Introduction
Dental ceramic furnaces are an essential tool for dentistry, used to create various dental restorations such as crowns, bridges, and veneers. These furnaces are expensive and require regular maintenance to ensure they function properly and produce accurate results. This blog post aims to provide a comprehensive guide on maintaining dental ceramic furnaces to achieve their maximum lifespan and avoid costly repairs. By following the guidelines, dentists and dental technicians can ensure that their dental ceramic furnaces are always in top condition and produce high-quality dental restorations.
Table of Contents
Importance of Regular Calibration
Dental ceramic furnaces are essential equipment in dental laboratories, used for firing dental prostheses like crowns and bridges. Calibration is the process of verifying the accuracy of the temperature readings of the furnace, ensuring that it is within the acceptable range. Regular calibration of dental ceramic furnaces is crucial as it can help prevent defective prostheses from being produced, which can lead to dissatisfied customers, wasted materials, and loss of money.
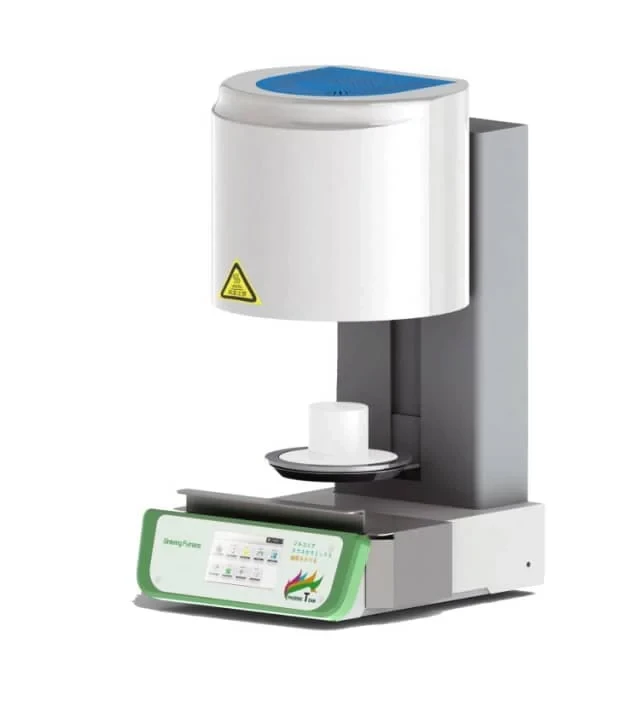
What is Calibration?
Calibration is the process of verifying and adjusting the settings of a measuring instrument to ensure its accuracy. In dental ceramic furnaces, calibration involves verifying the temperature readings of the furnace to ensure that they are within the acceptable range. This is crucial as the accuracy of temperature readings affects the quality of the fired prosthesis.
Why is Regular Calibration Important?
Regular calibration of dental ceramic furnaces is crucial as it can help prevent defective prostheses from being produced, which can lead to dissatisfied customers, wasted materials, and loss of money. Calibration can also ensure that the furnace operates at its optimum temperature, which can minimize energy consumption and extend the equipment's lifespan. Moreover, calibration can detect any problems with the furnace, such as malfunctioning heating elements or thermocouples, which need to be fixed.
How Often Should You Calibrate?
It is recommended to have dental ceramic furnaces calibrated once every six months or as per the manufacturer's instructions. However, the frequency of calibration may vary depending on the age and usage requirements of the furnace/muffle. With a relatively new, well-maintained furnace that is operating at average production levels, calibrating every six months should be sufficient. As the furnace/muffle age and usage requirements increase, more frequent calibration may be necessary.
Conclusion
Dentists and dental technicians rely on accurate and consistent results from their dental ceramic furnaces to provide high-quality dental prostheses to their patients. Therefore, it is of utmost importance to maintain and calibrate these furnaces regularly. Calibration is a simple and cost-effective procedure that can help save time, money, and resources in the long run while ensuring that the furnace produces accurate and consistent results.
Factors to Consider for Calibration Frequency
Calibration of a dental ceramic furnace is vital for producing high-quality dental restorations. The frequency of calibration depends on several factors.
Manufacturer's Recommendations
The manufacturer's recommendations play a significant role in determining calibration frequency. It is typically recommended to calibrate the furnace at least once a year or after a major repair.
Frequency of Use
The more frequently a furnace is used, the more often it may require calibration. A furnace that is frequently used may require more frequent calibration than one that is seldom used.
Type of Materials Used
Different types of materials used in the furnace may require adjustments in temperature and calibration. Factors such as the melting point and thermal conductivity of the materials can impact the calibration frequency.
Environmental Conditions
Environmental factors such as dust and temperature changes can also affect calibration. A furnace that operates in a dusty environment may require more frequent calibration than one that operates in a clean environment.
Regular maintenance, including keeping the furnace clean and replacing worn parts, can also help prolong the life of the furnace and prevent potential breakdowns. Proper maintenance and calibration of a dental ceramic furnace are essential for producing consistent and accurate dental restorations.
Common Troubleshooting
Maintaining a dental ceramic furnace is essential to ensure optimal performance and longevity of the equipment. However, even with regular maintenance, issues can still arise. Here are some common problems that you may encounter when operating a dental ceramic furnace, and some troubleshooting steps to address them.
Temperature Fluctuations
If your furnace is experiencing temperature fluctuations, the thermocouple or temperature controller may need to be recalibrated or replaced. Check the temperature controller settings to make sure they are properly set.
Vacuum Leaks
If you notice a decrease in vacuum or pressure, check the seals and gaskets. Tighten any loose fittings, and replace any damaged or worn-out seals. This should resolve any vacuum leak issues.
Overheating
Overheating is a common problem that can arise due to damaged, worn, or faulty heating elements. Adjust the temperature controller settings to prevent the furnace from overheating. Inspect each element and replace accordingly.
Power Issues
Supply failure is a common cause of power issues. If the furnace won't turn on or is having power issues, check the power supply and wiring for any damage or loose connections. You may need to repair or replace any damaged components.
Gas Flow Issues
If your furnace is using a gas supply, check the gas flow and pressure. Ensure that the gas supply is turned on, and check the valves and regulators for any damage or leaks.
By following these troubleshooting steps, you can fix common issues that arise with a dental ceramic furnace and ensure that the equipment continues to function correctly. However, if problems persist, it may be necessary to replace faulty parts or seek expert assistance.
Purging and Cooling Techniques
Proper maintenance of your dental ceramic furnace is essential to ensure the quality of dental work produced. Purging and cooling techniques are two essential aspects of maintenance that can prolong the lifespan of your furnace and keep it running efficiently.
Purging Techniques
Purging involves removing any contaminants from the furnace that can affect the quality of the ceramic work produced. It is recommended to purge the furnace after every use to remove any residue that could affect the next batch of ceramic work. Here are the steps to follow when purging your dental ceramic furnace:
- First, remove any leftover ceramic material from the furnace using a soft brush or vacuum.
- Next, set the furnace to a temperature of 300°C and allow it to heat up for 15 minutes.
- Once the furnace has reached the desired temperature, open the furnace door and allow it to cool down to 200°C.
- After it has reached the desired temperature, close the furnace door and turn on the vacuum pump to draw the vacuum.
- Leave the furnace under vacuum for 10 minutes to purge any contaminants from the furnace.
- Turn off the vacuum pump and allow the furnace to cool down naturally.
Cooling Techniques
Cooling techniques are necessary to prevent thermal shock, a common cause of cracks and damage to the furnace. It is essential to allow the furnace to cool down gradually to prevent any sudden temperature changes that could damage the furnace. Here are the steps to follow when cooling your dental ceramic furnace:
- First, turn off the furnace and allow it to cool down naturally for at least 30 minutes.
- Next, open the furnace door and allow it to cool down to 200°C.
- Once it has reached the desired temperature, close the furnace door and set the furnace to a temperature of 150°C.
- Allow the furnace to cool down to 100°C, then set the temperature to 50°C.
- Finally, turn off the furnace and wait for it to cool down completely before opening the door.
In summary, purging and cooling techniques are essential to maintaining your dental ceramic furnace. By following these steps, you can prolong the lifespan of your furnace, improve the quality of dental work produced, and save money in the long run. Remember to follow the manufacturer's instructions and consult with a professional if needed.
Simple Solutions for Maintaining a Dental Furnace
Maintaining your dental ceramic furnace is crucial to ensure its longevity and accuracy. Here are some simple solutions to help you maintain your dental furnace:
Clean Your Furnace Regularly
Cleaning your dental ceramic furnace regularly is the first step in maintaining it. You should clean the chamber, heating elements, and the fan using non-abrasive cleaning agents to avoid damaging the components of the furnace.
Inspect Your Furnace Regularly
Regular inspection of your dental ceramic furnace is essential. This will allow you to identify any issues before they become more serious and costly to repair. Look for signs of damage and wear, and replace worn components to ensure the furnace is operating at its full potential.
Follow the Manufacturer's Instructions
Following the manufacturer's instructions for use and maintenance is crucial to maintaining your dental ceramic furnace. This includes monitoring the temperature settings and replacing worn components.
Have Your Furnace Serviced Regularly
It is recommended to have your dental ceramic furnace serviced by a qualified technician on a regular basis. This will ensure that the furnace is operating at its full potential and will help to extend its lifespan.
By following these simple solutions for maintaining your dental furnace, you can ensure that it will continue to provide you with accurate and reliable results for years to come.
Conclusion
In conclusion, maintaining your dental ceramic furnace is essential to ensure that it produces accurate and consistent results. Regular calibration and maintenance play a crucial role in extending the life of your furnace and avoiding costly repairs. When choosing a dental furnace, consider factors such as temperature range, heating element, and overall build quality. Follow the manufacturer's instructions for purging and cooling techniques and troubleshoot any issues promptly. With proper care and maintenance, your dental furnace can provide reliable service for years to come.
CONTACT US FOR A FREE CONSULTATION
KINTEK LAB SOLUTION's products and services have been recognized by customers around the world. Our staff will be happy to assist with any inquiry you might have. Contact us for a free consultation and talk to a product specialist to find the most suitable solution for your application needs!