Understanding Vacuum Levitation Induction Melting Furnace
Explore the components of a vacuum levitation induction melting furnace, including the furnace body, medium frequency power, vacuum system, cooling system, and electric control system. Learn how each element contributes to the efficiency and precision of metal smelting processes.
Vacuum induction melting (VIM) furnaces have evolved from specialized processing of exotic alloys to more common use across various industries, including the production of stainless steels and other metals. These furnaces operate under vacuum conditions, offering precise control over the melting process.
How Does a Vacuum Induction Furnace Work?
Material is charged into the induction furnace under vacuum, where power is applied to initiate melting. Additional charges are added to achieve the desired melt capacity. The molten metal undergoes refinement under vacuum conditions, with adjustments made to achieve precise melt chemistry.
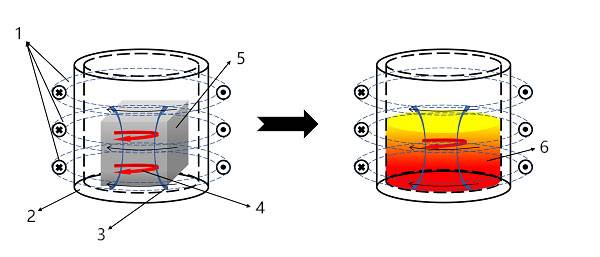
Key Components and Functions
In addition to the furnace body and vacuum system, a vacuum induction melting furnace is equipped with essential components such as a medium frequency power supply, electric control system, and cooling system. These components work together to provide energy input for melting while preventing overheating and ensuring structural integrity.
Auxiliary components like transmission trolleys, furnace door mechanisms, and observation windows may be added based on specific process requirements. For applications with high impurity levels, a gas filter system is essential for maintaining metal purity.
Advantages of Vacuum Induction Melting Furnaces
The compact structure of VIM furnaces, with only the smelting part enclosed in the vacuum chamber, enables better control over vacuum levels and faster evacuation times. Features like electromagnetic stirring ensure uniform mixing of added elements throughout the molten pool, maintaining consistent temperature.
The inclusion of filter baffles and other measures improves metal purity by mitigating the impact of impurities. Vacuum leak detection and repair are simplified due to the furnace's smaller volume, reducing downtime for maintenance.
Precision and Control
Vacuum induction melting furnaces offer precise temperature control through advanced electric control systems. Users can monitor the melting process in real-time, ensuring accuracy and consistency. The centralized cooling system regulates melting temperatures, enhancing process control and product quality.
Applications and Flexibility
VIM furnaces are available in a range of sizes, from small units suitable for gram-scale experiments to larger models for industrial production. This versatility allows users to adjust batch sizes according to their specific needs.
Gas Elimination and Oxidation Prevention
One of the primary benefits of vacuum induction melting is the removal of gases from molten metals. This process prevents quick oxidation, ensuring the purity and quality of the final product.
In conclusion, vacuum induction melting furnaces play a vital role in modern metal smelting processes, offering precise control, enhanced purity, and flexibility in production.
Efficiency and Flexibility
Delve into the range of vacuum furnaces available, from small-scale units suitable for gram-level batches to larger furnaces accommodating diverse batch sizes. Understand how this versatility empowers users to optimize production processes.
Advanced Automation and Control:
Our vacuum furnaces are equipped with advanced automation and control systems, empowering you with precise process management and monitoring capabilities. Our user-friendly interface allows you to effortlessly program and adjust various parameters, ensuring optimal performance and efficiency. With real-time data and diagnostics, you can make informed decisions, detect anomalies, and optimize your production processes for maximum output.
Energy Efficiency and Sustainability:
Vacuum Designs
Vacuum furnaces for low-temperature processing can be batch or continuous, stand-alone, integrated into continuous vacuum furnace systems or a separate “module” incorporated into a cellular system. For example, the basic operation for a batch vacuum furnace is as follows:
- Mechanical vacuum pumps, optionally equipped with blowers, produce vacuum levels down to 1.3 x 10-3 mbar (0.001 torr) with 6.7 x 10-3 mbar (0.005 torr) common. This is normally achieved within 10-30 minutes of the start of the cycle, depending on the size of the pumping systems and the nature of any contaminants present on the workload.
- The unit is then backfilled in the range of 66.7 x 101 mbar (500 torr) negative pressure to 0.10 bar (1.5 psig) positive pressure with an inert gas such as nitrogen, argon, or a mixture of nitrogen/hydrogen (3% maximum), and heating begins.
- Double pumpdown cycles are often found to be advantageous to speed the overall cycle time. After reaching setpoint and soaking at temperature, the cooling cycle is initiated.
Vacuum Furnace Features
KinTek vacuum furnaces offer precise temperature control, excellent temperature uniformity, and a wide range of applications for labs, universities, and any small-scale production application using industrial furnace models.
Each standard and customized vacuum furnace offers the following features and benefits:
- Excellent temperature accuracy and uniformity
- Energy-efficient ceramic fiber insulation
- Auto shut-off safety feature
Customized Vacuum Furnaces
Get a high-temperature vacuum furnace built specifically to meet your application needs. KinTek's experienced and knowledgeable representatives can help you design or build a custom furnace to meet your exact specifications or application needs.
This comprehensive range of features and options ensures that our vacuum furnaces provide the efficiency and flexibility required for a wide variety of laboratory and small-scale production applications.
Precision Temperature Control
Discover how the electric control system of vacuum induction melting furnaces ensures precise temperature control throughout the melting process. Explore the role of the cooling system in maintaining optimal melting temperatures and preventing oxidation.
Induction heating is a process wherein induced eddy currents heat conductive materials. This heating can be used to melt metals and make alloys. Vacuum Induction melting offers an attractive combination of a controlled atmosphere (vacuum or inert gas) and precise control on the melting process.
Description of Vacuum Sintering Furnace
A vacuum sintering furnace is a type of furnace where heated articles undergo sintering in a vacuum environment. This furnace is crucial in various industrial processes, particularly in powder metallurgy.
The sintering process is highly sensitive to temperature variations. A deviation of just a few degrees Celsius can significantly impact the quality of the final product. Hence, strict control over the sintering temperature is imperative, with deviations typically not exceeding a specified range of ±3℃ to ±5℃.
Advantages of Vacuum Induction Equipment
Compared to traditional smelting methods, vacuum induction equipment offers substantial advantages in process control. With advancements in computer technology, modern vacuum induction furnaces integrate intelligent control systems that streamline operations, reduce labor costs, and enhance precision.
Future developments in intelligent control systems will further enhance the capabilities of vacuum induction equipment. These systems will enable precise control over smelting temperatures, facilitate automated alloy additions at predetermined intervals, and streamline the entire smelting process. Additionally, the integration of comprehensive data collection and real-time analysis will empower operators to make informed decisions and optimize process parameters during smelting.
Components of Vacuum Induction Melting Furnace
The vacuum induction melting furnace comprises several essential components, including:
- Vacuum Furnace Body: Provides the chamber where melting occurs under vacuum or controlled atmosphere conditions.
- Medium Frequency Power: Supplies the energy required for induction heating.
- Vacuum System: Maintains the desired vacuum level within the furnace chamber.
- Cooling System: Prevents overheating and maintains optimal melting temperatures.
- Electric Control System: Enables precise temperature control and overall operation of the furnace.
Key Features and Benefits
- Accurate Temperature Control: The electric control system ensures precise regulation of melting temperatures, enhancing the quality and consistency of the final product.
- Gas Removal: The vacuum environment eliminates gases from the molten metals, preventing rapid oxidation and preserving the integrity of the alloy.
- Flexible Batch Sizes: Vacuum furnaces are available in various sizes, accommodating a range of batch sizes from small-scale to larger industrial applications.
- Centralized Cooling System: The cooling system efficiently dissipates heat, maintaining stable operating temperatures and prolonging equipment lifespan.
In conclusion, vacuum induction melting furnaces offer unparalleled precision and control in metal smelting processes. By leveraging advanced technologies and intelligent control systems, these furnaces facilitate efficient production, ensure product quality, and pave the way for future advancements in metallurgical processing.
Working Principle and Historical Significance
Uncover the historical roots of vacuum induction melting technology, tracing its origins to the aerospace and metallurgy industries. Learn how this technology has evolved to become a cornerstone in the production of high-performance alloys for various applications.
Vacuum Induction Melting: A Pathway to Advanced Materials
Vacuum induction melting (VIM) stands as a pivotal technology in the realm of metallurgy, particularly in the production of specialized and exotic alloys. Initially developed for the processing of superalloys, its application spectrum has expanded to encompass stainless steels and various other metals. This expansion owes much to the escalating demand for advanced materials across diverse industries.
The Vacuum Induction Melting Process
At the core of VIM lies the principle of melting metals under vacuum conditions, with electromagnetic induction serving as the primary energy source. The process entails the generation of electrical eddy currents within the metal, facilitated by an induction coil carrying alternating current. These currents, in turn, induce heating effects, ultimately leading to the melting of the metal charge.
The swift evolution of VIM technology finds its roots intertwined with the aerospace industry's quest for high-temperature alloy materials. These materials, essential for aerospace, missile, rocket, and atomic energy equipment, necessitated innovations in smelting processes. VIM furnaces emerged as a solution, enabling the smelting of nickel, iron, cobalt-based alloys under vacuum conditions. This environment effectively reduces the presence of gap elements like O2, N2, and H2, ensuring the removal of non-metallic inclusions and harmful impurities such as Pb, Bi, Sb, Cu, Sn, and Te.
Applications of Vacuum Induction Melting
The versatility of VIM extends across various applications within the metallurgical landscape:
- Refining of high-purity metals and alloys.
- Production of electrodes for remelting processes.
- Manufacture of master alloy sticks, vital in procedures like investment casting.
- Casting of critical components for aircraft engines.
Historical Evolution
The genesis of vacuum induction melting dates back to 1920 when the first prototype emerged. At its essence, VIM harnesses electromagnetic induction to induce eddy currents within conductors, thereby heating and melting the metal. Over the decades, this technology has found indispensable utility in both the aerospace and nuclear sectors, driving advancements in material science and engineering.
In summary, vacuum induction melting stands as a testament to human ingenuity, facilitating the production of materials that power modern technological marvels. From its humble origins to its current status as a cornerstone of metallurgical innovation, VIM continues to shape the landscape of advanced materials manufacturing.
Applications Across Industries
Explore the wide-ranging applications of vacuum induction melting technology in aerospace, electronics, energy, and more. Understand how this technology enhances the properties and quality of materials essential for advanced engineering and manufacturing.
Vacuum induction melting (VIM) technology has evolved significantly, originally developed for processing specialized and exotic alloys, it has now become increasingly common as advanced materials find broader applications. Initially utilized for materials like superalloys, VIM has expanded its utility to include stainless steels and various other metals.
The rapid development of VIM technology is closely linked to the demand for high-temperature alloy materials in industries such as aerospace, missile, rocket, and atomic energy equipment. Superalloys, crucial for these applications, benefit greatly from the capabilities of VIM furnaces.
How Vacuum Induction Furnaces Work
In a vacuum induction furnace, material is charged under vacuum, and power is applied to melt the charge. Additional charges are made to reach the desired melt capacity, and the molten metal is refined under vacuum conditions. This process allows for precise adjustment of the melt chemistry until the desired composition is achieved.
Advantages of Vacuum Induction Melting
-
High Purity and Quality: VIM excels in producing high-purity and high-quality materials. The vacuum environment eliminates the risk of contamination from oxygen, nitrogen, and other gases present in the atmosphere. This results in a cleaner, more homogeneous melt, devoid of harmful inclusions and impurities that could compromise mechanical properties.
-
Controlled Atmosphere: Within the vacuum chamber, the atmosphere is tightly controlled, with only specified gases introduced at precise pressures. This level of control enables precise management of the chemical composition of the melted material and prevents unwanted oxidation or reactions with ambient gases.
Vacuum induction melting furnaces are pivotal in the field of vacuum metallurgy, playing a significant role in the production of alloys and special steels crucial for aerospace, missile, rocket, atomic energy equipment, and the electronics industry. Notably, a considerable proportion of products in these sectors are manufactured using VIM technology.
Various materials, including stainless steel, heat-resistant steel, ultra-high-strength steel, tool steel, bearing steel, magnetic materials, elastic alloys, and expansion alloys, are melted using vacuum induction melting furnaces to ensure optimal performance and quality. These furnaces enhance the hot workability and mechanical properties of nickel-based, cobalt-based, and iron-based superalloys, making them indispensable in advanced engineering and manufacturing processes.
Advantages Over Traditional Methods
Vacuum induction melting technology stands out as a premier method for smelting metals due to its numerous advantages over traditional approaches. By comparing its efficiency, sustainability, and material purity with conventional methods, it becomes evident why vacuum induction smelting is increasingly favored in various industries.
Energy Efficiency and Environmental Sustainability
Vacuum induction melting (VIM) technology represents a significant leap forward in energy efficiency and environmental sustainability compared to traditional smelting methods. Unlike conventional approaches, VIM operates in a vacuum environment, which minimizes heat loss and reduces energy consumption. This efficient utilization of energy not only lowers production costs but also contributes to a greener manufacturing process by reducing carbon emissions and energy waste.
Material Purity and Quality
One of the foremost advantages of VIM is its capability to produce materials of exceptional purity and quality. The vacuum environment eliminates the presence of oxygen, nitrogen, and other gases that could contaminate the molten metal. As a result, VIM produces cleaner and more homogeneous melts, devoid of harmful impurities and inclusions. This purity enhances the mechanical properties and overall performance of the resulting materials, making them highly desirable for various applications.
Controlled Atmosphere
In the vacuum chamber of VIM equipment, the atmosphere is meticulously controlled, allowing for precise regulation of gas composition and pressure. By introducing only specified gases at exact pressures, VIM ensures tight control over the chemical composition of the molten material, minimizing the risk of unwanted oxidation or reactions with ambient gases. This level of control is crucial for producing alloys with consistent properties and minimizing material wastage.
Process Efficiency and Flexibility
Beyond its environmental and quality benefits, VIM offers unmatched process efficiency and flexibility. Its rapid heating cycles and uniform heating of metal charges significantly increase production rates while reducing defect rates. Moreover, VIM's versatility enables the melting of various metals and alloys with ease, facilitating quick changeovers between materials and allowing for immediate shutdown if necessary. This agility in production enhances operational efficiency and adaptability to changing manufacturing demands.
Application and Future Prospects
The widespread adoption of vacuum induction smelting technology across industries underscores its immense potential and versatility. From small-scale experimental research to large-scale industrial production, VIM has proven its effectiveness and reliability. Its straightforward operation and fast melting temperatures make it a preferred choice for manufacturers seeking precision and consistency in their production processes. As technology continues to advance, the application of VIM is expected to expand further, driving innovation and efficiency in metal smelting and refining processes.
Vacuum Sintering: Enhancing Efficiency and Quality
In addition to vacuum induction melting, vacuum sintering emerges as another vital process for enhancing efficiency and product quality in metal manufacturing. By sintering metal powders at temperatures below the melting point in a vacuum environment, vacuum sintering offers several advantages. It eliminates reactions between metals and gases, enhances densification, and reduces sintering temperatures, thereby conserving energy and extending the life of sintering furnaces. The result is the production of high-quality metal products with improved mechanical properties and reduced energy consumption.
In conclusion, vacuum induction melting and vacuum sintering represent cutting-edge technologies that offer numerous advantages over traditional smelting methods. From energy efficiency and material purity to process flexibility and environmental sustainability, these advanced techniques are driving innovation and reshaping the landscape of metal manufacturing. As industries continue to prioritize sustainability and quality, the adoption of vacuum-based processes like VIM and vacuum sintering is poised to accelerate, ushering in a new era of efficiency and excellence in metal production.
Key Features of Vacuum Induction Melting Furnaces
Vacuum induction melting furnaces are pivotal in metallurgical processes, offering a spectrum of features tailored for precise control and enhanced productivity. Here's a comprehensive exploration of their key components and advancements:
Structural Components
The furnace comprises an airtight water-cooled steel jacket, engineered to sustain requisite vacuum conditions during processing. Within this enclosure, metal undergoes melting in a crucible nestled within a water-cooled induction coil. Furthermore, the furnace interior is typically lined with refractories suited to withstand extreme temperatures.
Process Enhancements
1. Environmental Control
- Molten metal casting can be executed under vacuum or inert gas environments, ensuring optimal conditions for alloy formation and purity maintenance.
2. Additional Features
- Furnaces may integrate tilt and pour mechanisms, casting chambers, and sampling ports to facilitate varied production needs.
- Mould handling facilities enable automated or semi-automated processing, sometimes incorporating vacuum interlock systems for seamless operation.
Future Development Trends
The evolution of vacuum induction melting equipment reflects a transition towards multifunctional structures adept at accommodating diverse technological processes. Modular configurations are envisioned to dominate, allowing tailored combinations of components to meet specific process requirements efficiently.
Precision Control and Automation
The integration of advanced technologies such as computer systems and intelligent signal acquisition empowers precise process control. Friendly man-machine interfaces streamline operation, reducing labor costs and enhancing operational simplicity.
Auxiliary Systems
In addition to core components, auxiliary systems like power supplies, control units, and cooling systems play vital roles. These systems ensure energy input for melting and prevent overheating in critical components.
Structural Considerations
Attention to structural design is paramount to prevent vacuum discharge. Insulation of all charged bodies within the furnace shell and the elimination of sharp edges in inductor design are crucial to ensure uninterrupted operation.
Key Advantages
- Melting of Certain Titanium Alloys: Vacuum conditions enable the melting of titanium alloys, expanding the furnace's applicability.
- Prevention of Chemical Reactions: Vacuum environments shield melted metals and alloys from undesirable chemical reactions with non-metallic inclusions.
- Removal of Harmful Gases: The vacuum state facilitates the elimination of harmful dissolved gases and pollutants from liquid molten metal, ensuring material purity.
In conclusion, vacuum induction melting furnaces embody versatility and precision, driving advancements in metallurgical processes through innovative design and technological integration.
Environmental and Performance Benefits
Vacuum induction melting (VIM) offers significant environmental and performance advantages, making it a preferred method for producing high-purity materials with superior properties.
High Purity and Quality
VIM excels in producing materials of exceptional purity and quality. By operating within a vacuum environment, VIM eliminates the risk of contamination from atmospheric gases such as oxygen and nitrogen. This ensures a cleaner and more homogeneous melt, devoid of harmful inclusions and impurities that could compromise the mechanical integrity of the material. Consequently, the resulting alloys exhibit enhanced mechanical properties and performance characteristics.
Controlled Atmosphere
Within the vacuum chamber, the atmosphere is meticulously controlled, allowing for precise regulation of gas composition and pressure. This level of control is paramount in achieving the desired chemical composition of the melted material while preventing undesired oxidation or reactions with ambient gases. As a result, VIM enables the production of materials with consistent chemical properties and minimal reactivity, ensuring superior performance in various applications.
Advantages Summarized
The advantages of utilizing a vacuum induction melting furnace are manifold:
-
Elimination of Gases: VIM operates under extremely low pressures, typically around 0.000001 atmosphere. This environment facilitates the removal of undesirable gases and volatile elements from the raw materials during the melting process, ensuring the production of high-purity alloys.
-
Precise Chemical Analysis: The absence of atmosphere in the vacuum chamber allows for exceptional and reproducible control over the chemical composition of the melted materials. This precision enables the production of alloys with tailored compositions and desired properties, enhancing overall process efficiency and product quality.
-
Superior Process Control: VIM offers independent control over pressure, temperature, and inductive stirring, providing unparalleled process control. This flexibility allows for the development of optimized melt practices specific to each alloy composition, further enhancing the performance and consistency of the produced materials.
In addition to the environmental benefits, the advantages of a vacuum induction furnace extend to the processing of various metals and alloys:
- Purity Enhancement: The absence of air and slag pollution in vacuum induction furnaces contributes to the production of relatively pure alloys with high-performance levels.
- Gas Removal: Operating under vacuum conditions enables the reduction of gas content in melted steel and alloys, resulting in materials with lower gas concentrations and improved properties.
- Oxidation Prevention: Processing metals in a vacuum environment mitigates the risk of oxidation, preserving the integrity of the processed material.
- Impurity Evaporation: Impurities such as lead (Pb) and bismuth (Bi) can evaporate more readily in a vacuum, facilitating the purification of the material during the smelting process.
In conclusion, vacuum induction melting furnaces offer a comprehensive solution for producing high-purity materials with superior performance characteristics, while also mitigating environmental pollution and ensuring process efficiency.
CONTACT US FOR A FREE CONSULTATION
KINTEK LAB SOLUTION's products and services have been recognized by customers around the world. Our staff will be happy to assist with any inquiry you might have. Contact us for a free consultation and talk to a product specialist to find the most suitable solution for your application needs!