Introduction: Importance of a High-Quality Sintering Oven
Investing in a high-quality sintering oven is crucial for dental laboratories that want to produce high-quality zirconia restorations consistently. The sintering process is a critical step in the production of zirconia restorations, and the quality of the oven used in the process can significantly impact the final product's strength and durability. A high-quality sintering oven should have programmable options for multiple zirconia types, proper temperature control for maximum strength, capacity for multiple sintering trays, safety measures for high-temperature sintering, and multiple program stages for varied results. In this blog post, we will explore the top five features of a high-quality zirconia sintering oven.
Table of Contents
- Introduction: Importance of a High-Quality Sintering Oven
- Feature 1: Programmable options for multiple zirconia types
- Feature 2: Proper Temperature Control for Maximum Strength
- Feature 3: Capacity for Multiple Sintering Trays
- Feature 4: Safety measures for high-temperature sintering
- Feature 5: Multiple Program Stages for Varied Results
- Conclusion: Investing in a High-Quality Sintering Oven
Feature 1: Programmable options for multiple zirconia types
A high-quality zirconia sintering oven has several key features that set it apart from the rest. One of the most important features is programmable options for multiple zirconia types. This feature allows the oven to be programmed to sinter different types of zirconia, each with its unique properties and requirements.
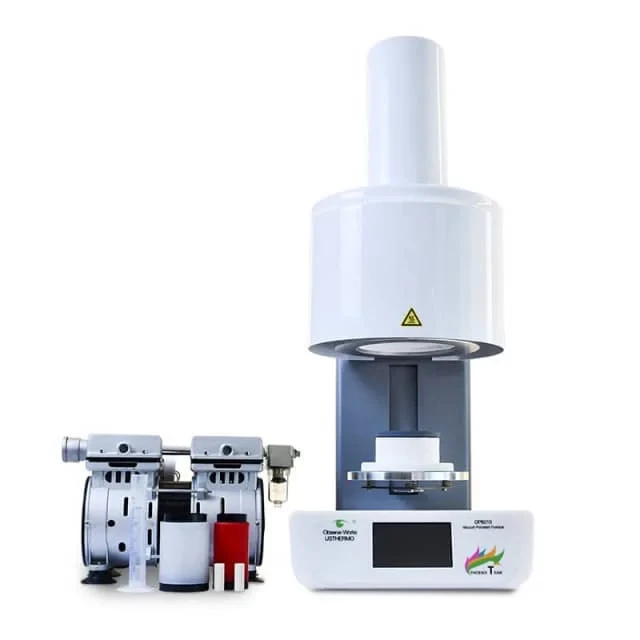
Benefits of Programmable Options
Programmable options for multiple zirconia types are not only convenient but also essential for producing consistent, high-quality results. Without programmable options for multiple zirconia types, the user would need to manually adjust the sintering parameters for each restoration, which would be time-consuming and prone to errors.
Customizable Parameters
A programmable oven allows the user to set the appropriate parameters for each type of zirconia, ensuring that each restoration is sintered to perfection. For example, some zirconia types require different sintering temperatures or hold times to achieve optimal results. With programmable options, the user can customize the parameters for each type of zirconia, ensuring that each restoration is sintered to perfection.
Time and Cost-Effective
Programmable options for multiple zirconia types are time and cost-effective. The user can easily switch between different types of zirconia without having to manually adjust the sintering parameters each time. This not only saves time but also reduces the risk of errors and improves the overall efficiency of the sintering process.
Consistent Results
Programmable options for multiple zirconia types ensure consistent results. By setting the appropriate parameters for each type of zirconia, the user can ensure that each restoration is sintered to perfection, resulting in a consistent and high-quality product. This feature is particularly important for dental labs that aim to produce precise and reliable zirconia restorations.
In conclusion, programmable options for multiple zirconia types are an essential feature of a high-quality zirconia sintering oven. This feature not only saves time and reduces the risk of errors but also ensures consistent and high-quality results. A programmable oven allows the user to customize the parameters for each type of zirconia, ensuring that each restoration is sintered to perfection.
Feature 2: Proper Temperature Control for Maximum Strength
Zirconia is a highly durable and biocompatible material that is widely used in dental restorations and other medical devices. However, to achieve maximum strength and durability, the zirconia must be sintered at precise temperatures for specific periods of time. A high-quality zirconia sintering oven should have advanced temperature control features such as programmable heating and cooling cycles, accurate temperature sensors, and automatic shut-off functions to prevent overheating.
Importance of Proper Temperature Control
Recent studies indicate that firing at approximately 1500°C - 1550°C produces maximum strength in zirconia. Firing above or below the recommended temperature by just 150°C can result in lower strengths due to grain growth. A higher temperature may result in lowered stability and uncontrolled transformation, causing cracking of the zirconia. Proper temperature control is critical to ensure that the zirconia is sintered at the optimal temperature for the proper amount of time, resulting in maximum strength and durability.
Temperature Sensors
A high-quality zirconia sintering oven should have accurate temperature sensors that can detect even the slightest changes in temperature. This helps in maintaining the desired temperature range throughout the sintering process. The temperature sensors must be calibrated regularly to ensure optimal performance.
Programmable Heating and Cooling Cycles
A high-quality zirconia sintering oven should have programmable heating and cooling cycles that can be customized according to the specific requirements of the zirconia material being used. This feature enables the operator to set the desired temperature range and dwell time for each cycle, ensuring that the sintering process is carried out precisely. The cooling cycle is equally important as the heating cycle, as it affects the final hardness and translucency of the zirconia.
Automatic Shut-off Functions
A high-quality zirconia sintering oven should have an automatic shut-off function that prevents overheating and damage to the zirconia material. This function is particularly important in case of power outages or other emergencies, as it ensures that the sintering process is stopped immediately to prevent any damage to the zirconia.
User-friendly Interface
A high-quality zirconia sintering oven should have a user-friendly interface that allows for easy programming and monitoring of the sintering process. The interface should be intuitive and easy to understand, with clear instructions and prompts to guide the operator through each step of the process.
In conclusion, proper temperature control is a crucial feature of a high-quality zirconia sintering oven. With advanced temperature control features such as accurate temperature sensors, programmable heating and cooling cycles, automatic shut-off functions, and a user-friendly interface, a high-quality zirconia sintering oven can produce dental restorations and other medical devices that are strong, durable, and long-lasting.
Feature 3: Capacity for Multiple Sintering Trays
One of the most important features of a high-quality zirconia sintering oven is its ability to accommodate multiple sintering trays. This feature is particularly important for laboratories that need to sinter a large number of zirconia restorations simultaneously.
Benefits of Multi-Tray Capacity
With a multi-tray capacity, labs can increase their productivity and reduce processing time, allowing them to take on more cases and meet the demands of their clients. The number of trays a sintering oven can hold may vary depending on the model, but the best ones can accommodate up to five or more trays. This means that labs can sinter several crowns, bridges, and other dental restorations at once, without sacrificing the quality of the sintering process.
Uniform Heating and Cooling
The trays in a high-quality sintering oven are designed to ensure uniform heating and cooling of the zirconia, resulting in a consistent and reliable sintering outcome. The trays are also made of durable materials that can withstand high temperatures and repeated use, ensuring longevity and cost-effectiveness.
Ideal Muffle Capacity
Muffle capacity is another area that can be important based on your laboratory’s production needs. Some furnaces allow only one sintering tray to be used per cycle, many offer the space for two, but the ideal space will accommodate 6 trays vertically stacked, enabling the processing of 60+ units and even Prettau bridges.
Increased Safety
Safety is another important feature to consider when investing in a sintering oven. These furnaces climb to extraordinarily high temperatures and they hold there for a long time. And they use high amperage to do it.
Conclusion
In summary, the capacity for multiple sintering trays is a crucial feature that labs should look for when investing in a zirconia sintering oven. It offers numerous benefits, including increased productivity, reduced processing time, and consistent sintering outcomes, making it an essential tool for any laboratory that specializes in producing high-quality dental restorations. By incorporating this feature, dental labs can meet their production demands and ensure the safety of their technicians while producing high-quality restorations that meet the needs of their clients.
Feature 4: Safety measures for high-temperature sintering
Sintering process requires extreme heat that can pose a risk to the operator and the environment. Therefore, a high-quality zirconia sintering oven should have safety measures in place to ensure safe and efficient sintering.
Automatic shut-off mechanisms and temperature sensors
A high-quality sintering oven should have automatic shut-off mechanisms and temperature sensors that prevent overheating and potential accidents. These safety features not only protect the operator but also prevent the oven from being damaged due to overheating.
Heat-resistant door and proper ventilation
The door of the sintering oven should be constructed with materials that can withstand high temperatures and prevent heat from escaping. Additionally, the oven should be designed with proper ventilation to minimize the risk of harmful fumes and gases being released during the sintering process. This safety measure ensures that the operator is not exposed to harmful gases and fumes during the process.
Protection against contamination and damage
Safety measures should also be in place to protect the zirconia restoration from any contamination or damage. Contamination can occur due to the release of gases or fumes during the sintering process. Therefore, the oven should be designed in such a way that it minimizes the risk of contamination. Additionally, the restoration should be protected from damage due to overheating or other accidents.
Importance of safety measures
Safety measures are crucial in a sintering oven because they prevent accidents and ensure that the sintering process is carried out efficiently. A malfunctioning sintering oven can not only damage the restoration but also pose a risk to the operator and the environment. Therefore, it is important to invest in a high-quality sintering oven that has all the necessary safety measures in place.
Conclusion
Safety measures are crucial in a high-quality zirconia sintering oven. Automatic shut-off mechanisms, temperature sensors, heat-resistant door, proper ventilation, and protection against contamination and damage are some of the key safety features that a sintering oven should have. These features not only ensure the safety of the operator and the environment but also help to carry out the sintering process efficiently.
Feature 5: Multiple Program Stages for Varied Results
A high-quality zirconia sintering oven is an essential tool for any dental laboratory. When choosing a sintering oven, there are several features to consider. One important feature is the ability to have multiple program stages for varied results.
Customizing the Sintering Process
This feature allows the user to customize the sintering process, resulting in more precise and consistent outcomes. With multiple program stages, the user can set different temperatures and hold times for each stage, allowing for the creation of complex dental restorations with varying levels of translucency and strength.
Saving Time and Increasing Efficiency
Additionally, this feature can save time and increase efficiency in the laboratory, as multiple jobs can be run simultaneously with different program stages. This means that the user can start one job, set the first stage of the program, and then move on to another job while the first one is sintering.
Choosing the Right Program
When choosing the right program, it's important to consider the type of restoration being made, the type of zirconia being used, and the desired translucency and strength. Different programs will have different temperatures, hold times, and ramp rates, and understanding how these factors affect the final product is crucial for achieving the desired result.
Older Laboratories Need More Programs
Nowadays, every new furnace seems to have more programs. It's not uncommon for a furnace to offer 200 programs. An older, established laboratory probably needs this kind of furnace more than a laboratory just starting out. An older laboratory often needs to support many older materials.
Manual vs. Digital Furnace Settings
Deciding whether to get a furnace with manual/analog settings versus digital settings really depends on who will operate the furnace. Less technologically savvy technicians will be more comfortable with setting programs manually, rather than needing to learn and adapt to digital settings and touchscreens.
In conclusion, a high-quality zirconia sintering oven with multiple program stages is a valuable investment for any dental laboratory looking to improve their precision, consistency, and efficiency in the creation of dental restorations. With the ability to customize the sintering process and run multiple jobs simultaneously, this feature can save time and increase efficiency in the laboratory. When choosing the right program, it's important to consider the type of restoration being made, the type of zirconia being used, and the desired translucency and strength.
Conclusion: Investing in a High-Quality Sintering Oven
Investing in a high-quality sintering oven is crucial for any dental laboratory looking to produce quality restorations. A sintering oven with programmable options for multiple zirconia types, proper temperature control for maximum strength, capacity for multiple sintering trays, safety measures for high-temperature sintering, and multiple program stages for varied results is essential. Not only does a high-quality sintering oven increase the efficiency and productivity of the laboratory, but it also ensures that the restorations produced are of the highest quality. Overall, investing in a high-quality sintering oven is a smart decision that can save time and money in the long run.
CONTACT US FOR A FREE CONSULTATION
KINTEK LAB SOLUTION's products and services have been recognized by customers around the world. Our staff will be happy to assist with any inquiry you might have. Contact us for a free consultation and talk to a product specialist to find the most suitable solution for your application needs!