Introduction: Importance of Dental Ceramic Furnaces
Dental ceramic furnaces play a crucial role in the production of dental restorations such as crowns, bridges, and veneers. These furnaces use high temperatures to fire dental ceramics and produce the desired strength, color, and translucency. The accuracy of temperature control in a dental furnace is paramount to ensure consistent and reliable results. The calibration of the furnace is also essential to ensure that the firing process is precise and accurate. Standardization of dental furnaces is necessary to ensure that the results are consistent across different laboratories. As technology advances, new developments in dental porcelains and furnace categories continue to improve the accuracy and efficiency of the manufacturing process.
Table of Contents
- Introduction: Importance of Dental Ceramic Furnaces
- Dental furnaces: Suitable for manufacturing dental restorations
- Temperature Range and Firing Results
- Importance of Accuracy in Temperature Control
- Differences in results due to varying calibration processes
- Consequences of Different Degrees of Firing
- Recent Developments in Dental Porcelains
- Conclusion: Importance of Choosing the Right Furnace
Dental furnaces: Suitable for manufacturing dental restorations
Dental furnaces are designed to work with a range of ceramic materials, making them suitable for the manufacturing of metal-ceramic and all-ceramic restorations for use in dentistry. These furnaces are particularly used for firing or sintering, respectively, of dental opaques, dentine and enamel materials to the respective compatible substructure materials.
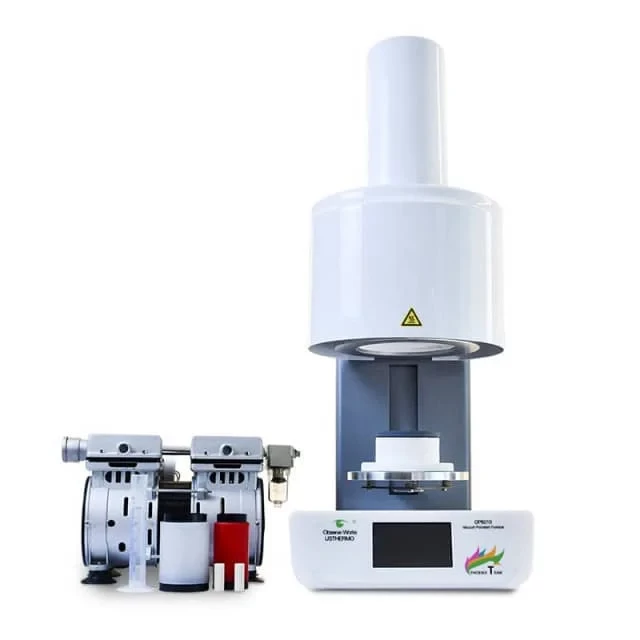
Firing or Sintering of Dental Materials
The firing process involves heating the ceramic material to a specific temperature, which causes it to fuse together and form a solid structure. The result is a dental restoration that is both aesthetically pleasing and functional. The firing result obtained is influenced by the accuracy of the actual temperature, which may be influenced by the different calibration processes applied by the manufacturers of dental furnaces as well as by the varying construction types of the dental furnaces currently on the market.
Types of Dental Furnaces
There are a variety of dental furnaces available, including ceramic combination furnaces, ceramic furnaces and sintering furnaces. Ceramic furnaces process conventional ceramics, while combination furnaces add the ability to operate under the pressure necessary to work with pressable ceramics. Sintering furnaces are capable of reaching the extreme temperatures required to process zirconia after milling. There are also glazing furnaces, which are used for setting certain stains and glazes that add the final shade details to a restoration.
Importance of Choosing the Right Furnace
When you’re ready to purchase a furnace, make sure you select one that is capable of processing the materials you use in your practice or lab. A different degree of firing does not only cause differences that can be judged directly by the human eye (e. g. colour and transparency), but also deviations that cannot be detected by eye. These are, for instance, the coefficient of thermal expansion, strength, and solubility of the dental opaque, dentine or enamel materials, and the bonding strength to its substructure. Such changes may result in clinical failures (e. g. fractures) as well as discoloration and changed aesthetics of the dental ceramic restoration. As with all equipment purchases, invest in a furnace from a reputable manufacturer.
In conclusion, dental furnaces are an essential tool for modern dentistry and are a testament to the advances in technology that have made it possible to create high-quality dental restorations with precision and accuracy. With the right training and expertise, dental technicians can use these furnaces to create durable and long-lasting dental restorations that meet the needs of their patients.
Temperature Range and Firing Results
Dental ceramic furnaces are designed to work with specific temperature ranges to achieve the desired firing results. The temperature range and firing results depend on the type of ceramic used, the thickness of the material, and the desired translucency. The firing temperature range typically ranges from 700°C to 1,550°C.
Factors Affecting Firing Temperature
The firing temperature range is dependent on several factors, including the type of ceramic used, the thickness of the material, and the desired translucency. For instance, a ceramic with high translucency requires a lower firing temperature than a less translucent ceramic. Similarly, thin ceramics require a lower firing temperature than their thicker counterparts.
Firing Time
The firing process takes several hours to complete, and the furnace needs to be precisely controlled to avoid any thermal shock that may cause the ceramic to crack or break. The firing time is dependent on the type of ceramic used, the thickness of the material, and the desired translucency. The thicker the ceramic and the higher the desired translucency, the longer the firing time.
Firing Results
The firing process is a critical step as it affects the final product's strength, color, and translucency. The firing temperature and time affect the ceramic's physical properties, such as its strength, hardness, and translucency. A higher firing temperature and longer firing time result in a stronger and more translucent ceramic. However, if the firing temperature is too high or the firing time is too long, the ceramic may become too translucent, resulting in a less desirable appearance.
Precision Temperature Control
Dental ceramic furnaces offer precise temperature control to achieve the desired firing results. The furnaces are designed to work with specific temperature ranges, and they maintain these temperatures throughout the firing process. The temperature inside the furnace is evenly distributed, ensuring that the ceramic is fired uniformly.
Thermal Shock
Thermal shock can cause the ceramic to crack or break during the firing process. To avoid this, the furnace needs to be precisely controlled. The furnace's heating and cooling rate should be carefully monitored to prevent any sudden temperature changes that may cause thermal shock. Additionally, the furnace needs to be equipped with QTK muffle technology and a reflecting floor to help spread the heat evenly throughout the firing chamber, further reducing the risk of thermal shock.
In conclusion, dental ceramic furnaces offer precise temperature control, ensuring that the ceramic is fired uniformly. The firing temperature and time affect the ceramic's physical properties, such as its strength, hardness, and translucency. The furnace's heating and cooling rate should be carefully monitored to prevent any sudden temperature changes that may cause thermal shock. Dental ceramic furnaces are a critical tool for dental laboratories, and they play a crucial role in creating long-lasting, aesthetically pleasing dental restorations.
Importance of Accuracy in Temperature Control
One of the most crucial aspects of dental ceramic furnaces is their accuracy in temperature control. The temperature must be controlled precisely to ensure the proper fusion of the ceramic material. Even a small deviation from the desired temperature can lead to a weak and brittle restoration.
Impact of Low Temperature
If the temperature is too low, the ceramic will not fuse properly, resulting in a weak and brittle restoration. The low temperature can also lead to porosity in the ceramic material, making it more susceptible to fractures and cracks. Additionally, the low temperature can also affect the color and translucency of the final restoration, resulting in a poor aesthetic outcome.
Impact of High Temperature
On the other hand, if the temperature is too high, the ceramic may become discolored or distorted, making it unusable. The high temperature can also lead to excessive shrinkage, causing the restoration to not fit properly. Moreover, the high temperature can cause the ceramic to lose its translucency, making it less aesthetically pleasing.
Achieving Accuracy in Temperature Control
To achieve the necessary accuracy, dental ceramic furnaces are equipped with advanced temperature control systems. These systems use thermocouples and sophisticated software to monitor and adjust the temperature throughout the firing process. The thermocouple is generally placed in the upper section of the firing chamber and at a close distance from the ceramic object. The temperature control system ensures that the temperature remains consistent and within the desired range, producing high-quality restorations that are both functional and aesthetically pleasing.
Programmable Temperature Control
Most modern dental furnaces are microprocessor controlled that offer programmability and memory system that can remember even up to 200 different programs, which can be performed accurately by the user. Multistage programs are used for firing or sintering of ceramics where it is necessary to heat and hold at one temperature and then heat or cool to another programmed temperature. This type of flexibility of the programming allows creating many different types of programs. The automatic temperature adjustment to ±1°C every time a program is started ensures the accuracy of temperature control.
Conclusion
In conclusion, accuracy in temperature control is crucial for producing high-quality dental restorations. The temperature control system in dental ceramic furnaces ensures that the temperature remains consistent and within the desired range. With the advancements in technology, modern dental furnaces offer programmability and memory system that can perform accurate firing or sintering of ceramics. Investing in a high-quality dental ceramic furnace with advanced temperature control systems is essential for dentists to create durable and natural-looking restorations for their patients.
Differences in results due to varying calibration processes
Calibration is a crucial process in dental ceramic furnaces that greatly affects the quality of the final product. The accuracy and consistency of the calibration process can vary from one manufacturer to another, and even within different models of furnaces. As a result, variations in calibration can lead to differences in the final product, such as the color, translucency, and strength of the dental restoration.
Importance of Calibration
Calibration is the process by which the temperature of the furnace is set to achieve specific results. The accuracy of the calibration process can directly impact the quality of the dental restoration. For example, if the temperature is too high, the restoration may be too opaque, while a lower temperature may result in a restoration that is too translucent.
Variations in Calibration Process
Different manufacturers may use different calibration processes, and even within the same manufacturer, different furnaces may have different calibration processes. These variations can lead to differences in the final product, making it essential for dental professionals to understand the science behind the calibration process.
Color and Translucency
The color and translucency of the dental restoration can be affected by variations in the calibration process. If the temperature is too high, the restoration may be too opaque, resulting in a less natural appearance. On the other hand, if the temperature is too low, the restoration may be too translucent, making it less durable.
Strength of the Restoration
The strength of the dental restoration is also affected by variations in the calibration process. If the temperature is too high, the restoration may become brittle and weak, while a lower temperature may not allow the restoration to achieve its desired strength.
Choosing a Furnace with Consistent Calibration Process
To ensure the highest quality dental restorations for their patients, dental professionals should invest in a high-quality dental ceramic furnace with a reliable calibration process. By choosing a furnace with a consistent calibration process, dental professionals can produce dental restorations that meet the highest standards of durability and aesthetics, ensuring patient satisfaction and trust in their practice.
In conclusion, the calibration process is a crucial step in the production of dental restorations. Variations in the calibration process can lead to differences in the final product, such as the color, translucency, and strength of the dental restoration. Dental professionals should choose a furnace with a consistent calibration process to ensure the highest quality dental restorations for their patients.
Consequences of Different Degrees of Firing
Dental ceramic furnaces are essential tools in creating high-quality dental restorations such as crowns, bridges, and veneers. The degree of firing is crucial in determining the strength and durability of the ceramic material, and different degrees of firing can have significant consequences on the final product.
Underfiring the Ceramic Material
Underfiring the ceramic material can result in a weak and brittle restoration. When the ceramic material is not heated to a high enough temperature, it remains porous, and as a result, the restoration becomes more prone to damage. Underfired ceramic restorations can have a chalky appearance and can break easily when subjected to biting forces.
Overfiring the Ceramic Material
Overfiring can cause the ceramic material to become too hard and prone to fractures. When the ceramic material is heated beyond its melting point, it can cause the material to shrink and crack. Overfired ceramic restorations can appear glassy, and the edges can be sharp and prone to chipping.
Finding the Right Balance
It is crucial to find the right balance of firing temperature to achieve optimal strength and durability of the restoration. Dental professionals must have a thorough understanding of the properties of the ceramic materials used in dental restorations and the effects of different firing temperatures. By finding the right balance of firing temperature, dental professionals can create restorations that are both functional and aesthetically pleasing.
The Role of Dental Ceramic Furnaces
Dental ceramic furnaces play an essential role in the field of dentistry by helping to create durable and long-lasting dental restorations that can improve patients' oral health and quality of life. Modern, 21st-century porcelain furnaces are technically sophisticated, electronically-controlled devices with programmable cycles for firing dental porcelains. These furnaces offer many settings that can be programmed precisely and independently of each other, such as preheating/drying, heat-rate, hold-time, cooling, and firing temperatures for various materials such as opaquer, shoulder and dentine porcelains as well as glaze firings programmed accurately.
Conclusion
In conclusion, dental ceramic furnaces are critical tools in the field of dentistry, helping to create durable and long-lasting dental restorations that can improve patients' oral health and quality of life. By understanding the properties of the ceramic materials used in dental restorations and the effects of different firing temperatures, dental professionals can create restorations that are both functional and aesthetically pleasing. With the help of modern, technologically advanced porcelain furnaces, dental professionals can achieve precise firing temperatures necessary to create high-quality dental restorations.
Recent Developments in Dental Porcelains
Dental porcelain furnaces have undergone significant developments in the past few years, leading to the creation of stronger and more esthetically pleasing materials. These developments have revolutionized the field of dentistry by making it possible to create highly precise, durable, and natural-looking dental prosthetics that improve patients' oral health and overall quality of life.
Zirconia-Based Ceramics
One of the recent developments in dental porcelains is the use of zirconia-based ceramics. These materials offer improved strength, durability, and color matching to natural teeth. Zirconia-based ceramics are highly biocompatible and are resistant to wear and chipping, making them ideal for dental restorations.
Computer-Aided Design and Manufacturing (CAD/CAM)
Advancements in computer technology have enabled dentists to create highly precise digital models of the patient's teeth, which can be used to create customized dental prosthetics. The use of computer-aided design and manufacturing (CAD/CAM) technology in dental laboratory equipment allows for the creation of highly accurate dental prosthetics in a shorter amount of time.
Lithium Disilicate Ceramics
Another recent development in dental porcelains is the use of lithium disilicate ceramics. These materials offer high strength and durability, making them ideal for dental restorations. Lithium disilicate ceramics are highly esthetic and can be matched to the natural color of the patient's teeth.
Hybrid Ceramics
Hybrid ceramics are a combination of porcelain and composite materials, and they offer improved strength and durability compared to traditional porcelain materials. These materials are highly esthetic and can be matched to the natural color of the patient's teeth, making them ideal for dental restorations.
In conclusion, recent developments in dental porcelains have led to the creation of stronger and more esthetically pleasing materials, such as zirconia-based ceramics, lithium disilicate ceramics, and hybrid ceramics. These materials offer improved strength, durability, and color matching to natural teeth, making them ideal for dental restorations. Advancements in computer technology have also enabled dentists to create highly precise digital models of the patient's teeth, which can be used to create customized dental prosthetics. These developments have revolutionized the field of dentistry by making it possible to create highly precise, durable, and natural-looking dental prosthetics that improve patients' oral health and overall quality of life.
Conclusion: Importance of Choosing the Right Furnace
Choosing the right dental ceramic furnace is vital for producing high-quality dental restorations. The furnace must be calibrated correctly to ensure accuracy in temperature control and firing results. The variation in calibration processes can cause differences in the degree of firing, which can lead to inconsistent and inferior results. Standardization of dental furnaces is essential to ensure reliable and accurate firing. Recent developments in dental porcelains have led to more advanced and sophisticated furnaces, offering improved precision and control. In summary, investing in the right furnace and ensuring proper calibration is crucial for achieving optimal results in dental restoration manufacturing.
CONTACT US FOR A FREE CONSULTATION
KINTEK LAB SOLUTION's products and services have been recognized by customers around the world. Our staff will be happy to assist with any inquiry you might have. Contact us for a free consultation and talk to a product specialist to find the most suitable solution for your application needs!