearing high positive pressure working, avoiding carbon burn loss. Additionally, the furnace utilizes a nickel-based alloy furnace tube for high temperature and corrosion resistance, and a superior quality Silicon Carbide (SiC) heating element for a long service life and trouble-free heating element maintenance.
Advantages
- High recovery rate of iodine value, economical steam inert atmosphere to prevent carbon oxidization, and promote the development of activated carbon porosity, increase the iodine value and improve the regenerated carbon adsorption rate
- Low carbon loss in the production, scientific feeding and discharging system to prevent the carbon breakage, advanced dynamic sealing technology capable to bear high positive pressure working, avoid the carbon burn loss
- Nickel based alloy furnace tube, high temperature and corrosion resistant, no deformation happen in the continuous working temperature at 1100 ℃
- Superior quality Silicon Carbide (SiC) hearing element, long service life and trouble free heating element maintenance
- Smokeless thermal efficiency can also be achieved and there would be no storage equipment for fuel or fuel transport costs
- Energy-saving function, automatically switch over to a stand-by mode to save up to 40% energy
Technical specifications
Constant work temperature | < 800℃ |
Rotary drum speed | 0-5rpm |
Rotary drum angle | 0-6 degree |
Chamber insulation material | Polycrystalline ceramic fiber |
Temperature controller | Touch screen PID controller |
Heating element | Silicon Carbide (SiC) |
Temperature sensor | Armed K type thermal couple |
Electric power supply | AC220-440V,50/60HZ |
Standard models
Model | Capacity (kg/h) | Rated power (kw) | Dimension (m) |
KT-CRF60 | 60 | 63 | 7.0*1.6*2.2 |
KT-CRF100 | 100 | 103 | 7.0*1.6*2.2 |
KT-CRF200 | 200 | 205.5 | 8.0*1.8*2.2 |
KT-CRF300 | 300 | 305.5 | 8.0*1.8*2.2 |
Warnings
Operator safety is the top important issue! Please operate the equipment with cautions. Working with inflammable& explosive or toxic gases is very dangerous, operators must take all necessary precautions before starting the equipment. Working with positive pressure inside the reactors or chambers is dangerous, operator must fellow the safety procedures strictly. Extra caution must also be taken when operating with air-reactive materials, especially under vacuum. A leak can draw air into the apparatus and cause a violent reaction to occur.
Designed for You
KinTek provide deep custom made service and equipment to worldwide customers, our specialized teamwork and rich experienced engineers are capable to undertake the custom tailoring hardware and software equipment requirements, and help our customer to build up the exclusive and personalized equipment and solution!
Would you please drop your ideas to us, our engineers are ready for you now!
FAQ
What Types Of Materials Can Be Processed In A Rotary Furnace?
What Is Electric Rotary Kiln?
What Is A Rotary Tube Furnace?
What Are The Rotary Furnace Types?
How Does A Electric Rotary Kiln Work?
How Does A Rotary Tube Furnace Work?
What Are The Advantages Of Rotor Furnace?
What Are The Advantages Of Electric Rotary Kiln?
What Are The Advantages Of A Rotary Tube Furnace?
What Is The Function Of Rotary Tube Furnace?
What Is The Efficiency Of A Rotary Furnace?
What Can Electric Rotary Kiln Be Used For?
What Are The Advantages Of Rotary Tube Furnace?
Can A Rotary Furnace Be Used For Continuous Production?
How Can The Performance Of A Rotary Furnace Be Optimized?
4.8
out of
5
I'm amazed by the speed of delivery! It arrived within 3 days of placing the order. The quality is top-notch, and I'm confident it will last for years.
4.9
out of
5
This electric activated carbon regeneration furnace is worth every penny. It's efficient and easy to use, and it has significantly reduced our operating costs.
4.7
out of
5
I was skeptical at first, but I'm glad I took a chance on this product. It's user-friendly, and the technical support team is always ready to assist. Highly recommended!
5.0
out of
5
This furnace has been a lifesaver for our laboratory. It's durable, reliable, and has helped us improve our productivity. A must-have for any lab.
4.8
out of
5
I'm impressed with the technological advancements in this furnace. It's energy-efficient and environmentally friendly, making it a responsible choice for our lab.
4.9
out of
5
The furnace arrived in perfect condition, and installation was a breeze. It's easy to operate and has quickly become an essential tool in our lab.
5.0
out of
5
This furnace is a game-changer for our research. It's accurate, precise, and has enabled us to obtain valuable data. Highly satisfied!
4.7
out of
5
I'm thrilled with this purchase. The furnace is well-made and functions flawlessly. It's a valuable addition to our lab equipment.
4.8
out of
5
The furnace exceeded my expectations. It's efficient, user-friendly, and has helped us streamline our research processes. Highly recommend!
4.9
out of
5
This furnace is a testament to technological innovation. It's efficient, reliable, and has improved the accuracy of our experiments. A must-have for any modern lab.
5.0
out of
5
I'm amazed by the quality and performance of this furnace. It's a valuable asset to our lab, enabling us to conduct experiments with precision and accuracy.
4.7
out of
5
This furnace is a great investment for our lab. It's durable, easy to operate, and has helped us improve the efficiency of our research.
4.8
out of
5
I'm glad I chose this furnace for our lab. It's reliable, accurate, and has helped us obtain consistent results in our experiments.
Products
Electric Rotary Kiln Small Rotary Furnace for Activated Carbon Regeneration
REQUEST A QUOTE
Our professional team will reply to you within one business day. Please feel free to contact us!
Related Products
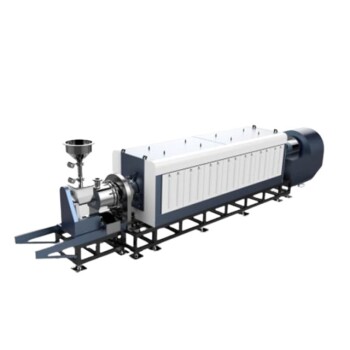
Electric Rotary Kiln Small Rotary Furnace Biomass Pyrolysis Plant
Learn about Rotary Biomass Pyrolysis Furnaces & how they decompose organic material at high temps without oxygen. Use for biofuels, waste processing, chemicals & more.
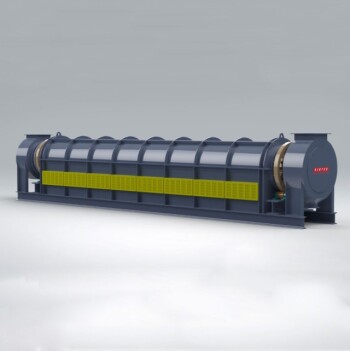
Electric Rotary Kiln Pyrolysis Furnace Plant Machine Calciner Small Rotary Kiln Rotating Furnace
Electric rotary kiln - precisely controlled, it's ideal for calcination and drying of materials like lithium cobalate, rare earths, and non-ferrous metals.
Electric Rotary Kiln Continuous Working Small Rotary Furnace Heating Pyrolysis Plant
Efficiently calcine and dry bulk powder and lump fluid materials with an electric heating rotary furnace. Ideal for processing lithium ion battery materials and more.
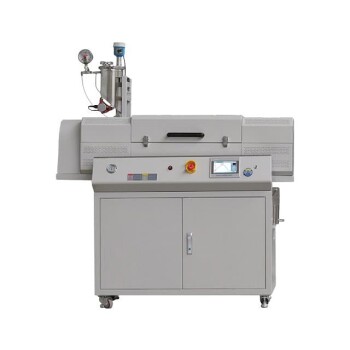
Laboratory Vacuum Tilt Rotary Tube Furnace Rotating Tube Furnace
Discover the versatility of Laboratory Rotary Furnace: Ideal for calcination, drying, sintering, and high-temperature reactions. Adjustable rotating and tilting functions for optimal heating. Suitable for vacuum and controlled atmosphere environments. Learn more now!
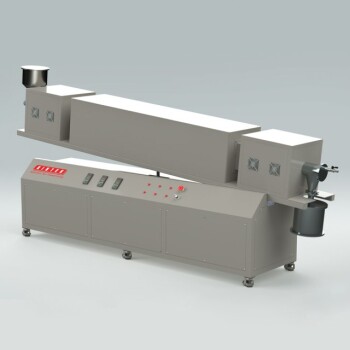
Vacuum Sealed Continuous Working Rotary Tube Furnace Rotating Tube Furnace
Experience efficient material processing with our vacuum-sealed rotary tube furnace. Perfect for experiments or industrial production, equipped with optional features for controlled feeding and optimized results. Order now.
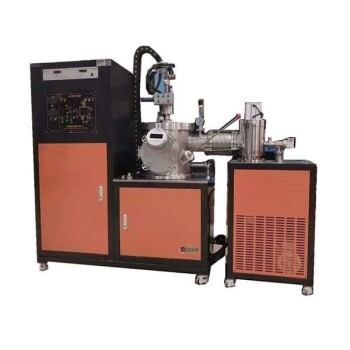
Vacuum Arc Induction Melting Furnace
Discover the power of Vacuum Arc Furnace for melting active & refractory metals. High-speed, remarkable degassing effect, and free of contamination. Learn more now!
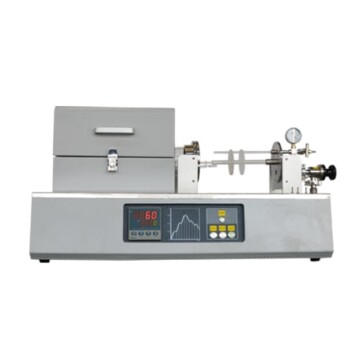
Laboratory Quartz Tube Furnace Tubular RTP Heating Furnace
Get lightning-fast heating with our RTP Rapid Heating Tube Furnace. Designed for precise, high-speed heating and cooling with convenient sliding rail and TFT touch screen controller. Order now for ideal thermal processing!
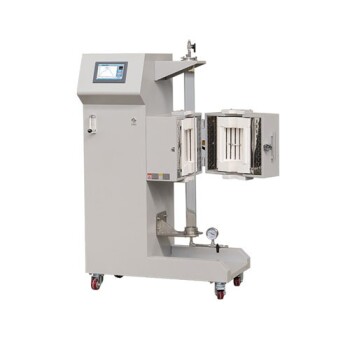
Vertical Laboratory Quartz Tube Furnace Tubular Furnace
Elevate your experiments with our Vertical Tube Furnace. Versatile design allows for operation under various environments and heat treatment applications. Order now for precise results!
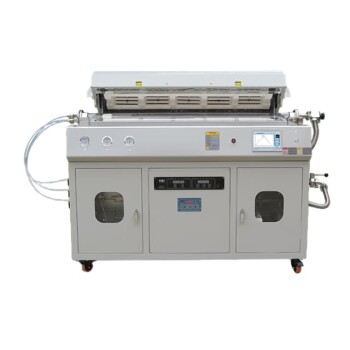
Multi Heating Zones CVD Tube Furnace Machine Chemical Vapor Deposition Chamber System Equipment
KT-CTF14 Multi Heating Zones CVD Furnace - Precise Temperature Control and Gas Flow for Advanced Applications. Max temp up to 1200℃, 4 channels MFC mass flow meter, and 7" TFT touch screen controller.
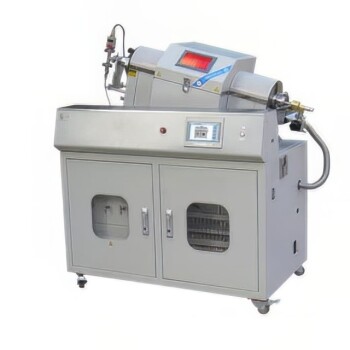
Inclined Rotary Plasma Enhanced Chemical Vapor Deposition PECVD Equipment Tube Furnace Machine
Introducing our inclined rotary PECVD furnace for precise thin film deposition. Enjoy automatic matching source, PID programmable temperature control, and high accuracy MFC mass flowmeter control. Built-in safety features for peace of mind.
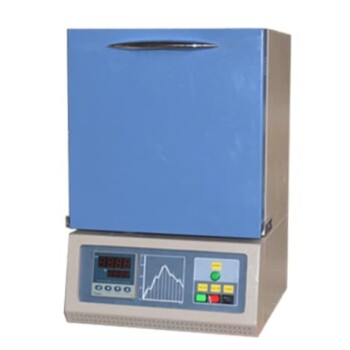
1200℃ Muffle Furnace Oven for Laboratory
Upgrade your lab with our 1200℃ Muffle Furnace. Achieve fast, precise heating with Japan alumina fibers and Molybdenum coils. Features TFT touch screen controller for easy programming and data analysis. Order now!
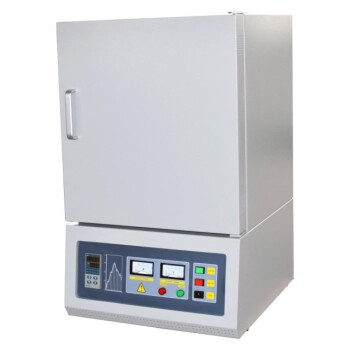
1700℃ Muffle Oven Furnace for Laboratory
Get superior heat control with our 1700℃ Muffle Furnace. Equipped with intelligent temperature microprocessor, TFT touch screen controller & advanced insulation materials for precise heating up to 1700C. Order now!
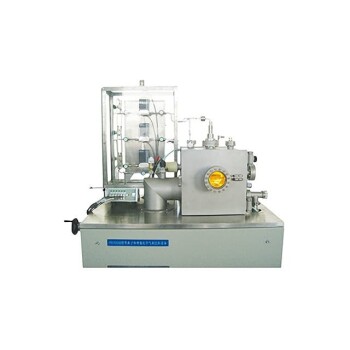
Inclined Rotary Plasma Enhanced Chemical Vapor Deposition PECVD Equipment Tube Furnace Machine
Upgrade your coating process with PECVD coating equipment. Ideal for LED, power semiconductors, MEMS and more. Deposits high-quality solid films at low temps.

Graphite Vacuum Furnace Bottom Discharge Graphitization Furnace for Carbon Materials
Bottom-out graphitization furnace for carbon materials, ultra-high temperature furnace up to 3100°C, suitable for graphitization and sintering of carbon rods and carbon blocks. Vertical design, bottom discharging, convenient feeding and discharging, high temperature uniformity, low energy consumption, good stability, hydraulic lifting system, convenient loading and unloading.
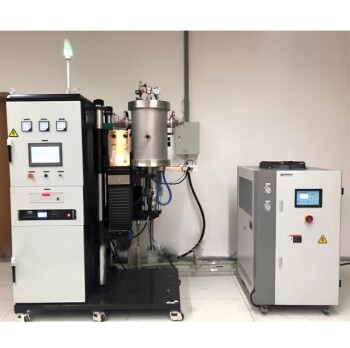
Vacuum Heat Treat and Molybdenum Wire Sintering Furnace for Vacuum Sintering
A vacuum molybdenum wire sintering furnace is a vertical or bedroom structure, which is suitable for withdrawal, brazing, sintering and degassing of metal materials under high vacuum and high temperature conditions. It is also suitable for dehydroxylation treatment of quartz materials.
Related Articles
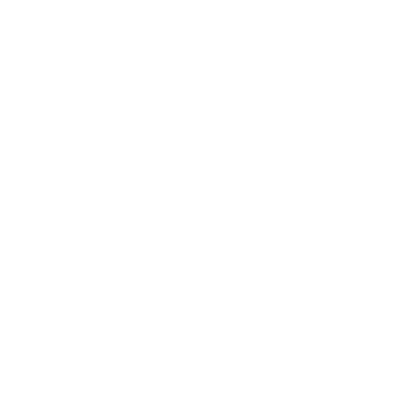
What is activated carbon regeneration Rotary Furnace
Electric activated carbon regeneration furnace is one typical electric external heating rotary furnace
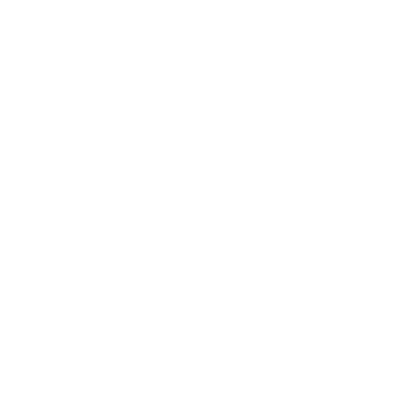
Electric Rotary Kiln Pyrolysis Furnace: A Comprehensive Guide to Pyrolysis Technology
Discover the principles, applications, and advantages of electric rotary kiln pyrolysis furnaces. Explore various heating methods, factors affecting efficiency, and the environmental benefits of this technology.
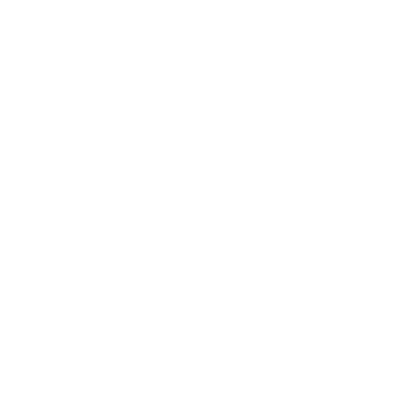
All About ACTIVATED CARBON THERMAL REGENERATION
Introduction, method and selection of activated carbon regeneration
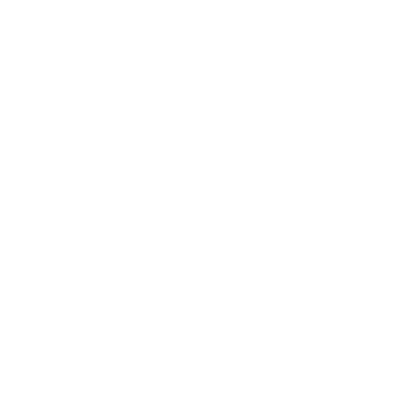
6 Ways To activated carbon regeneration
Activated Carbon Regeneration: Thermal Regeneration Method, Biological Regeneration Method, Wet Oxidation Regeneration Method, Solvent Regeneration Method, Electrochemical Regeneration Method, Catalytic Wet Oxidation Method
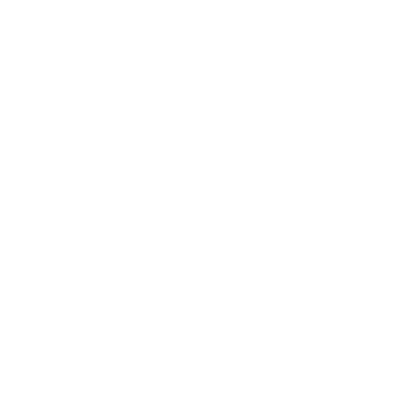
The Importance of Activated Carbon Regeneration in Water Treatment
In water treatment, activated carbon is often used as a means of removing unwanted contaminants, such as chlorine, chloramines, and organic matter, from drinking water and wastewater.
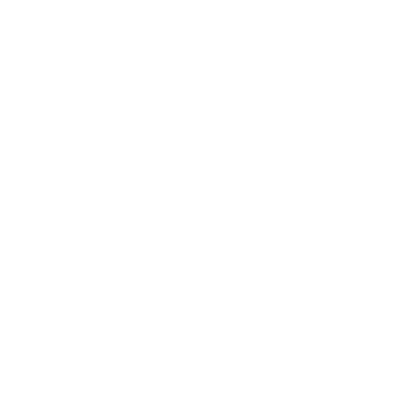
Optimizing Industrial Processes: Rotary Kiln and Laboratory Furnace Solutions
Discover how rotary kilns and laboratory furnaces revolutionize industrial processes. Learn about rotary kiln sizing and design, laboratory furnace features, and industries served. Explore the production of carbon products like biochar and activated carbon.
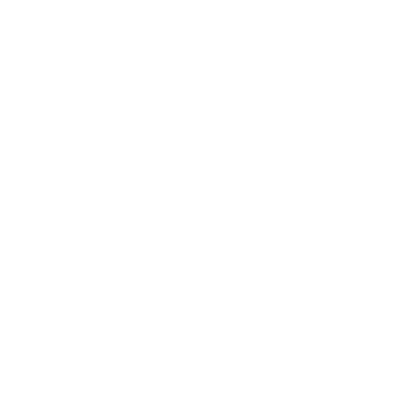
Rotary Furnaces: A Comprehensive Guide to Advanced Materials Processing
Rotary furnaces are widely used for advanced materials processing due to their versatility, temperature uniformity, and energy efficiency. This guide provides an overview of rotary furnace technology, including its working principle, applications, design improvements, and control systems.
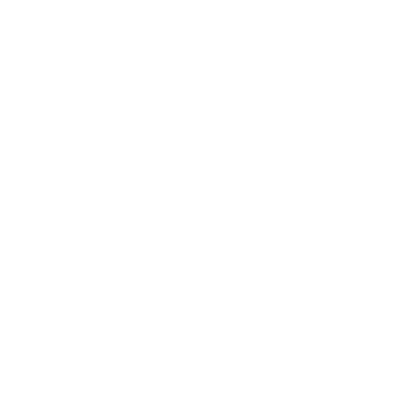
Electric Rotary Kiln Pyrolysis Furnace: Design, Operation, and Applications
Explore the comprehensive guide on electric rotary kiln pyrolysis furnaces, including their design, operation, efficiency factors, and diverse applications in industries like waste processing and biofuel production.
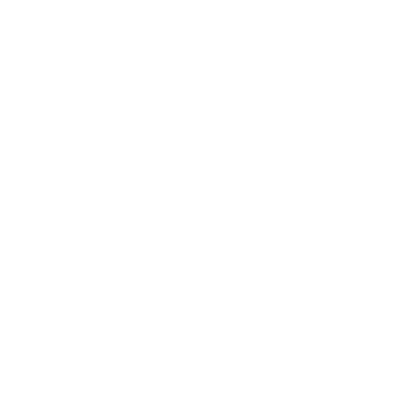
Comprehensive Guide to Muffle Furnaces: Applications, Types, and Maintenance
Explore the world of muffle furnaces with our detailed guide. Learn about their applications in various industries, types available, and essential maintenance tips to ensure optimal performance.
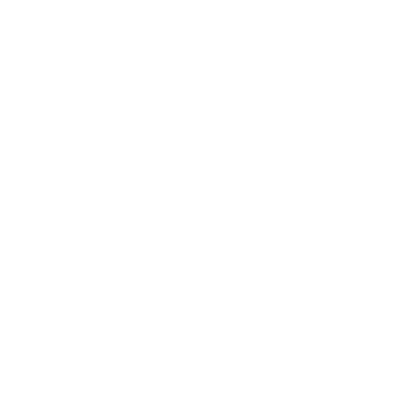
A Comprehensive Guide to Rotary Kilns: Applications, Types, and Working Principles
Discover the diverse applications of rotary kilns across industries such as carbon products manufacturing and industrial sintering. Learn about different types of rotary kilns and their working principles, along with insights into laboratory furnaces and pyrolysis furnaces.
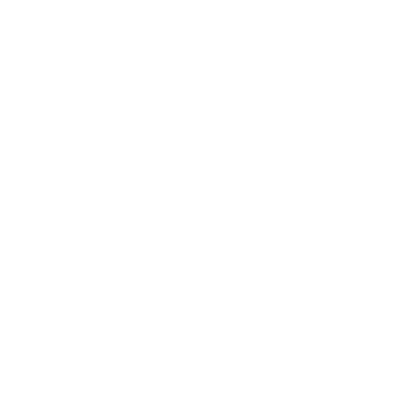
Exploring the Benefits and Applications of Rotary Furnaces: A Comprehensive Guide
Rotary tube furnaces are highly versatile tools that can be used for a wide range of physicochemical processing applications in the laboratory.
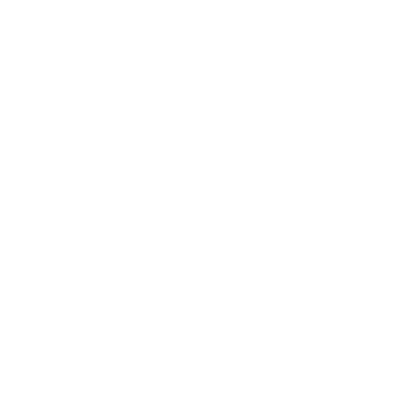
Maximize Rotary Furnace Performance: Design Advancements for Efficient Material Processing
Discover the intricacies of rotary furnaces, exploring their design improvements and applications in advanced materials processing. Learn how these furnaces optimize throughput, energy efficiency, and product quality.