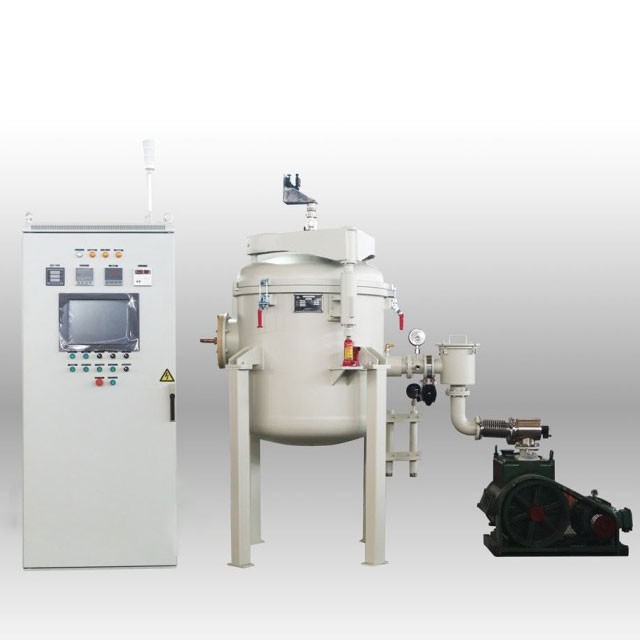
Graphitization furnace
Ultra-High Temperature Graphite Vacuum Graphitization Furnace
Item Number : GF-09
Price varies based on specs and customizations
- Specifications
- Please refer to the chart below for detailed parameters.
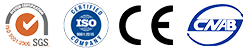
Shipping:
Contact us to get shipping details Enjoy On-time Dispatch Guarantee.
Why Choose Us
Reliable PartnerEasy ordering process, quality products, and dedicated support for your business success.
Introduction
The ultra-high temperature graphitization furnace utilizes medium frequency induction heating in a vacuum or inert gas environment. The induction coil generates an alternating magnetic field, inducing eddy currents in the graphite crucible, which heats up and radiates heat to the workpiece, bringing it to the desired temperature. This furnace is primarily used for graphitization and sintering of carbon materials, carbon fiber materials, and other composite materials. It comprises a furnace body, cover, heating sensor, insulation layer, electrode extraction device, water circulation distribution system, vacuum system, temperature control system, and more. The electrical system includes a 60KVA, IGBT transistor intermediate frequency power supply and water-cooled cable, equipped with various indicating instruments and alarm functions. The control part employs a 15-inch touch screen and programmable controller PLC.
Details & Part
Applications
The ultra-high temperature graphitization furnace finds applications in a wide range of industries, including:
- Ceramic firing
- Carbide growth
- Carbonization
- Graphitization
- Sintering
- Annealing
- Brazing
- Degassing
Features
The ultra-high temperature graphitization furnace offers a range of advanced features that provide significant benefits to users:
- High temperature capability: The furnace can reach temperatures up to 2200°C, making it suitable for a wide range of high-temperature applications.
- High efficiency: The graphite-based furnace is extremely efficient, resulting in lower energy consumption and faster heating times.
- Uniform heating: The furnace's design ensures uniform heating throughout the chamber, providing consistent results.
- Vacuum or inert gas environment: The furnace can be operated in a vacuum or inert gas environment, allowing for precise control of the atmosphere surrounding the workpiece.
- Intelligent control system: The furnace is equipped with an advanced touch screen and programmable controller for precise temperature control and monitoring.
- Safety features: The furnace includes audible and visual alarms for overvoltage, overcurrent, and water cutoff, ensuring safe operation.
Principle
Ultra-high temperature graphitization furnace operates based on the principle of medium frequency induction heating. The induction coil generates an alternating magnetic field, inducing eddy currents in the graphite crucible. This generates high temperatures that radiate to the workpiece, bringing it to the desired temperature. This furnace is employed for graphitization and sintering of carbon materials, carbon fiber materials, and composite materials.
Advantages
- High temperature: Ultra-high temperature graphitization furnace can reach a temperature of 2500°C, which is suitable for a variety of high temperature treatment and graphitization treatment applications.
- High efficiency: The ultra-high temperature graphitization furnace uses the principle of medium frequency induction heating, which has the advantages of high efficiency and uniform heating.
- Uniform heating: The ultra-high temperature graphitization furnace uses a graphite crucible to generate high temperature and radiates to the workpiece, which can achieve uniform heating of the workpiece.
- Wide application: The ultra-high temperature graphitization furnace is suitable for graphitization and sintering of carbon materials, carbon fiber materials and other composite materials.
- Easy to operate: The ultra-high temperature graphitization furnace is controlled by a 15-inch touch screen and programmable controller PLC, which is easy to operate.
- Safe and reliable: The ultra-high temperature graphitization furnace has audible and visual alarm functions such as overvoltage, overcurrent, and water cutoff, which is safe and reliable.
Technical specification
Power supply capacity | 60KVA |
Power supply | 4000~8000Hz (automatic tracking) |
Temperature | 3000℃ |
Temperature control accuracy | ±2℃ |
Temperature measurement method | 1100℃~3000℃ |
Effective working area size | Φ200×200 mm (diameter×height) |
Cold ultimate vacuum degree | 133Pa |
Pressure rise | 3.0 Pa/h |
Protective atmosphere | Argon Nitrogen |
Inflation pressure | ≤ 0.03MPa |
Material in and out method | Top loading and discharging |
Heating conditions | Atmosphere sintering (inert gas) |
FAQ
What Is A Graphitization Furnace?
What Is A Graphite Vacuum Furnace Used For?
What Is CVD Furnace?
Chemical vapor deposition (CVD) is a technology that uses various energy sources such as heating, plasma excitation or light radiation to chemically react gaseous or vapor chemical substances on the gas phase or gas-solid interface to form solid deposits in the reactor by means of chemical reaction.To put it simply, two or more gaseous raw materials are introduced into a reaction chamber, and then they react with each other to form a new material and deposit it on the substrate surface.
CVD furnace is one combined furnace system with high temperature tube furnace unit,gases control unit, and vacuum unit, it is widely used for experiment and production of composite material preparation, microelectronics process, semiconductor optoelectronic, solar energy utilization, optical fiber communication, superconductor technology, protective coating field.
What Is The Working Principle Of An Ultra-high Temperature Graphitization Furnace?
What Are The Main Components Of An Ultra-high Temperature Graphitization Furnace?
How To Maintain An Ultra-high Temperature Graphitization Furnace?
What Are The Main Applications Of Graphitization Furnaces?
What Are The Main Types Of Graphite Vacuum Furnaces?
How Does CVD Furnace Work?
CVD furnace system consists of high temperature tube furnace unit, reacting gas source precise control unit, vacuum pump station and corresponding assembling parts.
Vacuum pump is to remove the air from the reacting tube,and make sure there is no unwanted gases inside the reaction tube, after that the tube furnace will heat the reaction tube to a target temperature, then reacting gas source precise control unit can introduce different gases with a set ratio into the furnace tube for the chemical reaction, the chemical vapor deposition will be formed in the CVD furnace.
What Are The Different Types Of Graphitization Furnaces?
How Does A Graphite Vacuum Furnace Work?
Which Gas Is Used In CVD Process?
There are tremendous gas sources can be used in the CVD process, the common chemical reactions of CVD includes Pyrolysis, photolysis, reduction, oxidation, redox,so the gases involved in these chemical reactions can be used in the CVD process.
We take CVD Graphene growth for an example, the gases used in the CVD process will be CH4,H2,O2 and N2.
How Does A Graphitization Furnace Work?
What Are The Advantages Of Using A Graphite Vacuum Furnace?
What Is The Advantage Of CVD System?
- Wide range of films can be produced, metal film, nonmetal film and multi-component alloy film as required. At the same time, it can prepare high-quality crystals that are difficult to obtain by other methods, such as GaN, BP, etc.
- The film forming speed is fast, usually several microns per minute or even hundreds of microns per minute. It is possible to simultaneously deposit large quantities of coatings with uniform composition, which is incomparable to other film preparation methods, such as liquid phase epitaxy (LPE) and molecular beam epitaxy (MBE).
- The working conditions are carried out under normal pressure or low vacuum conditions, so the coating has good diffraction, and the workpieces with complex shapes can be uniformly coated, which is much superior to PVD.
- Due to the mutual diffusion of reaction gas, reaction product and substrate, a coating with good adhesion strength can be obtained, which is crucial for preparing surface strengthened films such as wear-resistant and anti-corrosion films.
- Some films grow at a temperature far lower than the melting point of the film material. Under the condition of low temperature growth, the reaction gas and reactor wall and impurities contained in them almost do not react, so a film with high purity and good crystallinity can be obtained.
- Chemical vapor deposition can obtain a smooth deposition surface. This is because compared with LPE, chemical vapor deposition (CVD) is carried out under high saturation, with high nucleation rate, high nucleation density, and uniform distribution on the whole plane, resulting in a macroscopic smooth surface. At the same time, in chemical vapor deposition, the average free path of molecules (atoms) is much larger than LPE, so the spatial distribution of molecules is more uniform, which is conducive to the formation of a smooth deposition surface.
- Low radiation damage, which is a necessary condition for manufacturing metal oxide semiconductors (MOS) and other devices
What Are The Advantages Of Using A Graphitization Furnace?
What Temperature Range Can A Graphite Vacuum Furnace Achieve?
What Does PECVD Stand For?
PECVD is a technology that uses plasma to activate reaction gas, promote chemical reaction on the surface of substrate or near surface space, and generate solid film. The basic principle of plasma chemical vapor deposition technology is that under the action of RF or DC electric field, the source gas is ionized to form a plasma, the low-temperature plasma is used as the energy source, an appropriate amount of reaction gas is introduced, and the plasma discharge is used to activate the reaction gas and realize chemical vapor deposition.
According to the method of generating plasma, it can be divided into RF plasma, DC plasma and microwave plasma CVD, etc...
What Industries Benefit From Graphite Vacuum Furnaces?
What Is The Difference Between CVD And PECVD?
The difference between PECVD and traditional CVD technology is that the plasma contains a large number of high-energy electrons, which can provide the activation energy required in the chemical vapor deposition process, thus changing the energy supply mode of the reaction system. Since the electron temperature in the plasma is as high as 10000K, the collision between electrons and gas molecules can promote the chemical bond breaking and recombination of the reaction gas molecules to generate more active chemical groups, while the whole reaction system maintains a lower temperature.
So compared to the CVD process, PECVD can carry out the same chemical vapor deposition process with a lower temperature.
4.8
out of
5
The furnace is very efficient and has uniform heating, which greatly improves our work efficiency.
4.9
out of
5
The furnace is easy to operate and can be controlled by a touch screen, which is very convenient.
4.7
out of
5
The furnace is very safe and reliable, with audible and visual alarm functions, which gives me a sense of security.
4.6
out of
5
The furnace has a wide range of applications and can be used for graphitization and sintering of various materials.
4.8
out of
5
The furnace is very durable and has a long service life, which saves us a lot of maintenance costs.
4.9
out of
5
The furnace is very economical and has a high cost performance, which is very suitable for our laboratory.
4.7
out of
5
The delivery speed of the furnace is very fast, and it can be delivered to our laboratory in a short time.
4.6
out of
5
The furnace is very valuable for money, and its price is very reasonable.
4.8
out of
5
The furnace is very durable and has a long service life, which saves us a lot of maintenance costs.
4.9
out of
5
The furnace is very economical and has a high cost performance, which is very suitable for our laboratory.
4.7
out of
5
The delivery speed of the furnace is very fast, and it can be delivered to our laboratory in a short time.
4.6
out of
5
The furnace is very valuable for money, and its price is very reasonable.
4.8
out of
5
The furnace is very efficient and has uniform heating, which greatly improves our work efficiency.
4.9
out of
5
The furnace is easy to operate and can be controlled by a touch screen, which is very convenient.
4.7
out of
5
The furnace is very safe and reliable, with audible and visual alarm functions, which gives me a sense of security.
4.6
out of
5
The furnace has a wide range of applications and can be used for graphitization and sintering of various materials.
4.8
out of
5
The furnace is very durable and has a long service life, which saves us a lot of maintenance costs.
4.9
out of
5
The furnace is very economical and has a high cost performance, which is very suitable for our laboratory.
Products
Ultra-High Temperature Graphite Vacuum Graphitization Furnace
REQUEST A QUOTE
Our professional team will reply to you within one business day. Please feel free to contact us!
Related Products
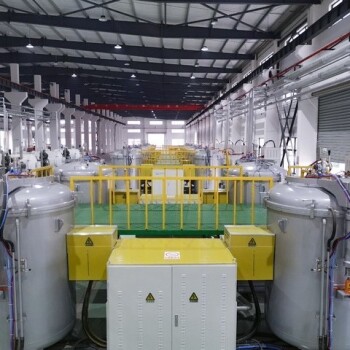
Vertical High Temperature Graphite Vacuum Graphitization Furnace
Vertical high temperature graphitization furnace for carbonization and graphitization of carbon materials up to 3100℃.Suitable for shaped graphitization of carbon fiber filaments and other materials sintered in a carbon environment.Applications in metallurgy, electronics, and aerospace for producing high-quality graphite products like electrodes and crucibles.
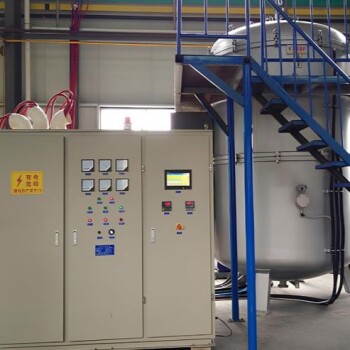
Large Vertical Graphite Vacuum Graphitization Furnace
A large vertical high-temperature graphitization furnace is a type of industrial furnace used for the graphitization of carbon materials, such as carbon fiber and carbon black. It is a high-temperature furnace that can reach temperatures of up to 3100°C.
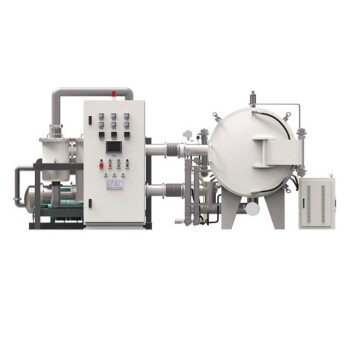
Horizontal High Temperature Graphite Vacuum Graphitization Furnace
Horizontal Graphitization Furnace: This type of furnace is designed with the heating elements placed horizontally, allowing for uniform heating of the sample. It's well-suited for graphitizing large or bulky samples that require precise temperature control and uniformity.
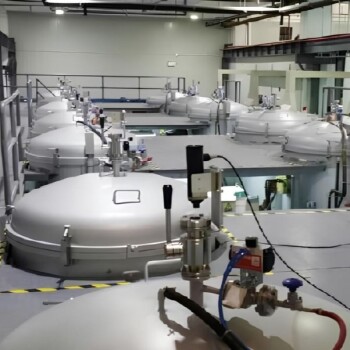
Graphite Vacuum Furnace High Thermal Conductivity Film Graphitization Furnace
The high thermal conductivity film graphitization furnace has uniform temperature, low energy consumption and can operate continuously.

Graphite Vacuum Furnace Bottom Discharge Graphitization Furnace for Carbon Materials
Bottom-out graphitization furnace for carbon materials, ultra-high temperature furnace up to 3100°C, suitable for graphitization and sintering of carbon rods and carbon blocks. Vertical design, bottom discharging, convenient feeding and discharging, high temperature uniformity, low energy consumption, good stability, hydraulic lifting system, convenient loading and unloading.
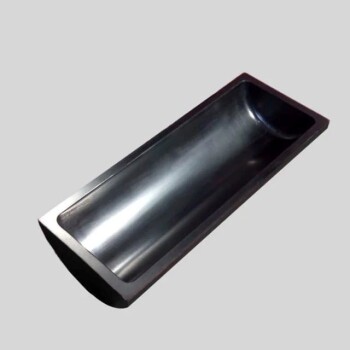
Carbon Graphite Boat -Laboratory Tube Furnace with Cover
Covered Carbon Graphite Boat Laboratory Tube Furnaces are specialized vessels or vessels made of graphite material designed to withstand extreme high temperatures and chemically aggressive environments.
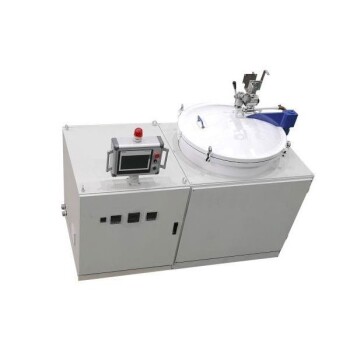
Graphite Vacuum Furnace IGBT Experimental Graphitization Furnace
IGBT experimental graphitization furnace, a tailored solution for universities and research institutions, with high heating efficiency, user-friendliness, and precise temperature control.
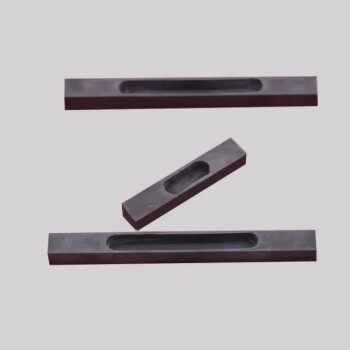
High Purity Pure Graphite Crucible for Evaporation
Vessels for high temperature applications, where materials are kept at extremely high temperatures to evaporate, allowing thin films to be deposited on substrates.
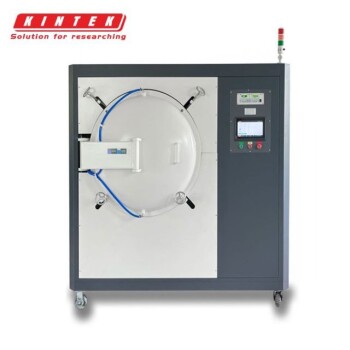
Vacuum Heat Treat Furnace with Ceramic Fiber Liner
Vacuum furnace with polycrystalline ceramic fiber insulation liner for excellent heat insulation and uniform temperature field. Choose from 1200℃ or 1700℃ max. working temperature with high vacuum performance and precise temperature control.
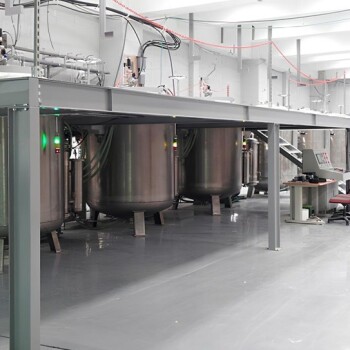
Graphite Vacuum Furnace Negative Material Graphitization Furnace
Graphitization furnace for battery production has uniform temperature and low energy consumption. Graphitization furnace for negative electrode materials: an efficient graphitization solution for battery production and advanced functions to enhance battery performance.
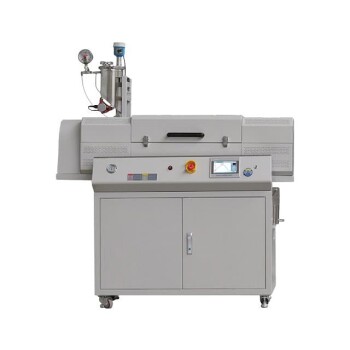
Laboratory Vacuum Tilt Rotary Tube Furnace Rotating Tube Furnace
Discover the versatility of Laboratory Rotary Furnace: Ideal for calcination, drying, sintering, and high-temperature reactions. Adjustable rotating and tilting functions for optimal heating. Suitable for vacuum and controlled atmosphere environments. Learn more now!
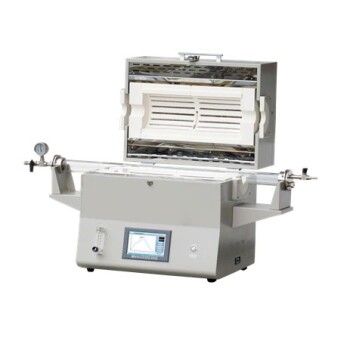
1400℃ Laboratory Quartz Tube Furnace with Alumina Tube Tubular Furnace
Looking for a tube furnace for high-temperature applications? Our 1400℃ Tube Furnace with Alumina Tube is perfect for research and industrial use.
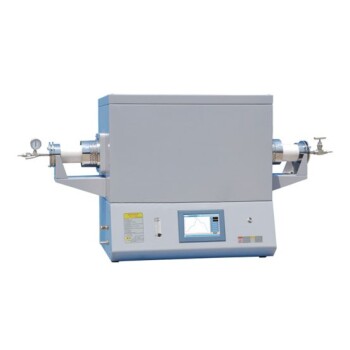
1700℃ Laboratory Quartz Tube Furnace with Alumina Tube Tubular Furnace
Looking for a high-temperature tube furnace? Check out our 1700℃ Tube Furnace with Alumina Tube. Perfect for research and industrial applications up to 1700C.
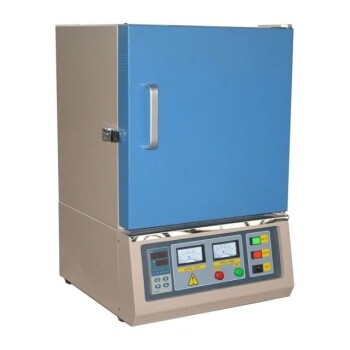
1400℃ Muffle Oven Furnace for Laboratory
Get precise high-temperature control up to 1500℃ with KT-14M Muffle furnace. Equipped with a smart touch screen controller and advanced insulation materials.
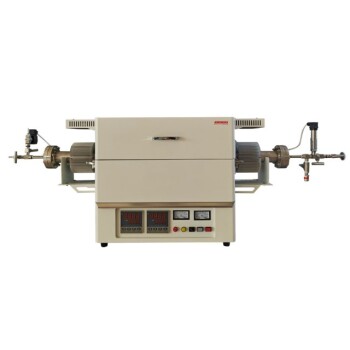
High Pressure Laboratory Vacuum Tube Furnace Quartz Tubular Furnace
KT-PTF High Pressure Tube Furnace: Compact split tube furnace with strong positive pressure resistance. Working temp up to 1100°C and pressure up to 15Mpa. Also works under controller atmosphere or high vacuum.
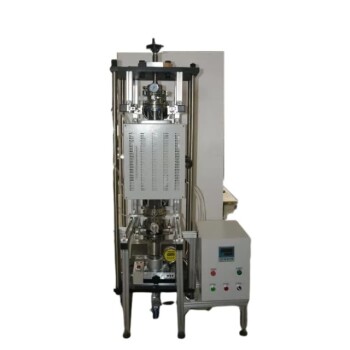
Vacuum Hot Press Furnace Heated Vacuum Press Machine Tube Furnace
Reduce forming pressure & shorten sintering time with Vacuum Tube Hot Press Furnace for high-density, fine-grain materials. Ideal for refractory metals.
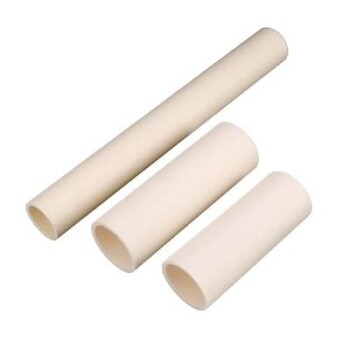
High Temperature Alumina (Al2O3) Furnace Tube for Engineering Advanced Fine Ceramics
High temperature alumina furnace tube combines the advantages of high hardness of alumina, good chemical inertness and steel, and has excellent wear resistance, thermal shock resistance and mechanical shock resistance.
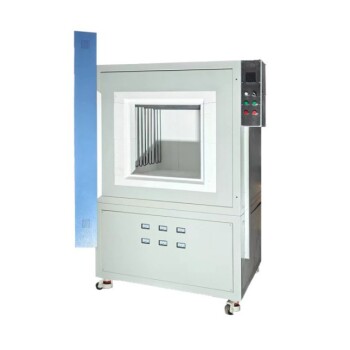
High Temperature Muffle Oven Furnace for Laboratory Debinding and Pre Sintering
KT-MD High temperature debinding and pre-sintering furnace for ceramic materials with various molding processes. Ideal for electronic components such as MLCC and NFC.
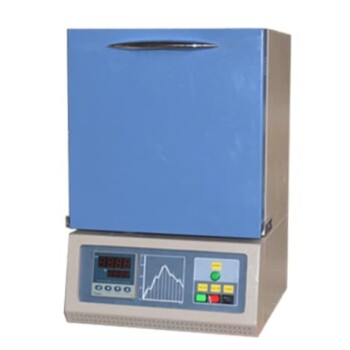
1200℃ Muffle Furnace Oven for Laboratory
Upgrade your lab with our 1200℃ Muffle Furnace. Achieve fast, precise heating with Japan alumina fibers and Molybdenum coils. Features TFT touch screen controller for easy programming and data analysis. Order now!
Related Articles
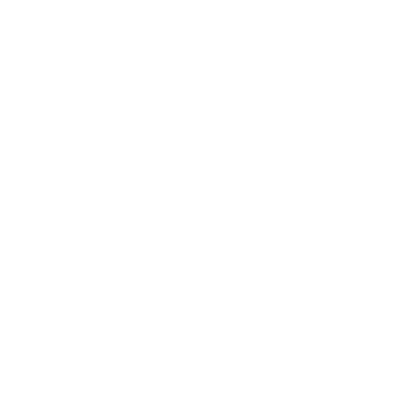
Maximizing Efficiency and Precision with Vacuum Graphite Furnaces
Discover how vacuum graphite furnaces revolutionize high-temperature material treatments with unmatched precision and efficiency. Explore customized solutions for various industries, advanced automation, and sustainable energy practices.
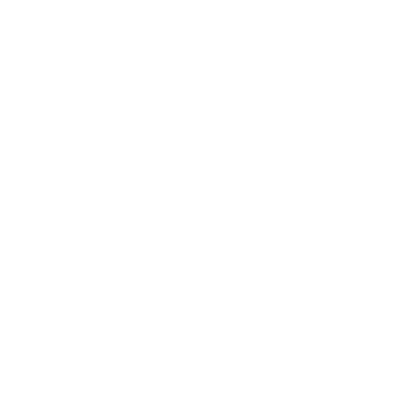
Unveiling Vacuum Graphite Furnaces: Performance, Applications, and Expert Insights
Delve into the world of vacuum graphite furnaces, exploring their exceptional performance, diverse applications, and crucial considerations. Our expert insights empower you to make informed decisions for your laboratory's high-temperature material treatment needs.
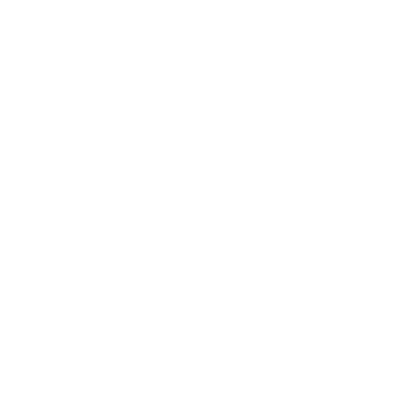
Optimizing Performance with Graphite Vacuum Furnaces: A Comprehensive Guide
Unlock the potential of graphite vacuum furnaces for high-temperature material treatment. Learn about their efficiency, customization options, automation, and key considerations for graphite rod usage.
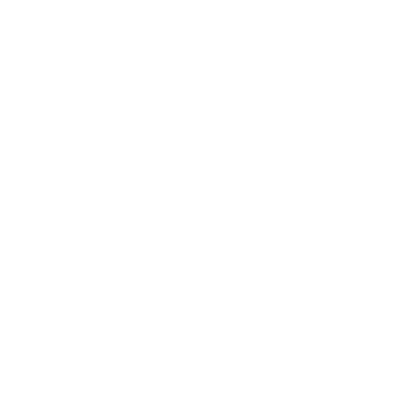
Enhancing Dental Work with a High-Quality Dental Furnace
A dental furnace is a specialized piece of equipment used in dentistry to heat materials to high temperatures. It is typically used to manipulate metal alloys or ceramics, such as those used in crowns, bridges, and other restorative treatments.
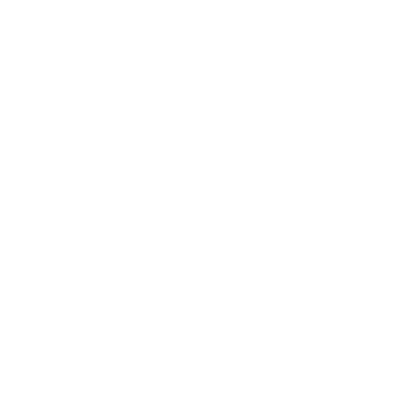
Spark Plasma Sintering Furnace: The Ultimate Guide to SPS Furnaces
Discover the world of Spark Plasma Sintering Furnaces (SPS). This comprehensive guide covers everything from its advantages and applications to its process and equipment. Learn how SPS furnaces can revolutionize your sintering operations.
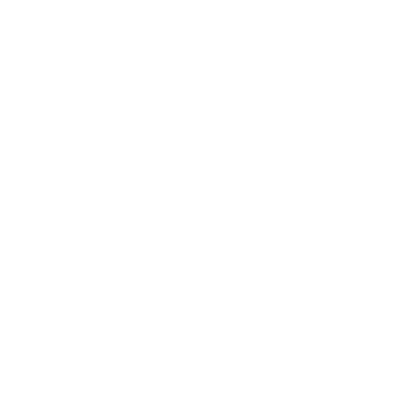
Understanding the Design and Functionality of Industrial Furnaces
Industrial furnaces are heating devices used in various industrial processes, including soldering, heat treatment of steels and alloys, and ceramics sintering.
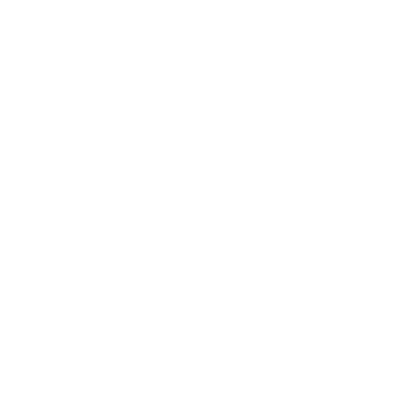
Vacuum Induction Melting Furnace: Principle, Advantages, and Applications
Discover the Vacuum Induction Melting Furnace, a specialized equipment that employs vacuum and induction heating to refine metals and alloys, ensuring high purity and precise composition control. Explore its principle, advantages, applications, and components in this comprehensive guide.
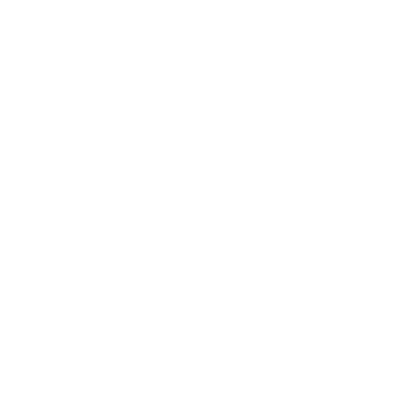
Exploring the Ashing Process and Ashing Furnace: A Comprehensive Guide
the ashing process involves heating a sample in the presence of oxygen to burn off organic compounds and leave behind the inorganic, non-combustible ash.
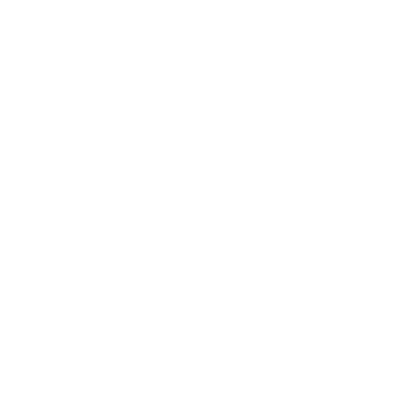
Vacuum Melting Furnace: A Comprehensive Guide to Vacuum Induction Melting
Discover the intricacies of vacuum induction melting furnaces, their components, operation, advantages, and applications. Explore how these furnaces revolutionize metal processing and achieve exceptional material properties.
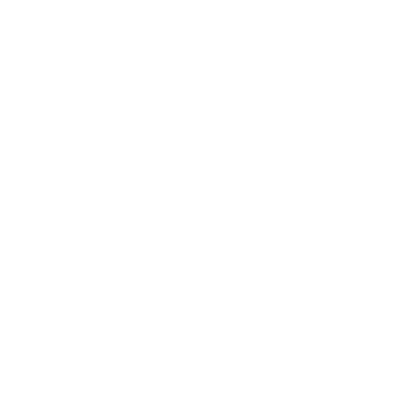
How Biomass Pyrolysis Machines Work A Comprehensive Overview
Biomass pyrolysis machines are designed to convert biomass materials into useful products such as biochar, bio-oil, and syngas.
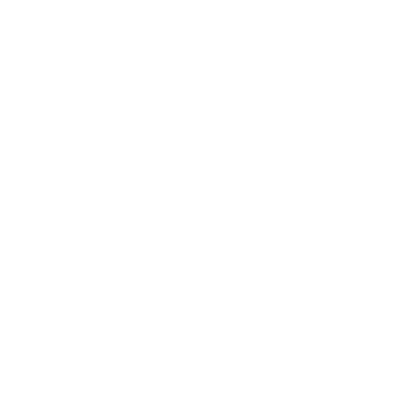
What is activated carbon regeneration Rotary Furnace
Electric activated carbon regeneration furnace is one typical electric external heating rotary furnace
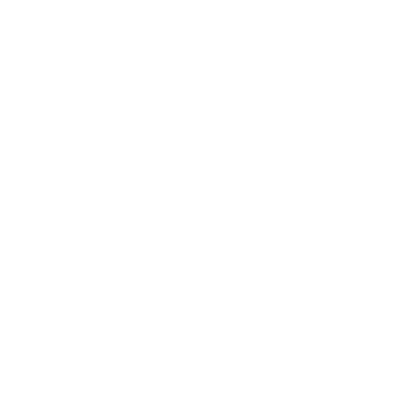
Understanding Electric Heating Systems(1): How Electric Furnaces Work and Their Advantages
Discover how electric heating systems, particularly electric furnaces, work efficiently without the need for flues or chimneys. Explore the benefits and components of electric furnaces, including heating elements, contactors, sequencers, and transformers.