Rotary tube furnaces are highly versatile tools that can be used for a wide range of physicochemical processing applications in the laboratory.
Rotary tube furnaces are useful for a wide range of applications, including thermal processing, material synthesis, and sample preparation. Some models are designed specifically for use in the laboratory, and they offer a number of features that make them well-suited for these types of applications.
One of the main advantages of rotary tube furnaces is that they allow materials to be heated and mixed simultaneously in a controlled atmosphere. This can be useful for a variety of physicochemical processing applications, as it allows for precise control over the temperature, gas composition, and other processing conditions.
Rotary tube furnaces can also be equipped with a range of additional features, such as feeders and inert gas packages, which can help to further optimize the processing conditions. The adjustable rotation speed, tilt, and heating zones of the KinTek model can also be used to fine-tune the performance of the furnace for specific applications.
Table of Contents
Applications of Rotary tube furnaces
Rotary furnaces like the KinTek range are often used for a wide range of applications in research and development, including those in the fields of material science and geology. The ability to heat and mix materials in a controlled atmosphere makes rotary furnaces particularly well-suited for these types of applications.
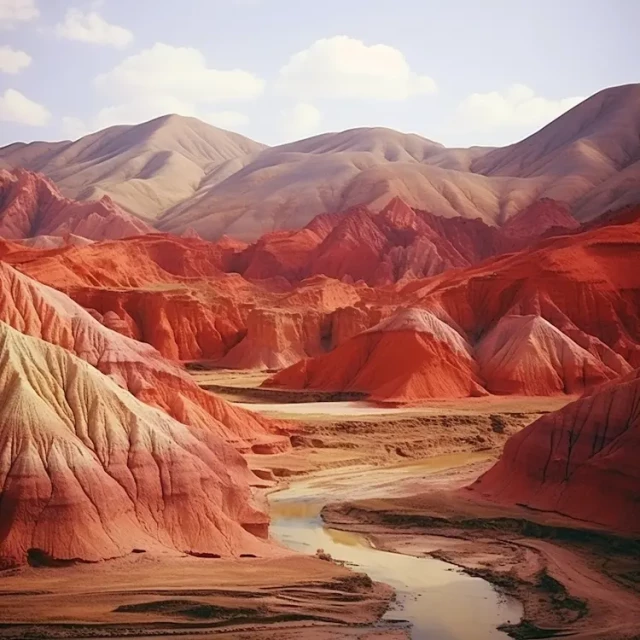
The gaseous reduction of ores and the synthesis of catalysts and pigments, are all examples of the types of physicochemical processing that can be carried out in a rotary furnace. The ability to control the temperature, gas composition, and other processing conditions allows researchers to study the effects of these variables on the materials being processed.
Rotary furnaces can also be used for calcination of oil shale, which is the process of heating shale to a high temperature to release hydrocarbons and other organic materials. This can be an important step in the production of various products, such as fuels, chemicals, and building materials.
Finally, the ability to dope ceramics with rare earth metals using a rotary furnace is another example of the versatility of these types of furnaces. By introducing small amounts of rare earth elements into ceramics, researchers can modify their physical and chemical properties, making them useful for a wide range of applications.
Temperature uniformity is an important consideration when using rotary furnace, as it can have a significant impact on the quality and consistency of the materials being processed. In general, rotary furnaces are known for their ability to provide excellent temperature uniformity, thanks in part to the high-quality heating elements that are used.
MATERIALS CAN BE PROCESSED
Rotary tube furnaces are designed to process granular or particulate materials that are capable of flowing at high temperatures. These types of materials are typically suitable for use in a rotary tube furnace because they can be easily moved through the furnace's work tube by the rotation of the furnace.
Examples of materials that can be processed in a rotary tube furnace include:
- Metals and alloys
- Ceramics
- Glass
- Carbon-based materials
- Oxides
- Sulfides
- Nitrides
- Carbides
Rotary tube furnaces can be used to process materials in either air or inert atmospheres, depending on the specific requirements of the application. Inert atmospheres can be used to prevent oxidation or other types of chemical reactions from occurring during the heat treatment process.
Materials that become sticky at high temperatures are generally not suitable for processing in a rotary tube furnace. This is because the sticky nature of these materials can make it difficult for them to flow through the work tube, which can interfere with the operation of the furnace.
Amount of material that can be processed
The amount of material that can be processed in a rotary tube furnace depends on the specific model and design of the furnace. In general, rotary tube furnaces can be classified as either batch processing furnaces or continuous processing furnaces.
Batch processing furnaces are designed to process a specific quantity of material in a single run, after which the furnace must be cooled and reloaded with additional material. The capacity of a batch processing rotary tube furnace is typically in the range of 620 to 2320 ml, although this can vary depending on the specific model.
Continuous processing furnaces, on the other hand, are designed to process material continuously, without the need for stopping and reloading the furnace. The capacity of a continuous processing rotary tube furnace is generally limited by the size of the feed or collection hopper, which can range from a few liters up to several hundred liters or more.
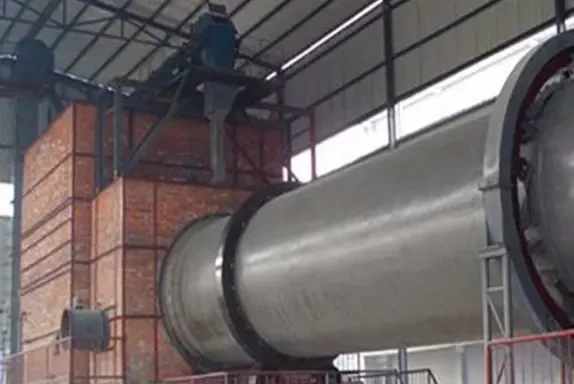
Advantages of rotary tube furnace
Rotary tube furnaces offer a number of advantages over other types of furnaces, making them a popular choice for a wide range of applications. Some of the key advantages of a rotary tube furnace include:
- Continuous movement of the sample: The continuous movement of the sample through the work tube of a rotary tube furnace ensures that the entire surface area is exposed to the atmosphere during processing. This can improve gas diffusion and reduce gas consumption, as well as increase the efficiency of the heat treatment process.
- Improved product homogeneity: The continuous passage of the material through a hot furnace that is maintaining a consistent temperature profile can help to improve product homogeneity. This is particularly important for applications where consistent material properties are critical, such as in the production of high-quality ceramics or other advanced materials.
- Versatility: Rotary tube furnaces are highly versatile tools that can be used for a wide range of applications, including thermal processing, material synthesis, and sample preparation. This versatility makes them an attractive option for researchers and manufacturers working in a variety of fields.
- Ease of use: Rotary tube furnaces are generally easy to operate, with simple controls and user-friendly interfaces. This can be especially useful for researchers and technicians who are new to using furnaces, or for those who need to switch between different processing conditions frequently.
The time taken for material to pass through
The time it takes for material to pass through a rotary tube furnace can vary widely, depending on a number of factors, including the specific model of the furnace, the properties of the material being processed, and the desired processing conditions.
In a continuous processing rotary tube furnace like the model of KinTek , the flow rate of the material can be controlled by adjusting the rotation speed of the work tube and the angle of work tube inclination. These parameters can be adjusted to achieve the desired processing time for a given application.
In general, continuous processing rotary tube furnaces are known for their fast processing times, as there is no need to wait for the furnace to heat up and cool down between runs, as is the case with batch processing furnaces. This can be especially useful for applications where fast turnaround times are critical, such as in research and development or in high-volume manufacturing environments.
The atmospheres within the work tube
Rotary tube furnaces are designed to operate in a variety of different atmospheres, depending on the specific requirements of the application. Some of the atmospheres that are possible within the work tube or vessel of a rotary tube furnace include:
- Air: Air is the most common atmosphere used in rotary tube furnaces, and it is generally suitable for a wide range of applications.
- Inert gases: Inert gases, such as nitrogen or argon, can be used in a rotary tube furnace to prevent oxidation or other types of chemical reactions from occurring during the heat treatment process. This is particularly useful for processing materials that are sensitive to oxygen or other reactive gases.
- Reactive gases: Reactive gases, such as hydrogen, can be used in a rotary tube furnace to facilitate specific chemical reactions or to modify the properties of the materials being processed. However, it is important to use appropriate safety equipment when working with reactive gases, as they can be highly flammable or explosive.
- Steam: Steam injection is also possible in a rotary tube furnace, and it can be used to control the humidity or other processing conditions within the furnace. Steam injection is often used in applications where moisture is an important factor, such as in the processing of ceramics or other hygroscopic materials.
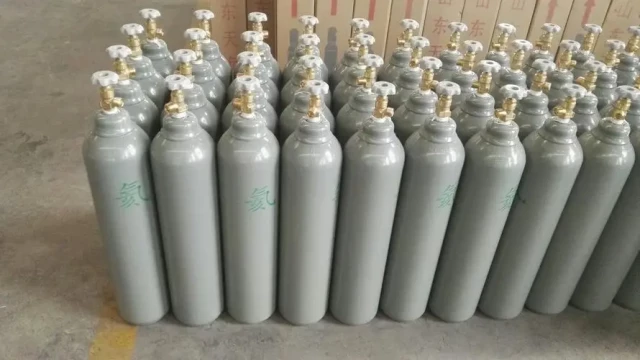
Custom designs
Custom-designed rotary tube furnaces can be an attractive option for researchers and manufacturers who have specific processing requirements that cannot be met by standard off-the-shelf models.
There are a number of factors that can be customized in a rotary tube furnace, including the size and shape of the work tube, the heating elements and controls, and the material of construction. Custom-designed rotary tube furnaces can be built to meet the specific needs of a given application, whether it be for use in the laboratory, pilot plant, or on an industrial scale.
Working with KinTek that has experience in engineering custom-made rotary tube furnaces can be especially beneficial, as they will have the expertise and resources needed to design and build a furnace that meets the unique requirements of your application. It is important to carefully communicate your specific processing needs and requirements to the manufacturer to ensure that they can design and build a rotary furnace that meets your needs.
CONTACT US FOR A FREE CONSULTATION
KINTEK LAB SOLUTION's products and services have been recognized by customers around the world. Our staff will be happy to assist with any inquiry you might have. Contact us for a free consultation and talk to a product specialist to find the most suitable solution for your application needs!