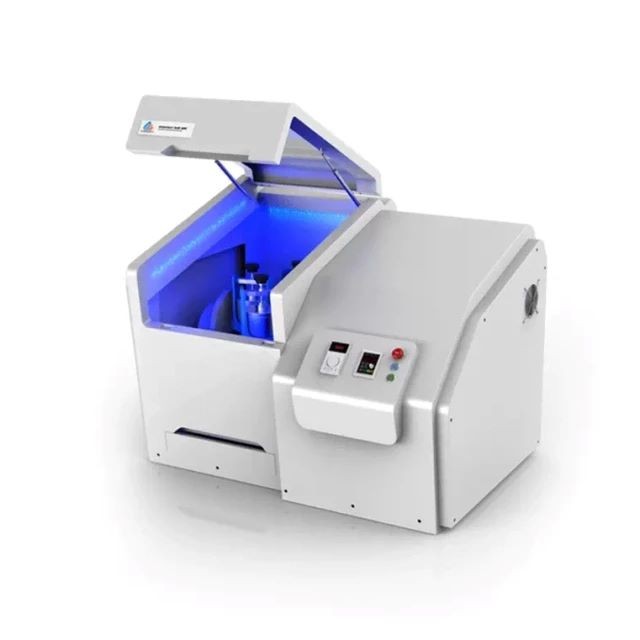
Milling Equipment
High-Energy Omnidirectional Planetary Ball Mill Machine for Laboratory
Item Number : KT-P2000E
Price varies based on specs and customizations
- Maximum injection size
- < 10 mm
- Sample particle size range
- 0.1-20um
- Number of ball mill jars
- 4
- Ball mill tank volume
- 500ml
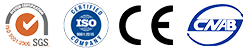
Shipping:
Contact us to get shipping details Enjoy On-time Dispatch Guarantee.
Why Choose Us
Reliable PartnerEasy ordering process, quality products, and dedicated support for your business success.
lntroduction
The KT-P2000E is a new product derived from the vertical high-energy planetary ball mill with a 360°rotation function. The product not only has the characteristics of the vertical high-energy ball mill, but also has a unique 360°rotation function for the planetary body. The sample and the grinding ball can move more vigorously and comprehensively in the ball mill jar, so as to obtain faster, more uniform, and smaller sample results. The product is equipped with 4 ball mill jars with a volume of 500ml or less.
Principle
The High-Energy Omnidirectional Planetary Ball Mill operates by rotating milling jars on a sun wheel and their own axes in opposite directions, generating high centrifugal and Coriolis forces. This rapid acceleration enhances impact and frictional forces between grinding balls and materials, efficiently producing ultra-fine particles.
Applications
The High-Energy Omnidirectional Planetary Ball Mill is a versatile and powerful tool used in various scientific and industrial applications. This type of ball mill is particularly effective for grinding hard and brittle materials, mechanical alloying, and producing ultra-fine particles. Its high-speed milling capabilities and the ability to generate significant impact energy make it a preferred choice for numerous applications. Here are the main application areas of the High-Energy Omnidirectional Planetary Ball Mill:
- Material Science: Used for the synthesis of advanced materials, including ceramics, metals, and alloys, through mechanical alloying and mixing processes.
- Nanotechnology: Ideal for producing nano powders of sizes ranging from 2 to 20 nm, crucial for various nanotechnology applications.
- Pharmaceuticals: Effective in the grinding of pharmaceutical compounds to produce fine powders, essential for drug formulation and development.
- Mineral Processing: Utilized for the size reduction and homogenization of minerals, aiding in the extraction and processing of valuable materials.
- Chemical Industry: Employed for the preparation of chemical compounds, facilitating the mixing and grinding of various chemicals.
- Environmental Science: Useful in the processing of materials for environmental remediation, such as the stabilization of hazardous waste materials.
- Food and Beverage Industry: Helps in the grinding and refining of food products to achieve desired textures and consistencies.
- Research and Development: Widely used in laboratories for research purposes, including the development of new materials and the study of material properties.
Features
The High-Energy Omnidirectional Planetary Ball Mill is a sophisticated laboratory equipment designed to efficiently grind and mix materials to produce ultra-fine particles. This advanced milling system leverages a unique planetary motion to enhance grinding efficiency and particle size reduction, making it an indispensable tool for researchers and scientists in various fields including materials science, pharmaceuticals, and nanotechnology. Here are the key features and benefits of this innovative ball mill:
- Dual Rotational Motion: The mill operates with a dual rotational motion where the grinding jars not only rotate around the central axis (sun wheel) but also rotate on their own axis in the opposite direction. This dual motion maximizes the kinetic energy transferred to the grinding media, significantly enhancing the grinding efficiency and allowing for the production of finer particles.
- High Impact Energy: The design of the planetary ball mill allows for high impact energy between the grinding balls and the material being processed. This high-energy impact can achieve particle sizes up to 40 times smaller than those produced by gravitational acceleration alone, making it ideal for producing nano-sized powders.
- Versatility in Grinding: The mill can accommodate multiple grinding jars simultaneously, each operating independently. This feature allows for the simultaneous processing of different materials or different grinding conditions, enhancing the versatility and efficiency of laboratory operations.
- Control and Precision: The High-Energy Omnidirectional Planetary Ball Mill offers precise control over the grinding parameters such as speed, time, and the type of grinding media used. This level of control ensures reproducible results and allows researchers to fine-tune the grinding process to meet specific requirements.
- Suitable for Mechanical Alloying: This ball mill is particularly effective for mechanical alloying, a process used to synthesize alloys with unique properties. The high energy and efficient grinding action facilitate the intimate mixing of elemental powders, leading to the formation of novel materials with tailored properties.
- Efficient Energy Utilization: The design of the planetary ball mill ensures that the energy input is efficiently utilized, reducing the overall energy consumption and making the process more environmentally friendly compared to traditional milling methods.
These features make the High-Energy Omnidirectional Planetary Ball Mill a high-performance tool for routine laboratory work, capable of handling a wide range of materials and applications with high precision and efficiency.
Detail & Parts
Functions
- Overturn control
- Continuous and intermittent operation
- Emergency stop
- Timing
- Power failure memory
- Overload and hazardous operation protection
- LED Lighting
- Heat Dissipation
Advantages
The High-Energy Omnidirectional Planetary Ball Mill offers several significant advantages that make it a superior choice for laboratory and industrial applications. Here are some of the key benefits:
- Enhanced Grinding Efficiency: The planetary ball mill utilizes a unique mechanism where the grinding jars rotate on their own axis while also moving around a central sun wheel in the opposite direction. This dual rotation results in a high-energy impact and friction between the grinding balls and the material, significantly enhancing the grinding efficiency and allowing for the production of ultra-fine particles.
- High Kinetic Energy: With the ability to generate up to 40 times higher impact energy than gravitational acceleration, this ball mill is ideal for grinding hard and brittle materials such as metals, alloys, ceramics, and minerals. The high kinetic energy ensures rapid and efficient size reduction, making it suitable for mechanical alloying and homogenization processes.
- Versatility in Applications: The mill is not only effective for routine laboratory work but also for advanced material synthesis. It can produce nano powders of 2 to 20 nm in size, making it invaluable for the development of innovative products requiring ultrafine and nano-sized materials.
- Operational Simplicity: Despite its high-energy capabilities, the planetary ball mill is relatively simple to operate. It requires minimal setup and can be easily integrated into existing laboratory workflows, making it a user-friendly option for researchers and technicians.
- Cost-Effectiveness: The process of ball milling is not only efficient but also cost-effective. It provides a reliable method for producing fine powders without the need for expensive equipment or complex procedures, which is beneficial for both research and commercial applications.
- Crystal Defects Creation: The mechanical energy applied during the milling process can induce crystal defects in the materials, which can be advantageous for certain applications where controlled defects are desired to modify the properties of the materials.
- Uniform Particle Size: The high-energy impacts and the controlled rotational speeds ensure that the resulting particles are uniform in size, which is crucial for many scientific and industrial applications where consistency is key.
The High-Energy Omnidirectional Planetary Ball Mill stands out for its ability to deliver high-energy grinding in a compact and efficient design, making it an essential tool for achieving precise and uniform particle sizes in various materials.
Technical specifications
Grinding principle | Impact & friction force |
Suitable materials | Small and medium-low hardness; brittle; dry or wet |
Materials input size | < 10 mm |
Materials output size | 0.1-20 um |
Processing volume | 2000ml |
Disc panspeed | 800 r/min |
Grinding panmaterial | Tungsten carbide;Ceramic; Agate; Stainless steel; Harden steel; Nylon, etc. |
Planetary disk space movement mode | X | Y axis 360° change planetary motion |
Motor power | 100-120V/200-240V AC ,50-60Hz,870W |
Net weight | 233kg |
Dimensions | L1120*W685*H780 mm |
Protection level | IP65 |
Quality standards | CE |
Warnings
Operator safety is the top important issue! Please operate the equipment with cautions. Working with inflammable& explosive or toxic gases is very dangerous, operators must take all necessary precautions before starting the equipment. Working with positive pressure inside the reactors or chambers is dangerous, operator must fellow the safety procedures strictly. Extra caution must also be taken when operating with air-reactive materials, especially under vacuum. A leak can draw air into the apparatus and cause a violent reaction to occur.
Designed for You
KinTek provide deep custom made service and equipment to worldwide customers, our specialized teamwork and rich experienced engineers are capable to undertake the custom tailoring hardware and software equipment requirements, and help our customer to build up the exclusive and personalized equipment and solution!
Would you please drop your ideas to us, our engineers are ready for you now!
FAQ
What Is A Planetary Ball Mill?
What Is A Laboratory Ball Mill?
What Is The Primary Function Of A High-Energy Omnidirectional Planetary Ball Mill?
How Does The High-Energy Omnidirectional Planetary Ball Mill Achieve High-speed Milling?
What Are The Benefits Of Using A High-Energy Omnidirectional Planetary Ball Mill?
What Makes The High-Energy Omnidirectional Planetary Ball Mill Different From Other Types Of Ball Mills?
What Are The Main Applications Of Planetary Ball Mills?
What Are The Applications Of A Laboratory Ball Mill?
What Is Milling Equipment Used For?
What Are The Key Features Of Planetary Ball Mills?
What Are The Main Types Of Laboratory Ball Mills?
What Are The Different Types Of Milling Equipment?
What Are The Advantages Of Using A Planetary Ball Mill?
What Is The Working Principle Of A Laboratory Ball Mill?
What Materials Can Be Processed Using Milling Equipment?
What Types Of Planetary Ball Mills Are Available?
What Are The Advantages Of Using A Laboratory Ball Mill?
How Does Milling Equipment Work?
How Does The Automatic Reversal Mechanism In Planetary Ball Mills Work?
What Materials Can Be Processed Using A Laboratory Ball Mill?
What Are The Advantages Of Using Milling Equipment?
What Makes Planetary Ball Mills Suitable For Small Particle Samples?
What Are The Key Features Of A High-energy Planetary Ball Mill?
What Factors Should Be Considered When Selecting Milling Equipment?
What Is The Difference Between A Planetary Ball Mill And A Vibratory Ball Mill?
4.9
out of
5
I highly recommend this planetary ball mill. It's a game-changer for our lab! The 360° rotation function ensures fast, uniform, and precise grinding.
4.8
out of
5
The KT-P2000E is a top-notch ball mill. Its versatility and user-friendly features make it a valuable asset in our laboratory. The continuous and intermittent operation modes provide great flexibility.
4.7
out of
5
This planetary ball mill delivers exceptional performance. The LED lighting and heat dissipation features ensure a safe and efficient operation. Our research team is thrilled with its capabilities.
4.9
out of
5
The KT-P2000E is a remarkable piece of equipment. Its ability to process materials down to 0.1-20 micrometers is truly impressive. It has significantly improved our sample preparation process.
4.8
out of
5
I'm thoroughly impressed with this ball mill. The overturn control and emergency stop features provide peace of mind during operation. The overall design is well-thought-out and user-friendly.
4.7
out of
5
The KT-P2000E has exceeded our expectations. Its robust construction and durable materials make it a reliable choice for our demanding applications. It's a valuable addition to our lab's equipment.
4.9
out of
5
This planetary ball mill is a fantastic investment. It's a powerful and efficient tool that has accelerated our research. The ability to customize grinding parameters gives us precise control over the desired results.
4.8
out of
5
We're very satisfied with the KT-P2000E. It's a versatile and high-performance ball mill. The choice of grinding jars with different materials allows us to optimize the process for various samples.
4.7
out of
5
The 360° rotation function of this ball mill is a game-changer. It ensures uniform grinding and reduces processing time. The sample results are consistently excellent.
4.9
out of
5
I highly recommend the KT-P2000E. It's a top-quality ball mill with exceptional grinding capabilities. The technical specifications are impressive, and the CE certification guarantees its reliability.
Products
High-Energy Omnidirectional Planetary Ball Mill Machine for Laboratory
REQUEST A QUOTE
Our professional team will reply to you within one business day. Please feel free to contact us!
Related Products
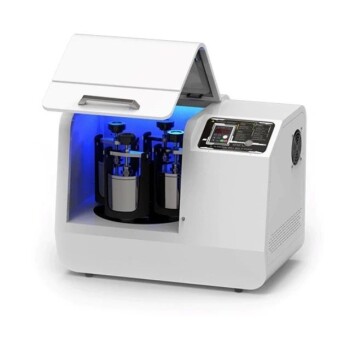
High Energy Planetary Ball Mill Milling Machine for Laboratory
The biggest feature is that the high energy planetary ball mill can not only perform fast and effective grinding, but also has good crushing ability
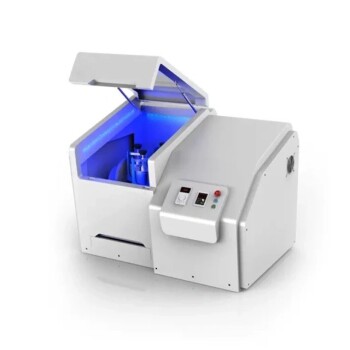
High-Energy Omnidirectional Planetary Ball Mill Milling Machine for Laboratory
The KT-P4000E is a new product derived from the vertical high-energy planetary ball mill with a 360° swivel function. Experience faster, uniform, and smaller sample output results with 4 ≤1000ml ball mill jars.
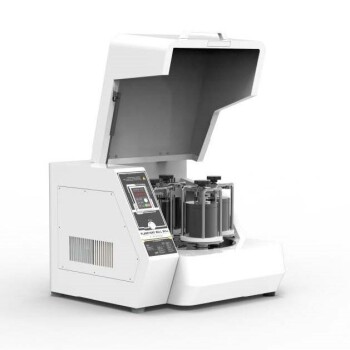
High Energy Planetary Ball Mill Milling Machine for Laboratory
Experience fast and effective sample processing with the F-P2000 high-energy planetary ball mill. This versatile equipment offers precise control and excellent grinding capabilities. Perfect for laboratories, it features multiple grinding bowls for simultaneous testing and high output. Achieve optimal results with its ergonomic design, compact structure, and advanced features. Ideal for a wide range of materials, it ensures consistent particle size reduction and low maintenance.
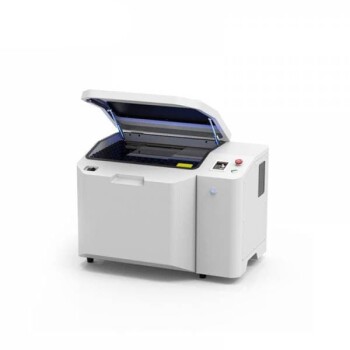
Laboratory Planetary Ball Mill Rotating Ball Milling Machine
KT-P400E is a desktop multi-directional planetary ball mill with unique grinding and mixing capabilities. It offers continuous and intermittent operation, timing, and overload protection, making it ideal for various applications.
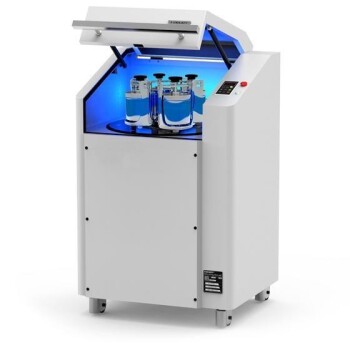
Laboratory Planetary Ball Mill Cabinet Planetary Ball Milling Machine
The vertical cabinet structure combined with ergonomic design enables users to obtain the best comfortable experience in standing operation. The maximum processing capacity is 2000ml, and the speed is 1200 revolutions per minute.
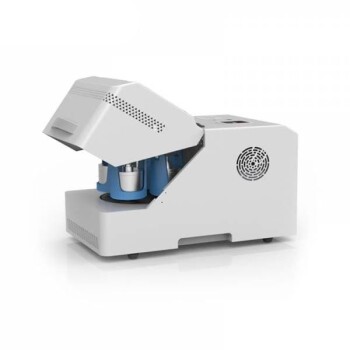
Mini Planetary Ball Mill Machine for Laboratory Milling
Discover the KT-P400 desktop planetary ball mill, ideal for grinding and mixing small samples in the lab. Enjoy stable performance, long service life, and practicality. Functions include timing and overload protection.
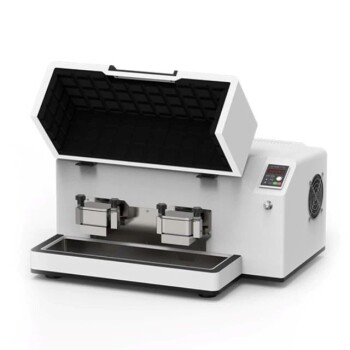
High Energy Vibratory Ball Mill for Lab Use
The high-energy vibrating ball mill is a high-energy oscillating and impacting multifunctional laboratory ball mill. The table-top type is easy to operate, small in size, comfortable and safe.
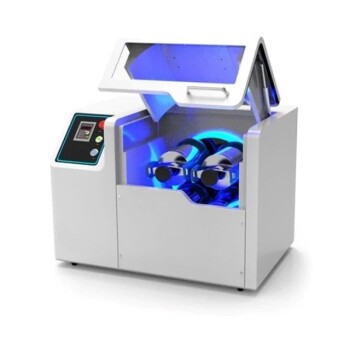
High Energy Planetary Ball Mill Machine for Laboratory Horizontal Tank Type
The KT-P2000H uses a unique Y-axis planetary trajectory, and utilizes the collision, friction and gravity between the sample and the grinding ball.
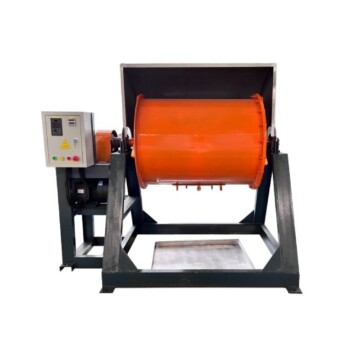
Stainless Steel Laboratory Ball Mill for Dry Powder and Liquid with Ceramic Polyurethane Lining
Discover the versatile stainless steel dry powder/liquid horizontal ball mill with ceramic/polyurethane lining. Ideal for ceramic, chemical, metallurgical, and building materials industries. High grinding efficiency and uniform particle size.
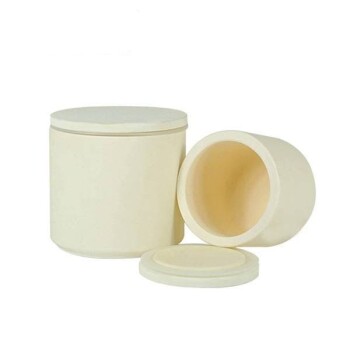
Laboratory Jar Ball Mill with Alumina Zirconia Grinding Jar and Balls
Grind to perfection with alumina/zirconia grinding jars and balls. Available in volume sizes from 50ml to 2500ml, compatible with various mills.
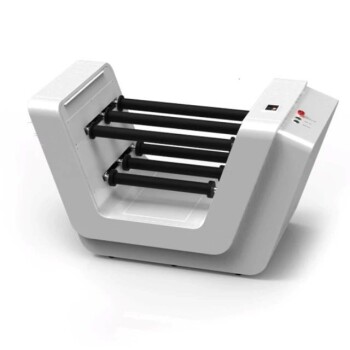
Laboratory Ten-Body Horizontal Jar Mill for Lab Use
The Ten-body horizontal jar mill is for 10 ball mill pots (3000ml or less). It has frequency conversion control, rubber roller movement, and PE protective cover.
Related Articles
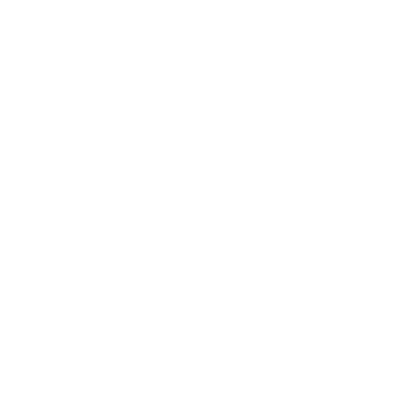
Maximizing Grinding Efficiency: The Power of Planetary Ball Mills
Discover why planetary ball mills offer higher grinding efficiency than ordinary ball mills. Learn about the technology behind their high-performance all-round capabilities. Find out the key factors influencing the productivity and specific energy consumption of ball mills.
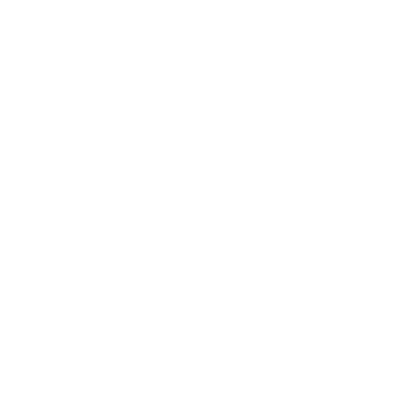
Planetary Ball Mills: Research Tools for Efficient Mixing and Nanoscale Grinding
Planetary ball mills are indispensable tools in modern laboratories, serving a crucial role in the mixing, fine grinding, and preparation of small samples. These mills are particularly adept at dispersing nanomaterials and facilitating the development and small-scale production of high-tech materials.
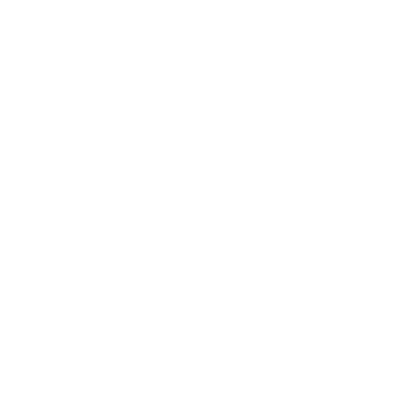
Advantages of Planetary Ball Mill in Laboratory Applications
Discover the advantages of using planetary ball mills in laboratory settings. Learn about its ability to produce fine powder, suitability for toxic materials, wide range of applications, continuous operation, and usage for milling abrasive materials. Explore how planetary ball mills differ from traditional milling machines and their function in creating ultrafine and nano-sized materials.
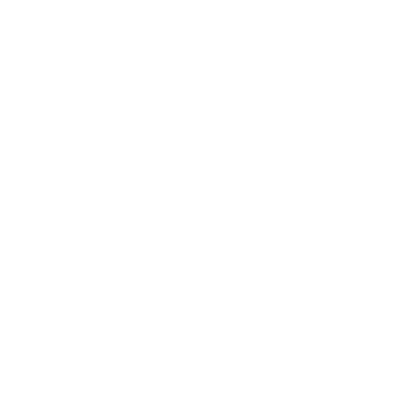
Choosing the Best Material for Ball Mill: Essential Factors and Recommendations
Discover the best material for ball mill applications and grinding success. Learn about the features and benefits of stainless steel, ceramic, agate, and tungsten carbide media. Find out how to ensure grinding success and the ideal grinding jars and media for planetary ball milling. Explore the applications of ball mills and the advantages of high-energy ball mills for ultra-fine particles.