Introduction to Vacuum Furnace Brazing
Discover the evolution of vacuum brazing technology since the 1940s, its initial applications in electronics and subsequent expansion into industries like aviation and petrochemicals. Vacuum furnace brazing has revolutionized the joining of materials, offering unparalleled benefits such as improved corrosion resistance, cost-effectiveness, and pollution-free production conditions. This comprehensive guide will delve into the principles behind vacuum brazing furnaces, their exceptional features, and the wide array of industries and applications where they are indispensable. Join us as we explore the advantages, applications, and techniques of mastering vacuum furnace brazing.
Advantages of Vacuum Brazing
Explore the unparalleled benefits of vacuum brazing, including improved corrosion resistance, cost-effectiveness, and pollution-free production conditions.
Vacuum brazing offers significant advantages over other heating methods, making it a preferred choice for various industrial applications. Here's a closer look at the key advantages:
Clean and Flux-Free Joints
One of the most notable advantages of vacuum brazing is the production of clean, flux-free joints with surfaces free of oxides. This results in high-quality brazed joints with minimal voids and excellent mechanical properties. Without the need for flux, vacuum brazing eliminates potential contamination and the need for post-brazing cleaning processes.
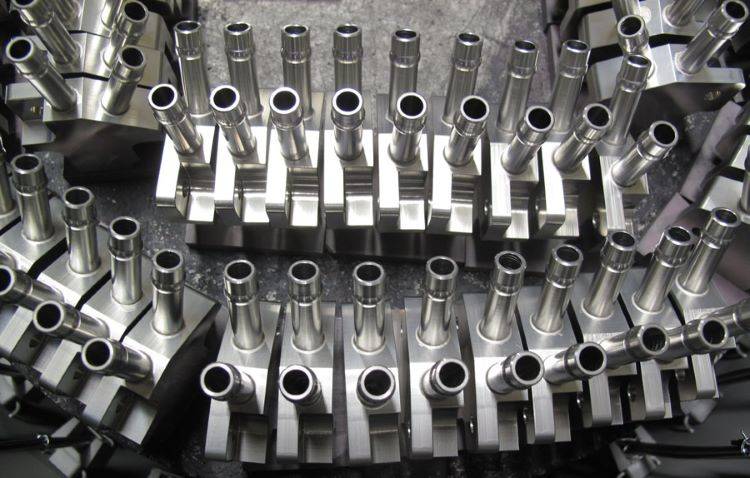
Improved Corrosion Resistance
Because vacuum brazing operates in a controlled environment free of contaminants, the resulting joints are shiny, bright, and clean. This environment enhances the corrosion resistance of the brazed components, ensuring longevity and reliability in various applications.
Precise Temperature Control
Vacuum brazing allows for precise temperature control throughout the brazing process, enabling the joining of materials with different melting points. This precise control ensures uniform heating and cooling, reducing residual stress in the brazed parts and maintaining their integrity and strength.
Versatility in Joining Materials
Vacuum brazing is suitable for joining dissimilar materials, such as ceramic to metal, expanding its applicability across a wide range of industries. This versatility opens up opportunities for innovative designs and complex assemblies.
Time and Cost Savings
The ability to perform multiple processes, including brazing, heat treating, and age hardening, in a single furnace cycle saves time and reduces production costs. Vacuum brazing offers efficiency and convenience, especially for high-volume production scenarios.
Enhanced Process Control and Repeatability
With vacuum brazing, every stage of the heating and cooling cycle can be accurately controlled, resulting in consistent and repeatable brazing outcomes. This level of process control ensures quality and reliability in the final product, meeting stringent industry standards.
Minimal Distortion and Movement
The uniform temperature distribution in vacuum brazing minimizes distortion or movement of the brazed parts, making it ideal for high-precision assemblies. This ensures dimensional accuracy and maintains the desired tolerances in the finished components.
In conclusion, vacuum brazing stands out as a superior joining method offering numerous advantages, including clean and flux-free joints, improved corrosion resistance, precise temperature control, versatility in joining materials, time and cost savings, enhanced process control and repeatability, and minimal distortion. Its widespread adoption across various industries underscores its importance and effectiveness in modern manufacturing processes.
Understanding Vacuum Brazing Furnaces
A vacuum brazing furnace is a crucial industrial equipment used in the metalworking process of brazing. It creates a clean, oxygen-free environment to join metal pieces using a filler metal with a lower melting temperature than the base metals. This process ensures strong, reliable joints and is widely used in various applications, including heating and cooling assemblies, aircraft components, medical devices, and structural components.
Operation and Structure
The vacuum brazing furnace operates by creating a vacuum inside the chamber to eliminate oxygen and other gases that could interfere with the brazing process. It utilizes a double-walled heating chamber, a sophisticated vacuum system, and a user-friendly interface. The furnace achieves exceptional temperature uniformity, efficient heating, and robust construction for longevity and reliability in demanding environments.
Principle
The furnace is composed of a furnace shell, lining, heating element, material tray, vacuum system, and electronic control system. It utilizes a three-stage vacuum pump, including a vacuum unit, oil diffusion pump, Roots pump, mechanical pump, pneumatic baffle valve, and manual butterfly valve. The heating elements consist of iron-chromium-aluminum wire arranged in a spiral shape for uniform heating.
Advantages
The vacuum brazing furnace offers several advantages, including the production of high-quality joints with minimal voids and excellent mechanical properties. It eliminates the need for flux, reduces oxidation and scaling, allows precise temperature control for joining materials with different melting points, and is suitable for complex assemblies. Moreover, it is an environmentally friendly process with minimal waste generation.
Working Principles of Vacuum Furnaces
A vacuum furnace operates in a low-pressure environment without oxygen and other reactive gases. It utilizes heating elements such as resistance heating, induction heating, or radiation heating to generate and control temperatures. The furnace serves various functions, including vacuum quenching, brazing, sintering, and magnetism application to metal materials.
Applications of Vacuum Brazing Furnace Technology
Vacuum brazing technology has evolved significantly since its inception in the 1940s, becoming a cornerstone welding method across various industries. Originally utilized in the electronics sector for brazing copper and stainless steel parts, its application swiftly expanded to encompass critical sectors such as aviation, atomic energy, and the production of stainless steel plate-fin heat exchangers.
Advantages of Vacuum Brazing
-
Enhanced Corrosion Resistance: Vacuum brazing obviates the need for flux, thereby substantially improving the corrosion resistance of products. This elimination of flux usage not only reduces pollution but also slashes the costs associated with pollution-free treatment equipment, fostering safer production conditions.
-
Cost Savings: The absence of flux in vacuum brazing translates to substantial savings in expensive metal fluxes. Furthermore, the elimination of intricate flux cleaning procedures further drives down production costs.
Vacuum furnaces serve as indispensable tools for various processes including annealing, brazing, sintering, and heat treatment, offering high consistency and minimal pollution.
Industries Leveraging Vacuum Furnaces
Aviation/Aerospace
The aerospace manufacturing sector demands cutting-edge technology to meet exacting specifications for aircraft, guided missiles, space vehicles, propulsion units, and related components.
Medical Device Manufacturing
Precision is paramount in crafting components for electronics and medical devices to ensure optimal fit and safety.
Advanced Ceramics
The high-temperature firing of ceramics is crucial in numerous applications. Industrial kilns play a pivotal role in refining and modifying ceramics to meet diverse requirements, including the production of components for aerospace and defense applications.
Vacuum Brazing Applications
Vacuum brazing finds extensive use in leveraging the thermal conductivity of aluminum and the deoxidizing properties of the process to join components across various domains, including:
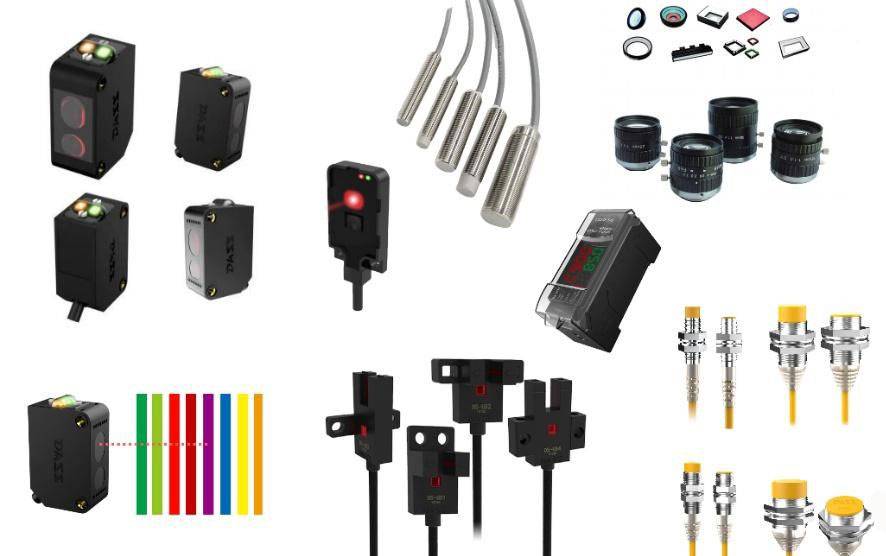
- Heating and Cooling Assemblies
- Micro-channel Heat Exchangers
- Aircraft Components
- Sensors
- Medical Devices
- Structural Components
- Other Thermal Products
Furthermore, our commitment to quality is underscored by our ITAR registration and ISO 9001 certification, ensuring that we meet and exceed the exacting standards demanded by our defense and aerospace clientele.
Features of Vacuum Brazing Furnaces
Vacuum brazing furnaces are essential for creating strong and durable joints in various industries. Their exceptional features make them stand out from other brazing methods, ensuring precise and reliable results. Let's delve into the key features that make vacuum brazing furnaces indispensable for high-quality applications.
Exceptional Temperature Uniformity
One of the standout features of vacuum brazing furnaces is their exceptional temperature uniformity. The design of these furnaces ensures that heat is distributed evenly throughout the chamber, resulting in consistent and precise brazing results. Unlike traditional brazing methods, the temperature in a vacuum brazing operation can be much lower, reducing the potential effects of heat on the product and providing close temperature uniformity throughout the assembly being brazed.
Efficient Heating System
Vacuum brazing furnaces are equipped with high-performance heating systems that rapidly reach and maintain the desired temperature. This efficiency reduces cycle times and increases productivity, making them ideal for high-volume production. The ability to achieve very high temperatures allows for the brazing of a wide variety of metals, including stainless steel, titanium, Cu, Ni, and aluminum, expanding their applications across different industries.
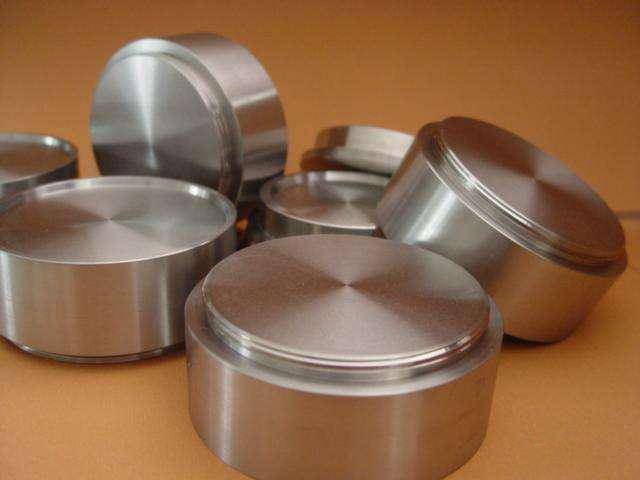
Advanced Vacuum System
Equipped with sophisticated vacuum systems, these furnaces effectively remove oxygen and other contaminants from the chamber. This creates a clean and controlled brazing environment, ensuring high-quality joints with minimal voids and excellent mechanical properties. The absence of flux in vacuum brazing eliminates potential contamination and post-brazing cleaning, making it an environmentally friendly process with minimal waste generation.
User-Friendly Interface
The user-friendly interface of vacuum brazing furnaces simplifies operation and monitoring, minimizing the need for extensive training. This feature enhances the overall usability of the furnaces, making them accessible to a wide range of operators and technicians.
Robust Construction
Constructed from durable materials and components, vacuum brazing furnaces are designed to withstand the demands of industrial environments. Their robust construction ensures longevity and reliability, making them a valuable investment for various applications.
In addition to these key features, vacuum brazing furnaces offer several advantages over traditional brazing methods. The absence of contaminants in the brazing environment results in shiny, bright, and clean metal surfaces. The process of heating and cooling the metal slowly reduces residual stress, helping the metals maintain their integrity and strength. Furthermore, some vacuum furnaces offer a quick cooling option known as quenching, which involves the use of inert gases, such as Argon, saving time and making them suitable for high-volume production.
The vacuum furnace's ability to carry out an identical heating cycle on a high number of loads and continuous brazing on larger pieces makes it an ideal system for various industrial applications. Its capability to repeat the same cycle accurately and clean the load thoroughly adds to its value in achieving high-quality brazing results.
In conclusion, the features of vacuum brazing furnaces make them indispensable for achieving strong, clean joints with precise temperature control and minimal waste generation. Their robust construction and efficient heating systems contribute to their reliability and longevity in demanding industrial environments. Whether for heating and cooling assemblies, aircraft components, medical devices, or other thermal products, vacuum brazing furnaces offer unparalleled benefits for a wide range of applications.
Principles Behind Vacuum Brazing Furnaces
Gain insights into the intricate principles governing vacuum brazing furnaces, from their horizontal furnace bodies to the composition of heating elements and vacuum systems.
A vacuum brazing furnace is a sophisticated piece of equipment designed for the precise joining of metal components through the brazing process. Here, we delve into the fundamental principles that underpin the operation and construction of vacuum brazing furnaces.
This article provides a comprehensive overview of vacuum brazing furnaces, covering their applications, features, principles, and advantages. Leveraging the insights presented here, manufacturers and researchers can make informed decisions regarding the utilization of vacuum brazing technology in their operations.
Advantages of Vacuum Brazing Furnaces
Revisit the advantages of vacuum brazing furnaces, emphasizing high-quality joints, minimal voids, precise temperature control, suitability for complex assemblies, and environmental friendliness.
Vacuum brazing furnaces offer a range of advantages that make them a preferred choice for various industrial applications. One of the key benefits is the ability to produce high-quality joints with minimal voids and exceptional mechanical properties. This results in strong, reliable connections between metal components, ensuring structural integrity and durability.
The absence of flux in the vacuum brazing process eliminates the risk of contamination and the need for extensive post-brazing cleaning. This not only saves time and resources but also ensures a clean and smooth surface finish on the brazed joints. Additionally, the reduced oxidation and scaling in a vacuum environment contribute to cleaner joints and improved overall quality of the brazed components.
Precise temperature control is another significant advantage of vacuum brazing furnaces. The ability to maintain precise temperature levels allows for the joining of materials with different melting points, expanding the range of applications for which vacuum brazing can be utilized. This level of control is particularly beneficial when working with complex assemblies that require careful heat management to prevent distortion or damage to the components.
Moreover, vacuum brazing furnaces are well-suited for joining complex components and assemblies that may have intricate shapes or configurations. The uniform heating provided by the furnace ensures that all parts of the assembly are brazed evenly, leading to consistent results and strong bonds between the different elements.
From an environmental perspective, vacuum brazing is a cleaner and more sustainable process compared to traditional methods. The minimal waste generation and reduced emissions make it an eco-friendly choice for various industries. By creating a controlled atmosphere within the furnace chamber, vacuum brazing minimizes the impact on the environment while delivering high-quality results.
In summary, the advantages of vacuum brazing furnaces, including high-quality joints, minimal voids, precise temperature control, suitability for complex assemblies, and environmental friendliness, make them a valuable asset in modern industrial applications. Their ability to produce strong, clean, and reliable joints while offering efficiency and sustainability highlights the importance of vacuum brazing technology in metalworking processes.
CONTACT US FOR A FREE CONSULTATION
KINTEK LAB SOLUTION's products and services have been recognized by customers around the world. Our staff will be happy to assist with any inquiry you might have. Contact us for a free consultation and talk to a product specialist to find the most suitable solution for your application needs!