Introduction to Vacuum Pressure Sintering Furnace
Vacuum pressure sintering furnace is a revolutionary technology that has transformed the manufacturing industry, offering numerous advantages and applications. This article will delve into the basic principle and components of the furnace, shedding light on how vacuum sintering promotes material reorganization at the microscopic level, resulting in dense structures and superior performance while preventing oxidation and pollution effects. As we explore the benefits, working principle, and applications of vacuum pressure sintering, it becomes evident that this technology is a game-changer for various industries, offering clean, bright parts, incredible design flexibility, and maximum productivity. Let's embark on a journey to uncover the incredible potential of vacuum pressure sintering furnace.
Benefits of Vacuum Pressure Sintering Furnace
Discover the clean, bright parts, incredible design flexibility, quick turnaround, superior quality, fewer defects, easy maintenance, and maximum productivity offered by vacuum sintering. Learn how it is an efficient way to join delicate and intricate parts with minimal waste.
What Is a Vacuum Sintering Furnace?
Sintering is defined as creating a solid material mass using heat and pressure – without liquefying the material. Vacuum sintering is a heat treatment used to join parts with the least waste to produce consistent components without seams, fillers, or joints. The components treated using a vacuum sintering furnace are often intricate, delicate, and tricky to make.
Benefits of vacuum sintering include:
-
Temperature and pressure limits can be chosen during the engineering phase and controlled manually or automatically during processing.
-
Vacuum furnaces can be built to perform both debinding and sintering, saving time and money by eliminating the need for part transfer, secondary machinery, or resources wasted on a repetitive process.
-
Perfect for higher temperature sintering applications, vacuum furnaces offer highly customizable controls for manual or automatic temperature changes depending on project needs, ensuring uniform temperature and consistent part quality.
Advantages of Vacuum Sintering Furnace
Vacuum sintering reduces the contamination of harmful substances (such as water, oxygen, nitrogen, and other impurities) in the atmosphere, thus avoiding adverse reactions like decarburization, carburization, reduction, oxidation, and nitriding. The vacuum environment surpasses other sintering methods, with residual gas purity reaching equivalent to 99.99987% argon when vacuum pressure reaches 1.3*10^-1 Pascal.
Vacuum Sintering Furnace
Small or complex parts are difficult to produce by casting or machining. Components requiring sintering are often delicate, intricate, and prone to errors. Vacuum sintering efficiently joins parts with minimal waste, producing consistent, bright parts with no seams, joints, or fillers. Technologies like powdered metal, metal injection molding, and 3D printing benefit greatly from the superior quality and flexibility of vacuum sintering.
Benefits of a Vacuum Sintering Furnace
- Clean, bright parts
- Incredible design flexibility
- Quick turnaround
- Superior quality
- Fewer defects
- Easy maintenance
- Maximum productivity
Working Principle of Vacuum Pressure Sintering
The process of vacuum pressure sintering plays a crucial role in achieving the binding of materials through atom migration. This innovative technology utilizes induction sintering to heat materials, effectively reducing the presence of harmful substances such as water vapor, oxygen, nitrogen, and other impurities in the atmosphere. By minimizing these impurities, a series of reactions including decarbonization, nitriding, carburizing, reduction, and oxidation are avoided, resulting in a tighter bond between materials and enhancing wear resistance and strength. The reduction of gas in the pores and the removal of oxide film on material surfaces contribute to the improved quality and performance of the sintered products. Additionally, vacuum induction sintering has been noted for its ability to reduce product cost, making it an economically advantageous process.
In a vacuum environment, the relatively low gas content reduces the impact of convection and conduction of heat, with heat primarily transmitted from the heating module to the material surface through radiation. The selection of a suitable heating module based on the specific sintering temperature and the physical and chemical characteristics of the material is crucial. Compared to vacuum resistance heating, induction sintering using medium frequency power supply heating helps mitigate the high temperature insulation challenges associated with vacuum furnaces that utilize resistance internal heating mode.
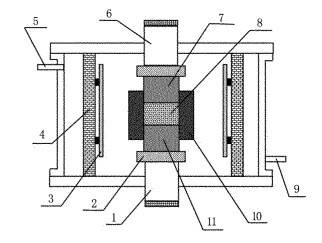
Temperature and pressure limits play a pivotal role in the engineering phase and can be controlled manually or automatically during the processing stage. Vacuum furnaces are engineered to perform both debinding and sintering, effectively saving time and resources by combining these processes in a single furnace. This integration eliminates the need for part transfer, secondary machinery, or wastage of resources on repetitive processes.
The utilization of vacuum furnaces is particularly advantageous for higher temperature sintering applications. These furnaces offer highly customizable controls that enable manual or automatic temperature adjustments based on the specific project requirements. The uniform temperature distribution within the vacuum furnace ensures consistent part quality, contributing to the overall reliability and performance of the sintered products.
The debinding process within the vacuum furnace plays a critical role in removing binder materials that can contaminate the furnace and the final product. While binding materials are essential for individual part compaction, they become unnecessary and detrimental during the sintering process. By eliminating these binders, the sintering process is optimized, leading to the production of clean, high-quality parts.
Vacuum sintering requires a high vacuum environment to ensure the production of clean and high-quality parts. The temperature must be carefully controlled to facilitate the smooth combination of metals without reaching a liquefaction point. The cooling speed post-sintering is dependent on the specific material properties and requirements.
The vacuum sintering furnace, a high-temperature, high-pressure, and low-pressure sintering device, is primarily utilized for the preparation of high-performance ceramics, metals, and composite materials. This furnace typically consists of a furnace body, heating device, vacuum system, and control system. Its fundamental principle revolves around sintering powder or lump material under high temperature, vacuum, or inert gas environment, promoting material reorganization at the microscopic level and recrystallization. This process results in the formation of a dense structure with excellent performance characteristics while mitigating undesirable effects such as oxidation and pollution on the material.
By understanding the working principle of vacuum pressure sintering and the intricacies of vacuum furnaces, manufacturers and researchers can leverage these advanced technologies to optimize the sintering process, enhance product quality, and achieve cost efficiencies in material preparation and production.
Applications and Functions of Vacuum Hot Press Furnace
Vacuum hot press furnaces play a crucial role in various scientific and industrial applications, offering precise control over temperature, pressure, and atmosphere. These furnaces are indispensable for hot-press sintering experiments in vacuum or protected atmospheres, facilitating the development and production of advanced materials. Let's delve into the applications and functions of vacuum hot press furnaces in detail:
Applications
1. Powder Metallurgy and Functional Ceramics: Vacuum hot press furnaces are extensively used for high-temperature hot forming of new materials such as powder metallurgy and functional ceramics. These furnaces enable the vacuum sintering of transparent ceramics, industrial ceramics, and metals, including alloy materials composed of refractory metals.
2. Sintering of Ceramic Materials: Materials like silicon carbide and silicon nitride undergo high-temperature sintering in vacuum hot press furnaces. This process enhances their mechanical properties and enables the production of advanced ceramic components with precise dimensional control.
3. Heat Treatment of Powders and Compacts: Vacuum hot press furnaces facilitate the heat treatment of powders and compacts below their melting points. This metallurgical process improves the strength of materials through particle bonding, enhancing their suitability for various applications.
4. Research and Development: These furnaces serve as indispensable tools in research and development activities, offering a controlled environment for studying material behaviors under high temperatures and pressures. They enable scientists and engineers to explore novel materials and fabrication techniques with unparalleled precision.
Functions
1. Highest Working Temperature: Vacuum hot press furnaces boast a remarkable maximum working temperature of up to 2200 degrees Celsius. This high temperature capability allows for the processing of a wide range of materials, including those requiring extreme heat conditions for sintering and densification.
2. Precision Control System: Equipped with a high-precision control system, these furnaces enable precise regulation of temperature, pressure, and suppression rate during hot-press sintering processes. This level of control ensures reproducibility and consistency in material properties, essential for research and industrial production.
3. Adjustable Working Pressure: The furnaces feature up and down suppress oils, allowing for the adjustment of working pressure according to specific technical requirements. This flexibility enables tailored processing conditions to meet the needs of different materials and applications, ensuring optimal performance and quality.
4. Temperature Stability: With adjustable temperature settings, vacuum hot press furnaces can maintain a constant temperature for extended periods, ensuring uniform heating and precise control over the sintering process. This temperature stability is critical for achieving desired material properties and avoiding defects in the final products.
In conclusion, vacuum hot press furnaces are versatile and indispensable tools for a wide range of applications in materials science, manufacturing, and research. With their advanced capabilities and precise control systems, these furnaces enable the development and production of innovative materials with tailored properties, driving advancements in various industries.
Advantages of Sintering Under Vacuum and Pressure
Sintering under vacuum offers numerous advantages in the manufacturing of parts and components. One key benefit is the production of bright parts after sintering, which results from the lack of oxidation and atmosphere contamination in the vacuum environment. This controlled setting allows for precise monitoring and adjustment of process parameters, ensuring the desired outcomes are consistently achieved.
In certain cases, materials, especially highly reactive ones like titanium, require sintering under specific pressure conditions. For instance, sintering extremely reactive materials often necessitates pressure levels between 10-2 millibars and 10-4 millibars to prevent undesired reactions and achieve optimal sintering results.
Additionally, materials such as stainless steels may require atmospheres enriched with inert gases during the sintering process. The use of inert gases, such as argon-based mixtures, helps avoid issues like chromium nitride precipitation during cooling, particularly when high cooling rates cannot be attained. Nitrogen-based mixtures, on the other hand, are suitable for various other material types.
One significant advantage of sintering under vacuum and pressure is the ability to tailor the sintering atmosphere to specific material requirements, thereby optimizing the sintering process for desired properties. By selecting the appropriate sintering atmosphere, manufacturers can achieve a balance between favorable outcomes and operational costs.
Moreover, the controlled environment provided by vacuum sintering furnaces contributes to enhanced material properties and part appearance. By reducing the presence of harmful contaminants like water, oxygen, and nitrogen, vacuum sintering minimizes the risk of detrimental reactions such as decarburization, carburization, oxidation, and nitriding. This purity of the vacuum environment, with residual gas purities reaching exceptional levels like 99.99987% argon, sets vacuum sintering apart from other sintering methods.
In conclusion, the advantages of sintering under vacuum and pressure are multifaceted. The ability to produce bright, clean parts with improved properties, simplified processes, and reproducible results underscores the value of utilizing vacuum sintering techniques in various manufacturing applications. By leveraging the benefits of vacuum sintering, manufacturers can achieve superior outcomes, reduce processing time, and enhance overall productivity in the production of high-quality components.
CONTACT US FOR A FREE CONSULTATION
KINTEK LAB SOLUTION's products and services have been recognized by customers around the world. Our staff will be happy to assist with any inquiry you might have. Contact us for a free consultation and talk to a product specialist to find the most suitable solution for your application needs!