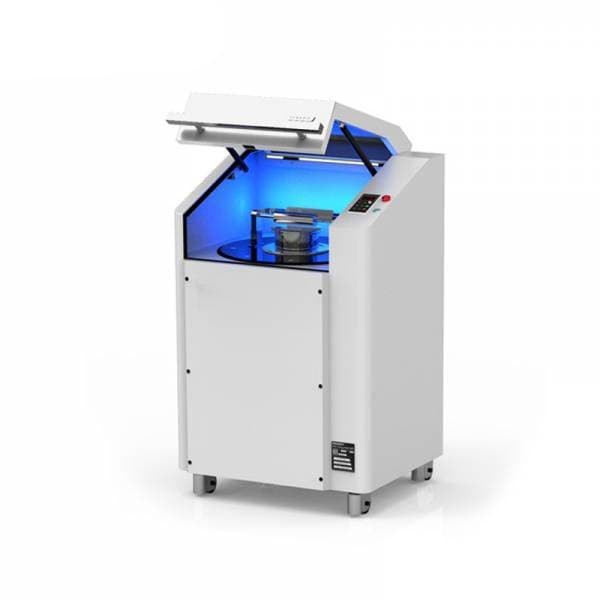
Milling Equipment
Lab Vibration Mill
Item Number : KT-VMS
Price varies based on specs and customizations
- Materials input size
- < 15 mm
- Materials output size
- 0.1-20 um
- Processing volume
- 250 / 500 ml
- Disc panspeed
- 1500 r/min
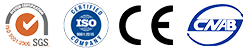
Shipping:
Contact us to get shipping details Enjoy On-time Dispatch Guarantee.
Why Choose Us
Reliable PartnerEasy ordering process, quality products, and dedicated support for your business success.
Introduction
Vibration mill is suitable for non-destructive crushing and fine grinding of larger particle size samples, and quickly prepares samples with analytical fineness and purity. It is suitable for the crushing and crushing of medium-hard, high-hardness, brittleness, fibrous, and elastic materials.
Grinding applications, support dry grinding, wet grinding, cryogenic grinding, vacuum or inert gas protection grinding; the sample loaded in the grinding disc kit is squeezed, collided, and rubbed under the action of high-speed circular motion, and it can be completed in 3-5 minutes The sample size varies from 15mm to 20 microns in a large span, and can fully guarantee the purity of the sample.
Applications
Vibration milling, a process that leverages mechanical vibrations and impact forces, is extensively utilized across multiple industries for material processing and synthesis. This technique is particularly effective in breaking down materials into smaller particles, facilitating a variety of applications. Here are the main application areas of vibration mills:
- Material Processing: Vibration mills are commonly employed in industries such as pharmaceuticals, cosmetics, and food for breaking down materials into fine particles. This process enhances the usability and effectiveness of the materials in various formulations.
- Synthesis of Nanoparticles: These mills play a crucial role in the synthesis of nanoparticles, where they are used to produce particles of metals, ceramics, and polymers with controlled size and shape, essential for advanced materials and technologies.
- Production of Advanced Materials: Vibration mills are integral in the production of advanced materials used in electronics, ceramics, chemicals, and the powdered metals industry. They are particularly useful for milling materials like tungsten, calcium carbide, and various compounds used in magnetic materials and high-frequency ceramics.
- Versatility in Milling: The laboratory vibratory ball mill, with its adaptable design and options for different tank linings (stainless steel, ceramic, zirconia, etc.), ensures suitability for both dry and wet milling processes, making it a versatile tool in laboratory settings.
- High-Efficiency Powder Making: Known for its high efficiency, the vibratory mill is available in single, double, and triple cylinder configurations, offering flexibility in operations and enhancing the production of fine powders required in various industrial applications.
Detail & Parts
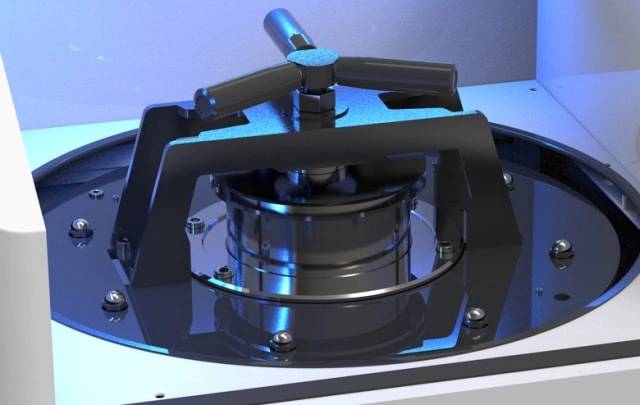
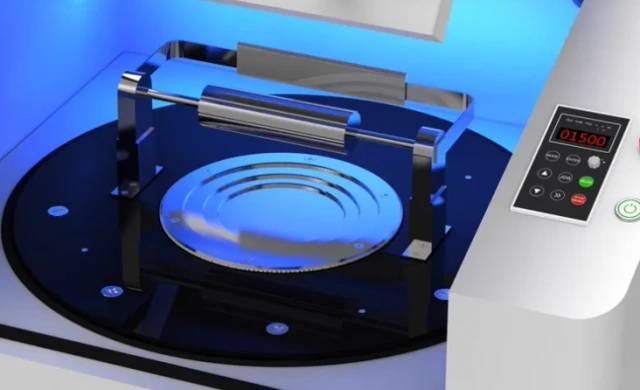
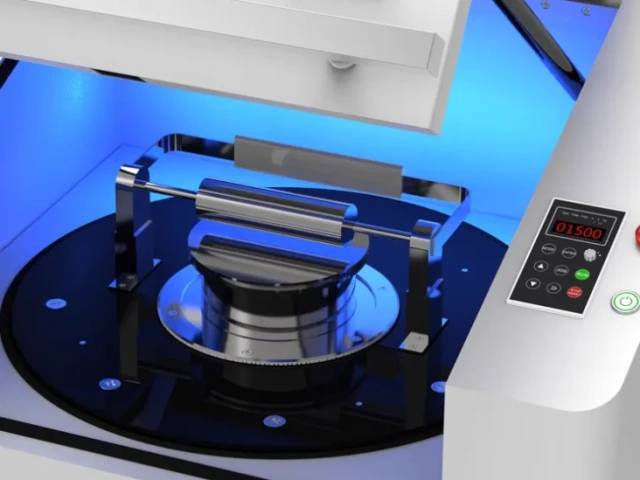
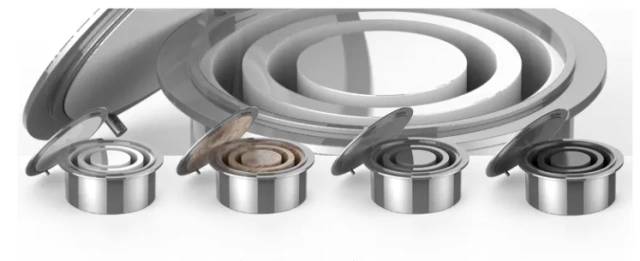
Features
The Laboratory Vibratory Ball Mill is a versatile and efficient powder making equipment designed to crush brittle and fibrous materials to a high degree of fineness. It offers a range of benefits that make it an essential tool in various industries, including electronics, ceramics, chemicals, and pharmaceuticals. Here are the key features and their benefits:
- Exchangeable Grinding Barrels: This feature allows for the customization of the milling process to suit different materials and fineness requirements. The ability to change barrels ensures that each material is processed optimally, enhancing the quality of the final product.
- Impact and Friction Reduction: The mill operates by using impact and friction inside vibrating grinding barrels filled with freely moving grinding balls. This method ensures a thorough and efficient reduction of material size, leading to a more uniform and fine powder.
- Versatile Material Processing: Capable of handling a wide range of materials including metals, ceramics, polymers, and composites, the vibratory mill is ideal for laboratories and industries that require flexibility in their milling processes.
- Reduced Contamination: With a closed container design, the mill minimizes contamination from external sources, ensuring the purity of the processed materials. This is particularly important in industries where contamination can affect the quality and performance of the final product.
- Special Options for Tank Lining: The ability to line the tank with materials such as stainless steel, ceramic, zirconia, nylon, PTFE, or rubber enhances the mill's adaptability to various materials and processing conditions, ensuring compatibility and safety.
- Efficient and Reliable Operation: Designed for both dry and wet ball milling, the laboratory vibratory mill is easy to operate, clean, and maintain, making it a reliable choice for continuous and high-volume processing needs.
These features not only enhance the functionality of the Laboratory Vibratory Ball Mill but also ensure that it meets the diverse needs of various industries, providing a high-quality and efficient solution for material size reduction.
Advantages
Vibration milling offers numerous advantages that make it a preferred choice for material processing and synthesis across various industries. Key benefits include:
- Reduced Contamination: Unlike other milling processes, vibration milling significantly minimizes contamination. This is achieved through the use of a closed container system that safeguards the material from external contaminants, ensuring purity and quality of the final product.
- Versatility: This milling technique is highly versatile, capable of handling a wide array of materials such as metals, ceramics, polymers, and composites. It can also produce particles with varying shapes, sizes, and structures, making it adaptable to diverse industrial needs.
- High Processing Capacity: With a filling capacity of up to 80% in the grinding cylinder, vibration mills outperform traditional ball mills in terms of processing capacity. This high efficiency leads to increased productivity and cost-effectiveness.
- Adjustability and Customization: The process parameters like amplitude, frequency, media, and ratio can be easily adjusted to produce different sizes of products. Additionally, these mills can be specially customized according to specific requirements, enhancing their utility in specialized applications.
- Temperature Control: Vibrating mills equipped with jacketed grinding cylinders allow for temperature adjustments during the grinding process, which is crucial for materials sensitive to heat.
- Continuous Production Capability: With integrated sieves and collection devices, these mills can facilitate continuous production, improving workflow and output.
- Operational Ease and Reliability: Vibration mills are designed for simple and convenient operation, ensuring reliable performance and easy maintenance. Their adaptability to various working conditions and ease of cleaning further enhance their operational efficiency.
- Dual Mode Operation: These mills support both dry and wet ball milling, providing flexibility in processing techniques.
- Compact and Efficient Design: Despite their high efficiency, vibration mills are lightweight and compact, saving space and energy while delivering superior grinding results.
These advantages collectively highlight the effectiveness and adaptability of vibration mills in meeting the rigorous demands of modern material processing and synthesis.
Functions
- Continuous and intermittent operation
- Emergency stop
- Timing
- Power failure memory
- Overload and dangerous operation protection
Technical specifications
Grinding principle | Impact & friction force |
Suitable materials | Small and medium-low hardness; brittle; dry or wet |
Materials input size | < 15 mm |
Materials output size | 0.1-20 um |
Processing volume | 250 / 500ml |
Disc panspeed | 1500 r/min |
Grinding panmaterial | Tungsten carbide;Ceramic; Agate; Stainless steel; Harden steel; Nylon, etc. |
Motor power | 550/750W |
Net weight | 218/228kg |
Dimensions | L780*W700*H1220 mm |
Protection level | IP65 |
Quality standards | CE |
Warnings
Operator safety is the top important issue! Please operate the equipment with cautions. Working with inflammable& explosive or toxic gases is very dangerous, operators must take all necessary precautions before starting the equipment. Working with positive pressure inside the reactors or chambers is dangerous, operator must fellow the safety procedures strictly. Extra caution must also be taken when operating with air-reactive materials, especially under vacuum. A leak can draw air into the apparatus and cause a violent reaction to occur.
Designed for You
KinTek provide deep custom made service and equipment to worldwide customers, our specialized teamwork and rich experienced engineers are capable to undertake the custom tailoring hardware and software equipment requirements, and help our customer to build up the exclusive and personalized equipment and solution!
Would you please drop your ideas to us, our engineers are ready for you now!
FAQ
What Is A Laboratory Crusher Used For?
How Does A Laboratory Crusher Work?
What Are The Main Features Of A Laboratory Jaw Crusher?
What Is The Working Principle Of A Laboratory Jaw Crusher?
What Are The Advantages Of Using A Laboratory Crusher?
4.9
out of
5
The vibration mill is a fantastic piece of equipment! It's easy to use, clean, and change products. It has significantly cut down the cost of trial production.
4.8
out of
5
I'm very impressed with the vibration mill. It's a durable and reliable machine that has met all of my expectations. It's also very quiet, which is a big plus.
4.7
out of
5
The vibration mill is a great investment. It's helped me to improve the efficiency of my lab and has also saved me money. I would highly recommend it to anyone looking for a quality vibration mill.
4.9
out of
5
I'm very happy with the vibration mill. It's a well-built machine that is easy to operate and maintain. It's also very versatile and can be used for a variety of applications.
4.8
out of
5
The vibration mill is a great addition to my lab. It's a powerful and efficient machine that has helped me to improve the quality of my research. I would highly recommend it to anyone looking for a top-of-the-line vibration mill.
4.7
out of
5
I'm very satisfied with the vibration mill. It's a reliable and durable machine that has exceeded my expectations. It's also very easy to use and clean.
4.9
out of
5
The vibration mill is a great value for the money. It's a well-made machine that is built to last. I've been using it for several months now and I've had no problems with it.
4.8
out of
5
I'm very impressed with the vibration mill. It's a powerful and efficient machine that has helped me to improve the productivity of my lab. I would highly recommend it to anyone looking for a top-of-the-line vibration mill.
4.7
out of
5
The vibration mill is a great investment. It's a versatile machine that can be used for a variety of applications. It's also very easy to use and maintain.
4.9
out of
5
I'm very happy with the vibration mill. It's a well-built machine that is easy to operate and maintain. It's also very quiet, which is a big plus.
4.8
out of
5
The vibration mill is a great addition to my lab. It's a powerful and efficient machine that has helped me to improve the quality of my research. I would highly recommend it to anyone looking for a top-of-the-line vibration mill.
4.7
out of
5
I'm very satisfied with the vibration mill. It's a reliable and durable machine that has exceeded my expectations. It's also very easy to use and clean.
4.9
out of
5
The vibration mill is a great value for the money. It's a well-made machine that is built to last. I've been using it for several months now and I've had no problems with it.
REQUEST A QUOTE
Our professional team will reply to you within one business day. Please feel free to contact us!
Related Products
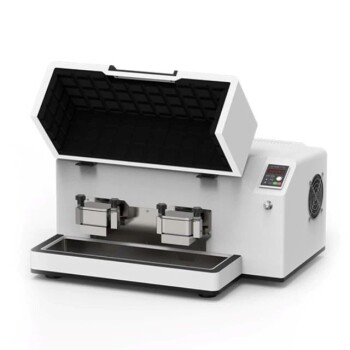
High Energy Vibratory Ball Mill for Lab Use
The high-energy vibrating ball mill is a high-energy oscillating and impacting multifunctional laboratory ball mill. The table-top type is easy to operate, small in size, comfortable and safe.
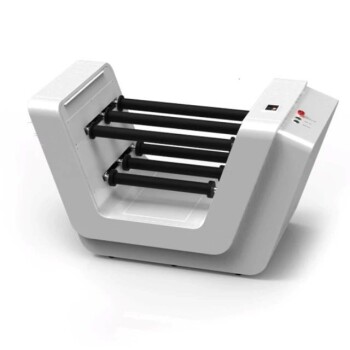
Laboratory Ten-Body Horizontal Jar Mill for Lab Use
The Ten-body horizontal jar mill is for 10 ball mill pots (3000ml or less). It has frequency conversion control, rubber roller movement, and PE protective cover.
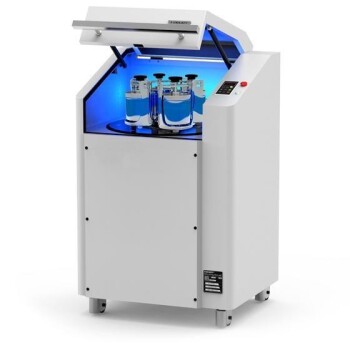
Laboratory Planetary Ball Mill Cabinet Planetary Ball Milling Machine
The vertical cabinet structure combined with ergonomic design enables users to obtain the best comfortable experience in standing operation. The maximum processing capacity is 2000ml, and the speed is 1200 revolutions per minute.
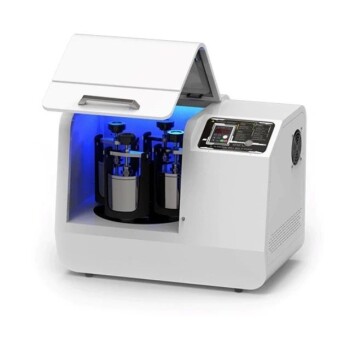
High Energy Planetary Ball Mill Milling Machine for Laboratory
The biggest feature is that the high energy planetary ball mill can not only perform fast and effective grinding, but also has good crushing ability
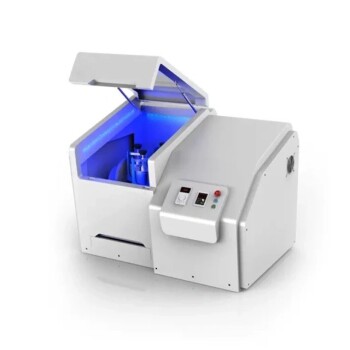
High-Energy Omnidirectional Planetary Ball Mill Milling Machine for Laboratory
The KT-P4000E is a new product derived from the vertical high-energy planetary ball mill with a 360° swivel function. Experience faster, uniform, and smaller sample output results with 4 ≤1000ml ball mill jars.
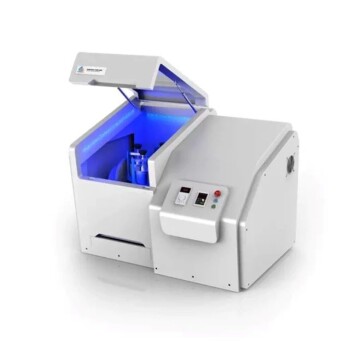
High-Energy Omnidirectional Planetary Ball Mill Machine for Laboratory
The KT-P2000E is a new product derived from the vertical high-energy planetary ball mill with a 360°rotation function. The product not only has the characteristics of the vertical high-energy ball mill, but also has a unique 360°rotation function for the planetary body.
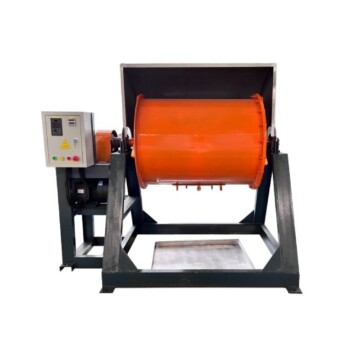
Stainless Steel Laboratory Ball Mill for Dry Powder and Liquid with Ceramic Polyurethane Lining
Discover the versatile stainless steel dry powder/liquid horizontal ball mill with ceramic/polyurethane lining. Ideal for ceramic, chemical, metallurgical, and building materials industries. High grinding efficiency and uniform particle size.
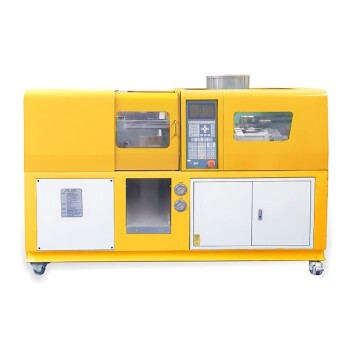
Small Injection Molding Machine for Lab Use
The small injection molding machinehas fast and stable movements; good controllability and repeatability, super energy saving; the product can be automatically dropped and formed; the machine body is low, convenient for feeding, easy to maintain, and no height restrictions on the installation site.
Related Articles
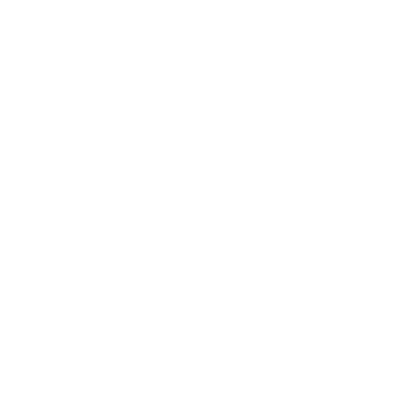
Disc / Cup Vibratory Mill: A Comprehensive Guide to Grinding Equipment
Discover the world of Disc / Cup Vibratory Mills! This guide covers everything from types and features to applications and benefits. Explore the versatility of these mills for grinding various materials in industries like pharmaceuticals, food, and chemicals.
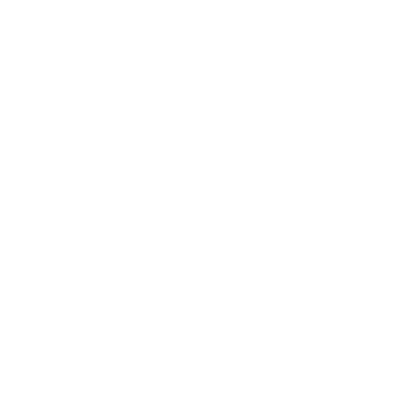
Disc / Cup Vibratory Mill: A Comprehensive Guide for Laboratory Experts
Discover the world of Disc / Cup Vibratory Mills! This comprehensive guide provides an in-depth understanding of their types, working principles, advantages, and applications in various industries, including pharmaceuticals, chemicals, and food processing.
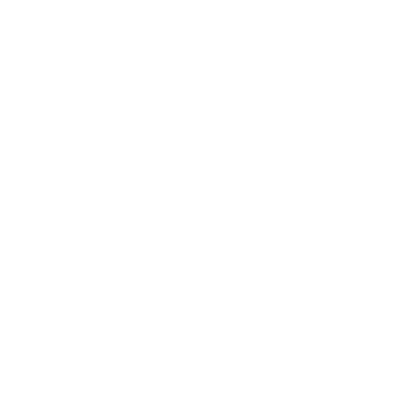
Disc / Cup Vibratory Mill: A Comprehensive Guide to Its Functions and Applications
Discover the world of Disc / Cup Vibratory Mills with our in-depth guide. Learn about their working principles, applications, advantages, and key features. Explore the various types of vibratory mills and their suitability for different industries.
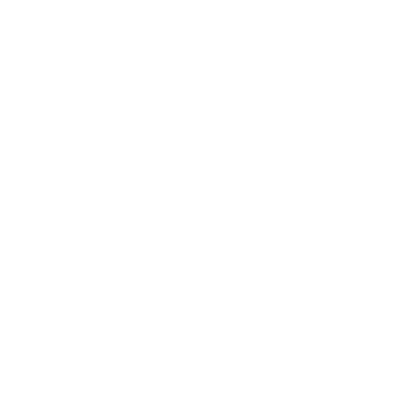
Key Features of the Micro Tissue Grinder: Usage, Advantages, and Applications
Discover the key features of the Micro Tissue Grinder, including usage instructions, advantages, and application fields. Learn the principles and structure of the Micro Tissue Grinder, and explore its benefits in sample preparation and industrial settings.
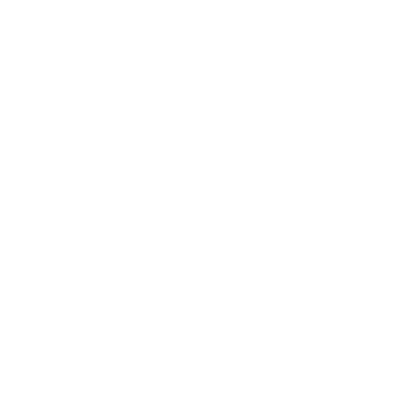
Features of Different Laboratory Mills: An Overview
Laboratory mills are specialized machines used to reduce non-homogenous batch samples into smaller, representative samples that are more uniform in composition.
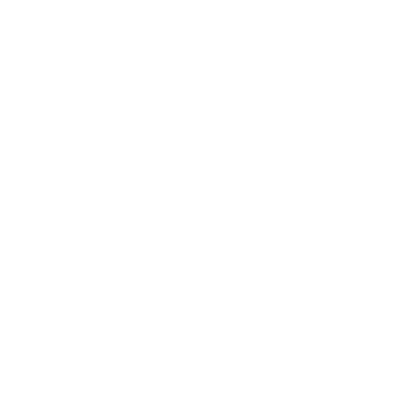
Planetary Ball Mills: Research Tools for Efficient Mixing and Nanoscale Grinding
Planetary ball mills are indispensable tools in modern laboratories, serving a crucial role in the mixing, fine grinding, and preparation of small samples. These mills are particularly adept at dispersing nanomaterials and facilitating the development and small-scale production of high-tech materials.
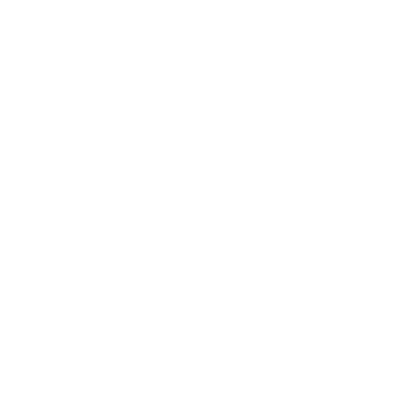
Advantages of Planetary Ball Mill in Laboratory Applications
Discover the advantages of using planetary ball mills in laboratory settings. Learn about its ability to produce fine powder, suitability for toxic materials, wide range of applications, continuous operation, and usage for milling abrasive materials. Explore how planetary ball mills differ from traditional milling machines and their function in creating ultrafine and nano-sized materials.
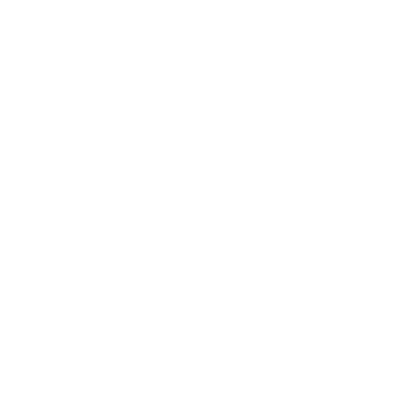
The Ultimate Guide to the Application and Benefits of Vibratory Sieve Shaker in Laboratory Testing
Discover the extensive application of vibratory sieve shaker in laboratory testing for industries such as food, medicine, chemical, and more. Learn about the benefits of using a sieve shaker.
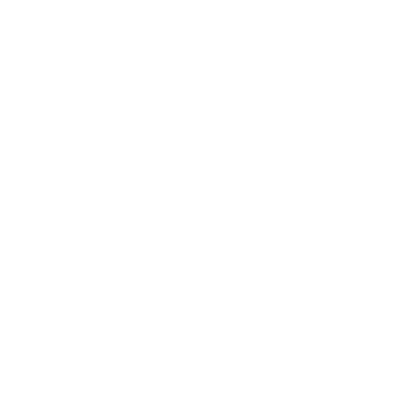
What is a Laboratory Crusher Used For?
Discover the uses and working mechanism of laboratory crushers. Explore various types of crushing equipment and their applications. Learn how laboratory crushers play a crucial role in scientific analysis and environmental studies.
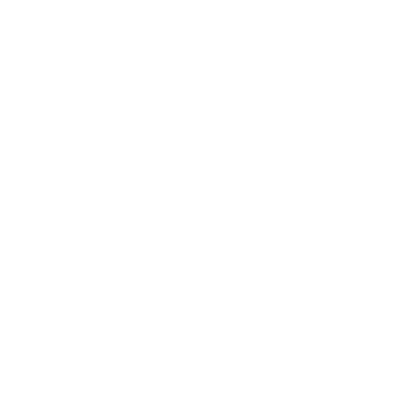
Revolutionizing Lab Efficiency: The Ultimate Guide to Laboratory Sieving Machines
Discover the common sieving methods used in laboratory analysis. Learn about single sieve and sieve set sieving, dry and wet sieving, and other techniques for effective particle separation. Find out how sieving has evolved over time and its importance in quality assurance.
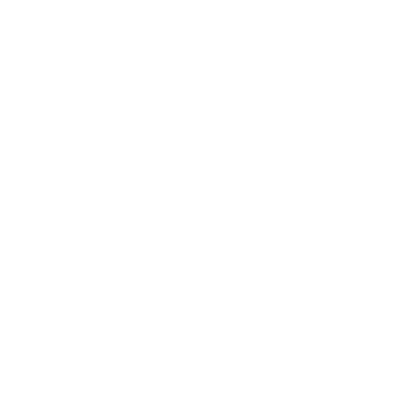
Maximizing Grinding Efficiency: The Power of Planetary Ball Mills
Discover why planetary ball mills offer higher grinding efficiency than ordinary ball mills. Learn about the technology behind their high-performance all-round capabilities. Find out the key factors influencing the productivity and specific energy consumption of ball mills.
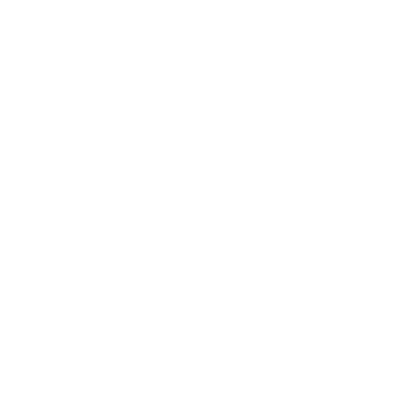
Unlocking the Power of Sieving Machines: Functions, Applications and Maintenance
Discover the significance of sieving machines in various industries and the essential functions they serve. Learn about the the maintenance requirements for optimal performance. Explore the benefits of using sieve shakers for automating the particle separation process.