Introduction to MPCVD Machines
MPCVD (Microwave Plasma Chemical Vapor Deposition) is a process used to deposit thin films of material onto a substrate using plasma generated by microwaves. An MPCVD machine consists of a microwave generator, a reaction chamber, and a substrate holder. The process starts with the substrate being placed on the holder inside the reaction chamber. The chamber is then evacuated to a low pressure, and a gas mixture containing the material to be deposited is introduced. Microwaves are then used to ionize the gas mixture, creating a plasma that deposits the material onto the substrate. MPCVD machines are widely used in the semiconductor industry due to their ability to deposit high-quality thin films at low temperatures.
Table of Contents
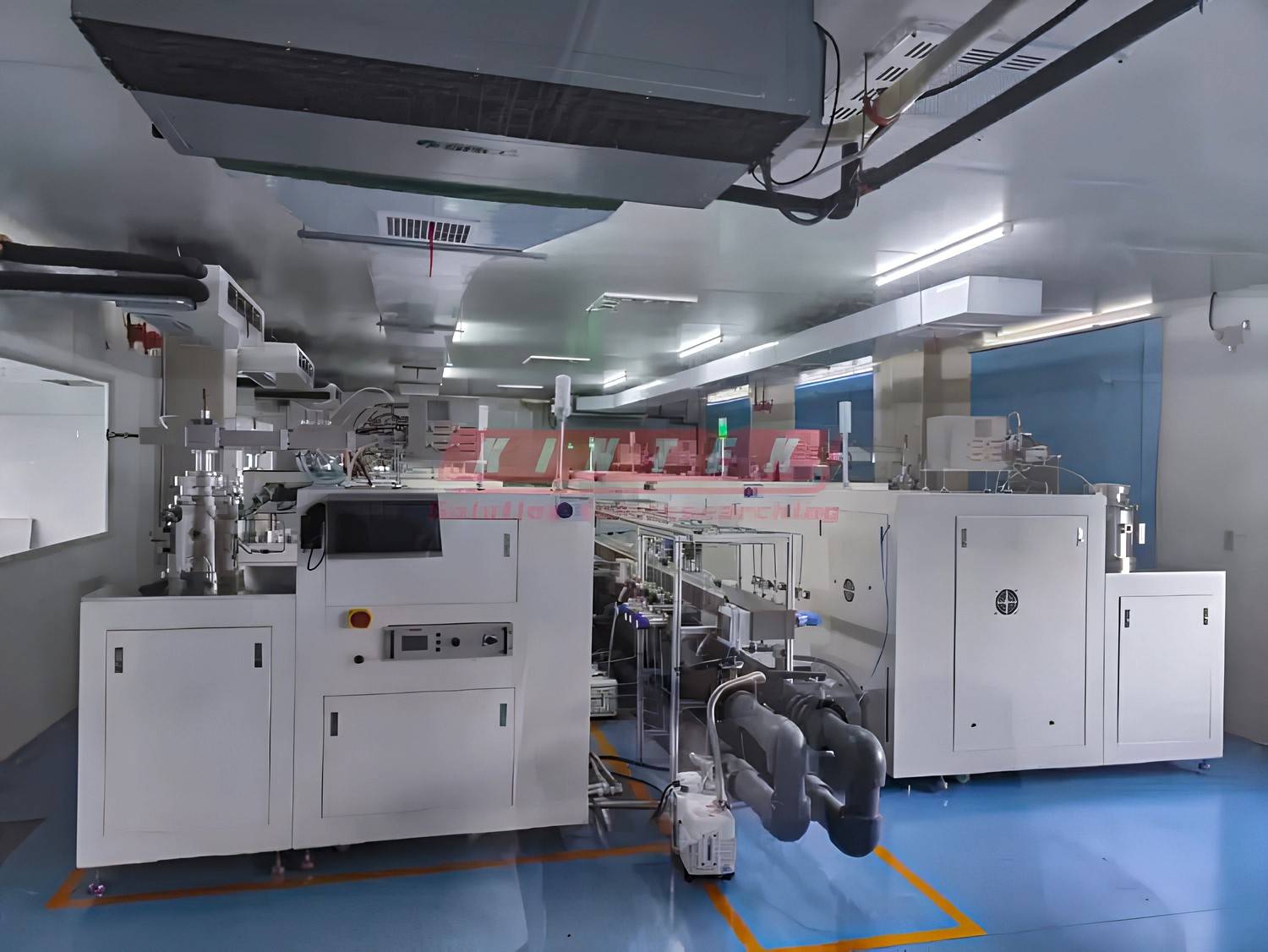
How an MPCVD Machine Works
Microwave Plasma Chemical Vapor Deposition (MPCVD) is a widely used technique for growing high-quality diamond films. In an MPCVD machine, thin films of diamond are deposited on a substrate by directing a carbon-rich plasma onto its surface. The process involves several components that work together to create the plasma and deposit the diamond film.
Components of an MPCVD Machine
An MPCVD machine consists of several components, including:
-
Microwave Plasma Generator: A microwave plasma generator produces a plasma by ionizing a mixture of gases. It operates at a frequency of 2.45 GHz and can deliver up to 2 kW of power.
-
Gas Delivery System: A gas delivery system introduces a mixture of gases into the vacuum chamber. Mass flow controllers (MFCs) calibrated in standard cubic centimeters per minute (sccm) regulate the gas flow.
-
Vacuum Chamber: The vacuum chamber houses the substrate and the gas mixture. It is maintained at a pressure of 1-10 Torr to facilitate the deposition process.
-
Substrate Holder: The substrate holder holds the substrate in place during the deposition process. The substrate temperature is controlled by the position of the plasma and is monitored using a thermocouple.
Deposition Process
The deposition process begins by introducing a mixture of hydrogen and methane gases into the vacuum chamber. The gas mixture is ionized by the microwave plasma generator, creating a plasma that is rich in carbon. The plasma is then directed onto the substrate, where it reacts with the surface to form a diamond film.
Several factors affect the quality of the diamond film produced by the MPCVD machine. These include the gas mixture, the pressure in the vacuum chamber, the temperature of the substrate, and the duration of the deposition process. It is important to carefully control these parameters to ensure that the diamond film is of high quality and uniform thickness.
Advantages of Our MPCVD System
Our MPCVD equipment has been running steadily for over 40,000 hours, demonstrating exceptional stability, reliability, repeatability, and cost-effectiveness. Our customers trust and use our equipment because of its high-quality diamond films, uniform thickness, and our expertise in the field of materials science.
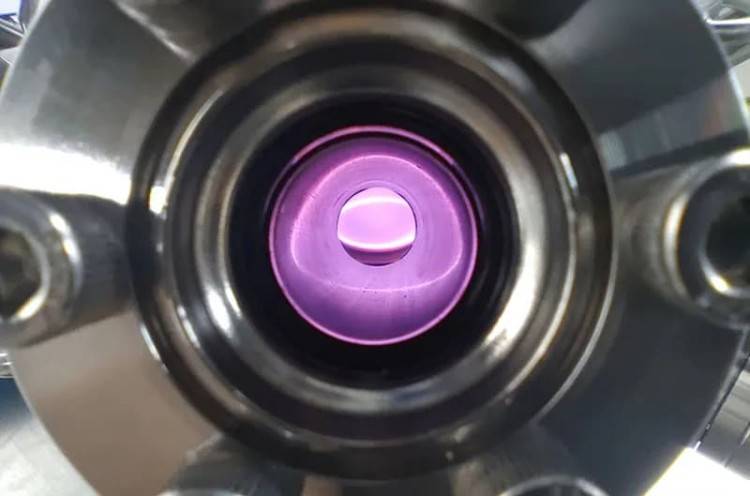
Advantages of MPCVD over other methods
MPCVD or microwave plasma chemical vapor deposition is a popular method for growing high-quality diamond films with various applications in the fields of electronics, optics, and even the medical industry. Compared to other methods, MPCVD offers several advantages that make it a preferred choice in the industry.
Non-Polar Discharge
Compared to the HFCVD method, MPCVD has the advantage of a non-polar discharge, avoiding contamination of the diamond by hot wires (tantalum, tungsten, etc.) at high temperatures. Hot wires are also sensitive to certain gases and their service life is affected during the growth process due to prolonged exposure to reaction gases, thus indirectly increasing the cost of synthesis.
Multiple Gas Usage
The MPCVD synthesis method is not only effective in avoiding diamond contamination, but also allows the use of multiple gases in the reaction system to meet different industrial needs. This is an advantage over other methods that cannot use multiple gases in their reaction systems.
Stable Control of Reaction Temperature
Compared to the DC-PJ CVD method, the MPCVD method enables smooth and continuous adjustment of microwave power and stable control of the reaction temperature, thus avoiding the problem of crystal seeds falling off the substrate due to arcing and flame failure in the DC-PJ CVD method.
Large Area of Stable Discharge Plasma
By adjusting the structure of the reaction chamber of the MPCVD equipment and by reasonably controlling the microwave power and pressure, a large area of stable discharge plasma can be obtained, which is necessary for the production of high-quality, large size single crystal diamonds. This is considered the most promising diamond synthesis method for industrial applications.
Ability to Control Diamond Film Thickness, Purity, and Crystal Quality
One of the advantages of using MPCVD over other methods is the ability to control the diamond film's thickness, purity, and crystal quality, resulting in a more uniform and higher-quality product. This is a significant advantage as it allows for the production of high-quality diamond films with precise specifications.
Versatility and Environmental Friendliness
MPCVD can be used with a wider range of materials and can produce large-area films, making it more versatile than other diamond film deposition methods. Additionally, the process does not require high temperatures, making it safer and more environmentally friendly.
In conclusion, MPCVD offers several advantages over other diamond film deposition methods, including non-polar discharge, multiple gas usage, stable control of reaction temperature, large area of stable discharge plasma, ability to control diamond film thickness, purity, and crystal quality, versatility, and environmental friendliness. These advantages make MPCVD a popular choice for the creation of high-quality diamond films with various applications in different industries.
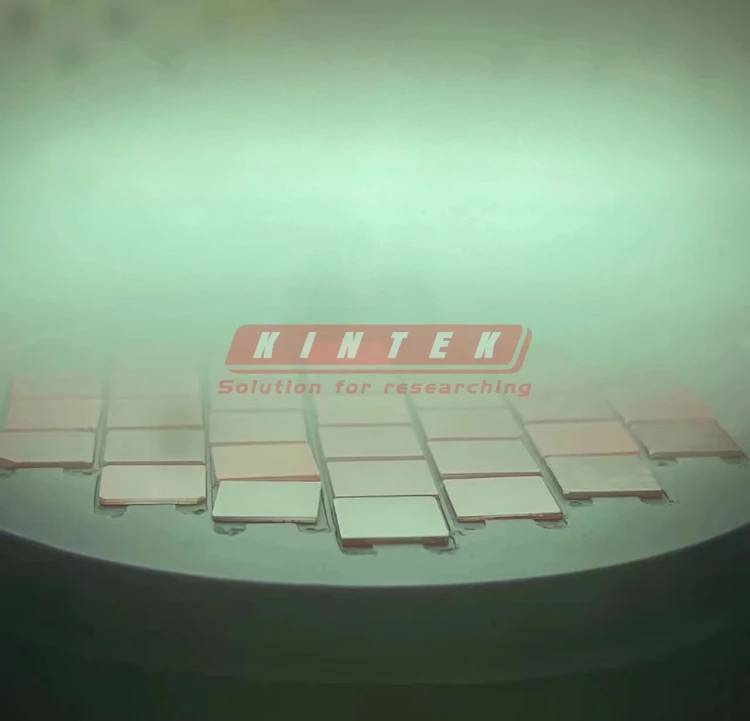
Factors that affect MPCVD growth process
The growth of high-quality thin films using MPCVD machines requires careful control of several factors. These factors can affect the purity, uniformity, and thickness of the deposited films. In this section, we will discuss some of the critical factors that affect the MPCVD growth process.
Temperature
The temperature is a crucial factor that affects the MPCVD growth process. The chemical reactions that take place during the deposition process are highly temperature-dependent. Therefore, controlling the temperature is essential to ensure that the reactions occur at the right rate and prevent the formation of unwanted compounds. The temperature must be precisely controlled to ensure that the deposited films have the desired properties.
Pressure
The pressure is another critical factor that affects the MPCVD growth process. The pressure must be carefully regulated to prevent the formation of unwanted by-products and ensure that the vapor reaches the substrate evenly. If the pressure is too high, the deposition rate may be too slow, and if it is too low, the deposited films may be non-uniform.
Gas flow rate
The gas flow rate is a crucial factor that affects the amount of precursor chemicals that are delivered to the substrate. The gas flow rate must be carefully controlled to ensure that the desired thickness and quality of the film are achieved. If the flow rate is too low, the deposition rate may be too slow, and if it is too high, the deposited films may be non-uniform.
Precursor concentration
The precursor concentration is a crucial factor that affects the amount of material that is deposited on the substrate. The precursor concentration must be carefully controlled to ensure that the right amount of material is deposited on the substrate. If the precursor concentration is too low, the deposition rate may be too slow, and if it is too high, the deposited films may be non-uniform.
Gas source and type
The type of gas used as the precursor is an essential factor that affects the quality of the deposited films. Methane is often preferred due to its high purity and structural similarity to diamond. In addition to methane, other carbon-containing gases can also be used. The preparation of the substrate requires gases like hydrogen, oxygen, or fluorine atoms.
In conclusion, the MPCVD growth process is highly dependent on several factors, including temperature, pressure, gas flow rate, precursor concentration, and gas source type. These factors must be carefully controlled to ensure that the deposited films have the desired properties.
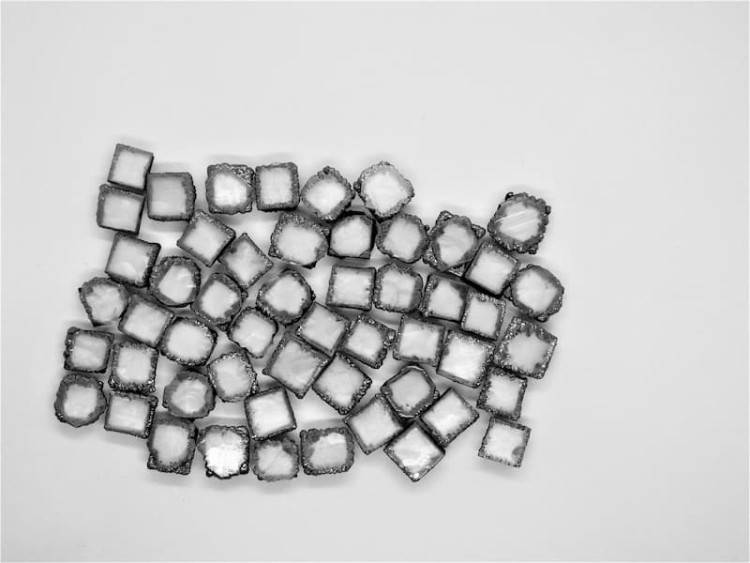
Techniques Used to Determine Film Quality
MPCVD is widely used to deposit thin films in a variety of applications, such as electronics, optics, and energy devices. However, it is essential to determine the quality of the deposited films to achieve the desired film properties. There are various techniques used to determine the quality of the deposited films.
X-ray Diffraction (XRD)
X-ray diffraction is a technique used to determine the crystallographic structure and orientation of the deposited films. This technique involves shining X-rays onto the sample and measuring the angle at which they are diffracted. The diffraction pattern generated can be used to identify the crystal structure of the deposited film.
Scanning Electron Microscopy (SEM)
Scanning electron microscopy provides high-resolution images of the surface morphology and topography of the films. This technique involves scanning the surface of the sample with a focused electron beam, which generates images of the surface. SEM is useful for determining the grain size and grain boundaries in the deposited films.
Ellipsometry
Ellipsometry is a technique used to measure the thickness and refractive index of the films. This technique involves measuring the change in polarization of light reflected from the surface of the sample. The change in polarization is related to the thickness and refractive index of the deposited film.
Raman Spectroscopy
Raman spectroscopy is a technique used to determine the vibrational modes of the deposited films. This technique involves shining laser light onto the sample and measuring the scattered light. The scattered light is related to the vibrational modes of the deposited film, which can provide information on the chemical composition and bonding.
By utilizing these techniques, one can determine the quality of the deposited films and optimize the MPCVD process parameters to achieve the desired film properties. X-ray diffraction is useful for determining the crystal structure of the deposited films, while SEM provides high-resolution images of the surface morphology and topography of the films. Ellipsometry is useful for measuring the thickness and refractive index of the films, and Raman spectroscopy provides information on the chemical composition and bonding.
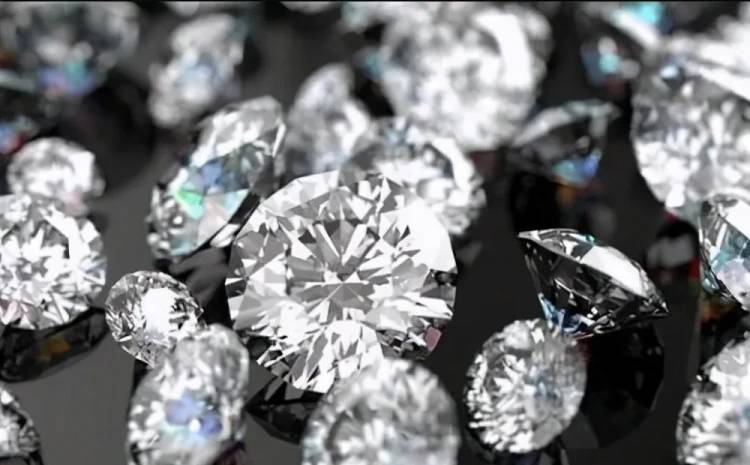
Comparison with Other CVD Methods
MPCVD is one of several CVD methods used to deposit thin films and coatings onto substrates. Compared to other CVD methods, such as LPCVD and PECVD, MPCVD has some distinctive advantages.
Faster Deposition Rate
One of the primary advantages of MPCVD is its faster deposition rate. This is due to the use of microwave plasma, which is generated by applying microwave radiation to a gas mixture. This results in a more efficient plasma generation process than other CVD methods.
High-Quality Films
MPCVD is known for its ability to produce high-quality films with excellent uniformity and adherence to the substrate. This is due to the highly ionized plasma generated by the microwave radiation, which results in a more homogeneous deposition process.
Lower Operating Temperatures
MPCVD can operate at lower temperatures, which is beneficial for materials that are sensitive to high temperatures. This is because the highly ionized plasma generated by the microwave radiation can perform the deposition process at lower temperatures, resulting in less thermal stress on the substrate.
Complex Setup
However, one of the major limitations of MPCVD is that it requires a complex setup, which can be more expensive than other CVD methods. This is because the microwave plasma generator and other equipment required for MPCVD are more complex and expensive to manufacture.
Substrate Damage
Another limitation of MPCVD is that the microwave plasma can cause damage to some types of substrates, such as organic materials. This can limit the types of substrates that can be used with MPCVD, making it less versatile than other CVD methods.
Overall, MPCVD is a versatile and efficient method for depositing thin films and coatings with high quality and uniformity. However, its suitability depends on the specific application and requirements of the user.
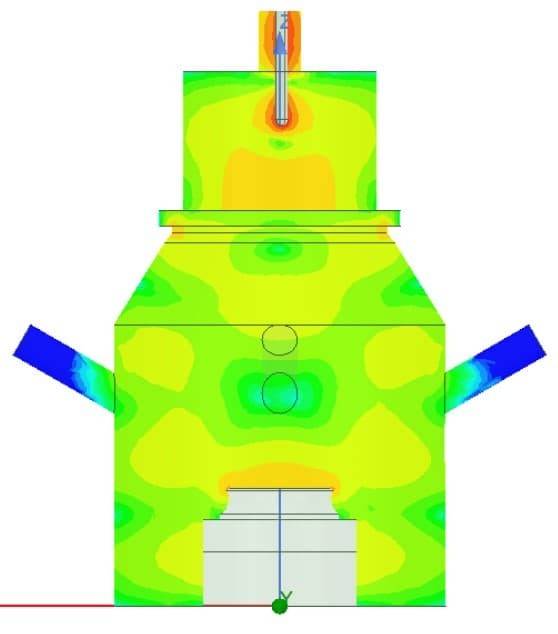
Conclusion
MPCVD is a highly sophisticated technique for producing high-quality carbon films with numerous advantages over other methods. MPCVD machines are designed to work under high vacuum conditions, producing films with exceptional mechanical properties, high purity, and low stress. Factors such as temperature, pressure, gas flow rate, and substrate material can affect the growth process of MPCVD films. Techniques such as Raman spectroscopy and X-ray diffraction are used to determine the film quality. Compared to other CVD methods, MPCVD offers several advantages, including higher film quality, better control of film properties, and lower operating costs. With its unique capabilities and advantages, MPCVD has become increasingly popular in the production of advanced carbon films for various industrial applications.
CONTACT US FOR A FREE CONSULTATION
KINTEK LAB SOLUTION's products and services have been recognized by customers around the world. Our staff will be happy to assist with any inquiry you might have. Contact us for a free consultation and talk to a product specialist to find the most suitable solution for your application needs!