Introduction
Table of Contents
Isostatic pressing is a crucial technique used in powder metallurgy to achieve high-density components with improved mechanical properties. It involves subjecting a powder compact to equal pressure from all directions, resulting in uniform compaction and minimal defects. Isostatic pressing offers several advantages over traditional uniaxial pressing, such as improved density and microstructure control. In this blog post, we will explore the fundamentals of isostatic pressing and its applications in various industries. Whether you are a materials engineer or a business professional looking to gain a better understanding of this technique, read on to discover the world of isostatic pressing in powder metallurgy.
Overview of Isostatic Pressing
Definition of Isostatic Pressing
Isostatic pressing is a powder processing technique that involves applying pressure uniformly over the entire surface of a mold to compact the powder and create the desired shape. Unlike cold pressing, isostatic compaction eliminates die-wall friction, resulting in more uniform densities. It also allows for the evacuation of air from the loose powder, leading to increased density and fewer compact defects. Isostatic pressing is commonly used for compacting brittle or fine powders and can be used to create more complex shapes than uniaxial pressing.
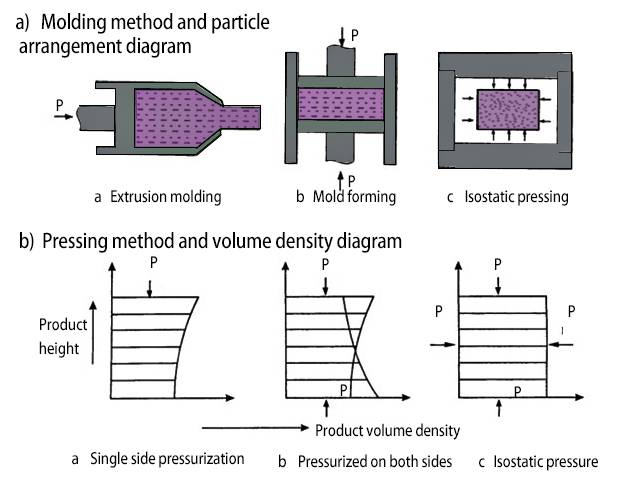
Impact on Density and Microstructure
Isostatic pressing provides increased and more uniform density compared to other pressing methods. By applying pressure equally in all directions, isostatic pressing eliminates die-wall friction and ensures uniform compaction of the powder. This results in a more uniform density distribution within the compacted part. The uniform density obtained through isostatic pressing is important for achieving good shape control and uniform properties during sintering.
Comparison with Uniaxial Pressing
Isostatic pressing differs from uniaxial pressing in several important ways. First, isostatic compaction takes place under hydrostatic conditions, where the pressure is transmitted equally in all directions. This eliminates die-wall friction and allows for the use of elastomeric molds instead of rigid dies. Second, isostatic pressing can be used to compact more complex shapes than uniaxial pressing. The uniform compaction pressure in isostatic pressing is not limited by the cross section-to-height ratio of the part.
When comparing uniaxial pressing to isostatic pressing, uniaxial pressing is more suitable for small shapes at high production rates. However, it may result in non-uniform densities, especially for large aspect ratios. Isostatic pressing, on the other hand, offers more even shrinkage during sintering and does not require a wax binder, eliminating the need for dewaxing operations.
Isostatic pressing is frequently chosen to achieve high compact densities and access shapes that cannot be compacted in uniaxial presses. It can be used for both small and large, simple or complex shapes. The tooling cost and complexity of the process are higher than for uniaxial pressing, but the uniform density and ability to produce more intricate shapes make it a preferred option in certain applications.
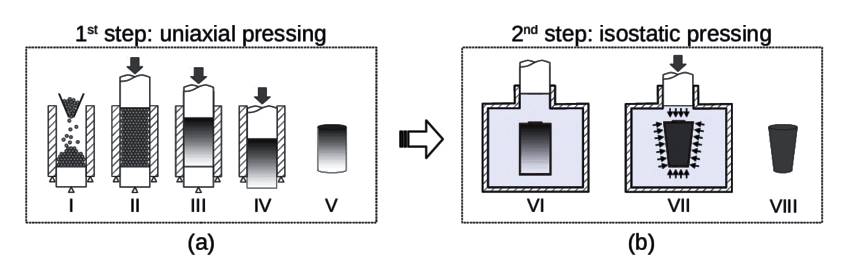
Overall, isostatic pressing provides a unique and effective method for achieving high-density compacts with uniform microstructure and shape control. Its advantages make it a valuable technique in various industries, including ceramics, metals, composites, plastics, and carbon.
Cold Isostatic Pressing vs Hot Isostatic Pressing
Definition of CIP and HIP
Cold Isostatic Pressing (CIP): Cold Isostatic Pressing, often referred to as cold isostatic compaction, involves subjecting a material to uniform pressure from all sides. This is achieved by immersing the material in a high-pressure fluid medium and applying hydraulic pressure. CIP is particularly effective for shaping and consolidating powdered materials, creating intricate shapes and achieving high green density.
Hot Isostatic Pressing (HIP): Hot Isostatic Pressing, on the other hand, takes the process a step further by combining high pressure with elevated temperatures. This method subjects a material to simultaneous high pressure and high temperature within a high-pressure chamber. HIP is used to densify materials, eliminate defects, and enhance properties through diffusion and consolidation. It's especially valuable for materials requiring improved structural integrity, reduced porosity, and higher mechanical properties.
Use Cases of CIP and HIP
In powder metallurgy, HIP allows us to compress a volume of metal powder at such high temperatures and pressures, that through a combination of deformation, creep, and diffusion, you actually create a product with a homogeneous annealed microstructure (compact solid) with minimal or no impurities in the materials. This is a key part of through-processing, from alloy design to component manufacture, and an essential process for aerospace components. The HIP has a 150mm diameter x 300mm long hot zone that is perfect for scaling up samples.
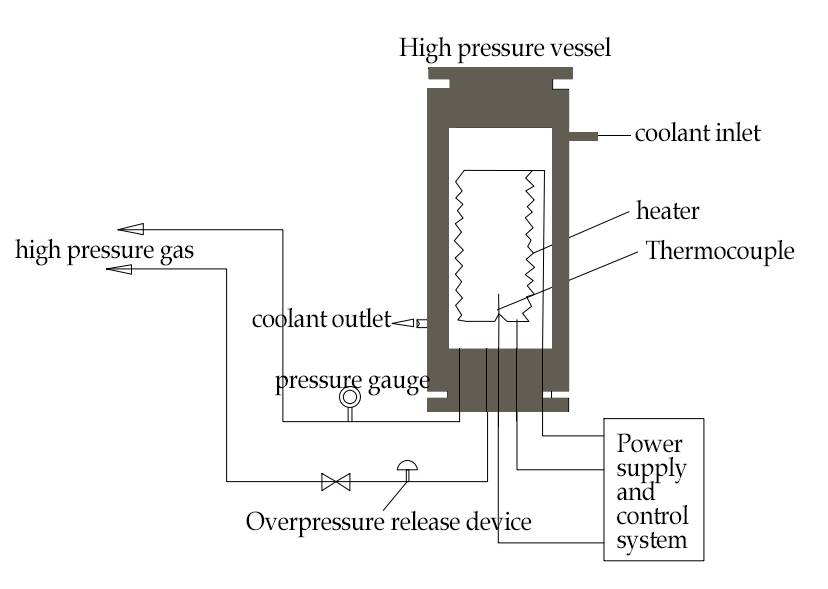
CIP, on the other hand, is often used for shaping and initial consolidation of powdered materials. Metal powder is placed inside a flexible mold made of rubber, urethane, or PVC. The assembly is then pressurized hydrostatically in a chamber, usually using water, with pressures ranging from 400 to 1000MPa. The powder gets compacted, and the green compact is taken out and sintered.
Role of HIP in Eliminating Residual Porosity
Hot Isostatic Pressing (HIP) is used to reduce the porosity of metals and increase the density of many ceramic materials. The pressure and temperature applied during the HIP process allow for plastic deformation, creep, and diffusion to occur, effectively eliminating internal microporosity and improving the mechanical properties of the material. HIP also enables the bonding or cladding of two or more materials together, either in solid or powder form.
In summary, Cold Isostatic Pressing and Hot Isostatic Pressing represent distinct approaches to materials processing, each with its own advantages. CIP is effective for shaping and consolidating powdered materials, while HIP is used to densify materials, eliminate defects, and enhance properties through diffusion and consolidation. The decision between the two techniques depends on the specific goals of your project and the characteristics of the materials involved.
Benefits and Applications of Cold Isostatic Pressing (CIP)
Advantages of CIP
Cold Isostatic Pressing (CIP) is a powder-compacting process that offers several advantages. One of the main benefits is the ability to produce parts with high green strength, which allows for premachining before sintering without causing breakage. This is especially useful when the high cost of pressing dies cannot be justified or when very large or complex compacts are needed.
CIP also provides the capability to produce parts with a density ranging from 60 to 80% of the theoretical density. The high compaction and uniform density obtained through CIP result in predictable shrinkage during the subsequent sintering process. This allows for better control over the final dimensions of the part.
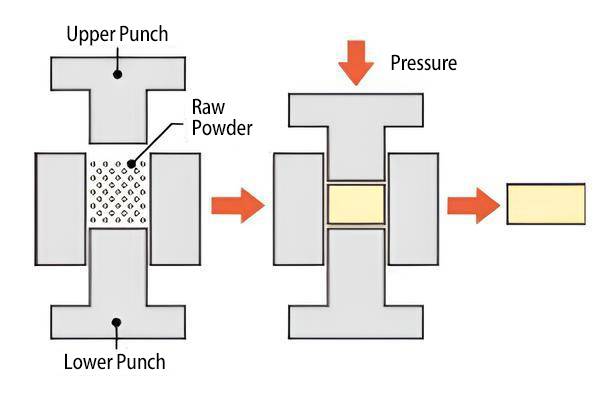
Another advantage of CIP is the ability to process large, complicated, and near-net shapes. This saves time and cost in after-treatment and allows for the production of parts with large aspect ratios (>2:1) and uniform densities.
The green strength obtained in CIP also allows for in-process handling and treatment, reducing production costs. Overall, CIP offers a cost-effective and efficient method for producing high-quality parts.
Types of Powders Suitable for CIP
A variety of powders can be pressed isostatically using CIP. This includes metals, ceramics, plastics, and composites. CIP is a versatile process that can be applied to a wide range of materials, making it suitable for various industries and applications.
Range of Pressures for Compacting in CIP
The pressures required for compacting powders in CIP can range from less than 5,000 psi to more than 100,000 psi (34.5 to 690 MPa). The specific pressure used depends on factors such as the material being compacted, the desired density of the part, and the size and complexity of the shape.
Compacting Process in CIP
In CIP, powders are compacted in elastomeric molds using either a wet or dry bag process. In the wet bag process, the powder is preformed and then sealed in a flexible bag or mold. The bag is placed within a hydraulic fluid, such as oil or water, in a pressure vessel. Pressure is applied to the fluid, evenly distributed across the material, typically between 10,000 and 60,000 psi. This method helps reduce distortion, improve accuracy, and minimize the risk of air entrapment and voids.
The dry bag process is similar, but the powder is compacted in a dry elastomeric mold without the need for a hydraulic fluid. The mold is then subjected to high pressure from all sides to achieve compaction.
CIP is a widely used process in industries such as powdered metallurgy, cemented carbides, refractory materials, graphite, ceramics, plastics, and more. It offers solid-state processing, uniform microstructure, shape complexity, low tooling cost, and process scalability, making it a viable processing route for metals as well.
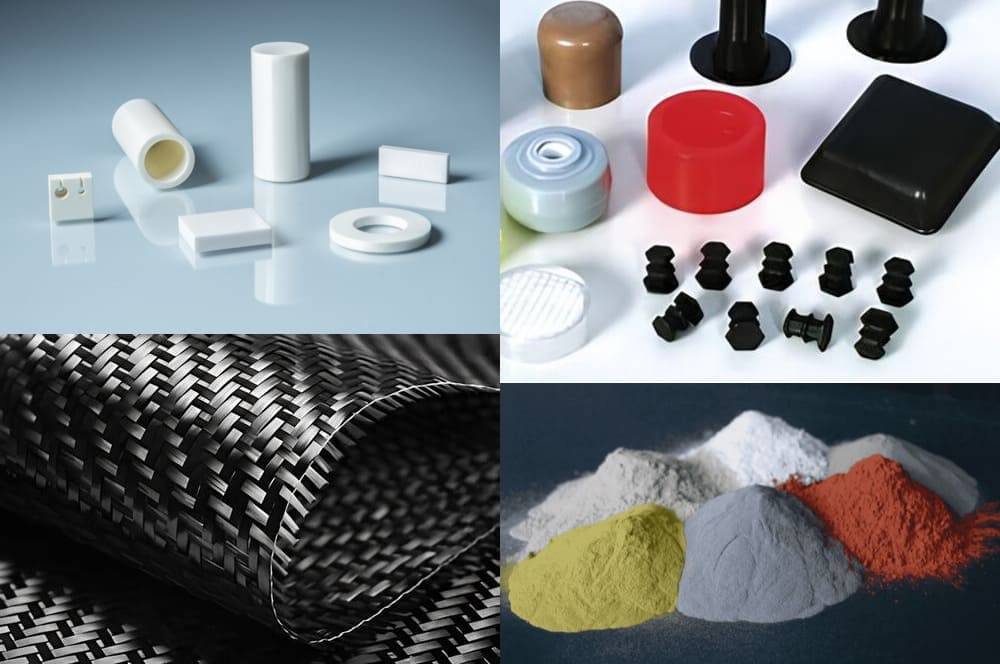
According to a report by DataIntelo, the global Cold Isostatic Pressing (CIP) Equipment Market is projected to grow at a substantial CAGR during the forecast period. The surge in demand for CIP-processed products in industries like precision manufacturing, aerospace & defense, and automotive is driving this growth.
In conclusion, Cold Isostatic Pressing (CIP) offers numerous benefits and applications in the production of metal and ceramic components. Its ability to produce high-density parts with predictable shrinkage, process large and complex shapes, and reduce production costs makes it a valuable method in various industries.
Conclusion
In conclusion, understanding the process of isostatic pressing in powder metallurgy is crucial for achieving high-density and structurally sound components. Isostatic pressing offers numerous advantages over traditional uniaxial pressing, including improved uniformity, enhanced density, and reduced residual porosity. Additionally, cold isostatic pressing (CIP) and hot isostatic pressing (HIP) have their own unique applications and benefits. CIP is particularly suitable for a wide range of powders and can be compacted at various pressures. Overall, isostatic pressing techniques play a vital role in the production of high-quality, reliable components in various industries such as aerospace, automotive, and medical.
If you are interested in this product you can browse our company website:https://kindle-tech.com/product-categories/isostatic-press, as an industry-leading laboratory equipment manufacturer, we are committed to providing the most advanced and high-quality laboratory equipment solutions. Whether you are engaged in scientific research, teaching or industrial production, our products will meet your needs for accurate and reliable laboratory equipment.
CONTACT US FOR A FREE CONSULTATION
KINTEK LAB SOLUTION's products and services have been recognized by customers around the world. Our staff will be happy to assist with any inquiry you might have. Contact us for a free consultation and talk to a product specialist to find the most suitable solution for your application needs!