Table of Contents
Introduction to Vacuum Melting Furnaces
Vacuum induction melting furnaces have emerged as a revolutionary technology in metal processing, catering to the unique demands of advanced materials. These furnaces operate under vacuum conditions, enabling precise temperature control, gas removal, and prevention of oxidation, resulting in high-purity and high-performance alloys. Vacuum induction melting furnaces have revolutionized the production of high-quality alloys with exceptional properties, making them indispensable tools in advanced manufacturing and research.
Components of a Vacuum Induction Melting Furnace
A vacuum induction melting furnace is a versatile equipment in metallurgy, capable of melting a wide range of metals and alloys, including superalloys, aluminum, stainless steel, and more. Its operation relies on electromagnetic induction under vacuum conditions, preventing the contamination of molten metals by reactive gases such as oxygen, nitrogen, and hydrogen.
The core components of a vacuum induction melting furnace include:
-
Furnace Body: The furnace body houses the other components and provides a sealed environment for vacuum operation. It is typically constructed from durable materials that can withstand high temperatures and maintain vacuum integrity.
-
Medium Frequency Power Supply: This unit provides the electrical power required to generate the magnetic field for induction heating. It consists of a power source, transformers, and control circuitry to regulate the power output.
-
Vacuum System: The vacuum system is responsible for creating and maintaining the vacuum within the furnace chamber. It comprises a vacuum pump, vacuum gauges, and valves to control the vacuum level. The vacuum pump removes air and other gases from the chamber, achieving the necessary vacuum conditions for melting.
-
Cooling System: The cooling system prevents overheating of the furnace components, particularly the induction coil and crucible. It typically employs a combination of water-cooled channels and fans to dissipate heat effectively.
-
Electric Control System: This system monitors and controls the furnace's operation, including temperature, vacuum level, and power input. It ensures that the furnace operates within safe and efficient parameters.
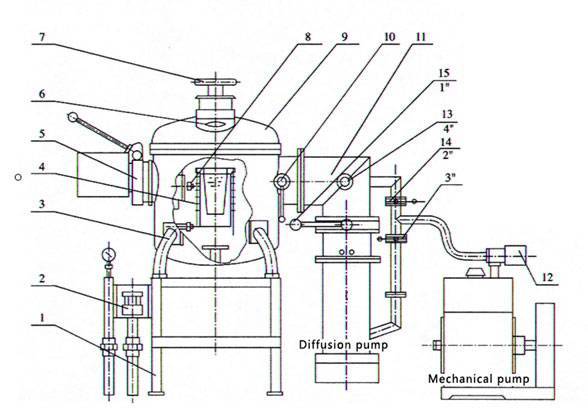
In addition to these essential components, vacuum induction melting furnaces may also be equipped with auxiliary components based on specific process requirements. These may include:
- Transmission trolley for easy movement of the furnace
- Furnace door opening and closing mechanisms
- Centrifugal casting pan for casting molten metal
- Observation window for monitoring the melting process
- Gas filter system for removing impurities in the vacuum environment
The configuration and selection of components in a vacuum induction melting furnace vary depending on the specific application and materials being melted. By carefully considering the requirements of the melting process, it is possible to optimize the furnace's performance and achieve the desired results.
Operation of a Vacuum Induction Melting Furnace
Vacuum induction melting is a specialized melting technique that involves heating and melting metal under vacuum conditions. This process offers several advantages, including the removal of impurities, precise temperature control, and the ability to melt a wide range of metals.
The vacuum induction melting furnace consists of several key components:
- Vacuum chamber: This airtight chamber houses the induction coil and crucible.
- Induction coil: This coil generates electromagnetic fields that induce eddy currents in the metal, causing it to heat and melt.
- Crucible: This container holds the metal during the melting process.
- Vacuum system: This system evacuates the air from the chamber, creating a vacuum.
- Cooling system: This system circulates water through the furnace to prevent overheating.
The operation of a vacuum induction melting furnace involves the following steps:
- Loading the furnace: The metal to be melted is placed into the crucible.
- Evacuating the chamber: The vacuum system is activated to remove the air from the chamber.
- Applying power: Power is applied to the induction coil, generating electromagnetic fields that heat the metal.
- Melting the metal: The metal gradually melts and forms a molten pool.
- Refining the metal: Impurities are removed from the molten metal through chemical reactions, disassociation, flotation, and volatilization.
- Adjusting the chemistry: The composition of the molten metal is adjusted by adding alloying elements or removing impurities.
- Pouring the metal: Once the desired composition and temperature are achieved, the molten metal is poured into a mold or crucible.
Vacuum induction melting is a versatile and efficient melting technique that is used for a wide range of applications, including:
- Production of high-purity metals: Vacuum induction melting can produce metals with extremely low levels of impurities.
- Melting of reactive metals: Metals that are reactive with oxygen or other gases can be melted under vacuum conditions to prevent contamination.
- Production of alloys: Vacuum induction melting can be used to produce alloys with precise compositions and properties.
- Recycling of metals: Vacuum induction melting can be used to recycle metals and remove impurities.
Advantages of Vacuum Induction Melting Furnaces
Vacuum induction melting furnaces (VIM) offer a multitude of advantages, making them an ideal choice for various applications in the metallurgical industry. These furnaces operate under vacuum conditions, allowing for precise control over the melting and solidification processes, resulting in high-quality materials with tailored properties. Let's explore the key advantages of VIM furnaces:
High Purity and Quality
One of the most significant advantages of VIM furnaces is the ability to produce high-purity and high-quality materials. The vacuum environment eliminates the risk of contamination from oxygen, nitrogen, and other gases present in the atmosphere. This results in a cleaner and more homogeneous melt, free from harmful inclusions and impurities that could impact the material's mechanical properties.
Controlled Atmosphere
In the vacuum chamber, the atmosphere is tightly controlled. Only specified gases are introduced at precise pressures. This level of control allows tight control over the chemical composition of the melted material and any reactivity. Unwanted oxidation or reactions with ambient gases are avoided, ensuring the purity and quality of the final product.
Rapid Melting and Cooling
VIM furnaces enable rapid melting and cooling rates due to the absence of air resistance and the use of induction heating. This rapid heating and cooling process results in refined grain structures, improved mechanical properties, and enhanced material homogeneity.
Reduced Energy Consumption
VIM furnaces are highly energy-efficient. The vacuum environment minimizes heat loss through convection and radiation, allowing for more efficient energy utilization. Additionally, the rapid melting and cooling cycles reduce the overall processing time, further reducing energy consumption.
Scalability
VIM furnaces can be designed and scaled to suit different production capacities and requirements. This flexibility makes it suitable for both small-scale research purposes and large-scale industrial production. Small furnaces can be used for laboratory-scale experiments and pilot studies, while larger furnaces can handle high-volume production for commercial applications.
Environmental Benefits
VIM furnaces offer certain environmental benefits. The vacuum environment eliminates the need for fluxing agents, reducing the generation of hazardous waste. Additionally, the absence of air and slag pollution during the melting process contributes to a cleaner and more environmentally friendly operation.
In conclusion, vacuum induction melting furnaces provide numerous advantages for the production of high-quality and pure metals and alloys. The vacuum environment, controlled atmosphere, rapid melting and cooling rates, reduced energy consumption, scalability, and environmental benefits make VIM furnaces a preferred choice in the metallurgical industry.
Applications of Vacuum Induction Melting Furnaces
Vacuum induction melting (VIM) furnaces are versatile tools utilized in diverse industries, including aerospace, medical, and automotive. Their primary function lies in processing specialized alloys, such as superalloys, titanium alloys, and stainless steels, where exceptional material performance is paramount.
Aerospace Industry
VIM furnaces play a crucial role in the aerospace industry, where the production of high-performance components for aircraft, missiles, and satellites demands the use of specialized alloys. These furnaces enable the precise melting and casting of superalloys and high-strength steels, many of which require vacuum processing due to the presence of reactive elements like titanium, niobium, and aluminum.
Medical Industry
In the medical field, VIM furnaces are employed to produce high-quality implants and surgical instruments. The ability to precisely control the melting process ensures the production of alloys with optimal purity and mechanical properties, which are essential for ensuring the safety and effectiveness of medical devices.
Automotive Industry
The automotive industry utilizes VIM furnaces to manufacture high-performance components such as gears, bearings, and engine parts. These furnaces facilitate the production of alloys with enhanced hardness, wear resistance, and fatigue strength, which are crucial for the durability and reliability of automotive components.
Other Applications
Beyond these primary industries, VIM furnaces also find applications in the nuclear industry for melting and casting low-enriched uranium metal into fuel rods. Additionally, they are used in the production of metals such as titanium and aluminum.
Advantages of VIM Furnaces
The use of VIM furnaces offers several advantages over traditional melting techniques:
- Precise temperature control: VIM furnaces allow for precise temperature control, which is essential for melting and casting alloys with specific properties.
- Vacuum environment: The vacuum environment prevents contamination of the molten metal and ensures the production of high-purity alloys.
- Improved material properties: The combination of precise temperature control and vacuum environment results in alloys with enhanced mechanical properties, such as strength, toughness, and corrosion resistance.
- Energy efficiency: VIM furnaces operate at lower temperatures and pressures compared to traditional melting techniques, leading to energy savings.
Conclusion
Vacuum induction melting furnaces are indispensable tools in various industries, enabling the production of high-performance alloys with exceptional material properties. Their versatility and ability to precisely control the melting process make them ideal for applications where quality and reliability are paramount.
Conclusion
Vacuum induction melting furnaces have transformed metal processing, enabling the production of high-purity alloys with exceptional properties. Their ability to control vacuum conditions, prevent contamination, and achieve precise temperature regulation makes them indispensable tools in advanced manufacturing and research. By unlocking the potential of specialized materials, vacuum melting furnaces continue to drive innovation and push the boundaries of material science.
CONTACT US FOR A FREE CONSULTATION
KINTEK LAB SOLUTION's products and services have been recognized by customers around the world. Our staff will be happy to assist with any inquiry you might have. Contact us for a free consultation and talk to a product specialist to find the most suitable solution for your application needs!