Introduction to Zirconia Sintering Furnaces
Zirconia sintering furnaces are designed to give dental professionals the ability to create dental restorations with the highest level of precision and accuracy. They work by heating zirconia material to a specific temperature, allowing it to bond and form into the desired shape. These furnaces are essential for creating strong, durable dental restorations that can withstand the pressure and strain of the human mouth. Without them, dental professionals would not be able to offer the same level of quality and longevity in their dental restorations.
Table of Contents
- Introduction to Zirconia Sintering Furnaces
- Dental Furnace Features for Optimal Results
- Program Stages and Their Benefits
- Capacity and Safety Considerations
- Latest Advancements in Sintering Furnaces
- Benefits of Newer Furnace Designs
- Chairside Sintering and Its Advantages
- Conclusion: Choosing the Best Sintering Furnace
Dental Furnace Features for Optimal Results
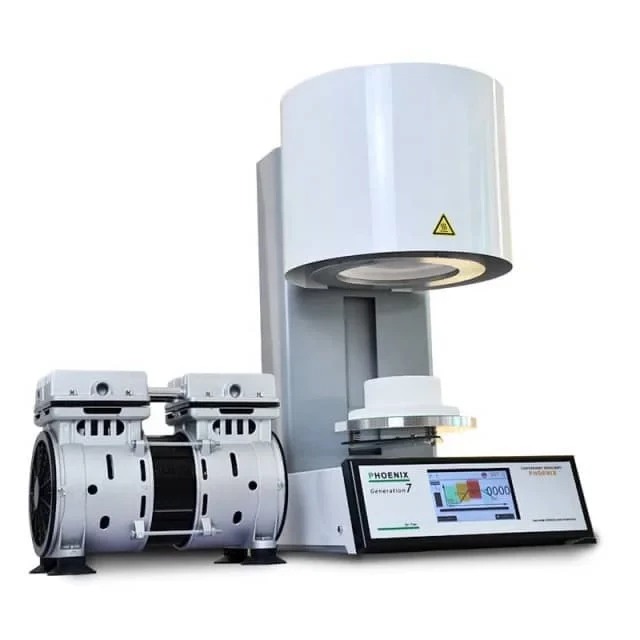
When it comes to producing high-quality dental restorations, investing in the latest zirconia sintering furnaces is crucial. To achieve optimal results, it is essential to consider the features of the furnace. Here are some important features to consider:
Vacuum Technology
One of the latest advancements in zirconia sintering furnaces is the use of vacuum technology. This feature reduces the risk of contamination and ensures a uniform sintering process, resulting in better quality dental restorations.
Pre-Programmed Sintering Cycles
Another important feature is the use of pre-programmed sintering cycles. This feature allows for greater control over the sintering process and better results. The sintering process can be programmed for specific materials, ensuring that the furnace heats and cools at the optimal rate for the material being used.
Cooling Function
Some furnaces also include a cooling function, which prevents cracks or defects from occurring during the cooling process. This feature is particularly important for preventing issues with the final product, as even small cracks or defects can affect the fit and function of the dental restoration.
Wireless Connectivity
In addition to the above features, some of the latest furnaces on the market are equipped with wireless connectivity. This feature enables dental technicians to monitor the sintering process remotely, providing greater flexibility and efficiency in the laboratory.
Ease of Use
When selecting a dental furnace, it is important to consider how easy it is to use. The furnace should have a large, easy-to-use touchscreen interface with icon controls that are familiar to the user. Additionally, the furnace should be easy to clean and maintain between uses.
Energy Efficiency
Energy efficiency is another important feature to consider when selecting a dental furnace. Some furnaces automatically switch to standby mode to save energy when not in use, reducing energy consumption and costs.
Shade Determination
Finally, some furnaces can help with the shade selection process. The clinician takes a picture of the selected shades and natural teeth with a smartphone and sends it to the lab. The digital shade assistant (DSA) software of the furnace determines the final tooth shade, which is then reproduced. This feature ensures greater accuracy and consistency in the final product.
In conclusion, investing in the latest zirconia sintering furnaces with advanced features not only improves the quality of dental restorations but also enhances the efficiency of the laboratory and reduces the risk of errors. When selecting a furnace, it is important to consider the features that are most important for your specific needs. By choosing a furnace with the right features, dental technicians can achieve optimal results and provide their clients with the best possible dental restorations.
Program Stages and Their Benefits
Zirconia sintering furnaces have come a long way in recent years, and one of the most significant advancements has been the development of program stages that enable an efficient, precise, and safe production process for dental prostheses. The program stages of modern zirconia sintering furnaces include pre-drying, heating, soaking, cooling, and venting.
Pre-Drying
The pre-drying stage is crucial for removing any moisture from the zirconia material, which can affect the sintering process's outcome. This stage ensures that the zirconia material is completely dry before the sintering process begins.
Heating
The heating stage is designed to prepare the zirconia material for the sintering process. The material is heated up to the required temperature, which can range from 1350°C to 1600°C, depending on the type of zirconia used. This stage also helps to eliminate any remaining moisture from the material.
Soaking
The soaking stage is where the zirconia material is held at the sintering temperature for a specific period, typically ranging from 30 minutes to 2 hours. This stage allows for the uniform distribution of heat, which is essential for the sintering process's success.
Cooling
The cooling stage is designed to reduce the risk of warping or cracking in the final product. The zirconia material is cooled down slowly to room temperature, which can take several hours, depending on the cooling rate used. This stage is critical in ensuring that the final product is consistent and stable.
Venting
The venting stage is the final stage in the sintering process. This stage removes any gases that may have been produced during the sintering process, ensuring that the final product is free of defects.
Each of these program stages has its own benefits, and the combination of them is what makes modern zirconia sintering furnaces so efficient and precise. These furnaces enable the production of high-quality dental prostheses that are long-lasting and provide patients with excellent results.
Capacity and Safety Considerations
Increased Capacity
Zirconia sintering furnaces have undergone significant advancements in recent years, with a focus on increasing their capacity and efficiency. One of the most notable developments in this regard is the development of larger furnace chambers. These chambers can now accommodate more dental prostheses in a single cycle, resulting in increased productivity and reduced processing time. This increase in capacity has allowed dental professionals to produce a greater number of high-quality dental prostheses in a shorter amount of time, thereby improving patient outcomes.
Advanced Control Systems
Another significant advancement in zirconia sintering furnaces is the use of advanced control systems. These systems are designed to monitor the temperature and pressure within the furnace to prevent any accidents or malfunctions. With this technology, dental professionals can now ensure that their furnaces operate at optimal levels, reducing the risk of equipment failure and improving safety.
Automatic Shut-Off Systems
In addition to advanced control systems, zirconia sintering furnaces now feature automatic shut-off systems. These systems are designed to ensure that the furnace shuts down in the event of a malfunction or overheating. This feature is critical for ensuring the safety of both the dental professional and the patient. With automatic shut-off systems in place, the risk of accidents or injuries is greatly reduced.
Safer and More Efficient
Overall, the latest advancements in zirconia sintering furnaces have made them safer, more efficient, and more cost-effective for dental laboratories. These improvements have revolutionized the dental industry, making it easier for dental professionals to provide their patients with the best possible care. By increasing capacity, improving control systems, and adding automatic shut-off systems, zirconia sintering furnaces have become a powerful tool for dental professionals, allowing them to produce high-quality dental prostheses quickly and safely. As dental technology continues to evolve, it's clear that zirconia sintering furnaces will continue to play an important role in dental laboratories around the world.
Latest Advancements in Sintering Furnaces
Sintering furnaces are an essential component of the manufacturing process of dental restorations. In recent years, there have been significant advancements in zirconia sintering furnaces for dental applications. These advancements have revolutionized the dental industry by providing greater precision, efficiency, and safety in the production of dental restorations. In this section, we will discuss the latest advancements in sintering furnaces that have made them more effective and efficient.
Improved Heating Technology
The latest advancements in sintering furnaces have introduced advanced heating technology that provides greater control over the sintering process. These furnaces use programmable software to regulate temperature and ensure uniform heating of the zirconia material. The heating elements are made of special ceramic materials that can withstand high temperatures and provide even heating throughout the sintering process. These improvements have resulted in more precise restorations.
Faster Sintering Times
The latest sintering furnaces offer faster sintering times, allowing for quicker production of restorations. The speed of sintering is crucial in dental laboratories where time is of the essence. With these advancements, dental laboratories can produce more restorations in less time, which is beneficial for both the laboratory and the patient.
Improved Safety Features
Some of the newer models of sintering furnaces have improved safety features, such as automatic shut-off in case of an emergency. These features help prevent accidents and ensure the safety of the patient and the dental laboratory staff. The latest sintering furnaces also have a built-in ventilation system that removes harmful fumes and gases, making them safer to use.
Greater Efficiency
The latest sintering furnaces are more efficient in terms of energy consumption and material usage. They can sinter more restorations using less energy and zirconia material, resulting in cost savings for the dental laboratory. These advancements have also made sintering furnaces more environmentally friendly, reducing the carbon footprint of dental laboratories.
In conclusion, the latest advancements in sintering furnaces have revolutionized the dental industry by providing greater precision, efficiency, and safety in the production of dental restorations. Improved heating technology, faster sintering times, improved safety features, and greater efficiency are some of the significant advancements that have made sintering furnaces more effective and efficient. Dental laboratories can benefit greatly from these advancements, producing more restorations in less time, reducing costs, and providing better quality restorations to their patients.
Benefits of Newer Furnace Designs
Advancements in zirconia sintering furnace designs have brought about several benefits over their older counterparts. These new furnace designs offer improved temperature control, cooling systems, and software interfaces, to name a few.
Improved Heating Elements
One of the significant benefits of newer furnace designs is the use of advanced heating elements that provide more even and precise temperature control. The use of zirconia dental restorations requires precise temperature control to ensure consistent sintering results. Advanced heating elements such as Moly Disilicide or Silicon Carbide provide better temperature control, which results in better quality dental restorations.
Advanced Cooling Systems
Incorporating advanced cooling systems is another benefit of newer furnace designs. Rapid cooling of sintered restorations is essential to prevent warping and cracking. Advanced cooling systems help cool the sintered restorations more efficiently, resulting in better quality restorations.
Intuitive Software Interfaces
Newer furnace designs come equipped with high-resolution touchscreens and intuitive software interfaces that allow for easy programming and monitoring of the sintering process. These interfaces provide a user-friendly experience, allowing for precise and accurate programming for the sintering process.
Improved Efficiency and Accuracy
The latest advancements in zirconia sintering furnaces have improved the efficiency and accuracy of the sintering process. With better temperature control, advanced cooling systems, and intuitive software interfaces, the sintering process is more consistent and accurate, resulting in higher quality dental restorations.
In conclusion, the latest advancements in zirconia sintering furnace designs have brought about significant benefits to the field of dental applications. Improved heating elements, advanced cooling systems, and intuitive software interfaces have improved the efficiency and accuracy of the sintering process, resulting in better quality dental restorations.
Chairside Sintering and Its Advantages
Zirconia sintering furnaces have revolutionized the dental industry by providing a more efficient and streamlined process for the manufacturing of dental prostheses. One of the latest advancements in zirconia sintering furnace technology is the development of chairside sintering capabilities. Chairside sintering enables the production and completion of restorations in a single dental appointment, providing numerous advantages.
Reduced Turnaround Time
The use of chairside sintering significantly reduces the turnaround time for dental restorations. Traditionally, the process of manufacturing dental prostheses required multiple appointments over a period of several weeks. With chairside sintering, the entire process is completed in a single appointment, allowing for a quicker and more efficient turnaround time.
Improved Patient Satisfaction
Chairside sintering also improves patient satisfaction by providing a more convenient and comfortable experience. Patients no longer have to schedule multiple appointments or wait weeks for their restoration to be completed. The entire process is completed in a single appointment, providing a more comfortable and stress-free experience for the patient.
Increased Productivity for Dental Practices
Chairside sintering also increases productivity for dental practices by allowing for a more efficient use of time and resources. With the traditional method of manufacturing dental prostheses, multiple appointments were required, which took up valuable time and resources. Chairside sintering enables the entire process to be completed in a single appointment, allowing for a more efficient use of time and resources.
Consistent and High-Quality Results
Zirconia sintering furnaces are designed to produce consistent and high-quality results, ensuring that each restoration is precise and accurate. With the latest advancements in technology, chairside sintering furnaces are able to produce consistent and high-quality results, providing dental professionals with a reliable and efficient solution for their dental restoration needs.
Conclusion: Choosing the Best Sintering Furnace
Choosing the right sintering furnace is crucial for obtaining optimal results in dental restorations. Several factors need to be considered, such as the furnace's capacity, safety features, and program stages. The latest advancements in sintering furnaces have made chairside sintering possible, which offers several advantages in terms of time and convenience. The benefits of newer furnace designs include more accurate temperature control and faster heating and cooling times. When choosing a sintering furnace, it's important to consider the specific needs of your dental practice and choose a furnace that meets those requirements.
CONTACT US FOR A FREE CONSULTATION
KINTEK LAB SOLUTION's products and services have been recognized by customers around the world. Our staff will be happy to assist with any inquiry you might have. Contact us for a free consultation and talk to a product specialist to find the most suitable solution for your application needs!