Introduction
Table of Contents
Warm Isostatic Pressing (WIP) is a technique used in the manufacturing industry to form and press powder materials. It involves the use of a flexible material as the envelope die and hydraulic pressure as the medium to shape the material. Unlike traditional pressing methods, WIP utilizes a liquid medium that is heated and injected into a sealed pressing cylinder. This technique is particularly beneficial for materials with special temperature requirements or those that cannot be formed at room temperature. In this article, we will explore the concept of Warm Isostatic Pressing and its applications in various industries.
Concept of Warm Isostatic Pressing
Definition of warm isostatic pressing
Warm isostatic pressing is a technique used to achieve isostatic pressing at a temperature that does not exceed the boiling point of the liquid medium. It involves the use of a flexible material as the envelope die and hydraulic pressure as the pressure medium to form and press the powder material. This process is typically used for powders, binders, and other materials with special temperature requirements or that cannot be formed at room temperature.
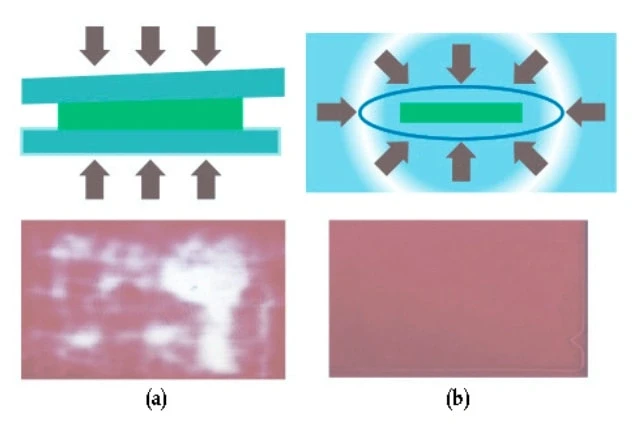
The use of a flexible material as the envelope die
In warm isostatic pressing, a flexible material is used as the envelope die. This allows for the application of uniform pressure to the powdered products from all directions. The flexibility of the material ensures that the pressure is evenly distributed, resulting in a uniform and consistent final product.
Utilization of hydraulic pressure as the pressure medium to form and press the powder material
Hydraulic pressure is used as the pressure medium in warm isostatic pressing to form and press the powder material. The liquid medium, typically warm water or a similar substance, is heated and continuously injected into a sealed pressing cylinder through a booster source. The hydraulic pressure applies uniform pressure to the powder material, ensuring its consolidation and shaping.
Warm isostatic pressing has revolutionized the manufacturing industry by enabling the production of complex parts and components with precision and efficiency. It is a cutting-edge technology that allows for isostatic pressing at controlled temperatures, opening up new possibilities for the fabrication of advanced materials.
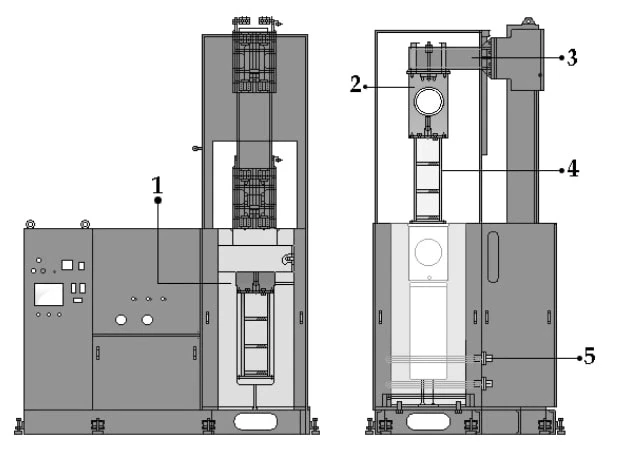
Processing Steps
Heating of the liquid medium
In the CIP process, heating of the liquid medium is an essential step. The liquid medium, usually water or a specialized solution, is heated to a specific temperature before being used in the molding process. This heating process helps in achieving the desired viscosity of the medium, which is important for proper mold filling and compression. The liquid medium is typically heated using a heat generator or a heating bath, which provides the necessary energy for evaporation.
Use of a booster source for injecting the heated liquid medium into the sealed pressing cylinder
Once the liquid medium is heated, it is injected into the sealed pressing cylinder. This injection process is facilitated by a booster source, which helps in maintaining the required pressure and flow rate of the medium. The booster source ensures that the heated liquid medium is delivered to the pressing cylinder with precision and accuracy, allowing for efficient mold filling and compression.
Use of a heat generator for maintaining the temperature accuracy
To ensure the temperature accuracy throughout the CIP process, a heat generator is used. The heat generator helps in maintaining the desired temperature of the liquid medium, which is crucial for achieving consistent results in the molding process. By continuously supplying heat to the medium, the heat generator ensures that the temperature remains within the specified range, minimizing variations and ensuring uniformity in the molded products.
In summary, the processing steps in CIP molding involve heating of the liquid medium, using a booster source for injecting the heated medium into the pressing cylinder, and utilizing a heat generator to maintain temperature accuracy. These steps are crucial for achieving successful mold filling, compression, and overall quality in the CIP molding process.
Applications of Warm Isostatic Pressing
Typical usage for materials with special temperature requirements
Warm isostatic pressing (WIP) is a variant of cold isostatic pressing (CIP) that includes a heating element. It employs warm water or a similar medium to apply uniform pressure to powdered products from all directions. This technology is commonly used for powders, binders, and other materials that have special temperature requirements or cannot be molded at room temperature.
WIP is revolutionizing the manufacturing industry by enabling the production of complex parts and components with precision and efficiency. It is widely used in various industries, including:
- Castings
- Powder metallurgy
- Ceramics industry
- Porous materials
- Near-net forming
- Material bonding
- Plasma spraying
- Manufacture of high-end graphite
Applications of hot isostatic presses (castings, powder metallurgy, ceramics, porous materials, near net shape materials, high-end graphite manufacturing, plasma spraying)
Suitable for materials that cannot be formed at room temperature
One of the main advantages of warm isostatic pressing is its ability to process materials that cannot be formed at room temperature. This technique allows for the shaping and pressing of powder materials that require specific temperature conditions for proper forming.
By heating the liquid medium and injecting it into a sealed pressing cylinder, WIP ensures the material reaches the necessary temperature for molding. The process is controlled through a heating element in the pressing cylinder, guaranteeing accurate temperature control.
In summary, warm isostatic pressing is a versatile technique that finds applications in various industries. It is especially beneficial for materials with special temperature requirements or those that cannot be formed at room temperature. WIP has revolutionized the manufacturing industry by enabling the production of complex parts and components with precision and efficiency.
Conclusion
In conclusion, the warm isostatic pressing (WIP) technique offers a versatile solution for materials with special temperature requirements. By utilizing a flexible material as the envelope die and hydraulic pressure as the pressure medium, WIP allows for the formation and pressing of powder materials in a controlled and accurate manner. The heating of the liquid medium, along with the use of a booster source and heat generator, ensures the temperature accuracy throughout the processing steps. WIP is particularly suitable for materials that cannot be formed at room temperature, making it a valuable technique in various industries.
CONTACT US FOR A FREE CONSULTATION
KINTEK LAB SOLUTION's products and services have been recognized by customers around the world. Our staff will be happy to assist with any inquiry you might have. Contact us for a free consultation and talk to a product specialist to find the most suitable solution for your application needs!