Introduction to Pyrolysis and Electric Rotary Kilns
Pyrolysis, a transformative process that utilizes heat to decompose organic materials in the absence of oxygen, plays a crucial role in various industries. Electric rotary kiln pyrolysis furnaces, with their unique design and heating capabilities, have emerged as a preferred choice for this process. These furnaces offer precise temperature control, uniform heating distribution, and high energy efficiency, making them an indispensable tool in the pyrolysis industry. This comprehensive guide delves into the principles of pyrolysis, the operating mechanisms of electric rotary kilns, and their significant applications in diverse fields.
Applications of Electric Rotary Kiln Pyrolysis Furnaces
Electric rotary kiln pyrolysis furnaces offer a wide range of applications in various industries, including high-temperature oxidation, reduction reactions, mineral product production, and plastics-to-fuel technology.
High-Temperature Oxidation and Reduction Reactions:
Electric rotary kilns are commonly used for high-temperature oxidation and reduction reactions. In the oxidation process, materials are heated in the presence of oxygen to remove impurities and modify their chemical properties. This process is often employed in the production of roofing granules, adsorbents, fillers, and desiccants.
In reduction reactions, materials are heated in the absence of oxygen to remove oxygen atoms and change their chemical composition. This process is frequently used in the production of magnetic iron oxide, cobalt oxide, manganese oxide, zinc oxide, molybdenum oxide, vanadium oxide, and tungsten oxide.
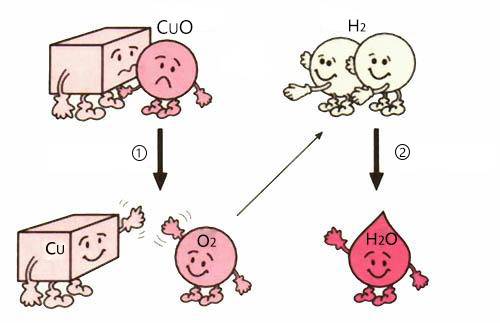
Mineral Product Production:
Rotary kilns play a significant role in the production of advanced mineral products, such as roofing granules, adsorbents, fillers, and desiccants. They are used to remove impurities, modify physical and chemical properties, bond coatings and colors to base materials, and more.
Plastics-to-Fuel (PTF) Technology:
Electric rotary kilns are becoming increasingly important in PTF technology, a process that converts plastic waste into fuel or building blocks of petroleum products. Rotary kilns are used to carry out pyrolysis, which is a thermal process that breaks down plastic materials into smaller molecules. This process allows a wider range of plastic waste types to be recycled, providing a much-needed alternative for plastics that cannot be processed through traditional mechanical approaches.
Advantages of Electric Rotary Kiln Pyrolysis Furnaces:
Electric rotary kiln pyrolysis furnaces offer several advantages in the production process:
- High thermal efficiency: Electric kilns have no emissions, ash, or slag, resulting in higher thermal efficiency.
- Precise temperature control: Electric kilns allow for accurate temperature control, making them suitable for narrow pre-firing temperature processes.
- Reduced fuel storage and transportation: Electric kilns eliminate the need for fuel storage and transportation, simplifying fuel management and reducing safety concerns.
- Environmental benefits: Electric kilns do not produce SO2 gas, which reduces corrosion of the kiln body and environmental pollution.
In summary, electric rotary kiln pyrolysis furnaces are versatile and efficient equipment widely used in high-temperature oxidation and reduction reactions, mineral product production, and plastics-to-fuel technology. Their high thermal efficiency, precise temperature control, and reduced environmental impact make them a preferred choice for various industrial applications.
Heating Methods for Pyrolysis Furnaces
Pyrolysis furnaces can be heated using a variety of methods, including electric resistance heating, gas-fired heating, and induction heating. The choice of heating method depends on the type of material being pyrolyzed and the desired operating conditions.
Electric Resistance Heating
Electric resistance heating is a method of heating in which an electric current is passed through a resistive element, causing it to heat up. This method of heating is often used in pyrolysis furnaces because it provides even, all-around heating to the material being pyrolyzed. Electric resistance heating is also relatively easy to control, making it a good choice for applications where precise temperature control is required.
Gas-Fired Heating
Gas-fired heating is a method of heating in which a gas burner is used to heat the material being pyrolyzed. This method of heating is often used in pyrolysis furnaces because it can provide high temperatures quickly and efficiently. Gas-fired heating is also relatively inexpensive to operate, making it a good choice for applications where cost is a concern.
Induction Heating
Induction heating is a method of heating in which an alternating current is passed through a coil, creating a magnetic field. This magnetic field induces eddy currents in the material being pyrolyzed, causing it to heat up. Induction heating is a very efficient method of heating, and it can be used to heat materials very quickly. However, induction heating is also more expensive than other heating methods, making it a less common choice for pyrolysis furnaces.
The choice of heating method for a pyrolysis furnace depends on a number of factors, including the type of material being pyrolyzed, the desired operating conditions, and the cost of the heating method. Electric resistance heating is a good choice for applications where even, all-around heating is required and precise temperature control is important. Gas-fired heating is a good choice for applications where high temperatures are required quickly and efficiently and cost is a concern. Induction heating is a good choice for applications where very high temperatures are required quickly and efficiently, but cost is not a concern.
Factors Affecting Pyrolysis Furnace Efficiency
Temperature
Temperature is one of the most important factors affecting pyrolysis furnace efficiency. The optimal temperature for pyrolysis depends on the specific feedstock and the desired end products. In general, higher temperatures favor the production of non-condensable gases (syngas, synthetic gas), while lower temperatures favor the production of high-quality solid products (charcoal, bio-coal, torrefied fuels).
Residence Time
The residence time of the material in the pyrolysis furnace is another important factor affecting efficiency. Longer residence times allow for more complete conversion of the feedstock, resulting in higher yields of desired products. However, excessively long residence times can also lead to the formation of unwanted byproducts.
Pressure
The pressure inside the pyrolysis furnace can also affect efficiency. Higher pressure can promote the formation of liquid products, while lower pressure favors the production of solid products.
Other Factors
In addition to the main factors discussed above, several other factors can also affect pyrolysis furnace efficiency, including:
-
Particle size: Smaller particle sizes promote faster thermal decomposition, resulting in greater quantities of pyrolysis oil and gas.
-
Feedstock moisture content: Higher moisture content can reduce pyrolysis efficiency and increase the production of unwanted byproducts.
-
Furnace design: The design of the pyrolysis furnace can also affect efficiency. Factors such as the size and shape of the furnace, the type of heating elements used, and the presence of baffles or other internal components can all influence performance.
-
Operating conditions: The operating conditions of the pyrolysis furnace, such as the temperature, pressure, and residence time, must be carefully controlled to ensure optimal performance.
By carefully considering all of these factors, it is possible to optimize the efficiency of a pyrolysis furnace and produce the desired end products.
Advantages of Electric Rotary Kiln Pyrolysis Furnaces
Electric rotary kiln pyrolysis furnaces offer several advantages over traditional pyrolysis furnaces, including:
High Energy Efficiency: Electric rotary kilns utilize electricity as their heat source, which is a more efficient form of energy than fossil fuels. This results in lower operating costs and reduced environmental impact.
Low Heat Losses: The rotating design of electric rotary kilns minimizes heat losses, as the heat is constantly being distributed throughout the kiln. This ensures that the pyrolysis process is carried out efficiently, with minimal energy wastage.
Suitability for Low-Temperature Thermolysis: Electric rotary kilns are well-suited for low-temperature thermolysis, which is a process that involves heating materials at relatively low temperatures to break down organic matter. This makes them ideal for applications such as the pyrolysis of biomass and waste materials.
Reduced Environmental Impact: Electric rotary kilns produce minimal emissions, as they do not rely on fossil fuels for heat generation. This reduces the environmental impact of the pyrolysis process and contributes to cleaner air quality.
Additional Advantages:
- Automated Operation: Electric rotary kilns can be automated to maintain precise temperature control, ensuring optimal pyrolysis conditions.
- Compact Design: Electric rotary kilns are often more compact than traditional pyrolysis furnaces, making them suitable for space-constrained applications.
- Easy Maintenance: The rotating design of electric rotary kilns facilitates easy maintenance and cleaning, minimizing downtime.
- Versatile Applications: Electric rotary kilns can be used for a wide range of pyrolysis applications, including waste treatment, biomass conversion, and materials recycling.
Environmental Benefits of Pyrolysis Furnaces
Pyrolysis furnaces offer a range of environmental benefits, making them a sustainable solution for waste management and renewable energy production.
Reduction of Greenhouse Gas Emissions
Pyrolysis converts organic waste materials into biofuels, which have a lower carbon footprint than fossil fuels. By replacing fossil fuels with biofuels, pyrolysis furnaces help reduce greenhouse gas emissions, mitigating climate change.
Energy Efficiency
Pyrolysis is an energy-efficient process. The energy used to heat the furnace is typically offset by the energy produced in the form of biofuels or other valuable products. This energy can be used to power the furnace itself or other operations, reducing the overall energy consumption.
Flexibility
Pyrolysis furnaces can process a wide range of organic materials, including agricultural waste, wood waste, and municipal solid waste. This flexibility makes pyrolysis a versatile solution for waste management and renewable energy production.
Safe and Responsible Operation of Pyrolysis Furnaces
Pyrolysis furnaces are essential equipment for various industrial processes, but their operation requires strict adherence to safety protocols and proper maintenance practices to ensure optimal performance and minimize risks.
Importance of Proper Operation and Maintenance
Pyrolysis furnaces operate at high temperatures and handle hazardous materials, making their safe operation paramount. Proper operation involves:
- Maintaining precise temperature control
- Ensuring adequate residence time for materials
- Controlling pressure within the furnace
- Regular cleaning and maintenance to prevent malfunctions
By following these guidelines, operators can optimize furnace efficiency, enhance product quality, and prolong equipment lifespan.
Safety Protocols and Regulatory Compliance
To ensure the safety of personnel and the environment, it is crucial to comply with local regulations and obtain necessary permits. Implementing a comprehensive safety management system is essential, including:
- Establishing clear operating procedures
- Providing adequate training for operators
- Conducting regular safety inspections and audits
- Maintaining emergency response plans
Factors Affecting Furnace Efficiency
Several factors influence the efficiency and effectiveness of pyrolysis furnaces:
- Temperature: The temperature of the furnace must be precisely controlled to achieve optimal pyrolysis conditions.
- Residence Time: The time materials spend in the furnace affects the extent of pyrolysis and the yield of desired products.
- Pressure: Maintaining proper pressure inside the furnace is crucial for controlling the pyrolysis process and preventing explosions.
By optimizing these factors, operators can maximize product yield, minimize energy consumption, and enhance furnace performance.
Additional Features and Components
In addition to the main pyrolysis chamber, furnaces may include various features and components:
- Feeding and Discharge Systems: These systems regulate the flow of materials into and out of the furnace.
- Gas Cleaning Systems: These systems remove harmful gases and emissions from the furnace exhaust.
- Safety and Control Systems: These systems monitor and control furnace parameters, such as temperature, pressure, and gas flow.
By incorporating these additional features, furnaces can operate more efficiently, safely, and environmentally responsibly.
Safe Operation Practices
Operating pyrolysis furnaces safely requires a combination of technical expertise and vigilance:
- Visual Monitoring: Operators must continuously monitor operating conditions, such as temperature and pressure.
- Integrated Control Loops: Automated control systems can monitor and adjust furnace parameters, ensuring optimal operation.
- Predictive Intelligence Models: Smart technologies can predict and rectify potential issues, minimizing downtime and enhancing safety.
- Improved Burner Management: Optimized burner systems improve fuel efficiency and reduce emissions.
- Remote Testing: Remote diagnostics and testing allow for proactive identification and resolution of issues.
- Automated Emergency Shutdown: Control loops can be programmed to trigger emergency shutdowns in case of malfunctions.
- Fluid System Maintenance: Regular maintenance of fluid systems prevents corrosion and ensures smooth operation.
Conclusion
Electric rotary kiln pyrolysis furnaces offer a versatile and environmentally friendly solution for waste management and resource recovery. Their high efficiency, low heat losses, and ability to process a wide range of materials make them a valuable asset in various industries.
CONTACT US FOR A FREE CONSULTATION
KINTEK LAB SOLUTION's products and services have been recognized by customers around the world. Our staff will be happy to assist with any inquiry you might have. Contact us for a free consultation and talk to a product specialist to find the most suitable solution for your application needs!