Overview of KinTek and Its Specialization
Table of Contents
KinTek's experience in CIP equipment design and production
KinTek has a strong expertise in the design and production of CIP (Cold Isostatic Pressing) equipment. CIP is a materials handling strategy that applies high pressure to metal powders in a fixed elastomer compartment. KinTek has been in the market for many years and has witnessed substantial development in the CIP equipment industry.
Focus on powder forming process of different materials
KinTek specializes in the powder forming process of various materials. Powder metallurgy is a manufacturing route that allows for the production of specific materials, especially for high-performance applications. It reduces material waste and produces parts that are close to the final shape. KinTek's CIP equipment has been successfully used to consolidate most common metals, and there is a growing interest in using it for metal powder processing in a wider range of applications.
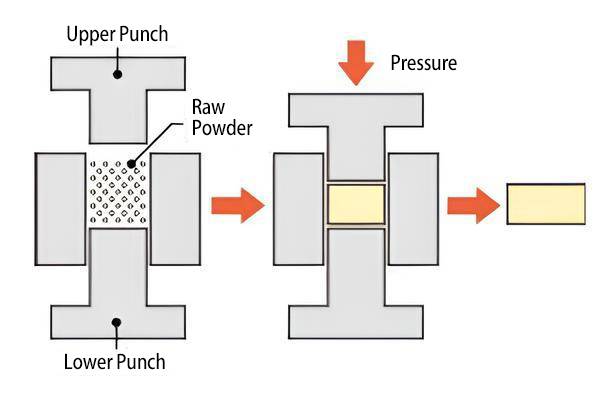
Application of CIP equipment in various industries
CIP equipment has applications in various industries, including medical implants, stainless steel filter cartridges, automotive, aerospace, power generation, and defense. It is used to produce complex shapes, forge preforms, and create components for different systems and structures. CIP offers advantages such as minimizing waste, shaping difficult-to-machine materials, achieving uniformity in microstructure, producing multi-materials or graded structures, and solid-state joining. KinTek's CIP equipment is designed to meet the specific needs of different industries and applications.
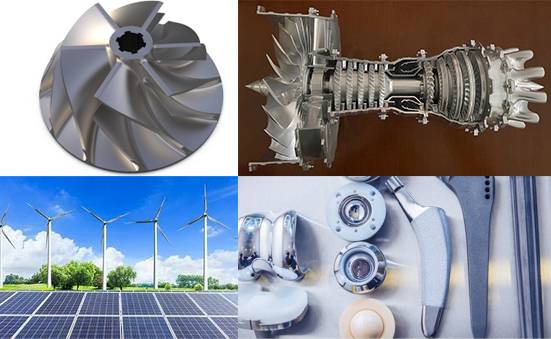
Solutions offered by KinTek
KinTek laboratory presses
KinTek offers highly precise and durable laboratory presses. These presses are equipped with a heavy-duty hydraulic system, iron bolsters, and high tensile steel tie rods, ensuring many years of service. They also feature threaded rods with nuts for rapid and precise platen adjustment, as well as heated platens with accurate digital control that can be integrated into manual and automated presses. KinTek's laboratory presses provide the necessary precision and customization options for various laboratory testing needs.
KinTek die sets
KinTek has expertise in the design and manufacture of both general and special die sets. Over the years, they have developed a wide range of die sets to meet the diversifying needs of customers. These include enclosed die sets for close-forging with general-purpose presses, high-precision die sets with a concentricity of 10 μm or less, and smart die sets that incorporate sensing technology. KinTek's die sets are known for their quality and ability to meet specific customer requirements.
KinTek agglomeration/pelletizing equipment
KinTek is a global leader in agitation agglomeration/pelletizing equipment and systems. They specialize in process testing and development, custom equipment design and manufacturing, and parts and service support. Producers looking to pelletize a powder feed can benefit from working with KinTek's agglomeration experts. They provide guidance throughout the process, helping producers minimize friction and make informed decisions. KinTek's expertise in pelletizing fine powders can help solve powder-related challenges.
KinTek rotary systems for high purity material processing
KinTek's rotary systems are designed to handle high purity applications. They engineer components for specialty alloys, fused silica quartz, and technical ceramics such as alumina or silicon carbide. These rotary systems provide a chemically inert environment while maintaining a gas-tight and dust-tight system. KinTek's experience in engineering components for advanced materials ensures the performance and safety required in modern applications.
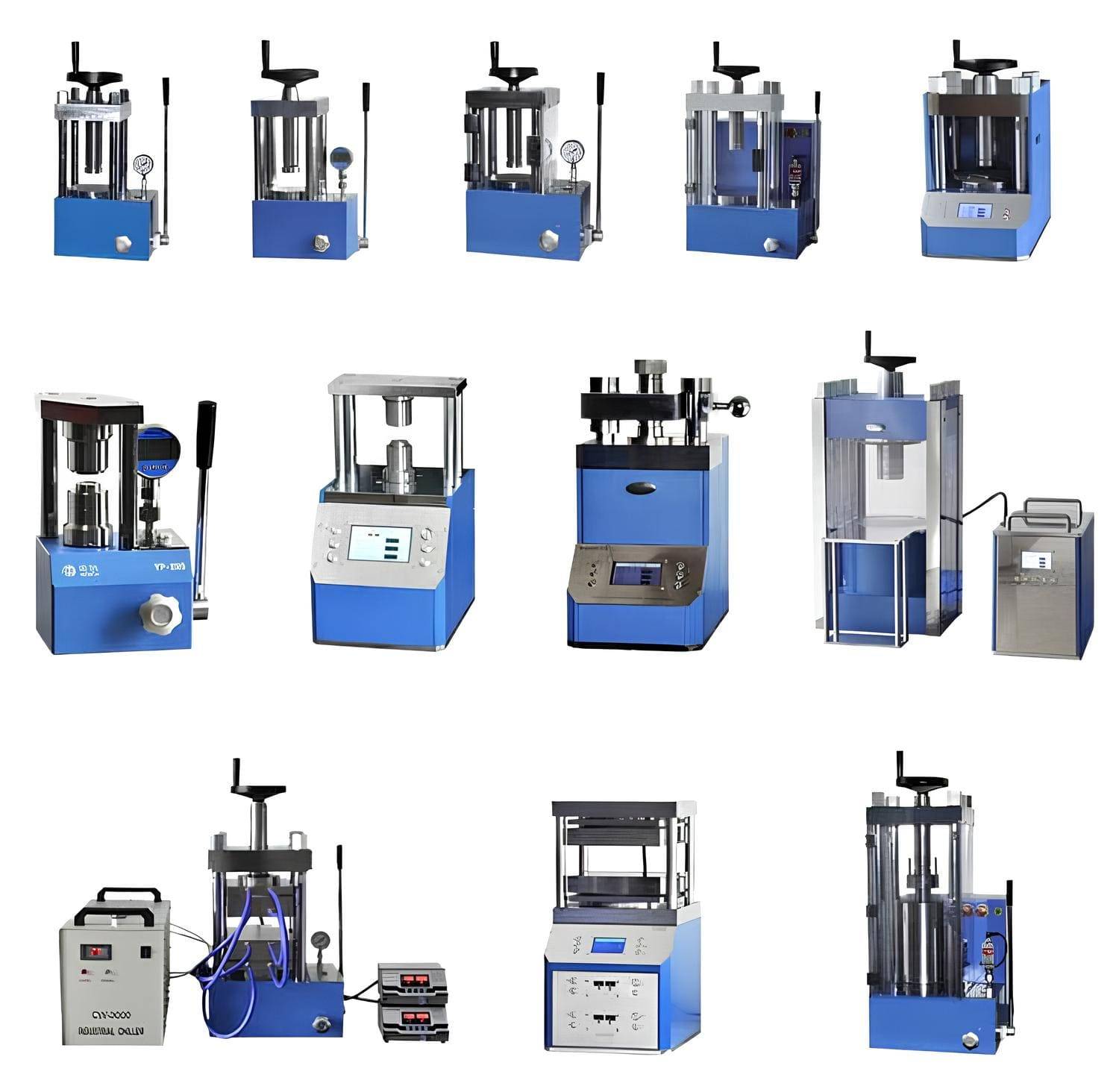
KinTek tablet presses
KinTek's tablet presses are known for their efficiency, precision, and quality. They offer a range of models, including the FE-series, i-series, and P-series, each catering to different needs. The FE-series is their flagship press model, featuring novel features for changeover, operation, and maintenance. The i-series is recognized worldwide for its precision and strength. The P-series provides KinTek's legendary quality in a more economical line. These tablet presses deliver consistent and accurate results, making them a trusted choice in the industry.
Overall, KinTek's specialization in CIP equipment design and production, as well as their expertise in various other areas such as laboratory presses, die sets, forged products, agglomeration/pelletizing equipment, rotary systems, and tablet presses, makes them a reliable partner for businesses in need of high-quality and customized solutions.
Design and Structural Features of the Dry Bag Cold Isostatic Press Machine
Optimal design of big force bearing parts
The dry bag cold isostatic press machine, developed by KinTek, is a specialized equipment for powder forming processes. It is designed to handle various powder bars or pipes under customized high-pressure conditions. One of the key design features of this machine is the optimal design of big force bearing parts.
Through finite element strength analysis, the big force bearing parts of the machine have been designed to withstand the high pressures involved in the isostatic pressing process. This ensures the durability and reliability of the machine during operation. The careful design of these parts also helps to minimize the risk of any structural failures or breakdowns.
By optimizing the design of the big force bearing parts, KinTek has created a dry bag cold isostatic press machine that can effectively handle the pressing of different materials and shapes with ease. The machine is capable of producing high-quality parts consistently, providing businesses with a reliable solution for their powder forming needs.
Real-time monitoring of stress and deformation
Another important feature of the dry bag cold isostatic press machine is the real-time monitoring of stress and deformation. This feature allows operators to closely monitor the main parts of the machine that bear the force during the pressing process.
By monitoring stress and deformation in real time, operators can ensure the safety and security of the machine. Any abnormal changes in stress or deformation can be quickly detected, allowing for immediate action to be taken to prevent any potential damage or accidents.
This real-time monitoring capability provides operators with valuable insights into the performance of the machine, allowing them to make adjustments as needed to optimize the pressing process. It also helps to extend the lifespan of the machine by identifying any potential issues early on and addressing them promptly.
Quality control and testing methods in different stages of production
To ensure the highest level of quality in the dry bag cold isostatic press machine, KinTek has implemented advanced quality control and testing methods in different stages of production. This comprehensive approach to quality management helps to guarantee that the machine meets the strictest standards and specifications.
Throughout the forging process, including forging flaw detection, machining, winding, equipment assembly, and commissioning, rigorous quality control measures are implemented. These measures help to identify any potential flaws or defects in the machine, ensuring that only high-quality components are used and that the final product is free from any manufacturing defects.
Thorough testing methods are also employed to verify the performance and functionality of the machine. This includes finished product flaw detection, which ensures that the machine operates as intended and meets all the necessary requirements.
By implementing these quality control and testing methods, KinTek strives to deliver a dry bag cold isostatic press machine that is reliable, efficient, and capable of producing high-quality parts. This commitment to quality ensures customer satisfaction and helps businesses achieve their production goals effectively.
In conclusion, the design and structural features of the dry bag cold isostatic press machine, including the optimal design of big force bearing parts, real-time monitoring of stress and deformation, and the implementation of quality control and testing methods, make it a reliable and efficient solution for powder forming processes. With its advanced capabilities and commitment to quality, the machine offers businesses the ability to produce high-quality parts consistently and efficiently.
Functionalities and Modes of Operation
Suitability for powder forming in different industries
Powdered metal processing allows for the production of products with properties that can surpass alloyed materials. It involves mixing metal, ceramic powders, or both, with a binder to create a mixture that can be pressed into desired shapes. This process is commonly used in various industries, including automotive, aerospace, and manufacturing, to create near-net shape products. For larger parts, the mixture is filled into molds, similar to the infiltration casting process used in the manufacturing of Polycrystalline Diamond Composite (PDC) drill bits for deep well drilling.
Pneumatic/Hydraulic control mode
There are different modes of operation for powder forming presses. Entry-level models use pneumatic control to generate the pressing pressure. They either utilize pneumatic cylinders or hoses mounted below the lower plate to generate the required pressure. Hand hydraulic control is another mode of operation where a hydraulic pump, manually activated, directs the platen to its closer position until the pre-set pressure is built up. Most modern veneer presses are equipped with electro-hydraulic pressure generation, which involves an hydraulic aggregate.
Safety features
Powder forming presses are equipped with numerous safety features to minimize the risk of accidents and ensure the safety of operators. These safety features include emergency stop lines that immediately interrupt the closing process of the press when pulled or pressed, minimizing the risk of injuries. Additionally, safety acrylic guards with limit switches, overload relay controls, and controls placed outside the compression zone contribute to the overall safety of the equipment.
Automatic and manual operating modes
Powder forming presses offer both automatic and manual operating modes. In the automatic mode, the press can run automatically from room temperature to a set temperature. The system is controlled by thyristor and features a modularized temperature control system. It allows for remote control, real-time tracking, history record, output report, and more. The manual mode allows operators to have more control over the process and make adjustments as needed.
In conclusion, powder forming presses offer convenient controls, enhanced safety features, and different modes of operation to suit the needs of various industries. Whether it's for creating near-net shape products or performing specific functions like hot-pressing or pellet pressing, these presses provide reliable performance and flexibility.
Advantages of Using the Dry Bag Cold Isostatic Press Machine
Efficiency in automatic batch production
The dry bag cold isostatic press machine offers efficiency in automatic batch production. It allows for the simultaneous pressing of multiple shapes and parts in one high-pressure cylinder, making it suitable for small batch production. This process saves time and increases productivity, making it a cost-effective solution for businesses.
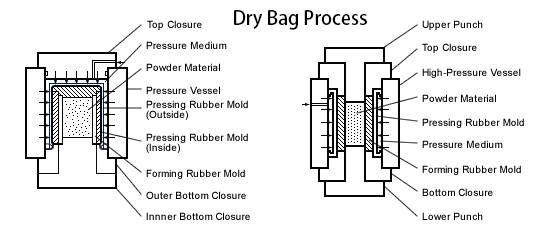
Safety measures to prevent accidents
Safety is a top priority in any manufacturing process. The dry bag cold isostatic press machine is designed with safety measures in place to prevent accidents. With advanced technology and real-time monitoring of stress and deformation, the machine ensures the safety and security of the operators.
Quality of products
The dry bag cold isostatic press machine provides high-quality products. By applying pressure from all sides, it mechanically bonds the powder particles, creating a solid green body. This process results in products with excellent density and uniformity, ensuring consistent quality and performance.
Environmental benefits
In addition to its efficiency and quality, the dry bag cold isostatic press machine also offers environmental benefits. It utilizes a room-temperature liquid in the pressure chamber, eliminating the need for high-temperature processing. This reduces energy consumption and minimizes carbon emissions, making it an eco-friendly manufacturing option.
Cost savings in raw materials and electricity
Using the dry bag cold isostatic press machine can lead to significant cost savings. The process allows for the use of lower-cost powder materials compared to other pressing methods. Additionally, the machine operates at lower energy consumption levels, resulting in reduced electricity costs for businesses.
Flexibility in pressure settings
The dry bag cold isostatic press machine offers flexibility in pressure settings. It can be adjusted to meet the specific requirements of different materials and products. This versatility allows for customization and ensures optimal results for various applications.
Capability to produce long bars or pipes
With its specialized design, the dry bag cold isostatic press machine has the capability to produce long bars or pipes. This feature makes it suitable for industries such as cemented carbides, ceramics, magnetic materials, graphite, refractories, and refractory alloys. It provides a reliable solution for manufacturing complex and extended products.
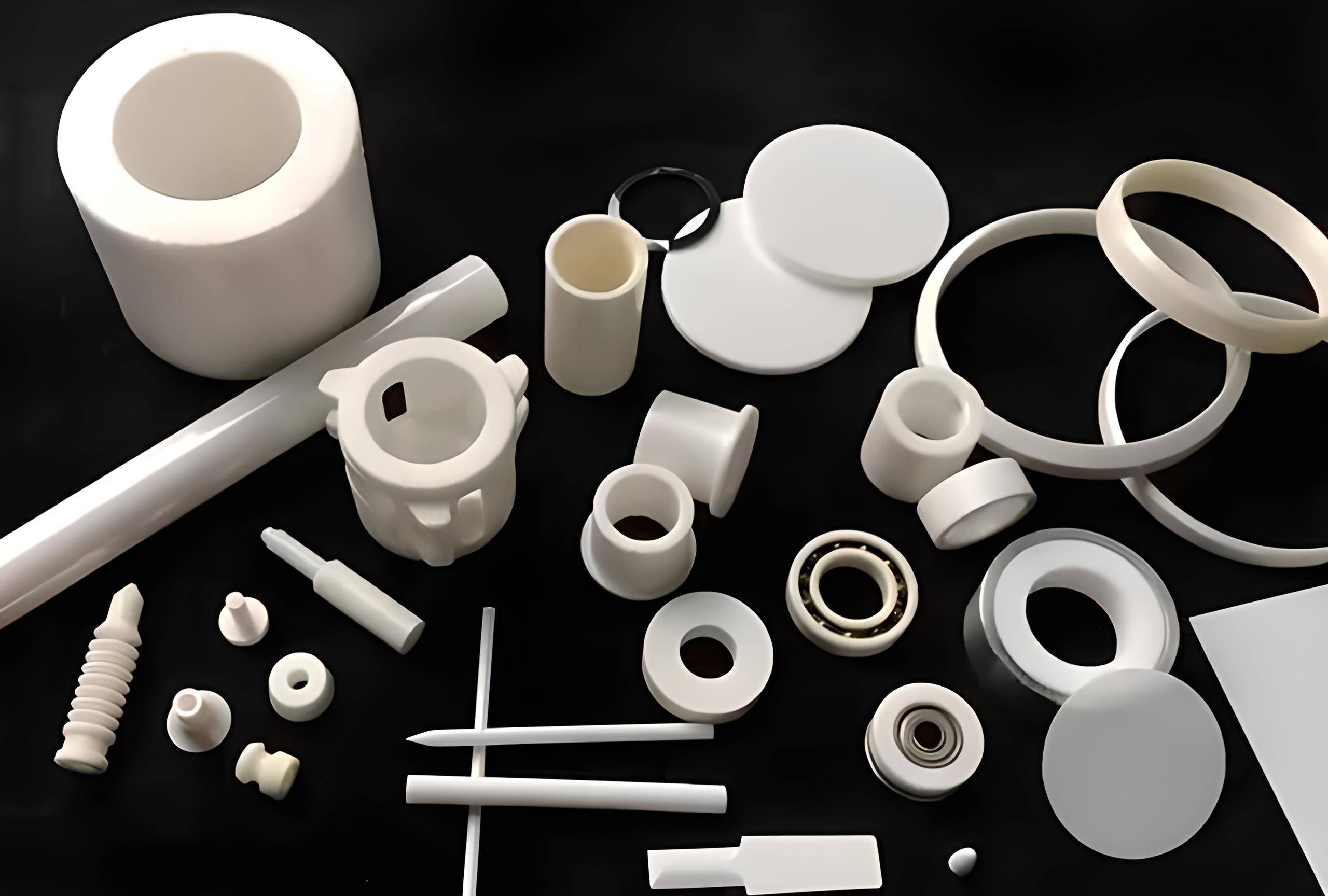
Durability and cost-effectiveness of the mould
The dry bag cold isostatic press machine utilizes an elastomeric mould, which offers durability and cost-effectiveness. The mould can be engineered to shape the powder into complex forms, and it can withstand the high pressures involved in the pressing process. This long-lasting mould reduces maintenance and replacement costs for businesses.
In summary, the dry bag cold isostatic press machine offers numerous advantages for businesses in various industries. From efficiency in automatic batch production to cost savings and environmental benefits, this machine provides a reliable and high-quality solution for powder forming processes. With its flexibility, capability, and durability, it is a valuable asset for businesses seeking to optimize their manufacturing processes.
Conclusion
In conclusion, the Dry Bag Cold Isostatic Press Machine by KinTek is a highly efficient and versatile piece of equipment that offers numerous benefits to various industries. With its optimal design and real-time monitoring capabilities, it ensures the production of high-quality products while maintaining safety standards. The machine's automatic batch production capability and flexibility in pressure settings contribute to cost savings in raw materials and electricity. Additionally, its durability and cost-effectiveness make it a worthwhile investment for businesses. Overall, the Dry Bag Cold Isostatic Press Machine provides a reliable and sustainable solution for powder forming processes.
CONTACT US FOR A FREE CONSULTATION
KINTEK LAB SOLUTION's products and services have been recognized by customers around the world. Our staff will be happy to assist with any inquiry you might have. Contact us for a free consultation and talk to a product specialist to find the most suitable solution for your application needs!