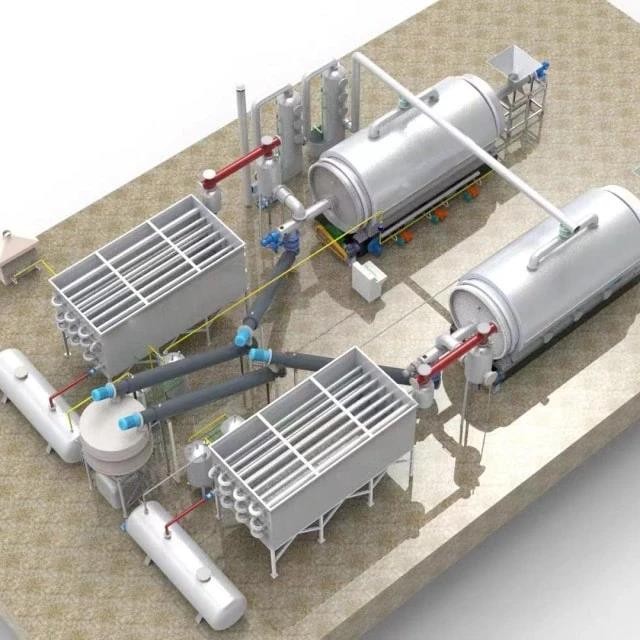
Electric Rotary Kiln
Waste Tire Pyrolysis Plant for Recycling and Energy Recovery
Item Number : KWRE
Price varies based on specs and customizations
- Host volume
- 31.8-46.2 cubic meters
- Daily throughput
- 8-15 ton
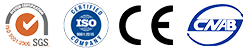
Shipping:
Contact us to get shipping details Enjoy On-time Dispatch Guarantee.
Why Choose Us
Reliable PartnerEasy ordering process, quality products, and dedicated support for your business success.
Introductions
In order to solve waste tires, the waste tire refining equipment produced by our company adopts a new type of pyrolysis technology, which makes tires heated under the condition of complete anoxic or limited oxygen supply, so that high molecular polymers and organic additives are degraded into low molecular or small molecules compounds, thereby recovering tire oil, solid carbon and steel wire. The whole technological process ensures that no three wastes are produced: each equipment is equipped with a dust removal system to purify the flue gas generated during the operation of the equipment to ensure that the smoke and dust emissions meet the standards: the cooling system is used to cool high-temperature oil and gas, in which water can be recycled and no waste water is discharged; waste residue And carbon black, because it has been treated at a high temperature of more than 500 degrees, it has no toxicity, and carbon black can be refined, so it has a wide range of applications.
Waste tires and plastic pyrolysis process
The pyrolysis process does not require fine treatment of impurities such as sediment, water, and iron wire in the raw materials, and can directly load organic waste such as waste tires, rubber, and waste plastics into the pyrolysis processor. The mixture of oil and steam can be distilled, and the oil and gas can be condensed through a multi-stage separator and a cooling system to obtain fuel oil. The exhaust gas and dust from the pyrolysis processor enters the atomizing dust device for treatment and then discharges; part of the low-carbon chain non-condensable gas enters the combustible gas recovery system through the water seal, and is burned as fuel for the pyrolysis.
Applications
The waste tire pyrolysis plant has a wide range of applications in various industries, including:
- Fuel production: The pyrolysis oil can be used as a fuel source in industries such as steel and iron, boiler factories, ceramics, power plants, chemical industries, hotels, and restaurants. It can also be used in generators to produce electricity.
- Construction materials: The carbon black produced by the pyrolysis process can be used in the production of construction bricks, or as a fuel source.
- Recycling: The steel wire recovered from the pyrolysis process can be sold directly or recycled to produce new steel products.
Process flow
Step 1: Feeding | Put the waste tires into the pyrolysis axe. This process can be fed by manual feeding, flat conveyor feeding and hydraulic feeding machine and other feeding methods. Most factories usually use a hydraulic feeder to feed materials. Because of its high production efficiency, labor cost savings, and safety, it is widely used by many factories. Close the loading door after loading. | |
Step 2: Heating | You can use tire oil or non-condensable gas (excess non-condensable gas produced during the pyrolysis process of several other equipment) to heat the reactor evenly. When the temperature reaches 80°C, some Gas precipitation (most of the gas at this time is water vapor, the liquefied part is water, and the non-liquefiable gas reaches the combustion chamber through the gas circulation system for combustion). When the temperature reaches 120°C, the combustible gas is precipitated and enters the gas distribution bag. The residual oil (contains part of the residue, which can be used as fuel to heat the main furnace) sinks to the residual oil tank, while the light oil automatically enters the condenser and liquefies. into light oil tanks. In this way, heavy oil and light oil (for heating and heating of the whole project) can be obtained. | |
Step 3: Non-condensable gas treatment | Non-condensable gas (C1-C4 components) flowing into the oil tank together with the oil, the gas that cannot be condensed, has passed through two safety water seals (one for standby and one for use, water The role of the seal is to prevent the open flame from returning from the combustion chamber to meet the exhaust gas, and to prevent the gas from flowing back), and return to the heating chamber as fuel to heat the furnace. Therefore, at the beginning of equipment operation, the fuel is fuel oil or natural gas. When the temperature continues to rise, the non-condensable gas generated can be used as fuel. | |
Step 4: Smoke and dust treatment | All the smoke and dust produced by combustion are pumped by the induced draft fan to the general dust removal system for treatment. The treated smoke and dust are white water vapor without black particles, and then the water vapor will enter the industrial purification device Carry out standard discharge treatment to ensure that the emitted smoke and dust discharge meets the emission standards required by environmental protection. | |
Step 5: Slag discharge | After the slag is discharged, the pyrolysis process is over. The steel wire and carbon black we need are in the main furnace. The equipment adopts a fully automatic sealed slag discharge system. Furnace screw, slag outlet sealer and slag remover are used for slag removal. Carbon black is mainly used for ink, pigment, reinforcing agent, additive, etc. | |
Step 6: Steel wire | The steel wire is pulled out by the tractor, which saves labor and achieves automatic production of equipment. When the steel wire is discharged, it cooperates with ventilation and dust removal equipment to ensure no dust. |
Technical Parameters
Model | Host volume | Daily throughput | Total operating power |
2600*6000 | 31.8 cubic meters | 8 tons | 16 kW/h |
2600*6600 | 35 cubic meters | 9 tons | 16 kW/h |
2800*6600 | 40.6 cubic meters | 12 tons | 18 kW/h |
2800*7500 | 46.2 cubic meters | 15 tons | 20 kW/h |
Advantages
- Integrated design, compact structure, complete integrity and guaranteed safety. The main body of the equipment adopts the standard Q345R special boiler steel plate (high temperature and oxidation resistant alloy steel) resistant to oxidation, corrosion, long life and safety.
- The equipment adopts a special anti-coking structure, which greatly solves the current situation that the sludge is coked and inconvenient to clean during the pyrolysis process.
- The main engine adopts the outer ring gear to rotate. In addition, the ring gear is formed once, which is strong and durable. It is more stable than the pin-pin sleeve transmission on the market. In case of damage, protect the host motor and reducer and prolong its service life.
- The welding of the main engine is (automatic submerged arc machine welding), and the welding is formed once, even and full.
- The cooling system includes: cooling pipes, air distribution bag, cooling pool, etc. It has the characteristics of large cooling area, good cooling effect and high oil collection rate.
- The waste residue after pyrolysis can meet the emission standard required by environmental protection the oil content of 2%.
Warnings
Operator safety is the top important issue! Please operate the equipment with cautions. Working with inflammable& explosive or toxic gases is very dangerous, operators must take all necessary precautions before starting the equipment. Working with positive pressure inside the reactors or chambers is dangerous, operator must fellow the safety procedures strictly. Extra caution must also be taken when operating with air-reactive materials, especially under vacuum. A leak can draw air into the apparatus and cause a violent reaction to occur.
Designed for You
KinTek provide deep custom made service and equipment to worldwide customers, our specialized teamwork and rich experienced engineers are capable to undertake the custom tailoring hardware and software equipment requirements, and help our customer to build up the exclusive and personalized equipment and solution!
Would you please drop your ideas to us, our engineers are ready for you now!
FAQ
What Is A Pyrolysis Furnace?
How Does A Pyrolysis Furnace Work?
What Are The Applications Of Pyrolysis Furnaces?
What Are The Advantages Of Using Pyrolysis Furnaces?
What Factors Should Be Considered When Selecting A Pyrolysis Furnace?
What Safety Precautions Should Be Followed When Using A Pyrolysis Furnace?
4.8
out of
5
The setup was seamless, and the staff were very professional and knowledgeable. The equipment is top-notch and has improved our waste management.
4.9
out of
5
The plant's efficiency and eco-friendliness impressed me. It's amazing how we can turn waste tires into valuable resources like fuel and carbon black.
4.7
out of
5
The plant's compact design saved us a lot of space, and the installation process was surprisingly smooth. We're very satisfied with the results.
5.0
out of
5
The waste tire pyrolysis plant has significantly reduced our landfill waste and increased our energy independence. It's a win-win situation!
4.8
out of
5
The plant's operation costs are surprisingly low, and the maintenance requirements are minimal. It's a cost-effective solution for waste tire management.
4.9
out of
5
The plant's safety features are top-notch, ensuring the protection of our workers and the environment. We're very impressed with the overall quality and performance.
4.7
out of
5
The plant's modular design allowed us to customize it to our specific needs. The flexibility and scalability are truly impressive.
5.0
out of
5
The plant's automation features have streamlined our operations and improved efficiency. It's a game-changer for our waste management process.
4.8
out of
5
The plant's construction was completed ahead of schedule, and the installation process was flawless. We're thrilled with the speed and professionalism of the team.
4.9
out of
5
The plant's integration with our existing waste management system was seamless. The compatibility and ease of use have made it a valuable addition to our operations.
4.7
out of
5
The plant's environmental impact is minimal, and the emissions are well within regulatory limits. We're proud to be contributing to a cleaner and greener future.
5.0
out of
5
The plant's durability and longevity are exceptional. We're confident that it will continue to serve us well for many years to come.
4.8
out of
5
The plant's technological advancements are impressive. The innovative features and processes have set a new standard for waste tire management.
4.9
out of
5
The plant's versatility is remarkable. It can handle a wide range of tire sizes and types, making it a versatile solution for various applications.
4.7
out of
5
The plant's customer support is outstanding. The team is responsive, knowledgeable, and always willing to go the extra mile to ensure our satisfaction.
5.0
out of
5
The plant's value for money is unbeatable. The cost savings and environmental benefits far outweigh the initial investment. It's a wise choice for any organization looking to manage waste tires responsibly.
4.8
out of
5
The plant's delivery was prompt, and the packaging ensured that it arrived in perfect condition. We were able to start using it immediately, which minimized downtime.
4.9
out of
5
The plant's ease of operation is remarkable. The intuitive controls and user-friendly interface make it accessible to personnel of all skill levels.
4.7
out of
5
The plant's reliability is exceptional. It operates smoothly and efficiently, with minimal downtime. We can count on it to consistently deliver the desired results.
Products
Waste Tire Pyrolysis Plant for Recycling and Energy Recovery
REQUEST A QUOTE
Our professional team will reply to you within one business day. Please feel free to contact us!
Related Products
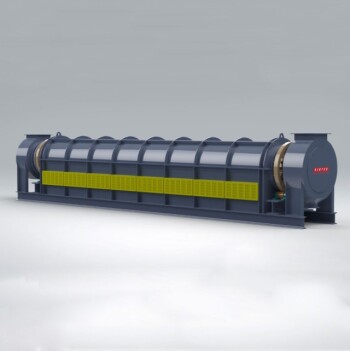
Electric Rotary Kiln Pyrolysis Furnace Plant Machine Calciner Small Rotary Kiln Rotating Furnace
Electric rotary kiln - precisely controlled, it's ideal for calcination and drying of materials like lithium cobalate, rare earths, and non-ferrous metals.
Related Articles
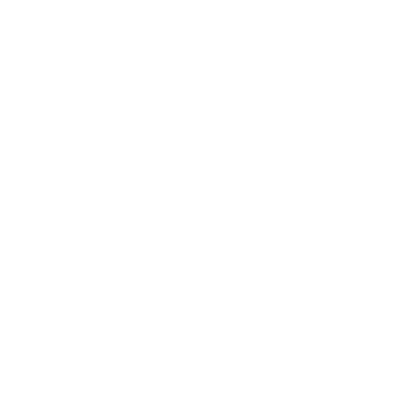
Electric Rotary Kiln Pyrolysis Furnace: A Comprehensive Guide to Pyrolysis Technology
Discover the principles, applications, and advantages of electric rotary kiln pyrolysis furnaces. Explore various heating methods, factors affecting efficiency, and the environmental benefits of this technology.
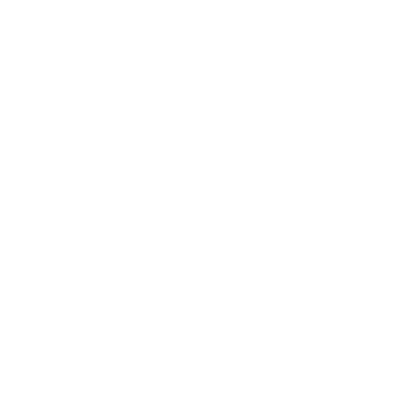
Biomass Pyrolysis Equipment A Sustainable Solution for Waste Management
Biomass pyrolysis has gained increased attention as a sustainable solution for waste management and renewable energy generation.
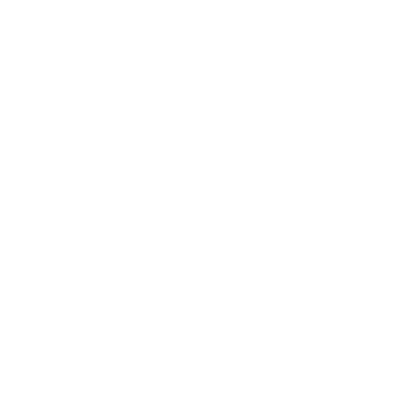
How Biomass Pyrolysis Machines Work A Comprehensive Overview
Biomass pyrolysis machines are designed to convert biomass materials into useful products such as biochar, bio-oil, and syngas.
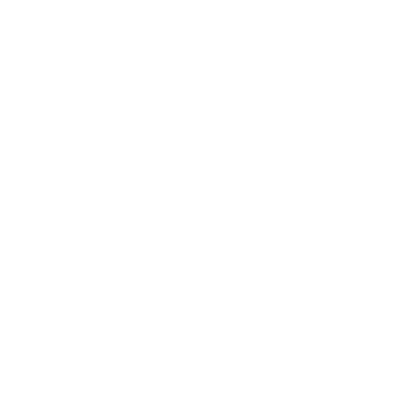
Biomass Pyrolysis An Effective Means of Producing Biofuels
Biomass pyrolysis is a process that involves heating organic matter in the absence of oxygen to break it down into smaller molecules. This technology has gained popularity due to its potential to produce biofuels.
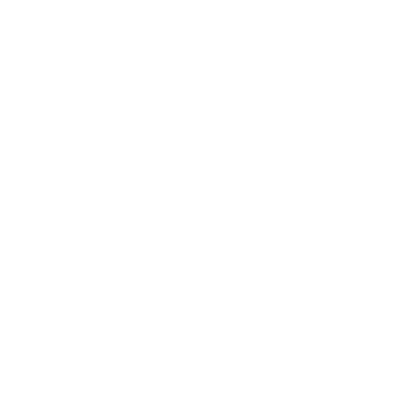
The Advantages and Disadvantages of Different Biomass Feedstocks for Pyrolysis
Different feedstocks have their own unique advantages and disadvantages for pyrolysis, which must be carefully considered when selecting the most suitable feedstock for a particular application.
markdown to html 用
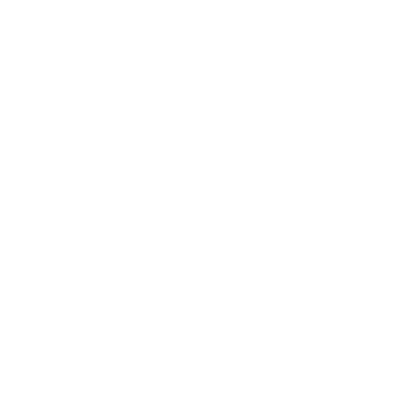
How Biomass Pyrolysis Can Help Meet Growing Energy Demands
Biomass pyrolysis is a process that converts organic material into energy-rich biofuels through heating in the absence of oxygen. This renewable energy source is becoming increasingly popular due to its environmental and economic benefits.
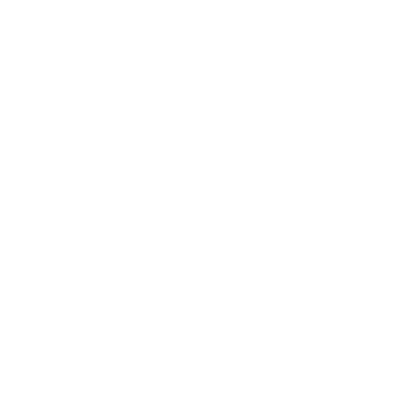
Electric Rotary Kiln Pyrolysis Furnace: Design, Operation, and Applications
Explore the comprehensive guide on electric rotary kiln pyrolysis furnaces, including their design, operation, efficiency factors, and diverse applications in industries like waste processing and biofuel production.
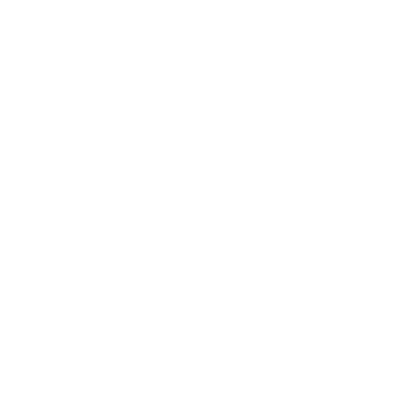
The Importance of Activated Carbon Regeneration in Water Treatment
In water treatment, activated carbon is often used as a means of removing unwanted contaminants, such as chlorine, chloramines, and organic matter, from drinking water and wastewater.
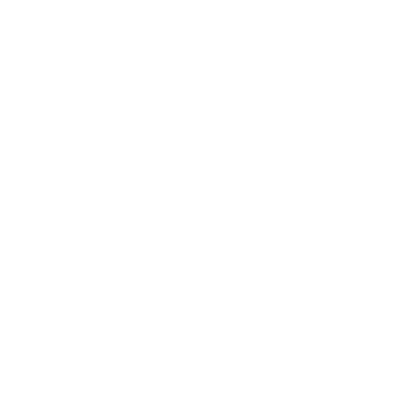
6 Ways To activated carbon regeneration
Activated Carbon Regeneration: Thermal Regeneration Method, Biological Regeneration Method, Wet Oxidation Regeneration Method, Solvent Regeneration Method, Electrochemical Regeneration Method, Catalytic Wet Oxidation Method
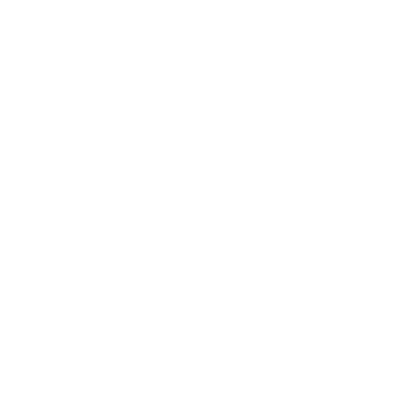
Mastering Rotary Kilns: A Comprehensive Guide to Operation, Applications, and Maintenance
Unlock the potential of rotary kilns with our comprehensive guide. Learn about their versatile applications, from industrial sintering to organic combustion. Discover how they work, the difference between direct and indirect kilns, and the wide range of fuels they can utilize. Whether you're in cement production or specialized thermal processing, this guide will equip you with the knowledge to optimize your rotary kiln operations.
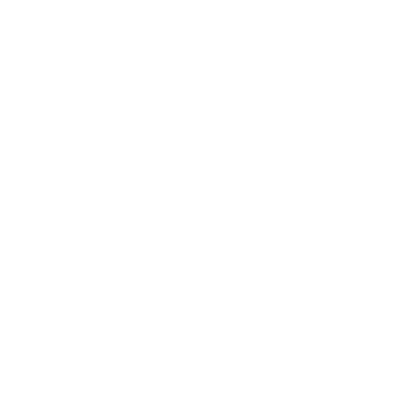
Understanding the Warm Isostatic Pressing Technique
Warm Isostatic Pressing (WIP) is a technique used in the manufacturing industry to form and press powder materials. It involves the use of a flexible material as the envelope die and hydraulic pressure as the medium to shape the material. Unlike traditional pressing methods, WIP utilizes a liquid medium that is heated and injected into a sealed pressing cylinder. This technique is particularly beneficial for materials with special temperature requirements or those that cannot be formed at room temperature.