Introduction: Importance of Porcelain Furnaces in Dental Labs
Porcelain furnaces play a crucial role in the dental laboratory industry as they are used for firing ceramic materials that are commonly used for restorations. These furnaces are essential for producing high-quality dental prosthetics that are durable and aesthetically pleasing. With the recent advances in restorative dentistry, the demand for porcelain furnaces has increased significantly. Dental laboratories have to carefully select the type of furnace they need based on their specific requirements. The future of porcelain furnaces in dental labs looks promising, with the development of advanced technologies that can improve accuracy and efficiency in the production process.
Table of Contents
- Introduction: Importance of Porcelain Furnaces in Dental Labs
- Types of Dental Furnaces: Ceramic, Combination, Sintering, Glazing
- Factors to Consider When Selecting Dental Furnaces
- Recent Advances in Restorative Dentistry
- What is Dental Porcelain and its Uses?
- The Process of Making Dental Porcelain
- The Two Main Components of Dental Porcelains
- The Future of Porcelain Furnaces in Dental Labs
Types of Dental Furnaces: Ceramic, Combination, Sintering, Glazing
Dental furnaces are essential tools in modern dental laboratories, allowing dental technicians to create high-quality dental restorations such as crowns, bridges, and veneers. There are four main types of dental furnaces: ceramic, combination, sintering, and glazing.
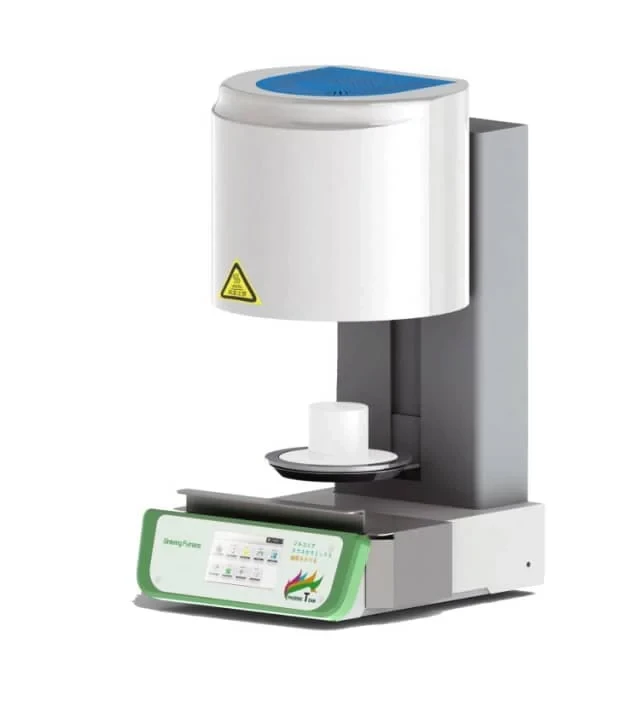
Ceramic Furnaces
Ceramic furnaces are primarily used to build porcelain layers on metal frameworks. They are suitable for all-metal-free and porcelain-fused-to-metal crowns. Most ceramic furnaces are fully automated, providing exceptional productivity. They are easy to use and maintain and are available at an affordable price.
Combination Furnaces
Combination furnaces are designed to handle both pressing ceramics and firing ceramic restorations. They can work with various dental materials and are suitable for different laboratory workflows. These furnaces are highly versatile and provide excellent value for money.
Sintering Furnaces
Sintering furnaces are primarily used to fuse zirconia frameworks. These dental furnaces can reach high temperatures, which is necessary for zirconia to achieve hardness. During the sintering process, zirconia undergoes a significant amount of shrinkage. Sintering furnaces are capable of reaching extreme temperatures required to process zirconia after milling.
Glazing Furnaces
Glazing furnaces are used to add a final layer of shine to the restorations. They are used for setting certain stains and glazes that add the final shade details to a restoration. These furnaces are highly efficient and are easy to operate. They are equipped with built-in infrared technology that offers reliable firing results and increases efficiency. The predrying process controlled by infrared technology reduces the risk of cracks occurring in the ceramic during the closing process.
In conclusion, the different types of dental furnaces are essential tools that help dental technicians create high-quality dental restorations. Ceramic furnaces are suitable for all-metal-free and porcelain-fused-to-metal crowns. Combination furnaces are highly versatile and can handle both pressing ceramics and firing ceramic restorations. Sintering furnaces are capable of reaching extreme temperatures required to process zirconia after milling. Glazing furnaces are used to add a final layer of shine to the restorations. With the rise of digital dentistry, dental furnaces are also becoming more integrated with computer-aided design and manufacturing (CAD/CAM) systems, allowing for even greater precision and accuracy.
Factors to Consider When Selecting Dental Furnaces
When it comes to selecting dental furnaces, several factors need to be taken into consideration to ensure that the furnace chosen meets the specific needs and preferences of the laboratory. Here are some of the essential factors to consider:
Firing Capacity and Temperature Range
The furnace's firing capacity and temperature range are critical factors to consider when selecting a dental furnace. The furnace must be able to handle the materials used in the dental lab, and its temperature range should be sufficient to fire the porcelain crowns and bridges onto metal frameworks.
Size and Design
The size and design of the furnace should match the lab's space and workflow. A furnace that is too large or too small for the lab's needs can cause space constraints and workflow issues, leading to inefficiencies.
Energy Efficiency
Energy efficiency is another crucial factor to consider, as it can impact the lab's electricity bill. Selecting a furnace with an energy-saving function can help to save electricity and reduce the lab's carbon footprint.
Programmable Firing Cycles and Automatic Temperature Control Systems
Furnaces with programmable firing cycles and automatic temperature control systems are becoming more popular. These advanced features reduce the risk of human error and improve consistency in firing results.
Maintenance Requirements and Technical Support
It is essential to consider the furnace's maintenance requirements and the availability of technical support from the manufacturer. A furnace that requires frequent maintenance or has limited access to technical support can cause significant downtime and hamper the lab's operations.
In conclusion, selecting a porcelain furnace for dental laboratories requires careful consideration of the lab's specific needs and preferences. The furnace's firing capacity and temperature range, size and design, energy efficiency, programmable firing cycles and automatic temperature control systems, maintenance requirements, and technical support are all important factors to consider. As technology continues to advance, the future of porcelain furnaces in dental laboratories looks bright, with more advanced features and capabilities expected to emerge in the coming years.
Recent Advances in Restorative Dentistry
Restorative dentistry is constantly evolving, and recent advances have brought about significant changes in the field. One of the key advancements is the increasing use of digital technology in the creation of restorations. Computer-aided design and computer-aided manufacturing (CAD/CAM) systems have revolutionized the way dental restorations are made. These systems use digital scans of a patient's teeth to create highly precise and accurate restorations, reducing the need for manual labor and traditional porcelain furnaces.
Another important development is the use of newer materials such as zirconia and lithium disilicate. These materials are gaining popularity due to their strength and esthetic qualities, which may require different firing techniques and equipment compared to traditional porcelain. Zirconia, in particular, has become a popular material for dental restorations due to its strength and durability, making it ideal for use in areas of the mouth that experience high stress, such as the molars.
In addition to these developments, advancements in bonding agents and adhesive technology have also significantly improved the durability and longevity of dental restorations. These bonding agents allow for stronger and more reliable adhesion between the restoration and the tooth, reducing the risk of failure and the need for replacement.
One of the most exciting developments in restorative dentistry is the use of 3D printing technology. 3D printers can create highly precise and accurate dental restorations, reducing the need for manual labor and traditional porcelain furnaces. This technology is particularly useful for creating highly complex and customized restorations, such as dental implants.
Despite these advancements, porcelain furnaces remain an essential tool for dental labs, particularly for the creation of complex and highly esthetic restorations. They also remain a cost-effective option for smaller labs or those with limited resources. As restorative dentistry continues to evolve, it is likely that porcelain furnaces will continue to play a role in dental labs, albeit in conjunction with newer technologies and materials.
In conclusion, recent advances in restorative dentistry have brought about significant changes in the field, including the increasing use of digital technology, newer materials such as zirconia and lithium disilicate, advancements in bonding agents and adhesive technology, and the use of 3D printing technology. While these developments have reduced the need for manual labor and traditional porcelain furnaces, porcelain furnaces remain an essential tool for dental labs and will continue to play a role in conjunction with newer technologies and materials.
What is Dental Porcelain and its Uses?
Dental porcelain, also known as dental ceramic, is a type of material used in dental laboratories to create dental restorations such as crowns, bridges, and veneers. These restorations are used to replace or repair damaged or missing teeth and improve both their function and appearance.
Porcelain is an inorganic, non-metallic material that is produced by heating raw minerals at high temperatures. It is a type of ceramic material that is usually made up of a combination of metals and non-metallic elements, such as oxygen. Porcelain is known for its natural appearance and ability to mimic the look of natural teeth, making it a popular choice for dental restorations.
Porcelain furnaces are used to heat and shape the porcelain into the desired shape and size for each restoration. The furnace heats the porcelain up to very high temperatures, causing the particles to fuse together and form a hard, durable material. Once the porcelain has been shaped and hardened, it can be polished and colored to match the natural teeth of the patient.
Porcelain restorations are used to replace or repair teeth that have been damaged due to decay or trauma. They are also used to improve the appearance of teeth that are discolored, misshapen, or have gaps between them. Porcelain is particularly well-suited for use in front teeth, where aesthetics are of the utmost importance.
In recent years, there have been advancements in dental materials and technology, leading to the development of stronger and more durable options such as zirconia and lithium disilicate. However, porcelain remains a popular choice for many dentists and patients due to its natural appearance and ability to mimic the look of natural teeth.
In conclusion, dental porcelain is a type of ceramic material used to create dental restorations such as crowns, bridges, and veneers. Porcelain furnaces are used to heat and shape the porcelain into the desired shape and size for each restoration. Porcelain restorations are used to replace or repair damaged or missing teeth and improve their function and appearance. While there are other options available, porcelain remains a popular choice due to its natural appearance and ability to mimic the look of natural teeth.
The Process of Making Dental Porcelain
Dental porcelain is a common material used to create dental restorations such as crowns, bridges, and veneers. The process of making dental porcelain requires a high-temperature furnace known as a porcelain furnace. These furnaces are typically made of porcelain to withstand the high temperatures required for firing dental porcelain.
Step 1: The Preparation
The process of making dental porcelain starts with the preparation of the materials. The materials used to make dental porcelain include feldspar, kaolin, and quartz. These materials are mixed with water to form a paste-like consistency. The mixture is then placed in a mold and allowed to dry.
Step 2: The Firing
Once the mold is dry, it is placed in the porcelain furnace. The furnace is preheated to a high temperature, usually between 1200 and 1400 degrees Celsius. The mold is then heated in the furnace for several hours until the porcelain is fully fired.
Step 3: The Finishing
Once the firing process is complete, the porcelain is removed from the mold and allowed to cool. The porcelain is then polished and shaped to fit the patient's teeth. This process is known as finishing.
Step 4: The Glazing
After the porcelain is shaped and polished, it is glazed. The glaze is a liquid coating that is applied to the surface of the porcelain. The porcelain is then fired again at a lower temperature to fuse the glaze to the surface of the porcelain.
Step 5: The Final Inspection
The final step in the process of making dental porcelain is the inspection. The finished product is inspected for any defects, including cracks, chips, or other imperfections. The porcelain is also checked for proper fit and color.
In conclusion, the process of making dental porcelain is a complex one that requires a high level of skill and precision. The continued evolution of porcelain furnaces in dental laboratories will ultimately lead to better outcomes for patients and dentists alike.
The Two Main Components of Dental Porcelains
Dental porcelains are a type of ceramic material that is used to create dental restorations such as crowns, bridges, and veneers. Porcelain furnaces are vital in firing dental porcelains to create durable and aesthetically pleasing dental restorations. The two main components of dental porcelains are silica and feldspar.
Silica
Silica is a mineral that gives dental porcelains their strength and hardness. It is a major component of dental porcelains, accounting for up to 60% of the material. Silica is naturally occurring and is commonly used in many dental materials due to its strength and durability. It is an essential ingredient in dental porcelains as it provides the material with the necessary strength to withstand the forces of biting and chewing.
Feldspar
Feldspar is the second main component of dental porcelains. It provides the material with its translucency and color. Feldspar is a type of mineral that is commonly found in rocks. It is used in dental porcelains to give them their natural appearance by providing a range of colors that can be matched to the patient's existing teeth. The use of feldspar allows dental restorations to blend seamlessly with natural teeth, resulting in aesthetically pleasing results.
The Importance of Silica and Feldspar
The combination of silica and feldspar creates a durable and aesthetically pleasing material that is highly sought after in the field of dentistry. The strength and hardness provided by silica make dental porcelains suitable for use in dental restorations that require durability and strength. The use of feldspar allows dental restorations to blend naturally with existing teeth, making them an excellent choice for cosmetic dental procedures.
Conclusion
In conclusion, dental porcelains are an essential material used in dental restorations such as crowns, bridges, and veneers. The two main components of dental porcelains are silica and feldspar. Silica provides the material with its strength and hardness, while feldspar provides the material with its translucency and color. The combination of these two components creates a durable and aesthetically pleasing material that is highly sought after in the field of dentistry. With the advancements in porcelain furnace technology, it is now easier than ever to achieve consistent and accurate firing temperatures, resulting in high-quality dental restorations that meet the needs of both dental professionals and patients alike.
The Future of Porcelain Furnaces in Dental Labs
Porcelain furnaces have been a vital tool in dental laboratories for many years, and they remain essential in the creation of high-quality dental restorations. However, with the constant advancements in technology, many dental professionals are curious about what the future holds for these furnaces.
Integration of digital technology
One of the most significant trends in porcelain furnaces is the integration of digital technology. Many modern porcelain furnaces now come equipped with digital controls and interfaces, allowing for greater precision and accuracy in the firing process. Additionally, some manufacturers are exploring the use of artificial intelligence to optimize firing parameters and improve the quality of the finished product.
Energy-efficient porcelain furnaces
Another trend is the development of compact, energy-efficient porcelain furnaces that can be easily integrated into smaller dental laboratories. These furnaces often use advanced insulation materials and heating elements to reduce energy consumption and minimize heat loss. This development will make it possible for smaller labs to invest in and utilize these furnaces.
Alternative heating sources
Some manufacturers are exploring the use of alternative heating sources such as microwaves or lasers to further improve the firing process. These alternative heating sources have the potential to increase efficiency and reduce firing times, which can be beneficial for busy dental laboratories.
Sintering furnaces and zirconia
Sintering furnaces are used to process dental zirconia after it has been milled into a crown, bridge, framework, or other restoration. With the recent increase in full-contour zirconia restorations, it is not surprising to see more laboratories adding sintering furnaces to their assortment of production equipment. Given the growing number of zirconia materials and their required sintering parameters, the driving force behind newer furnace designs and capabilities is the need to accommodate these materials.
Proper temperature
Recent studies indicate that firing at approximately 1500⁰C - 1550⁰C, depending on the temperature accuracy of the furnace, produces maximum strength in zirconia. This has led to the development of furnaces that offer multiple program stages and a way to control the cooling rate of your zirconia restorations. This feature is important for labs that use more than one type of zirconia or are looking for varied results depending on the patient and the location of the restoration.
Safety
Safety is perhaps the most important feature of a sintering furnace. These furnaces climb to extraordinarily high temperatures and hold there for a long time. And they use high amperage to do it. Therefore, the furnace should have safety features like over-temperature protection, vacuum pump, and pressure relief valve.
Porcelain furnaces will remain a vital tool for dental laboratories in the future, with new technologies and innovations promising to make the process of creating high-quality dental restorations faster, more efficient, and more precise than ever before.
CONTACT US FOR A FREE CONSULTATION
KINTEK LAB SOLUTION's products and services have been recognized by customers around the world. Our staff will be happy to assist with any inquiry you might have. Contact us for a free consultation and talk to a product specialist to find the most suitable solution for your application needs!