Introduction
Table of Contents
In the world of molding and manufacturing, it's crucial to understand the various technologies available. One such technology that has gained significant attention is the Warm Isostatic Press (WIP). This innovative process offers unique advantages in terms of molding quality and efficiency. By utilizing specific operating temperatures, the WIP can achieve exceptional results. In this blog post, we will delve into the intricacies of this technology, exploring how operating temperatures impact molding quality and efficiency. So, let's dive in and explore the fascinating world of the Warm Isostatic Press!
Understanding Warm Isostatic Press
Definition and use of warm isostatic press
Warm isostatic pressing (WIP) is a variant of cold isostatic pressing (CIP) that includes a heating element. It employs warm water or a similar medium to apply uniform pressure to powdered products from all directions. WIP is a cutting-edge technology that enables isostatic pressing at a temperature that does not exceed the boiling point of the liquid medium. This process typically involves utilizing flexible materials as a jacket mold and hydraulic pressure as a pressure medium to shape and press the powder material.
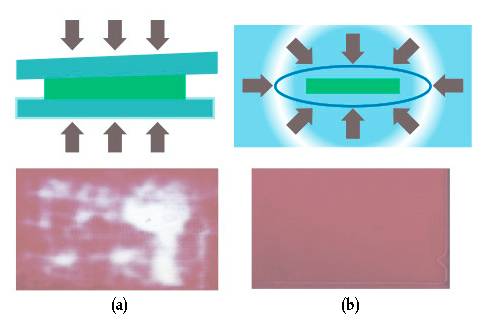
The warm isostatic press is usually heated to the liquid medium first, and then through the booster source, the heated liquid medium is continuously injected into the sealed pressing cylinder. The pressing cylinder is equipped with a heat generator to ensure the accuracy of temperature control requirements. This technique is generally used for powder, binder, and other materials with special temperature requirements, or materials that cannot be formed at room temperature.
Working parameters of warm isostatic press including working and ambient temperatures
The working parameters of the warm isostatic press include the working and ambient temperatures. The working temperature of the press refers to the temperature at which the liquid medium is heated and injected into the pressing cylinder. It is important to ensure that the working temperature does not exceed the boiling point of the liquid medium. The ambient temperature, on the other hand, refers to the temperature of the surrounding environment in which the warm isostatic press operates.
The working temperature of the warm isostatic press is typically set based on the temperature requirements of the materials being processed. It is crucial to maintain a precise working temperature to achieve the desired results. The ambient temperature, on the other hand, can affect the overall performance of the warm isostatic press. Extreme temperatures can impact the efficiency and effectiveness of the press, so it is important to operate it within the recommended ambient temperature range.
Working static pressure of warm isostatic press
The working static pressure is another important parameter of the warm isostatic press. It refers to the pressure applied to the powdered products during the pressing process. The working static pressure ensures that the powder material is evenly compressed from all directions, resulting in a uniform and high-quality final product.
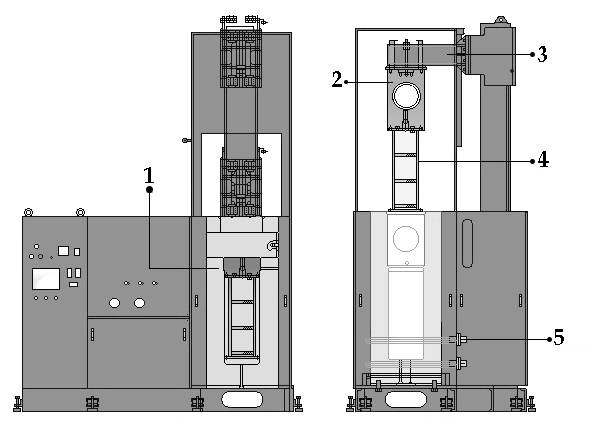
The working static pressure of the warm isostatic press is typically determined based on the specific requirements of the materials being processed. It is essential to apply the appropriate pressure to achieve the desired density and structural integrity of the final product. The working static pressure is carefully controlled and monitored throughout the pressing process to ensure consistent and reliable results.
In summary, warm isostatic pressing is a valuable technique for shaping and pressing powder materials at specific temperature requirements. By understanding the working parameters, including the working and ambient temperatures, as well as the working static pressure, businesses can utilize warm isostatic presses effectively to produce high-quality products.
Selection of Operating Temperature of Warm Isostatic Press
Dependency of operating temperature on powder material characteristics and molding requirements
The operating temperature of a warm isostatic press plays a critical role in achieving optimal molding results. The selection of the operating temperature depends on the characteristics of the powder material and the desired molding effect.
If the temperature is too low, the powder material may not be fully densified, leading to a lower quality finished product. On the other hand, if the temperature is too high, the powder material may be sintered or deformed, resulting in a loss of shape and integrity.
Therefore, it is crucial to determine the operating temperature of the warm isostatic press based on the specific requirements of the powder material and the desired molding quality. By finding the right balance, you can ensure both the efficiency and the quality of the molding process.
Implications of low and high operating temperatures on powder material
Operating the warm isostatic press at a low temperature can have adverse effects on the powder material. Insufficient densification may occur, leading to a weaker and less durable finished product. This can compromise the structural integrity and overall performance of the material.
Conversely, operating the press at a high temperature can result in sintering or deformation of the powder material. Sintering occurs when the powder particles bond together, altering the original structure and properties of the material. Deformation, on the other hand, can lead to dimensional inaccuracies and shape distortions.
To avoid these issues, it is essential to carefully consider the temperature requirements of the powder material and select the appropriate operating temperature for the warm isostatic press.
Importance of reasonable determination of operating temperature
Choosing the right operating temperature for a warm isostatic press is crucial for achieving the desired molding quality and efficiency. A reasonable determination of the operating temperature ensures the following:
-
Optimal densification: By setting the operating temperature within the appropriate range, you can ensure that the powder material is fully densified, resulting in a strong and durable final product.
-
Structural integrity: Operating the press at the right temperature prevents sintering and deformation of the powder material, preserving its original structure and properties. This ensures that the finished product meets the required specifications.
-
Efficient molding process: By selecting the optimal operating temperature, you can maximize the efficiency of the warm isostatic press. This leads to faster production cycles and increased productivity.
Warm isostatic press
In conclusion, the selection of the operating temperature for a warm isostatic press should be based on the specific characteristics of the powder material and the desired molding requirements. By finding the right balance, you can achieve optimal densification, maintain the structural integrity of the material, and enhance the efficiency of the molding process.
Conclusion
In conclusion, understanding the operating temperatures of a warm isostatic press is crucial for ensuring high-quality and efficient molding. The selection of the operating temperature depends on the powder material characteristics and molding requirements. It is important to strike a balance between low and high operating temperatures to avoid negative implications on the powder material. By reasonably determining the operating temperature, businesses can optimize their warm isostatic press processes and achieve the desired molding outcomes. So, make sure to consider the operating temperature carefully to achieve the best results for your molding needs.
If you are interested in this product you can browse our company website: https://kindle-tech.com/product-categories/isostatic-press, we always insist on the principle of quality first. During the production process, we strictly control every step of the process, using high quality materials and advanced production technology to ensure the stability and durability of our products. to ensure that their performance meets the highest standards. We believe that only by providing customers with excellent quality can we win their trust and long-term cooperation.
CONTACT US FOR A FREE CONSULTATION
KINTEK LAB SOLUTION's products and services have been recognized by customers around the world. Our staff will be happy to assist with any inquiry you might have. Contact us for a free consultation and talk to a product specialist to find the most suitable solution for your application needs!