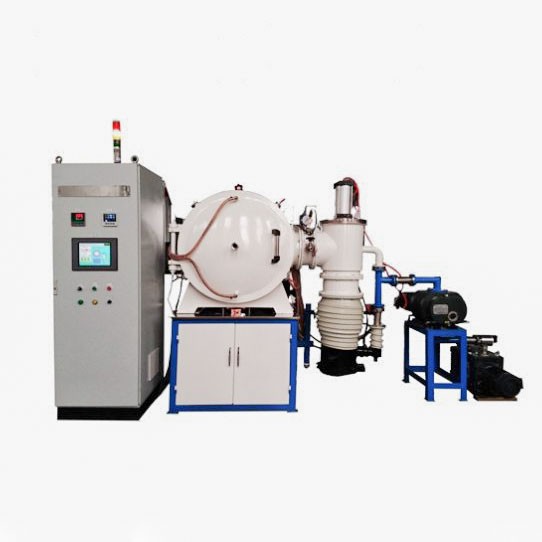
Vacuum Furnace
2200 ℃ Graphite Vacuum Heat Treat Furnace
Item Number : KT-VG
Price varies based on specs and customizations
- Max. temperature
- 2200 ℃
- Constant work temperature
- 2100 ℃
- Heating rate
- 0-10 ℃/min
- Effective volume
- 12-150 L
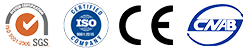
Shipping:
Contact us to get shipping details Enjoy On-time Dispatch Guarantee.
Why Choose Us
Reliable PartnerEasy ordering process, quality products, and dedicated support for your business success.
Introduction
The 2200℃ Graphite Vacuum Furnace is a high-temperature furnace that utilizes graphite felt as its thermal insulation material and graphite resistant rods as its heating element. It can reach a maximum working temperature of up to 2200℃, making it ideal for vacuum reaction sintering of various materials such as tungsten alloy, silicon carbide, molybdenum alloy, titanium alloy, cemented carbide, and carbon materials.
The furnace features a high vacuum performance, with a maximum vacuum level of up to 6*10-3Pa, and no high-temperature gassing. It also has an excellent vacuum pressure maintaining performance, with a 0.67Pa/h vacuum pressure rise rate.
The furnace's safety features include overcurrent protection and over-temperature alarming function, with automatic power-off. It also has a built-in thermal couple detecting function, with automatic heating stoppage and alarm in case of breakage or failure detection.
Applications
The KT-VG Graphite vacuum furnace is an exceptional high-temperature furnace that is widely used in various industries for high-temperature treatment of materials in a vacuum or protective atmosphere environment. Here are some of its main application areas:
- Vacuum reaction sintering of various materials such as tungsten alloy, silicon carbide, molybdenum alloy, titanium alloy, cemented carbide, and carbon materials
- High-temperature brazing and soldering
- Annealing and heat treatment of metals and alloys
- Debinding and sintering of ceramic materials
- Crystal growth
- Vacuum coating and deposition
- Research and development of new materials
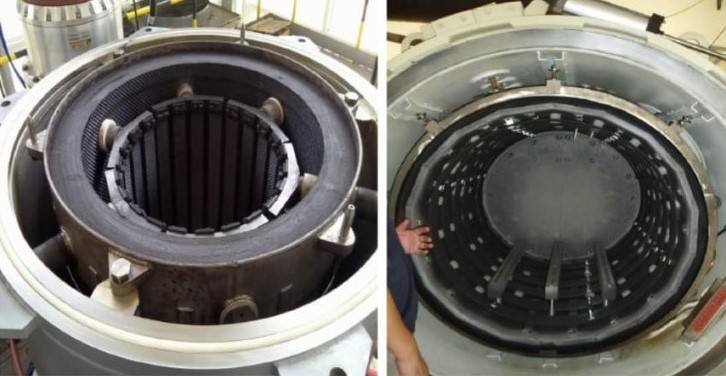
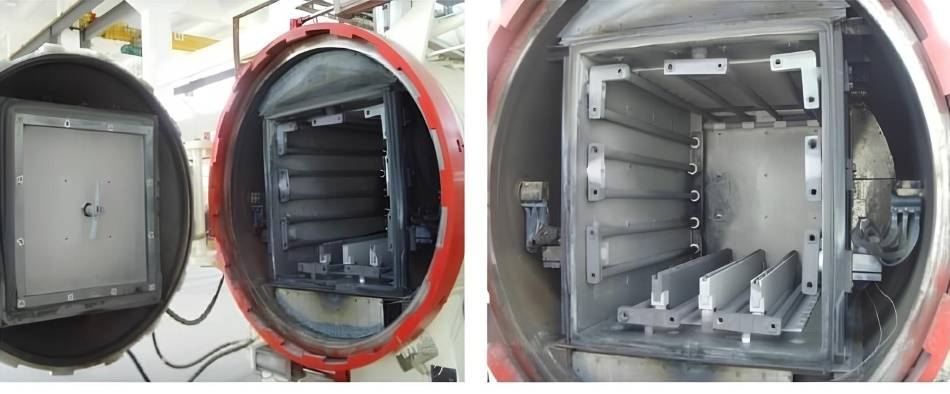
Features
The Vacuum Graphite Furnace Horizontal Type is a high-performance furnace ideal for vacuum and controlled atmosphere sintering applications. With its advanced features and capabilities, this furnace offers numerous benefits to users, including:
- Super high working temperature:** Capable of reaching temperatures up to 2200℃, making it suitable for high-temperature treatment of various materials.
- High vacuum performance:** Achieves a maximum vacuum level of up to 6*10-3Pa, ensuring a clean and controlled environment for material processing.
- Excellent vacuum pressure maintaining performance:** Maintains a stable vacuum environment with a pressure rise rate of only 0.67Pa/h, preventing contamination and ensuring process integrity.
- Vacuum shell body double-layer design:** Features a double-layer jacket for cold water circulation fast cooling, effectively reducing the outer shell surface temperature for improved safety and operator comfort.
- Independent air input and output ports:** Allows for controlled atmosphere working, enabling users to tailor the furnace environment to specific process requirements.
- Optional manual and automatic pneumatic vacuum valves:** Provides flexibility in vacuum control, accommodating different working requirements and automation needs.
- PID programmable microprocessor temperature control system:** Ensures precise temperature control, optimizing process outcomes and reducing product defects.
- Professional heating elements configuration:** Optimized for heat radiation and longevity, maximizing performance and extending service life.
- Safety interlock system:** Powers off the furnace when the door is open or in cases of over-temperature or sensor failure, ensuring operator safety and preventing accidents.
Principle
The 2200 ℃ Graphite Vacuum Furnace utilizes a high-temperature graphite heating element within an insulated graphite chamber. This specialized design allows for precise temperature control and uniform heating distribution. The furnace operates under vacuum conditions, enabling the controlled atmosphere processing of materials at elevated temperatures. The vacuum environment minimizes gas contamination, oxidation, and degassing, ensuring the purity and integrity of the treated materials.
Advantages
- Super high working temperature in vacuum and controlled atmosphere sintering
- High vacuum performance, with a maximum vacuum level of up to 6*10-3Pa, and no high temperature gassing
- Excellent vacuum pressure maintaining performance, with a 0.67Pa/h vacuum pressure rise rate
- Vacuum shell body double-layer design, with a jacket for cold water circulation fast cooling
- Independent air input and output ports, with a controlled atmosphere working function available too
- Optional manual and automatic pneumatic vacuum valves for different working requirements
- PID programmable microprocessor temperature control system, ensuring accurate temperature control
- Professional heating elements configuration to optimize heat radiation properties, and ensure the longest service life
- Safety interlock system, which powers off the furnace when the door is open, or in cases of over-temperature or sensor failure
Safety Advantage
- Overcurrent protection and over-temperature alarming function, with automatic power-off
- Built-in thermal couple detecting function, with automatic heating stoppage and alarm in case of breakage or failure detection
- Power failure restarting function, which resumes the furnace heating program when power is restored after a power failure
Technical specifications
Furnace model | KT-VG | ||
Max. temperature | 2200 ℃ | ||
Constant work temperature | 2100 ℃ | ||
Chamber insulation material | Graphite felt | ||
Heating element | Graphite resistant rod | ||
Heating rate | 0-10℃/min | ||
Temperature sensor | T/R thermocouple and infrared thermometer | ||
Temperature controller | Touch screen PID controller with PLC | ||
Temperature control accuracy | ±1℃ | ||
Electric power supply | AC110-440V,50/60HZ | ||
Standard Chamber Sizes Stocks | |||
Chamber size (mm) | Effective volume (L) | Chamber size (mm) | Effective volume (L) |
200x200x300 | 12 | 400x400x600 | 96 |
300x300x400 | 36 | 500x500x700 | 150 |
Customer design sizes and volume is accepted |
Optional Setup
- Independent furnace temperature monitoring and recording
- RS 485 communication port for PC remote control and data exporting
- Optional pneumatic vacuum valve linkage with temperature controller
- Touch screen temperature controller with versatile operator friendly functions
- Cold water circulation cooling machine for furnace shell jacket cooling system
Warnings
Operator safety is the top important issue! Please operate the equipment with cautions. Working with inflammable& explosive or toxic gases is very dangerous, operators must take all necessary precautions before starting the equipment. Working with positive pressure inside the reactors or chambers is dangerous, operator must fellow the safety procedures strictly. Extra caution must also be taken when operating with air-reactive materials, especially under vacuum. A leak can draw air into the apparatus and cause a violent reaction to occur.
Designed for You
KinTek provide deep custom made service and equipment to worldwide customers, our specialized teamwork and rich experienced engineers are capable to undertake the custom tailoring hardware and software equipment requirements, and help our customer to build up the exclusive and personalized equipment and solution!
Would you please drop your ideas to us, our engineers are ready for you now!
FAQ
What Is A Graphite Vacuum Furnace Used For?
What Are The Main Types Of Graphite Vacuum Furnaces?
How Does A Graphite Vacuum Furnace Work?
What Are The Advantages Of Using A Graphite Vacuum Furnace?
What Temperature Range Can A Graphite Vacuum Furnace Achieve?
What Industries Benefit From Graphite Vacuum Furnaces?
4.6
out of
5
KT-VG Graphite vacuum furnace is a remarkable advanced intelligent heating furnace, with accurate temperature control. It's a great choice for high-temperature treatment of materials.
4.7
out of
5
The graphite-based furnace offers top-notch thermal efficiency, thanks to its graphite wafer. It's lightweight and provides uniform heating, making it an ideal choice for various applications.
4.8
out of
5
The electron microscope pictures clearly showcase the transformation of graphite layers before and after heat treatment. This furnace delivers exceptional results for graphitization processes.
4.9
out of
5
The graphite rod selection is crucial for uniform heating and extended service life. Proper usage and temperature control ensure the longevity of the graphite rod.
4.7
out of
5
Vacuum sintering furnace offers versatility for processing various materials like hard alloys, carbon composites, and photoelectric coating materials. It's a valuable tool for high-temperature sintering.
4.8
out of
5
The choice of heating elements, like graphite, molybdenum, or tungsten, enables precise temperature control and efficient heating in vacuum furnaces.
4.9
out of
5
KT-VG Graphite vacuum furnace excels in vacuum reaction sintering of materials like tungsten alloy, silicon carbide, and molybdenum alloy. Its exceptional temperature control ensures consistent results.
4.6
out of
5
The temperature sensor with a Tungsten rhenium thermocouple and an infrared thermometer enhances temperature accuracy and reliability, ensuring precise control during the heating process.
4.7
out of
5
The vacuum shell body's double-layer design with cold water circulation cooling effectively reduces the outer shell temperature, enhancing safety and user comfort.
4.8
out of
5
The independent air input and output ports allow for a controlled atmosphere working function, expanding the furnace's capabilities and enabling various process conditions.
4.9
out of
5
The PID programmable microprocessor temperature control system ensures accurate and stable temperature regulation, ensuring precise heating and uniform results.
4.6
out of
5
The professional heating elements configuration optimizes heat radiation properties, maximizing energy efficiency and extending the service life of the furnace.
4.7
out of
5
The safety interlock system provides peace of mind, automatically powering off the furnace when the door is open or in cases of over-temperature or sensor failure, ensuring user safety.
4.8
out of
5
The overcurrent protection and over-temperature alarming function, along with automatic power-off, ensure safe operation and prevent potential hazards, enhancing user confidence.
4.9
out of
5
The built-in thermal couple detecting function offers an additional layer of safety by automatically stopping heating and triggering an alarm in case of breakage or failure detection, minimizing downtime and ensuring reliable operation.
4.6
out of
5
The power failure restarting function is a lifesaver! It resumes the heating program upon power restoration, preventing disruptions and ensuring seamless continuation of processes.
4.7
out of
5
The optional setups, such as independent furnace temperature monitoring and RS 485 communication port, provide enhanced control and data management capabilities, making the furnace even more versatile and user-friendly.
4.8
out of
5
The cold water circulation cooling machine for the furnace shell jacket cooling system is a great addition, ensuring effective temperature regulation and extending the lifespan of the furnace.
4.9
out of
5
KT-VG Graphite vacuum furnace is an exceptional choice for high-temperature applications. Its advanced features, safety mechanisms, and optional setups make it a reliable and versatile tool in any laboratory.
Products
2200 ℃ Graphite Vacuum Heat Treat Furnace
REQUEST A QUOTE
Our professional team will reply to you within one business day. Please feel free to contact us!
Related Products
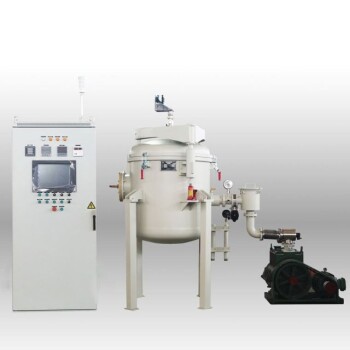
Ultra-High Temperature Graphite Vacuum Graphitization Furnace
The ultra-high temperature graphitization furnace utilizes medium frequency induction heating in a vacuum or inert gas environment. The induction coil generates an alternating magnetic field, inducing eddy currents in the graphite crucible, which heats up and radiates heat to the workpiece, bringing it to the desired temperature. This furnace is primarily used for graphitization and sintering of carbon materials, carbon fiber materials, and other composite materials.
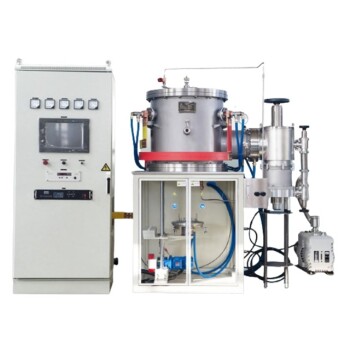
2200 ℃ Tungsten Vacuum Heat Treat and Sintering Furnace
Experience the ultimate refractory metal furnace with our Tungsten vacuum furnace. Capable of reaching 2200℃, perfect for sintering advanced ceramics and refractory metals. Order now for high-quality results.
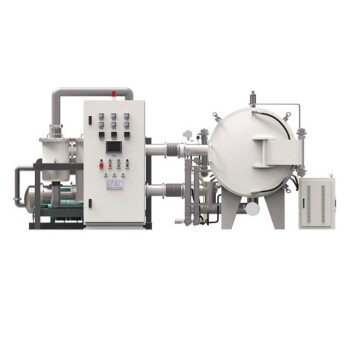
Horizontal High Temperature Graphite Vacuum Graphitization Furnace
Horizontal Graphitization Furnace: This type of furnace is designed with the heating elements placed horizontally, allowing for uniform heating of the sample. It's well-suited for graphitizing large or bulky samples that require precise temperature control and uniformity.
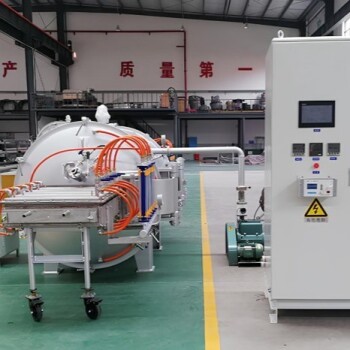
Graphite Vacuum Continuous Graphitization Furnace
High-temperature graphitization furnace is a professional equipment for graphitization treatment of carbon materials. It is a key equipment for the production of high-quality graphite products. It has high temperature, high efficiency and uniform heating. It is suitable for various high-temperature treatments and graphitization treatments. It is widely used in metallurgy, electronics, aerospace, etc. industry.
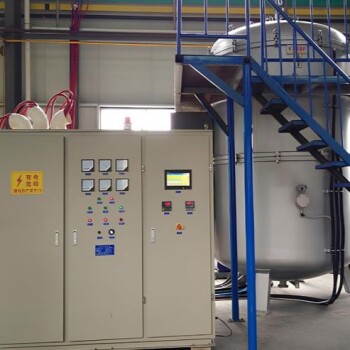
Large Vertical Graphite Vacuum Graphitization Furnace
A large vertical high-temperature graphitization furnace is a type of industrial furnace used for the graphitization of carbon materials, such as carbon fiber and carbon black. It is a high-temperature furnace that can reach temperatures of up to 3100°C.
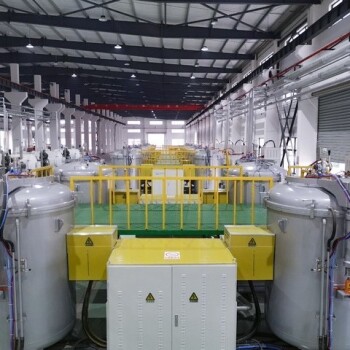
Vertical High Temperature Graphite Vacuum Graphitization Furnace
Vertical high temperature graphitization furnace for carbonization and graphitization of carbon materials up to 3100℃.Suitable for shaped graphitization of carbon fiber filaments and other materials sintered in a carbon environment.Applications in metallurgy, electronics, and aerospace for producing high-quality graphite products like electrodes and crucibles.
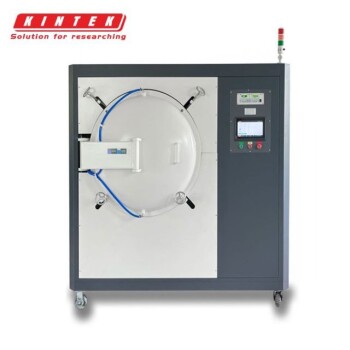
Vacuum Heat Treat Furnace with Ceramic Fiber Liner
Vacuum furnace with polycrystalline ceramic fiber insulation liner for excellent heat insulation and uniform temperature field. Choose from 1200℃ or 1700℃ max. working temperature with high vacuum performance and precise temperature control.
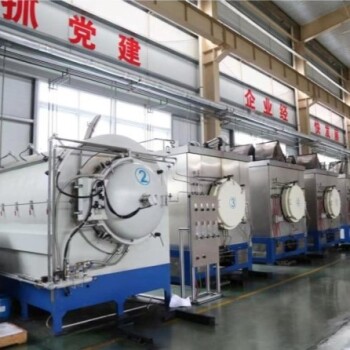
Vacuum Heat Treat Sintering Brazing Furnace
A vacuum brazing furnace is a type of industrial furnace used for brazing, a metalworking process that joins two pieces of metal using a filler metal that melts at a lower temperature than the base metals. Vacuum brazing furnaces are typically used for high-quality applications where a strong, clean joint is required.
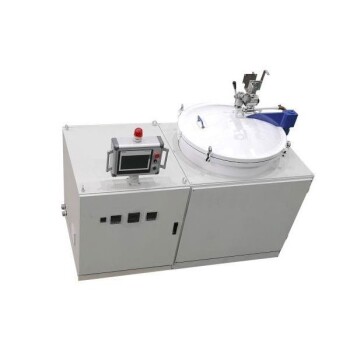
Graphite Vacuum Furnace IGBT Experimental Graphitization Furnace
IGBT experimental graphitization furnace, a tailored solution for universities and research institutions, with high heating efficiency, user-friendliness, and precise temperature control.

Graphite Vacuum Furnace Bottom Discharge Graphitization Furnace for Carbon Materials
Bottom-out graphitization furnace for carbon materials, ultra-high temperature furnace up to 3100°C, suitable for graphitization and sintering of carbon rods and carbon blocks. Vertical design, bottom discharging, convenient feeding and discharging, high temperature uniformity, low energy consumption, good stability, hydraulic lifting system, convenient loading and unloading.
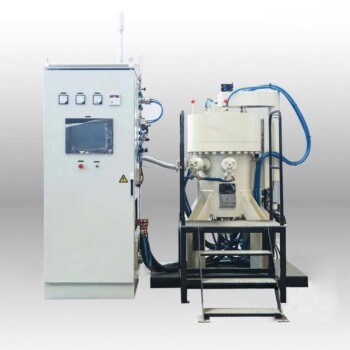
Vacuum Heat Treat and Sintering Furnace with 9MPa Air Pressure
The air pressure sintering furnace is a high-tech equipment commonly used for the sintering of advanced ceramic materials. It combines vacuum sintering and pressure sintering techniques to achieve high-density and high-strength ceramics.
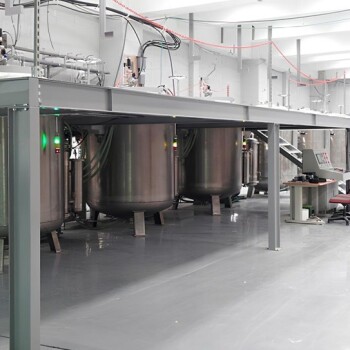
Graphite Vacuum Furnace Negative Material Graphitization Furnace
Graphitization furnace for battery production has uniform temperature and low energy consumption. Graphitization furnace for negative electrode materials: an efficient graphitization solution for battery production and advanced functions to enhance battery performance.
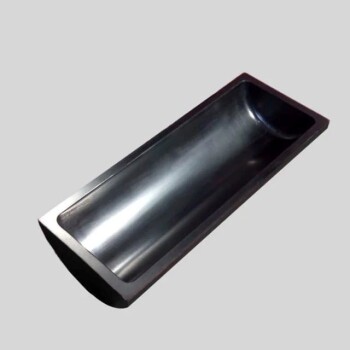
Carbon Graphite Boat -Laboratory Tube Furnace with Cover
Covered Carbon Graphite Boat Laboratory Tube Furnaces are specialized vessels or vessels made of graphite material designed to withstand extreme high temperatures and chemically aggressive environments.
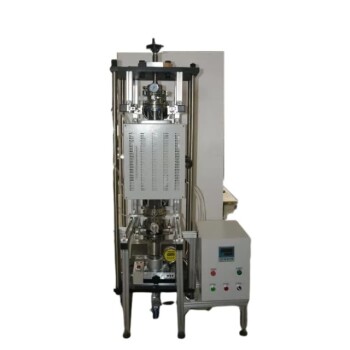
Vacuum Hot Press Furnace Heated Vacuum Press Machine Tube Furnace
Reduce forming pressure & shorten sintering time with Vacuum Tube Hot Press Furnace for high-density, fine-grain materials. Ideal for refractory metals.
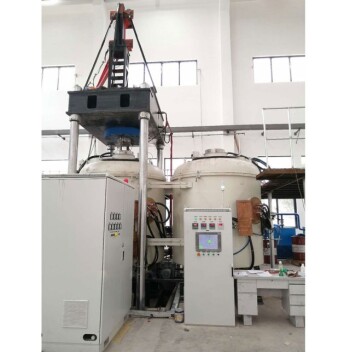
600T Vacuum Induction Hot Press Furnace for Heat Treat and Sintering
Discover the 600T Vacuum Induction Hot Press Furnace, designed for high-temperature sintering experiments in vacuum or protected atmospheres. Its precise temperature and pressure control, adjustable working pressure, and advanced safety features make it ideal for nonmetal materials, carbon composites, ceramics, and metal powders.
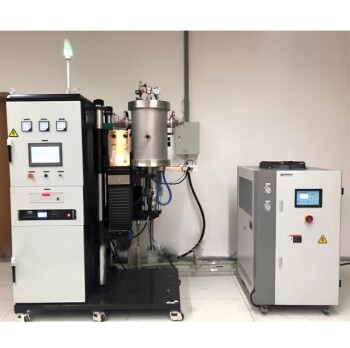
Vacuum Heat Treat and Molybdenum Wire Sintering Furnace for Vacuum Sintering
A vacuum molybdenum wire sintering furnace is a vertical or bedroom structure, which is suitable for withdrawal, brazing, sintering and degassing of metal materials under high vacuum and high temperature conditions. It is also suitable for dehydroxylation treatment of quartz materials.
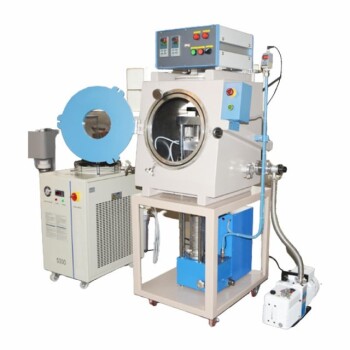
Vacuum Hot Press Furnace Machine for Lamination and Heating
Experience clean and precise lamination with Vacuum Lamination Press. Perfect for wafer bonding, thin-film transformations, and LCP lamination. Order now!
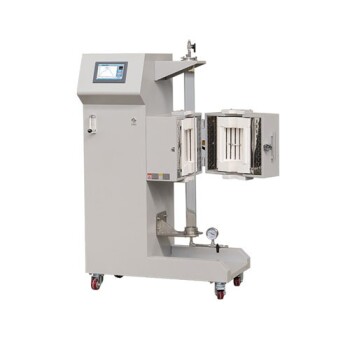
Vertical Laboratory Quartz Tube Furnace Tubular Furnace
Elevate your experiments with our Vertical Tube Furnace. Versatile design allows for operation under various environments and heat treatment applications. Order now for precise results!
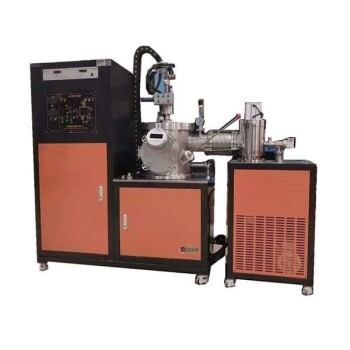
Vacuum Arc Induction Melting Furnace
Discover the power of Vacuum Arc Furnace for melting active & refractory metals. High-speed, remarkable degassing effect, and free of contamination. Learn more now!
Related Articles
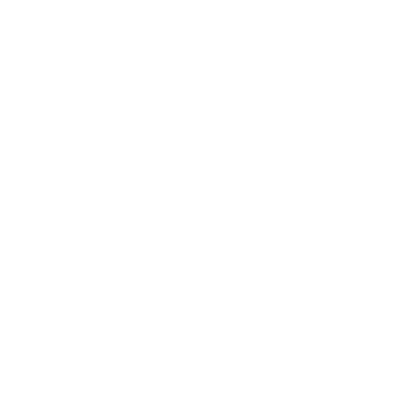
How to Choose Crucible Materials That Prevent Chemical Degradation in Vacuum Induction Melting
Learn how to choose crucible materials for vacuum induction melting to prevent chemical degradation and optimize alloy purity. Essential guide for industrial applications.
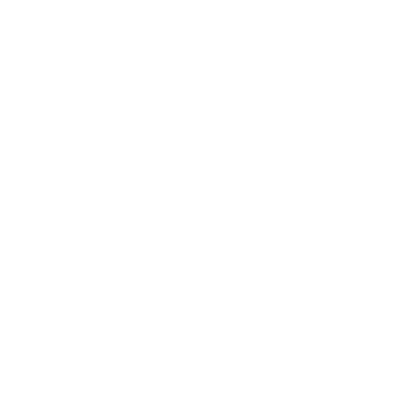
How Vacuum Induction Melting Prevents Catastrophic Material Failures in Critical Components
Discover how Vacuum Induction Melting (VIM) prevents material failures in aerospace, nuclear, and EV components by eliminating atomic-level contamination.
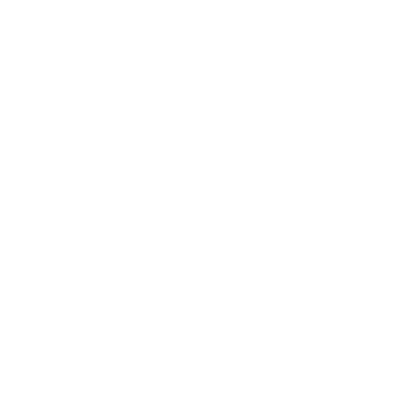
How Vacuum Induction Melting Elevates High-Performance Alloy Production
Discover how Vacuum Induction Melting (VIM) enhances alloy purity, reduces defects, and optimizes costs for aerospace and energy sectors.
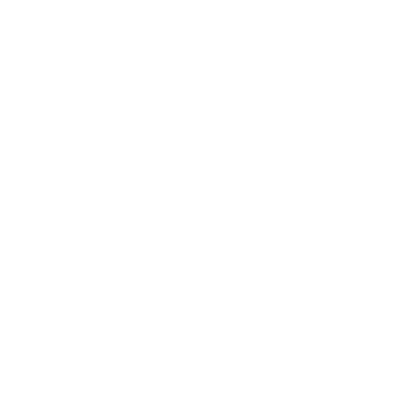
How Vacuum Induction Melting Powers Superior Material Performance in Critical Industries
Discover how Vacuum Induction Melting (VIM) ensures 99.99% pure alloys for aerospace and medical industries, boosting performance and compliance.
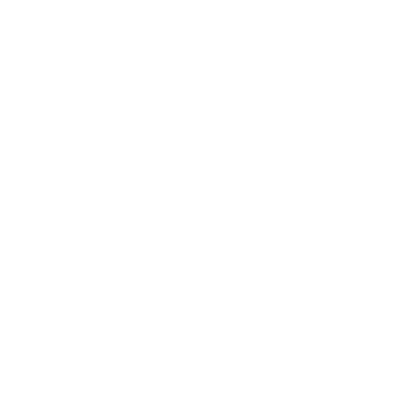
How Vacuum Induction Melting Outperforms Traditional Methods in Advanced Alloy Production
Discover how vacuum induction melting (VIM) outperforms traditional methods in advanced alloy production, offering precision, purity, and cost savings.
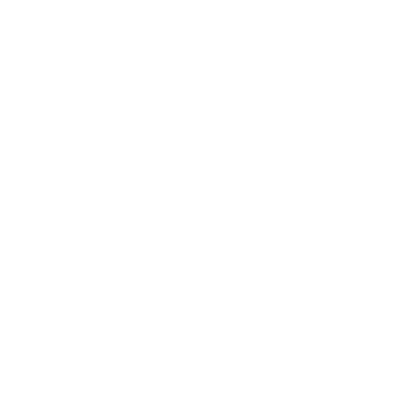
How Vacuum Induction Melting (VIM) Transforms High-Performance Alloy Production
Discover how Vacuum Induction Melting (VIM) enhances alloy purity for aerospace, medical, and nuclear industries, reducing defects and costs.
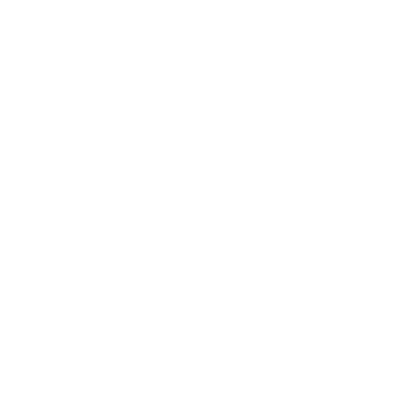
How Vacuum Induction Melting Ensures Unmatched Reliability in Critical Industries
Vacuum induction melting (VIM) ensures metallurgical purity, durability, and efficiency in aerospace, nuclear, and critical industries. Learn why VIM outperforms traditional methods.
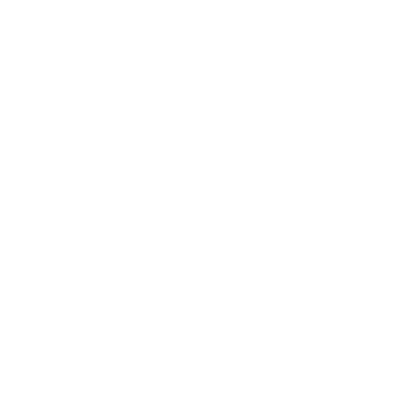
Optimizing Performance with Graphite Vacuum Furnaces: A Comprehensive Guide
Unlock the potential of graphite vacuum furnaces for high-temperature material treatment. Learn about their efficiency, customization options, automation, and key considerations for graphite rod usage.
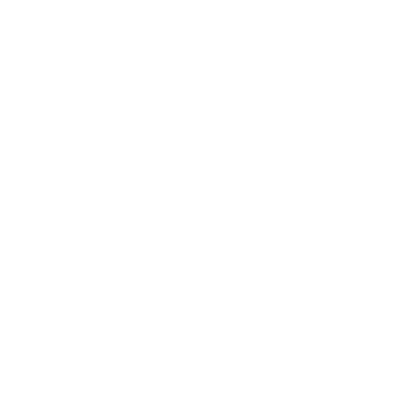
Maximizing Efficiency and Precision with Vacuum Graphite Furnaces
Discover how vacuum graphite furnaces revolutionize high-temperature material treatments with unmatched precision and efficiency. Explore customized solutions for various industries, advanced automation, and sustainable energy practices.
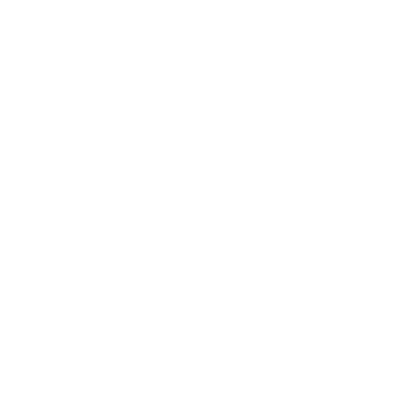
Unveiling Vacuum Graphite Furnaces: Performance, Applications, and Expert Insights
Delve into the world of vacuum graphite furnaces, exploring their exceptional performance, diverse applications, and crucial considerations. Our expert insights empower you to make informed decisions for your laboratory's high-temperature material treatment needs.
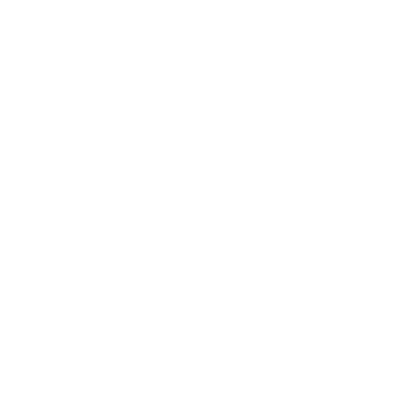
Comprehensive Guide to Vacuum Hot Press Furnace Application
The Vacuum Hot Press Furnace is a versatile tool especially suited for sintering experiments involving non-metallic materials, carbon composites, ceramic materials and metal powder materials.
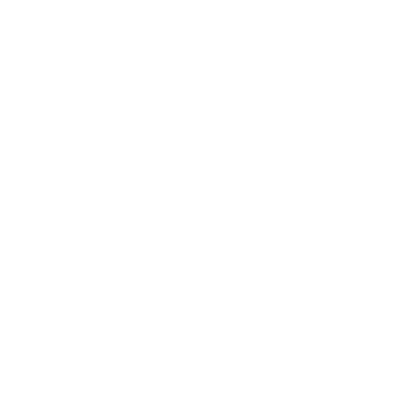
Molybdenum Vacuum Furnace: High-Temperature Sintering and Heat Treatment
Explore the advanced features and applications of molybdenum vacuum furnaces in high-temperature sintering and heat treatment. Learn about their construction, control systems, and maintenance tips.