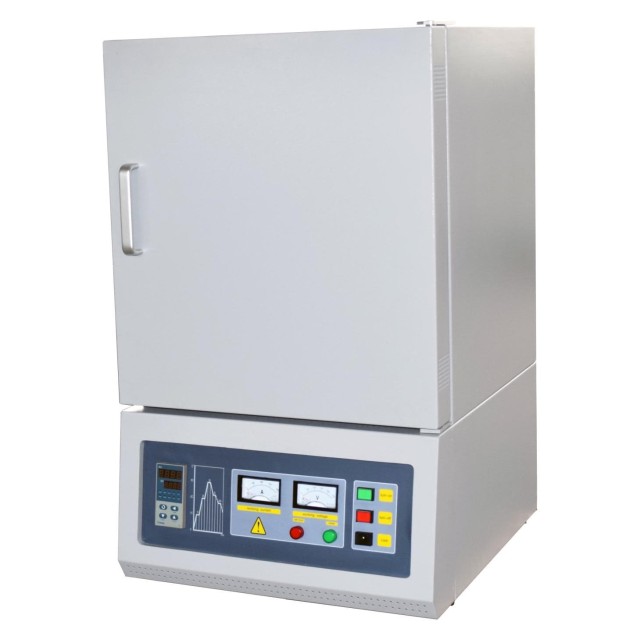
Muffle Furnace
1700℃ Muffle Oven Furnace for Laboratory
Item Number : KT-17M
Price varies based on specs and customizations
- Max. temperature
- 1700 ℃
- Constant work temperature
- 1600 ℃
- Heating rate
- 0-20 ℃/min
- Effective volume
- 1-512 L
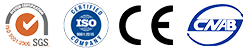
Shipping:
Contact us to get shipping details Enjoy On-time Dispatch Guarantee.
Why Choose Us
Reliable PartnerEasy ordering process, quality products, and dedicated support for your business success.
Introduction
KT-17M muffle furnace insulation materials is Japan 1800 Al2O3 polycrystalline fibe broads, heating element is Silicon Molybdenum(MoSi2), which working temperature is up to 1700C, PID intelligent temperature microprocessor, high temperature control accuracy and excellent temperature uniformity.
KT-17M Pro muffle furnace equipped with one versatile 7 inches TFT smart touch screen controller, operator can set and save different heating programs in the smart controller, reduce the difficulty of traditional digital controller greatly and assist the operator to analysis the furnace historical data.
Applications
Muffle furnaces are versatile high-temperature heating devices used in various industrial and laboratory settings. They are designed to provide precise temperature control and isolation from combustion contaminants, making them ideal for a range of applications including ashing samples, heat treatment, and materials research. Here are the main application areas of muffle furnaces:
- Ashing Samples: Muffle furnaces are commonly used in laboratories for the ashing of organic and inorganic materials, which is crucial for determining the residue content in samples.
- Heat Treatment: They are essential for processes like annealing, hardening, and tempering of metals and alloys, ensuring the desired material properties are achieved.
- Materials Research: Used in research and development to study the behavior of materials at high temperatures, including the synthesis of new materials.
- Melting Glass: Ideal for melting and fusing glass for various applications, including the creation of technical ceramics and enamel coatings.
- Soldering and Brazing: Muffle furnaces provide the necessary high temperatures for soldering and brazing operations, ensuring strong and reliable joints.
- Technical Ceramics: Used in the production and testing of technical ceramics, which require precise temperature control for optimal performance.
- Enamel Coatings: Essential for creating durable and aesthetically pleasing enamel coatings on various materials.
Detail & Parts
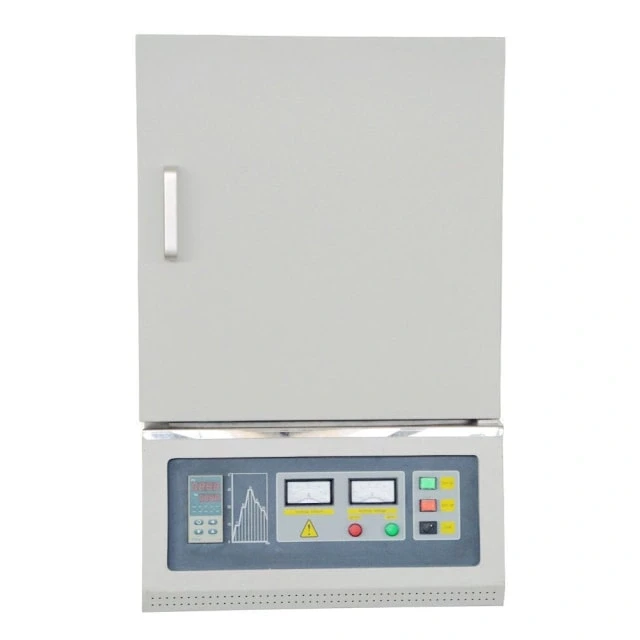
Mainly used in college laboratories, industrial and mining enterprise laboratories, for chemical analysis, physical determination and metal, ceramics, etc.It can be used for debinding, pre-firing and firing of electronic components, powder metallurgy, magnetic materials and other products, and can also be used for heat treatment processes of other materials.
CaptionBottom-opening high-temperature energy-saving muffle furnace adopts bottom-opening design, which is more convenient to take and unload materials: the furnace adopts a new type of ceramic fiber furnace, which has a good heat preservation effect and keeps the surface of the shell not hot after 1 hour. It can reduce the sintering temperature by a large margin up to 500°C; greatly reduce energy consumption and save energy by up to 70-90%;Short sintering time, up to 50% or more: increase the structure density, refine the grain, improve the material performance, the equipment has the characteristics of uniform temperature, stable control, fast heating speed, energy saving, high service temperature and long service life.
Principle
Muffle furnaces operate on indirect heating, using a separate muffle chamber to isolate materials from direct heat sources. Heating elements outside the chamber heat a ceramic muffle, which in turn heats the contents inside, ensuring precise temperature control and preventing contamination.
Advantages
- Compact design,small footprint,versatile functions
- Double furnace shell design, forced air flow between the inner and outer shell, so as to keep a low temperature of the furnace surface
- PID programmable temperature control,excellent control accuracy and stable heating performance, support remote control and centralized control
- Ceramic polycrystalline fiber insulation liner, less heat loss and superior energy saving efficiency
- Professional heating elements configuration to optimize heat radiation properties, and ensure a longest service life
- Safety interlock system power shuts off when furnace door open, over temperature and sensor broken
- KT-17M Pro model applies one 7 inches TFT touch screen controller, more friendly program setting and history data analysis,different program recipes can be saved and select
Features
The Muffle Furnace is a highly specialized device designed to create an optimal environment for heating materials to extremely high temperatures, primarily used in industries such as metalworking and manufacturing. This furnace is engineered to maintain a controlled, isolated environment, ensuring that the materials being heated are protected from external contaminants and chemicals. Here are the key features that not only enhance its functionality but also provide significant benefits to its users:
- High-Temperature Capabilities: The Muffle Furnace can reach and maintain extremely high temperatures, which is crucial for processes like annealing, sintering, and other high-heat applications. This ensures that materials are processed effectively and efficiently.
- Effective Insulation: Equipped with advanced insulation, the furnace prevents heat from escaping, thereby conserving energy and maintaining a stable internal temperature. This insulation also acts as a barrier, keeping the external environment safe from the high temperatures inside.
- Contamination-Free Environment: By isolating the heating process from external elements, the Muffle Furnace ensures that the materials being heated are not exposed to any contaminants. This is vital for maintaining the purity and integrity of the materials, especially in sensitive applications.
- Safety and Efficiency: The design of the Muffle Furnace prioritizes safety, reducing the risk of work injuries by keeping high temperatures contained. Additionally, the efficient use of energy contributes to cost savings and environmental sustainability.
Safety Advantage
- Kindle Tech tube furnace owns over current protection, over temperature alarming function, furnace will turn off the power automatically
- Furnace build in thermal couple detecting function, furnace will stop heating and alarm will be on once broken or failure detected
- KT-12M Pro support power failure restarting function,furnace will resume the furnace heating program when power is incoming after failure
Technical specifications
Furnace model | KT-17M | ||
---|---|---|---|
Max. temperature | 1700℃ | ||
Constant work temperature | 1600℃ | ||
Chamber material | Japan alumina fiber | ||
Heating element | Molybdenum Disilicide | ||
Heating rate | 0-20℃/min | ||
Temperature sensor | B type thermal couple | ||
Temperature controller | Digital PID controller/Touch screen PID controller | ||
Temperature control accuracy | ±1℃ | ||
Temperature uniformity | ±5℃ | ||
Electric power supply | AC110-220V,50/60HZ | ||
Standard Chamber Sizes Stocks | |||
Chamber size (mm) | Effective volume (L) | Chamber size (mm) | Effective volume (L) |
100x100x100 | 1 | 300x300x400 | 36 |
120x120x130 | 2 | 400x400x400 | 64 |
150x150x200 | 4.5 | 500x500x500 | 125 |
200x200x200 | 8 | 600x600x600 | 216 |
200x200x300 | 12 | 800x800x800 | 512 |
Customer design sizes and volume is accepted |
Standard Package
No. | Description | Quantity |
---|---|---|
1 | Furnace | 1 |
2 | Thermal block | 1 |
3 | Crucible tong | 1 |
4 | Heat resistant glove | 1 |
5 | Operation manual | 1 |
Optional Setup
- Independent furnace temperature monitoring and recording
- RS 485 communication port for PC remote control and data exporting
- Insert gases port,exhaust output port,observation window port
- Touch screen temperature controller with versatile operator friendly functions
Warnings
Operator safety is the top important issue! Please operate the equipment with cautions. Working with inflammable& explosive or toxic gases is very dangerous, operators must take all necessary precautions before starting the equipment. Working with positive pressure inside the reactors or chambers is dangerous, operator must fellow the safety procedures strictly. Extra caution must also be taken when operating with air-reactive materials, especially under vacuum. A leak can draw air into the apparatus and cause a violent reaction to occur.
Designed for You
KinTek provide deep custom made service and equipment to worldwide customers, our specialized teamwork and rich experienced engineers are capable to undertake the custom tailoring hardware and software equipment requirements, and help our customer to build up the exclusive and personalized equipment and solution!
Would you please drop your ideas to us, our engineers are ready for you now!
FAQ
What Are Muffle Furnace Used For?
What Are The Types Of Muffle Furnace?
What Is Muffle Furnace In Chemistry?
What Is The Use Of Muffle Furnace For Ash?
What Is The Temperature Of Muffle Furnace?
4.9
out of
5
This muffle furnace is an excellent choice for high-temperature applications. It heats up quickly and maintains a consistent temperature.
4.8
out of
5
I'm very satisfied with the performance of this muffle furnace. It's easy to use and delivers accurate and consistent results.
4.7
out of
5
This muffle furnace is a great value for the price. It's well-made and has a long lifespan.
5.0
out of
5
I highly recommend this muffle furnace. It's a top-of-the-line product that meets all my needs.
4.6
out of
5
This muffle furnace has exceeded my expectations. It's a reliable and efficient piece of equipment.
4.9
out of
5
I'm very happy with this muffle furnace. It's easy to operate and provides precise temperature control.
4.8
out of
5
This muffle furnace is a great addition to my laboratory. It's helped me improve the quality of my work.
5.0
out of
5
I'm very impressed with this muffle furnace. It's a powerful and versatile tool that has made my work much easier.
4.7
out of
5
This muffle furnace has been a lifesaver in my laboratory. It's helped me save time and improve the accuracy of my experiments.
4.9
out of
5
I highly recommend this muffle furnace. It's a great value for the price and has made a big difference in my work.
5.0
out of
5
This muffle furnace is a must-have for any laboratory. It's easy to use and delivers consistent results.
4.8
out of
5
I'm very satisfied with this muffle furnace. It's a great investment that has paid for itself in no time.
4.7
out of
5
This muffle furnace is a great addition to my laboratory. It's helped me improve the efficiency of my work.
Products
1700℃ Muffle Oven Furnace for Laboratory
REQUEST A QUOTE
Our professional team will reply to you within one business day. Please feel free to contact us!
Related Products
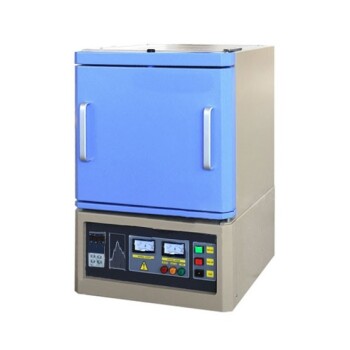
1800℃ Muffle Oven Furnace for Laboratory
KT-18 muffle furnace with Japan Al2O3 polycrystalline fibe and Silicon Molybdenum heating element, up to 1900℃, PID temperature control and 7" smart touch screen. Compact design, low heat loss, and high energy efficiency. Safety interlock system and versatile functions.
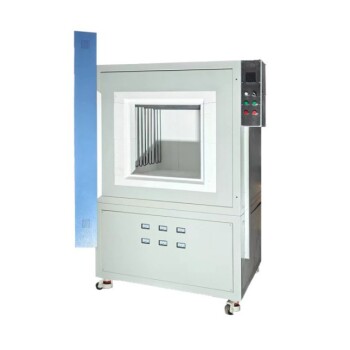
High Temperature Muffle Oven Furnace for Laboratory Debinding and Pre Sintering
KT-MD High temperature debinding and pre-sintering furnace for ceramic materials with various molding processes. Ideal for electronic components such as MLCC and NFC.
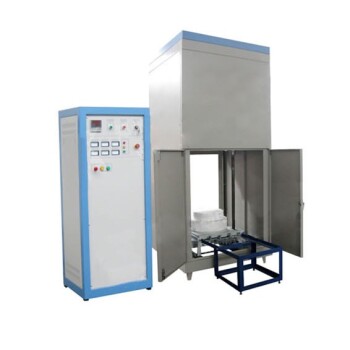
Laboratory Muffle Oven Furnace Bottom Lifting Muffle Furnace
Efficiently produce batches with excellent temperature uniformity using our Bottom Lifting Furnace. Features two electric lifting stages and advanced temperature control up to 1600℃.
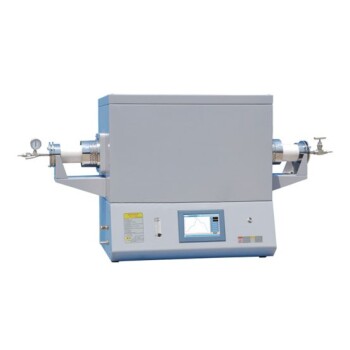
1700℃ Laboratory Quartz Tube Furnace with Alumina Tube Tubular Furnace
Looking for a high-temperature tube furnace? Check out our 1700℃ Tube Furnace with Alumina Tube. Perfect for research and industrial applications up to 1700C.
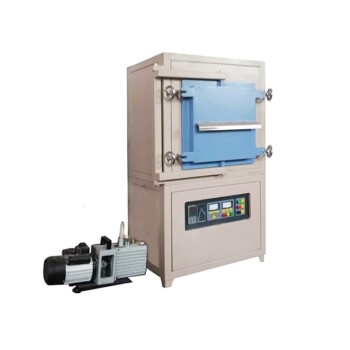
1700℃ Controlled Atmosphere Furnace Nitrogen Inert Atmosphere Furnace
KT-17A Controlled atmosphere furnace: 1700℃ heating, vacuum sealing technology, PID temperature control, and versatile TFT smart touch screen controller for laboratory and industrial use.
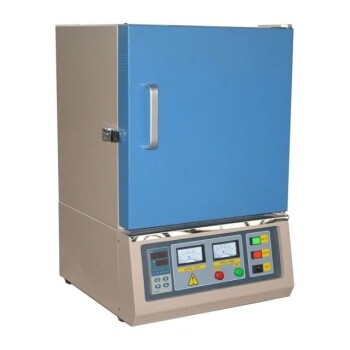
1400℃ Muffle Oven Furnace for Laboratory
Get precise high-temperature control up to 1500℃ with KT-14M Muffle furnace. Equipped with a smart touch screen controller and advanced insulation materials.
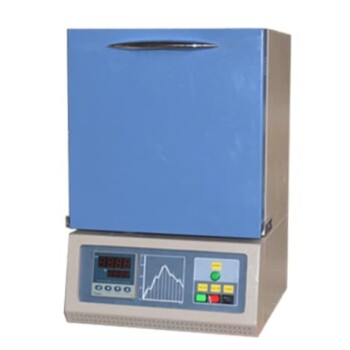
1200℃ Muffle Furnace Oven for Laboratory
Upgrade your lab with our 1200℃ Muffle Furnace. Achieve fast, precise heating with Japan alumina fibers and Molybdenum coils. Features TFT touch screen controller for easy programming and data analysis. Order now!
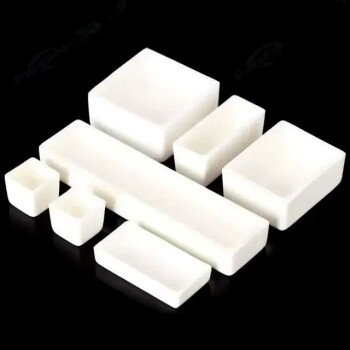
Engineering Advanced Fine Alumina Al2O3 Ceramic Crucible for Laboratory Muffle Furnace
Alumina ceramic crucibles are used in some materials and metal melting tools, and flat-bottomed crucibles are suitable for melting and processing larger batches of materials with better stability and uniformity.
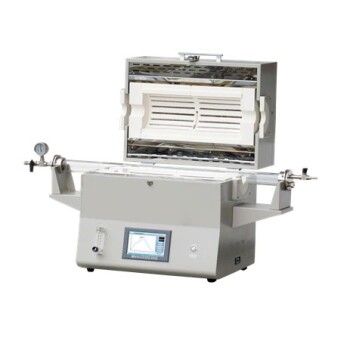
1400℃ Laboratory Quartz Tube Furnace with Alumina Tube Tubular Furnace
Looking for a tube furnace for high-temperature applications? Our 1400℃ Tube Furnace with Alumina Tube is perfect for research and industrial use.
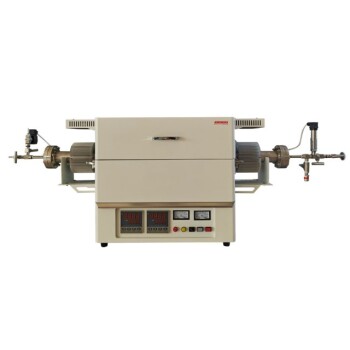
High Pressure Laboratory Vacuum Tube Furnace Quartz Tubular Furnace
KT-PTF High Pressure Tube Furnace: Compact split tube furnace with strong positive pressure resistance. Working temp up to 1100°C and pressure up to 15Mpa. Also works under controller atmosphere or high vacuum.
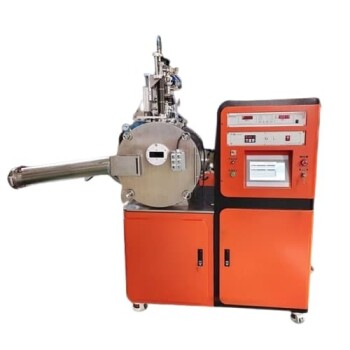
Vacuum Induction Melting Spinning System Arc Melting Furnace
Develop metastable materials with ease using our Vacuum Melt Spinning System. Ideal for research and experimental work with amorphous and microcrystalline materials. Order now for effective results.
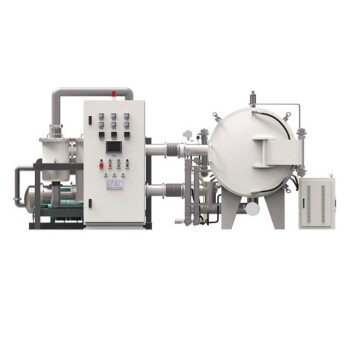
Horizontal High Temperature Graphite Vacuum Graphitization Furnace
Horizontal Graphitization Furnace: This type of furnace is designed with the heating elements placed horizontally, allowing for uniform heating of the sample. It's well-suited for graphitizing large or bulky samples that require precise temperature control and uniformity.
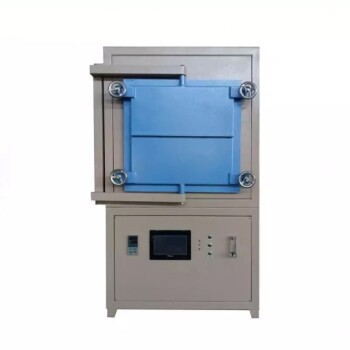
1400℃ Controlled Atmosphere Furnace with Nitrogen and Inert Atmosphere
Achieve precise heat treatment with KT-14A controlled atmosphere furnace. Vacuum sealed with a smart controller, it's ideal for lab and industrial use up to 1400℃.
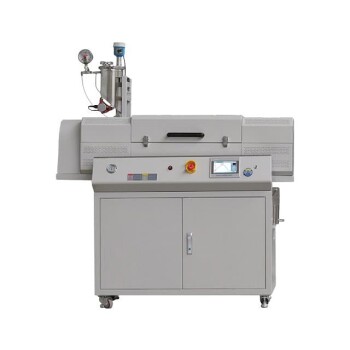
Laboratory Vacuum Tilt Rotary Tube Furnace Rotating Tube Furnace
Discover the versatility of Laboratory Rotary Furnace: Ideal for calcination, drying, sintering, and high-temperature reactions. Adjustable rotating and tilting functions for optimal heating. Suitable for vacuum and controlled atmosphere environments. Learn more now!
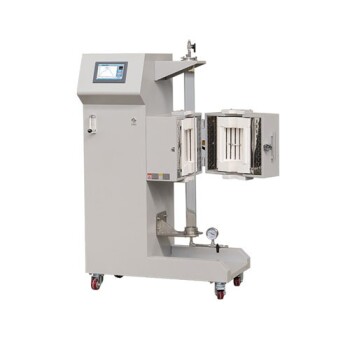
Vertical Laboratory Quartz Tube Furnace Tubular Furnace
Elevate your experiments with our Vertical Tube Furnace. Versatile design allows for operation under various environments and heat treatment applications. Order now for precise results!
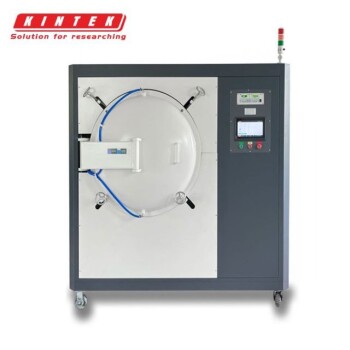
Vacuum Heat Treat Furnace with Ceramic Fiber Liner
Vacuum furnace with polycrystalline ceramic fiber insulation liner for excellent heat insulation and uniform temperature field. Choose from 1200℃ or 1700℃ max. working temperature with high vacuum performance and precise temperature control.
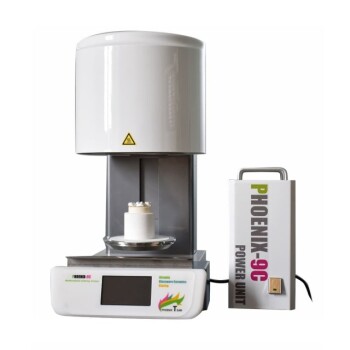
Dental Porcelain Zirconia Sintering Ceramic Furnace Chairside with Transformer
Experience top-notch sintering with Chairside Sintering Furnace with Transformer. Easy to operate, noise-free pallet, and automatic temperature calibration. Order now!
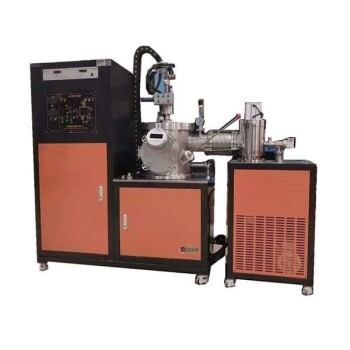
Vacuum Arc Induction Melting Furnace
Discover the power of Vacuum Arc Furnace for melting active & refractory metals. High-speed, remarkable degassing effect, and free of contamination. Learn more now!
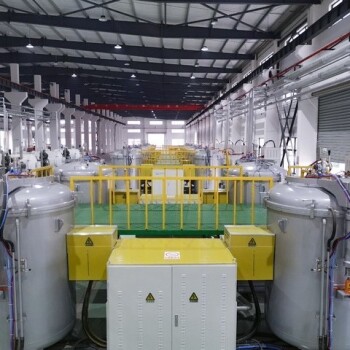
Vertical High Temperature Graphite Vacuum Graphitization Furnace
Vertical high temperature graphitization furnace for carbonization and graphitization of carbon materials up to 3100℃.Suitable for shaped graphitization of carbon fiber filaments and other materials sintered in a carbon environment.Applications in metallurgy, electronics, and aerospace for producing high-quality graphite products like electrodes and crucibles.
Related Articles
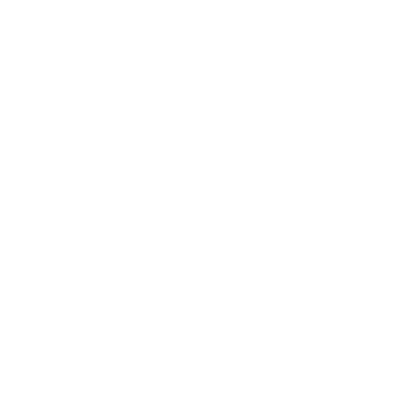
Comprehensive Guide to Muffle Furnaces: Types, Uses, and Maintenance
Explore the world of muffle furnaces with our detailed guide. Learn about their types, applications in various industries, and essential maintenance tips to ensure optimal performance.
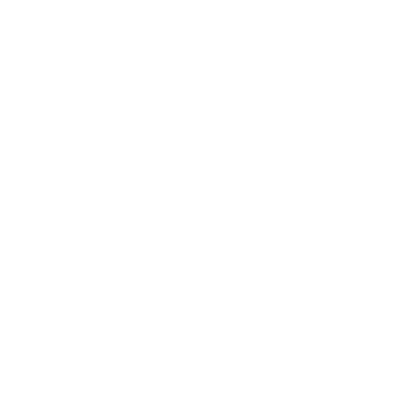
Comprehensive Guide to Muffle Furnaces: Applications, Types, and Maintenance
Explore the world of muffle furnaces with our detailed guide. Learn about their applications in various industries, types available, and essential maintenance tips to ensure optimal performance.
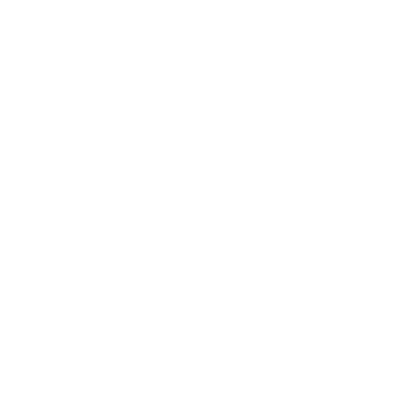
Advanced Laboratory Furnaces: Box, Muffle, and Tube Options for High-Temperature Applications
we will explore the various types of lab furnaces and how they function in different high-temperature applications.
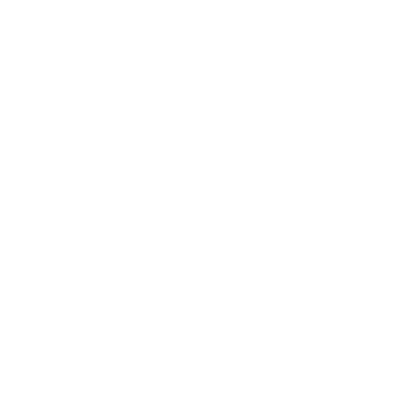
How to Choose Right Muffle Furnace for Your Laboratory?
A few other important considerations for your muffle furnace include the desired maximum temperature, process cycle time, and loading or unloading method. In order to choose the best muffle furnace for your needs, it is important to first consider the design specifications required for your desired production or application. This includes factors such as the crucible size, chamber size, and input voltage. Once you have a good understanding of the basics, you can then move on to other important considerations such as the maximum temperature, process cycle time, and loading or unloading method. By taking all of these factors into account, you can be sure to choose the best muffle furnace for your particular needs.
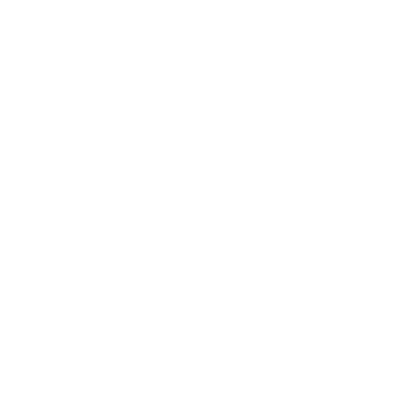
Muffle Furnace: Unraveling the Secrets of Uniform Heating and Controlled Atmosphere
Discover the intricacies of a muffle furnace, an indispensable tool for material processing and analysis. Learn about its working principle, applications, types, features, and benefits, empowering you to make informed decisions for your laboratory or industrial needs.
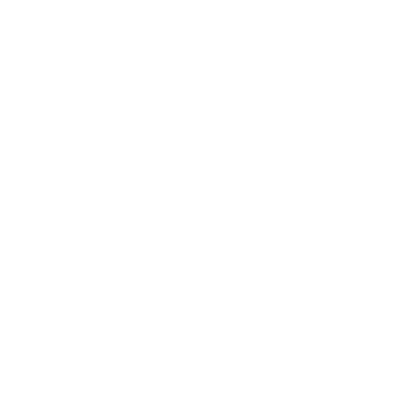
Exploring the Using a Chamber Furnace for Industrial and Laboratory Applications
A laboratory chamber furnace is a type of heating equipment that is specifically designed for use in a laboratory setting. It is typically used for applications that require precise temperature control and uniformity, such as ashing or heat treatment of materials.
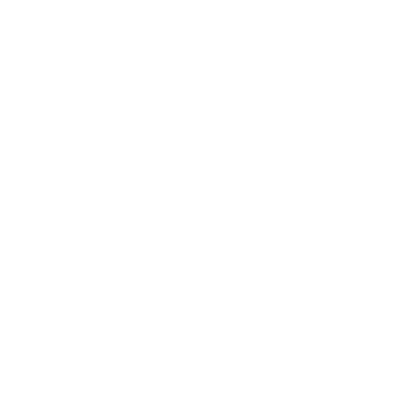
Infrared Heating Quantitative Flat Plate Mold: Design, Applications, and Benefits
Explore the advanced design and applications of infrared heating quantitative flat plate molds. Learn about their benefits in achieving uniform heat distribution and efficient processing.
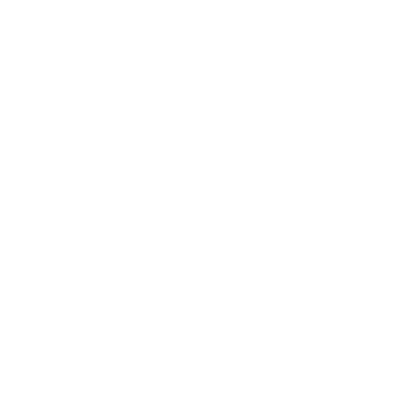
Electric Rotary Kiln Pyrolysis Furnace: Design, Operation, and Applications
Explore the comprehensive guide on electric rotary kiln pyrolysis furnaces, including their design, operation, efficiency factors, and diverse applications in industries like waste processing and biofuel production.
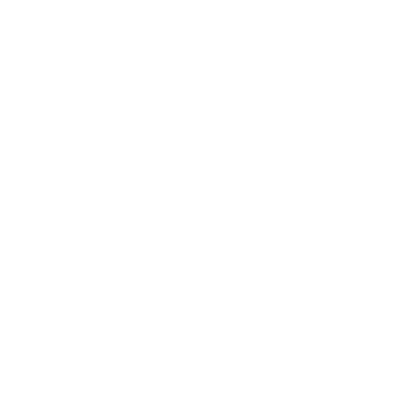
Understanding the Design and Functionality of Industrial Furnaces
Industrial furnaces are heating devices used in various industrial processes, including soldering, heat treatment of steels and alloys, and ceramics sintering.
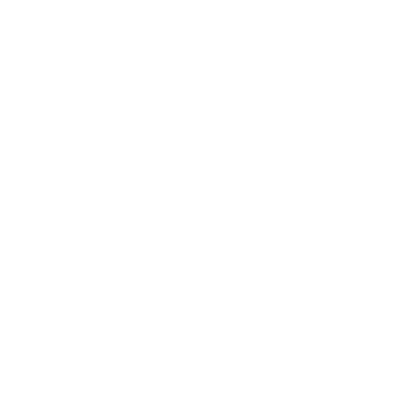
Exploring the Key Performance Indicators of an Atmosphere Furnace
Atmosphere furnaces are specialized pieces of equipment used in a variety of industries for applications such as heat treatment, ceramics, and metallurgy.
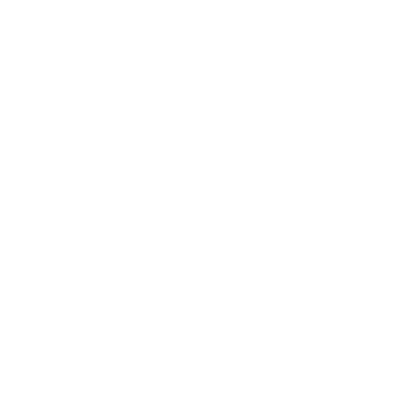
Advancements in Muffle Furnace Technology and Applications
Explores the principles, types, research, and future prospects of muffle furnaces in various industries.
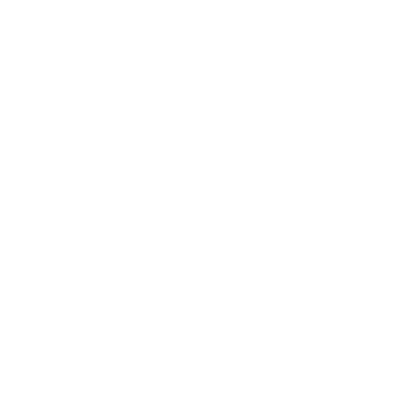
Dos and don'ts during the installation of molybdenum disilicide (MoSi2) heating element
Precautions when installing MoSi2 heating elements