Introduction to Dental Sintering Furnaces
Dental sintering furnaces play a crucial role in the manufacturing process of dental crowns and other restorations. These furnaces are responsible for firing the restoration materials at the precise temperature and duration required to achieve optimal restoration quality and durability. They come in different types, such as open or closed furnaces, and offer various features, such as programmable firing cycles and vacuum systems. Choosing the right dental sintering furnace is essential for the success of dental restorations, as it can impact the accuracy of the fit, the strength of the material, and the overall longevity of the restoration.
Table of Contents
- Introduction to Dental Sintering Furnaces
- Importance of Proper Temperature and Firing Quality
- Types of Dental Sintering Furnaces
- Features to Consider When Choosing a Furnace
- The Impact of Furnace on Restoration Quality
- The Role of Dental Furnaces in Crown Manufacturing
- Conclusion: Importance of Choosing the Right Furnace
Importance of Proper Temperature and Firing Quality
Dental sintering furnaces play a crucial role in the production of dental restorations. One of the most significant factors that impact the quality and durability of the restoration is the temperature and firing quality. The process of sintering involves the heating of ceramic materials to a point where they fuse together, forming a solid, durable restoration. However, if the temperature or firing quality is not adequate, it can result in weak, brittle restorations that are prone to fracture.
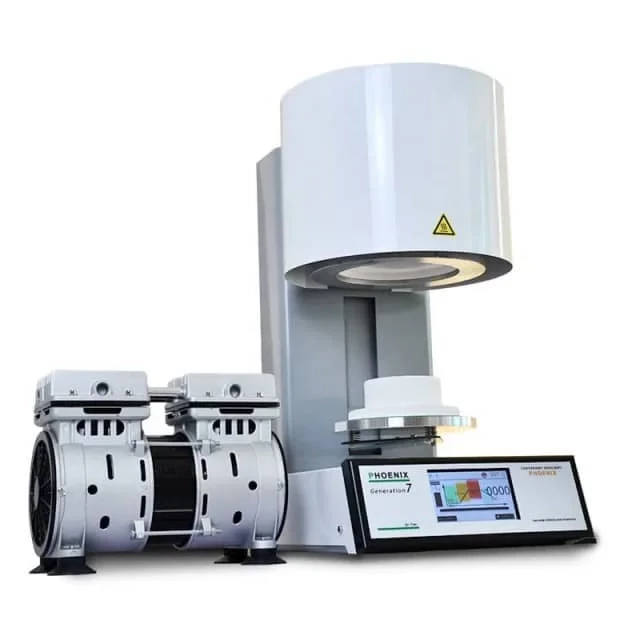
Proper Temperature
Proper temperature is crucial to achieving optimal restoration quality and durability. Firing at too low a temperature or for too short a time can result in weak, brittle restorations that are prone to fracture. On the other hand, firing at too high a temperature or for too long can lead to over-sintering, resulting in restorations that are too hard and prone to chipping or cracking. Recent studies indicate that firing at approximately 1500⁰C – 1550⁰C (depending on the temperature accuracy of the furnace) produces maximum strength in zirconia. A specific case in the study showed that strength drops from about 1280 MPa at 1500⁰C to about 980 MPa at 1600⁰C and only about 600 MPa at 1700⁰C. Most yttria partially-stabilized zirconia materials attain their ideal physical, mechanical and esthetic properties at approximately 1550⁰C.
Firing Quality
Dental technicians must also pay attention to the quality of the firing process itself, as inconsistencies in temperature or heat distribution can lead to uneven sintering and compromised restoration quality. The temperature within the furnace should be evenly distributed. It should also be equipped with QTK muffle technology and a reflecting floor to help spread the heat evenly throughout the firing chamber. A furnace with built-in infrared technology offers peace of mind. This type of technology will achieve reliable firing results and increase efficiency. The predrying process controlled by infrared technology reduces the risk of cracks occurring in the ceramic during the closing process.
In conclusion, the proper balance of temperature and firing time is crucial to achieving optimal restoration quality and durability. The use of dental sintering furnaces is essential to the production of quality, durable dental restorations. Dental technicians must ensure they use a furnace that offers pre-set programs and automation features, multiple program stages and a way to control the cooling rate of the zirconia restorations. By taking these factors into consideration, dental technicians can produce high-quality dental restorations that meet the needs of their patients.
Types of Dental Sintering Furnaces
Dental sintering furnaces are essential for producing high-quality dental restorations. There are several types of dental sintering furnaces available in the market today. In this section, we will discuss the three main types of dental sintering furnaces.
Conventional Sintering Furnace
The conventional sintering furnace is the most common type of sintering furnace available in the market. It uses a heating element to heat the ceramic material to a high temperature, which causes the material to fuse together. The conventional sintering furnace is capable of producing high-quality dental restorations such as crowns, bridges, and implants. It is also less expensive than other types of sintering furnaces. However, it is slower and less energy-efficient than other types of furnaces.
Microwave Sintering Furnace
Another type of sintering furnace is the microwave sintering furnace. It uses microwaves to heat the ceramic material, which makes it faster and more energy-efficient than conventional sintering furnaces. The microwave sintering furnace is capable of producing high-quality dental restorations such as crowns, bridges, and implants. However, it is more expensive than the conventional sintering furnace and requires careful handling of the ceramic material to avoid cracking.
Vacuum Sintering Furnace
The vacuum sintering furnace is the most advanced type of sintering furnace available in the market. It uses vacuum technology to sinter the ceramic material, which reduces the amount of air bubbles and porosity in the final product. The vacuum sintering furnace produces high-quality restorations that are resistant to wear and tear. However, it is the most expensive type of sintering furnace and requires specialized knowledge to operate.
In conclusion, the choice of dental sintering furnace depends on the specific needs of the dentist and the type of restoration required. The conventional sintering furnace is suitable for most dental restorations and is less expensive than other types of furnaces. The microwave sintering furnace is faster and more energy-efficient than the conventional sintering furnace but is more expensive and requires careful handling of the ceramic material. The vacuum sintering furnace is the most advanced type of sintering furnace and produces high-quality restorations, but is the most expensive and requires specialized knowledge to operate.
Features to Consider When Choosing a Furnace
When selecting a dental sintering furnace, it's essential to consider various features to ensure that you choose the right equipment for your dental laboratory. The following are some essential features to consider when selecting a furnace:
Temperature Range
The temperature range of a dental sintering furnace is crucial to consider since it determines the types of dental restorations that you can produce. The furnace should have a wide temperature range to accommodate different materials, such as ceramics and metals. A furnace with a temperature range of 1400°C to 1600°C is ideal for sintering zirconia and other dental materials.
Heating and Cooling Rates
The heating and cooling rates of a dental sintering furnace are crucial to consider since they affect the quality of the final restoration. A furnace with a fast heating rate will save you time, but it should not compromise the quality of the final restoration. The cooling rate should also be considered, as it can affect the strength and durability of the restoration.
Furnace Size and Capacity
The size and capacity of a dental sintering furnace are also essential features to consider. The furnace should have enough space to accommodate the size of the restorations you will be producing. A larger furnace is ideal for producing multiple restorations simultaneously, which increases productivity.
Build Quality and Durability
The build quality and durability of a dental sintering furnace are important factors to consider since the equipment is a significant investment. A durable furnace will last longer and provide a higher return on investment than a low-quality one. A furnace with a robust construction, such as ceramic fiberboard and high-purity heating elements, is more durable and reliable.
Automation and Programmability
Automation and programmability are also essential features to consider when selecting a dental sintering furnace. Programmable furnaces have pre-set cycles that ensure consistent firing and sintering of dental restorations. Automated furnaces also save time and reduce the risk of human error.
In conclusion, choosing the right dental sintering furnace is essential to produce high-quality, durable dental restorations. By considering the temperature range, heating and cooling rates, furnace size and capacity, build quality and durability, and automation and programmability, you can select a furnace that meets your specific needs and produces consistent, high-quality restorations.
The Impact of Furnace on Restoration Quality
Dental sintering furnaces play a vital role in ensuring the quality and durability of dental restorations. The sintering process involves heating a ceramic material to a high temperature, causing it to fuse together and become denser. The furnace used in this process must maintain an accurate and consistent temperature to ensure that the restoration is properly sintered and has the desired strength and durability.
The Importance of Choosing the Right Furnace
The type of furnace used can significantly impact the quality of the restoration. Factors such as the heating rate, cooling rate, and atmosphere control can all influence the final product. Investing in a high-quality dental sintering furnace is critical for dental laboratories and practitioners to consistently produce high-quality restorations. In addition to ensuring the proper sintering of the ceramic material, a quality furnace can also reduce the chance of defects such as warping or cracking.
The Role of Calibration
The temperature control in the dental furnace changes with time due to chemical and physical influences, as well as soiling and deposits caused by the fired objects. The thermocouple, the heating element, and the insulation are particularly affected by these influences. Calibration ensures that the temperature control is correct again. If you do not calibrate, this can lead to faulty temperatures in the furnace, which will have a negative effect on your restorations. Therefore, the furnace must be calibrated at regular intervals.
The Importance of Understanding Your Furnace
Differences in sintering furnaces are not just based on brand and price. Heating elements, number of programs, heating chamber configurations, sintering speeds, and even unit size all vary somewhat. The driving force behind newer furnace designs and capabilities is the growing number of zirconia materials and their required sintering parameters. Most zirconia materials are sintered at or below 1,550⁰C with a slow heat rise (4⁰C - 10⁰C per minute). Some zirconia manufacturers are recommending lower temperatures and some higher.
Proper Temperature
Proper temperature is crucial to the quality of the restoration. Recent studies indicate that firing at approximately 1500⁰C - 1550⁰C (depending on the temperature accuracy of the furnace) produces maximum strength in zirconia. A higher temperature may result in lowered stability and uncontrolled transformation, causing cracking of the zirconia. Temperatures that are too high for the material also cause a lowering of translucency. Sticking to the manufacturer’s recommended firing schedule is critical, as long as the manufacturer is reputable. Most yttria partially-stabilized zirconia materials attain their ideal physical, mechanical and esthetic properties at approximately 1550⁰C.
Program Stages
Program Stages enable you to vary temperature, delayed starts, ramp rates, and hold times to adjust your final result. Since most sintering cycles are long, you may want to increase the rate rise from ambient temperature to the point where sintering begins, then throttle back in a subsequent stage to optimize the translucency.
In conclusion, investing in a high-quality dental sintering furnace and understanding the impact of furnace on restoration quality is critical for dental professionals. Factors such as the type of furnace used, calibration, proper temperature, and program stages can all significantly impact the quality and durability of dental restorations. By understanding the role of the furnace in the sintering process and choosing the appropriate furnace for their laboratory, dental professionals can consistently produce high-quality restorations that meet the needs of their patients.
The Role of Dental Furnaces in Crown Manufacturing
Dental sintering furnaces have revolutionized the field of crown manufacturing, improving the quality and durability of restorations. These furnaces use high temperatures to fuse dental materials together, resulting in a strong and resilient restoration.
The Need for Dental Furnaces in Crown Manufacturing
Before the introduction of dental furnaces, dental restorations were made using low-quality materials and outdated techniques. These restorations were prone to failure, such as chipping, cracking, and fracture. Dental furnaces have played a significant role in improving the quality and durability of crowns, bridges, inlays, and onlays.
The Working Principle of Dental Furnaces
Dental furnaces work by subjecting dental materials to high temperatures and pressures to process them into a hardened, final state. The heating coils are usually located in the upper housing of the furnace and arranged concentrically around the restoration. A motor-driven mechanism closes the firing chamber with the restoration inside, either by raising the firing platform or lowering the upper housing of the furnace.
Precise Control of the Sintering Process
The role of dental furnaces in crown manufacturing cannot be overstated, as they allow for precise control of the sintering process, ensuring consistent and reliable results. Many settings can be programmed precisely and independently of each other, for example times can be set to the split second (preheating/drying, heat-rate, hold-time, cooling) and firing temperatures for various materials such as opaquer, shoulder and dentine porcelains as well as glaze firings programmed accurately.
Advancements in Dental Furnace Technology
With the advancements in dental furnace technology, manufacturers can now produce furnaces that are easy to use and maintain, with features such as programmable settings and automatic shut-off functions. The latest dental furnaces feature touchscreen controls, pre-set programs and even the ability to connect to the internet.
Dental Furnaces for Ceramic Restorations
Dental furnaces are designed to work with a range of ceramic materials, and some furnaces are designed to also produce the pressure needed to press glass ceramics, and other pressable materials. Modern, 21st century porcelain furnaces are technically sophisticated, electronically-controlled devices with programmable cycles for firing dental porcelains.
Conclusion: Importance of Choosing the Right Furnace
In conclusion, the choice of dental sintering furnace is crucial in ensuring the quality and durability of dental restorations. Proper temperature and firing quality are essential to achieve accurate and consistent results. There are various types of dental sintering furnaces available, each with unique features to consider when choosing the right one for your needs. The furnace plays a critical role in the manufacturing process of dental crowns and other restorations, and choosing the right one can make a significant impact on the final product. Therefore, it is essential to invest in a high-quality dental sintering furnace to ensure the longevity and success of dental restorations.
CONTACT US FOR A FREE CONSULTATION
KINTEK LAB SOLUTION's products and services have been recognized by customers around the world. Our staff will be happy to assist with any inquiry you might have. Contact us for a free consultation and talk to a product specialist to find the most suitable solution for your application needs!