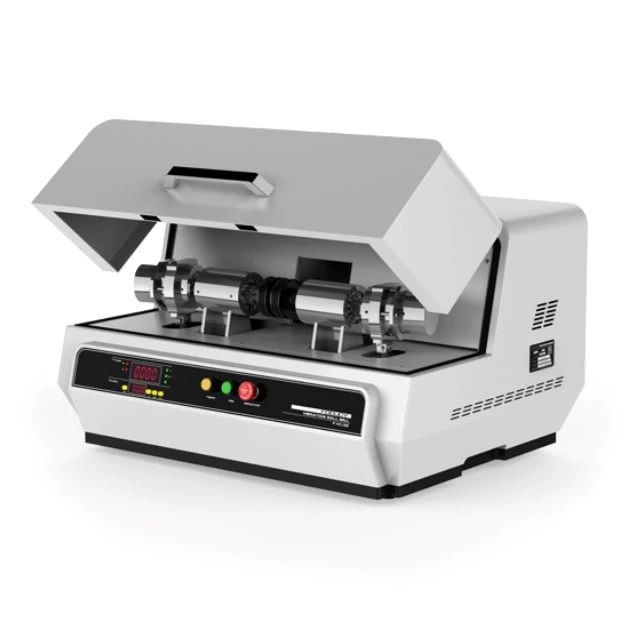
Milling Equipment
High Energy Vibratory Laboratory Ball Mill Double Tank Type
Item Number : KT-VB200
Price varies based on specs and customizations
- Maximum injection size
- < 1 mm
- Sample particle size range
- 0.1-20um
- Maximum processing volume
- 160ml
- Sample minimum throughput
- 1g
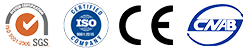
Shipping:
Contact us to get shipping details Enjoy On-time Dispatch Guarantee.
Why Choose Us
Reliable PartnerEasy ordering process, quality products, and dedicated support for your business success.
Introduction
High-energy vibration ball mill is a small desktop laboratory grinding instrument. It uses 1700r/min high-frequency three-dimensional vibration to make the sample achieve the result of grinding or mixing. It is used with two ball mill jars with a volume of 50ml or 80ml, and the minimum processing capacity 1g, it is used to test the processing of a small amount or a small amount of samples. The processing efficiency of the K-VB200 high-energy vibration ball mill is 3-5 times that of the planetary ball mill. It can be ball-milled or mixed with different particle sizes and materials by dry and wet methods. All kinds of solids, suspensions and pastes can also be equipped with a vacuum ball mill tank to achieve vacuum or inert gas protection grinding.
- Processing principle: impact force | friction force
- Application sample characteristics: fine | medium-low hardness | brittle | dry or low viscosity
- Processing Type: Grinding | Blending
- Main functions: combination lock | continuous and intermittent operation | emergency stop | intermittent timer | run timer | memory | overload protection | heat dissipation | windows
Applications
The High Energy Vibratory Ball Mill (Double Tank Type) is a versatile and powerful tool used in various industries for grinding, mixing, and mechanical alloying. This equipment is particularly effective for processing hard and brittle materials, as well as for achieving ultra-fine particle sizes. Here are the main application areas of this product:
- Materials Science: Used for mechanical alloying and synthesis of advanced materials, including metals, alloys, and ceramics.
- Pharmaceuticals: Essential for the grinding and homogenization of pharmaceutical ingredients to ensure consistent particle size and quality.
- Electronics: Involved in the preparation of fine powders used in the production of electronic components, such as ceramics and magnetic materials.
- Chemical Industry: Employed for the fine grinding of various chemicals, aiding in the production of high-quality chemical products.
- Environmental Remediation: Useful in the processing of materials for environmental applications, such as the stabilization of hazardous waste.
- Food and Beverage: Can be used for the grinding of food ingredients to achieve desired textures and consistencies.
- Research and Development: Widely used in laboratories for R&D purposes, particularly in the development of new materials and formulations.
Features
The High Energy Vibratory Ball Mill (Double Tank Type) is a cutting-edge laboratory equipment designed for efficient and rapid grinding of hard and brittle materials. This mill stands out for its ability to produce ultra-fine particles quickly, making it an essential tool for various industries including electronics, ceramics, and pharmaceuticals. The double tank design enhances its capacity and versatility, allowing for simultaneous or sequential processing of different materials. Here are the key features that make this ball mill a standout choice for high-energy grinding needs:
- Special Gear Design for Low Noise and Vibration: This feature ensures a quieter operation and minimal disturbance, making it suitable for use in laboratory environments where noise control is crucial.
- LCD Control Panel: Provides intuitive and precise control over the milling process, allowing users to easily set and monitor parameters such as speed and duration.
- Safety Mechanism: Ensures the safe operation of the mill, protecting both the user and the equipment from potential hazards during the grinding process.
- Stable Rotation Speed: Maintains consistent milling performance, which is critical for achieving uniform particle size and quality in the final product.
- Reliable Heavy-Duty Design: Built to withstand the rigors of continuous high-energy grinding, ensuring durability and long-term reliability.
- Programmable Milling Segment: Allows for customized grinding cycles, optimizing the milling process for specific materials and desired outcomes.
- Customized Power Supply: Adaptable to various power configurations (110V, 220V, or 380V), making it suitable for international use and compatible with different power grids.
These features not only enhance the functionality and efficiency of the High Energy Vibratory Ball Mill but also ensure safety, reliability, and ease of use, making it an indispensable tool in modern laboratories.
Detail & Parts
Advantages
The High Energy Vibratory Ball Mill (Double Tank Type) offers a multitude of advantages that make it a superior choice for grinding and material processing. Here are the key benefits:
- High Processing Capacity: With a filling capacity of up to 80% for the grinding medium, this mill outperforms others in terms of processing volume, making it ideal for high-throughput applications.
- Versatile Grinding Options: The mill's simple yet robust structure allows for adjustments in amplitude, frequency, and media ratios, enabling the production of various particle sizes to meet specific requirements.
- Temperature Control: Equipped with jacketed grinding cylinders, the mill can regulate the grinding temperature, which is crucial for maintaining the integrity of heat-sensitive materials.
- Continuous Production Capability: Integrated with sieves and collection devices, the mill supports continuous operation, enhancing productivity and efficiency in industrial settings.
- User-Friendly Operation: The design prioritizes ease of use with reliable performance, easy cleaning, and adaptability to different working conditions, ensuring minimal downtime and maintenance.
- Dual Milling Capabilities: Supports both dry and wet ball milling, providing flexibility in processing different types of materials without the need for additional equipment.
- Compact and Efficient: Despite its powerful performance, the mill is lightweight and compact, saving space while delivering high efficiency and output.
- Customizable Solutions: The ability to customize the tank lining with materials like stainless steel, ceramic, zirconia, and more, allows for specialized applications, including those in pharmaceuticals and electronics.
These advantages collectively position the High Energy Vibratory Ball Mill (Double Tank Type) as a cutting-edge solution for laboratories and industries requiring precision grinding and efficient material processing.
Technical specifications
Maximum injection size | < 1 mm |
Sample particle size range | 0.1-20um |
Maximum processing volume | 160ml |
Sample minimum throughput | 1g |
Ball milling tank speed | 1700r/min |
Movement mode of ball mill jar | High-frequency three-dimensional motion |
Ball mill material | Tungsten carbide | Zirconia | Stainless steel optional |
Number of ball mill jars | 2 |
Ball mill tank volume | 25ml / 50ml / 80ml optional |
Grinding ball material | Tungsten carbide | Zirconia | Stainless steel optional |
Grinding method | Dry Grinding | Wet Grinding | Vacuum Grinding |
Electrical description | 220V AC, 50-60Hz, 500W |
Power port | National Standard | European Standard | American Standard | British Standard, etc. |
Net weight | 68kg |
Dimensions (L*W*H) | 620*320*268mm |
Protection class | IP65 |
Standard: | CE |
Warnings
Operator safety is the top important issue! Please operate the equipment with cautions. Working with inflammable& explosive or toxic gases is very dangerous, operators must take all necessary precautions before starting the equipment. Working with positive pressure inside the reactors or chambers is dangerous, operator must fellow the safety procedures strictly. Extra caution must also be taken when operating with air-reactive materials, especially under vacuum. A leak can draw air into the apparatus and cause a violent reaction to occur.
Designed for You
KinTek provide deep custom made service and equipment to worldwide customers, our specialized teamwork and rich experienced engineers are capable to undertake the custom tailoring hardware and software equipment requirements, and help our customer to build up the exclusive and personalized equipment and solution!
Would you please drop your ideas to us, our engineers are ready for you now!
FAQ
What Is A Laboratory Ball Mill?
What Are The Applications Of A Laboratory Ball Mill?
What Are The Main Types Of Laboratory Ball Mills?
What Is The Working Principle Of A Laboratory Ball Mill?
What Are The Advantages Of Using A Laboratory Ball Mill?
What Materials Can Be Processed Using A Laboratory Ball Mill?
What Are The Key Features Of A High-energy Planetary Ball Mill?
What Is The Difference Between A Planetary Ball Mill And A Vibratory Ball Mill?
4.7
out of
5
The high energy vibratory ball mill is a game-changer in our lab. It's incredibly efficient and versatile, allowing us to grind and mix various materials with ease.
4.8
out of
5
This ball mill is a lifesaver! It has significantly reduced our processing time and improved the quality of our samples.
4.9
out of
5
The programmable milling segment feature is a godsend. It allows us to customize the grinding process and achieve consistent results.
4.6
out of
5
The safety mechanisms on this ball mill give me peace of mind. I know my team is safe when operating it.
4.7
out of
5
The customized power supply option is a huge plus. We were able to choose the voltage that best suited our lab's needs.
4.8
out of
5
The LCD control panel makes operating the ball mill a breeze. It's user-friendly and provides all the necessary information at a glance.
4.9
out of
5
The stable rotation speed ensures consistent particle size reduction, which is crucial for our research.
4.6
out of
5
The low noise and vibration levels make this ball mill a pleasure to work with. It doesn't disrupt our other lab activities.
4.7
out of
5
The reliable heavy-duty design gives me confidence in the longevity of this ball mill. It's built to last.
4.8
out of
5
The ability to perform milling either wet or dry expands the range of materials we can process.
4.9
out of
5
The different milling jar options allow us to optimize the grinding process for various sample sizes and materials.
4.6
out of
5
The high-speed and versatile nature of this ball mill make it a valuable addition to our lab's equipment.
4.7
out of
5
The processing efficiency of this ball mill is truly remarkable. It saves us time and resources.
4.8
out of
5
The combination lock feature ensures the safety of our samples during processing.
Products
High Energy Vibratory Laboratory Ball Mill Double Tank Type
REQUEST A QUOTE
Our professional team will reply to you within one business day. Please feel free to contact us!
Related Products
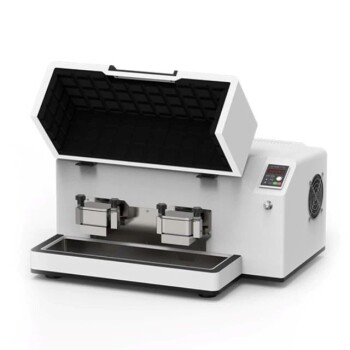
High Energy Vibratory Ball Mill for Lab Use
The high-energy vibrating ball mill is a high-energy oscillating and impacting multifunctional laboratory ball mill. The table-top type is easy to operate, small in size, comfortable and safe.
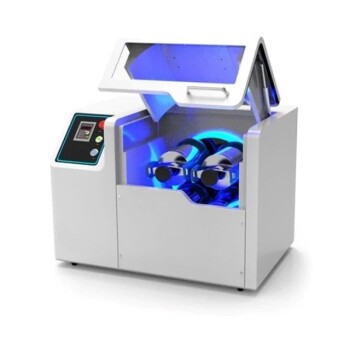
High Energy Planetary Ball Mill Machine for Laboratory Horizontal Tank Type
The KT-P2000H uses a unique Y-axis planetary trajectory, and utilizes the collision, friction and gravity between the sample and the grinding ball.
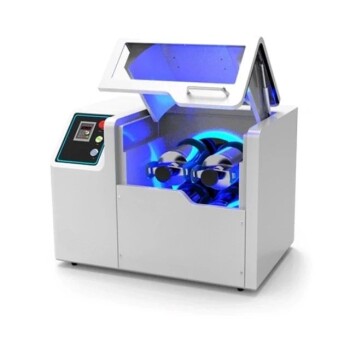
High Energy Planetary Ball Mill for Laboratory Horizontal Tank Type Milling Machine
KT-P4000H uses the unique Y-axis planetary motion trajectory, and utilizes the collision, friction and gravity between the sample and the grinding ball to have a certain anti-sinking ability, which can obtain better grinding or mixing effects and further improve the sample output.
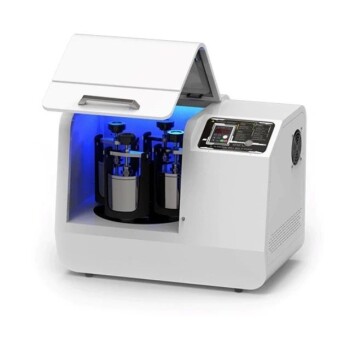
High Energy Planetary Ball Mill Milling Machine for Laboratory
The biggest feature is that the high energy planetary ball mill can not only perform fast and effective grinding, but also has good crushing ability
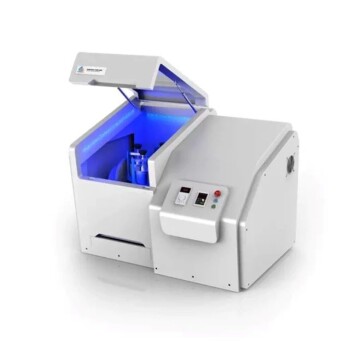
High-Energy Omnidirectional Planetary Ball Mill Machine for Laboratory
The KT-P2000E is a new product derived from the vertical high-energy planetary ball mill with a 360°rotation function. The product not only has the characteristics of the vertical high-energy ball mill, but also has a unique 360°rotation function for the planetary body.
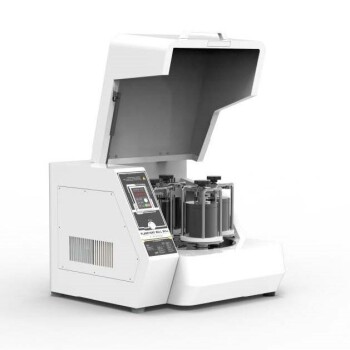
High Energy Planetary Ball Mill Milling Machine for Laboratory
Experience fast and effective sample processing with the F-P2000 high-energy planetary ball mill. This versatile equipment offers precise control and excellent grinding capabilities. Perfect for laboratories, it features multiple grinding bowls for simultaneous testing and high output. Achieve optimal results with its ergonomic design, compact structure, and advanced features. Ideal for a wide range of materials, it ensures consistent particle size reduction and low maintenance.
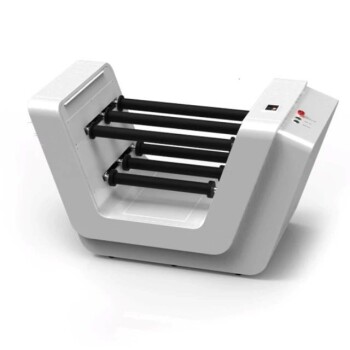
Laboratory Ten-Body Horizontal Jar Mill for Lab Use
The Ten-body horizontal jar mill is for 10 ball mill pots (3000ml or less). It has frequency conversion control, rubber roller movement, and PE protective cover.
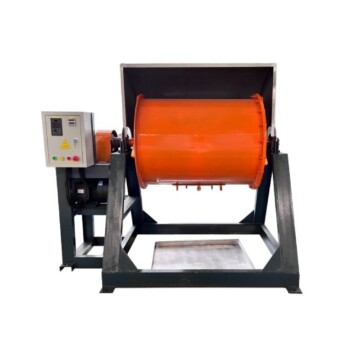
Stainless Steel Laboratory Ball Mill for Dry Powder and Liquid with Ceramic Polyurethane Lining
Discover the versatile stainless steel dry powder/liquid horizontal ball mill with ceramic/polyurethane lining. Ideal for ceramic, chemical, metallurgical, and building materials industries. High grinding efficiency and uniform particle size.
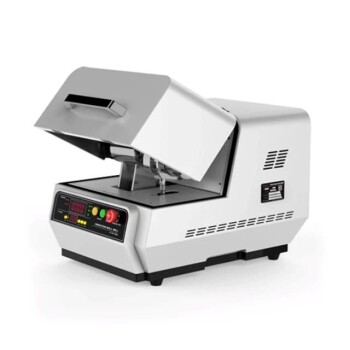
High Energy Vibratory Laboratory Ball Mill Grinding Mill Single Tank Type
High-energy vibration ball mill is a small desktop laboratory grinding instrument.It can be ball-milled or mixed with different particle sizes and materials by dry and wet methods.
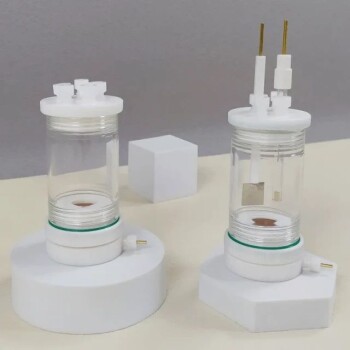
Multifunctional Electrolytic Electrochemical Cell Water Bath Single Layer Double Layer
Discover our high-quality Multifunctional Electrolytic Cell Water Baths. Choose from single or double-layer options with superior corrosion resistance. Available in 30ml to 1000ml sizes.

Laboratory Vibratory Sieve Shaker Machine for Dry and Wet Three-Dimensional Sieving
KT-VD200 can be used for sieving tasks of dry and wet samples in the laboratory. The screening quality is 20g-3kg. The product is designed with a unique mechanical structure and an electromagnetic vibrating body with a vibration frequency of 3000 times per minute.
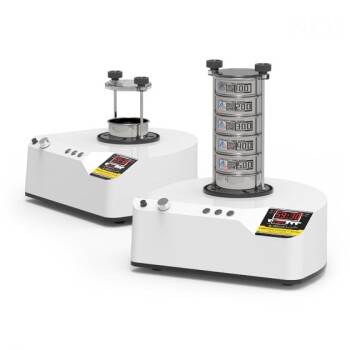
Three-dimensional electromagnetic sieving instrument
KT-VT150 is a desktop sample processing instrument for both sieving and grinding. Grinding and sieving can be used both dry and wet. The vibration amplitude is 5mm and the vibration frequency is 3000-3600 times/min.
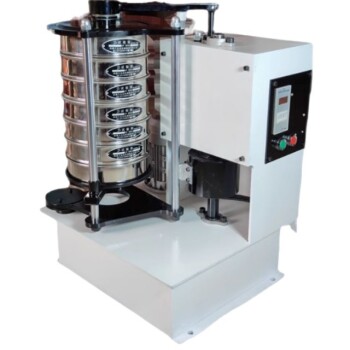
Laboratory Vibratory Sieve Shaker Machine Slap Vibrating Sieve
KT-T200TAP is a slapping and oscillating sieving instrument for laboratory desktop use, with 300 rpm horizontal circular motion and 300 vertical slapping motions to simulate manual sieving to help sample particles pass through better.
Related Articles
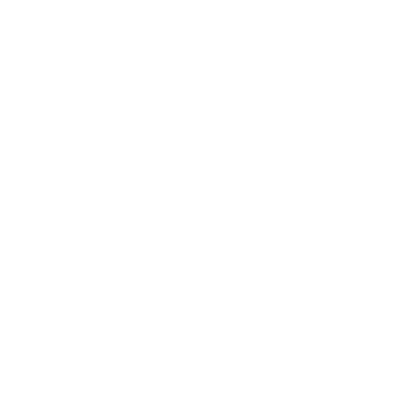
Disc / Cup Vibratory Mill: A Comprehensive Guide for Laboratory Experts
Discover the world of Disc / Cup Vibratory Mills! This comprehensive guide provides an in-depth understanding of their types, working principles, advantages, and applications in various industries, including pharmaceuticals, chemicals, and food processing.
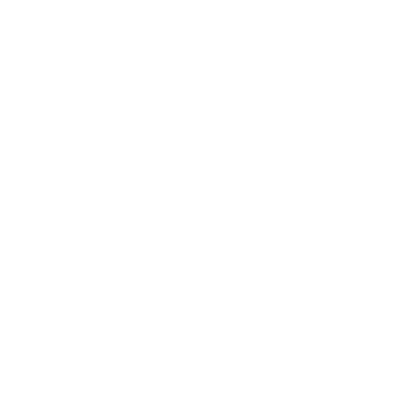
Disc / Cup Vibratory Mill: A Comprehensive Guide to Grinding Equipment
Discover the world of Disc / Cup Vibratory Mills! This guide covers everything from types and features to applications and benefits. Explore the versatility of these mills for grinding various materials in industries like pharmaceuticals, food, and chemicals.
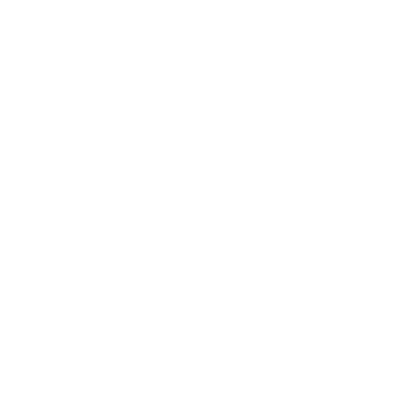
Disc / Cup Vibratory Mill: A Comprehensive Guide to Its Functions and Applications
Discover the world of Disc / Cup Vibratory Mills with our in-depth guide. Learn about their working principles, applications, advantages, and key features. Explore the various types of vibratory mills and their suitability for different industries.
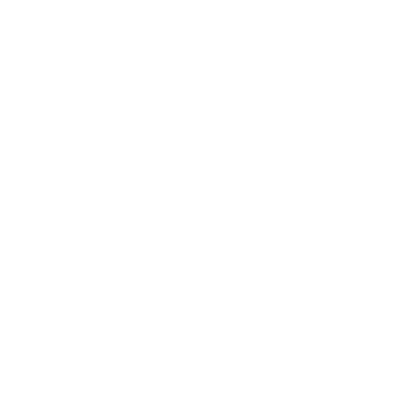
Choosing the Best Material for Ball Mill: Essential Factors and Recommendations
Discover the best material for ball mill applications and grinding success. Learn about the features and benefits of stainless steel, ceramic, agate, and tungsten carbide media. Find out how to ensure grinding success and the ideal grinding jars and media for planetary ball milling. Explore the applications of ball mills and the advantages of high-energy ball mills for ultra-fine particles.
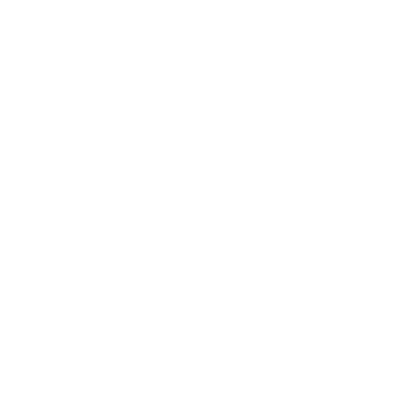
Revolutionizing Lab Efficiency: The Ultimate Guide to Laboratory Sieving Machines
Discover the common sieving methods used in laboratory analysis. Learn about single sieve and sieve set sieving, dry and wet sieving, and other techniques for effective particle separation. Find out how sieving has evolved over time and its importance in quality assurance.
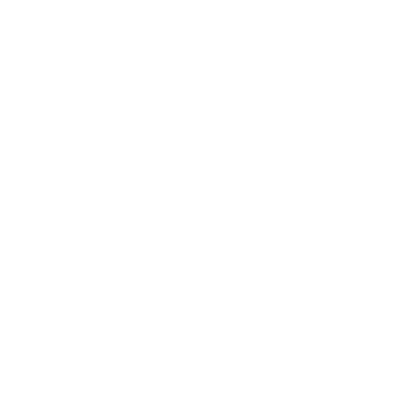
The Ultimate Guide to the Application and Benefits of Vibratory Sieve Shaker in Laboratory Testing
Discover the extensive application of vibratory sieve shaker in laboratory testing for industries such as food, medicine, chemical, and more. Learn about the benefits of using a sieve shaker.
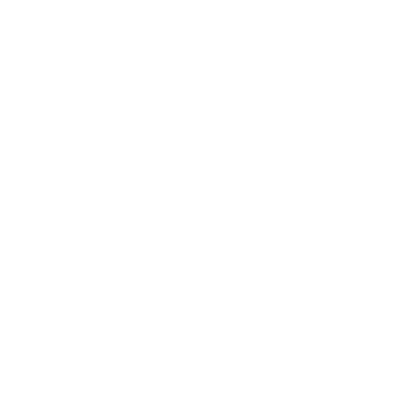
Three-Dimensional Vibrating Sieve: Working Principle and Application Fields
Discover the working principle and application fields of the three-dimensional vibrating screener. Learn how this laboratory equipment uses vibration force to efficiently separate and analyze granular materials. Explore its uses in the pharmaceutical, chemical, and various other industries.
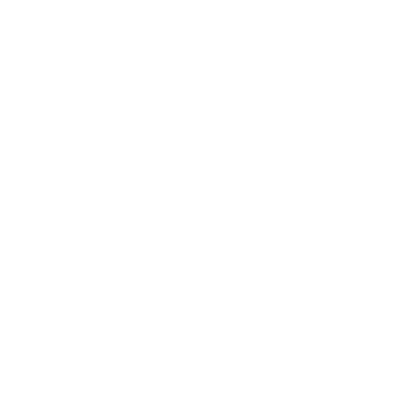
Maximizing Grinding Efficiency: The Power of Planetary Ball Mills
Discover why planetary ball mills offer higher grinding efficiency than ordinary ball mills. Learn about the technology behind their high-performance all-round capabilities. Find out the key factors influencing the productivity and specific energy consumption of ball mills.
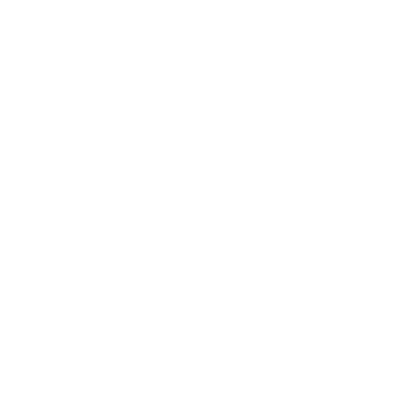
Sieving technology for particle size analysis and its applications
Introducing screening technology, explaining the working principle of vibrating screens and the advantages of using them for particle size analysis in screening technology. Learn about the types of vibrating screens and how to choose one.
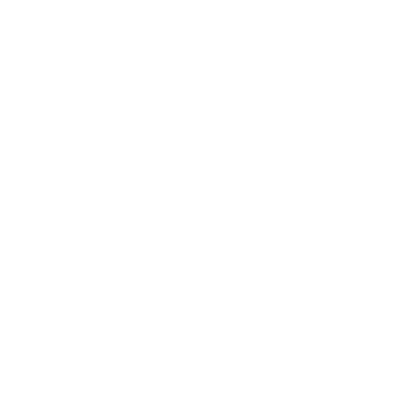
Development and Principles of Frozen Tissue Crushers
Explore the history, classification, and principles of frozen tissue crushers, including grinding ball selection and how to choose the right crusher.
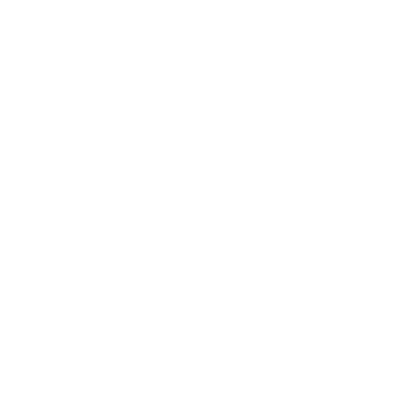
Understanding the Advantages and Disadvantages of Ball Mills in Laboratory and Industrial Applications
Discover the pros and cons of using ball mills for grinding materials. Explore the potential applications of ball mills for various industries.
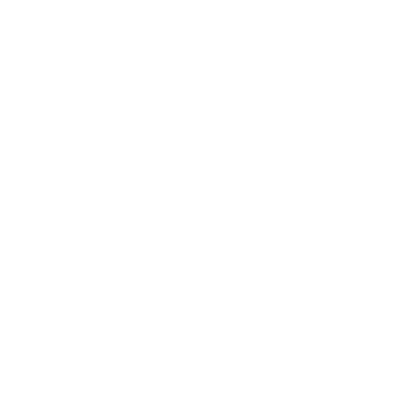
Working Principle of Vertical Ball Mill : Impact, Attrition, and Size Reduction
Discover the working principle of vertical ball mills through impact and attrition mechanisms. Learn how materials like iron ore and ceramics are ground to a fine medium. Explore the construction, operations, advantages of vertical mills in this detailed guide.