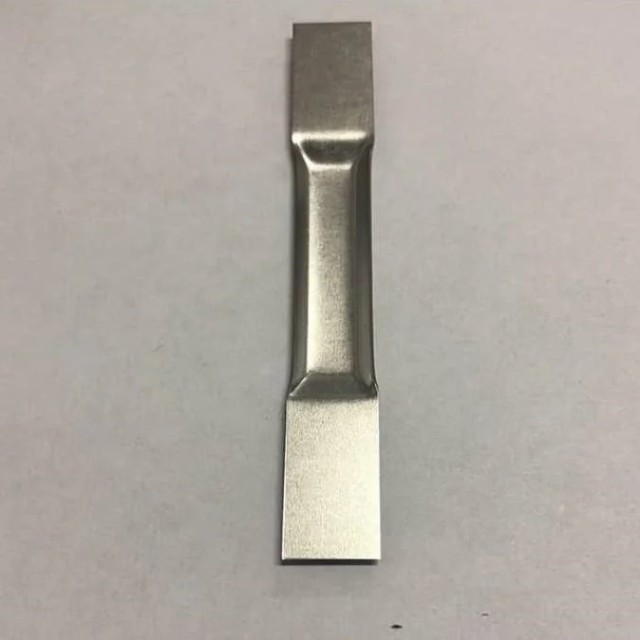
Thin Film Deposition Parts
Molybdenum Tungsten Tantalum Evaporation Boat for High Temperature Applications
Item Number : KME01
Price varies based on specs and customizations
- Material
- Tungsten / Molybdenum / Tantalum
- Specification
- See the form
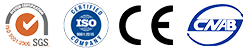
Shipping:
Contact us to get shipping details Enjoy On-time Dispatch Guarantee.
Why Choose Us
Reliable PartnerEasy ordering process, quality products, and dedicated support for your business success.
Introduction
Evaporation boats are used in the resistance evaporation process to heat and evaporate materials. They are made of materials with low vapor pressures, such as tungsten, molybdenum, molybdenum-lanthanum (ML), molybdenum-yttrium oxide (MY), or tantalum, to ensure that no particles of the boat material enter the vapor and the final layer. Evaporation boats have excellent corrosion resistance, low vapor pressures, good electrical conductivity, a very high melting point, and are dimensionally stable.
Application
Evaporation boat sources are used in thermal evaporation systems to deposit metals, alloys, and materials. They come in different thicknesses made of tungsten, tantalum, and molybdenum, ensuring compatibility with various power sources. These boats are crucial for vacuum evaporation and thin film deposition, including electron beam fabrication. They are widely employed in industries such as vacuum coating, electronics, solar energy, and metallurgy. To prevent cracking, gradual heating of the container is essential. Evaporation boats are versatile tools playing a vital role in materials analysis and thin film deposition processes.
Molybdenum, tungsten, and tantalum evaporation boats find applications in various industries, including:
- Vacuum evaporation of materials
- Carrying boats in furnace machines
- Rare earth industry
- Nuclear fuel sintering
- Capacitor discharge sintering
Detail & Parts
Length 100 width 8 thickness 0.2/0.3mm | Length 100 width 15 thickness 0.2/0.3/0.5mm | Length 100 width 20 thickness 0.2/0.3/0.5mm | Groove size: length 50 deep 2.6 |
Principle
Molybdenum/tungsten/tantalum evaporation boats are used in thermal evaporation systems to deposit a wide range of metals, alloys, and materials. The boats are heated by passing an electric current through them, which causes the material to evaporate. The evaporated material then condenses on the substrate, forming a thin film. The thickness of the film can be controlled by the amount of current passed through the boat and the evaporation time.
Advantages
- Excellent corrosion resistance
- Low vapor pressures
- Good electrical conductivity
- Very high melting point
- Dimensionally stable
FAQ
What Are Thermal Evaporation Sources?
Precautions For Using Evaporation Boats.
What Are The Main Types Of Thermal Evaporation Sources?
How Do Thermal Evaporation Sources Work?
What Are The Advantages Of Using Thermal Evaporation Sources?
What Applications Are Thermal Evaporation Sources Used For?
4.8
out of
5
The build quality of this boat is superb. It's well worth the money.
4.6
out of
5
These evaporation boats are of the highest quality and worked very well for my research.
4.9
out of
5
The tantalum evaporation boat I received arrived quickly and it functions perfectly.
4.7
out of
5
I highly recommend these boats. They're durable and heat resistant, making them perfect for my application.
4.9
out of
5
These evaporation boats are a great value for the price. They're made of high-quality materials and perform very well.
4.7
out of
5
I'm very satisfied with these evaporation boats. They're easy to use and clean, and they produce excellent results.
4.8
out of
5
These evaporation boats are a great addition to my lab. They're versatile and can be used for a variety of applications.
4.6
out of
5
I'm very happy with these evaporation boats. They're well-made and perform as expected.
Products
Molybdenum Tungsten Tantalum Evaporation Boat for High Temperature Applications
REQUEST A QUOTE
Our professional team will reply to you within one business day. Please feel free to contact us!
Related Products
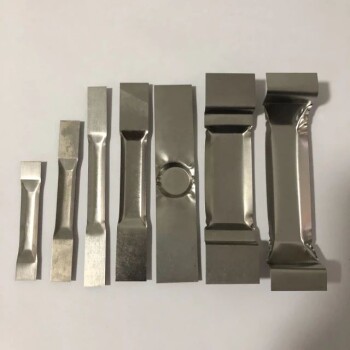
Tungsten Evaporation Boat for Thin Film Deposition
Learn about tungsten boats, also known as evaporated or coated tungsten boats. With a high tungsten content of 99.95%, these boats are ideal for high-temperature environments and widely used in various industries. Discover their properties and applications here.
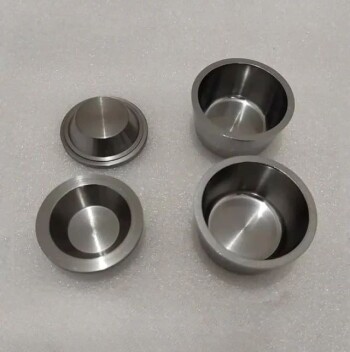
Tungsten and molybdenum crucibles are commonly used in electron beam evaporation processes due to their excellent thermal and mechanical properties.
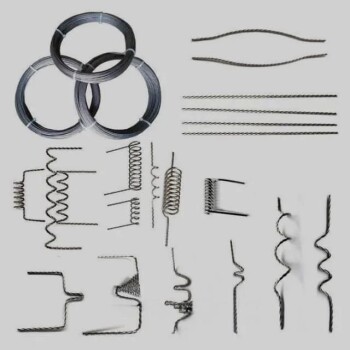
Thermally Evaporated Tungsten Wire for High Temperature Applications
It has a high melting point, thermal and electrical conductivity, and corrosion resistance. It is a valuable material for high temperature, vacuum and other industries.
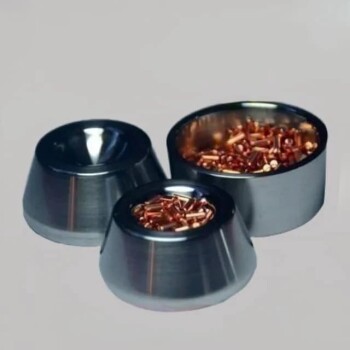
Electron Beam Evaporation Coating Gold Plating Tungsten Molybdenum Crucible for Evaporation
These crucibles act as containers for the gold material evaporated by the electron evaporation beam while precisely directing the electron beam for precise deposition.
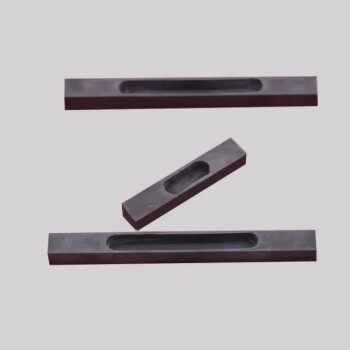
High Purity Pure Graphite Crucible for Evaporation
Vessels for high temperature applications, where materials are kept at extremely high temperatures to evaporate, allowing thin films to be deposited on substrates.
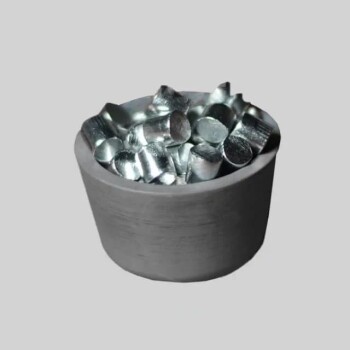
Electron Beam Evaporation Coating Conductive Boron Nitride Crucible BN Crucible
High-purity and smooth conductive boron nitride crucible for electron beam evaporation coating, with high temperature and thermal cycling performance.
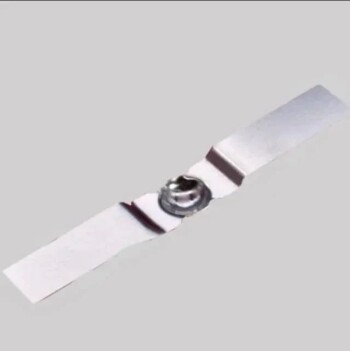
Hemispherical Bottom Tungsten Molybdenum Evaporation Boat
Used for gold plating, silver plating, platinum, palladium, suitable for a small amount of thin film materials. Reduce the waste of film materials and reduce heat dissipation.
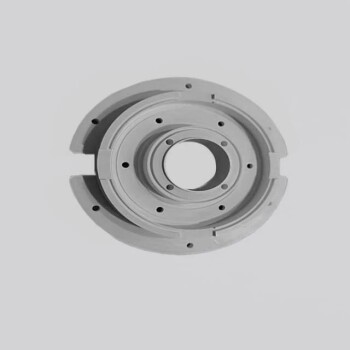
Custom Boron Nitride (BN) Ceramic Parts
Boron nitride (BN) ceramics can have different shapes, so they can be manufactured to generate high temperature, high pressure, insulation and heat dissipation to avoid neutron radiation.
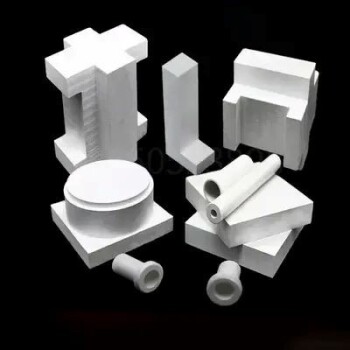
Advanced Engineering Fine Ceramics Boron Nitride (BN) Ceramic Parts
Boron nitride ((BN) is a compound with high melting point, high hardness, high thermal conductivity and high electrical resistivity. Its crystal structure is similar to graphene and harder than diamond.
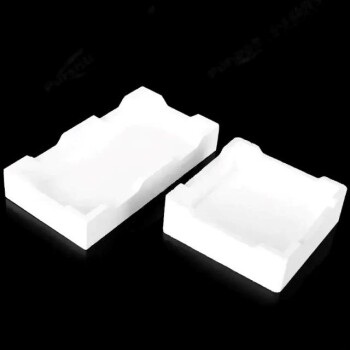
Advanced Engineering Fine Ceramics Alumina Ceramic Saggar for Fine Corundum
Alumina sagger products have the characteristics of high temperature resistance, good thermal shock stability, small expansion coefficient, anti-stripping, and good anti-powdering performance.
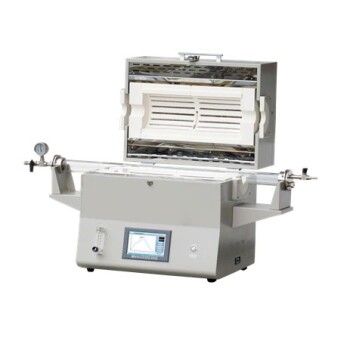
1400℃ Laboratory Quartz Tube Furnace with Alumina Tube Tubular Furnace
Looking for a tube furnace for high-temperature applications? Our 1400℃ Tube Furnace with Alumina Tube is perfect for research and industrial use.

Zirconia Ceramic Gasket Insulating Engineering Advanced Fine Ceramics
Zirconia insulating ceramic gasket has high melting point, high resistivity, low thermal expansion coefficient and other properties, making it an important high temperature resistant material, ceramic insulating material and ceramic sunscreen material.
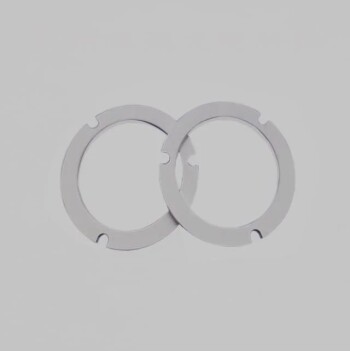
Hexagonal Boron Nitride HBN Ceramic Ring
Boron nitride ceramic (BN) rings are commonly used in high temperature applications such as furnace fixtures, heat exchangers and semiconductor processing.
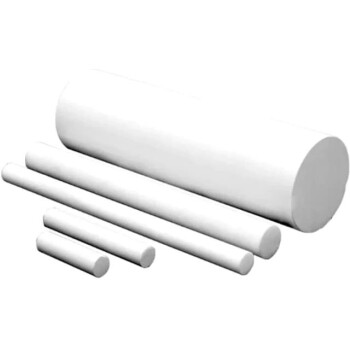
Boron Nitride (BN) Ceramic Rod for High Temperature Applications
Boron nitride (BN) rod is the strongest boron nitride crystal form like graphite, which has excellent electrical insulation, chemical stability and dielectric properties.
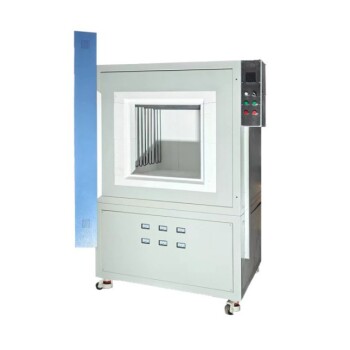
High Temperature Muffle Oven Furnace for Laboratory Debinding and Pre Sintering
KT-MD High temperature debinding and pre-sintering furnace for ceramic materials with various molding processes. Ideal for electronic components such as MLCC and NFC.
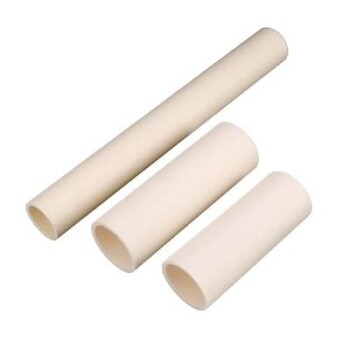
High Temperature Alumina (Al2O3) Furnace Tube for Engineering Advanced Fine Ceramics
High temperature alumina furnace tube combines the advantages of high hardness of alumina, good chemical inertness and steel, and has excellent wear resistance, thermal shock resistance and mechanical shock resistance.
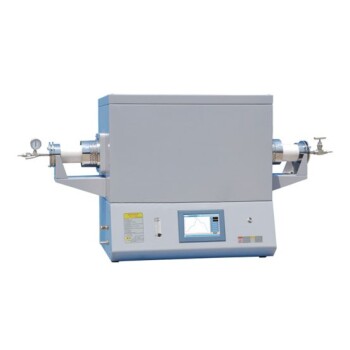
1700℃ Laboratory Quartz Tube Furnace with Alumina Tube Tubular Furnace
Looking for a high-temperature tube furnace? Check out our 1700℃ Tube Furnace with Alumina Tube. Perfect for research and industrial applications up to 1700C.
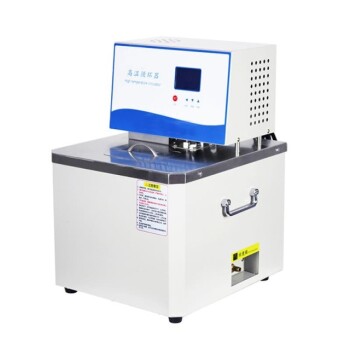
Efficient and reliable, KinTek KHB Heating Circulator is perfect for your lab needs. With a max. heating temperature of up to 300℃, it features accurate temperature control and fast heating.
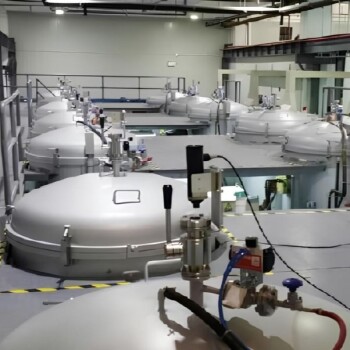
Graphite Vacuum Furnace High Thermal Conductivity Film Graphitization Furnace
The high thermal conductivity film graphitization furnace has uniform temperature, low energy consumption and can operate continuously.
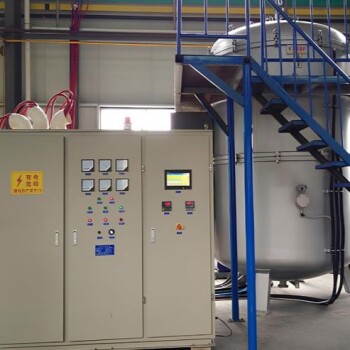
Large Vertical Graphite Vacuum Graphitization Furnace
A large vertical high-temperature graphitization furnace is a type of industrial furnace used for the graphitization of carbon materials, such as carbon fiber and carbon black. It is a high-temperature furnace that can reach temperatures of up to 3100°C.
Related Articles
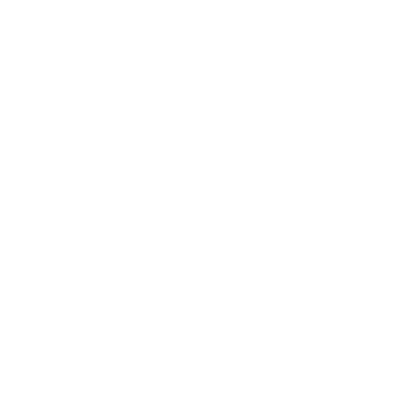
Understanding Evaporation Boats in Vacuum Coating
An in-depth look at evaporation boats, their materials, arrangement, temperature control, and corrosion issues in vacuum coating processes.
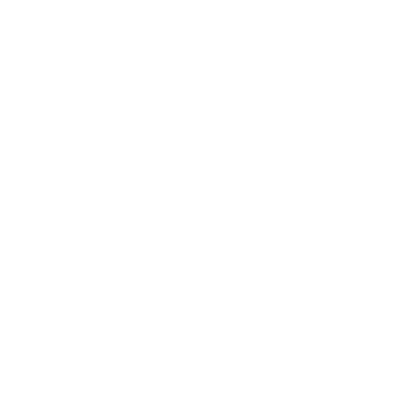
Challenges in the Development and Application of Tantalum in Vacuum Deposition Equipment
This article discusses the role of tantalum in vacuum deposition equipment, focusing on its properties, manufacturing challenges, and its critical applications in industries like OLED screen production.
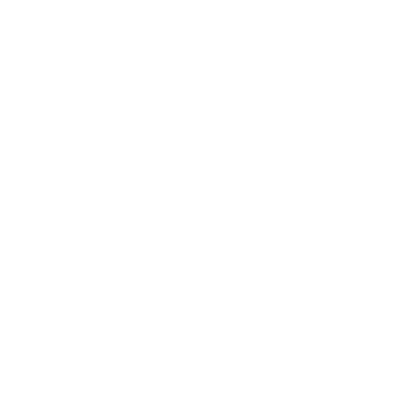
Electron Beam Evaporation Coating: Principles, Characteristics, and Applications
An in-depth analysis of electron beam evaporation coating technology, its advantages, disadvantages, and applications in thin film manufacturing.
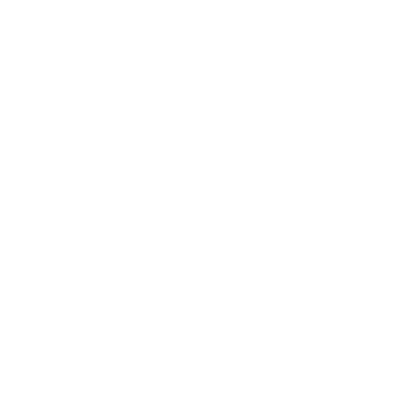
Electron Beam Evaporation Coating: Advantages, Disadvantages, and Applications
An in-depth look at the pros and cons of electron beam evaporation coating and its various applications in industries.
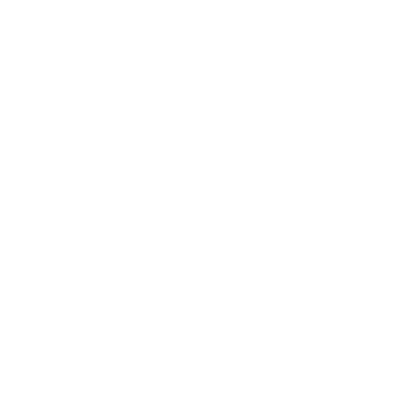
Types of Evaporation Sources for Evaporative Coating
Explore different evaporation sources used in thin film deposition, including filaments, crucibles, and evaporation boats.
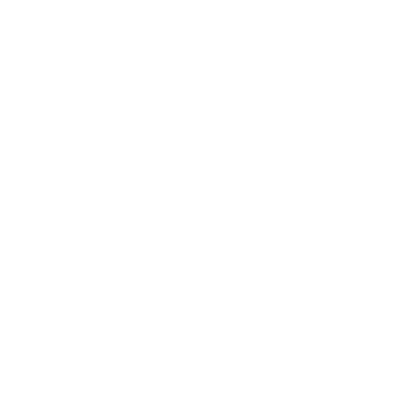
Electron Beam Evaporation Technology in Vacuum Coating
An in-depth look at electron beam evaporation, its types, advantages, and disadvantages in vacuum coating processes.
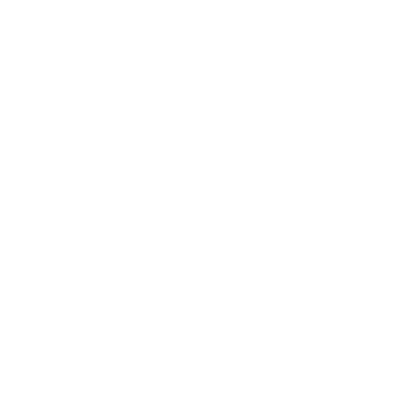
Electron Beam Evaporation: Advanced Thin Film Creation
Explores the technology and applications of electron beam evaporation in thin film production.
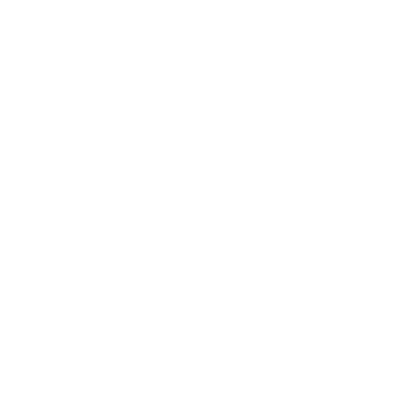
Understanding Evaporation Plating, Sputtering Plating, and Ion Plating
A detailed comparison of evaporation plating, sputtering plating, and ion plating techniques, their principles, types, and characteristics.
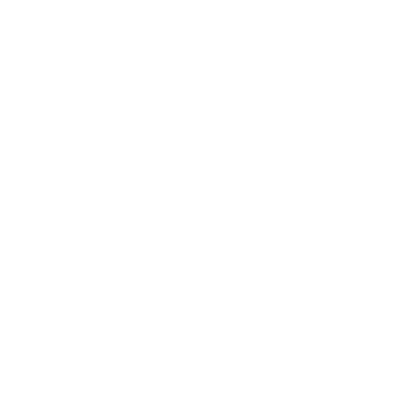
Electron Beam Evaporation Coating Technology and Material Selection
An in-depth look at the principles and applications of electron beam evaporation coating technology, including material selection and various fields of application.
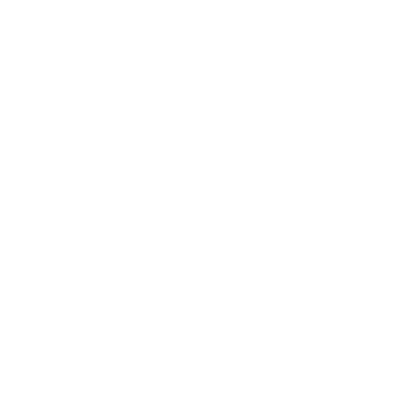
Comprehensive Overview of Vacuum Evaporation Systems
An in-depth look at vacuum evaporation systems, their principles, components, and applications.
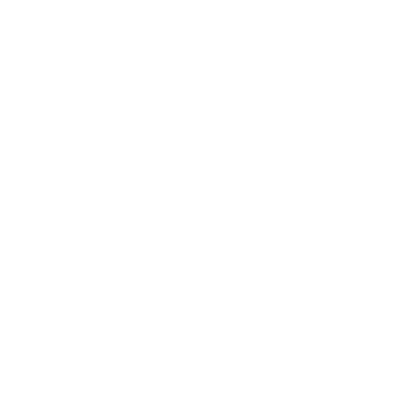
Exploring Various Vacuum Coating Technologies: Evaporation, Sputtering, and Ion Plating
This article delves into the different vacuum coating technologies, focusing on evaporation, sputtering, and ion plating, detailing their principles, advantages, and applications.
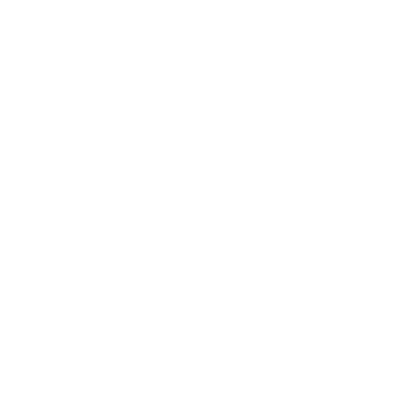
Selecting Heating Elements for Vacuum Furnaces
Guide on choosing heating elements and insulation screens for efficient vacuum furnace operation.