Introduction
Table of Contents
- Introduction
- Market Driver: Combining HIP With Other Heat Treatment Processes
- Market Restraint: High Initial Investment Requirement
- Market Opportunity: Rising Demand for Low-cost Titanium in Automotive Industry
- Market Challenge: Limited Size and Shape Capabilities of Isostatic Pressing
- Market Segmentation: Services Segment and HIP Segment
- Trending Sectors: Medical Industry
- Key Market Players
- Conclusion
Isostatic pressing, is a manufacturing process that involves applying high-pressure gas to a material in order to shape and consolidate it. This technique is widely used in various industries, including aerospace, automotive, and medical, due to its ability to produce high-quality, defect-free components. In this blog post, we will analyze the isostatic pressing market, including its drivers, restraints, opportunities, challenges, market ecosystem, segmentation, trending sectors, and key market players. So let's dive in and explore the fascinating world of isostatic pressing!
Market Driver: Combining HIP With Other Heat Treatment Processes
The hot isostatic pressing (HIP) market is experiencing substantial growth, driven by various factors. Industries such as aerospace, automotive, medical, energy, and manufacturing increasingly demand reliable, high-performance components. As a response, there is a notable adoption of HIP technology, which provides advanced manufacturing solutions to enhance material properties and component performance. Moreover, advancements in materials, alloys, and improvements in HIP equipment technology further facilitate market expansion. The industry's focus on cost efficiency, waste reduction, and sustainable manufacturing practices supports the market’s growth.
Advancements in HIP equipment
HIP's industrial base is ever expanding as the demand for improved material properties, the use of powder materials, and the desire to produce net or near net shape parts accelerates. Improvements in HIP equipment, the shortening of processing times, and the ever-improving economics make the HIP process a more viable choice for an ever-increasing array of materials.
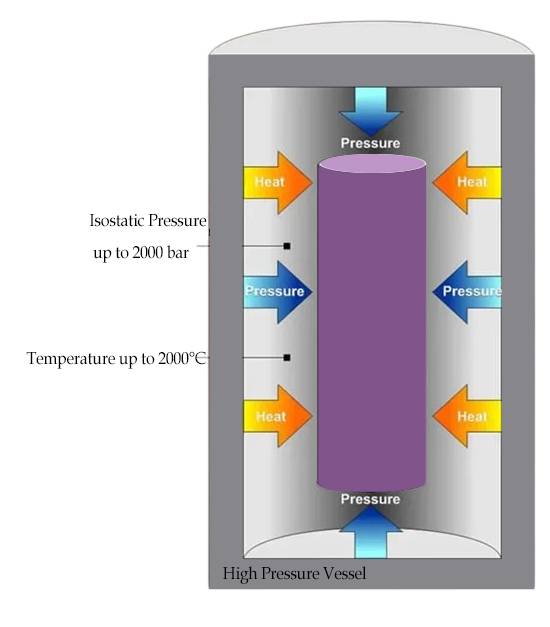
Implementation of combined techniques in the aerospace and nuclear sectors
The HIP and heat treatment processes in a conventional practice are carried out at different facilities, where the parts have to be loaded and unloaded into process vessels twice and shipped from one facility to another, which consumes time. Thus, combining HIP and other heat treatment processes in a single and integrated unit can help reduce energy consumption and meet the components' delivery time. The constant improvements in HIP equipment from the 1970s have led to advanced processing options, such as rapid cooling capability and automatic processing.
For instance, processes such as HIP, additive manufacturing, and spark plasma sintering can be used as a single unit to create high-integrity, near-net-shaped parts from metal powder while reducing processing costs and energy consumption. Processing economics, as well as some final material properties, have greatly benefited from the development of advanced cooling technology. By utilizing the highly convective nature of argon gas, combined with the ability to build multiple layer vessels with internal cooling and advanced furnace designs, large loads in HIP cycles are able to cool down faster.
With rates possible up to 500°C per minute, this hundredfold increase in cooling rates has cut many process cycles by more than half and has also allowed for the possibility of combining the HIP cycle with a solution heat treatment. This ability to gas quench rather than liquid quench can minimize distortion and part cracking, minimize surface reactions, and provide for more homogenous properties throughout the part.
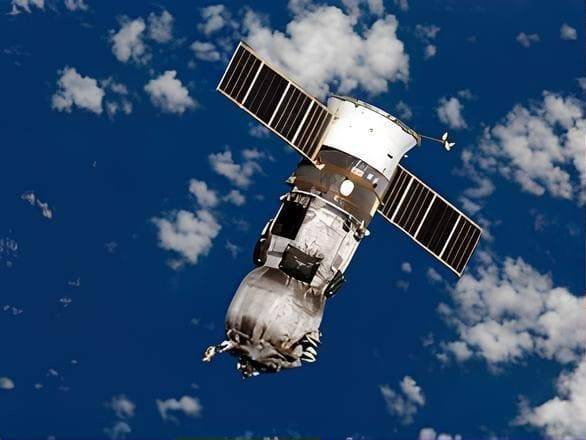
Market Restraint: High Initial Investment Requirement
Barrier to entry for new market players
Entering the market for isostatic pressing requires a significant initial investment. This includes acquiring advanced machinery, specialized technologies, and high-pressure vessels. The costs associated with establishing an isostatic pressing facility can be substantial, making it difficult for new players to enter the market. This barrier to entry contributes to a competitive landscape that is dominated by established companies.
Justification of investment through long-term market growth and demand
Despite the high initial costs, investing in isostatic pressing can be justified by the potential for long-term benefits. The market for isostatic pressing is expected to experience significant growth in the coming years. The ability to meet the increasing demand for high-quality components makes the investment in isostatic pressing worthwhile.
Isostatic pressing offers several advantages that make it an attractive option for manufacturers. These include:
- Lowest initial capital equipment investment cost.
- Adequate process control, ensuring repeatability.
- Capability of high-volume output using a wide variety of equipment styles and types.
- Full automation capability, allowing for precise control of heat treat cycles.
- Well-understood process problems, enabling effective troubleshooting.
Isostatic pressing also offers versatility and scalability. KINTEK, for example, specializes in process scale-up, designing systems that can accommodate mass rates ranging from tens to thousands of pounds per hour.
In terms of compliance and quality, isostatic pressing equipment is designed to meet the stipulations of cGMP (current Good Manufacturing Practice). Product contact parts are made of high-quality materials such as AISI 316/316L.
Despite its advantages, isostatic pressing is not without its limitations. Some of these include the need to run the equipment continuously, the requirement for conditioning the furnace atmosphere if it is idled or shut down, and the operator-dependent nature of the knowledge required to achieve repeatable results.
Additionally, post-processing operations may be necessary to accommodate dimensional changes and finish requirements, leading to large material stock allowances. The quality of the case produced through isostatic pressing can also be compromised, as post-heat-treatment operations such as grinding may remove the area of highest hardness.
Environmental considerations, such as air and water quality, waste disposal, and safety issues related to the combustible atmosphere and quench oils, must be carefully monitored.
Despite these limitations, the potential for long-term market growth and the ability to meet the demand for high-quality components make the investment in isostatic pressing a worthwhile endeavor.
Market Opportunity: Rising Demand for Low-cost Titanium in Automotive Industry
Benefits of using titanium and its alloys
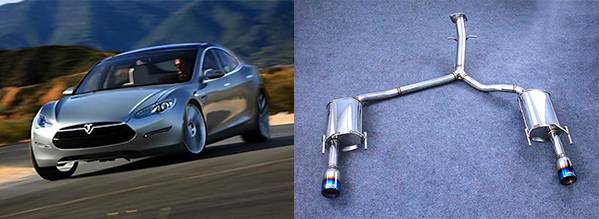
Titanium and its alloys offer several advantages that make them highly desirable for use in the automotive industry. These benefits include:
-
Lightweight: Titanium is known for its low density, which makes it one of the lightest metals available. Using titanium and its alloys in automobile applications can significantly reduce the overall weight of the vehicle, leading to improved fuel efficiency and better performance.
-
Corrosion resistance: Titanium exhibits exceptional corrosion resistance, even in harsh environments. This property makes it an ideal choice for components that are exposed to moisture, chemicals, and other corrosive elements.
-
High strength: Despite its lightweight nature, titanium boasts impressive strength. It has a high strength-to-weight ratio, making it suitable for applications that require structural integrity and durability.
-
Heat resistance: Titanium can withstand high temperatures without losing its mechanical properties. This characteristic makes it suitable for components that are exposed to extreme heat, such as engine parts and exhaust systems.
Cost reduction through HIP processes
One of the main challenges associated with using titanium in the automotive industry is its high cost. However, manufacturers are actively seeking innovative ways to produce low-cost titanium and its alloys to overcome this hurdle. One such method is the use of Hot Isostatic Pressing (HIP) processes.
HIP processes involve subjecting titanium and its alloys to high temperatures and pressure in a sealed container. This process helps eliminate defects and improve the mechanical properties of the material. Additionally, HIP processes enable the
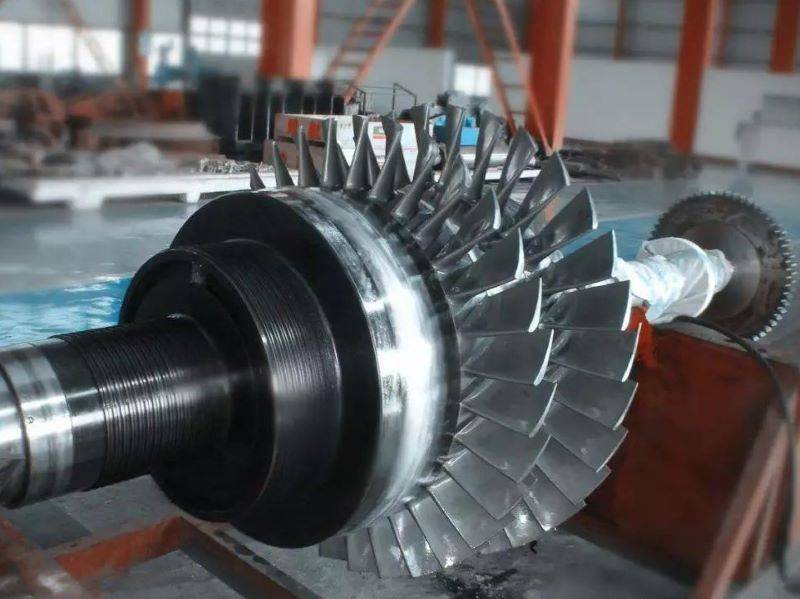
production of complex-shaped components with reduced manufacturing time and cost compared to conventional methods.
The cost-related benefits of HIP processes have led to increased adoption in the manufacturing of titanium alloys for the automotive industry. This trend is expected to create lucrative opportunities for market players in the coming years.
Hot isostatic pressing segment to hold largest market share in the year 2022
The hot isostatic pressing (HIP) market is experiencing significant growth, driven by various factors. Industries such as aerospace, automotive, medical, energy, and manufacturing are increasingly demanding reliable, high-performance components. In response to this demand, there has been a notable adoption of HIP technology, which provides advanced manufacturing solutions to enhance material properties and component performance.
Advancements in materials, alloys, and improvements in HIP equipment technology further facilitate the expansion of the market. The industry's focus on cost efficiency, waste reduction, and sustainable manufacturing practices also supports the growth of the HIP market.
HIP has diverse applications in industries such as aerospace, automotive, energy, medical, and tooling. It is used for manufacturing critical components like turbine blades, engine parts, medical implants, tool steels, and advanced materials such as super alloys and ceramics.
Rise in demand for high-performance materials and complex-shaped components
The increasing demand for high-performance materials and complex-shaped components is expected to drive the adoption of HIP in the near future. As industries continue to prioritize efficiency, durability, and lightweight design, the need for advanced manufacturing processes like HIP becomes crucial.
By utilizing HIP processes, manufacturers can produce components with improved mechanical properties, enhanced performance, and reduced costs. This trend aligns with the growing demand for high-performance materials and complex-shaped components in various industries, including automotive.
Market Challenge: Limited Size and Shape Capabilities of Isostatic Pressing
Isostatic pressing is a manufacturing process that offers various advantages, such as uniform density and shape flexibility. However, it also comes with certain limitations in terms of size and shape capabilities. These limitations can pose challenges in certain applications. Let's explore these challenges in detail:
Suitability for small and medium-sized parts
Isostatic pressing is typically best suited for small to medium-sized parts. The process involves subjecting the powder material to uniform pressure from all directions, resulting in a compacted piece. This method is more effective for smaller parts, as achieving uniform pressure distribution becomes more challenging with larger parts.
Difficulty in manufacturing complex shapes
While isostatic pressing allows for the production of shapes and dimensions that are difficult to achieve by other methods, it can be more challenging to manufacture complex shapes using this process. The powder material needs to be evenly distributed in the mold to ensure uniform density. Achieving this uniform distribution becomes more difficult as the complexity of the shape increases.
Cost implications of tooling
The tooling cost required for isostatic pressing can be significant, especially for parts with complex shapes. The molds used in the process need to be designed and manufactured according to the specific shape requirements. This can result in higher tooling costs, making the process less cost-effective for parts with irregular shapes.
Despite these challenges, isostatic pressing offers several benefits that make it a valuable manufacturing solution. Let's explore some of these advantages:
- Uniform density: Isostatic pressing results in a compacted piece with uniform shrinkage during sintering or hot isostatic pressing, minimizing warpage.
- Shape flexibility: Isostatic pressing enables the production of shapes and dimensions that may be difficult or impossible to achieve using other methods.
- Wide range of component sizes: Isostatic pressing can be used to manufacture a wide range of component sizes, from massive near net PM shapes to smaller MIM parts.
- Low tooling cost: For short production runs, the tooling cost associated with isostatic pressing is generally lower compared to other manufacturing methods.
- Enhanced alloying possibilities: Isostatic pressing allows for the incorporation of alloying elements without inducing material segregation.
- Reduced lead times: Isostatic pressing enables the economical production of complex shapes from prototype to production quantities, resulting in significantly reduced lead times compared to forgings or machined components.
- Material and machining cost reduction: Near net shape parts produced through isostatic pressing can greatly reduce material and machining costs.
The growing versatility and adaptability of isostatic pressing are driving its demand in various industries. Additionally, the increasing adoption of additive manufacturing has further fueled the demand for isostatic pressing as a post-processing technique. The combination of additive manufacturing and isostatic pressing provides a comprehensive solution for the production of complex and functional parts.
Despite the market challenges, the isostatic pressing industry is expected to witness growth in the coming years. The demand for products with short production cycles in the healthcare sector and the surge in demand for low-cost spare parts manufacturing techniques in the automotive sector are driving this growth. However, high initial investments required for hot isostatic pressing can hinder its demand in developing countries.
In conclusion, while isostatic pressing has limitations in terms of size and shape capabilities, it offers unique advantages that make it a valuable manufacturing process. The industry continues to evolve, addressing these challenges and providing advanced manufacturing solutions.
Market Segmentation: Services Segment and HIP Segment
Increasing applications in various industries
HIP's industrial base is ever-expanding as the demand for improved material properties, the use of powder materials, and the desire to produce net or near-net shape parts accelerates. Improvements in HIP equipment, the shortening of processing times, and the ever-improving economics make the HIP process a more viable choice for an ever-increasing array of materials.
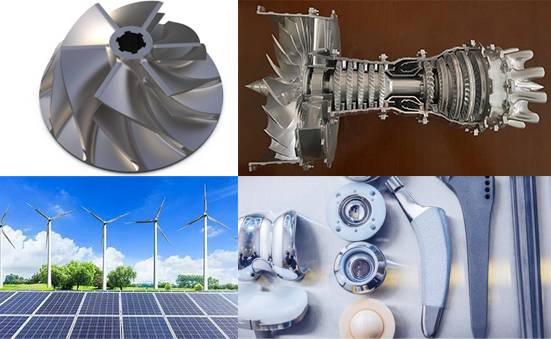
HIP has applications in various industries, including aerospace, automotive, energy, medical, and tooling. It is used for manufacturing critical components such as turbine blades, engine parts, medical implants, tool steels, and advanced materials such as super alloys and ceramics.
Rise in demand for high-performance materials and complex-shaped components is expected to drive the adoption of HIP in the near future.
Growth in the HIP market
The hot isostatic pressing (HIP) market is experiencing substantial growth, driven by various factors. Industries such as aerospace, automotive, medical, energy, and manufacturing increasingly demand reliable, high-performance components. As a response, there is a notable adoption of HIP technology, which provides advanced manufacturing solutions to enhance material properties and component performance. Moreover, advancements in materials, alloys, and improvements in HIP equipment technology further facilitate market expansion. The industry's focus on cost efficiency, waste reduction, and sustainable manufacturing practices supports the market’s growth.
The hot isostatic pressing segment is projected to hold the largest market share in the year 2022.
Isostatic Pressing Market
By Offering
The services segment is projected as one of the most lucrative segments. The isostatic pressing market share is analyzed by offering, type, HIP capacity, CIP process type, application, and region. On the basis of offering, it is fragmented into services and systems. The systems segment dominated the market, in terms of revenue in 2019, and is expected to follow the same trend during the forecast period.
By Type
On the basis of type, it is segregated into hot isostatic pressing (HIP) and cold isostatic pressing (CIP). The hot isostatic pressing (HIP) segment dominated the market, in terms of revenue in 2019; however, the cold isostatic pressing (CIP) segment is projected to witness significant market share during the forecast period.
By HIP Capacity
By HIP capacity, it is divided into small-sized HIP, medium-sized HIP, and large-sized HIP. The global isostatic pressing market share of the large-sized HIP segment accounted for the highest in 2019 and is expected to follow the same trend during the forecast period.
By CIP Process Type
By CIP process type, it is bifurcated into dry-bag pressing and wet-bag pressing. The dry pressing bag segment accounted for a major share in the global isostatic pressing market in 2019; however, the wet-bag pressing segment is expected to witness the highest CAGR during the forecast period.
Regional Outlook of Global Isostatic Pressing Industry
As per isostatic pressing market trends, Asia Pacific accounted for the largest share of the global isostatic pressing market in 2022. This is ascribed to the rise in industrialization, infrastructural development, and an increase in investment in sectors such as aerospace, automotive, and energy.
Trending Sectors: Medical Industry
Adoption of new technologies
The players in the medical industry are continuously adopting new technologies, such as additive manufacturing or 3D printing, in a wide range of applications. One such technology is Cold Isostatic Pressing (CIP), which is gaining traction in the medical sector. CIP is a materials handling strategy in which high pressure is applied to metal powder in a fixed elastomer compartment molded for the application. It is used for the consolidation of 3D-printed parts, ceramic powders, and other fine or advanced grades of ceramics used in the dental and medical sectors. CIP is essential for developing artificial bone, artificial tooth material, and resin powder, as it allows for the creation of complex shapes with uniform and high-density parts.
Use of CIP for developing medical parts
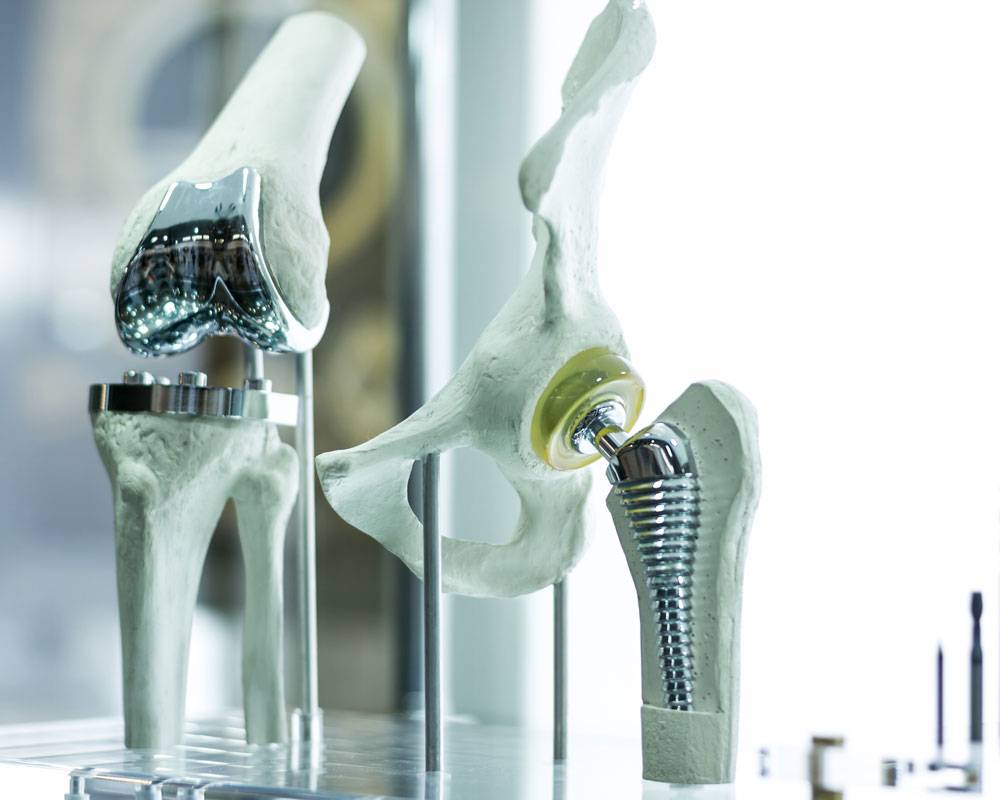
The use of CIP in the medical industry is driven by the need for advanced materials and manufacturing techniques. CIP helps in the development of artificial bone, artificial tooth material, and resin powder, which are used in various medical applications. The medical industry requires complex shapes with uniform and high-density parts, and CIP provides the necessary capabilities to achieve this. Additionally, CIP is also used in other industries such as pharmaceutical, food, and environmental protection, due to its wide application and high adaptability.
According to market projections, the medical industry is expected to register the highest compound annual growth rate (CAGR) during the forecast period. This growth is driven by the continuous adoption of new technologies and the increasing demand for complex and high-quality medical parts. As the medical industry continues to evolve, the use of technologies like CIP will play a crucial role in shaping its future.
In conclusion, the adoption of new technologies, such as CIP, is revolutionizing the medical industry. This technology allows for the development of complex shapes with uniform and high-density parts, which are essential for various medical applications. The use of CIP in the medical industry is expected to grow significantly in the coming years, driven by the need for advanced materials and manufacturing techniques. As the medical industry continues to evolve, the use of technologies like CIP will play a crucial role in improving patient care and advancing medical innovation.
Key Market Players
Organic and inorganic growth strategies
Isostatic pressing companies have implemented various organic and inorganic growth strategies to strengthen their offerings in the market. These strategies include:
- Product launches
- Collaborations
- Partnerships
- Acquisitions
These initiatives have helped the key market players in expanding their market presence and staying competitive in the industry.
Conclusion
In conclusion, the Isostatic Pressing market is driven by advancements in HIP equipment and the implementation of combined techniques in sectors such as aerospace and nuclear. However, the market faces the challenge of a high initial investment requirement, which acts as a barrier to entry for new players. Despite this, the rising demand for low-cost titanium in the automotive industry presents a significant opportunity for growth. The limited size and shape capabilities of Isostatic Pressing pose challenges, particularly in manufacturing complex shapes. Nonetheless, the market segmentation of services and HIP segments continues to witness growth with increasing applications in various industries. Additionally, the medical industry is a trending sector, adopting new technologies and utilizing CIP for developing medical parts. Overall, the Isostatic Pressing market offers promising opportunities for both existing and new market players.
If you are interested in our products, please visit our company website:https://kindle-tech.com/product-categories/isostatic-press, where innovation has always been a priority. Our R&D team consists of experienced engineers and scientists who closely follow industry trends and are constantly pushing the boundaries of what is possible. Our laboratory equipment incorporates the latest technology to ensure that you can obtain accurate and repeatable results during your experiments. From high-precision instruments to intelligent control systems, our products will provide you with unlimited possibilities for your experimental work.
CONTACT US FOR A FREE CONSULTATION
KINTEK LAB SOLUTION's products and services have been recognized by customers around the world. Our staff will be happy to assist with any inquiry you might have. Contact us for a free consultation and talk to a product specialist to find the most suitable solution for your application needs!